Yield Strength of 304, 316, 2205 Stainless Grades
Are you specifying stainless steel for a new project and feeling uncertain about which grade to choose? Selecting a grade with inadequate yield strength can lead to structural failure, costly redesigns, and significant safety risks. The pressure to balance performance with budget is immense, and a wrong choice has lasting consequences.
This guide provides the typical minimum yield strength values for annealed stainless steel grades: Type 304 is approximately 205 MPa (30 ksi), Type 316 is also around 205 MPa (30 ksi), and Duplex 2205 is significantly higher at about 450 MPa (65 ksi).
As the Global Business Director at MFY, I've seen how a deep understanding of material properties can make or break a project. Simply looking at a data sheet isn't enough. Yield strength1 dictates how much stress a material can take before it permanently deforms, a critical factor for any load-bearing application. Let's explore why these numbers are more than just specs—they are crucial inputs for safe, efficient, and cost-effective design.
Choosing the right stainless steel is a critical decision that impacts a project's structural integrity, service life, and overall cost. While many engineers are familiar with the basic corrosion resistance properties of grades like 304 and 316, a nuanced understanding of their mechanical properties, particularly yield strength, is what separates a good design from a great one. The dramatic jump in strength offered by a duplex grade like 2205 isn't just an incremental improvement; it opens up entirely new design possibilities2. It allows for thinner, lighter structures without sacrificing safety, a concept we frequently discuss with our clients in the construction and engineering sectors. This isn't just about preventing failure; it's about optimizing material usage, reducing weight, and ultimately, delivering a more competitive and innovative final product.
What are the yield strength values of 304, 316, and 2205 stainless steel grades?
Are you struggling to find clear, reliable yield strength values for common stainless steel grades? Inconsistent data from various sources can lead to confusion and incorrect calculations, potentially compromising your design's integrity before it even leaves the drawing board. You need definitive, industry-standard figures to ensure safety and compliance.
In the annealed condition, the typical minimum yield strength (0.2% offset) for Type 304 stainless steel is 205 MPa (30 ksi). Similarly, Type 316 stainless steel also has a minimum yield strength of approximately 205 MPa (30 ksi). Duplex 2205 stands apart with a significantly higher minimum yield strength of about 450 MPa (65 ksi).
These values are the baseline for engineers and designers, representing the stress at which the material begins to deform permanently. As a supplier of these materials to global markets, we at MFY treat these specifications as the foundational promise of our product's performance. When a client in Southeast Asia is designing a storage tank, they rely on that 205 MPa figure for their 304 or 316 sheets to calculate the required thickness. The much higher 450 MPa for 2205 allows an engineering contractor building a pedestrian bridge in a coastal, salt-spray environment to design lighter support structures, saving on both material cost and foundation requirements. Understanding these fundamental values is the first and most critical step in material selection, directly influencing the safety, efficiency, and economic viability of any project. It's the language of mechanical performance that transcends borders.

The specified minimum yield strength is a critical parameter derived from tensile testing3, a cornerstone of material science and engineering design. It is defined as the stress at which a material exhibits a specified limiting deviation from the proportionality of stress to strain, typically 0.2% for stainless steels. This 0.2% offset point is the practical definition of the transition from elastic (temporary) to plastic (permanent) deformation. For a designer, this number is paramount; it represents the maximum allowable stress a component can endure under normal operating conditions before permanent, and potentially unsafe, structural changes occur. The values for 304, 316, and 2205 are not arbitrary; they are a direct result of their fundamental chemical composition and microstructure, which dictate their mechanical behavior. While 304 and 316 share a common austenitic (face-centered cubic) crystal structure, leading to similar strength profiles, the dual-phase ferrite-austenite microstructure of Duplex 2205 is what gives it a remarkable leap in strength. This fundamental difference is something I constantly emphasize to our clients. Choosing between them is not just about corrosion resistance; it's a strategic decision based on the mechanical load demands of the application.
Understanding Austenitic Yield Strength: 304 and 316
Grades 304 and 316 are the workhorses of the stainless steel world, belonging to the austenitic family. Their microstructure is characterized by a face-centered cubic (FCC) crystal lattice, which imparts excellent ductility and formability. However, this structure is also inherently lower in strength compared to other steel families like ferritic or martensitic steels. The typical minimum yield strength for both grades in their standard annealed (softened) condition hovers around 205 MPa (30,000 psi). This value is a baseline—it's the guaranteed minimum a designer can count on as per international standards like ASTM A240.
While their yield strengths are nearly identical, the choice between them is typically driven by corrosion resistance needs. Type 316 contains molybdenum (typically 2-3%), which significantly enhances its resistance to chlorides and other industrial solvents, making it the preferred choice for marine, chemical, and pharmaceutical applications. From a purely mechanical standpoint, however, a designer specifying a simple structural component in a non-corrosive environment would see little difference in the initial strength performance between 304 and 316.
I once worked with an equipment integrator building food processing machinery for the Indian market. They were using 316 for everything out of habit. After reviewing their designs, we identified several structural components that were not in direct contact with corrosive food products. By switching these specific parts to 304, which offered the same yield strength, they were able to reduce material costs by nearly 15-20% without compromising the structural integrity or safety of the equipment. It was a classic case of understanding that while strength was similar, the application didn't warrant the extra cost of 316's superior corrosion resistance.
