Stainless Steel Density & Weight Calc (mm ➜ kg)
Are you struggling with project cost overruns due to inaccurate material estimates? Miscalculating stainless steel weight can throw your entire budget off track, leading to unexpected expenses and logistical headaches. Mastering the role of density in weight calculations is the key to achieving precision and financial control.
Stainless steel's weight in kilograms is calculated by multiplying its volume (length x width x thickness in meters) by its specific density, which typically ranges from 7,700 to 8,050 kg/m³ depending on the grade. This formula provides an accurate basis for all project quoting and logistics planning.
Getting this calculation right is more than just an academic exercise; it's the bedrock of successful project management in any industry that relies on steel. In my role at MFY, I’ve seen firsthand how a precise understanding of weight impacts everything from international shipping costs to on-site structural integrity1. An error of a few kilograms can scale up to tons in a large order, creating a ripple effect of complications. This guide will walk you through the essential factors, ensuring your next project is built on a foundation of accuracy.
The seemingly simple task of calculating steel weight is, in fact, a critical process fraught with potential for error. It’s a discipline where precision is paramount. A superficial understanding can lead to significant financial and operational discrepancies, a lesson many learn the hard way. For instance, a leading construction firm in Southeast Asia nearly faced a major setback when their initial calculations for a skyscraper façade failed to account for the specific density of the duplex stainless steel specified2. This oversight could have led to incorrect load-bearing calculations for the entire structure, jeopardizing safety and requiring costly last-minute engineering revisions. This underscores the necessity of moving beyond generic figures and embracing a more nuanced, data-driven approach grounded in material science and industry best practices.
What is the density of stainless steel and how is it determined?
Confused about why different stainless steel grades have different densities, and concerned that using a generic value could be compromising your projects? This uncertainty can lead to costly material ordering errors. Understanding how density is scientifically determined empowers you to use grade-specific values for ultimate precision.
The density of stainless steel, a measure of its mass per unit volume, is primarily determined by its unique chemical composition—the specific percentages of iron, chromium, nickel, molybdenum, and other elements. It's typically measured in kilograms per cubic meter (kg/m³) or grams per cubic centimeter (g/cm³).
This fundamental property, density, is far more than just a number on a technical data sheet. It's the very foundation upon which accurate weight calculations, structural engineering, and logistical planning are built. At MFY, we often consult with engineering contractors who are surprised to learn how much density can vary between different grades of stainless steel. For example, a client planning a large-scale desalination plant in the Middle East initially budgeted their stainless steel piping based on a generic density value. Our team intervened, explaining that the specified Grade 316L, with its higher nickel content, is tangibly denser than the Grade 304 they had used for a previous project. This early clarification prevented a significant budget overrun and ensured the structural supports for the piping system were designed with the correct load in mind. This small detail highlights a massive principle: in the world of steel, precision at the elemental level translates directly to project success and safety on a macro scale. It’s a detail we will explore more deeply now.
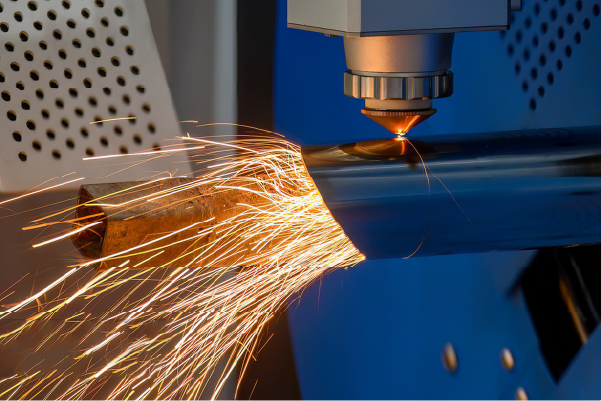
To truly master weight calculation, one must first appreciate the science that defines the material's density. This isn't just an abstract number; it's a direct reflection of the steel's atomic structure and elemental makeup. Failing to respect these nuances is a common pitfall that can have significant downstream consequences in both cost and application performance. A deeper dive into the "how" and "why" of density determination reveals the precision required in the steel industry and reinforces why partnering with a knowledgeable supplier is critical for project success.
