How Stainless Steel Coils Are Made: Step-by-Step
Ever wondered about the fiery journey and meticulous processes behind the gleaming stainless steel coils used in countless applications? This lack of insight can make it hard to appreciate their value or discern quality. Imagine understanding each critical stage, empowering you to make more informed decisions.
Stainless steel coils are made through a multi-stage process involving melting raw materials like iron ore, chromium, and nickel, casting into slabs, hot rolling to reduce thickness, cold rolling for finer precision and surface, and finally, annealing and pickling for desired properties and finish.
This complex transformation from basic elements to high-performance stainless steel coils is a testament to modern engineering and metallurgical science. As Global Business Director at MFY, I've had the privilege of witnessing this intricate dance of heat, pressure, and precision firsthand. We'll embark on a detailed exploration of this fascinating manufacturing process.
The journey of a stainless steel coil, from raw ore to a finished product ready for global markets, is a symphony of advanced technology and rigorous quality control. At MFY, we are deeply integrated into this supply chain, from raw material trading to cold-rolled processing1 and export. Understanding this process is key not only for us as producers but also for our clients – manufacturing companies, engineering contractors, and distributors across India, Southeast Asia, and the Middle East. It allows them to appreciate the value embedded in each coil and make specification choices that best suit their applications, whether it's for robust industrial equipment or precision components. This knowledge, which we'll delve into, underpins our commitment to transparency and quality, ensuring our MFY-branded coils meet the highest international standards.
What raw materials are required for producing stainless steel coils?
Curious about the fundamental building blocks that give stainless steel its renowned strength and corrosion resistance? Not knowing these raw materials makes it difficult to understand the coil's intrinsic value and specific properties. We're about to unveil the essential ingredients.
The primary raw materials for stainless steel coils include iron ore (for iron), chromium (for corrosion resistance), nickel (for formability and ductility, especially in austenitic grades), molybdenum (for enhanced corrosion resistance), and often recycled stainless steel scrap.
The specific blend of these raw materials is what defines the different grades of stainless steel, each with unique characteristics tailored for specific environments and applications. For instance, the higher nickel content in 300-series austenitic grades, like the popular 304 or 316, imparts excellent corrosion resistance and formability, making them staples for our clients at MFY, from kitchenware manufacturers to automotive component producers. The selection and quality control of these raw materials are the very first, and arguably one of the most critical, steps in ensuring the final coil meets the stringent standards our customers in markets like India, Southeast Asia, and Russia expect. It's a precise science; even small variations in the input materials can significantly impact the mechanical properties and performance of the finished stainless steel coil. This initial stage sets the foundation for the entire manufacturing process, influencing everything from melting parameters to the final surface finish. We'll explore how these elements are sourced, processed, and combined to initiate the creation of high-quality MFY stainless steel.
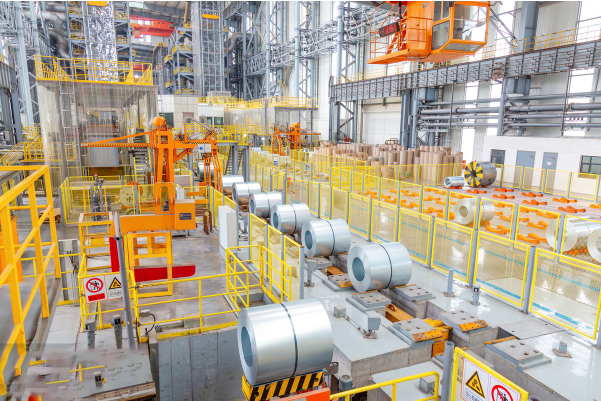
The creation of stainless steel is akin to a master chef preparing a gourmet meal; the quality of the final dish is inextricably linked to the quality of the starting ingredients. At MFY, with our deep roots in the stainless steel industry and a business model that integrates raw material trading, we understand this principle intimately. The selection of raw materials is not merely a procurement task; it's a strategic decision that impacts the entire value chain, from our production efficiency to the performance of our coils in our clients' diverse applications across the globe. The core elements – iron, chromium, nickel, and molybdenum, among others – are carefully chosen and balanced to achieve the specific properties of the desired stainless steel grade. For example, the precise amount of chromium is critical for forming the passive layer that gives stainless steel its signature corrosion resistance. Nickel enhances formability and toughness, particularly at low temperatures, which is a key requirement for some of our clients in colder regions like Russia. Molybdenum is added to grades like 316 to bolster resistance against pitting and crevice corrosion, especially in chloride-rich environments, a frequent concern for our customers in coastal areas or the chemical processing industry. The journey of these materials, from mines and recycling centers to our melting furnaces, is one we monitor closely to uphold the MFY promise of quality and reliability.
Core Alloying Elements: The Foundation of Stainless Steel's Properties
The defining characteristic of stainless steel is its chromium content, which must be at least 10.5% by weight. This is the magic ingredient that reacts with oxygen in the air to form a thin, invisible, and incredibly tenacious layer of chromium oxide on the surface of the steel. This "passive layer" is self-repairing; if scratched, it reforms almost instantly, providing continuous protection against corrosion. It's this property that makes stainless steel "stainless." At MFY, when we source materials for grades like the common 304, we ensure the chromium content is well within the specified range (typically 18-20%) to guarantee optimal corrosion resistance for applications ranging from food processing equipment to architectural panels. I remember a client in Southeast Asia, a manufacturer of high-quality kitchen sinks, who specifically chose our MFY 304 coils precisely because of their consistent passivation quality, which they attributed to our rigorous control over chromium content.
Nickel is another cornerstone, particularly for the widely used austenitic stainless steels (like the 300 series – 304, 316). Nickel acts as an austenite stabilizer, meaning it helps maintain the face-centered cubic crystal structure of the steel even at room temperature. This structure imparts excellent ductility, formability (making it easier to shape into complex coil forms and subsequent products), toughness (even at cryogenic temperatures), and good weldability. The typical nickel content in 304 stainless steel is around 8-10.5%. Molybdenum, often found in grades like 316 (usually 2-3%), significantly enhances resistance to pitting and crevice corrosion, especially in environments containing chlorides (like seawater or de-icing salts). This makes 316 MFY coils a preferred choice for marine applications or chemical processing equipment, a demand we see consistently from our clients in the Middle East.
Other elements like manganese, silicon, carbon, nitrogen, titanium, and niobium are also added in smaller, controlled amounts to fine-tune specific properties. For instance, carbon content is carefully controlled; lower carbon (e.g., in 304L or 316L grades, where 'L' means low carbon, typically <0.03%) improves weldability by reducing the risk of sensitization (chromium carbide precipitation at grain boundaries). Nitrogen can increase strength and further improve pitting resistance. At MFY, our integrated R&D and production capabilities allow us to manage these complex alloying recipes, ensuring that each coil of stainless steel we produce, whether it's a standard grade or a specialized variant, possesses the precise chemical composition required for its intended service. This meticulous attention to alloying is fundamental to our vision of becoming a leading international trade and service brand in China’s stainless steel industry.
The Crucial Role of Recycled Stainless Steel Scrap
Beyond virgin raw materials like iron ore, chromium, and nickel sourced from primary mining operations, recycled stainless steel scrap plays an indispensable and increasingly important role in the production of new stainless steel. In fact, stainless steel is one of the most recycled materials on the planet, with studies indicating that up to 60-80% of new stainless steel is typically made from recycled scrap2. This high recyclability is a significant environmental advantage, reducing the need for virgin resource extraction, lowering energy consumption in the melting process (using scrap can save up to 75% of the energy compared to using only primary raw materials), and minimizing landfill waste. This aligns perfectly with the growing global emphasis on sustainability, a value MFY champions.