The Duplex Advantage: Understanding 2205's Strength
Duplex 2205 (UNS S32205) is a different class of material entirely. As its name suggests, it has a "duplex" microstructure containing a balanced mix of both austenite (like 304/316) and ferrite (the primary microstructure in carbon steels). This two-phase structure is the key to its exceptional properties. The ferrite phase contributes high strength and resistance to stress corrosion cracking, while the austenite phase provides good ductility and general corrosion resistance. The result is a material with a minimum yield strength of approximately 450 MPa (65,000 psi)—more than double that of its austenitic counterparts.
This leap in strength is a game-changer for structural applications. It means that for a component designed to withstand a specific load, a designer can use a significantly thinner section of 2205 compared to 304 or 316. This "lightweighting" has a domino effect: it reduces the amount of material that needs to be purchased, lowers the shipping weight, and can even reduce the load on supporting structures and foundations.
A construction contractor in the Middle East, one of our clients, was bidding on a project for a large architectural canopy exposed to coastal air. Their initial design using 316 stainless steel required thick, heavy support beams, driving up the cost. We proposed redesigning the structure using our 2205 sheets and pipes. The higher yield strength allowed their engineers to reduce the wall thickness of the primary structural elements by nearly 40%. While the per-kilogram cost of 2205 was higher than 316, the massive reduction in total weight made the Duplex solution more cost-effective overall. They won the bid because of this optimized, value-engineered approach.
What "Minimum" Specification Really Means for Engineers
It is crucial to emphasize the word "minimum" when discussing these values. Standards like ASTM and EN provide minimum specified mechanical properties. This is a guarantee from the manufacturer, like MFY, that the material supplied will meet or exceed this value. In reality, the actual yield strength of a given batch of steel is often slightly higher than the specified minimum due to minor variations in chemistry and processing. However, a conservative and safe engineering design must always be based on the guaranteed minimum value.
Engineers use this minimum yield strength, along with an appropriate safety factor, to calculate the maximum allowable design stress for a component. The safety factor accounts for uncertainties in loading, manufacturing tolerances, and the consequences of failure. For a non-critical architectural element, the safety factor might be low, whereas for a high-pressure vessel, it will be much higher.
This reliance on a guaranteed minimum is the foundation of modern engineering codes and global construction standards. It ensures that structures are safe and reliable, regardless of which certified mill produced the material. It provides a common, conservative baseline that allows for global trade and construction. When we ship our stainless steel coils to a distributor in Russia, they and their customers can design with the same confidence as an engineer in China, knowing that the material will perform as specified by these universally accepted standards.
How do the yield strengths of 304, 316, and 2205 stainless steels compare to each other?
Are you finding it difficult to visualize the real-world performance difference between stainless steel grades? Simply knowing the numbers isn't enough; you need to understand the practical implications of one material being "stronger" than another to make informed, cost-effective design choices.
Duplex 2205's yield strength of ~450 MPa (65 ksi) is more than double that of both 304 and 316 stainless steel, which are nearly identical at ~205 MPa (30 ksi). This makes 2205 vastly superior in applications where strength per unit of weight is a critical design factor yield strength comparison of stainless steel alloys.
This comparison is one of the most important conversations I have with our clients. While 304 and 316 are mechanically interchangeable for many standard applications, introducing Duplex 2205 changes the entire equation. A manufacturer of pressure vessels, for example, can significantly reduce the wall thickness—and thus the weight and cost—of a tank by using 2205 instead of 316L stainless steel. I worked with a client in the chemical transport sector who was able to increase the payload of their tanker trucks simply by rebuilding the tanks with lighter, stronger 2205 stainless steel supplied by MFY. The initial material cost was higher, but the long-term operational revenue from carrying more product on every trip provided a rapid return on investment. This illustrates a key principle: higher initial strength can lead to greater long-term economic efficiency.
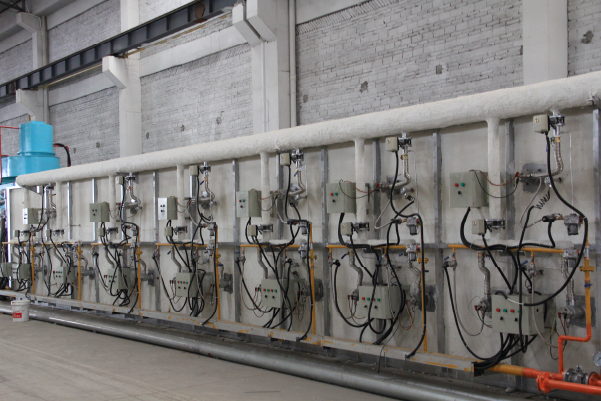
Comparing the yield strengths of these three popular grades reveals a distinct tier system in mechanical performance. At the base, we have the austenitic grades 304 and 316, which, for all practical purposes in structural design, can be considered mechanical equals. They offer moderate strength combined with outstanding ductility and toughness austenitic stainless steel properties4, making them easy to form and weld. The significant leap occurs when we move to Duplex 2205. Its strength is not just incrementally higher; it's in a different category altogether. This dramatic increase—more than double that of the austenitic grades—stems directly from its dual-phase microstructure. This comparison is not just an academic exercise; it has profound consequences for engineering design, material selection, and project economics. The ability to use a stronger material allows for more efficient designs, a concept known as "strength-to-weight ratio." A higher ratio means you can achieve the required structural performance with less material, which translates directly into lower weight. This is a critical advantage in applications ranging from transportation, where fuel efficiency is key, to civil engineering, where foundation loads must be minimized.
