Hot-Rolled vs Cold-Rolled Stainless Coil Guide
Struggling to decide between hot-rolled and cold-rolled stainless steel coils1 for your project? The wrong choice can lead to increased costs and compromised performance. This guide will clarify the differences, helping you select the optimal material for your specific needs and applications.
Hot-rolled stainless steel is processed at high temperatures, resulting in a rougher surface and looser tolerances, while cold-rolled steel is processed further at room temperature for a smoother finish and precise dimensions, impacting their respective applications and costs.
Understanding these fundamental differences is just the beginning. As a Global Business Director at MFY, I've seen firsthand how this choice impacts project success across various industries. Let's delve deeper into what sets these two types of stainless steel coils apart and explore their unique characteristics to ensure you're well-equipped to make an informed decision.
The decision between hot-rolled and cold-rolled stainless steel isn't merely a technicality; it's a strategic choice that reverberates through your entire production process, influencing everything from manufacturing efficiency to the final product's quality and cost-effectiveness. At MFY, with our integrated supply chain spanning from raw material trading to advanced processing, we frequently guide clients through this selection. For instance, a construction project in Dubai might prioritize the corrosion resistance and aesthetic finish of cold-rolled for visible structures, whereas an industrial equipment manufacturer in India might opt for hot-rolled for internal components where surface finish is less critical than structural integrity and cost. This guide aims to provide that critical thinking framework, drawing on MFY's extensive experience across markets like India, Southeast Asia, the Middle East, and Russia, serving manufacturing companies, engineering contractors, distributors, and equipment integrators.
What are the differences between hot-rolled and cold-rolled stainless steel coils?
Confused about the fundamental distinctions between hot-rolled and cold-rolled stainless steel coils? This ambiguity can lead to selecting a material that doesn't meet your project's specific mechanical or aesthetic requirements. Let's clearly outline their core differences for you.
The primary differences lie in their processing methods, surface finish, dimensional tolerances, and mechanical properties. Hot-rolled steel is rolled above its recrystallization temperature, while cold-rolled steel is further processed at room temperature, resulting in distinct characteristics.
Beyond the basic processing temperature, these differences manifest in very practical ways that I've seen impact countless projects during my tenure at MFY. Hot-rolled stainless steel, due to its high-temperature processing, generally has a scaled surface, which might be perfectly acceptable for applications where aesthetics are secondary, or where further surface treatment is planned. Think of robust structural components for an industrial facility in Russia or internal parts for heavy machinery where the slight roughness isn't a concern. Its dimensional tolerances are also typically wider, which is fine for applications not requiring pinpoint precision. On the other hand, cold-rolling, which occurs after hot-rolling and subsequent cooling and pickling, involves passing the steel through rollers at room temperature. This additional, meticulous processing significantly refines the material. It not only improves the surface finish, making it smoother, brighter, and more suitable for consumer-facing products, but it also enhances its strength (often by up to 20% due to work hardening) and allows for much tighter dimensional tolerances. This precision is absolutely crucial for applications like automotive bodies where panel gaps are critical, for home appliances manufactured in high-volume facilities in Southeast Asia where consistency is key, or for precision instruments where every micron matters. At MFY, we often work with clients who manufacture high-end consumer goods; for them, the superior finish and unwavering consistency of our cold-rolled coils are non-negotiable. Conversely, some of our partners in heavy industry might prefer hot-rolled for its cost-effectiveness in demanding structural applications. Understanding these nuances is pivotal for optimizing both the performance characteristics of your final product and your overall budget. We'll explore these aspects in more detail, looking at specific properties and how they impact real-world use scenarios, drawing from our experiences across MFY's diverse client base.
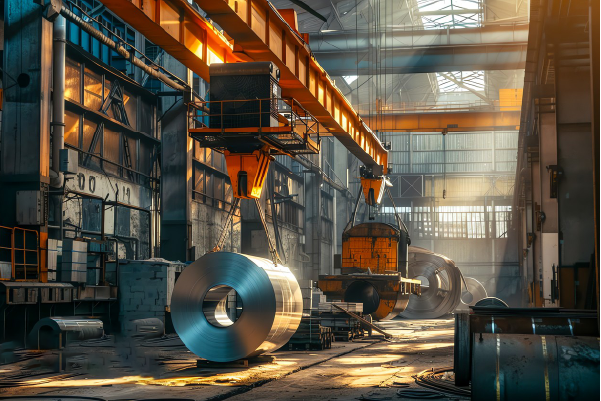
The journey from raw steel to a finished coil involves intricate processes, and the divergence between hot and cold rolling marks a critical juncture that defines the steel's ultimate characteristics and suitability for various applications. As a company, MFY, deeply integrated in the stainless steel supply chain from raw material trading to sophisticated processing like cold-rolling, we have a granular understanding of these processes and their implications for our clients, be they manufacturing companies or engineering contractors.
Understanding the Manufacturing Processes: From Heat to Precision
Hot rolling2 is a steel shaping process that occurs at temperatures exceeding 1700°F (926°C), which is above the recrystallization temperature for most stainless steels. At this elevated temperature, the steel becomes highly malleable, allowing it to be easily formed and shaped into coils. Large slabs or billets of steel are heated in a furnace and then passed between a series of powerful rollers that progressively reduce their thickness and elongate them to achieve the desired coil form. This high-temperature process imparts certain characteristics to the steel: a rougher, scaled surface (known as mill scale) due to oxidation occurring at these temperatures, and slightly rounded, less precise edges and corners. The cooling process after hot rolling is typically done at ambient temperature and is less controlled, which can lead to some internal stresses and variations in the final microstructure and mechanical properties. For MFY, when we source hot-rolled bands, either for direct sale or as feedstock for our cold-rolling mills, we meticulously assess the originating mill's capabilities, as the consistency of the hot-rolled product is fundamental to subsequent quality.
Cold rolling, in stark contrast, is a finishing process that takes place after the hot-rolled steel has cooled down and has typically undergone a pickling process to remove the mill scale. The pickled hot-rolled coil is then passed through a series of rollers at room temperature. This process involves significant compressive forces and work-hardens the material, which means it increases its tensile strength and hardness. Because it's performed at lower temperatures, no new scale formation occurs, resulting in a significantly smoother, cleaner, and often brighter surface finish. The dimensional accuracy of cold-rolled steel is markedly higher, with much tighter tolerances achievable on thickness, width, parallelism, and overall shape. This precision is indispensable for applications where a high-quality surface is non-negotiable or where exact dimensions are critical for automated assembly or fitment. For example, an automotive client in India manufacturing exterior panels would demand the tight tolerances and superior finish of cold-rolled coils that MFY provides.
The strategic choice between these processes is fundamentally driven by the end-use application and the desired balance of properties, cost, and aesthetics. A client constructing large industrial storage tanks in the Middle East might specify hot-rolled stainless steel for its cost-effectiveness and sufficient structural strength, understanding that the internal surface finish is less critical than overall integrity and material cost. However, if that same client were producing high-end architectural panels for a skyscraper facade, cold-rolled stainless steel with a specific polished or brushed finish would be the unequivocal choice due to its superior aesthetic qualities and dimensional consistency. At MFY, our integrated production capabilities, including our own cold-rolling facilities, allow us to manage both the sourcing of high-quality hot-rolled feedstock and the precision manufacturing of cold-rolled products, offering our global clients highly tailored solutions.