At MFY, our raw material trading arm actively engages in sourcing high-quality stainless steel scrap. The scrap can come from various sources: "process scrap" generated during manufacturing (like off-cuts from our own coil processing or from our clients' manufacturing operations) and "end-of-life scrap" from discarded stainless steel products (like old appliances, decommissioned industrial equipment, or demolished structures). The key is careful sorting and analysis of this scrap to ensure its chemical composition is known and suitable for re-melting into specific grades. For example, if we are producing a batch of 316 stainless steel, the scrap used must also be predominantly 316 or have a known composition that can be blended with virgin alloys to achieve the target 316 chemistry. Advanced analytical techniques like X-ray fluorescence (XRF) are often employed to rapidly verify scrap composition.
The use of scrap not only offers environmental benefits but can also provide economic advantages by reducing reliance on often volatile primary commodity markets. However, it requires sophisticated melt shop practices to manage potential impurities that might be present in scrap. Our partner mills and our own quality control processes ensure that the inclusion of scrap does not compromise the final quality of MFY stainless steel coils. We view effective scrap utilization as a key component of our fully integrated supply chain and our commitment to innovation-driven development, contributing to a more circular economy within the stainless steel industry. This responsible approach resonates well with our environmentally conscious clients, particularly in markets like Europe (though our primary exports are listed as India, SE Asia, Middle East, Russia) and increasingly, large manufacturing companies globally who are tracking their own Scope 3 emissions.
MFY's Sourcing Strategy and Quality Assurance for Raw Materials
At MFY, our diversified group structure, which includes raw material trading, gives us a strategic advantage in sourcing the essential ingredients for our stainless steel coils. Our sourcing strategy is multi-faceted, focusing on securing high-quality virgin alloys (chromium, nickel, molybdenum, etc.) from reputable global suppliers and concurrently optimizing the intake of certified recycled stainless steel scrap. This balanced approach helps us manage costs, ensure supply chain resilience, and uphold our commitment to sustainability. We have established long-term relationships with key mining companies and metal traders, allowing us to procure materials that meet stringent purity and compositional standards. For instance, the ferrochrome (an alloy of iron and chromium) and ferronickel we source are subject to rigorous incoming inspection.
Quality assurance begins well before the materials reach the melting furnace. Upon arrival at our partner facilities or our own processing centers, all raw materials, including scrap, undergo thorough inspection and chemical analysis. We employ advanced spectroscopic techniques to verify the composition of each batch. This is critical because, as mentioned, even slight deviations in alloying elements can affect the final properties and performance of the stainless steel. For example, if producing a batch of 304L stainless steel, the carbon content of all inputs must be carefully monitored to ensure the final product meets the low-carbon specification (<0.03%), which is vital for preventing weld decay in applications our engineering and construction contractor clients might undertake. This meticulous QA process is a cornerstone of MFY’s brand promise.
Furthermore, our digital innovation initiatives extend to our raw material management. We utilize sophisticated inventory systems and traceability protocols that allow us to track materials from source to final product. This not only aids in quality control but also provides valuable data for process optimization and for providing our customers with comprehensive material certifications. As Global Business Director, I've seen how this level of transparency and commitment to input quality builds immense trust with our clients, from large distributors who rely on our consistent product to manufacturing companies who integrate our coils into their own high-value products. This diligent front-end work ensures that the MFY stainless steel coils shipped to India, Southeast Asia, or any of our export markets are built on a foundation of verified quality.
Element | Symbol | Key Role in Stainless Steel | Typical % in 304 | Typical % in 316 | Source Example |
---|---|---|---|---|---|
Iron | Fe | Base metal, forms the bulk of the alloy | Balance | Balance | Iron Ore |
Chromium | Cr | Forms passive layer for corrosion resistance (min 10.5%) | 18-20% | 16-18% | Ferrochrome |
Nickel | Ni | Stabilizes austenite, enhances formability, ductility, toughness | 8-10.5% | 10-14% | Ferronickel, Nickel Cathodes |
Molybdenum | Mo | Enhances pitting/crevice corrosion resistance (in chloride env.) | Trace (if any) | 2-3% | Ferromolybdenum |
Carbon | C | Affects strength and weldability (low C for better welding) | <0.08% (<0.03% for L) | <0.08% (<0.03% for L) | Present in raw materials |
Manganese | Mn | Austenite stabilizer, deoxidizer, improves hot workability | <2% | <2% | Ferromanganese |
Silicon | Si | Deoxidizer, improves strength and scaling resistance | <0.75% | <0.75% | Ferrosilicon |
Nickel improves stainless steel's formabilityTrue
Nickel stabilizes austenite structure, enhancing ductility and formability in 300-series stainless steels.
Stainless steel can't be recycledFalse
60-80% of new stainless steel is made from recycled scrap, making it highly sustainable.
How is stainless steel melted and cast into slabs?
Ever pictured the intense heat and precision required to transform solid raw materials into molten stainless steel, ready for shaping? Without this understanding, the journey to a coil seems almost magical, obscuring the critical controls. Let's illuminate this fiery stage.
Stainless steel is typically melted in an Electric Arc Furnace (EAF) or an Induction Furnace, followed by refining in an Argon Oxygen Decarburization (AOD) converter to adjust composition and remove impurities, before being continuously cast into solid slabs.
This melting and casting phase is where the carefully selected raw materials are fused and their chemical composition is precisely honed. At MFY, we work with partner mills that employ state-of-the-art melting technologies to ensure the homogeneity and purity of the steel. The choice between EAF and AOD, for example, depends on the scale of production and the specific grades being produced, but the goal is always the same: to create a clean, molten steel with the exact target chemistry. The subsequent continuous casting process is a marvel of engineering, transforming the liquid metal into uniform, defect-free slabs – the semi-finished product that will then embark on its journey through the rolling mills. This stage is critical; any inconsistencies here can propagate through the entire manufacturing chain, impacting the quality of the final MFY coil destined for our discerning customers.
