ASTM A240 Plate Tolerance Chart Explained
Struggling with stainless steel plates that don't fit your project specifications precisely? These dimensional mismatches, often stemming from poor tolerance control, can lead to costly project delays, material wastage, and significant budget overruns. Understanding the ASTM A240 tolerance chart is your first step toward ensuring every single plate fits exactly as designed.
The ASTM A240 plate tolerance chart is a technical standard that outlines the acceptable dimensional variations for chromium and chromium-nickel stainless steel plates. It covers key parameters like thickness, width, length, flatness, and camber, ensuring material consistency and interchangeability for predictable fabrication and structural reliability.
Getting these tolerances right isn't just about meeting a requirement on paper; it's a fundamental pillar of your project's success. Throughout my career at MFY, I’ve repeatedly seen how a thorough grasp of these specifications prevents the kinds of costly, last-minute errors that can jeopardize a timeline. Let's delve into why these figures are far more than just numbers on a chart.
This standard is more than a quality control document; it's the universal language of precision in the global steel trade1. For an international supplier like MFY, it ensures that the plate we produce in China meets the exact requirements of an engineering contractor in India or a fabricator in the Middle East. This shared understanding of acceptable deviation is what makes global supply chains possible. It allows engineers to design with confidence, knowing the material they specify will behave as expected, and it allows us, the producers, to deliver on that promise of quality and reliability.
What are the key features of the ASTM A240 plate tolerance chart?
Ever received a steel plate that was frustratingly thicker on one end than the other? This inconsistency can completely derail your fabrication process, leading to misaligned joints, weld gaps, and critical structural weak points. The ASTM A240 chart tackles this by providing clear, specific limits for every key dimension.
The primary features of the ASTM A240 tolerance chart are the defined permissible variations for plate dimensions. These include specific allowances for thickness, width, length, camber (the straightness of an edge), and flatness. These tolerances are crucial for ensuring the material's uniformity and suitability.
I recall a case with a valued client, a large engineering contractor in Southeast Asia responsible for building a series of chemical storage tanks. They came to us after facing significant setbacks with a previous supplier. The plates they had received had inconsistent thickness and poor flatness, causing major fit-up issues during automated welding. The welders had to manually correct gaps, which not only tripled the labor time but also introduced potential stress points along the seams—a critical risk for a pressure-rated vessel. This experience was a stark reminder that the specifications within the ASTM A240 chart aren't just guidelines; they are the bedrock of safe and efficient construction. Understanding these features in detail is the first step to avoiding such costly complications and ensuring the integrity of your final product.
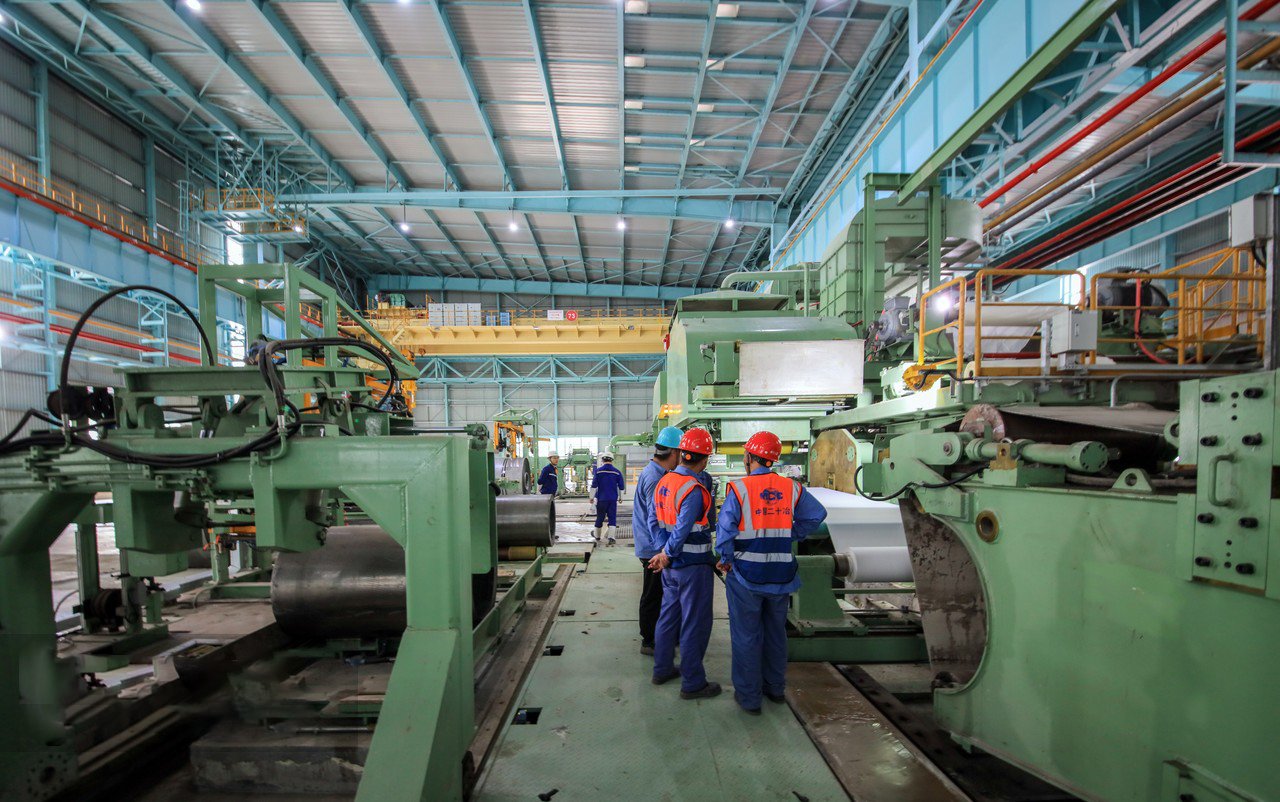
The challenge my client faced is a perfect illustration of why a deep dive into the specifics of ASTM A240 is essential for anyone in the manufacturing or construction sectors. It's not enough to simply know that tolerances exist; one must understand how each specified parameter functions to guarantee quality. These standards are meticulously designed to control the physical characteristics of the plate, ensuring that when it arrives at your facility, it behaves exactly as your engineers and designers intended. The chart provides a framework that governs the entire production process, from the initial hot rolling to the final finishing passes. For us at MFY, our integrated supply chain allows for rigorous oversight at every stage, ensuring that the final product adheres strictly to these standards. This control is what gives our clients peace of mind, knowing that the material they receive will be consistent, reliable, and ready for immediate, hassle-free integration into their projects. The chart is effectively a contract of quality between the manufacturer and the end-user, and honoring that contract is a responsibility we take very seriously.
