Temperature Rating for Stainless Pipes (-200 - 800 °C): An In-Depth Guide
Are you struggling to find piping materials that can withstand extreme temperature fluctuations without failing? Many industries face the challenge of sourcing pipes that maintain integrity from cryogenic lows to scorching highs, impacting safety and operational efficiency. At MFY, we understand that selecting the right stainless steel is paramount for reliable performance.
Stainless steel pipes are suitable for extreme temperatures from -200°C to 800°C due to their specific austenitic microstructures, chromium content providing oxidation resistance, and nickel enhancing low-temperature toughness and high-temperature strength. Alloying elements further refine these properties for specific thermal demands.
Choosing the correct stainless steel pipes for demanding temperature applications can seem daunting, but it's crucial for operational success and safety. In my years at MFY, I've seen firsthand how understanding the nuances of material science translates into long-term reliability for our clients. This guide will walk you through the critical factors, ensuring you're well-equipped to make informed decisions for your projects.
The world of stainless steel is vast, and its application across a wide temperature spectrum, from -200°C to 800°C, is a testament to its versatility. However, not all stainless steels are created equal, especially when pushed to thermal extremes. At MFY, we often guide clients through the selection process, emphasizing that factors like alloy composition1, manufacturing quality, and specific operational conditions dictate performance. For instance, austenitic grades like 304 or 316 are workhorses, but for severe high-temperature or cryogenic applications, specialized grades or considerations come into play. Understanding these nuances is key to leveraging stainless steel's full potential in challenging thermal environments.
What makes stainless steel pipes suitable for extreme temperature ranges?
Are your operations hampered by pipe materials that can't handle the heat or the cold? This common problem leads to costly failures and downtime. Selecting stainless steel pipes with the appropriate composition and properties is the key to ensuring durability across a wide temperature spectrum.
Stainless steel's suitability stems from its chromium content, forming a passive oxide layer for corrosion and oxidation resistance, and nickel, which enhances toughness at low temperatures and strength at high temperatures. The specific grade's alloying elements precisely tune these characteristics.
Navigating the material specifications for extreme temperature applications can feel like walking a tightrope. One misstep in selecting a stainless steel grade, and you could be looking at premature failure, operational disruptions, or even safety hazards. I recall a client in the petrochemical industry who initially opted for a standard grade for a high-temperature application, only to face rapid scaling and loss of mechanical strength. This experience highlighted the critical importance of matching the material to the environment. The inherent properties of stainless steel, particularly its austenitic grades, provide a fantastic starting point. The face-centered cubic (FCC) crystal structure of austenitic stainless steels, like the 300 series we frequently supply at MFY, is key to their excellent formability and toughness, even at cryogenic temperatures where other steels might become brittle. Furthermore, the chromium content, typically above 10.5%, is fundamental in forming a self-healing passive chromium oxide layer. This layer is crucial for resisting oxidation at elevated temperatures and preventing various forms of corrosion across the entire temperature spectrum. It’s this combination of structural stability and protective surface chemistry that sets stainless steel apart. We'll explore these fascinating properties more deeply.
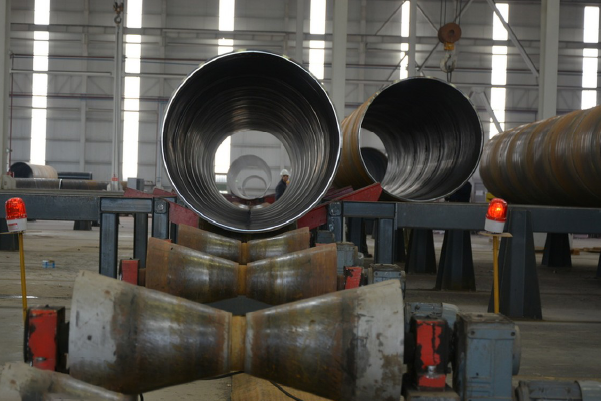
The remarkable ability of stainless steel pipes to perform reliably across a vast temperature range, from the frigid -200°C encountered in cryogenics to the blistering 800°C found in industrial furnaces, is not accidental. It's a direct result of meticulous metallurgical design and an understanding of how different alloying elements interact at a microscopic level. At MFY, we've supplied stainless steel pipes to clients ranging from LNG facilities in Southeast Asia, handling temperatures as low as -162°C, to manufacturing plants in India dealing with high-temperature processing. These experiences have consistently reinforced the importance of selecting the right grade for the specific thermal challenge. The journey into understanding this suitability begins with the fundamental composition and microstructure of stainless steel.
The Crucial Role of Alloying Elements
Stainless steel isn't a single material but a family of alloys, each with unique characteristics imparted by its specific chemical composition. The primary elements, iron and chromium, are just the beginning. For extreme temperature performance, other elements play pivotal roles. Chromium, typically present at 10.5% or more, is the star player for high-temperature oxidation resistance. It forms a stable, adherent, and self-healing chromium oxide (Cr₂O₃) layer on the surface. This passive layer acts as a barrier, significantly slowing down further oxidation and scaling, especially critical as temperatures rise towards 800°C. Consider a furnace application: without this protective layer, the steel would rapidly degrade.
Nickel is another key constituent, particularly for austenitic stainless steels like the 304, 316, and 310 grades that MFY frequently provides. Nickel stabilizes the austenite phase, which maintains excellent ductility and toughness even at cryogenic temperatures down to -200°C. This prevents the brittle fracture that plagues many carbon and low-alloy steels at such low temperatures. For example, in LNG (Liquefied Natural Gas) applications, where temperatures can plummet to -162°C, austenitic stainless steels are the material of choice precisely because of their nickel-imparted toughness. Furthermore, nickel also contributes to increased strength and creep resistance at elevated temperatures, complementing the role of chromium.
Other elements like molybdenum (found in Grade 316) enhance pitting and crevice corrosion resistance, which can be exacerbated at moderate to high temperatures in certain chemical environments. Molybdenum also contributes to high-temperature tensile and creep strength. Elements like titanium or niobium (in stabilized grades like 321 or 347) are added to prevent sensitization – the formation of chromium carbides at grain boundaries during high-temperature exposure (around 450-850°C), which can lead to intergranular corrosion. This is particularly important for welded components that will operate at elevated temperatures. Our clients in the chemical processing industry often require these stabilized grades for welded reactors and piping systems operating within this sensitization range.
Microstructural Stability Across Temperatures
The microstructure of stainless steel, particularly the austenitic grades, is fundamental to its wide temperature applicability. The face-centered cubic (FCC) crystal structure of austenite is inherently more ductile and resistant to brittle fracture at low temperatures compared to the body-centered cubic (BCC) structure of ferritic or martensitic steels. This is why austenitic stainless steels, such as those in the 300 series, retain their toughness remarkably well down to liquid helium temperatures (-269°C), far exceeding the -200°C lower bound of our discussion. This makes them indispensable for cryogenic storage and transportation of liquefied gases like nitrogen, oxygen, and argon. I remember a project with an industrial gas supplier where the integrity of 304L stainless steel pipes at -196°C was paramount for safety and efficiency.
At the higher end of the temperature spectrum, up to around 800°C, the stability of the austenite phase and the protective chromium oxide layer are key. However, prolonged exposure to high temperatures can introduce microstructural changes. As mentioned, sensitization can occur in non-stabilized grades if held within the 450-850°C range. For even higher temperatures, approaching and exceeding 800°C, grades with higher chromium and nickel content, like 310S (often used up to 1150°C for intermittent service) or specialized heat-resistant alloys, are preferred. These grades are designed to resist high-temperature scaling, maintain mechanical strength, and resist phenomena like sigma phase embrittlement, which can occur in some stainless steels after long exposures to temperatures between approximately 550°C and 850°C, leading to a loss of toughness at room temperature.