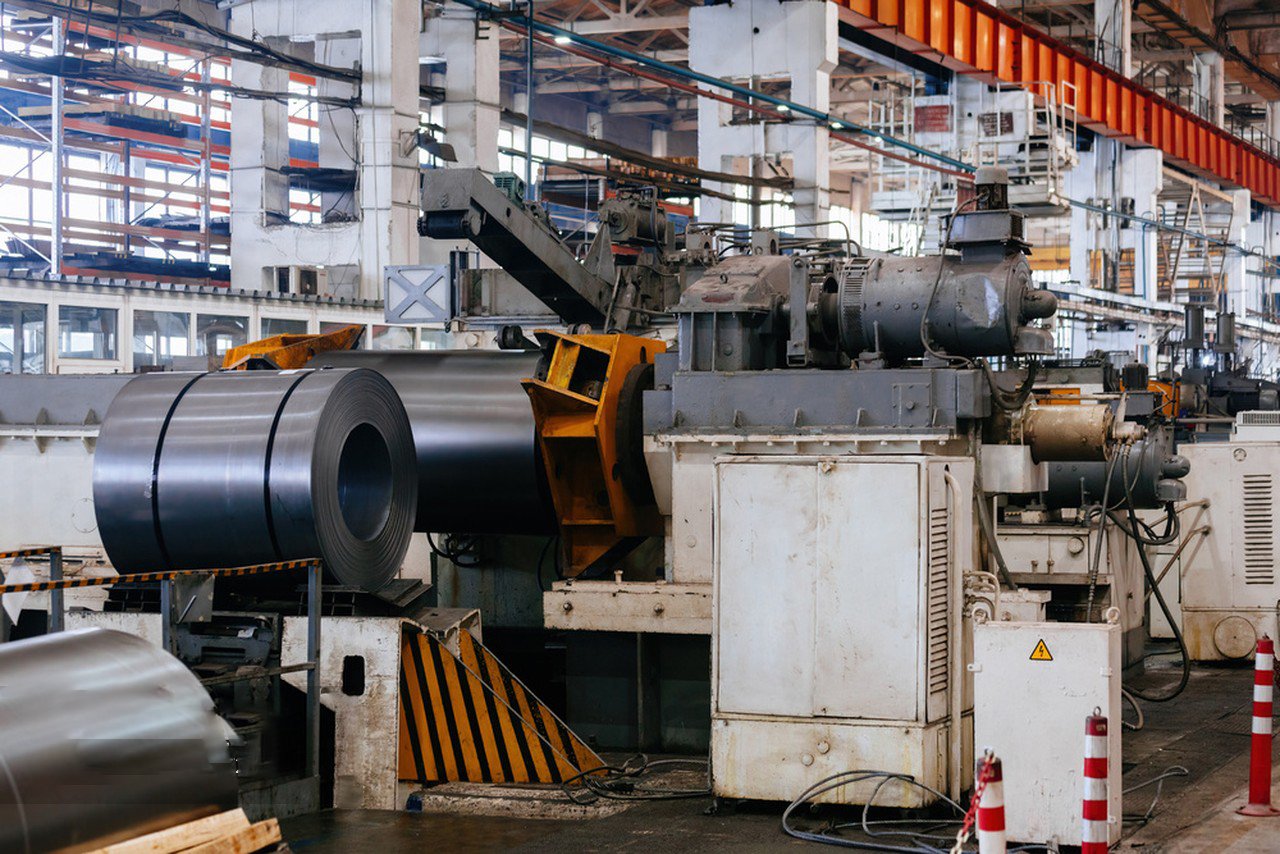
The transformation of solid raw materials and scrap into a precisely formulated molten bath, and then into solid, manageable slabs, is a cornerstone of stainless steel production. This stage is characterized by immense energy, sophisticated metallurgical control, and precision engineering. At MFY, our integration into the stainless steel supply chain means we have a deep appreciation for the complexities involved in this 'hot metal' phase. The choice of melting technology, the refining processes, and the casting techniques all have profound impacts on the cleanliness, consistency, and ultimately the performance characteristics of the stainless steel. For instance, the ability to tightly control carbon content during refining in an AOD converter is crucial for producing low-carbon grades like 304L or 316L, which offer superior weldability – a key requirement for many of our clients in engineering, construction, and equipment manufacturing. Similarly, the continuous casting process must be carefully managed to prevent defects like cracks, porosity, or segregation of alloying elements, any of which could compromise the integrity of the final MFY stainless steel coil. Our commitment to quality means we partner with mills that demonstrate excellence in these foundational processes, ensuring that the slabs forming the basis of our coils are of the highest standard.
The Melting Process: Electric Arc Furnace (EAF) and Argon Oxygen Decarburization (AOD)
The journey of converting raw materials into stainless steel typically begins in an Electric Arc Furnace (EAF). The EAF is a high-powered furnace that uses graphite electrodes to generate intense heat through electrical arcs, melting the charge of scrap steel and virgin alloying elements. Temperatures inside an EAF can exceed 1600°C (2900°F). This initial melting phase is primarily about liquefying the materials and achieving a base composition. EAFs are highly efficient for melting scrap, contributing to the sustainability of stainless steel production. At MFY, we understand that the operational efficiency and control within the EAF process at our partner mills directly impact the initial quality and cost-effectiveness of the steel that will eventually become our MFY branded coils.
Once the initial melt is achieved in the EAF (or sometimes an induction furnace for smaller, specialized batches), the molten steel is typically transferred to an Argon Oxygen Decarburization (AOD) converter for refining. The AOD process is crucial for producing most stainless steel grades, especially those requiring precise control of carbon content and removal of impurities like sulfur. In the AOD vessel, a mixture of argon and oxygen (and sometimes nitrogen) is injected into the molten bath. The oxygen reacts with carbon to form carbon monoxide gas, effectively reducing the carbon content to very low levels (e.g., below 0.03% for 'L' grades) without excessive oxidation of valuable chromium. Argon is used to dilute the gases, improving the efficiency of carbon removal and protecting chromium. The AOD process also allows for precise additions of other alloying elements to fine-tune the final chemistry and for desulfurization. I've visited several advanced melt shops, and the control room for an AOD converter is like a high-tech command center, with operators closely monitoring temperatures and chemical compositions in real-time.
The EAF-AOD duplex process is the workhorse for high-volume stainless steel production, offering a balance of productivity, quality control, and cost-efficiency. For certain specialty grades or smaller production runs, Vacuum Induction Melting (VIM) or Vacuum Oxygen Decarburization (VOD) might be used for even tighter control over impurities and gas content, though these are generally more expensive. MFY’s diverse product range, including various grades of stainless steel coils, relies on the capability of our supply chain to employ the appropriate melting and refining technologies to meet the specific requirements of each grade, ensuring consistent quality for our clients in demanding markets like the Middle East and Russia.
Continuous Casting: From Molten Steel to Solid Slabs
After the molten stainless steel has been refined to the precise chemical composition in the AOD or other refining vessels, it is ready for casting. The dominant method for casting stainless steel intended for coils is continuous casting. This highly efficient process transforms the liquid steel into solid, semi-finished shapes – typically thick slabs – in a continuous operation, avoiding the need for individual ingot casting and subsequent reheating and shaping, which saves energy and improves yield. The molten steel is poured from a ladle into a tundish, which acts as a reservoir and helps regulate the flow of metal into the caster. The tundish feeds the steel at a controlled rate into a water-cooled copper mold, which is open at the bottom. The mold oscillates to prevent the solidifying steel from sticking.
As the steel passes through the mold, a thin solid shell forms around the still-molten core. The partially solidified strand is then continuously withdrawn from the bottom of the mold by a series of support and guide rolls. As it travels, it is further cooled by water sprays, causing solidification to progress inwards until the entire cross-section is solid. The strand, now a continuous length of solid steel, is then straightened from its curved path (if a curved mold caster is used) and cut by torches or mechanical shears into individual slabs of predetermined lengths, typically several meters long and 150-250 mm thick. The dimensions of these slabs (width and thickness) are carefully controlled as they will directly influence the subsequent hot rolling process. For instance, a wider slab will be used to produce wider stainless steel coils, a key product for MFY.
The continuous casting process offers significant advantages over older ingot casting methods, including improved product quality (more uniform structure and fewer defects), higher yield (less material wasted), increased productivity, and energy savings. However, it requires precise control over casting speed, cooling rates, and mold conditions to prevent defects such as surface cracks, internal porosity, or centerline segregation of alloying elements. MFY relies on partner mills that have mastered continuous casting technology, ensuring that the slabs used to produce our stainless steel coils are homogenous and free from defects that could compromise the final product's integrity. This consistent slab quality is vital for our downstream processing and for meeting the expectations of our manufacturing and engineering clients.
Quality Control and Metallurgical Adjustments in the Hot Metal Stage
Throughout the melting and casting stages, rigorous quality control measures are paramount. This is not just about achieving the target chemical composition but also about controlling temperature, removing impurities, and ensuring the cast slab has the desired internal structure and surface quality. Samples of molten steel are taken frequently from the EAF, AOD, and tundish for rapid chemical analysis using spectrographic techniques. These near real-time results allow metallurgists to make precise additions of alloying elements or adjust process parameters to bring the steel within the tight specification limits for the intended grade. For example, if analysis shows slightly low nickel content for a batch of 304 stainless, precise additions of ferronickel will be made in the AOD.