Understanding Thickness and Weight Tolerances
The most fundamental tolerance in the ASTM A240 standard is thickness. It is typically specified as a permissible percentage deviation from the nominal thickness or, for thinner plates, as a fixed undersize tolerance. For example, a stainless steel plate with a nominal thickness of 1 inch (25.4 mm) might have a thickness tolerance of -0.01 inches, meaning it can be no thinner than 0.99 inches, with an over-tolerance governed by weight. This is critical because plate is often sold by weight, but engineered for its thickness. Exceeding the allowable weight tolerance can lead to unexpected cost increases, while falling below the thickness minimum compromises structural integrity.
This was precisely the issue for my client in Southeast Asia. The plates from their previous supplier were technically within the weight tolerance but were thinner than the minimum specified thickness in several areas. This meant they paid for steel they couldn't structurally rely on. When we supplied them with our MFY plates, our precision cold-rolling process2 ensured a uniform thickness across the entire plate, well within the -0.01" specification. This not only guaranteed the required structural strength for their tanks but also made their project cost calculations far more accurate and predictable.
The impact extends directly to engineering calculations. When designing a pressure vessel or a structural beam, engineers base their load calculations on the minimum required thickness. If a supplier provides a plate that dips below this minimum, even in small patches, the entire component's safety factor is compromised. For this reason, reputable manufacturers like MFY aim for the nominal thickness, ensuring any variation stays comfortably above the minimum threshold. This commitment to precision is a non-negotiable aspect of our production philosophy, as we understand its direct correlation to the safety and longevity of our clients' projects.
Navigating Width and Length Tolerances
Width and length tolerances ensure that the plate you order is the size you receive, preventing costly trimming or scrap. The ASTM A240 standard specifies these tolerances based on the plate's dimensions. For a standard mill plate, there might be an "over-tolerance" only, meaning the plate will be at least the specified size, but could be slightly larger. For applications requiring high precision, one can specify a "resquared" plate, which has much tighter tolerances on all four sides.
For projects involving automated cutting or assembly, these tolerances are paramount. If a plate arrives wider or longer than the maximum tolerance allows, it can jam machinery or fail to fit into a pre-designed assembly jig. Conversely, a plate that is too small results in gaps that may be impossible to resolve without ordering new material, causing significant delays. Here’s a simple comparison to illustrate the difference:
Tolerance Type | Typical Width/Length Allowance (for a 1" thick, 48" x 96" plate) | Best For |
---|---|---|
Standard Mill Edge | +1/4" to +1/2" over specified dimension | General fabrication where some on-site trimming is acceptable. |
Resquared Edge | +/- 1/16" on specified dimension | High-precision applications like CNC cutting, architectural panels, or automated assembly lines. |
In my client's tank project, the circular shell sections were designed to be rolled from rectangular plates. The inconsistent dimensions from their initial supplier meant that after rolling, the cylinder heights didn't match up perfectly. This created a "stair-step" effect where the shell courses met, complicating the crucial vertical welds. When we supplied them with plates cut to a tighter tolerance, the rolled sections aligned perfectly, drastically improving both the speed and quality of their welding process. This precision is a direct result of MFY's advanced processing capabilities and our commitment to understanding the end-use of our products.
The Critical Importance of Flatness and Camber
Flatness and camber are tolerances that define a plate's shape, and they are arguably among the most critical for modern fabrication. Flatness refers to the deviation from a perfectly flat plane, often seen as waves or buckles in the plate. Camber refers to the deviation of a side edge from a straight line. ASTM A240 provides specific tables to define the maximum allowable deviation for both, based on the plate's thickness and dimensions. A lack of flatness can make it impossible for vacuum or magnetic lifters to handle the plate, and it can cause the material to shift or rock during CNC plasma or laser cutting, resulting in inaccurate parts.