The thermal expansion coefficient of austenitic stainless steels is also a significant design consideration. It's generally higher than that of carbon steels or ferritic stainless steels. While this doesn't directly affect the material's suitability per se, it must be accounted for in engineering design to prevent excessive thermal stresses, warping, or fatigue in systems that experience wide temperature swings. At MFY, when supplying pipes for high-temperature systems, we always advise our clients, often engineering contractors, to incorporate appropriate expansion joints or loops in their designs. For instance, a 10-meter pipe heating from 20°C to 800°C can expand by over 13 cm, a significant displacement that needs careful management.
Synergistic Effects of Composition and Structure for Thermal Performance
The suitability of stainless steel pipes for extreme temperatures is not just about individual alloying elements or a stable microstructure alone; it's the synergistic effect of these factors working in concert. The chromium ensures oxidation resistance at high temperatures, while nickel ensures low-temperature toughness and contributes to high-temperature strength. The austenitic structure provides an excellent foundation for these properties across the entire -200°C to 800°C range. This combination allows for a versatile material that can be tailored through precise alloying for specific segments of this broad temperature spectrum.
Consider the interplay: the chromium oxide layer protects the underlying metal from aggressive environments at high temperatures, allowing the inherent mechanical properties of the nickel-stabilized austenite to be maintained. At cryogenic temperatures, the FCC structure, supported by nickel, prevents the ductile-to-brittle transition, ensuring the pipe remains robust. Different grades showcase this synergy in distinct ways. For example, Grade 304L, with its lower carbon content, minimizes sensitization issues after welding, making it suitable for applications involving moderate high temperatures where post-weld heat treatment isn't feasible. Grade 310S, with its high chromium (around 25%) and nickel (around 20%) content, is specifically designed for superior high-temperature oxidation resistance and strength, making it a go-to for furnace parts, heat exchangers, and combustion chambers operating continuously near the 800°C mark and even higher.
The following table provides a simplified overview of how key elements and structure contribute to performance at temperature extremes for common austenitic grades MFY supplies:
Feature | Low Temperature (-200°C) Performance | High Temperature (up to 800°C) Performance | Key Contributing Factors | Typical Grades |
---|---|---|---|---|
Toughness/Ductility | Excellent, resists brittle fracture | Good, though strength decreases with temperature | Austenitic (FCC) structure, Nickel content | 304/L, 316/L |
Oxidation Resistance | Not a primary concern | Good to Excellent, forms protective Cr₂O₃ layer | Chromium content | 304/L, 316/L |
High-Temp Strength | Not applicable | Moderate to Good, depends on grade and specific temperature | Nickel, Molybdenum, Nitrogen, Solid solution | 304H, 316H |
Specialized High-Temp | Good low-temp toughness (though not primary design driver) | Excellent oxidation resistance and strength at very high temperatures | High Cr & Ni content | 310S, 321, 347 |
Cryogenic Performance | Specifically designed for excellent toughness and resistance to embrittlement | Not primary design focus, but generally good oxidation resistance | Austenitic structure, controlled impurities | 304L, 316L |
This synergistic design allows engineers and operators to select stainless steel pipes with confidence for a wide array of demanding thermal applications, ensuring both safety and longevity. At MFY, our integrated supply chain and production capabilities ensure that these carefully designed alloys are manufactured to the highest standards, delivering the performance our clients expect.
Chromium prevents high-temperature oxidationTrue
Chromium forms a protective oxide layer that resists scaling and oxidation at temperatures up to 800°C.
All stainless steels perform equally at cryogenic temperaturesFalse
Only austenitic grades with sufficient nickel content maintain toughness at cryogenic temperatures below -100°C.
How do current industries utilize stainless steel pipes within this temperature spectrum?
Struggling to identify the right applications for stainless steel pipes across diverse temperature needs2? Many industries require robust piping solutions for conditions ranging from deep cryogenics to intense heat. Stainless steel pipes offer versatile solutions, proven in numerous demanding environments globally.
Industries utilize stainless steel pipes from -200°C in cryogenics (LNG, industrial gases) to 800°C in petrochemicals (furnaces, reformers), power generation (boilers, superheaters), and specialized manufacturing, leveraging their corrosion resistance and mechanical integrity at these extremes.
The versatility of stainless steel pipes across the -200°C to 800°C temperature range is truly remarkable, and at MFY, we've seen firsthand how various sectors leverage these properties. It's not just about a single industry; it's a broad spectrum of applications, each with unique challenges and requirements. For instance, our clients in the LNG sector in Southeast Asia rely on austenitic stainless steel grades like 304L and 316L for their cryogenic properties, essential for safely handling liquefied natural gas at -162°C. Moving to the other extreme, we supply high-chromium, high-nickel grades like 310S to petrochemical plants in India and the Middle East for high-temperature reformers and cracking units operating at or near 800°C. The common thread is the need for reliability and resistance to extreme conditions, whether it's preventing brittle fracture at sub-zero temperatures or combating oxidation and creep at elevated ones. Beyond these, the food and beverage industry uses stainless steel for its hygienic properties and ability to withstand temperature cycling during sterilization processes. Similarly, the pharmaceutical sector demands high-purity stainless steel for processes that often involve varied thermal conditions. Each application underscores the adaptability of stainless steel, a testament to its carefully engineered composition and microstructure.
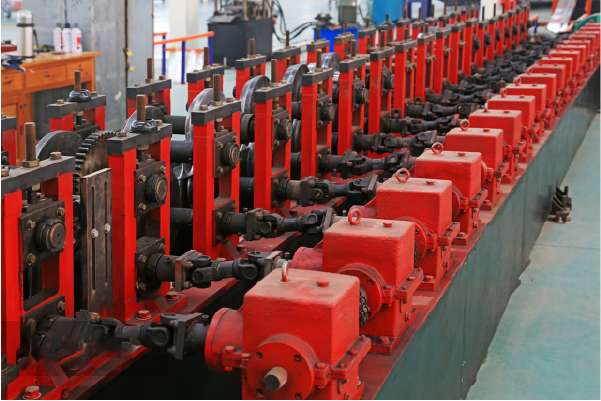
The adoption of stainless steel pipes across the -200°C to 800°C temperature spectrum is widespread, driven by the material's unique combination of mechanical strength, corrosion resistance, and thermal stability. At MFY, our experience supplying diverse global markets, from India and Southeast Asia to the Middle East, has given us a panoramic view of these applications. Manufacturing companies, engineering contractors, and equipment integrators all turn to stainless steel for critical operations where temperature extremes are the norm. The choice of specific grades, like our popular 300 series coils, sheets, and pipes, is always tailored to the precise thermal and chemical environment. Let's delve into some specific industrial applications that showcase this versatility.
Cryogenic Applications: Handling the Extreme Cold (-200°C to 0°C)
In the realm of extreme cold, austenitic stainless steels like 304, 304L, 316, and 316L are indispensable. Their face-centered cubic (FCC) crystal structure remains stable and ductile even at temperatures approaching absolute zero, preventing the brittle fracture that plagues many other materials. The Liquefied Natural Gas (LNG) industry is a prime example. LNG is stored and transported at approximately -162°C. Stainless steel pipes are extensively used in liquefaction plants, storage tanks, regasification terminals, and LNG carriers. I recall a project with an engineering contractor building an LNG import terminal in Southeast Asia; MFY supplied a significant quantity of 304L pipes, chosen for their excellent cryogenic toughness and weldability. The low carbon content in 304L minimizes carbide precipitation during welding, maintaining corrosion resistance and toughness in the heat-affected zone.