Temperature control is also critical. The steel must be hot enough to ensure fluidity during casting but not so hot as to damage refractory linings or cause excessive alloy oxidation. Optical pyrometers and thermocouples are used extensively to monitor and control temperatures at each step. Beyond chemistry and temperature, controlling dissolved gases like oxygen, nitrogen, and hydrogen is important. Excessive dissolved gases can lead to porosity in the cast slab or affect the steel's mechanical properties. The refining processes (AOD, VOD) are designed to manage these gas levels. For instance, the argon bubbling in AOD helps to remove dissolved gases.
Once the slabs are cast and cut, they undergo further inspection. This includes visual inspection for surface defects like cracks or slag patches. Sometimes, ultrasonic testing may be employed to check for internal defects. Slabs with minor surface defects might be conditioned (e.g., by grinding) before hot rolling, while slabs with severe defects would be rejected and recycled. This meticulous attention to quality in the hot metal stage, something MFY insists upon in its supply chain, ensures that only sound, correctly composed slabs proceed to the hot rolling mill. This foundational quality is essential for producing the high-caliber stainless steel coils that MFY exports to markets like India and Southeast Asia, where product reliability is non-negotiable. Our integrated approach, combining raw material trading with production oversight, allows us to maintain this focus on quality from the very beginning.
Process Stage | Equipment Used | Key Objective(s) | MFY's Focus / Implication |
---|---|---|---|
Initial Melting | Electric Arc Furnace (EAF) or Induction Furnace | Melt scrap & raw materials, initial chemical composition. | Efficient, cost-effective melting of quality inputs. |
Refining | Argon Oxygen Decarburization (AOD) Converter, VOD/VIM (specialty) | Precise carbon control, removal of impurities (S, gases), final alloy trimming. | Crucial for grade purity (e.g., 'L' grades), cleanliness. |
Pre-Casting | Ladle Metallurgy Furnace (LMF) (optional) | Temperature homogenization, inclusion modification, final fine-tuning of chemistry. | Enhanced steel cleanliness and consistency. |
Casting | Continuous Casting Machine (Slab Caster) | Solidify molten steel into uniform slabs with good internal & surface quality. | Defect-free slabs, consistent dimensions for rolling. |
Quality Control | Spectrometers, Pyrometers, Ultrasonic Testers | Verify chemical composition, temperature, internal/surface integrity. | Ensures only sound, on-spec slabs proceed to rolling. |
AOD reduces carbon contentTrue
The Argon Oxygen Decarburization process specifically targets carbon removal while protecting chromium from excessive oxidation.
EAF melts finished coilsFalse
Electric Arc Furnaces melt raw materials and scrap, not finished products. Coils are produced much later in the manufacturing process.
What processes are involved in hot rolling stainless steel slabs?
Now that we have solid slabs, how are they transformed into much thinner, longer pieces suitable for coiling? This stage is a powerful display of force and heat, but without understanding it, the coil's basic form remains a mystery. Let's explore this shaping process.
Hot rolling involves reheating stainless steel slabs to high temperatures (typically above 1000°C) and then passing them through a series of powerful rollers to progressively reduce their thickness and elongate them, ultimately forming a hot-rolled band or strip.
This high-temperature deformation process is fundamental to achieving the initial thickness reduction and refining the grain structure of the steel. At MFY, we understand that the precision of the hot rolling process3 directly impacts the dimensional accuracy and mechanical properties of the precursor material for our cold-rolled coils. The slabs are heated in a reheating furnace to ensure they are malleable enough for rolling. They then travel through roughing stands and finishing stands, each pass further squeezing and stretching the steel. The final hot-rolled coil, though not yet possessing the fine finish or tight tolerances of a cold-rolled product, is a critical intermediate step. The quality achieved here sets the stage for all subsequent cold processing operations that MFY might undertake or oversee.
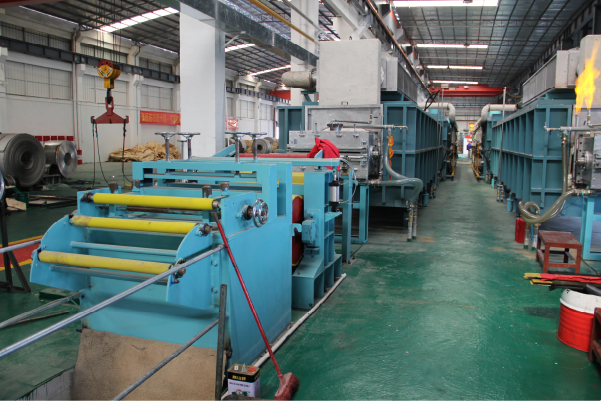
Hot rolling is a truly transformative process, where brute force, extreme temperatures, and metallurgical science converge to reshape massive stainless steel slabs into thinner, more manageable strips. As someone deeply involved in MFY's global business, I've seen how the capabilities of a hot rolling mill – its power, precision, and control systems – are pivotal to the quality of the feedstock for further processing, including our own cold-rolling operations and the hot-rolled coils we might directly trade. The reheating of the slab must be uniform to ensure consistent plastic deformation. The successive passes through the rolls are not just about reducing thickness; they also critically influence the microstructure of the steel, breaking down the coarse, as-cast grain structure into finer, more uniform grains, which enhances mechanical properties like toughness and ductility. Control over temperature throughout the rolling and subsequent cooling process is also vital to prevent undesirable phase transformations or the formation of excessive scale (oxide layer) on the surface. This careful orchestration of heat and pressure4 is essential for producing hot-rolled stainless steel coils that meet MFY's stringent quality benchmarks before they even enter the cold-rolling phase or are supplied to our clients who use hot-rolled products directly.
Reheating Slabs for Optimal Malleability
Before the stainless steel slabs can undergo the significant deformation of hot rolling, they must be uniformly heated to a specific temperature range where the material is highly malleable and its resistance to deformation is low. This is typically done in large reheating furnaces, such as walking beam furnaces or pusher-type furnaces. The target temperature for hot rolling stainless steel is generally above 1000°C (1832°F), often in the range of 1100°C to 1250°C (2012°F to 2282°F), depending on the specific grade. For example, austenitic grades like 304 or 316 are typically heated to the higher end of this range. The reheating process must be carefully controlled to ensure the entire slab reaches the target temperature uniformly, from surface to core. Non-uniform heating can lead to inconsistencies during rolling, affecting dimensional accuracy and mechanical properties.
The atmosphere within the reheating furnace is also controlled to minimize the formation of excessive scale (iron and chromium oxides) on the slab surface. While some scale formation is inevitable at these high temperatures, excessive scaling results in material loss and can be pressed into the surface during rolling, leading to defects. Modern reheating furnaces often use controlled fuel-air ratios or protective atmospheres to manage this. The time the slab spends in the furnace (soaking time) is also critical – long enough to ensure thorough and uniform heating, but not so long as to cause excessive grain growth or scaling. At MFY, we ensure our partner mills utilize advanced reheating technologies. I recall discussing with engineers at a leading mill how their precise temperature profiling within their walking beam furnace, using numerous thermocouples and a sophisticated control system, significantly improved the consistency of their hot-rolled product, which ultimately benefits the quality of MFY coils.
Proper reheating is the first critical step in the hot rolling sequence. If the slab is too cold, it will require excessive rolling forces, potentially damaging the mill equipment, and the steel may crack. If it's too hot, there's a risk of incipient melting at the grain boundaries or excessive grain growth, which can degrade mechanical properties. Therefore, the expertise in managing this reheating stage is a key indicator of a mill's capability to produce high-quality hot-rolled stainless steel, the essential precursor for MFY's cold-rolled products and some direct hot-rolled offerings.