Comparative Analysis of Mechanical Properties and Tolerances
Hot-rolled stainless steel generally exhibits lower strength and hardness compared to cold-rolled steel of the same grade and initial chemical composition. The high-temperature processing allows for the formation of larger grain sizes within the steel's microstructure, which can contribute to greater ductility and formability but may reduce overall strength and hardness. The less controlled cooling process can also introduce some variability in mechanical properties across the coil. However, hot-rolled steel often demonstrates better overall formability for severe deformations and enhanced weldability due to its lower internal stresses compared to heavily cold-worked material, especially if the cold-rolled material hasn't been subsequently annealed. For applications like heavy structural sections, railway track components, or large-diameter pipes where high formability and cost-effectiveness are key drivers, hot-rolled stainless steel is often the preferred material. We've supplied hot-rolled coils for major infrastructure projects where these robust properties were paramount.
Cold-rolled stainless steel, as a result of the work-hardening effect during the cold reduction process, typically possesses significantly higher tensile strength, yield strength, and hardness. This makes it more resistant to denting and deformation, a desirable trait in many applications, from automotive panels to appliance casings. However, this increased strength often comes at the expense of reduced ductility, meaning it might be less suitable for very complex forming operations unless it undergoes an annealing process after cold rolling to restore some ductility. The most significant advantage of cold-rolled steel, beyond its surface finish, lies in its superior dimensional control. Thickness tolerances can be exceptionally tight, sometimes as precise as ±0.01mm for specialized products, which is crucial for precision manufacturing processes. For example, a manufacturer of high-precision electronic components or automotive fuel system parts in Southeast Asia relies on MFY's cold-rolled coils for their consistent thickness, ensuring flawless performance in their automated, high-speed assembly lines and final product quality.
Here's a simplified comparison table highlighting typical differences:
Feature | Hot-Rolled Stainless Steel | Cold-Rolled Stainless Steel |
---|---|---|
Manufacturing Temp. | Above recrystallization temp. (e.g., >926°C) | Room temperature |
Surface Finish | Rougher, may have mill scale (bluish-grey oxide) | Smoother, brighter, more uniform (e.g., 2B, BA) |
Dimensional Tolerance | Wider, less precise (e.g., thickness ±0.2mm) | Tighter, more precise (e.g., thickness ±0.05mm or less) |
Thickness Control | Less uniform across width/length | Highly uniform |
Strength (Tensile) | Generally lower | Generally higher (due to work hardening) |
Hardness | Generally lower | Generally higher |
Ductility | Generally higher | Generally lower (can be improved by annealing) |
Internal Stresses | Lower | Higher (can be relieved by annealing) |
Edge Condition | Often mill edge (rounded, less precise) | Can be mill edge or slit edge (sharper, precise) |
Cost | Typically lower | Typically higher |
It's important to note that these are general characteristics, and specific properties can vary significantly based on the stainless steel grade, the exact processing parameters, and any subsequent treatments like annealing or tempering.
Impact on Surface Finish and Aesthetics
The surface finish of hot-rolled stainless steel is fundamentally characterized by the presence of a layer of iron oxide scale, often referred to as "mill scale." This scale, typically bluish-grey in color, forms during the high-temperature rolling and subsequent cooling processes. While this mill scale can offer a degree of initial, albeit limited, corrosion resistance, it is generally considered undesirable for applications requiring a clean, smooth, or decorative appearance. It's often removed through processes like pickling (an acid cleaning treatment) or abrasive blasting if a better surface is needed, or more commonly, if the steel is destined for further processing, such as cold rolling. For many purely industrial or hidden structural applications—think internal supports in machinery or foundational elements in construction—the as-rolled surface might be perfectly acceptable and cost-effective. I recall a project where MFY supplied hot-rolled coils for manufacturing heavy-duty agricultural equipment components; the client painted the final product, so the initial mill scale wasn't a primary concern, and the robustness of the hot-rolled material was ideal.
Cold-rolled stainless steel, in contrast, boasts a significantly superior and more versatile range of surface finishes. Because it's processed at room temperature, and the hot-rolled feedstock is typically pickled before cold rolling, the final surface is inherently smooth, bright, and free of detrimental scale. Various distinct surface finishes can be achieved during or after the cold rolling process, often designated by industry standards. Common finishes include the "2B" finish, which is a smooth, moderately reflective cold-rolled annealed and pickled finish – perhaps the most widely used stainless steel finish globally. Then there's the "BA" or Bright Annealed finish, which is highly reflective, almost mirror-like, achieved by annealing in a controlled atmosphere furnace after cold rolling. Beyond these mill finishes, cold-rolled stainless steel can be further processed to achieve various polished finishes (e.g., #3, #4, #7, #8 mirror), brushed finishes, or even patterned/embossed textures. This vast palette of aesthetic options makes cold-rolled stainless steel the preferred choice for applications where appearance is a critical factor. Think of sleek kitchen appliances, gleaming automotive trim, sophisticated architectural details, and hygienic medical equipment. A key client of ours in the high-end appliance market in Europe specifically requests MFY's BA finish cold-rolled coils for their products, valuing the pristine look and consistency that enhances their brand image.
The aesthetic difference between hot-rolled and cold-rolled stainless steel is therefore stark and directly influences their respective end-use suitability. While hot-rolled steel prioritizes raw function and cost-effectiveness for less visible or purely structural roles, cold-rolled steel adds indispensable layers of precision, visual appeal, and tactile quality, making it essential for consumer-facing products, architectural statements, and applications where a high-quality, often hygienic, finish is paramount. This fundamental distinction is something we at MFY constantly emphasize when guiding our diverse clientele – from construction contractors needing robust, economical solutions to equipment integrators designing cutting-edge, aesthetically refined products – in their crucial material selection process.
Material grade determines available sizesTrue
Different stainless steel grades have varying ranges of available thicknesses and widths, as shown in the chart.
Tolerances are the same for all gradesFalse
Tolerances can vary by grade and manufacturer, with some offering tighter tolerances than standard specifications.
How is hot-rolled stainless steel currently used in various industries?
Are you wondering where hot-rolled stainless steel truly shines despite its rougher finish? Misunderstanding its applications can lead to overspending on unnecessarily refined materials. Let's explore the diverse industries that effectively utilize hot-rolled coils.
Hot-rolled stainless steel is widely used in construction for structural components, automotive for frames, agriculture for machinery, and for manufacturing pipes, tanks, and industrial equipment where high strength and cost-effectiveness are prioritized over a perfect surface finish.
The versatility of hot-rolled stainless steel often surprises those unfamiliar with its broad range of applications, especially when the conversation is frequently dominated by the aesthetic appeal of its cold-rolled counterpart. Its inherent strength, coupled with its notable economic advantages in applications not demanding a pristine surface, makes it a go-to material for a multitude of heavy-duty tasks where robustness and functionality take precedence. In my experience as Global Business Director at MFY, navigating supply chains across India, Southeast Asia, the Middle East, and Russia, we've seen a consistent and strong demand for hot-rolled coils from sectors that value toughness, weldability, and cost-efficiency. For example, in the booming construction industry across many of these regions, it forms the literal backbone of many buildings and infrastructure projects as structural beams, channels, and plates3. The automotive sector, particularly for commercial vehicles and internal structural parts, relies on it for chassis components and wheel rims, where durability under stress is paramount. Furthermore, it's extensively used in the manufacturing of large-diameter welded pipes for water or industrial fluid transport, robust industrial containers, and critical components for railway cars. Its generally good weldability and formability allow for complex fabrications without the need for the more specialized handling that some highly work-hardened cold-rolled products might require. Even in shipbuilding, where corrosion resistance is crucial, specific grades of hot-rolled stainless steel play a vital role in structural elements. The key takeaway, which we always emphasize to our clients at MFY, whether they are large manufacturing companies or specialized engineering contractors, is understanding that "fitness for purpose" often means prioritizing mechanical properties and overall project cost over achieving a mirror-like shine. This is precisely where hot-rolled stainless steel truly proves its enduring worth across a global landscape of critical industrial applications. We'll delve into specific examples and illustrative case studies to further illuminate its practical utility and widespread adoption.