Beyond LNG, stainless steel pipes are critical for handling other industrial liquefied gases such as nitrogen (-196°C), oxygen (-183°C), and argon (-186°C). These gases are used in myriad applications, from food preservation and medical uses to specialized manufacturing processes like semiconductor fabrication. Research facilities and aerospace applications also frequently employ stainless steel piping for cryogenic fluid transfer. For instance, cryocoolers and superconducting magnet systems often rely on stainless steel for its low thermal conductivity (reducing heat leak) in addition to its mechanical properties at low temperatures. The reliability of MFY's stainless steel pipes in these demanding cryogenic conditions is a testament to our stringent quality control from raw material sourcing to final product delivery.
The selection criteria for cryogenic applications often include not just toughness (measured by Charpy impact tests at specific low temperatures) but also fatigue resistance, especially if thermal cycling is involved. Dimensional stability is another factor; while stainless steel does contract at low temperatures, its behavior is predictable. For example, a 304 stainless steel pipe will contract by approximately 0.3% when cooled from room temperature to -196°C. This must be accounted for in system design to avoid undue stress. Our technical teams at MFY often work with clients to ensure they have the necessary data for their design calculations.
High-Temperature Services: Enduring the Heat (Approx. 400°C to 800°C)
As temperatures climb, different properties of stainless steel come to the forefront. Oxidation resistance, creep strength, and resistance to microstructural degradation become paramount. Austenitic stainless steels, particularly those with higher chromium and nickel content (like 310S, 309S) and stabilized grades (321, 347), excel in these environments. The petrochemical industry extensively uses stainless steel pipes in reformers, cracking furnaces, and heat exchangers where process fluids can reach 800°C or higher. For example, steam methane reformers operate at very high temperatures and pressures; 304H, 316H, or even more specialized alloys are used for the radiant coils and outlet piping. The 'H' grades have a higher carbon content (0.04-0.10%) which imparts greater high-temperature strength and creep resistance.
Power generation is another major user. Boiler tubes, superheaters, and reheaters in thermal power plants operate under extreme conditions of temperature and pressure. While carbon steels and low-alloy steels are used in cooler sections, austenitic stainless steels are required for the hottest parts to resist steam oxidation and maintain strength. For instance, superheater tubes handling steam above 600°C often utilize grades like TP304H, TP316H, TP321H, or TP347H. MFY has supplied such grades to manufacturing companies producing boiler components. The choice depends on the specific temperature, pressure, and corrosive environment. For instance, in environments with sulfur-containing flue gases, higher chromium grades are preferred for better sulfidation resistance.
Industrial furnaces, kilns, and heat treatment equipment also rely heavily on heat-resistant stainless steel pipes for components like radiant tubes, muffles, and conveyor systems. Here, grades like 310S (typically serviceable up to 1100-1150°C for intermittent service and lower for continuous, but well within our 800°C upper discussion limit for many continuous applications) are common due to their excellent oxidation resistance resulting from high chromium (24-26%) and nickel (19-22%) content. We've seen these grades perform exceptionally well in applications involving frequent thermal cycling, where resistance to scaling and maintaining structural integrity is crucial. The key is to match the grade's capabilities, such as its maximum allowable stress at temperature (derived from creep data), with the operational demands.
Moderate and Fluctuating Temperature Applications (0°C to 400°C and Cycling)
While not "extreme" in the same vein as cryogenics or high-temperature furnaces, the 0°C to 400°C range, especially with thermal cycling, presents its own set of challenges where stainless steel thrives. The food and beverage industry, for example, uses stainless steel (commonly 304/304L and 316/316L) extensively for its hygienic properties, corrosion resistance to food products, and ability to withstand cleaning-in-place (CIP) and sterilization-in-place (SIP) processes. These processes often involve rapid temperature changes, for instance, from ambient to steam temperatures (e.g., 121°C or higher) and back. Stainless steel's resistance to thermal fatigue and its ability to maintain a cleanable surface make it ideal.
Pharmaceutical manufacturing has similar requirements, with an even greater emphasis on purity and cleanability. Stainless steel pipes are used for transporting purified water, water-for-injection (WFI), and various process fluids. These systems often undergo regular steam sterilization cycles. The chemical processing industry also utilizes a vast amount of stainless steel piping in this temperature range for reactors, heat exchangers, and general piping, handling a wide variety of corrosive chemicals. Here, the specific grade is chosen based on corrosion resistance to the particular media, with 316L being a common choice due to its enhanced resistance to chlorides and acids thanks to its molybdenum content.
Automotive exhaust systems, although parts can exceed 800°C closer to the engine, have components operating within and cycling through this moderate range. Ferritic stainless steels (like 409 or 439) are often used for their cost-effectiveness and good resistance to exhaust gas condensates, but austenitic grades can be found in higher-performance systems. Even in building and construction, stainless steel pipes are used for hot water systems, solar thermal applications, and specialized architectural features where longevity and corrosion resistance under varying ambient conditions are required. MFY's ability to provide a range of stainless steel products, from coils and sheets for tank fabrication to pipes for fluid transport, supports these diverse industrial needs across the entire temperature spectrum.
The following table summarizes some common industrial applications of stainless steel pipes within the -200°C to 800°C range and typical grades used:
Temperature Range (°C) | Industry | Common Applications | Typical Stainless Steel Grades MFY Supplies |
---|---|---|---|
-200 to -100 | LNG, Industrial Gases, Cryogenics | Liquefaction, Storage, Transport | 304, 304L, 316, 316L |
-100 to 0 | Refrigeration, Food Processing | Cooling systems, Chilled fluid transport | 304, 304L, 316, 316L |
0 to 200 | Food & Beverage, Pharmaceutical | Process piping, CIP/SIP systems, Water systems | 304, 304L, 316, 316L |
200 to 500 | Chemical Processing, Power Gen | Heat exchangers, Low-temp steam lines, Process piping | 304/H, 316/H, 321/H, 347/H |
500 to 800 | Petrochemical, Power Gen, Furnaces | Reformer tubes, Superheaters, Furnace components | 304H, 316H, 321H, 347H, 309S, 310S |
This extensive utilization underscores why MFY remains committed to a fully integrated supply chain, ensuring we can deliver high-quality stainless steel pipes that meet the rigorous demands of these varied industries.
304L resists cryogenic brittle fractureTrue
304L's low carbon content maintains ductility below -160°C, preventing catastrophic failure in LNG applications.
Carbon steel outperforms at 800°CFalse
Specialized stainless grades like 310S maintain strength and oxidation resistance where carbon steel would rapidly degrade.
What challenges arise when stainless steel pipes are exposed to temperatures beyond their standard rating?
Operating equipment outside its designed temperature limits is a recipe for disaster, isn't it? When stainless steel pipes are pushed beyond their specified temperature ratings, their material properties can degrade significantly. This leads to unexpected failures, safety risks, and costly operational shutdowns.
Exposing stainless steel pipes beyond their standard rating leads to challenges like reduced tensile strength, creep deformation and rupture at high temperatures, or embrittlement (e.g., sigma phase, sensitization, 475°C embrittlement) and loss of toughness at incorrect temperature exposures.