The Hot Rolling Mill: Roughing and Finishing Stands
Once uniformly reheated, the glowing hot slab is conveyed to the hot rolling mill. The mill typically consists of two main sections: roughing stands and finishing stands. The roughing stands are designed for large thickness reductions. A slab, which might be 150-250 mm thick, is passed back and forth (in a reversing mill) or through a series of non-reversing stands, each equipped with powerful rolls that squeeze the slab, reducing its thickness and increasing its length. High-pressure water jets are often used during this stage to descale the surface, removing the initial layer of oxide scale formed during reheating. This prevents the scale from being rolled into the steel surface, which would create defects.
After the roughing passes, the partially rolled piece, now called a transfer bar or breakdown, proceeds to the finishing mill. The finishing mill usually consists of a tandem train of several (e.g., 4 to 7) closely spaced rolling stands. The transfer bar enters the first finishing stand and is continuously rolled through all stands in a single pass, emerging from the last stand as a long, thin strip at the target hot-rolled thickness (typically ranging from about 1.5 mm to 10 mm or more, depending on the final application). The speed of rolling increases through the finishing train as the strip elongates and thins. Precise control over roll gaps, rolling speeds, and inter-stand tensions is crucial for achieving the desired thickness, width, and flatness of the hot-rolled strip. Advanced process control systems, utilizing sensors for thickness, width, temperature, and shape, continuously monitor and adjust rolling parameters in real-time. For MFY, the consistency of gauge (thickness) and profile (cross-sectional shape) from the hot rolling process is paramount, as this directly affects the efficiency and quality of subsequent cold rolling if the material is destined for our cold-rolled coils.
The forces involved in hot rolling are immense, and the mill stands are massive, robust structures. The work rolls, which are in direct contact with the hot steel, are made of special alloy steels or cast iron and are water-cooled to maintain their shape and prolong their life. These rolls are periodically reground or replaced to ensure a good surface finish on the rolled product. The sophistication of the hot rolling mill, including its mechanical setup and its automation and control systems, is a major factor in the quality of the hot-rolled stainless steel coils that serve as input for MFY's value-added processes.
Cooling, Coiling, and Initial Quality Checks of Hot-Rolled Bands
As the hot-rolled strip exits the final finishing stand, typically at temperatures still around 800-900°C, it undergoes controlled cooling on a run-out table before being coiled. The cooling rate on the run-out table is a critical metallurgical step, as it influences the microstructure (e.g., grain size, phase transformations) and, consequently, the mechanical properties of the hot-rolled product. Water sprays are strategically arranged along the run-out table to achieve the desired cooling profile. For austenitic stainless steels like 304 or 316, rapid cooling is often employed to retain alloying elements in solid solution and prevent the precipitation of detrimental phases like chromium carbides, which could impair corrosion resistance.
Once cooled to an appropriate temperature (e.g., 550-750°C), the long strip is fed into a downcoiler, which winds it into a compact hot-rolled coil, often referred to as a Hot Rolled Band (HRB) or Hot Rolled Black Coil (due to the dark oxide scale on its surface). These coils can weigh several tons. After coiling, the hot-rolled coils are allowed to cool further to ambient temperature. At this stage, initial quality checks are performed. These include verifying the dimensions (thickness, width) against specifications using gauges and measuring instruments. The surface quality is visually inspected for defects like scale patches, roll marks, or cracks. Samples may also be taken for preliminary mechanical testing (e.g., tensile strength, hardness) and microstructural examination to ensure the hot rolling process has achieved the desired outcomes.
These hot-rolled coils are a significant intermediate product in the MFY supply chain. Some may be sold directly to customers who use hot-rolled stainless steel for applications where surface finish is less critical, such as certain structural components or industrial equipment. However, a large proportion of these hot-rolled coils, particularly those of higher quality and finer gauges, will proceed to the next stage of processing: annealing and pickling, followed by cold rolling, to produce the MFY cold-rolled stainless steel coils that boast superior surface finish, tighter dimensional tolerances, and enhanced mechanical properties. The quality and consistency achieved during hot rolling are thus foundational for the excellence of our final products that reach our clients in construction, manufacturing, and distribution.
Parameter | Roughing Mill Objective | Finishing Mill Objective | Impact on MFY Coil Quality |
---|---|---|---|
Thickness Reduction | Significant reduction (e.g., 200mm to 20-40mm) | Precise reduction to final hot-rolled gauge (e.g., 20mm to 2mm) | Determines starting gauge for cold rolling, overall yield. |
Temperature Control | Maintain high malleability, prevent excessive heat loss | Control exit temperature for microstructure, coiling temp | Affects grain structure, mechanical properties, formability. |
Width Control | Initial width setting, edge rolling (if applicable) | Maintain consistent width, minimize spread | Ensures coils meet specified width for client applications. |
Surface Quality | Descaling to remove primary scale | Minimize new scale formation, prevent surface defects | Impacts surface of HR coils and feedstock for CR coils. |
Shape & Flatness | Basic shape control | Achieve good strip flatness and profile | Critical for smooth cold rolling and final product flatness. |
Grain Structure | Break down as-cast structure, initial grain refinement | Further refine grain structure through deformation & cooling | Influences strength, toughness, and ductility of the coil. |
Hot rolling requires temperatures above 1000°CTrue
Stainless steel slabs must be heated to 1100-1250°C for proper hot rolling malleability.
Cold rolling precedes hot rollingFalse
Hot rolling is the initial process that prepares slabs for subsequent cold rolling operations.
How are hot rolled stainless steel coils further processed into cold rolled coils?
Hot-rolled coils have taken shape, but what if your application demands a smoother surface, tighter tolerances, or enhanced strength? This is where the magic of cold rolling comes in, but its intricacies can be elusive. Let's delve into this refining stage.
Hot rolled stainless steel coils are processed into cold rolled coils through annealing and pickling processes (to clean and soften), followed by cold rolling (rolling at room temperature to reduce thickness, improve surface, and increase strength), and often further annealing.
This transformation from a relatively rough, scaled hot-rolled product to a bright, smooth, and precise cold-rolled coil is a critical value-adding process in the stainless steel industry, and a key part of MFY's production capabilities. The initial annealing and pickling step is vital to remove the oxide scale from the hot-rolled surface and to recrystallize the grain structure, making the steel soft and ductile enough for cold reduction. The cold rolling itself, performed on powerful multi-stand mills, imparts a superior surface finish, much tighter thickness tolerances, and can significantly enhance the steel's mechanical properties through work hardening. As Global Business Director at MFY, I've seen how our advanced cold rolling facilities and expertise allow us to produce coils that meet the exacting standards of our diverse clientele, from manufacturers of precision automotive parts to producers of high-end appliances and architectural elements across our export markets like India and the Middle East.