The Science Behind Density: Alloying Elements' Role
The density of any stainless steel grade is a direct result of its specific recipe of alloying elements. The base element for all steel is iron, which has a density of approximately 7,870 kg/m³. However, it is the addition of other elements that gives stainless steel its desired properties, such as corrosion resistance and strength, and also alters its density. For example, chromium, the defining element of stainless steel (typically 10.5% or more), is slightly less dense than iron. In contrast, nickel, a key element in the common 300-series austenitic grades like 304 and 316, is significantly denser than iron.
This interplay of elements means each grade has a unique density fingerprint. For instance, austenitic grades like SS 304 (with around 8% nickel) have a density of about 7930 kg/m³. Grade 316, which contains more nickel (around 10%) and adds molybdenum, is even denser, typically around 8000 kg/m³. On the other hand, ferritic grades like SS 430, which contain chromium but virtually no nickel, are lighter, with a density closer to 7700 kg/m³. These differences, while seemingly small, are crucial for accurate weight calculations on large orders, where a 2-3% variance can amount to several tons of steel.
At MFY, we handle a diverse portfolio of products for global clients, from manufacturers in India requiring 400-series ferritic coils to engineering contractors in Russia building with 300-series austenitic pipes. For each client, we emphasize the importance of using the correct density for their specific grade. Below is a comparative table illustrating these critical differences, which we use to guide our clients in their planning and procurement phases.
Stainless Steel Grade | Key Alloying Elements | Typical Density (kg/m³) |
---|---|---|
304 (Austenitic) | 18% Cr, 8% Ni | ~7930 |
316L (Austenitic) | 17% Cr, 12% Ni, 2.5% Mo | ~8000 |
430 (Ferritic) | 16% Cr, 0% Ni | ~7700 |
2205 (Duplex) | 22% Cr, 5% Ni, 3% Mo | ~7850 |
Standardized Measurement Techniques in the Industry
The density values listed on technical data sheets are not arbitrary; they are determined through rigorous, standardized scientific methods. The most traditional and intuitive method is the Archimedes' principle, which involves measuring the mass of a sample in air and then its apparent mass when submerged in a liquid of known density (like water). The difference in mass allows for the calculation of the sample's volume, and from there, its density. While highly accurate for solid, non-porous materials, this method is primarily used in laboratory settings for certification and research.
In a high-volume production and trading environment like ours at MFY, speed and efficiency are paramount. For this, we rely on advanced analytical tools. One of the most critical is the X-ray fluorescence (XRF) analyzer. This handheld device allows for rapid and non-destructive analysis of the steel's elemental composition. By bombarding the metal surface with X-rays, it causes the atoms within the alloy to emit secondary X-rays at characteristic energies for each element. The analyzer measures these emissions to provide a precise percentage breakdown of chromium, nickel, molybdenum, and other elements in seconds.
Once we have this precise chemical composition, we can calculate a highly accurate density value, rather than relying on a generic textbook figure. This capability is essential for our quality assurance process. It allows us to verify that the material we receive from mills and supply to our clients meets the exact specifications required by international standards like ASTM and ISO. This documented verification, often provided in a Material Test Certificate (MTC), gives our clients the confidence that the steel they are purchasing will perform as expected and that their weight-based calculations are sound.
Case Study: Density's Impact on a High-Pressure Pipeline Project
The practical implications of precise density are best illustrated with a real-world example. We recently worked with an engineering and construction contractor on a major natural gas pipeline project in Southeast Asia. The project specifications called for several kilometers of high-strength duplex stainless steel pipe (Grade 2205), which needs to withstand high pressure and a corrosive environment. The contractor's initial cost estimates and structural plans were based on a generic density for austenitic steel (~8000 kg/m³), which they had used in past projects.
During our initial consultation, our technical team immediately flagged this as a potential issue. Duplex Grade 2205 has a different microstructure and composition (approx. 22% Cr, 5% Ni) than austenitic grades, resulting in a lower density of around 7850 kg/m³. While a difference of 150 kg/m³ (less than 2%) may seem minor, we prompted the client to recalculate the total project tonnage. Across the entire length of the pipeline, this "minor" density difference translated into a multi-ton reduction in the required material weight.