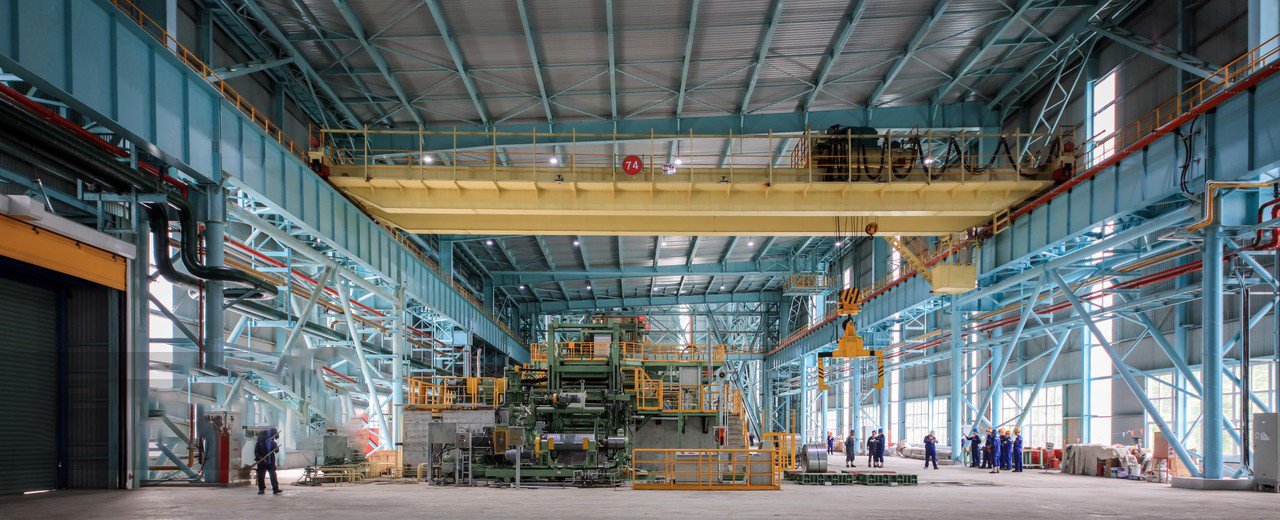
The application landscape for hot-rolled stainless steel is vast and varied, underpinning many of the foundational elements of modern industry and infrastructure. Its selection is typically driven by a pragmatic assessment of required mechanical performance against cost, where its characteristic surface finish is either acceptable or will be subsequently altered. At MFY, we supply hot-rolled stainless steel coils to a wide spectrum of industries, each leveraging its unique benefits.
Applications in Construction and Infrastructure: Building Strong Foundations
In the demanding construction and infrastructure sector, hot-rolled stainless steel is a workhorse material, highly valued for its structural integrity, inherent durability, and relatively lower initial cost compared to its cold-rolled counterpart, especially when a high-end surface finish isn't a primary requirement. It's commonly manufactured into I-beams, H-beams, C-channels, angles, and heavy plates that form the skeletons of industrial buildings, bridges, pedestrian overpasses, and other large-scale structures. The material's excellent strength-to-weight ratio, particularly in duplex or lean duplex stainless grades, provides outstanding load-bearing capabilities. For instance, in coastal or heavily industrialized environments like those found in parts of India or the Middle East, where atmospheric corrosion poses a significant threat to carbon steel, hot-rolled stainless steel sections offer a considerably longer lifespan, thereby reducing long-term maintenance costs. MFY has supplied hot-rolled stainless steel coils and plates to contractors in these regions for fabricating support structures for large petrochemical plants and desalination facilities, where the material's resistance to harsh atmospheric conditions and process-related corrosives was a key deciding factor. According to a report by the World Steel Association, construction accounts for over 50% of world steel demand, and while much of this is carbon steel, the use of stainless steel, including hot-rolled forms, is growing in more demanding or iconic projects.
Another significant and growing application within infrastructure is in the production of stainless steel reinforcement bars (rebar) for concrete structures, particularly in environments highly susceptible to chloride-induced corrosion. This includes marine structures, bridges in areas where de-icing salts are frequently used (a concern in parts of Russia, for example), and tunnels. Stainless steel rebar, often produced from hot-rolled round bars or slit hot-rolled coils, dramatically extends the service life of concrete structures by preventing rust, which leads to concrete cracking and spalling. While the initial material cost for stainless rebar is higher than for traditional carbon steel rebar, comprehensive life-cycle cost analyses consistently demonstrate substantial long-term economic advantages. Studies by organizations like the Nickel Institute and Euro Inox highlight projected lifespans for stainless-reinforced structures exceeding 100 years with minimal maintenance, a compelling argument for infrastructure planners.
Furthermore, hot-rolled stainless steel plates, often in checkered or embossed patterns for slip resistance, are extensively used for constructing industrial walkways, service platforms, trench covers, and heavy-duty industrial flooring. Its capacity to withstand significant loads, impacts, and harsh operating conditions makes it an ideal choice for demanding industrial settings such as factories, processing plants, and offshore platforms. At MFY, we frequently engage with engineering and construction contractors who specify hot-rolled stainless steel for these foundational, utilitarian, and safety-critical purposes. They recognize its optimal balance of robust performance and cost-effectiveness for non-aesthetic structural elements that must endure challenging environments. For instance, a recent project involved supplying patterned hot-rolled plates for a large manufacturing facility in Southeast Asia, ensuring worker safety and long-term durability of their elevated platforms.
Role in Automotive and Transportation: Driving Durability
The automotive and transportation industries represent another major consumer of hot-rolled stainless steel, relying on it for a variety of components where strength, toughness, formability, and cost are crucial, and where the surface finish is often secondary or will be concealed or coated. Key applications include chassis components, suspension arms, cross members, and various structural reinforcements within vehicle bodies. Its ability to be formed into complex shapes while maintaining high strength is essential for creating safe, durable, and increasingly lightweight vehicle architectures. For example, many high-strength low-alloy (HSLA) steels, which offer improved mechanical properties and weight reduction potential, are produced via the hot-rolling process. These are vital in meeting stringent crash safety standards while contributing to fuel efficiency.
In the commercial vehicle sector, encompassing trucks, trailers, buses, and specialized utility vehicles, hot-rolled stainless steel finds extensive use. It's employed for robust frames, support brackets, fifth-wheel plates, and even in certain parts of exhaust systems where specific grades offer good resistance to high temperatures and corrosive exhaust gases. I recall a significant engagement with a client in India who manufactures heavy-duty truck chassis; they specifically chose MFY's hot-rolled coils (in a specific micro-alloyed grade) for their excellent weldability, consistent mechanical properties, and toughness, which were critical for the demanding road conditions and heavy payloads their vehicles are designed to withstand. The overall cost-effectiveness of hot-rolled steel also plays a significant role in managing production costs in this highly competitive global industry. Data from automotive industry associations often show that while cold-rolled steel dominates in visible body panels, hot-rolled products form a substantial part of the vehicle's underlying structure and powertrain components.
Beyond road vehicles, hot-rolled steel is indispensable in the railway industry. It's used for manufacturing structural components of rolling stock, such as underframes, bolsters, and side walls of freight cars and some passenger carriages. Its robustness and fatigue resistance ensure longevity and operational reliability under the heavy loads and dynamic stresses characteristic of rail transport. The American Iron and Steel Institute (AISI) and similar global bodies frequently publish data on steel usage in transportation, consistently highlighting hot-rolled products as a foundational material. The ability to produce hot-rolled steel in a wide array of thicknesses and strength levels allows engineers to meticulously optimize designs for both performance and manufacturing economy, a balance MFY strives to help its clients achieve.