Direct Strength Comparison: A Tale of Two Tiers
The most straightforward way to compare these grades is to place their typical minimum yield strengths side-by-side. What emerges is a clear picture of two distinct performance levels. Tier one consists of the austenitic grades, 304 and 316. They share a similar chemical base (iron, chromium, nickel) and the same crystal structure, resulting in nearly identical mechanical properties in the annealed state. Their yield strength is a reliable, albeit modest, figure that serves countless applications well, from kitchen sinks to architectural cladding.
Tier two is occupied by Duplex 2205. Its yield strength is a defining characteristic, immediately setting it apart. This isn't a minor 10% or 20% improvement; it's a 120% increase over the austenitic grades. This significant gap means that in any application where the design is limited by yield strength, 2205 presents a compelling alternative. An engineer can either carry more than twice the load for the same cross-sectional area or use a much smaller cross-section to carry the same load. This fundamental difference is the primary driver for choosing duplex grades in demanding structural roles.
Consider the design of a catwalk in a manufacturing plant. If designed with 304 or 316 angle iron, the support beams would need to be of a certain size to prevent sagging (permanent deformation) under load. If the same catwalk were designed using 2205, the beams could be made from significantly thinner material, making the entire structure lighter and potentially easier to install. This is the practical application of the strength comparison.
Strength-to-Weight Ratio and Its Economic Impact
The concept of the strength-to-weight ratio is where the comparison becomes economically critical. While Duplex 2205 has a higher cost per kilogram than 304 or 316, its superior strength allows for the use of less material strength-to-weight ratio in stainless steel design5. This can often lead to a lower overall project cost, a concept that can seem counterintuitive at first. This is a conversation I have frequently with MFY's clients, especially those in the engineering and construction sectors.
Let's illustrate with an example. A client needs to fabricate a large-diameter pipe for a water treatment plant, designed to handle a certain internal pressure.
- Design A (316L): Requires a pipe wall thickness of 10 mm.
- Design B (2205): Due to its higher yield strength, it only requires a wall thickness of 6 mm to handle the same pressure safely.
Although the cost of 2205 per ton might be higher, the total tonnage of steel required for Design B is 40% less. This reduction in material volume often outweighs the higher unit price. Furthermore, the cost savings extend beyond just the material purchase. The lighter pipe from Design B is cheaper to transport, easier to handle on-site, requires less welding time and consumables, and puts less strain on supporting structures. This holistic view of project costs is essential when comparing materials based on strength.
The following table provides a clear comparison of the key mechanical properties for these three grades in their annealed condition, highlighting the stark differences.
Property | Type 304 | Type 316 | Duplex 2205 |
---|---|---|---|
Min. Yield Strength (0.2% Offset) | ~205 MPa (30 ksi) | ~205 MPa (30 ksi) | ~450 MPa (65 ksi) |
Min. Tensile Strength | ~515 MPa (75 ksi) | ~515 MPa (75 ksi) | ~655 MPa (95 ksi) |
Elongation (in 50mm) | ~40% | ~40% | ~25% |
Hardness (Rockwell B) | ~92 HRB | ~95 HRB | ~293 HBW (~31 HRC) |
Implications for Ductility and Toughness
While Duplex 2205 is the clear winner in terms of strength, it's important to consider the trade-offs. As shown in the table above, the higher strength of 2205 comes with lower ductility, as indicated by the lower elongation percentage. Austenitic grades like 304 and 316 are incredibly ductile, meaning they can undergo significant plastic deformation before fracturing. This makes them exceptionally forgiving during fabrication processes like deep drawing or complex bending.
Duplex 2205, while still possessing good toughness, is less forgiving than its austenitic counterparts. Forming operations require more powerful equipment and careful consideration of bend radii to avoid cracking. Its higher strength also means it is harder to machine. This is a critical part of the comparison I stress to our manufacturing clients. The choice of material must align with the available fabrication capabilities.
For a client manufacturing complex, deep-drawn components like a multi-stage kitchen sink, 304 is the ideal choice due to its high elongation and excellent formability formability of austenitic stainless steels6. Attempting the same process with 2205 would be impractical and likely result in failure. Conversely, for a client fabricating a straightforward I-beam for a building frame, the high strength of 2205 is a major advantage, and its lower ductility is not a limiting factor for that simple geometry. The "better" material is always the one best suited to both the end-use application and the manufacturing process.
What factors influence the yield strength of stainless steel grades?
Have you ever noticed that the actual strength of the steel you receive can vary from the datasheet? This happens because the nominal yield strength is not a fixed number. It's influenced by several factors, and overlooking them can lead to over-engineering or, worse, unexpected failures in demanding applications.
The primary factors influencing the yield strength of stainless steel are its chemical composition—including carbon and nitrogen, the amount of cold work or strain hardening it has undergone, and its service temperature. Grain size and heat treatment also play significant roles in determining the final mechanical properties.
This is a technical area where my team at MFY provides significant value to our clients. For instance, a manufacturing company producing high-pressure fittings might require a yield strength slightly higher than the standard annealed 316. By working with them, we can supply a lightly cold-drawn 316 stainless steel bar that meets their specific strength requirements. This process of strain hardening significantly increases the yield strength. Conversely, for a client performing extensive forming operations, we ensure they receive material in the fully annealed (softest) state to maximize ductility. Understanding and controlling these influencing factors is key to tailoring a material to a specific application, optimizing both performance and manufacturability.