The impact was twofold. First, the client realized a significant, direct cost saving on the material purchase itself. Second, and more critically, the entire project's engineering calculations had to be revised. The lighter actual weight of the pipes affected the load calculations for the support structures, the seismic bracings, and even the specifications for the cranes needed for installation. By identifying this discrepancy early, we helped the client not only refine their budget but also ensure the long-term safety and structural integrity of the pipeline. It was a powerful lesson in how a small detail in material science can have a massive impact on engineering and construction.
How does the density of stainless steel affect weight calculations?
Have you ever been surprised when the calculated weight of a steel order doesn't match the final shipping invoice? This discrepancy often stems from a misunderstanding of density's powerful role3. This knowledge gap can lead to logistical nightmares and budget blowouts. Understanding density as a direct multiplier is your first step toward flawless calculations.
Density is the critical multiplier in the weight calculation formula (Weight = Volume × Density). Therefore, any inaccuracy in the density value is directly and proportionally magnified by the material's total volume, leading to significant errors in the final weight, especially for large-scale industrial orders.
The relationship between density and weight is direct and unforgiving. Think of it as a lever: a small input force (a slight error in density) can produce a massive output difference when applied over a long distance (a large volume of steel). For a hobbyist ordering a single sheet, this might be negligible. But for the industrial-scale clients MFY serves, this multiplier effect is a major financial and operational variable. We frequently ship hundreds of tons of stainless steel coils to manufacturing hubs in India and Southeast Asia4. In these scenarios, a 1% density miscalculation doesn't just mean a 1% cost difference; it means an entire shipping container might be improperly loaded, customs declarations could be flagged for inaccuracies, and production lines could be halted waiting for material that was miscalculated. It’s a chain reaction of risk that originates from one single, critical data point. We must, therefore, treat density not as an estimate, but as a precise specification central to the entire supply chain.
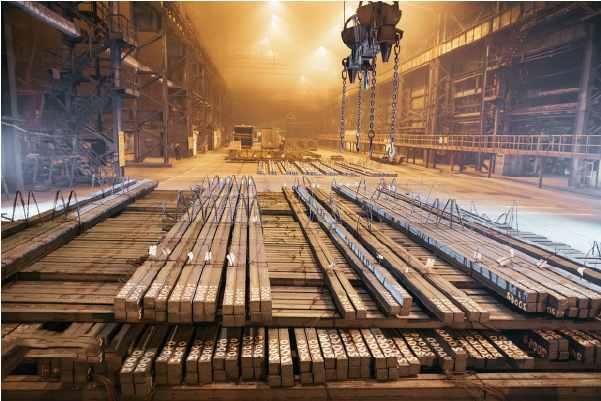
To move from approximation to precision, we must dissect the mechanics of how density functions within the calculation itself. It's not enough to know that density matters; a professional must understand how it scales, where the risks lie, and why even minor variations within a single grade can be significant for certain applications. This deeper understanding transforms weight calculation from a simple multiplication problem into a sophisticated risk management tool, protecting budgets, timelines, and the integrity of the final product. Let's explore the practical mechanics and real-world consequences of this fundamental principle.
The Core Formula: Volume x Density = Weight
The fundamental formula for calculating the weight of any uniform object is elegantly simple: Weight is the product of its Volume and its Density. For stainless steel products like sheets or plates, the volume is calculated by multiplying its three dimensions: Length × Width × Thickness. The critical step is to ensure unit consistency. Since density is typically expressed in kilograms per cubic meter (kg/m³), all dimensions must be converted to meters before the calculation.
Let's walk through a tangible example. A client, a distributor in the Middle East, orders a standard stainless steel sheet of Grade 304. The dimensions are 1.5mm (thickness) x 1219mm (width) x 2438mm (length).
First, we convert all dimensions to meters:
- Thickness: 1.5 mm = 0.0015 m
- Width: 1219 mm = 1.219 m
- Length: 2438 mm = 2.438 m
Next, we calculate the volume:
Volume = 0.0015 m × 1.219 m × 2.438 m = 0.004456 m³
Now, we introduce the density. The standard density for Grade 304 is approximately 7930 kg/m³.
Weight = 0.004456 m³ × 7930 kg/m³ = 35.34 kg.