Industrial Equipment and Machinery Manufacturing: Powering Production
Hot-rolled stainless steel is extensively utilized in the manufacturing of a wide array of industrial equipment and machinery, primarily due to its favorable combination of strength, good weldability, formability, and overall cost-effectiveness. It serves as a common material for fabricating storage tanks, hoppers, silos, and certain types of pressure vessels (though specific grades, stringent certifications, and often thicker plates are required for pressure applications, adhering to codes like ASME). These are used across various process industries, including chemical processing, petrochemicals, mining, pulp and paper, and even in some segments of the food and beverage industry (typically for non-food-contact surfaces or where hygiene standards are met through design and cleaning protocols rather than an inherently smooth surface). The thicker gauges readily available in hot-rolled coils and plates are particularly well-suited for these heavy-duty applications. A key client of MFY's, an equipment integrator based in the Middle East specializing in systems for the oil and gas sector, frequently orders specific grades of hot-rolled stainless steel plates and coils from us for building large-scale storage tanks and process skids. For them, the material's reliable performance in corrosive environments (dictated by the grade) and its structural integrity are paramount, and the hot-rolled finish is perfectly adequate for these robust, functional applications.
Agricultural machinery and equipment, such as plows, harrows, seeders, parts of harvesters, and tractor implements, often incorporate numerous components made from hot-rolled steel. These machines operate in extremely demanding and often abrasive environments, requiring materials that can withstand significant impact, wear, and fluctuating loads. The inherent durability, toughness, and good impact resistance of many hot-rolled steel grades make them a practical and economical choice. According to reports from industry bodies like the Association of Equipment Manufacturers (AEM), steel, predominantly in its hot-rolled form, constitutes the bulk of the material mass used in constructing agricultural equipment, prized for its ability to deliver reliable performance season after season.
Furthermore, hot-rolled steel is a staple in the fabrication of general machinery components. This includes machine base plates, heavy frames, structural supports, machine guards, and conveyor system components. The relative ease of fabrication, including straightforward cutting, bending, and welding, allows manufacturers to efficiently produce these often complex parts. While cold-rolled steel might be chosen for aesthetically critical enclosures or visible control panels that require a finer finish, the underlying robust structure of the machinery often benefits from the cost and strength advantages offered by hot-rolled steel. Our ability at MFY to provide a comprehensive range of stainless steel products, encompassing both hot and cold-rolled coils, sheets, and plates, in various grades and specifications, allows us to effectively serve the diverse and evolving needs of machinery manufacturers across all our export markets.
Hot-rolled steel dominates agricultural machineryTrue
Industry reports confirm hot-rolled steel constitutes the majority of material mass in agricultural equipment due to its durability and cost-effectiveness.
Cold-rolled steel is better for all vehicle partsFalse
Hot-rolled steel is actually preferred for structural vehicle components like chassis and frames where strength and cost matter more than surface finish.
What are the current applications for cold-rolled stainless steel coils?
Seeking a superior finish and tight tolerances for your products? Using a material that doesn't meet these aesthetic and precision demands can compromise your brand's quality perception. Discover the wide-ranging applications where cold-rolled stainless steel excels.
Cold-rolled stainless steel coils are favored for applications demanding a high-quality surface finish and precise dimensions, such as automotive bodies, home appliances (refrigerators, washing machines), cookware, medical equipment, architectural trim, and precision electronics components.
The refined characteristics of cold-rolled stainless steel—its smooth surface, bright appearance, and precise dimensional control—make it the material of choice for countless applications where aesthetics, precision, and enhanced mechanical properties are paramount. As I've observed in my role at MFY, facilitating stainless steel solutions for clients from India to the Middle East, the demand for high-quality cold-rolled products is consistently strong from industries that interface directly with consumers or require components manufactured to exacting specifications. Its inherently smooth, often lustrous surface lends itself perfectly to products where visual appeal is a key selling point, directly influencing consumer choice and brand perception.
Think of the sleek, modern finish on contemporary kitchen appliances, the gleaming decorative trim on luxury automobiles, or the impeccably hygienic and easily sterilizable surfaces required in medical devices and food processing equipment. Beyond its visual appeal, the significantly tighter dimensional tolerances achieved through the cold-rolling process are absolutely critical for today's sophisticated automated manufacturing processes and for parts that need to fit together with seamless precision. This level of accuracy ensures consistency, quality, and interchangeability in mass-produced items, reducing assembly time and scrap rates. Industries such as electronics and aerospace also benefit immensely from these properties for producing intricate casings, sensitive internal components, and parts that must perform reliably under demanding conditions. We will now explore specific sectors and products in greater detail to highlight how cold-rolled stainless steel is shaping the world around us, delivering an unparalleled combination of beauty, functionality, and precision.
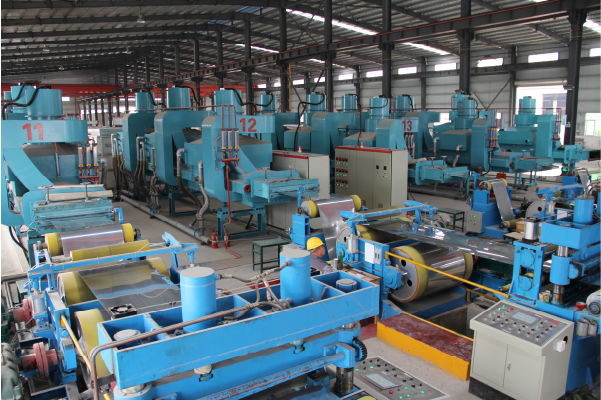
Cold-rolled stainless steel, with its superior surface characteristics and dimensional accuracy, caters to a segment of the market where performance extends beyond mere strength to include aesthetics, precision, and specialized properties. At MFY, our cold-rolling facilities are geared towards producing coils that meet these exacting demands for a diverse range of global clients.
Consumer Goods and Appliances: Marrying Aesthetics with Functionality
Cold-rolled stainless steel is virtually ubiquitous in the modern consumer goods and appliance industry, prized for its winning combination of sophisticated aesthetic appeal, excellent hygienic properties, corrosion resistance, and long-term durability. Iconic products such as refrigerators, washing machines, dishwashers, ovens, cooktops, and microwaves extensively feature cold-rolled stainless steel for their exteriors, control panels, and sometimes critical internal components. The smooth, easily cleanable surface (often a standard 2B finish or a more reflective BA – Bright Annealed – finish4) is not only visually attractive, contributing to a premium feel, but also inherently resists corrosion, staining from food spills, and the growth of bacteria, thereby contributing to the product's longevity and ease of maintenance. Major global appliance brands, whose products are sought after in markets like Southeast Asia and the Middle East, heavily market the "stainless steel look" of their premium appliance lines, a trend MFY directly supports by supplying high-quality coils to their OEMs or component manufacturers. According to industry statistics from bodies like APPLiA (Home Appliance Europe), stainless steel remains a preferred material for high-value appliances due to these combined benefits.
In the cookware, cutlery, and kitchen sink sector, cold-rolled stainless steel is the undisputed standard. Austenitic grades like 304 (1.4301) and sometimes 316 (1.4401, for enhanced corrosion resistance) are commonly used for manufacturing pots, pans, kitchen utensils, and sinks. This is due to their excellent formability (allowing for deep drawing of sinks and complex cookware shapes), outstanding resistance to corrosion from various foodstuffs and cleaning agents, and their ability to maintain a polished, attractive finish over years of use. The material's non-reactivity with food ensures safety and hygiene, a critical factor for consumers worldwide. I've personally worked with several large distributors in India who supply MFY's food-grade cold-rolled coils and sheets to local cookware manufacturers, and for them, the consistency of our material's surface quality and mechanical properties are always top priorities to ensure defect-free production runs.