Pushing any material beyond its limits is asking for trouble, and stainless steel, despite its robustness, is no exception. At MFY, we often counsel our clients, particularly those in manufacturing and engineering contracting, on the critical importance of adhering to specified temperature ratings. I’ve encountered situations where, perhaps due to process changes or oversight, pipes were subjected to temperatures higher than their design, leading to accelerated degradation. For example, using a standard 304L grade in an application that unexpectedly saw temperatures creep into the sensitization range 450-850°C3 for prolonged periods resulted in intergranular corrosion issues that weren't initially anticipated. Similarly, at extremely high temperatures, well beyond the usual design envelope for common grades, issues like excessive scaling, significant loss of mechanical strength (creep), or even localized melting can occur if an inappropriate grade is used. Conversely, using a grade not suited for cryogenic service can lead to brittle fracture. These challenges aren't just academic; they have real-world implications for safety, equipment longevity, and operational continuity. Understanding these potential pitfalls is the first step in avoiding them, guiding the selection towards grades specifically engineered for such demanding conditions, like the specialized high-temperature or cryogenic grades MFY can provide.
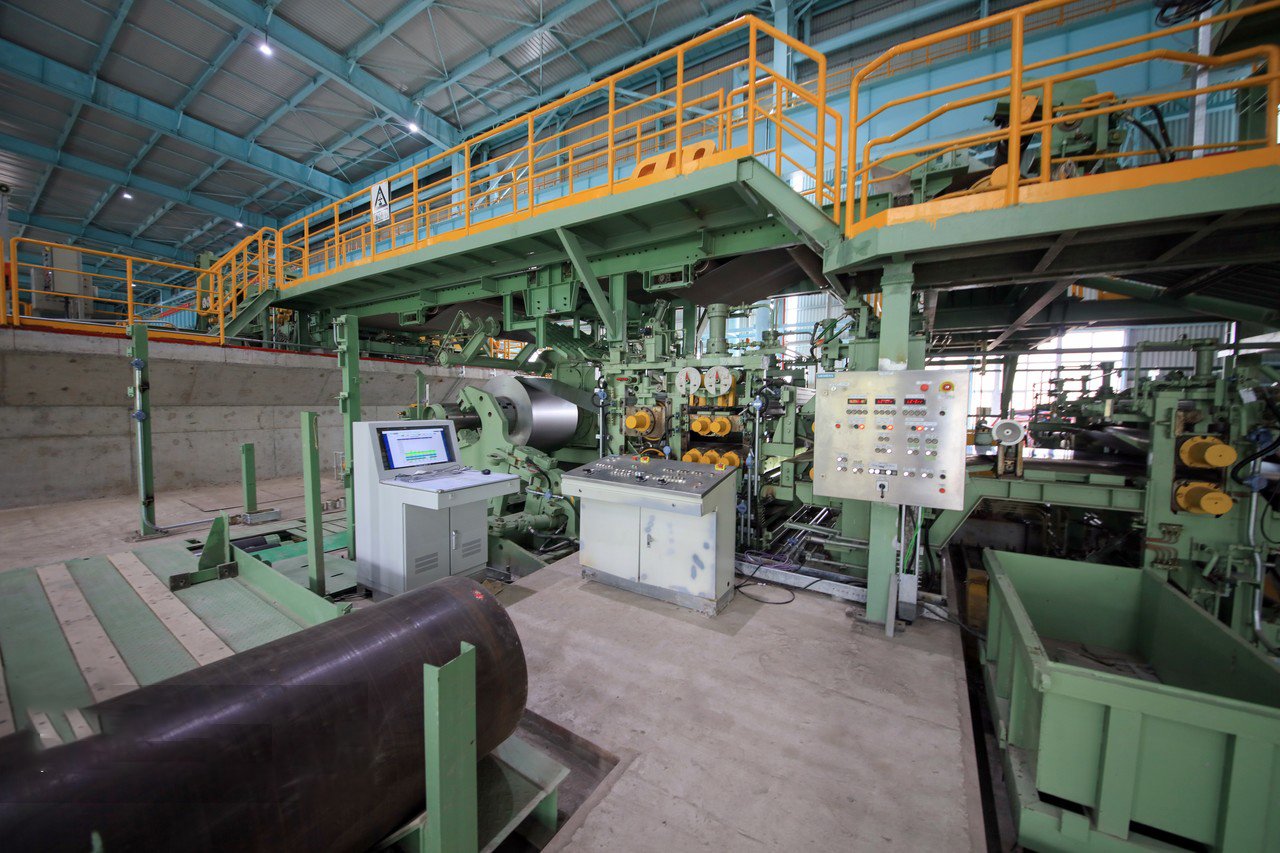
While stainless steel offers remarkable performance across a wide temperature spectrum, it's crucial to understand that each grade has its operational limits. Exceeding these limits, whether on the high or low side of its intended service temperature, can introduce a host of challenges that compromise the integrity and safety of the piping system. My experience at MFY, dealing with clients across diverse sectors from manufacturing to heavy engineering, has shown that a thorough understanding of these potential failure modes is vital for reliable system design and operation. Ignoring these limitations can lead to premature failures, costly downtime, and significant safety hazards. Let's explore some of the specific challenges that arise when stainless steel pipes are pushed beyond their comfort zone.
High-Temperature Degradation Mechanisms
When stainless steel pipes are exposed to temperatures exceeding their recommended limits, several degradation mechanisms can come into play, significantly reducing their service life. One of the primary concerns is accelerated oxidation and scaling. While the chromium oxide layer provides protection, its effectiveness diminishes at very high temperatures or if the temperature exceeds the design limit for a particular grade. Excessive scaling can lead to a loss of material thickness, reducing the pipe's pressure-carrying capacity. For example, while 304 stainless steel might be rated for continuous service up to about 870°C4 for oxidation resistance, its mechanical strength at that temperature is significantly reduced. Pushing it to, say, 950°C, even if for short periods, could lead to rapid scaling and loss of structural integrity.
Another critical issue is creep deformation and rupture. Creep is the tendency of a solid material to move slowly or deform permanently under the influence of persistent mechanical stresses, especially at elevated temperatures (typically above 0.4-0.5 times the melting temperature in Kelvin). If pipes are operated at temperatures where creep becomes significant for that specific grade, they can gradually deform, bulge, and eventually rupture, even if the stress is below the short-term yield strength. For instance, a 304H pipe designed for 650°C service will have a certain allowable stress based on its 100,000-hour creep rupture strength. Operating it at 750°C under the same stress would drastically reduce its lifespan. MFY supplies 'H' grades (e.g., 304H, 316H) which have higher carbon content and are solution annealed at higher temperatures to promote a coarser grain size, both of which improve creep resistance. However, even these have their limits.
Sensitization leading to intergranular corrosion is a major concern for austenitic stainless steels if held within or cooled slowly through the range of approximately 450°C to 850°C. In this range, chromium carbides precipitate at grain boundaries, depleting chromium in the adjacent regions and making these areas susceptible to corrosion. While stabilized grades (like 321, containing titanium, or 347, containing niobium) or low-carbon 'L' grades (like 304L, 316L) are designed to mitigate this, operating even these outside their intended thermal envelope or for excessively long times in the sensitization range can still pose risks, especially if subsequent exposure to a corrosive environment occurs at lower temperatures. I recall a client who used standard 304 for a component that experienced unexpected temperature excursions into this range, followed by exposure to a mildly corrosive atmosphere during shutdown, leading to cracking.