If this client had mistakenly used the density of a ferritic grade like 430 (approx. 7700 kg/m³), the calculated weight would be 34.31 kg. That's a difference of over 1 kg (or 3%) on a single sheet—a seemingly small discrepancy that becomes enormous when scaled up.
The Ripple Effect of Inaccuracy in Large-Scale Projects
The true impact of a density error is only revealed at scale. Let's continue with the previous example. Our distributor client isn't ordering one sheet; they're ordering a full container load of 500 sheets to supply to local manufacturers. The 1.03 kg difference per sheet now becomes a total discrepancy of 515 kg (500 sheets × 1.03 kg/sheet). This is over half a ton of steel that is either over- or under-accounted for.
From my position at MFY, I see the cascading consequences of such an error. A 515 kg miscalculation directly impacts:
- Quotation & Costing: The client would be quoted incorrectly, leading to financial disputes upon delivery.
- Shipping & Logistics: International freight is priced by weight. The shipping documents would be inaccurate, potentially causing delays and fines at customs. Container load balancing could also be compromised.
- Inventory Management: The distributor's stock records would be incorrect from the moment the material arrives, causing issues for their own sales and fulfillment processes.
- Client Trust: Most importantly, such errors erode trust. A reliable supply chain is built on accuracy and transparency. We prevent this by embedding the correct, grade-specific density into our ERP system, ensuring every quote and packing list we generate is precise from the start.
Density Variation Within the Same Grade: A Critical Consideration
Even more nuanced is the fact that density can vary slightly even within the same stainless steel grade. Industry standards, such as ASTM specifications for chemical composition, permit a small tolerance range for the elemental composition of any given grade. One batch of SS 316L from one mill might have a slightly different ratio of nickel and molybdenum compared to another batch, both still falling within the 316L specification. This can result in minute variations in their actual density.
For most general fabrication or construction applications, these minor variations are negligible and using the standard nominal density is perfectly acceptable. However, for high-precision industries, this is a critical factor. We once supplied stainless steel sheets to a client manufacturing components for aerospace guidance systems. In their application, the weight and balance of every component were paramount to performance. An unaccounted-for variance of even a few grams could be catastrophic.
In such cases, we don't rely on the nominal density. Instead, we provide the client with the Material Test Certificate (MTC) for the specific production batch] (or "heat") of steel they are purchasing. The MTC provides a detailed chemical analysis of that exact batch. The client's engineering team then uses this precise composition data to calculate a density value that is accurate to several decimal places. This level of detail and documentation is a core part of MFY's commitment to supporting clients in even the most demanding sectors. It’s a testament to the fact that in the world of stainless steel, there is no such thing as a "small" detail.
What factors should be considered when calculating stainless steel weight in kilograms?
Ready to calculate weight, but worried you might be overlooking a critical variable? Simply using a basic formula without considering all factors can lead to flawed estimates. To ensure accuracy, you must account for the material's specific grade, its exact dimensions, and its physical form.
Beyond the basic dimensions, crucial factors for accurate stainless steel weight calculation include the specific grade's density, the manufacturing tolerances for thickness and width, and the form of the product (e.g., sheet, coil, pipe), as each has a unique geometric formula.
A successful calculation is a comprehensive one. It's easy to focus solely on length and width, but the reality of industrial steel products is far more complex. Factors like manufacturing tolerances, which are the acceptable deviations in dimensions allowed during production5, can have a noticeable impact on the final weight of a large order. A steel coil isn't a perfect geometric shape, and a pipe's weight calculation is entirely different from that of a plate. As a global supplier, MFY has built its reputation on managing these complexities for our clients. We once helped a new equipment integrator in India who was struggling to reconcile their calculated weights with our packing lists. The issue wasn't the density, but their failure to account for the nominal vs. actual thickness tolerances of the cold-rolled coils they were ordering. By walking them through the industry standards (like ASTM A480) and how they affect volume, we empowered them to refine their internal costing models and avoid future discrepancies. This holistic view is essential for anyone serious about procurement.