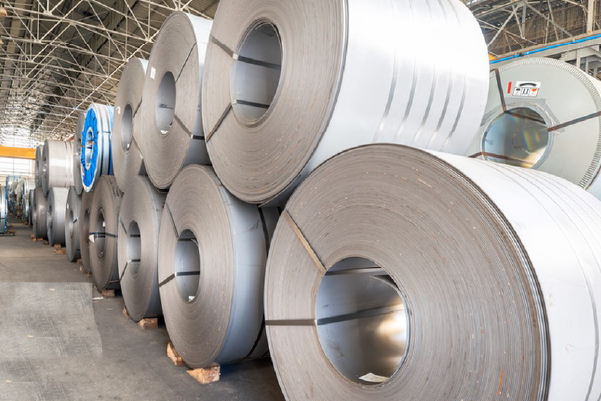
The journey from a hot-rolled band to a sophisticated cold-rolled stainless steel coil involves several meticulously controlled steps designed to enhance the material's properties and aesthetics. This is where MFY’s expertise in cold-rolled processing5 truly shines, transforming a good intermediate product into a premium material suitable for the most demanding applications. The initial annealing and pickling of the hot-rolled coil is not just a cleaning process; it's a crucial metallurgical treatment that prepares the steel for the rigors of cold reduction. It relieves internal stresses, refines the grain structure, and ensures a clean, scale-free surface, which is essential to prevent defects during cold rolling and to achieve the desired bright finish. The subsequent cold rolling operation is a feat of precision engineering, where massive forces are applied to reduce the steel's thickness at ambient temperature. This process not only achieves very tight dimensional tolerances but also significantly improves the surface quality and can be used to impart specific mechanical properties through controlled work hardening. Many of our clients, particularly equipment integrators and manufacturing companies requiring superior formability and a flawless finish, rely on MFY’s cold-rolled coils produced through these carefully managed processes.
Annealing and Pickling: Preparing the Hot-Rolled Coil
Before a hot-rolled stainless steel coil can be cold-rolled, it must undergo an essential preparatory stage: annealing followed by pickling6. Hot-rolled coils, as they come off the downcoiler, have a hardened microstructure due to the deformation and cooling experienced during hot rolling, and they are covered with a layer of dark oxide scale. Annealing is a heat treatment process where the coil is uncoiled and passed through a continuous annealing furnace. Here, it is heated to a specific temperature (e.g., around 1040-1150°C for austenitic grades like 304) and held for a certain time (soaked) to allow the microstructure to recrystallize. This process relieves internal stresses, softens the steel, refines the grain size, and dissolves most chromium carbides that might have precipitated, thereby restoring ductility and improving corrosion resistance. The cooling rate after annealing is also controlled, often rapidly, to prevent re-precipitation of carbides.
Following annealing, the steel strip, now softened but still covered with a tenacious oxide scale (which would be detrimental if rolled into the surface during cold rolling), proceeds to the pickling line. Pickling is a chemical descaling process where the strip is passed through a series of tanks containing acid solutions (typically a mixture of nitric and hydrofluoric acids for stainless steels, though other formulations exist). These acids dissolve the oxide scale, revealing a clean, metallic surface. The strip is then thoroughly rinsed with water to remove any residual acid and dried. At MFY, we work with facilities that employ advanced annealing and pickling lines (APLs) with strict environmental controls to manage acid fumes and wastewater. I've seen firsthand how the effectiveness of the pickling process directly impacts the surface quality of the final cold-rolled product; incomplete scale removal can lead to surface defects and reduced corrosion resistance.
The annealed and pickled (A&P) hot-rolled coil is now in an optimal condition for cold rolling: it is soft, ductile, and has a clean, scale-free surface. This A&P material is sometimes referred to as "HRAP" (Hot Rolled Annealed and Pickled) or "No. 1 Finish" (a common designation for this product state). This preparatory stage is non-negotiable for producing high-quality cold-rolled coils, and MFY ensures that this process is executed to the highest standards within our integrated supply chain.
The Cold Rolling Process: Achieving Precision and Finish
With the hot-rolled coil duly annealed and pickled, it's ready for cold rolling. Cold rolling is performed at room temperature (below the steel's recrystallization temperature) by passing the strip multiple times through a series of powerful rolling mills, such as Sendzimir mills (cluster mills known for high precision) or tandem cold mills (e.g., 4-high or 6-high mills). Each pass reduces the thickness of the strip by a controlled amount, typically ranging from a few percent up to 50% or more reduction in some initial passes. Since the steel is rolled cold, significant work hardening occurs – the material becomes stronger and harder, but less ductile. The total thickness reduction from the A&P hot-rolled band to the final cold-rolled gauge can be substantial, often exceeding 50-75% for many products.
The primary objectives of cold rolling are to achieve very precise thickness tolerances (often within a few hundredths of a millimeter), a superior surface finish (much smoother and brighter than hot-rolled), and to impart desired mechanical properties through work hardening. The rolls used in cold rolling mills are made of highly polished, hardened steel or tungsten carbide to ensure a smooth surface transfer to the stainless steel strip. Lubricants and coolants are used during cold rolling to reduce friction, dissipate the heat generated by deformation, and protect the rolls and strip surface. MFY's production network includes advanced cold rolling mills capable of producing coils with exceptional dimensional accuracy and surface quality. For instance, our capabilities allow us to produce coils with finishes like 2B (a bright, smooth finish commonly used for many applications), BA (Bright Annealed, a mirror-like finish), or other specific finishes required by our clients, such as those in the automotive or appliance sectors in India or the Middle East.
The degree of cold reduction significantly influences the final mechanical properties. A lightly cold-rolled product will be relatively soft and ductile, while a heavily cold-rolled product (sometimes referred to as "full hard" or specific tempers like 1/4 hard, 1/2 hard) will have much higher tensile strength and hardness but lower ductility. This ability to tailor mechanical properties through controlled cold work is a key advantage, allowing MFY to supply coils meeting specific strength requirements for various manufacturing processes and end-uses. The precision of our cold rolling operations is a testament to our innovation-driven development and a core part of our competitive strength.
Intermediate Annealing and Final Temper Rolling (Skin Pass)
For significant total thickness reductions or to achieve specific properties, one or more intermediate annealing and pickling steps may be required during the cold rolling sequence. As the stainless steel strip is cold-rolled, it work-hardens, becoming progressively harder and less ductile. If the desired final thickness requires a very large total reduction, the steel might become too hard to roll further without cracking or damaging the mill. In such cases, the partially cold-rolled coil is taken off the mill, annealed to soften it and restore ductility, pickled to clean its surface, and then returned to the cold rolling mill for further reduction. This cycle can be repeated as necessary.
After the final cold rolling pass to the target gauge, the coil might undergo a final annealing process, especially if a soft, ductile product is required (e.g., for deep drawing applications). If a bright, reflective surface is desired, this final annealing is often done in a protective atmosphere (like hydrogen or a hydrogen-nitrogen mixture) in a Bright Annealing (BA) furnace, which prevents oxidation and results in a mirror-like finish without the need for subsequent pickling. MFY supplies such BA finish coils for applications where aesthetics are paramount. However, for the common 2B finish, the coil is typically annealed and then lightly pickled after the final cold rolling.
Following the final anneal (and pickle, if applicable), many cold-rolled stainless steel coils undergo a light cold rolling pass known as a skin pass or temper pass. This involves a very small reduction in thickness (typically 0.5% to 2%). The skin pass serves several purposes: it improves flatness, imparts the desired final surface texture (e.g., making a 2B finish smoother and more uniform), minimizes the tendency for stretcher strains (unsightly lines that can appear during forming of annealed material), and can provide a slight increase in strength and hardness if desired. MFY’s cold-rolled coils, whether destined for distributors or direct use by manufacturing companies, often benefit from this final skin pass to ensure optimal surface quality and formability, reflecting our commitment to delivering high-quality, one-stop solutions.