Beyond large appliances and cookware, a multitude of smaller household appliances, high-end electronics casings (such as those for premium laptops, audio equipment, or smartphones), and various decorative items also leverage the premium feel, precise formability, and durability of cold-rolled stainless steel. The ability to achieve intricate designs, sharp bends, and maintain extremely tight tolerances is crucial for these applications where miniaturization and aesthetic precision are key. Data from organizations like the World Steel Association often point to the appliance and consumer electronics sectors as major and growing consumers of cold-rolled flat stainless steel products, underscoring its pivotal importance in products that define modern lifestyles.
Automotive Exteriors and Precision Components: Driving Precision and Style
While hot-rolled steel often forms the hidden structural backbone of vehicles, cold-rolled stainless steel plays a significant and often visible role in automotive exteriors, interiors, and critical precision components where finish, corrosion resistance, and dimensional accuracy are absolutely critical. This includes applications such as decorative trim (window surrounds, grilles, body side moldings), exhaust system components (mufflers, tailpipes, catalytic converter shells – especially those requiring a polished look or enhanced heat/corrosion resistance), and sometimes even specialized body panels on luxury, sports, or niche vehicles where a unique aesthetic or superior longevity is desired. The superior surface quality of cold-rolled steel ensures a flawless paint application if coated, or a brilliant, durable polished or brushed finish if left exposed. This contributes significantly to the vehicle's perceived quality and value.
Inside the vehicle and under the hood, cold-rolled stainless steel is utilized for a variety of precision-engineered parts. These include components for fuel injection systems, various sensor housings, small intricate brackets, seatbelt components, and airbag inflator parts. The tight dimensional tolerances and consistent mechanical properties of cold-rolled steel ensure a perfect fit, reliable performance, and interchangeability in complex automated assemblies. For instance, the European Automobile Manufacturers' Association (ACEA) and similar bodies like SAE International frequently publish research and standards related to material trends, often highlighting the increasing use of advanced steels, including specialized cold-rolled stainless grades (like ferritic stainless for exhaust systems or specific austenitic grades for fuel system components), to meet stringent performance, emissions, and safety standards.
MFY has a track record of supplying specialized cold-rolled stainless steel coils to Tier 1 and Tier 2 automotive suppliers across our export markets, including those manufacturing exhaust systems and decorative trim parts. Their specifications are invariably demanding, focusing keenly on parameters like controlled surface roughness (e.g., specific Ra values to ensure good paint adhesion or consistent polishing results), extremely tight thickness tolerances (often within a few hundredths of a millimeter), and highly consistent mechanical properties (yield strength, tensile strength, elongation) to ensure predictable forming behavior in their high-speed stamping, roll-forming, or hydroforming processes. The innovation-driven development ethos at MFY helps us meet these exacting automotive standards.
Medical, Architectural, and High-Tech Applications: Precision for Critical Needs
The medical industry relies profoundly on cold-rolled stainless steel, particularly austenitic grades such as 304L (1.4307) and 316L (1.4404 – low carbon variants for enhanced weldability and corrosion resistance after welding), for a vast range of applications. These include surgical and dental instruments, medical implants (like bone screws and plates, where biocompatibility is paramount), hospital equipment (such as operating tables, instrument carts, and sterilizable trays), and components for diagnostic machinery. The material's exceptional corrosion resistance (especially 316L against bodily fluids and aggressive cleaning agents), profound ease of cleaning and sterilization, inherent biocompatibility (for specific grades and surface treatments), and its smooth, crevice-free surface finish are all indispensable attributes in this highly regulated field. Regulatory bodies like the FDA in the USA and equivalent authorities globally have stringent material requirements for medical devices, and stainless steel frequently meets or exceeds these critical standards. We've seen a steadily increasing demand from medical equipment integrators and manufacturers in markets like India and Southeast Asia for MFY's high-quality, certified cold-rolled sheets and coils.
In the realm of architecture and construction, cold-rolled stainless steel is extensively used for both its striking aesthetic qualities and its outstanding functional performance. Applications include prestigious building facade cladding, durable roofing systems, intricate decorative interior and exterior panels, high-traffic elevator interiors and doors, elegant handrails and balustrades, and a wide variety of high-end fixtures and fittings. Its excellent corrosion resistance ensures impressive longevity and low maintenance requirements, especially in aggressive urban, industrial, or coastal environments. The diverse range of available finishes—from matte to bright annealed, brushed, polished (including mirror #8), patterned, or even color-coated—offers architects unparalleled design flexibility to create iconic and lasting structures. Many landmark buildings worldwide prominently feature stainless steel for its contemporary look, structural efficiency, and sustainable credentials (high recycled content and recyclability). A notable project MFY supplied to in the Middle East involved providing highly polished, blemish-free cold-rolled stainless steel sheets for the expansive lobby and facade elements of a luxury hotel, where the visual impact and long-term pristine appearance were paramount design objectives.
High-technology industries, including electronics, telecommunications, and aerospace, also strategically utilize cold-rolled stainless steel for numerous precision components. This can range from minute parts within hard disk drives, specialized springs and connectors, casings for sensitive electronic equipment, components for semiconductor manufacturing equipment (requiring ultra-clean, non-contaminating surfaces), to intricate parts in aerospace applications where an optimal combination of strength-to-weight ratio, corrosion resistance, and performance at varying temperatures is critical. The material's inherent ability to be fabricated into highly complex shapes while maintaining extremely tight tolerances makes it uniquely suitable for these demanding and often mission-critical fields. The continuous evolution value at MFY drives us to explore solutions for these advanced sectors.
Cold-rolled steel excels in appliancesTrue
Cold-rolled stainless steel is preferred for appliances due to its smooth finish, corrosion resistance, and hygienic properties that meet consumer expectations.
Hot-rolled steel dominates car exteriorsFalse
While hot-rolled steel is used structurally, cold-rolled stainless steel is crucial for automotive exteriors and precision components where finish and dimensional accuracy are critical.
What challenges do industries face when choosing between hot and cold-rolled coils?
Facing a dilemma choosing between hot and cold-rolled coils? Making the wrong choice can lead to budget overruns or products that fail to meet performance or aesthetic standards. Let's identify the common challenges industries encounter.
Industries face challenges balancing cost versus performance, understanding the impact of surface finish and dimensional tolerances on their specific application, managing material workability and potential fabrication issues, and assessing the long-term durability and maintenance implications of each type of coil.
Selecting the appropriate type of stainless steel coil5—hot-rolled or cold-rolled—is a critical decision that extends far beyond a simple comparison of initial price tags. As I've seen in my global interactions at MFY, supporting clients from manufacturing companies in India to engineering contractors in the Middle East, businesses across diverse sectors grapple with a complex interplay of technical and economic factors. The most immediate and often most prominent challenge is the cost-benefit analysis: hot-rolled stainless steel is generally less expensive upfront, but will its inherent properties suffice for the intended application's demands, or will the superior finish, tighter tolerances, and enhanced mechanical properties of cold-rolled stainless steel ultimately justify its higher initial price? This decision becomes particularly nuanced and critical when considering the entire lifecycle of the product. This includes the intricacies of manufacturing processes, the potential costs associated with rework or higher scrap rates, and ultimately, end-user satisfaction and product longevity.