The issues my Southeast Asian client faced with automated welding were directly linked to poor flatness. The wavy plates would not sit flush against each other, creating variable gaps along the weld seam. An automated welding robot is programmed for a consistent, minimal gap; when it encounters a large, variable one, it can result in incomplete penetration or excessive burn-through, creating a defective weld that must be manually reworked. This single issue, stemming from poor flatness control, became the biggest bottleneck in their entire production line.
At MFY, we utilize advanced leveling techniques, such as temper passing and tension leveling, during our cold-rolling process. These methods apply controlled pressure and tension to the steel to ensure it meets strict flatness tolerances. For applications like architectural facades, machine beds, or any project where visual perfection and precise assembly are key, superior flatness is non-negotiable. By controlling for flatness and camber, we don't just supply a piece of steel; we provide a component that is optimized for our clients' downstream manufacturing processes, saving them time, reducing rework, and ensuring a higher quality final product.
How do these tolerance specifications affect material performance?
Considering how a plate's dimensions impact more than just its physical fit is crucial. Deviations from specified tolerances can significantly affect everything from the quality of welds and corrosion resistance to the overall structural stability of the final assembly. So, how does adherence to ASTM A2403 directly translate into predictable and reliable material performance?
Tolerance specifications directly influence material performance by guaranteeing uniform stress distribution, predictable welding behavior, and consistent structural integrity. Adhering to these tolerances prevents the creation of weak points, improves the fit-up for stronger joints, and ensures the final product behaves exactly as engineered under load.
The connection between a number on a chart and the real-world performance of a massive structure becomes incredibly clear when you see the consequences of failure. A plate that is too thin in one area creates a localized stress concentration, a weak link in the chain that can become a catastrophic failure point under pressure or load. This isn't theoretical; it's a fundamental principle of mechanical engineering stress concentration4. When we at MFY produce a plate, our quality control isn't just about passing a gauge test. It's about upholding our responsibility to the safety and success of the project it's destined for. Our fully integrated production model, from raw material sourcing to final finishing, gives us granular control over these tolerances. This ensures that the performance we promise is the performance our clients receive, whether they are building a bridge, a chemical tank, or a high-tech piece of equipment.

This principle of "tolerance equals performance" is a core tenet of our work at MFY. When a client specifies a grade of stainless steel, like 304L or 316L5, they are choosing it for its known mechanical properties and corrosion resistance. However, these properties are only guaranteed if the material's physical form is also correct. For instance, the load-bearing capacity of a structural component is calculated based on its cross-sectional area, which is directly determined by its thickness and width. If the thickness is below the minimum tolerance, the component simply cannot carry its designed load, regardless of the steel's intrinsic strength. This is why we invest so heavily in state-of-the-art rolling mills and leveling equipment—to ensure that the material’s performance isn't compromised by dimensional inconsistency. We see it as our duty to deliver a product where the theoretical properties listed on a data sheet are fully realized in its physical form.
The Link Between Tolerance and Structural Integrity
The most direct impact of plate tolerance on performance is in structural integrity. In any load-bearing application, from a building's support beam to a pressure vessel's wall, engineers design based on the material's minimum guaranteed thickness. According to a study published in the Journal of Constructional Steel Research, even a 5% deviation below the specified minimum thickness in a structural element can lead to a disproportionate increase in localized stress, sometimes by as much as 15-20% under certain load conditions. This creates a hidden weak point that compromises the safety factor of the entire design.
When a plate has inconsistent thickness, the load it bears is no longer distributed evenly across its surface. The thinner sections are subjected to higher stress than the surrounding material. Over time, under cyclic loading or high pressure, this stress concentration can become the initiation point for fatigue cracks or catastrophic failure. This is why standards like ASTM A240 are so unforgiving on minimum thickness.
At MFY, our process control is designed to produce plates with a highly uniform thickness, minimizing this risk. By using advanced gauge control systems in our mills, we can ensure that the plate delivered is consistent, allowing engineers to have full confidence that their safety margins are maintained and the structure will perform as designed for its entire service life. We aren't just selling steel; we are selling predictability and safety.
Ensuring Predictable Weldability and Fabrication Speed
In modern fabrication, especially with the rise of automation, tolerance is synonymous with efficiency. Welding, whether performed by a robot or a skilled human, relies on a consistent and predictable fit-up between the parts being joined. According to the American Welding Society (AWS), poor fit-up caused by dimensional deviations is one of the leading causes of weld defects. When a gap between two plates is too large due to width or flatness issues, it requires excessive filler metal, increases welding time, and raises the risk of defects like lack of fusion or undercut.
Consider an automated welding process for a large pipe. The robot is programmed with specific parameters for travel speed and wire feed rate, all based on a precise, uniform V-groove. If a plate's inconsistent flatness creates a variable gap, the robot cannot adapt. The result is a flawed weld that requires a human to grind it out and repair it manually, completely negating the benefits of automation. This was the exact scenario my client in Southeast Asia faced, where poor flatness from their previous supplier turned their efficient automated line into a slow, manual repair station.