Low-Temperature Embrittlement and Challenges
While austenitic stainless steels (like 304, 316) are renowned for their excellent toughness at cryogenic temperatures, not all stainless steels fare as well, and even austenitic grades have considerations. If ferritic, martensitic, or duplex stainless steels (which contain ferrite) are used below their ductile-to-brittle transition temperature (DBTT), they can become extremely brittle and fracture catastrophically under impact or stress. For austenitic grades, while generally very tough, factors like high interstitial content (carbon, nitrogen if not controlled), severe cold work, or the presence of delta ferrite (in welds, for instance) can somewhat reduce their low-temperature toughness, although they typically remain suitable for services down to -196°C or lower. The key is ensuring the correct grade is chosen and that its condition (e.g., heat treatment, weld quality) is appropriate for the cryogenic service.
Another phenomenon, though less common for the typical austenitic grades used in cryogenics, is martensitic transformation in some less stable austenitic stainless steels (e.g., 301, or 304 under severe strain) at low temperatures. This transformation from austenite (FCC) to martensite (BCT) can increase strength but significantly reduces ductility and toughness, potentially leading to embrittlement. This is why grades like 304L and 316L, which have higher nickel content and are more stable, are preferred for deep cryogenic applications.
Furthermore, thermal stresses due to differential contraction can be a challenge if dissimilar materials are joined or if complex geometries lead to high stress concentrations during cooling to cryogenic temperatures. While a property of the system design rather than a material degradation per se, it's a critical challenge when operating at the lower end of the temperature spectrum. MFY always emphasizes careful material selection, sourcing from our integrated supply chain to ensure consistent material properties that meet cryogenic specifications. For example, ensuring low impurity levels (like sulfur and phosphorus) is crucial for maintaining excellent cryogenic toughness in 304L pipes supplied to our clients in the industrial gas sector.
Microstructural Instabilities and Other Temperature-Induced Issues
Prolonged exposure to certain temperature ranges, even if below the absolute maximum oxidation limit, can induce undesirable microstructural changes in some stainless steel grades. Sigma phase embrittlement is a concern for many austenitic and duplex stainless steels when exposed to temperatures roughly between 550°C and 850°C for extended periods. The sigma phase is a hard, brittle intermetallic compound that can severely reduce room-temperature ductility and toughness, as well as corrosion resistance. For example, a 316 stainless steel component operating for thousands of hours at 700°C might become brittle at ambient temperature, making it susceptible to fracture during shutdowns or startups. This is a critical consideration for equipment in power plants or petrochemical facilities that see long service times at such temperatures.
Another issue is 475°C (or 885°F) embrittlement, which primarily affects ferritic stainless steels and the ferrite phase in duplex stainless steels when held in or slowly cooled through the temperature range of about 350°C to 550°C. This leads to an increase in hardness and a severe loss of toughness at room temperature. While austenitic grades are generally immune, it's a key consideration if high-chromium ferritic grades are inadvertently used or if duplex stainless steels are pushed into this thermal window beyond their design.
Beyond these specific phase transformations, general thermal fatigue can occur if pipes are subjected to frequent and significant temperature cycling. The repeated expansion and contraction can lead to crack initiation and propagation, especially at stress concentration points like welds or geometric discontinuities. The magnitude of the temperature swing, the rate of change, and the number of cycles all play a role. While stainless steels have good thermal fatigue resistance compared to some materials, it's not infinite, and exceeding design cycle limits or temperature ranges can accelerate this type_of failure. This is often a concern for clients with batch processes or systems that undergo frequent startups and shutdowns.
The table below summarizes key challenges when operating beyond typical ratings:
Challenge Type | Specific Issue | Temperature Range of Concern | Primary Stainless Steel Types Affected | Consequence |
---|---|---|---|---|
High-Temp Degradation | Accelerated Oxidation/Scaling | > Grade's max operating temp | All (varies by grade) | Material loss, reduced strength |
Creep Deformation & Rupture | > ~0.4-0.5 Tmelt (K) | All (esp. under load at high temp) | Deformation, failure under pressure | |
Sensitization | ~450-850°C | Austenitic (non-stabilized, non-L grades) | Intergranular corrosion, reduced toughness | |
Low-Temp Embrittlement | Brittle Fracture | < DBTT | Ferritic, Martensitic, some Duplex | Catastrophic failure |
Reduced Toughness (even in Austenitic) | Cryogenic temps | Austenitic (if high impurities/cold work) | Reduced impact resistance | |
Microstructural Issues | Sigma Phase Embrittlement | ~550-850°C (prolonged exposure) | Austenitic (esp. high Cr, Mo), Duplex | Severe loss of room-temp ductility/toughness |
475°C (885°F) Embrittlement | ~350-550°C | Ferritic, Duplex | Loss of toughness, increased hardness | |
General | Thermal Fatigue | Significant, repeated temp cycles | All | Crack initiation and propagation |
Understanding these potential pitfalls is why, at MFY, we emphasize the importance of collaborative material selection with our clients, ensuring the chosen stainless steel grade is perfectly matched to the intended service conditions, including any potential (but designed-for) excursions.
304H improves creep resistanceTrue
304H has higher carbon content and is solution annealed at higher temperatures to enhance creep resistance at elevated temperatures.
All stainless steels perform well at cryogenic temperaturesFalse
Only austenitic stainless steels maintain good toughness at cryogenic temperatures; ferritic and martensitic grades become brittle.
What strategies can be implemented to improve the performance of stainless steel pipes at extreme temperatures?
Are you looking for ways to bolster your stainless steel pipes against the rigors of extreme temperatures? Simply selecting a standard grade isn't always enough. Proactive strategies are needed to enhance durability and prevent premature failure in demanding thermal environments.
To improve performance, select appropriate grades (e.g., high-nickel/chromium for heat, stabilized or low-carbon for sensitization resistance, specific austenitic grades for cryogenics), apply correct heat treatments, incorporate proper design considerations (e.g., expansion allowances), and consider surface treatments.
Ensuring stainless steel pipes perform optimally at the fringes of the temperature spectrum, from deep cryogenic conditions to searing heat, requires more than just picking a grade off a shelf. It demands a holistic approach. In my role at MFY, guiding global clients through these choices, I've seen that success often hinges on a combination of meticulous material selection, thoughtful design, and appropriate manufacturing or post-fabrication treatments. For instance, for a client in India dealing with high-temperature exhaust gases, we didn't just supply a heat-resistant grade; we also discussed design allowances for thermal expansion and the importance of weld procedures that maintain the material's integrity. Similarly, for cryogenic applications in Southeast Asia, ensuring the cleanliness and specific compositional controls of the 304L or 316L pipes5 was paramount. These strategies aren't just about preventing failure; they're about maximizing the service life and reliability of the entire system. It's about engineering resilience into the application from the ground up, leveraging the inherent strengths of stainless steel while mitigating its potential vulnerabilities at extreme temperatures.