Another significant hurdle is accurately assessing and specifying the required dimensional tolerances and surface finish. A misjudgment in this area can cascade into significant downstream problems, such as assembly issues in automated lines, aesthetic failures leading to product rejection, or even functional impairments compromising performance and safety. Furthermore, the differing mechanical properties6 between hot and cold-rolled steel, such as hardness, strength, and ductility, directly influence formability, weldability, and machinability, thereby impacting production efficiency, tooling wear, and overall manufacturing costs. For instance, the increased hardness characteristic of cold-rolled steel might necessitate more robust forming equipment or specialized tooling, an investment that needs to be factored in. We will now explore these common challenges in greater depth, providing insights and practical considerations to help navigate them effectively and make a truly informed material selection.
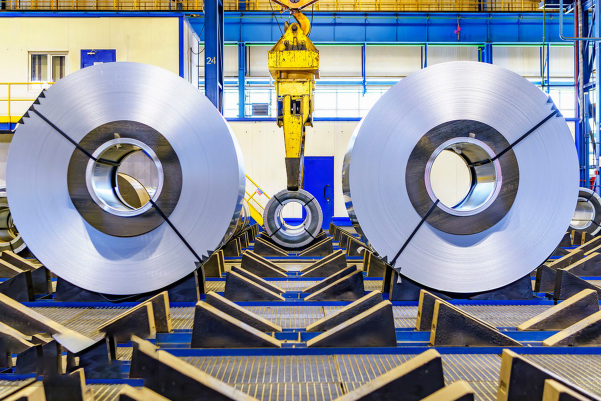
The decision-making process between hot-rolled and cold-rolled stainless steel is fraught with potential pitfalls if not approached systematically. At MFY, our role often involves helping clients understand these challenges to ensure they select materials that align perfectly with their technical needs and commercial objectives. Our fully integrated supply chain gives us a unique perspective on these issues, from raw material nuances to final application performance.
Balancing Cost Implications with Holistic Performance Requirements
One of the most significant and persistent challenges industries face is navigating the direct cost difference versus the comprehensive performance benefits. Hot-rolled stainless steel is generally less expensive to produce than cold-rolled steel due to fewer processing steps (no secondary rolling at room temperature, often less stringent annealing and pickling). For projects with very tight budgets or for applications where surface finish and extremely tight dimensional tolerances are not critical—think internal structural components or back-of-house industrial equipment—hot-rolled appears to be the more economical choice. However, this initial cost saving can be profoundly misleading if the material ultimately fails to meet the holistic performance requirements of the application. For example, if a slightly rougher surface finish on a hot-rolled component leads to premature wear in a dynamic application, or if its wider dimensional tolerances cause significant assembly problems downstream in a highly automated production line, the perceived initial "savings" are quickly eroded by increased costs associated with rework, higher rejection rates, production delays, or even costly warranty claims and reputational damage. I've consulted with numerous manufacturing companies, for instance in Southeast Asia's competitive electronics component sector, who initially opted for lower-cost hot-rolled material for certain brackets, only to find they needed to invest in additional surface finishing processes or encountered unacceptably high scrap rates during assembly, ultimately increasing their total expenditure beyond what selecting an appropriate cold-rolled product would have initially cost.
Conversely, specifying cold-rolled steel, with its attendant higher price, when its superior properties are not strictly necessary for the application, can lead to over-engineering and an unnecessary inflation of product costs. While the smoother finish, enhanced strength, and precise dimensions of cold-rolled steel are undoubtedly advantageous in many scenarios, these benefits come at a premium that isn't always justified. A common challenge for distributors and traders we work with at MFY, particularly those serving diverse small and medium-sized enterprises, is educating their end-customers on precisely when this premium for cold-rolled steel is a value-added investment versus an avoidable expense. For instance, for an internal structural bracket within a piece of industrial machinery that will be painted and completely hidden from view, and where existing tolerances are wide, the aesthetic benefits and ultra-tight tolerances of cold-rolled are largely redundant. According to cost analyses often cited in metal fabrication journals, material costs can represent 40-60% of a finished metal product's cost, so optimizing this choice is critical.
A truly effective cost-benefit analysis must therefore consider the Total Cost of Ownership (TCO) or Life Cycle Costing (LCC). This holistic approach includes not just the raw material purchase price but also all associated processing costs (e.g., impact on tooling wear, forming difficulty, welding consumables and time), finishing costs (if any are required, like descaling hot-rolled or polishing cold-rolled), scrap rates during production, assembly efficiency, and crucially, the expected service life, reliability, and maintenance requirements of the final product. A study by the Specialty Steel Industry of North America (SSINA) often emphasizes the importance of looking at life-cycle costing, particularly for stainless steel applications where its inherent durability and corrosion resistance can significantly offset higher initial material costs over the product's lifespan, leading to lower TCO. This is a principle MFY champions.
Understanding and Accurately Specifying Appropriate Tolerances and Finishes
A frequent and often costly challenge arises from a lack of precise understanding, or inadequate communication, regarding the truly necessary dimensional tolerances and surface finishes for a given application. Engineers and designers, sometimes working with outdated information or a "better safe than sorry" mentality, may over-specify, requesting much tighter tolerances or finer surface finishes than the application genuinely needs. This invariably increases material costs and can sometimes limit supplier options. On the other hand, under-specifying these critical parameters can lead to disastrous outcomes: parts that simply don't fit together during assembly, surfaces that are aesthetically unacceptable to the end-customer, or even functional problems that compromise the product's performance or safety. For example, a client manufacturing precision electronic enclosures in India, requiring components to slot together with minimal gaps for EMI shielding, might legitimately require thickness tolerances of ±0.05mm, a specification readily achievable with MFY's cold-rolled stainless steel. If they mistakenly accept or specify hot-rolled material with typical tolerances of ±0.2mm or wider for these critical parts, their entire automated assembly line could be disrupted, leading to manual rework and significant production losses.
The diverse array of available surface finishes, particularly for cold-rolled steel (e.g., the common 2B matte finish, the highly reflective BA bright annealed finish, various polished finishes like No. 4 brushed or No. 8 mirror, and patterned/embossed options), can also be a source of confusion and misapplication if not fully understood. Each finish has distinct aesthetic qualities, different levels of reflectivity, varying surface roughness (Ra values), and sometimes, different practical performance characteristics, such as cleanability or resistance to fingerprinting. Choosing an inappropriate finish can negatively impact the product's market appeal, its suitability for the intended operational environment (e.g., a highly reflective finish causing glare issues), or even its functional performance (e.g., a rougher finish harboring contaminants in a hygienic application). At MFY, as part of our service, we often provide detailed consultations, finish samples, and comprehensive specifications to help clients, ranging from equipment integrators to architectural firms, select the most appropriate and cost-effective finish for their specific application. This might involve choosing a food-grade 2B finish for large-scale processing equipment or a highly consistent, blemish-free BA finish for premium decorative elements.
Moreover, the inherent surface characteristics—the presence of mill scale on hot-rolled steel versus the clean, smooth surface of cold-rolled steel—directly dictate the necessity and cost of subsequent processing steps. If hot-rolled steel is chosen for an application that ultimately requires a smooth, painted, or coated surface, then the costs associated with descaling (e.g., through pickling or abrasive blasting) and further surface preparation must be meticulously factored into the economic equation. These additional steps can sometimes negate, or even reverse, hot-rolled steel's initial price advantage over a cold-rolled product that might be ready for painting with minimal preparation. This foresight into the entire production chain is crucial for making an economically sound decision, a level of insight MFY's integrated supply chain experience provides.