By providing plates that adhere strictly to ASTM A240 flatness and dimensional tolerances, we give our clients the consistency they need for modern manufacturing. Our plates fit together precisely, minimizing gaps and enabling faster, higher-quality welds. This directly translates to increased throughput, lower labor costs, and a superior final product for our customers. This is a clear example of how investing in quality material upfront pays significant dividends on the workshop floor.
Impact on Corrosion Resistance and Service Life
While less obvious than structural integrity, plate tolerance can also have a subtle but significant impact on corrosion resistance and overall service life. The manufacturing processes used to achieve tight tolerances, such as precision cold rolling and advanced leveling, also contribute to a smoother, more uniform surface finish. A plate with a poor surface finish and internal stresses from improper rolling can have microscopic inconsistencies that compromise the passive layer on stainless steel—the thin chromium oxide film that gives stainless steel its corrosion resistance.
Industry research, particularly in the chemical processing and marine sectors, has shown that surface imperfections can become initiation sites for localized corrosion, such as pitting or crevice corrosion. For a client in the Middle East using stainless steel for a desalination plant, for example, this is a critical concern. The high-chloride environment is extremely aggressive, and any weak point in the material's surface can lead to premature failure.
Therefore, our focus at MFY on tight tolerance control is part of a holistic approach to quality. The same processes that ensure a plate is flat and dimensionally accurate also help create a defect-free surface with low residual stress. This enhances the material's natural ability to resist corrosion, ensuring a longer and more reliable service life. By delivering a plate that is superior both dimensionally and metallurgically, we provide our clients with a product that will not only fit their design but will also stand the test of time, even in the most demanding environments.
What factors influence the variations in plate tolerances specified by ASTM A240?
Have you ever wondered why tolerances for a thin, narrow plate are different from those for a thick, wide one? The variations aren't arbitrary; they are based on the physics of steel production. The specified tolerances in ASTM A2406 are influenced by a combination of factors.
The primary factors influencing ASTM A240 plate tolerance variations are the material's thickness, width, and the production process itself. Thicker and wider plates naturally exhibit more variation due to the immense forces and thermal effects involved in rolling, leading to more generous tolerances.
Understanding these influencing factors is key for both producers and users. For us at MFY, it dictates the machinery, processes, and quality control measures we need to implement. For our clients, it helps them set realistic expectations and specify the right plate for their application. For example, knowing that a very wide plate will have a looser flatness tolerance might lead an engineer to design a project using multiple, narrower plates instead to achieve a flatter final surface. It’s a collaborative process informed by the realities of manufacturing.

The entire steel rolling process is a battle against the laws of physics. When a massive slab of steel, heated to over 1,200°C, is passed through powerful rollers, it doesn't behave like soft clay. The immense pressures can cause the rollers themselves to deflect slightly in the middle, a phenomenon known as "roll bending." This can result in a plate that is slightly thicker in the center than at the edges. Similarly, as the plate cools, thermal stresses can cause it to warp or buckle, affecting flatness. The specifications in ASTM A240 are a pragmatic acknowledgment of these manufacturing realities. They represent a balance between the ideal of a perfectly uniform plate and what is practically and economically achievable with modern production technology. At MFY, our continuous investment in advanced technology, like work roll shifting and dynamic cooling systems, is all aimed at fighting these physical tendencies to produce plates that are as close to perfect as possible.
The Role of Plate Thickness and Width
The single greatest factor influencing tolerance specifications is the nominal dimension of the plate itself. As a plate gets thicker, the forces required to reduce its thickness increase exponentially. This makes it more difficult to maintain a consistent thickness across its entire width and length. Consequently, ASTM A240 allows for greater variation in thicker plates compared to thinner sheets. For example, the permissible thickness variation for a 3/16" plate is significantly tighter than for a 3" plate.
Similarly, the width of the plate plays a crucial role. As mentioned, the rollers used in a mill can flex under pressure. This effect is more pronounced on wider plates, making it harder to maintain uniform thickness from edge to edge. This also impacts flatness. A wider plate has more surface area to be affected by uneven cooling, which can introduce waves or buckles. Therefore, the ASTM A240 flatness tolerance tables show a direct correlation: as the width and length increase, the allowable deviation from perfect flatness also increases.
For a practical example, a client manufacturing long, slender conveyor belts required extremely high straightness (camber). They initially wanted to use the widest plate possible to minimize longitudinal welds. However, after consulting with our technical team, they understood that by opting for narrower plates, they could achieve a much tighter camber tolerance as specified by ASTM A240. This decision, guided by an understanding of how dimension influences tolerance, ultimately resulted in a better-performing final product.
Impact of Production Methods: Hot Rolling vs. Cold Rolling
The manufacturing process is another key determinant of achievable tolerances. The vast majority of stainless steel plate begins its life as a hot-rolled product7. Hot rolling, done at high temperatures where steel is more malleable, is an efficient way to achieve the basic shape and thickness. However, the process is less precise. The high temperatures and subsequent cooling lead to scale formation on the surface and greater dimensional variability. Hot-rolled plates, therefore, generally have more generous tolerances.
Cold rolling, in contrast, is performed at or near room temperature. After the initial hot rolling and annealing, the plate is passed through another set of rollers to reduce its thickness further. This process requires much more force but allows for exceptionally tight control over the final thickness and surface finish. Tolerances for cold-rolled products are significantly tighter than for hot-rolled ones. For instance, a cold-rolled sheet will have a much more uniform thickness and a superior surface finish compared to a hot-rolled plate of the same nominal thickness.