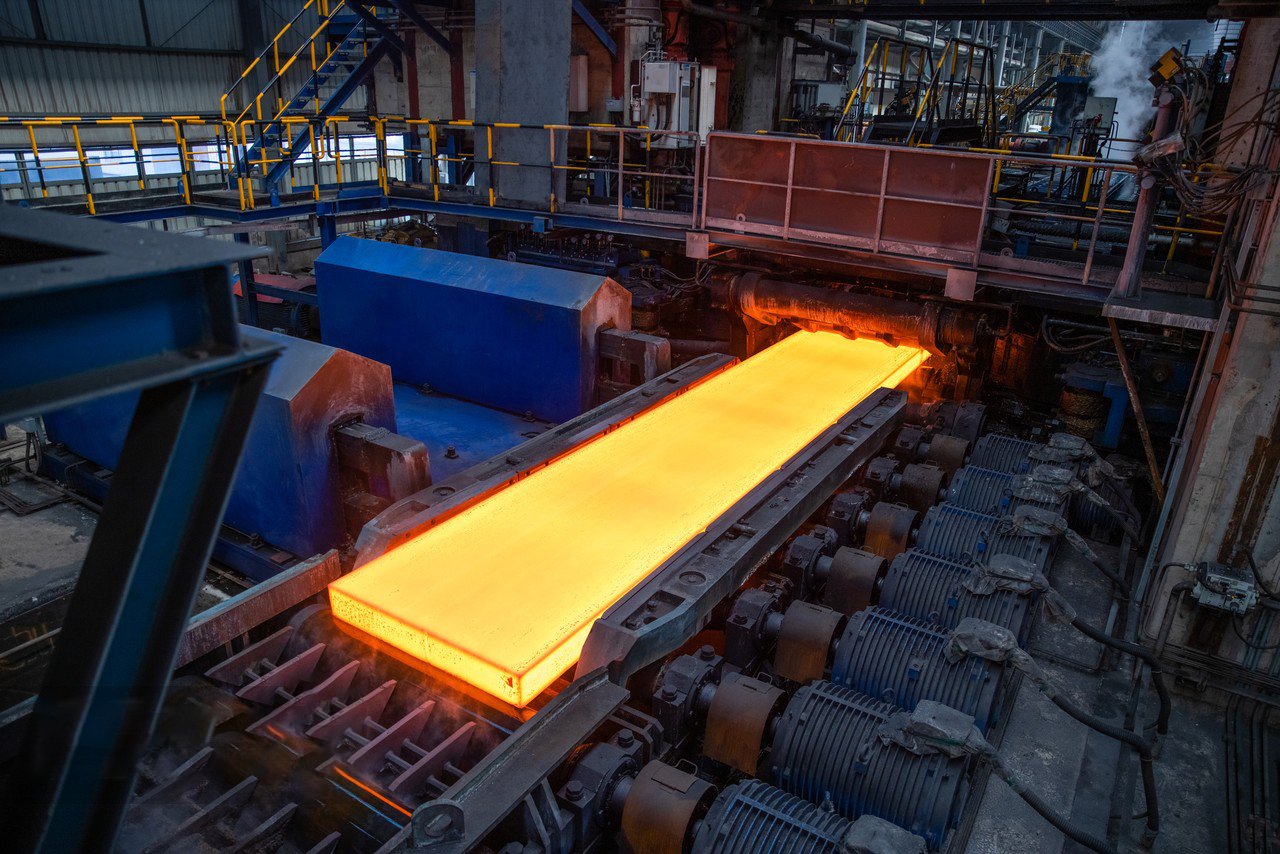
The nominal yield strength values provided on technical datasheets represent a baseline for the material in a specific, standardized condition—typically fully annealed. However, the true yield strength of a stainless steel component7 in its final form is a dynamic property, shaped by a combination of its inherent chemistry and the thermomechanical history it experiences during processing and in its service environment. As a material supplier, we at MFY are acutely aware of how these factors can be manipulated to achieve desired engineering outcomes. A deep understanding of these influences allows engineers and manufacturers to move beyond using "off-the-shelf" properties and begin to specify materials that are precisely optimized for their application. Whether it's increasing strength through mechanical means or accounting for its reduction at high temperatures, a holistic view of these factors is critical for advanced and reliable design. It's the difference between simply using a material and truly engineering with it.
The Role of Chemical Composition
The foundation of any alloy's properties is its chemical composition. For stainless steels, certain elements have a profound impact on yield strength. While major alloying elements like chromium and nickel define the grade and its basic corrosion resistance, minor elements play a huge role in strength. Nitrogen is a particularly potent strengthening agent in austenitic and duplex grades8. It is an "interstitial solid solution strengthener," meaning its small atoms fit into the spaces between the larger iron atoms in the crystal lattice, distorting the lattice and making it more difficult for atomic planes to slip past one another—the very mechanism of plastic deformation.
In Duplex 2205, nitrogen is a crucial alloying element (typically 0.14-0.20%) that not only enhances pitting corrosion resistance but also significantly boosts its yield strength. In austenitic grades like 316, special "nitrogen-strengthened" variants (e.g., 316N) are produced for applications needing higher strength than the standard grade can offer, such as in the power generation and petrochemical industries. Carbon is another powerful interstitial strengthener, but its content is often kept low in grades like 304L and 316L to improve weldability and prevent sensitization (the formation of chromium carbides that reduces corrosion resistance). It's a constant balancing act that mill metallurgists must manage to achieve the desired combination of strength, corrosion resistance, and fabricability.