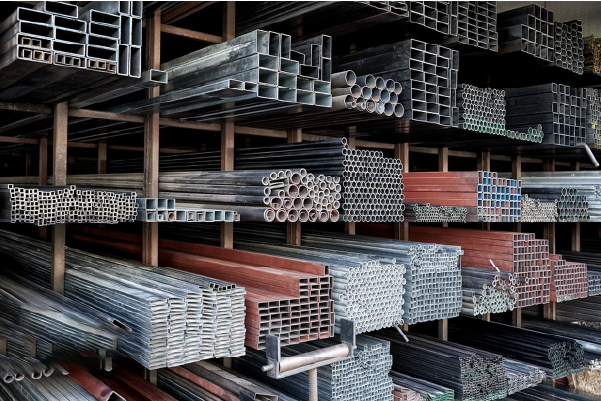
Optimizing the performance of stainless steel pipes in environments characterized by extreme temperatures—be it the icy grip of -200°C or the intense heat approaching 800°C—is a multifaceted challenge that goes beyond simple material specification. It involves a strategic blend of material science, engineering design, and operational diligence. At MFY, with our integrated supply chain and deep expertise in stainless steel production and application, we actively work with our clients, from manufacturing firms to engineering contractors, to implement these strategies. The goal is always to achieve maximum durability, safety, and cost-effectiveness. Let’s explore some of the key strategies that can significantly enhance the performance of stainless steel pipes under such demanding conditions.
Advanced Material Selection and Alloying
The cornerstone of high performance at extreme temperatures is selecting the right stainless steel grade. This means going beyond standard grades for many applications. For high-temperature service (approaching 800°C and beyond), this involves choosing grades with higher chromium and nickel content, such as 309S, 310S, or more specialized alloys6 if conditions are particularly severe. These elements enhance oxidation resistance (chromium) and high-temperature strength/creep resistance (nickel, along with elements like molybdenum, nitrogen, and controlled carbon). For instance, 310S, with approximately 25% Cr and 20% Ni, offers excellent resistance to oxidation and good strength at temperatures up to 1100°C in intermittent service. Using 'H' grades (e.g., 304H, 316H, 321H, 347H) with controlled higher carbon content (0.04-0.10%) and solution annealing at higher temperatures provides improved creep strength for applications above 500-550°C. One of our clients, a manufacturer of industrial furnaces, saw a significant improvement in component lifespan by switching from a standard 304 to 310S for elements operating continuously near 800°C, based on MFY’s recommendation.
For cryogenic applications (down to -200°C and lower), austenitic stainless steels like 304, 304L, 316, and 316L are standard due to their excellent toughness. Here, strategies involve ensuring low carbon content ('L' grades) to prevent sensitization if any welding is followed by stress relief in the critical range (though this is rare for cryo parts), and controlling impurities like sulfur and phosphorus, which can impair toughness. Nitrogen alloying can also be beneficial in austenitic steels for enhancing strength at both room and cryogenic temperatures without significantly sacrificing toughness. MFY ensures that stainless steel pipes destined for cryogenic service meet stringent compositional and mechanical property requirements, including Charpy V-notch impact testing at the specified low temperature (e.g., -196°C for liquid nitrogen service).
Preventing sensitization during high-temperature exposure (450-850°C) is critical. The primary strategies are using low-carbon 'L' grades (e.g., 304L, 316L), where the reduced carbon content limits chromium carbide formation, or using stabilized grades like 321 (titanium-stabilized) or 347 (niobium/tantalum-stabilized). These stabilizing elements preferentially form carbides, leaving chromium in solution to maintain corrosion resistance. This is vital for welded components that operate in or pass through this temperature range.
Optimized Design and Engineering Practices
Material selection alone is not a panacea. System design plays an equally crucial role. For high-temperature applications, accommodating thermal expansion is critical. Austenitic stainless steels have a relatively high coefficient of thermal expansion (around 17-18 µm/m°C). A long pipe run heated to 800°C can expand significantly. Designs must incorporate expansion joints, loops, or bellows to prevent excessive thermal stresses that could lead to buckling, distortion, or fatigue failure. Furthermore, support systems must allow for this movement while adequately supporting the pipe's weight, which is also affected by reduced yield strength at high temperatures. We always advise our engineering contractor clients to perform thorough stress analysis considering thermal loads.
In cryogenic systems, insulation is key not only for process efficiency (preventing heat ingress) but also to prevent unwanted side effects like atmospheric moisture condensation and ice formation on uninsulated parts, which can cause corrosion or mechanical damage. Design must also prevent stress concentrations, as these can be initiation points for brittle fracture, even in tough materials, if flaws are present. Smooth transitions and generous radii are good practice.
For all extreme temperature applications, weld procedures are critical. Welding can alter the microstructure and properties of the base metal in the heat-affected zone (HAZ). Using appropriate filler metals (often over-alloyed for high-temp or matching for cryo), controlling heat input, and employing proper pre-heat or post-weld heat treatment (PWHT), if required by the specific grade and application, are essential. For example, PWHT might be used to relieve residual stresses or to re-dissolve any carbides formed during welding in certain grades, though for many austenitic steels used at extremes, PWHT may not be needed or could even be detrimental if not done correctly (e.g., causing sensitization or sigma phase). MFY provides detailed material data to help clients develop optimal welding protocols for our stainless steel pipes.
Surface Treatments and Protective Coatings
While the inherent properties of stainless steel provide significant protection, in some exceptionally aggressive environments or at the very limit of a grade's capability, surface treatments or coatings can offer an additional performance boost. For high-temperature oxidation/corrosion resistance, specialized coatings like aluminizing or chromizing7 can form intermetallic layers that provide enhanced protection beyond what the base stainless steel offers, sometimes allowing a less expensive grade to be used or extending the life of a higher-alloyed one. Ceramic coatings can also act as thermal barriers, reducing the substrate metal's actual temperature and protecting against erosive wear at high temperatures. These are more common in highly specialized applications like gas turbines or advanced furnace components.
For preventing specific types of corrosion that might be exacerbated by temperature, various surface treatments can be applied. Electropolishing, for example, creates a smoother, more passive surface that can improve resistance to product adhesion and certain types of corrosion in food, pharmaceutical, or high-purity applications, which may also see temperature cycling. Passivation treatments, which enhance the natural chromium oxide layer, are standard practice after fabrication or welding to ensure optimal corrosion resistance.
It's important to note that the applicability and effectiveness of coatings and surface treatments are highly dependent on the specific service conditions (temperature, atmosphere, cycling) and the stainless steel grade. Not all coatings are stable or adherent at 800°C, and some can introduce issues like spalling due to differential thermal expansion. As such, these are often considered for niche applications where the base material alone, even an advanced alloy, might not be sufficient, or where a cost-benefit analysis favors a coated solution. MFY typically focuses on providing the optimal base material, but we can advise on compatibility with subsequent treatments our clients might consider.
Below is a table summarizing strategies for performance enhancement:
Strategy Category | Specific Action | Target Temperature Regime | Benefit | Example Grades/Considerations |
---|---|---|---|---|
Material Selection | Choose high Cr & Ni grades, 'H' grades | High Temperature | Improved oxidation & creep resistance, high-temp strength | 310S, 309S, 304H, 316H, 321H, 347H |
Select stable austenitic grades, control impurities, 'L' grades | Cryogenic | Excellent toughness, prevents brittle fracture, maintains ductility | 304L, 316L (low S, P; N-alloying) | |
Use 'L' grades or stabilized grades | High Temp (Sensitization) | Prevents intergranular corrosion | 304L, 316L, 321, 347 | |
Design & Engineering | Incorporate expansion joints/loops, perform stress analysis | High Temperature | Accommodates thermal expansion, prevents overstress | System design, FEA analysis |
Ensure proper insulation, avoid stress concentrators | Cryogenic | Process efficiency, prevents icing, minimizes fracture risk | Insulation design, smooth geometries | |
Develop qualified weld procedures, appropriate filler metals, control heat input | All Extremes | Maintains material integrity in HAZ, ensures sound joints | AWS D1.6, ASME IX, specific procedures | |
Surface Modification | Aluminizing, Chromizing, Ceramic coatings | High Temperature | Enhanced oxidation/corrosion resistance, thermal barrier | Specialized applications |
Electropolishing, Passivation | Varied (esp. cycling) | Improved surface passivity, cleanability, corrosion resistance | Food, pharma, high-purity |
By thoughtfully applying these strategies, users can significantly extend the life and improve the reliability of stainless steel piping systems operating at the challenging ends of the temperature spectrum.