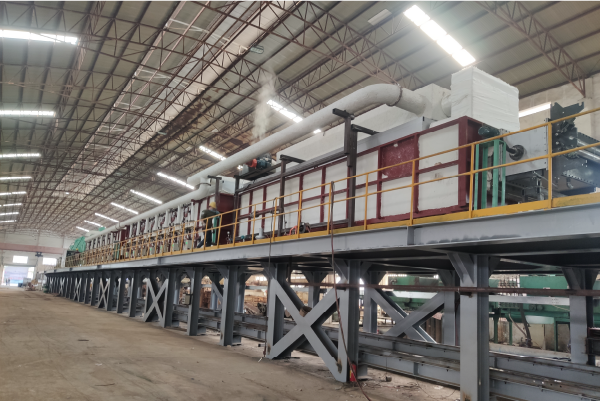
Achieving precision in weight calculation requires a methodical approach that honors the physical realities of the material and its manufacturing process. It's a blend of geometry, material science, and an understanding of industry standards for stainless steel calculation6. Ignoring any one of these components introduces a variable of error that can be costly and disruptive. The professional approach involves a detailed checklist of factors, ensuring every aspect that contributes to the final mass is considered before a purchase order is ever signed. Let's deconstruct these critical factors to build a robust framework for calculation.
Dimensional Accuracy and Unit Conversion
The most fundamental factor is, of course, the product's dimensions. However, precision here is non-negotiable. For a sheet or plate, this means Length (L), Width (W), and Thickness (T). For a pipe, it's the Outer Diameter (OD), Wall Thickness (WT), and Length (L). The cardinal rule is to ensure all units are consistent before any multiplication occurs. Since the standard unit for stainless steel density is kilograms per cubic meter (kg/m³), the most reliable practice is to convert all measurements into meters first.
A common source of error we see with new clients is the mishandling of millimeters. For example, a 2mm thick sheet must be entered into the volume formula as 0.002 meters. Forgetting this simple conversion can lead to an error by a factor of 1000—a catastrophic miscalculation. I recall a case with a distributor where their internal system was misconfigured, treating millimeters as centimeters. This led to a weight estimate that was ten times too low, causing major confusion during the budgeting phase. At MFY, our online tools and quoting systems have built-in unit conversion logic to prevent these basic but costly mistakes, ensuring a seamless and accurate process for our clients.
Furthermore, it's crucial to distinguish between nominal and actual dimensions. A sheet sold as "2mm thick" will have a manufacturing tolerance. Depending on the standard (e.g., ASTM, EN), the actual thickness could be slightly more or less. For bulk orders, especially of coils, we often work with clients to clarify whether calculations should be based on the nominal thickness or the theoretical minimum thickness, as this can impact total weight and cost significantly.
The Impact of Product Form (Sheet, Pipe, Coil)
The shape of the stainless steel product dictates the correct formula for calculating its volume. A one-size-fits-all approach does not work. Each form has its own geometric reality, and using the wrong formula is a guaranteed path to an incorrect weight calculation. As a diversified supplier, MFY deals with these different forms daily, and we ensure our clients use the appropriate calculation for their specific product.
For a simple rectangular sheet or plate, the formula is straightforward:
- Volume (Sheet/Plate) = Length × Width × Thickness
For pipes or tubes, the calculation must account for the hollow center. The volume is the volume of the outer cylinder minus the volume of the inner cylinder:
- Volume (Pipe) = [π × (OD/2)² - π × (ID/2)²] × Length, where ID = OD - 2 × Wall Thickness. A more common industry formula is: Weight (kg/m) = (OD - WT) × WT × 0.02466 for austenitic grades (the constant changes slightly for other grades).
For stainless steel coils, the calculation is essentially the same as for a very long, wide sheet. The weight is typically determined by:
- Weight (Coil) = Width (m) × Thickness (m) × Length (m) × Density (kg/m³). However, since the length of a coil can be hundreds of meters, it's often more practical to work with the total weight provided by the mill, which is measured on a calibrated scale.
Grade-Specific Density and Manufacturing Tolerances
As extensively discussed, the single most important material-specific factor is the density of the stainless steel grade. Never use a generic "stainless steel" density. Always confirm the grade (e.g., 304, 316L, 430, 2205) and use the corresponding standard density. For a project involving multiple grades, the weight for each must be calculated separately before being summed. A client in the manufacturing sector fabricating large tanks might use Grade 304 for the main body but a more corrosion-resistant Grade 316L for the nozzles and fittings. Calculating the total weight requires two separate sets of calculations using two different densities.