Work Hardening (Strain Hardening)
One of the most effective ways to increase the yield strength of austenitic stainless steels is through cold working, also known as strain hardening. When grades like 304 and 316 are deformed at a temperature below their recrystallization point (e.g., by rolling, drawing, or bending at room temperature), dislocations are created within their crystal structure. These dislocations interfere with each other's movement, making further deformation more difficult and thus increasing the material's yield strength and tensile strength.
This effect can be dramatic. A standard annealed 304 stainless steel with a yield strength of 205 MPa can easily exceed 550 MPa or more after significant cold rolling. This is the principle used to produce high-strength stainless steel for applications like springs, high-tensile wires, and fasteners. As a supplier, we offer various "tempers" of stainless steel coil and sheet, such as 1/4 hard, 1/2 hard, and full hard, which correspond to different levels of cold work and, therefore, different levels of yield strength.
I once worked with a client manufacturing automotive components that required a flat spring with a specific clamping force. Standard annealed 304 was too soft and would permanently deform. A high-strength alloy was too expensive. The solution was to supply them with a cold-rolled 304 strip in a "3/4 hard" temper. It had the required yield strength to function as a spring, while still being a cost-effective material. This is a perfect example of leveraging work hardening to achieve specific engineering properties.
The Influence of Temperature
Temperature has a significant and inverse effect on yield strength. As the service temperature of stainless steel increases, its yield strength decreases. The atoms in the metal vibrate more energetically at higher temperatures, making it easier for dislocations to move and for the material to deform under load. This is a critical consideration for any equipment designed for elevated temperature service, such as pressure vessels, heat exchangers, and furnace components. Engineering design codes like the ASME Boiler and Pressure Vessel Code provide tables of allowable stresses for different materials at various temperatures, which are based on this reduction in strength.
Conversely, as temperatures decrease into the cryogenic range, the yield strength of austenitic stainless steels like 304 and 316 actually increases significantly, while they retain their excellent toughness. This makes them ideal materials for cryogenic applications like LNG (Liquefied Natural Gas) storage and transportation, a key market for MFY's products. Duplex steels, however, have a limitation. While strong at ambient temperatures, they can become brittle at very low temperatures (e.g., below -50°C) and also at elevated temperatures (above 300°C), which limits their use to a more moderate temperature range compared to the austenitic grades. An engineer must always consider the full operational temperature range when selecting a material and assessing its effective yield strength.
How can the yield strength of these stainless grades affect their applications?
Are you unsure how to translate a material's yield strength into practical advantages for your specific application? Choosing a grade that is "too strong" can be needlessly expensive and difficult to fabricate, while choosing one that is too weak is a recipe for disaster. This decision directly impacts cost, safety, and performance.
Yield strength directly dictates a component's load-bearing capacity. Higher yield strength (like in 2205) allows for thinner, lighter designs, reducing material costs and weight. Lower yield strength (in 304/316) is often paired with higher ductility, making them ideal for applications requiring extensive forming.
This is a critical trade-off I discuss with our clients daily. For a manufacturer of deep-drawn kitchen sinks, the high ductility and moderate yield strength of our 304 coils are perfect. The material forms easily without cracking. For a different client, an engineering and construction contractor building a chemical storage tank farm, the high yield strength of our 2205 plates is the key selling point. It allows them to build larger, more efficient tanks that meet all safety codes while using significantly less steel, directly impacting their project's profitability. The application always dictates the optimal balance between strength and formability.
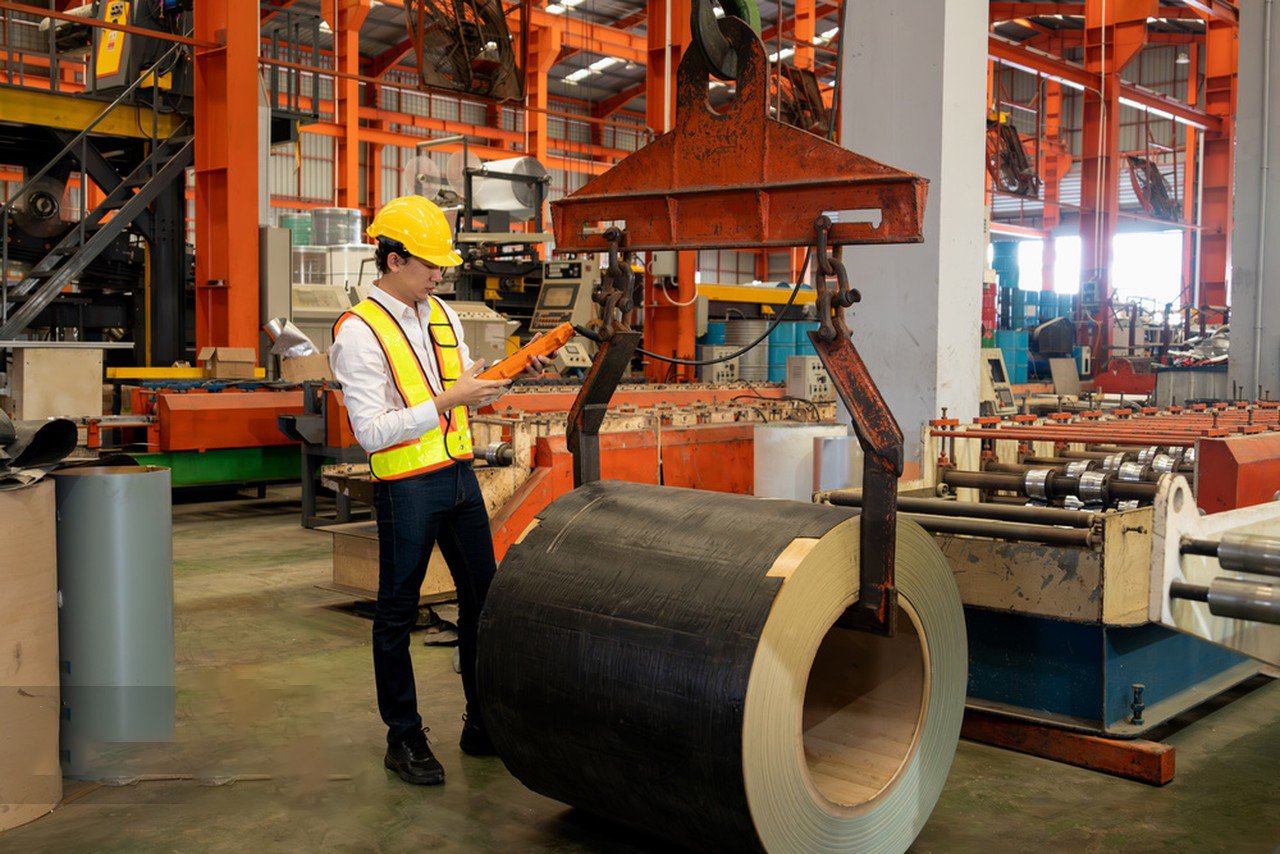