310S resists oxidation at 1100°CTrue
Grade 310S with 25% Cr/20% Ni offers excellent oxidation resistance up to 1100°C in intermittent service.
Standard 304 is ideal for cryogenicsFalse
While standard 304 can be used, 304L with controlled impurities is preferred for cryogenic applications to ensure toughness.
What technological advancements exist to enhance the durability of stainless steel pipes in varied thermal conditions?
Are your current stainless steel pipes falling short under fluctuating or extreme thermal loads? Standard solutions may not suffice as industrial processes become more demanding. The good news is that ongoing technological advancements are continuously pushing the boundaries of stainless steel performance.
Technological advancements include new alloy development (e.g., super-austenitics, duplex steels with enhanced thermal stability), improved manufacturing processes (e.g., precision casting, advanced welding techniques), innovative surface engineering/coatings, and sophisticated non-destructive testing (NDT) for in-service monitoring.
The quest for materials that can reliably withstand ever more demanding thermal conditions is a continuous journey in metallurgy and materials science. At MFY, we are keenly aware that our clients, from equipment integrators to large-scale manufacturing facilities, are always seeking an edge in performance and longevity. While traditional stainless steel grades offer a fantastic baseline, the frontiers are constantly being expanded. I've seen how the introduction of newer alloys, for instance, has solved problems that were once considered intractable with older materials. Think about processes involving highly corrosive media at elevated temperatures or systems requiring exceptional fatigue life under severe thermal cycling. These advancements aren't just incremental; they often represent step-changes in capability, enabling new industrial processes or making existing ones more efficient and safer. This evolution encompasses everything from the very composition of the steel to how it's made, treated, and monitored in service, all aimed at enhancing durability in varied thermal landscapes.
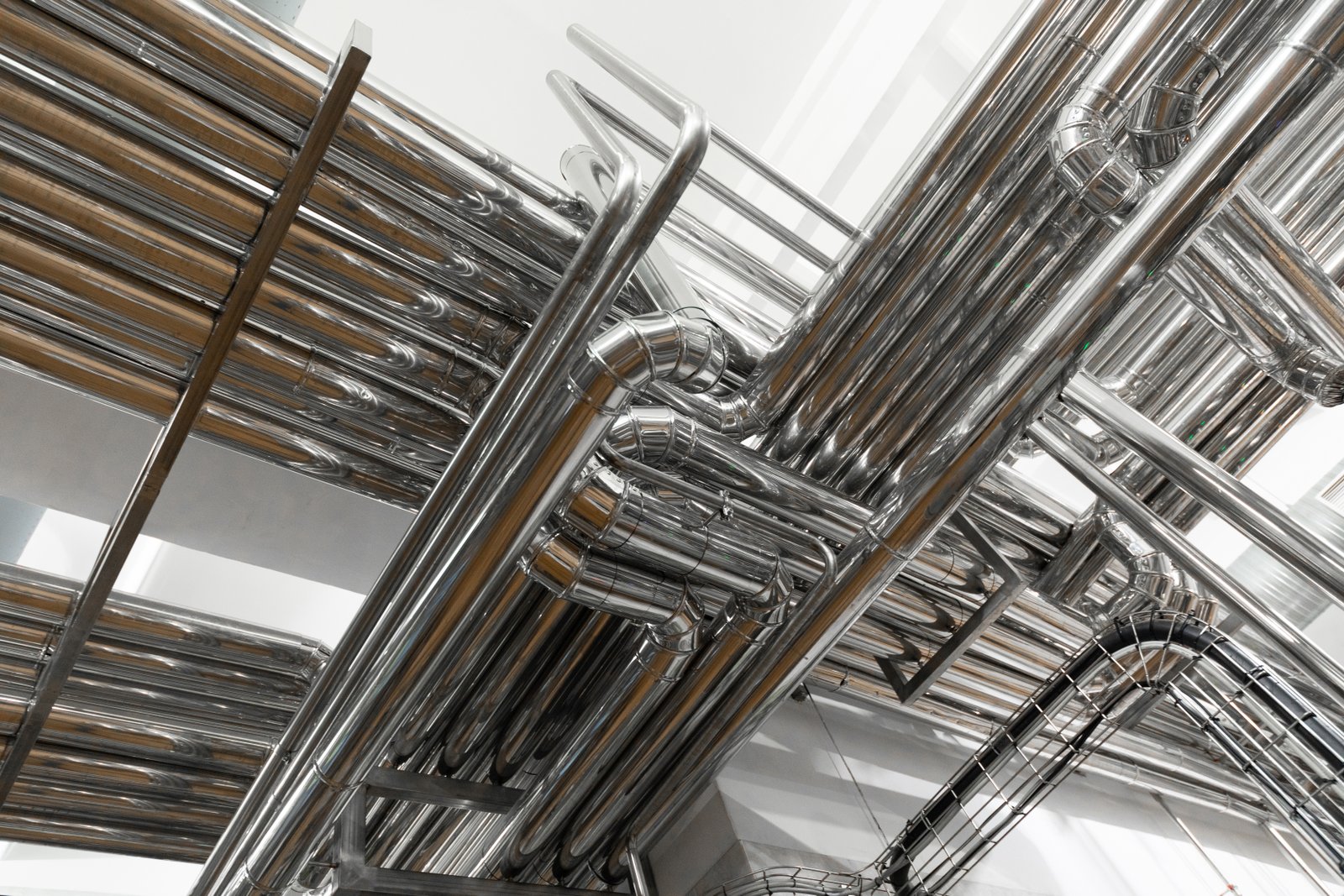
The relentless push for greater efficiency, safety, and operational capability in industries dealing with extreme or varied thermal conditions has spurred significant technological advancements in the realm of stainless steel pipes. These innovations aim to enhance durability, extend service life, and broaden the application window for stainless steels. As a company like MFY, deeply rooted in stainless steel innovation from R&D to digital integration, we closely monitor and often incorporate these advancements to provide our clients with superior products and solutions. The progress is evident across several key areas: alloy development, manufacturing processes, surface engineering, and in-service monitoring and life assessment.
Innovations in Alloy Development and Compositional Control
One of the most impactful areas of advancement is the development of new and improved stainless steel alloys. Super-austenitic stainless steels, for example, contain even higher levels of chromium, nickel, molybdenum, and often nitrogen, compared to standard 300-series grades. Alloys like 6Mo (e.g., UNS S31254) or 254 SMO®8 offer vastly superior resistance to pitting and crevice corrosion, especially in chloride-rich environments, even at elevated temperatures. While their primary driver is corrosion, this enhanced stability often translates to better performance in thermally challenging corrosive environments. For instance, in heat exchangers using seawater as a coolant where process side temperatures are high, super-austenitics can outperform 316L significantly. MFY is equipped to source and process such advanced materials as client needs evolve.
Duplex stainless steels, characterized by a mixed austenite-ferrite microstructure (typically 50/50), offer a compelling combination of high strength (often double that of austenitic grades), good toughness, and excellent resistance to stress corrosion cracking. Newer generations of duplex and super-duplex steels9 have improved weldability and can maintain useful properties over a broader temperature range than earlier versions. While their upper service temperature is generally limited to around 250-320°C due to the risk of embrittlement (sigma phase, 475°C embrittlement in the ferrite), they are excellent for many applications involving moderate heat and corrosive conditions where austenitic grades might suffer from chloride stress corrosion cracking. Their lower nickel content can also offer a price advantage.