At MFY, our integrated capabilities allow us to leverage both processes. We start with high-quality hot-rolled material and then utilize our advanced cold-rolling facilities for applications that demand higher precision. This flexibility allows us to provide the most cost-effective solution for our clients. If a project can accommodate hot-rolled tolerances, we provide that. If it requires the precision of cold-rolled plate, we have the capability to deliver that as well, ensuring the material is perfectly matched to the application's needs.
Influence of Material Grade and Alloy Composition
ly, the specific alloy of stainless steel can influence tolerances, albeit more subtly than dimension or production method. Different alloys have different mechanical properties at rolling temperatures. Some alloys are "stiffer" or less malleable than others, meaning they resist deformation more. For example, duplex stainless steels, which have a mixed austenitic-ferritic microstructure, are significantly stronger than standard austenitic grades like 304L at both high and room temperatures.
This higher strength means that more force is required to roll duplex grades, which can lead to greater roll deflection and slightly more variation in the final product. While ASTM A240 generally provides a single set of tolerances for a wide range of chromium and chromium-nickel steels, manufacturers must account for these material-specific behaviors in their process controls. The heat treatment process (annealing) required to soften the material and stabilize its microstructure also differs between alloys and can affect the final flatness.
This is where deep material expertise becomes critical. When a client specifies a high-strength or specialized alloy, our metallurgical team works in tandem with our production engineers to fine-tune the rolling and annealing parameters. This proactive approach ensures that even with more challenging materials, we can consistently produce plates that meet the stringent requirements of ASTM A240. It’s a level of expertise that goes beyond simply reading a chart and delves into the fundamental science of the material itself.
How can manufacturers ensure compliance with ASTM A240 tolerances?
Receiving a material certification is one thing, but how do you, as a user, gain confidence in consistent compliance? For manufacturers like us, ensuring every plate meets ASTM A240 standards isn't a final inspection step; it's a philosophy embedded throughout the entire production process.
Manufacturers ensure compliance with ASTM A240 tolerances through a rigorous quality management system that includes advanced process controls, state-of-the-art measurement equipment, and comprehensive operator training. This involves in-line sensors, laser-based scanning, and meticulous final inspections before shipment.
At MFY, this begins with our raw material selection and continues through every stage of rolling, annealing, and finishing. We use automated gauge controls on our mills that continuously monitor and adjust roller pressure in real-time. Laser scanners verify width and camber as the plate is processed, and our leveling equipment is calibrated to achieve flatness standards that often exceed the minimum requirements of ASTM A240. ASTM A240 flatness tolerances and methods It’s this fusion of technology and a robust quality culture that turns the standard from a document into a deliverable reality.
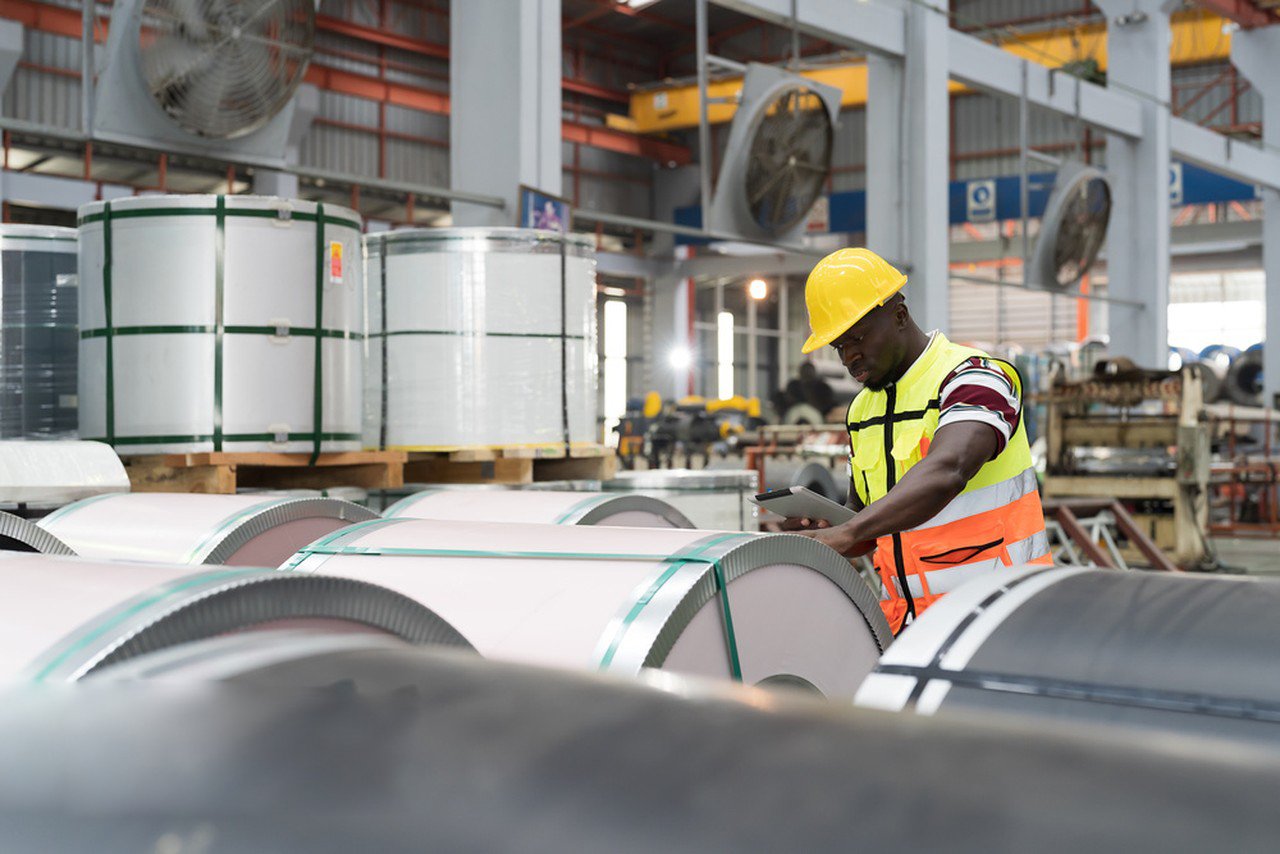
Achieving consistent compliance is a dynamic and multi-faceted endeavor. It's a closed loop of setting standards, manufacturing to those standards, measuring the output, and feeding that data back to refine the process. A simple pass/fail check at the end of the line is insufficient. A truly quality-focused manufacturer aims to control the process so tightly that the output is always centered within the tolerance band, not just barely inside it. This concept, known as statistical process control (SPC), is fundamental to our operations at MFY. We don't just check for defects; we analyze process data to predict and prevent them before they can occur. This proactive approach involves empowering our machine operators with the data and training they need to make micro-adjustments on the fly. It also means regular, certified calibration of all our measurement tools—from simple calipers to sophisticated laser scanners—to ensure that the data we rely on is impeccably accurate. This deep-seated commitment to process control is what allows us to confidently certify every plate we ship.