The yield strength of a stainless steel grade is arguably one of the most critical properties influencing its suitability for a particular application. It fundamentally determines the material's ability to resist permanent deformation under load, which is the very essence of structural integrity. The choice of a material with an appropriate yield strength has far-reaching consequences, affecting not only the safety and reliability of the final product but also its weight, cost, and manufacturability. The decision-making process involves a careful analysis of the mechanical demands of the application. An engineer must ask: Is this component primarily load-bearing? Does it need to be lightweight? Will it undergo significant forming during manufacturing? The answers to these questions will guide the selection towards the grade with the most appropriate balance of properties. From my vantage point at MFY, I see our diverse range of clients making these calculations every day, leveraging the distinct yield strengths of 304, 316, and 22059 to optimize their products for their unique markets.
Designing for Load-Bearing Capacity: The 2205 Advantage
In any application where a component must support a significant load, yield strength is the primary design constraint. This includes structural beams, pressure vessels, support columns, and pump shafts. In these cases, a higher yield strength is almost always advantageous. Duplex 2205, with its yield strength of over 450 MPa, excels in this arena. Its high strength allows designers to create components with thinner cross-sections that can support the same load as a much thicker component made from an austenitic grade.
This principle is crucial in industries where weight is a penalty. In the transportation sector, for example, a chemical tanker built from 2205 will be significantly lighter than one made from 316L. This reduced deadweight allows for a larger payload, increasing the operational efficiency and profitability of the tanker over its service life. Similarly, in offshore oil and gas platforms, weight reduction is critical to managing the load on the platform's foundation. Using high-strength 2205 for piping systems and structural modules helps to minimize overall platform weight.
A client of ours, a contractor for infrastructure projects, regularly uses our 2205 stainless steel pipes for long-span pipe bridges. By using high-strength duplex, they can increase the distance between support piers, reducing the number of costly foundations that need to be built. Here, the higher yield strength directly translates into a lower total installed cost for the project.
Designing for Formability: The Austenitic Domain
While high strength is desirable for structural components, it can be a significant drawback for applications that require extensive forming. Processes like deep drawing, stretching, and complex bending require a material with high ductility (the ability to stretch without breaking) and a relatively low yield strength to allow the material to flow easily into the die. This is the domain where austenitic grades 304 and 316 shine. Their lower yield strength and excellent elongation values make them ideal for complex manufacturing processes.
Consider the manufacturing of a common kitchen sink. This process involves taking a flat sheet of stainless steel and drawing it into a deep, complex shape in a single operation. This requires a material that can stretch and thin out considerably without tearing. Type 304 is the global standard for this application precisely because its mechanical properties are perfectly suited for it. Attempting to make a sink from Duplex 2205 would require immense press force and would almost certainly result in the material cracking.
We supply large quantities of 304 stainless steel coils to manufacturers of cookware, appliances, and sanitary ware across Southeast Asia. For these clients, consistent, low yield strength and high ductility are the most important material properties, as they ensure high production yields and minimal defects during their forming operations. In this context, the "weaker" material is actually the superior choice.
Designing for a Balance: Cost vs. Performance
In many applications, the choice is not as clear-cut and involves a careful balance of performance requirements and budget constraints. The yield strength of a material is directly linked to its cost—higher strength alloys typically command a higher price per kilogram. An engineer must determine if the benefits of a higher-strength material justify the increased cost.