There's also ongoing research into nanostructured stainless steels or those with ultra-fine grain sizes. These can exhibit exceptionally high strength and improved fatigue resistance. While widespread commercial application in piping might still be some way off due to manufacturing complexities and cost, the potential for enhanced mechanical performance at various temperatures is significant. Furthermore, precise control over trace elements and impurities during steelmaking, leveraging advanced refining techniques, leads to cleaner steels with more consistent and predictable properties, which is crucial for demanding cryogenic or high-temperature applications.
Advanced Manufacturing and Fabrication Techniques
How stainless steel pipes are made and fabricated has also seen significant progress. Advanced welding technologies such as laser beam welding, electron beam welding, and friction stir welding offer more precise control over heat input, leading to narrower heat-affected zones (HAZs), reduced distortion, and potentially improved mechanical properties and corrosion resistance in the welded joint. For instance, reduced heat input can be beneficial in minimizing sensitization in austenitic steels or preserving the carefully balanced microstructure of duplex steels. While not universally applied for all piping due to cost and setup, these techniques are increasingly used for critical components or specialized applications. MFY emphasizes quality in its tube manufacturing processes, incorporating best practices to ensure weld integrity.
Powder metallurgy (PM) and additive manufacturing (AM), or 3D printing, are emerging as transformative technologies for producing complex stainless steel components, potentially including specialized pipe fittings or customized sections. AM allows for intricate geometries that are difficult or impossible to achieve with traditional methods, and can also enable the creation of functionally graded materials where composition varies across a component to optimize properties for different thermal zones. While still evolving for large-scale piping, the potential to create bespoke solutions for extreme temperature applications with optimized material usage is immense. For example, AM could be used to create integrated cooling channels within a high-temperature pipe wall.
Improvements in seamless pipe manufacturing and precision cold-rolling and drawing processes for welded pipes also contribute to enhanced durability. Tighter dimensional tolerances, improved surface finishes, and more consistent microstructures translate to better performance under thermal stress and fatigue conditions. At MFY, our investment in cold-rolling processing is part of this commitment to quality and precision.
Sophisticated Surface Engineering and Intelligent Monitoring
Surface engineering continues to evolve beyond traditional coatings. Advanced PVD (Physical Vapor Deposition) and CVD (Chemical Vapor Deposition) coatings can apply very thin, highly adherent layers of ceramics (e.g., TiN, CrN, Al₂O₃) or other metallic alloys to enhance wear resistance, oxidation resistance, or reduce friction at various temperatures. Some of these coatings are engineered to be stable at very high temperatures. Thermal spray coatings (like plasma spray or HVOF - High-Velocity Oxygen Fuel) can deposit thicker protective layers, often used to combat severe erosion-corrosion at elevated temperatures. The challenge often lies in ensuring good adhesion and matching thermal expansion coefficients to prevent spalling during thermal cycling.
A significant leap forward is the integration of sensor technology and data analytics for in-service monitoring and predictive maintenance. Embedding sensors (e.g., fiber optic sensors for temperature and strain, ultrasonic transducers) within or on pipes can provide real-time data on operating conditions and material degradation. This data, when fed into AI-powered predictive maintenance models, can help anticipate failures, optimize inspection schedules, and extend the safe operating life of piping systems. For example, monitoring creep strain in high-temperature pipes or detecting acoustic emissions from crack growth can provide early warnings. MFY's own embrace of digital innovation aligns with this trend, recognizing that the future of material performance lies in intelligent systems.
Advanced Non-Destructive Testing (NDT) techniques are also crucial. Phased array ultrasonic testing (PAUT), eddy current testing with advanced probes, and digital radiography allow for more accurate and comprehensive inspection of pipes for flaws, corrosion, or microstructural changes both during manufacturing and in-service, without damaging the component. This enables earlier detection of potential issues related to thermal degradation, ensuring timely intervention.
The table below highlights some key technological advancements:
Advancement Category | Specific Technology/Innovation | Benefit for Thermal Durability | Example Impact |
---|---|---|---|
Alloy Development | Super-Austenitic & High-Mo Alloys (e.g., 6Mo, S31254) | Enhanced corrosion resistance at elevated temps, improved stability | Use in aggressive chemical/seawater heat exchangers with high process temps |
Advanced Duplex/Super-Duplex Steels | High strength, good toughness, SCC resistance; improved temp range over older versions | Structural applications in moderately hot, corrosive environments (e.g., <300°C) | |
Nanostructured/Ultra-Fine Grain Steels | Potential for superior strength, fatigue resistance | Future applications requiring extreme mechanical performance across temperatures | |
Manufacturing | Advanced Welding (Laser, EBW, Friction Stir) | Reduced HAZ, lower distortion, improved joint properties | Critical welds in high-performance or specialized pipe systems |
Additive Manufacturing (3D Printing) / Powder Metallurgy | Complex geometries, functionally graded materials, customized parts | Bespoke solutions for extreme thermal zones, integrated cooling features | |
Surface Engineering | Advanced PVD/CVD Coatings (Ceramics, Alloys) | Enhanced wear, oxidation, corrosion resistance at high temps | Protection for components in highly erosive/corrosive hot gas streams |
Monitoring & NDT | Embedded Sensors & Predictive Maintenance (AI) | Real-time monitoring of degradation, early failure warning, optimized life | Predicting creep life in high-temp pipes, detecting thermal fatigue cracks |
Advanced NDT (PAUT, Advanced Eddy Current) | More accurate and comprehensive flaw detection, material characterization | Improved quality control, more reliable in-service inspection for thermally induced damage |
These technological strides ensure that stainless steel pipes will continue to be a go-to solution for even more demanding thermal applications in the future, offering enhanced durability and reliability. MFY is committed to being at the forefront of leveraging these innovations for our global clientele.
Super-austenitics resist chloride corrosionTrue
Super-austenitic stainless steels like UNS S31254 contain higher chromium/nickel/molybdenum, providing exceptional pitting resistance in chloride environments even at elevated temperatures.
Duplex steels work above 400°CFalse
Duplex stainless steels are typically limited to 250-320°C service due to risks of sigma phase embrittlement and 475°C embrittlement in the ferrite phase.
Conclusion
Stainless steel pipes offer exceptional performance from -200°C to 800°C due to tailored alloying and stable microstructures. Proper grade selection, design, and new technologies ensure their durability in diverse industrial applications, making them a reliable choice for extreme thermal conditions.
-
Discover the role of alloy composition in enhancing stainless steel's temperature resilience ↩
-
Discover industrial applications for stainless steel pipes in diverse ↩
-
Learn about the temperature risk zone for intergranular corrosion in 304L grade ↩
-
Understand the operational temperature limits for 304 steel in high-temperature environments ↩
-
Learn about the toughness and composition control in 304L and 316L for cryogenics. ↩
-
Know the oxidation resistance and high-temp strength of 309S and 310S alloys. ↩
-
Discover how aluminizing or chromizing coatings offer enhanced surface protection. ↩
-
Discover why 6Mo is preferred for high-temperature, corrosive environments ↩
-
Learn how duplex steels are optimized for broader temperature applications ↩
Have Questions or Need More Information?
Get in touch with us for personalized assistance and expert advice.