Process Step | Input Material | Key Action(s) | Output Material / Condition | MFY Focus / Importance |
---|---|---|---|---|
1. Annealing (Hot-Rolled) | Hot-Rolled Coil (Black) | Heat to recrystallization temp, soak, controlled cool. | Softened, stress-relieved microstructure. | Prepares for pickling & cold rolling, improves ductility. |
2. Pickling | Annealed Hot-Rolled Coil | Chemical descaling in acid baths, rinsing, drying. | Clean, scale-free surface (No. 1 Finish / HRAP). | Essential for good surface in cold rolling, prevents defects. |
3. Cold Rolling | A&P Hot-Rolled Coil | Multiple passes through rolls at room temp, significant thickness reduction. | Thinner gauge, improved surface, work-hardened material. | Achieves precise thickness, desired finish (e.g., 2D), strength. |
4. Intermediate A&P (Optional) | Partially Cold-Rolled Coil | If further significant reduction needed; anneal to soften, pickle to clean. | Softened, clean material for more cold rolling. | Allows for very high total reductions, maintains formability. |
5. Final Annealing | Final Gauge Cold-Rolled Coil | Heat treatment to soften (if needed), or Bright Anneal for mirror finish. | Soft & ductile (e.g., for 2B finish) or bright (BA finish). | Tailors final mechanical properties and surface aesthetics. |
6. Skin Pass / Temper Rolling | Final Annealed Coil | Light cold roll (0.5-2% reduction). | Improved flatness, uniform surface (e.g., 2B), reduced stretcher strains. | Enhances final coil quality, appearance, and formability. |
Pickling removes oxide scaleTrue
Pickling uses acid solutions to dissolve the oxide scale formed during hot rolling, revealing a clean metallic surface essential for cold rolling.
Cold rolling is done at high temperaturesFalse
Cold rolling is performed at room temperature, below the steel's recrystallization temperature, unlike hot rolling which occurs at high temperatures.
What final treatments and quality checks ensure the standards of stainless steel coils?
The coils are now formed, but how do we guarantee they meet the exacting demands of various industries and applications? This final stage of refinement and verification can seem like a behind-the-scenes detail, yet it's crucial for assurance. Let's uncover these vital steps.
Final treatments for stainless steel coils include tension leveling for flatness, slitting to specific widths, and applying protective coatings. Rigorous quality checks involve dimensional verification, mechanical testing (tensile, hardness, bend), corrosion tests, and surface inspection to ensure compliance with standards.
These concluding steps are where the stainless steel coil is polished, perfected, and proven to meet the stringent quality benchmarks set by international standards and specific customer requirements. At MFY, our commitment to delivering high-quality products and one-stop solutions means that this final phase is executed with utmost diligence. From ensuring perfect flatness vital for automated manufacturing processes used by our clients, to slitting coils to precise widths needed by equipment integrators, every detail matters. The comprehensive quality assurance regime, encompassing a battery of tests, provides the ultimate guarantee that MFY stainless steel coils shipped to India, Southeast Asia, the Middle East, or Russia will perform reliably, upholding our reputation for agility, resilience, and continuous evolution.
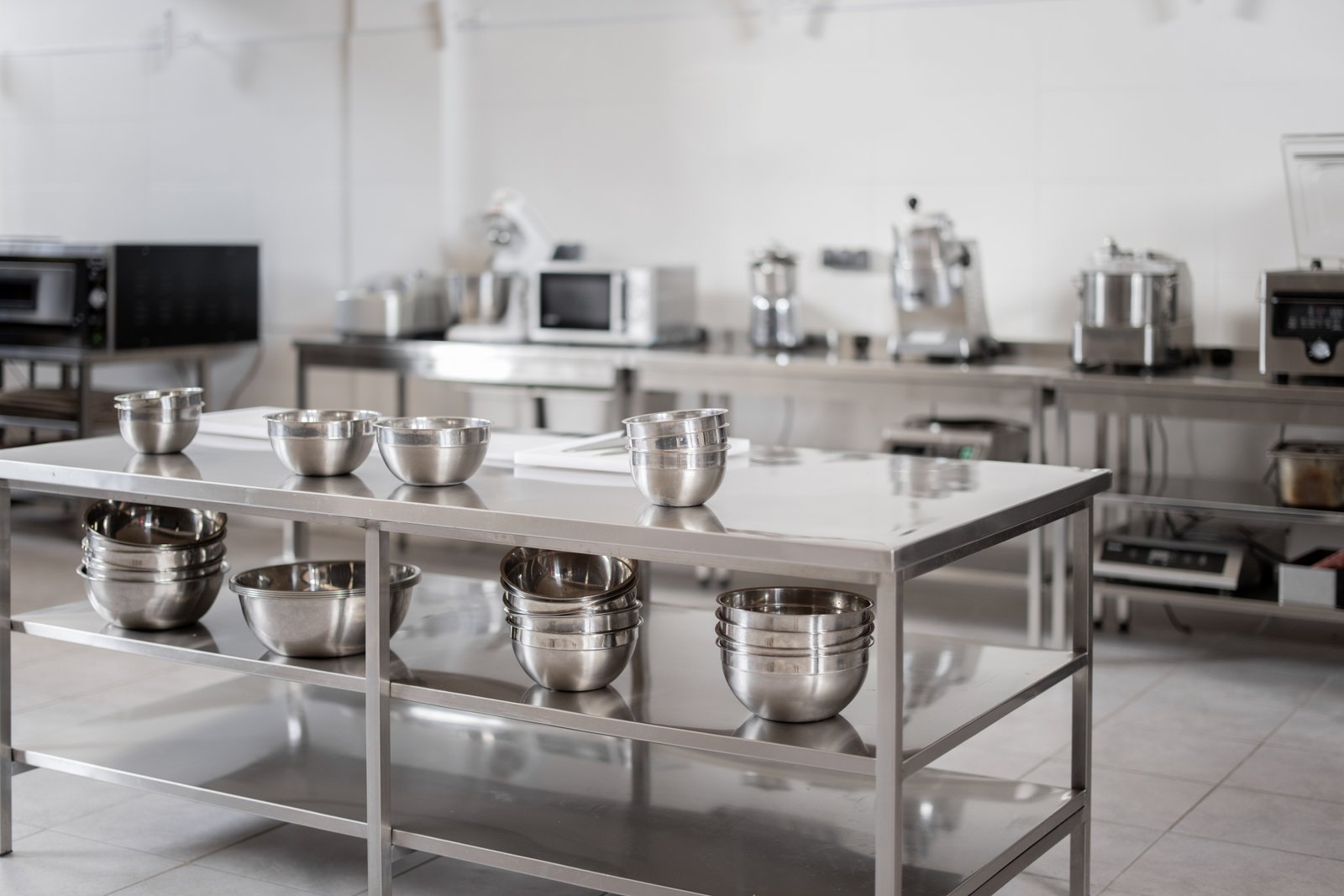
The journey of a stainless steel coil doesn't end when it comes off the cold rolling mill or the final annealing line. A series of crucial finishing treatments and exhaustive quality checks are performed to ensure that each coil not only meets the specified dimensional and mechanical properties but also possesses the surface quality and internal integrity expected by our discerning clients at MFY. These final steps are critical in transforming a well-manufactured coil into a certified, market-ready product. For example, ensuring excellent flatness through tension leveling is vital for our manufacturing clients who use automated stamping or forming processes where uneven material can cause significant production issues. Slitting a master coil into narrower widths with high precision is another key service MFY provides, catering to the specific needs of various industries. And underpinning all of this is a robust quality assurance system that validates every critical parameter, from chemical composition (verified earlier) to final surface appearance, ensuring that every MFY coil that leaves our facility embodies our commitment to excellence and supports our vision to be the leading international trade and service brand in China’s stainless steel industry.
Finishing Operations: Tension Leveling, Slitting, and Surface Protection
After the primary rolling and annealing processes, stainless steel coils often undergo several finishing operations to meet specific customer requirements or to prepare them for shipment. Tension leveling is one such important process. Even with advanced rolling techniques, coils can sometimes exhibit minor shape defects like waviness or crossbow. Tension leveling corrects these by subjecting the uncoiled strip to controlled tension while it passes over a series of small-diameter, intermeshing rolls. This process elongates the strip slightly, equalizing internal stresses and resulting in exceptionally flat material. For MFY clients involved in precision sheet metal fabrication, such as automotive component manufacturers or appliance makers, the superior flatness achieved through tension leveling is critical for trouble-free processing and high-quality finished parts.