Beyond density, manufacturing tolerances introduce another layer of complexity. No manufacturing process is perfect; there will always be slight variations in the final dimensions. For example, ASTM A480/A480M, a key standard for stainless steel plate, sheet, and strip, specifies allowable tolerances for thickness. A 1mm thick sheet might have a tolerance of ±0.05mm. When ordering hundreds of tons, this 5% potential variance in thickness can have a real impact on the total weight.
Experienced procurement managers and engineers account for this. When planning a project, they may calculate weight based on the nominal thickness for budgeting but will be aware that the actual delivered weight on the final invoice may differ slightly. At MFY, we promote transparency by making clients aware of these standards. On our MTCs and packing lists, we provide the actual measured weight, ensuring that our clients are billed for exactly the amount of material they receive, fostering a relationship built on trust and accuracy.
What common mistakes are made during stainless steel weight calculation and how to avoid them?
Are your weight calculations consistently off, causing friction with your finance and logistics teams? These persistent errors often arise from a few common, yet easily avoidable, mistakes. By identifying these pitfalls—like unit conversion errors or using the wrong density7—you can eliminate inaccuracies for good.
Common mistakes in stainless steel weight calculation include using incorrect units (e.g., mm instead of m), applying a generic density for all grades, ignoring manufacturing tolerances, and using the wrong formula for different product forms like pipes or coils. These are avoided through careful unit conversion and grade-specific data.
In my years of experience in the global steel trade, I've seen how small oversights can snowball into significant operational problems. The most frequent errors are not complex engineering miscalculations but simple lapses in diligence. The pressure to generate quick quotes or material lists often leads people to take shortcuts, like grabbing a generic density value from a web search or forgetting to convert inches to millimeters. A classic case involved a client who calculated the weight for a large order of SS 316 pipe but used the formula for a solid bar. The resulting weight estimate was nearly double the actual weight, causing unnecessary alarm in their finance department and almost leading them to lease extra warehouse space they didn't need. These are not just mathematical errors; they are business errors with real-world costs. Avoiding them requires building a systematic, detail-oriented process, a discipline we instill in our own teams at MFY to protect our clients from these preventable headaches.
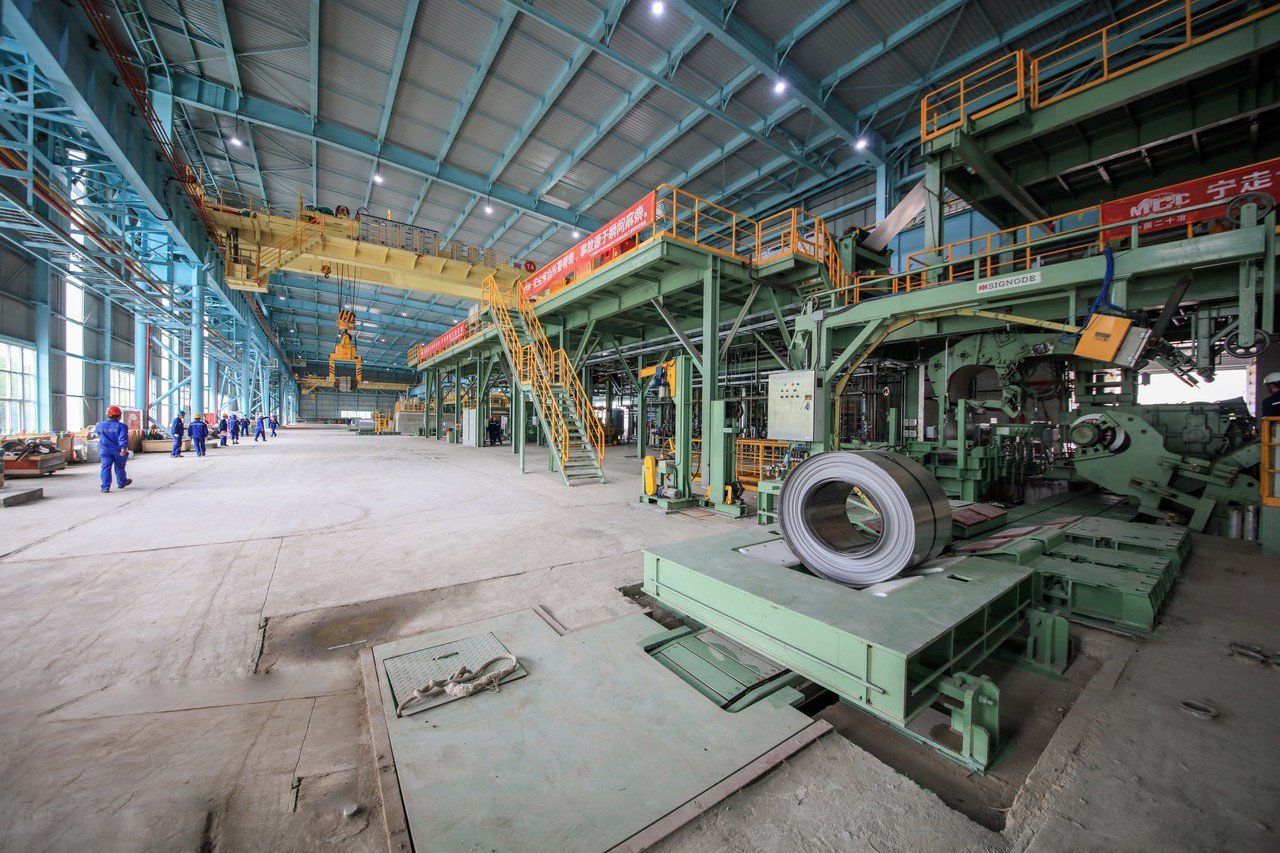