Navigating Formability, Weldability, and Machinability Differences
The distinct mechanical properties imparted by the hot versus cold rolling processes significantly affect how the material behaves during subsequent fabrication operations such as forming, welding, and machining. Hot-rolled stainless steel, being generally softer and possessing greater ductility (for a given grade before any significant cold work is introduced), is often easier to form into complex shapes or deep-drawn components. It is also typically considered more forgiving to weld, with fewer concerns about issues like cracking or loss of toughness in the heat-affected zone (HAZ), especially when dealing with thicker sections. However, its characteristically rougher surface, if not descaled, can sometimes lead to increased friction and consequently accelerated tool wear during forming operations like stamping or bending, which can add to tooling maintenance costs over time.
Cold-rolled stainless steel, due to the significant work hardening it undergoes during the cold reduction process, is notably stronger and harder but consequently less ductile than its hot-rolled counterpart (again, assuming the cold-rolled material has not been subsequently annealed to restore ductility). This increased strength and hardness can make it more challenging to form, often requiring more powerful forming equipment, more robust and wear-resistant tooling materials, and careful attention to process parameters to manage issues like increased springback or the potential for cracking during severe bending or deep drawing operations. While the weldability of most cold-rolled stainless steels is generally good (especially for austenitic grades), the higher internal stresses present in heavily cold-worked material might necessitate pre- or post-weld heat treatment in some critically stressed applications or for certain grades to prevent problems like stress corrosion cracking or to restore optimal corrosion resistance in the weld zone. Machinability characteristics can also differ; some fabricators find that the harder, more uniform surface of cold-rolled steel provides a better machined finish and improved chip control, while others might find certain highly work-hardened grades more challenging to machine due to their increased toughness and tendency to cause rapid tool wear.
Industries must therefore carefully consider their existing fabrication capabilities, the skill level of their workforce, the complexity of the part design, and the expected production volumes. A decision to switch from hot-rolled to cold-rolled steel (or vice-versa) for a particular product might necessitate significant adjustments in tooling design, machinery settings, lubrication practices, or even entire process sequences. For instance, a construction contractor primarily accustomed to welding thicker hot-rolled structural sections might need to adjust their welding parameters, techniques, and possibly even consumables when working with thinner gauge, harder cold-rolled stainless steel for intricate architectural features or lighter-gauge ductwork. As a comprehensive stainless steel supplier, MFY often provides detailed technical data sheets that clearly outline these crucial forming, welding, and machining properties to help our diverse clients—from large-scale manufacturing companies to specialized engineering contractors—anticipate and effectively manage these fabrication challenges, ensuring a smoother production flow and higher quality end-products. Our innovation-driven approach also means we are constantly exploring new grades and processing techniques to enhance these characteristics.
Hot-rolled steel has wider tolerancesTrue
Hot-rolled steel typically has dimensional tolerances around ±0.2mm compared to cold-rolled's ±0.05mm, making it less precise but more economical for non-critical applications.
Cold-rolled steel is always betterFalse
Cold-rolled steel's superior properties aren't always necessary - for hidden structural components or applications with wide tolerances, hot-rolled may be more cost-effective without compromising performance.
How can companies make informed decisions about using hot or cold-rolled stainless steel?
Worried about making a suboptimal material choice that could inflate costs or compromise quality? An uninformed decision can have lasting negative impacts on your projects. Let's outline how your company can confidently choose the right stainless steel.
Companies can make informed decisions by thoroughly evaluating application requirements, considering the total cost of ownership, consulting with material experts or suppliers like MFY, reviewing industry standards and case studies, and potentially conducting material testing for critical applications.
Making the right choice between hot-rolled and cold-rolled stainless steel isn't just about comparing basic material datasheets; it's a strategic process that demands careful consideration of multiple interconnected factors, ensuring optimal alignment between material properties, application demands, and economic realities. As I've learned through countless consultations with a diverse range of clients at MFY—from large multinational manufacturing enterprises in India to specialized engineering firms7 executing complex projects in the Middle East—an informed decision invariably hinges on a holistic and nuanced understanding of the project's unique demands.
It commences with a deep and thorough dive into the end-use application: What are the absolute critical performance criteria? Is surface aesthetics a primary driver of value, or is uncompromised structural integrity the paramount concern? What specific environmental conditions—temperature extremes, corrosive agents, mechanical stresses—will the final product or component face throughout its operational life? Beyond these crucial technical aspects, overarching economic considerations such as stringent budget constraints, expected production volumes, and the capabilities and limitations of available fabrication technologies play an equally pivotal role. Simply opting for the cheapest available option by default, or conversely, over-specifying with an unnecessarily high-grade or overly processed material, can swiftly lead to significant inefficiencies, inflated costs, or compromised product performance. Therefore, a structured, methodical approach that involves thorough evaluation of all parameters, proactive expert consultation (which MFY readily provides), and a keen, analytical eye on the total lifecycle impact is absolutely essential for navigating this selection process with confidence and precision. We will now explore practical steps and key considerations to empower your company to make this crucial decision effectively.

Empowering companies to make well-founded decisions between hot-rolled and cold-rolled stainless steel is a core part of MFY's mission to drive the global expansion of China’s stainless steel supply chain with agility and resilience. It requires a multi-faceted approach, blending technical understanding with commercial acumen. Our experience serving diverse clients like manufacturing companies, engineering contractors, distributors, and equipment integrators has shown that a few key strategies are universally effective.
Conducting a Thorough and Granular Application Requirements Analysis
The absolute cornerstone of any informed material selection decision is a meticulous, granular analysis of the specific requirements of the end-use application. This critical first step involves asking, and rigorously answering, a series of detailed questions: What is the primary, and secondary, function of the component or product being designed? What precise mechanical loads (static, dynamic, fatigue, impact) will it be expected to bear throughout its service life? What are the non-negotiable, minimum acceptable values for strength (yield, tensile), hardness, and ductility? For instance, a heavy-duty structural beam in a corrosive marine environment clearly needs exceptional strength and superior corrosion resistance, but perhaps a mirror-like surface finish is entirely superfluous, making a suitably graded hot-rolled stainless steel profile a potentially viable and cost-effective candidate. Conversely, a casing for a sophisticated medical imaging device not only requires specific structural integrity but also demands an impeccably smooth, hygienic, and aesthetically pleasing surface, strongly pointing towards a specific grade and finish of cold-rolled stainless steel8. According to a study by Granta Design (now Ansys), material selection accounts for a significant portion of product cost and performance, underscoring the importance of this initial analysis.
Furthermore, it's vital to comprehensively consider the intended operating environment. Will the part be exposed to extreme temperatures (high or cryogenic), aggressive chemical agents, persistent moisture or humidity, significant abrasion, or ultraviolet radiation? The answers to these questions will significantly influence not only the fundamental choice between hot-rolled and cold-rolled processing but also, crucially, the selection of the specific grade of stainless steel required (e.g., austenitic, ferritic, martensitic, duplex) and any necessary surface treatments. For example, MFY frequently advises clients involved in the chemical processing industry or marine applications in regions like India or Southeast Asia (known for their warm, humid, and saline coastal environments) to carefully consider stainless steel grades with higher molybdenum content (like 316L or certain duplex grades) for enhanced resistance to pitting and crevice corrosion. Once the grade is determined, the decision on hot- versus cold-rolled can be made based on the specific finish, tolerance, and secondary forming requirements.
Employing a structured analytical tool, such as a detailed requirements checklist, a Pugh matrix for concept selection, or even a simplified Quality Function Deployment (QFD) approach, can be immensely beneficial during this phase. These tools help translate often vague customer needs and broad functional requirements into specific, measurable material properties and performance targets. This systematic evaluation ensures that all critical aspects are considered, preventing costly oversights or assumptions. I vividly recall a client, an equipment integrator for the food processing industry, who initially focused almost exclusively on the corrosion resistance and strength requirements for a conveyor system component. However, during a detailed review with our MFY technical team, it became apparent that the extremely tight assembly tolerances required by their new automated production line, coupled with the need for an easily cleanable surface to meet hygiene standards, unequivocally necessitated the precision and superior finish of cold-rolled stainless steel—a factor that had been overlooked in their initial, less granular assessment.