Implementing Advanced Process Control (APC) Systems
The foundation of modern tolerance compliance lies in advanced process control8. In a steel mill, this means integrating sophisticated sensors and feedback loops directly into the production line. For thickness control, modern mills use Automatic Gauge Control (AGC) systems9. These systems employ X-ray or isotope-based sensors to measure the plate's thickness in real-time as it exits the rollers. This data is instantly fed back to the hydraulic actuators that control the roll gap, making micro-adjustments thousands of times per second to maintain a consistent thickness.
Similarly, for flatness, systems often use laser-based shape meters that scan the entire width of the plate. This creates a topographical map of the plate's surface, identifying any waves or buckles. This information is then used to control specific zones in the leveling equipment or cooling sprays, selectively applying pressure or cooling to create a perfectly flat product.
At MFY, our investment in these APC systems is a cornerstone of our quality promise. It allows us to move from a reactive "inspect and reject" model to a proactive "predict and prevent" one. By controlling the process with such high precision, we ensure that the vast majority of our production is already well within ASTM A240 specifications, making the final inspection a verification of quality rather than a search for defects. A 2021 report by the Association for Iron & Steel Technology highlighted that mills with integrated APC systems see a reduction in out-of-spec material by over 60% compared to those relying solely on manual controls.
Rigorous Calibration and Measurement Protocols
Technology is only as good as its calibration. A manufacturer can have the most advanced sensors in the world, but if they aren't calibrated correctly, the data they produce is meaningless. Ensuring ASTM A240 compliance requires a meticulous and non-negotiable protocol for equipment calibration and measurement verification. This means that all measurement devices, from the operator's handheld micrometer to the in-line laser scanners, must be regularly calibrated against traceable national or international standards.
This process involves creating a calibration schedule, keeping detailed records, and having dedicated personnel trained in metrology (the science of measurement). At our facilities, for example, our quality assurance team performs daily checks on key equipment and contracts third-party specialists for certified annual calibrations. This ensures our measurements are not only precise but also legally and technically defensible.
Furthermore, the measurement protocol itself is standardized. We have clear work instructions on exactly where and how to measure a plate for thickness, width, length, and flatness. For example, ASTM A240 specifies that thickness should be measured at least 3/8" from the edge. Our internal protocols are even stricter to guarantee compliance. This disciplined approach ensures that whether a plate is measured in our facility in China or at our client's site in Russia, the results will be consistent and reliable.
Comprehensive Workforce Training and Quality Culture
Ultimately, compliance is driven by people. The most sophisticated machinery can fail if the operator is not properly trained or motivated to prioritize quality. Therefore, a core component of ensuring compliance is building a deep-rooted quality culture, supported by continuous and comprehensive workforce training. The importance of workforce training in manufacturing quality10 This starts with educating every team member—from the furnace operator to the shipping coordinator—on the importance of tolerances and the specific requirements of standards like ASTM A240.
Training goes beyond simply teaching how to operate a machine. It involves teaching operators how to interpret SPC data, how to spot the early signs of a process drifting out of spec, and empowering them to take corrective action. When an operator understands why flatness is critical for a client's automated welding line, they become a proactive partner in the quality process, not just a machine tender.