For a simple storage tank holding water at ambient pressure, the moderate strength of Type 304 is more than sufficient. Using a stronger, more expensive material like 2205 would be a case of "over-engineering"—it would provide no functional benefit and would simply increase the project cost unnecessarily. However, if that same tank were designed to hold a pressurized chemical, the higher yield strength of 2205 could allow for a thinner wall, potentially making it the more economical choice after a full cost analysis (material + fabrication + transport).
This cost-benefit analysis is a service we constantly provide to our distributor and trader clients. They rely on us not just to supply steel, but to provide the technical guidance that helps their customers make the most economical choice. By understanding the specific application, we can help them decide when it's best to use a standard austenitic grade or when the upfront investment in a high-strength duplex grade will pay dividends in the long run.
What are the recommended applications for 304, 316, and 2205 stainless steel based on their yield strength?
Feeling unsure which stainless steel grade is the right fit for your project? Matching the material's yield strength to the application's demands is crucial for ensuring safety, longevity, and cost-effectiveness. A mismatch can lead to overspending on an unnecessarily strong material or risking failure with one that's too weak.
Based on yield strength, Type 304 is for general-purpose structural and decorative use. Type 316 is for similar applications but in corrosive environments. High-strength Duplex 2205 is recommended for demanding load-bearing applications like pressure vessels, bridges, and marine structures where weight reduction is also critical.
This application-specific guidance is central to my role at MFY. We help clients navigate these choices daily. For instance, a manufacturer of architectural hardware in Russia will find 304 perfectly adequate. An equipment integrator for a desalination plant in the Middle East will require 316 for its corrosion resistance at a moderate strength level. Meanwhile, a major construction contractor building an offshore platform will specify 2205 for its high strength-to-weight ratio, a critical factor for that demanding environment. The optimal choice is always a function of load, environment, and cost.
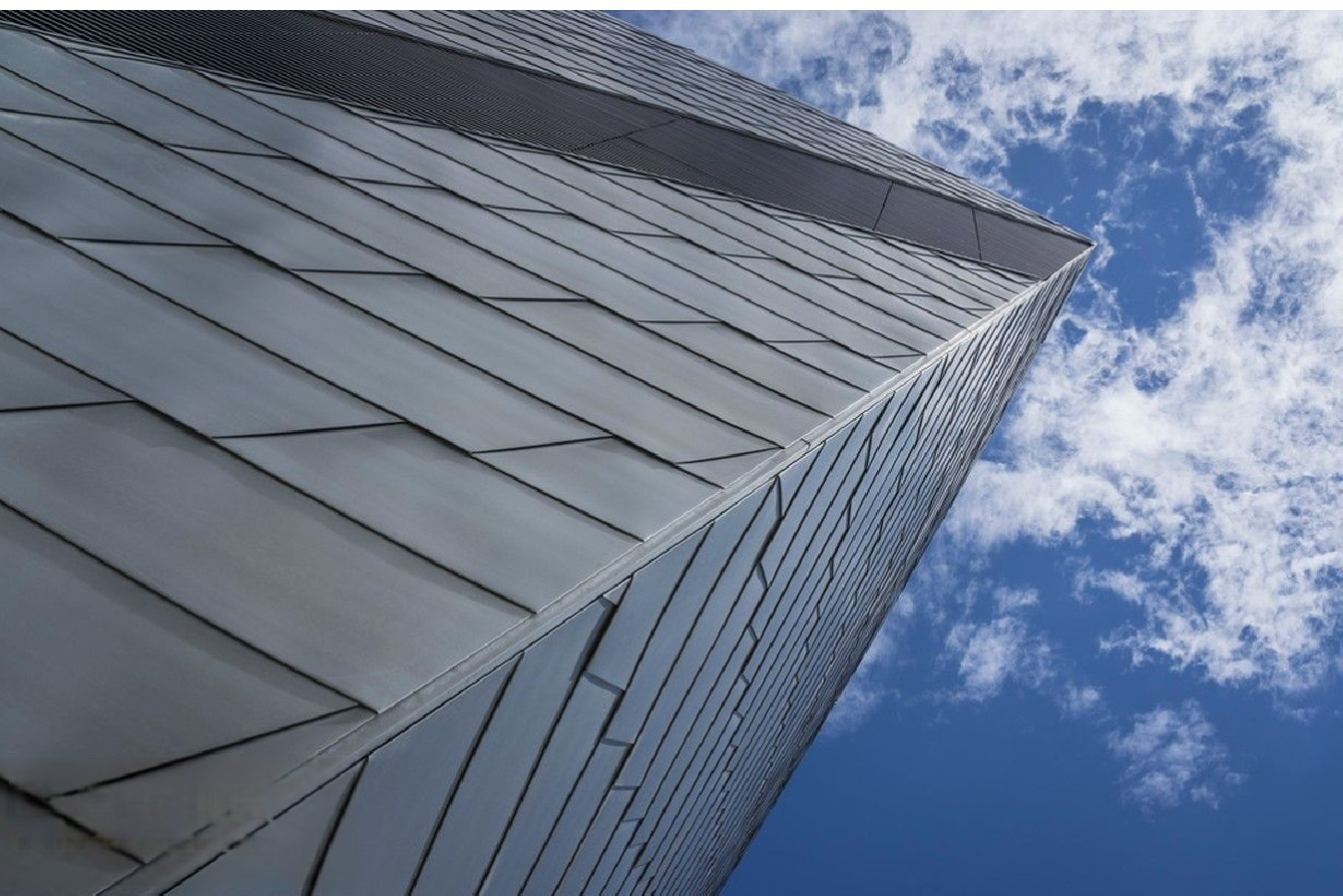
The selection of the correct stainless steel grade is a critical engineering decision where yield strength plays a pivotal, though not exclusive, role. Each grade—304, 316, and 2205—occupies a distinct niche defined by a unique combination of strength, corrosion resistance, and cost. Recommending a grade requires a holistic understanding of the end-use environment and the mechanical loads the component will face throughout its service life. As a global supplier, MFY engages in this consultative process continuously, guiding engineers and contractors toward the material that offers the optimal blend of properties for their specific project, whether it's a simple bracket or a complex, mission-critical pressure vessel. The following recommendations illustrate how yield strength, in concert with other characteristics, dictates the ideal application for each of these versatile materials.