Evaluating Total Cost of Ownership (TCO) and Comprehensive Lifecycle Impact
Moving decisively beyond the often misleading simplicity of initial purchase price per kilogram, companies must rigorously evaluate the Total Cost of Ownership (TCO) associated with their material choice. This comprehensive financial assessment encompasses not only the direct cost of the raw stainless steel material but also all subsequent fabrication costs (including cutting, forming, bending, welding, and machining – each of which can be affected by the choice between hot and cold-rolled), any necessary finishing costs (such as descaling and painting hot-rolled steel, or specialized polishing for cold-rolled steel), costs associated with assembly (which can be higher if tolerances are poor), anticipated scrap and rework rates (often lower with the precision of cold-rolled), and any investment in specialized tooling or modifications to existing equipment that might be necessitated by the chosen material. Hot-rolled stainless steel might indeed present a lower upfront cost, but if its use leads to significantly higher tool wear due to surface scale, requires extensive and costly surface preparation before painting, or results in a higher percentage of rejected parts due to dimensional inconsistencies, its TCO might ultimately exceed that of a seemingly more expensive cold-rolled alternative.
The concept of lifecycle impact extends this analysis further to include critical long-term factors such as ongoing maintenance requirements, the ease and cost of potential repairs, and the overall expected longevity or service life of the final product. A marginally more expensive cold-rolled stainless steel component, perhaps featuring a superior intrinsic corrosion resistance due to its grade and a more robust surface finish, might require significantly less maintenance or offer a substantially longer operational life in certain aesthetic or mildly corrosive applications. This can more than justify its higher initial upfront cost over time, particularly for infrastructure or long-life capital equipment. For example, the International Stainless Steel Forum (ISSF) and various national steel development institutes frequently publish compelling case studies and technical papers demonstrating the substantial long-term economic benefits of using appropriate grades of stainless steel in applications like public infrastructure, bridges, and building facades, primarily due to dramatically reduced maintenance, repair, and replacement frequency over decades of service. MFY actively promotes this TCO/LCC perspective among our clients, especially targeting manufacturing companies and engineering contractors who are designing products or systems intended for extended operational lives. We once worked closely with a client producing high-volume commercial kitchen equipment who made a strategic shift from a cheaper carbon steel alternative (which required frequent replacement due to corrosion) to MFY's durable 304 grade cold-rolled stainless steel. While their initial material unit cost increased, their warranty claims related to corrosion plummeted, rework rates during manufacturing dropped significantly due to better formability and consistency, and overall customer satisfaction improved markedly due to the enhanced aesthetic appeal, hygiene, and durability of the final products. This ultimately had a profoundly positive impact on their TCO and brand reputation.
Furthermore, a critical component of TCO, often overlooked, is the "cost of failure." If choosing a less-than-optimal material (perhaps solely based on minimizing initial price) leads to premature product failure in the field, it can trigger a cascade of dire financial and reputational consequences. These include expensive warranty claims, product recall costs, potential legal liabilities, loss of customer trust, and significant damage to the company's brand image. The initial perceived savings from a cheaper material choice become utterly insignificant when weighed against these potentially catastrophic downstream costs.
Leveraging Supplier Expertise, Collaborative Partnerships, and Material Testing
Companies should never hesitate to proactively consult with experienced and knowledgeable material suppliers and technical experts. As a Global Business Director at MFY, a diversified group company with a deeply integrated stainless steel supply chain—encompassing everything from raw material trading and R&D to advanced cold-rolled processing, tube manufacturing, and digital innovation—I and my dedicated team have accumulated a wealth of practical knowledge and technical expertise across an extensive array of applications and diverse global industries. We are well-positioned to provide invaluable insights into nuanced material behavior under various conditions, recommend the most suitable stainless steel grades and finishes for specific and often unique requirements, and help clients confidently navigate the often-complex landscape of international standards (ASTM, EN, JIS, GB, etc.) and specifications. Reputable and technically proficient suppliers like MFY can offer much more than just material; we provide comprehensive technical data sheets, relevant industry case studies, mill test certificates (MTCs) verifying chemical composition and mechanical properties, and sometimes even direct assistance with prototype development or fabrication process optimization. For example, if a client is uncertain about the formability of a particular high-strength cold-rolled grade for a new, complex product design, our R&D team can provide typical forming limit diagrams, offer advice on appropriate tooling, or even conduct trial runs on our equipment. Our commitment to continuous evolution means we are always ready to collaborate on innovative solutions.
For critical applications, when introducing a new product, or when transitioning to an entirely new material or grade of stainless steel, conducting thorough material testing and/or creating functional prototypes can be an invaluable risk-mitigation strategy. This hands-on approach allows companies to empirically verify the material's performance characteristics under actual or accurately simulated operating conditions and to identify and fine-tune their manufacturing processes (e.g., welding parameters, bending radii, lubrication for forming) before committing to expensive large-scale production runs. Testing protocols can range from relatively simple workshop evaluations like bend tests, weld penetration checks, and surface roughness measurements to more sophisticated laboratory analyses involving corrosion immersion testing, tensile testing at various temperatures, fatigue life testing, or detailed metallographic examination. Many of our target clients at MFY, such as major engineering and construction contractors or manufacturers of critical equipment, routinely request MTCs to verify conformance to specifications. For new or particularly challenging projects, they will often conduct their own independent validation tests on material samples that we readily provide, fostering a transparent and collaborative partnership.
Finally, diligently reviewing established industry standards (such as those published by ASTM International, European Committee for Standardization (CEN), Japanese Industrial Standards (JIS), etc.) and seeking out relevant, well-documented case studies from similar applications or industries can also provide extremely valuable guidance and benchmarks. These resources often contain a wealth of empirical data on material performance, best practices for design and fabrication, and lessons learned from past projects. By systematically combining rigorous internal analysis with proactive external expert consultation, leveraging the capabilities of a strong supply partner like MFY, and grounding decisions in empirical data from testing and established industry knowledge, companies can significantly reduce the risk of making an inappropriate or suboptimal material choice. This structured approach ensures not only technical success and product reliability but also robust economic efficiency and a strengthened competitive edge in the marketplace.
Cold-rolled steel has better surface finishTrue
Cold-rolled stainless steel undergoes additional processing that results in smoother surfaces and tighter tolerances, making it ideal for applications requiring aesthetic appeal or precision.
Hot-rolled steel always costs lessFalse
While hot-rolled steel typically has lower initial costs, its total cost of ownership may be higher due to additional processing needs, higher scrap rates, and maintenance requirements in certain applications.
Conclusion
Choosing between hot-rolled and cold-rolled stainless steel coils hinges on understanding your specific application's needs for finish, tolerance, and mechanical properties against cost. A thorough analysis and expert consultation, like that offered by MFY with our integrated supply chain and global expertise, ensures optimal material selection for project success and efficiency.
-
Compare processing methods and applications for better material selection ↩
-
Understand influence of high-temperature processing on stainless steel characteristics ↩
-
Learn about applications of hot-rolled stainless steel in construction and infrastructure ↩
-
Learn why BA is ideal for aesthetic, easy-clean surfaces ↩
-
Understand cost, performance, and application differences between the two product types ↩
-
Learn about the impact on fabrication processes and production efficiency ↩
-
Understand factors influencing steel choices in complex engineering projects ↩
-
Identify optimal grades for medical device applications ensuring best performance ↩
Have Questions or Need More Information?
Get in touch with us for personalized assistance and expert advice.