Another common finishing operation is slitting. Master coils produced by the rolling mills are often quite wide (e.g., 1000mm, 1220mm, 1500mm). Many applications, however, require narrower strips. Slitting lines uncoil the master coil and pass the strip through a set of rotating circular knives (slitters) that cut it longitudinally into multiple narrower strips of specified widths. These narrower strips are then recoiled. Precision in slitting is key, ensuring straight edges and accurate widths with minimal burr. MFY offers custom slitting services, providing coils tailored to the exact width requirements of our diverse clientele, from engineering contractors needing specific dimensions for ductwork to distributors who stock a variety of standard and non-standard widths.
Finally, surface protection is often applied, especially for coils with delicate finishes like Bright Annealed (BA) or polished surfaces. This typically involves interleaving the coil wraps with paper or applying a temporary protective plastic film (PVC or PE coating) to one or both sides of the strip. This safeguards the pristine surface from scratches, abrasions, or contamination during handling, transit, and subsequent fabrication by the end-user. At MFY, we understand that the coil's journey doesn't end at our warehouse; it continues to our clients' facilities, often across long distances to markets like India or the Middle East. Therefore, appropriate surface protection and robust packaging are integral parts of our commitment to delivering our stainless steel coils in perfect condition.
Comprehensive Quality Control and Testing Regimen
Throughout the entire manufacturing process, and especially at the final stages, a comprehensive quality control (QC) and testing regimen is implemented to ensure every MFY stainless steel coil meets or exceeds the relevant international standards (like ASTM, EN, JIS, GOST) and customer specifications. This begins with verifying the chemical composition against the ordered grade, typically using certificates from the melt shop backed by our own checks. Dimensional checks are paramount: thickness is measured meticulously across the width and along the length of the coil using precision micrometers or automated gauging systems to ensure it's within the tight tolerances. Width, camber (edge straightness), and flatness are also rigorously verified.
Mechanical properties are assessed by taking samples from the coil and performing a battery of tests. Tensile testing determines yield strength, ultimate tensile strength, and elongation (a measure of ductility). Hardness tests (e.g., Rockwell, Brinell, or Vickers) measure the material's resistance to indentation. For certain applications, bend tests are performed to ensure the material can withstand forming operations without cracking. For specific grades or critical applications, impact testing (e.g., Charpy test) might be conducted, especially for material intended for low-temperature service. I've often reviewed test certificates with our QC managers, and the level of detail is impressive, providing a complete mechanical profile of the coil. These tests are not just formalities; they are crucial for safety and performance in the end application, whether it's a structural component in a building or a critical part in industrial machinery.
Beyond dimensional and mechanical checks, surface inspection is critical. This is often done visually by trained inspectors, looking for any defects like scratches, roll marks, pits, stains, or color variations. For coils with special finishes, instrumental surface roughness measurements might be taken. In some cases, non-destructive testing (NDT) methods like ultrasonic testing or eddy current testing might be employed to detect internal flaws or surface-breaking cracks, though this is more common for plates or tubes than for all coils. All test results are documented in a Mill Test Certificate (MTC) or Certificate of Conformity, which accompanies the MFY coil, providing full traceability and assurance of quality to our clients, like the manufacturing companies and engineering contractors who rely on our products' certified performance.
Certification, Packaging, and Logistics for Global Markets
Once a stainless steel coil has passed all quality checks and is certified to meet the required standards, it is prepared for dispatch. Proper packaging is essential to protect the coil during storage and transit, especially for export to MFY's diverse markets like India, Southeast Asia, the Middle East, and Russia. Coils are typically strapped securely with steel bands. For added protection, they may be wrapped in waterproof paper or plastic sheeting. Often, coils are placed on wooden pallets or skids, and sometimes edge protectors are used to prevent damage to the coil edges. For sea freight, coils might be packed into containers with appropriate dunnage to prevent movement and damage during the voyage. The type of packaging can often be customized based on client requirements or the specific shipping conditions.
The Mill Test Certificate (MTC), as mentioned, is a critical document. It provides a detailed summary of the coil's properties, including its chemical composition, mechanical test results (tensile strength, yield strength, elongation, hardness), dimensional measurements, material grade, heat number (for traceability to the melt), and a statement of conformity to specified standards. This document is MFY's guarantee to the customer that the supplied coil meets all agreed-upon specifications. As Global Business Director, I know how important these MTCs are for our clients, particularly for engineering and construction contractors who need to provide full documentation for their projects, or for distributors who need to assure their own customers of the product quality.
MFY's robust logistics network ensures rapid export delivery. Our team coordinates closely with shipping lines and freight forwarders to manage the complexities of international trade, ensuring timely and cost-effective delivery to our global clients. This integrated approach, from meticulous manufacturing and quality control to careful packaging and efficient logistics, is central to MFY’s mission to drive the global expansion of China’s entire stainless steel supply chain. It's how we deliver on our promise of high-quality products and one-stop solutions, helping our clients build efficient supply chains and gain a competitive edge. The final handshake, so to speak, is when the perfectly conditioned and certified MFY coil arrives at our customer's doorstep, ready for its intended application.
Quality Check / Treatment | Purpose | Method / Equipment Used | MFY's Standard / Importance |
---|---|---|---|
Tension Leveling | Improve strip flatness, remove shape defects (waves, buckles). | Tension leveler machine (intermeshing rolls under tension). | Ensures excellent flatness for downstream processing. |
Slitting | Cut master coil into narrower strips of precise customer-specified widths. | Slitting line with rotary knives. | Provides custom widths, minimizes client scrap. |
Surface Protection | Prevent scratches, contamination during handling/transit. | Paper interleaving, PVC/PE protective film application. | Maintains pristine surface, especially for BA/Polished finishes. |
Dimensional Checks | Verify thickness, width, camber, flatness against tolerances. | Micrometers, automated gauges, straight edges, feeler gauges. | Guarantees coil meets exact size specifications. |
Mechanical Testing | Determine strength, ductility, hardness. | Tensile tester, hardness tester, bend test machine. | Confirms material meets performance requirements for grade. |
Surface Inspection | Identify and classify any visual surface defects. | Visual inspection by trained personnel, sometimes instrumental. | Ensures aesthetic quality and freedom from harmful defects. |
Certification | Provide documented proof of quality and conformity. | Mill Test Certificate (MTC) detailing all test results. | Essential for traceability, client assurance, and compliance. |
Tension leveling improves flatnessTrue
Tension leveling corrects shape defects by equalizing internal stresses through controlled tension.
Slitting reduces coil lengthFalse
Slitting cuts master coils into narrower widths while maintaining the original length.
Conclusion
The creation of stainless steel coils is a sophisticated, multi-stage journey from raw materials to precision-finished products. MFY meticulously manages each step—melting, casting, rolling, and finishing—to deliver superior quality coils, empowering industries globally with reliable and innovative stainless steel solutions.
-
Understand how cold-rolled processing impacts the precision and surface of stainless steel coils. ↩
-
Learn about the environmental benefits and role of scrap in stainless steel recycling. ↩
-
Learn how hot rolling impacts dimensional accuracy and mechanical properties of stainless steel coils ↩
-
Discover the essential factors in achieving high-quality hot-rolled stainless steel ↩
-
Discover how cold rolling achieves precision and desired mechanical properties ↩
-
Understand the importance of preparing hot-rolled coils for cold reduction ↩
Have Questions or Need More Information?
Get in touch with us for personalized assistance and expert advice.