I have personally led workshops with our production teams, using case studies—like the challenges faced by my client in Southeast Asia—to illustrate the real-world impact of our work. When our team sees the connection between their actions and our client's success, it fosters a sense of pride and ownership. This human element, this shared commitment to excellence, is the final and most crucial ingredient in ensuring that every plate that leaves our facility with the MFY name on it is a product we can all be proud of.
What are the best practices for using ASTM A240 plates in construction and manufacturing?
You've specified the right material and received high-quality plates that comply with ASTM A240. What's next? Proper handling and utilization are essential to preserve the quality you've paid for. Adhering to best practices ensures that the plate's built-in tolerances translate to a successful project outcome.
Best practices for using ASTM A240 plates include proper storage to maintain flatness, verifying dimensions upon receipt, using appropriate cutting and welding techniques to minimize distortion, and consulting with your supplier to match the right tolerance level to the specific application's requirements.
From my experience, the most successful projects are those where communication flows freely between the material supplier and the end-user. For example, a client planning to do extensive laser cutting should communicate this to us. We can then ensure we supply a plate with superior flatness, perhaps even from a specific batch known for its laser-cutting performance. This collaborative approach, combined with smart handling on-site, transforms a simple steel plate into a solution perfectly tailored for high performance and efficiency in your specific project.
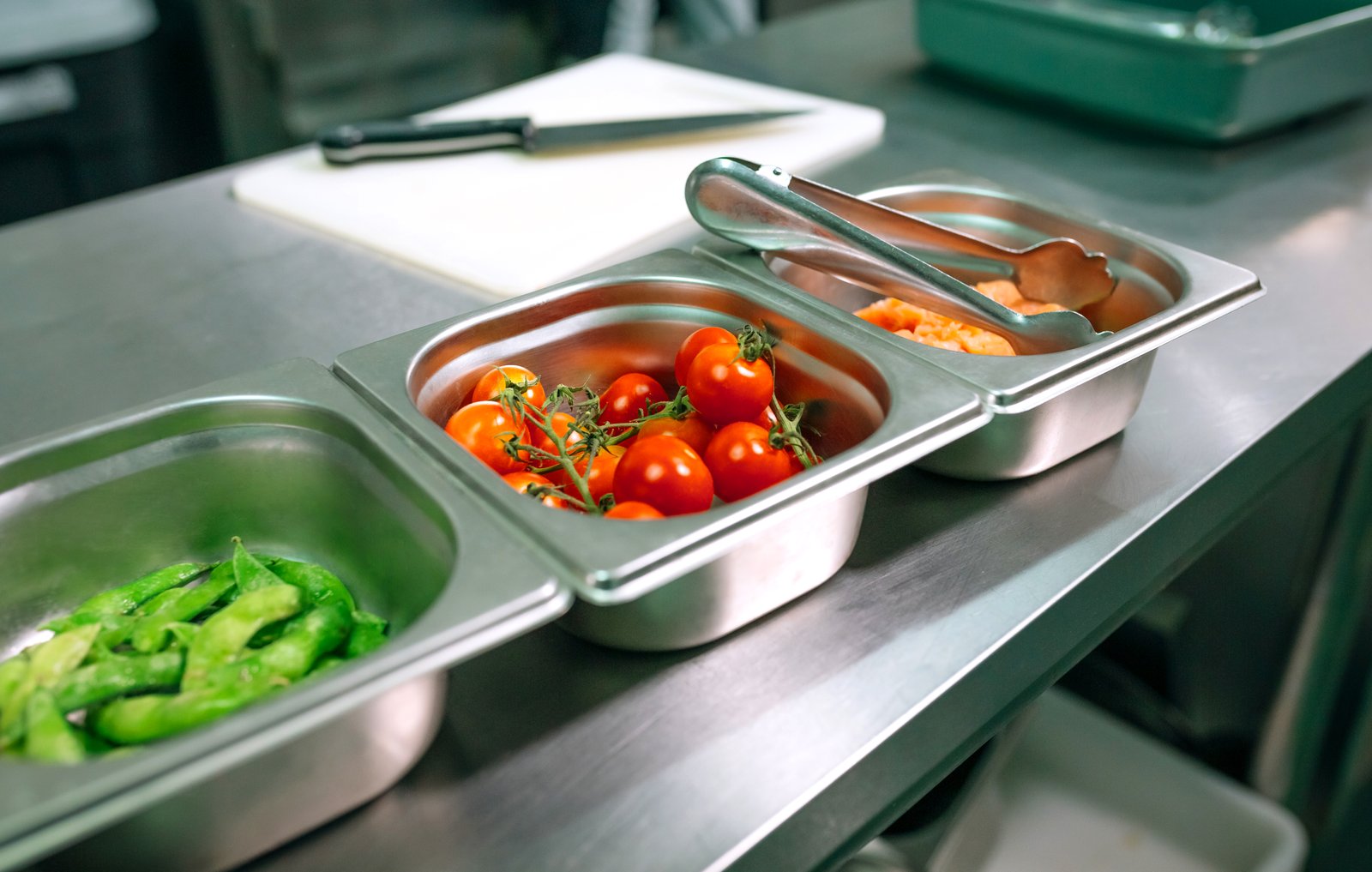
The journey of a steel plate doesn't end when it leaves the mill; in many ways, it's just beginning. The value of a perfectly manufactured plate can be quickly diminished through improper handling, storage, and fabrication11. I've seen instances where plates, delivered perfectly flat, were stored improperly on uneven ground, causing them to develop a permanent bend before they ever reached the workshop. Similarly, using overly aggressive cutting methods or incorrect welding sequences can introduce significant stress and distortion, undoing all the precision work done at the mill. Therefore, implementing best practices is not just a recommendation; it's a critical step in risk management and quality assurance for any project. It ensures that the investment made in high-quality, compliant material pays off in the form of a smooth fabrication process and a durable, reliable final product. At MFY, we often provide our clients with handling and fabrication guidelines to help them protect this investment.