Grade 304: The General-Purpose Standard
With its moderate yield strength of ~205 MPa, excellent formability, and good general corrosion resistance10, Type 304 is the quintessential "all-rounder" of the stainless steel world. Its strength is sufficient for a vast array of applications where high loads are not the primary concern. Its affordability and ease of fabrication make it the default choice for countless products across numerous industries.
The defining characteristic that drives its application is its balance. The yield strength is high enough for light structural applications like framework for food processing equipment, handrails, and brackets. At the same time, it is low enough to allow for the extreme ductility needed for deep-drawing processes. This is why 304 is ubiquitous in consumer goods. It's the material of choice for kitchen sinks, cookware, and appliance housings—products that require significant forming but don't face extreme mechanical loads.
A typical client for MFY in this space is a manufacturer of commercial kitchen equipment in Southeast Asia. They use our 304 sheets and tubes extensively. The material's yield strength is perfectly adequate to build sturdy tables, shelves, and cabinets, while its excellent formability allows them to press and form sinks and sanitary trays efficiently. For these applications, a higher-strength material would offer no functional advantage and would only increase cost and fabrication difficulty.
Grade 316: The Standard for Corrosive Environments
Mechanically, Type 316 is a twin to 304, sharing a similar yield strength of ~205 MPa. The recommendation to use 316 is therefore not driven by strength, but by the presence of corrosive agents, particularly chlorides11. The addition of molybdenum gives 316 superior resistance to pitting and crevice corrosion, making it essential for applications exposed to saltwater, de-icing salts, and various industrial chemicals.
Recommended applications for 316 are essentially "304 applications in a harsher environment." This includes architectural paneling in coastal cities, laboratory equipment, pharmaceutical processing vessels, and boat railings. The yield strength is still the same moderate value, meaning it is suitable for similar light-to-medium load applications, but with an added layer of chemical defense.
I often work with engineering contractors designing water treatment and desalination plants in the Middle East. For them, 316L is the baseline material for pipes, tanks, and valves. The moderate yield strength is sufficient for the pressure requirements of many parts of the system, and the molybdenum content is critical for resisting corrosion from the saline and treated water. Here, the choice is dictated by the need for longevity in a corrosive medium, with the yield strength being a secondary, albeit sufficient, property.
Duplex 2205: The High-Strength Solution
The recommendation for Duplex 2205 is driven almost entirely by its high yield strength of ~450 MPa. This grade is specified when the primary requirement is high load-bearing capacity, often combined with a need for weight reduction and excellent corrosion resistance (generally superior to 316). It is the material of choice for true structural engineering.
Recommended applications include pressure vessels and chemical storage tanks where high pressure allows for significant wall thickness reduction. It is used for bridges, building supports, and other infrastructure, especially in marine environments where its high strength and chloride resistance are both valued. In the oil and gas industry, it's used for pipelines and processing equipment that must handle high pressures and corrosive fluids. Pulp and paper digesters, which operate under both pressure and aggressive chemical conditions, are another classic application.
A prime example from my own experience is a project we supplied in India for the construction of a series of large chemical storage tanks. The client's initial design used 316L, which resulted in very thick, heavy, and expensive tanks. By redesigning with 2205, they leveraged its high yield strength to reduce the required plate thickness by over 30%. This not only saved a significant amount on the total material purchase from MFY but also reduced welding time and costs, making the entire project more competitive. This is the power of specifying a material based on high yield strength.
Conclusion
Understanding the distinct yield strengths of 304, 316, and 2205 is fundamental to sound engineering. While 304 and 316 offer versatile formability, Duplex 2205 provides double the strength, enabling lighter, more efficient, and often more economical designs for demanding structural applications.
-
Learn how yield strength determines safe load limits for stainless steel in design applications. ↩
-
Understand how Duplex 2205 enables thinner, lighter, and more cost-effective structures in demanding environments. ↩
-
Gain insight into how mechanical properties like yield strength are measured and certified in the lab. ↩
-
Get in-depth property charts for 304/316 stainless, including toughness, ductility, and typical uses ↩
-
Understand the engineering and economic importance of strength-to-weight in real-world projects ↩
-
Find explanations and process limits for forming operations with common stainless steel grades ↩
-
Discover practical reasons for yield strength variation in real-world applications ↩
-
Find out how nitrogen's interstitial effect improves both strength and corrosion resistance ↩
-
See a data-driven comparison of mechanical properties among the most common stainless grades ↩
-
Learn about the environments and applications where 304's corrosion resistance is advantageous ↩
-
Understand how molybdenum improves 316's resistance to salt and chemical corrosion ↩
Have Questions or Need More Information?
Get in touch with us for personalized assistance and expert advice.