Verification and Incoming Material Inspection
The first best practice begins the moment the material arrives at your facility. Don't assume compliance; verify it. While a reputable supplier like MFY provides a Material Test Report (MTR) certifying compliance with ASTM A240, a simple incoming inspection is a crucial quality assurance step. This doesn't have to be exhaustive for every single plate, but a random sampling protocol should be in place. This involves checking the key dimensions—thickness, width, and length—against the MTR and your purchase order12.
A quick visual inspection for flatness and any potential shipping damage is also essential. Lay the plate on a known flat surface to easily spot any significant buckles or waves. This initial check is your first line of defense. It allows you to identify any potential issues before the plate enters your production workflow, where discovering a problem becomes much more costly and disruptive.
I once worked with a construction contractor who implemented a strict incoming verification process. They found that a small percentage of plates from a previous supplier were consistently just outside the camber tolerance. By catching this upon delivery, they were able to reject the non-compliant material immediately, preventing it from being cut into dozens of incorrect parts, which saved them an estimated week of rework and thousands of dollars in wasted material and labor.
Proper Storage and Handling Techniques
Once the plate is accepted, its quality must be preserved. Stainless steel plates should always be stored flat, on a level surface, with sufficient support (dunnage) to prevent sagging. For stacks of plates, separators should be used to allow air circulation and prevent surface-to-surface contact, which can trap moisture and lead to cosmetic staining or even crevice corrosion over time. The supports should be aligned vertically through the stack to distribute the load evenly.
Handling is equally important. Use lifting equipment with wide, padded slings or appropriate plate clamps to avoid marring the surface or bending the edges. Dragging a plate across a concrete floor or another plate can cause deep scratches that can compromise the protective passive layer and become sites for corrosion. For high-finish architectural plates, leaving the protective PVC film on for as long as possible through the fabrication process is a simple but highly effective way to protect the surface.
These practices are especially critical for thinner plates, which are more susceptible to bending and damage. By treating the plate with care, you ensure that the flatness and surface finish you specified and paid for are the same ones that make it into your final product.
Optimizing Fabrication: Cutting, Forming, and Welding
How you process the plate is just as important as the plate itself. When cutting, choose the method that best suits the material's thickness and your project's edge requirements while minimizing heat input. For example, underwater plasma cutting or fiber laser cutting introduces far less heat into the material than traditional plasma-in-air, significantly reducing the risk of heat-induced warping, especially on thinner plates.
When forming or rolling plates, it's vital to account for springback, the tendency of the material to partially return to its original shape. Different stainless steel grades have different springback characteristics, so forming parameters must be adjusted accordingly. Over-bending slightly is often necessary to achieve the desired final angle or radius.
For welding, developing a proper welding procedure specification (WPS) is non-negotiable. This includes using the correct filler metal, setting appropriate amperage and travel speed, and defining the weld sequence. For long seams, using a "back-step" or "balanced" welding sequence—where you alternate welding short sections on opposite sides of the structure—helps to distribute heat evenly and minimize distortion. Ensuring a good, clean fit-up, made possible by using dimensionally accurate plates, is the first and most important step in achieving a strong, defect-free weld. By optimizing these fabrication processes, you leverage the plate's inherent quality to achieve a superior result.
Conclusion
Ultimately, the ASTM A240 tolerance chart is the essential blueprint for precision in the stainless steel industry. Understanding its features, impacts, and the factors behind them is crucial for ensuring structural integrity, manufacturing efficiency, and the overall success and safety of your project.
-
Understand the global impact of standardized steel tolerances on trade ↩
-
See how advanced rolling processes enhance plate precision and consistency ↩
-
Learn about ASTM A240 and its importance in defining stainless steel plate tolerances ↩
-
See real-world examples of stress concentration and engineering mitigation methods ↩
-
Discover why 304L and 316L are commonly chosen for corrosion resistance and
mechanical strength ↩ -
Find the original ASTM A240 standards and detailed tolerance requirements for stainless steel plates ↩
-
Compare hot-rolled and cold-rolled methodologies for plate production and their typical tolerances ↩
-
See how advanced process control systems transform steel production quality and efficiency ↩
-
Explore AGC technology and its effect on maintaining steel plate thickness consistency ↩
-
Learn how ongoing training ensures product quality and compliance with industry standards ↩
-
Avoid costly damage by understanding typical errors with stainless steel plates. ↩
-
Step-by-step guide for verifying plate dimensions and ensuring compliance with ASTM A240. ↩
Have Questions or Need More Information?
Get in touch with us for personalized assistance and expert advice.