Precision in business is a habit, not an accident. When it comes to stainless steel weight calculation, cultivating this habit means creating a standardized process that actively prevents the most common errors. It involves moving beyond a casual approach and implementing rigorous checks and balances. By understanding the psychology behind these common mistakes—often haste and assumption—we can build robust systems and mental checklists to counteract them. The goal is to make accuracy the path of least resistance. Let's break down the most frequent blunders and establish clear, actionable strategies to eliminate them from your workflow permanently.
Error 1: Unit Conversion Catastrophes
This is arguably the most common and most devastating mistake. The weight formula's integrity depends entirely on the consistency of the units used. The standard formula relies on volume in cubic meters (m³) and density in kilograms per cubic meter (kg/m³). When dimensions are provided in millimeters (mm), inches ("), or feet ('), they must be converted to meters before any calculation begins.
A frequent blunder is confusing millimeters and meters. For a 3mm thick plate, the thickness value in the formula must be 0.003m. Using '3' instead of '0.003' will result in a weight calculation that is 1000 times too high. Similarly, failing to correctly convert from imperial to metric units is a major pitfall, especially in global trade. A US-based contractor might specify a pipe with a 1/2-inch wall thickness, which must be accurately converted to 12.7mm and then to 0.0127m.
How to Avoid It:
- Standardize Your Process: Create a calculation template or spreadsheet where the first step is always to convert all input dimensions into meters.
- Use Conversion Tools: Employ reliable online conversion calculators or software with built-in unit conversion functions. Double-check the conversion factors (e.g., 1 inch = 0.0254 meters).
- Sanity Check: After calculating, perform a quick mental check. Does the number seem reasonable? A single sheet of steel shouldn't weigh thousands of kilograms. This simple final review can catch most major unit conversion errors.
Error 2: The "One-Density-Fits-All" Assumption
The second most common mistake is using a generic, non-specific density value for all types of stainless steel. As we've established, the density of a ferritic grade like 430 (~7700 kg/m³) is significantly different from an austenitic grade like 316L (~8000 kg/m³). Using an average or incorrect value introduces an immediate, built-in error of up to 4% or more. On a 100-ton order, that's a 4-ton discrepancy.
This error often happens when someone searches for "stainless steel density" online and uses the first result without verifying the grade. It's a shortcut that undermines the entire calculation. We once had a purchasing agent from a manufacturing company question our invoice, stating our shipped weight was higher than their calculation. The issue was traced back to them using the density of carbon steel for a shipment of Grade 304 stainless steel coil, a fundamental material mix-up.
How to Avoid It:
- Be Grade-Specific: Always identify the exact grade of stainless steel being ordered.
- Use a Reliable Density Chart: Maintain a trusted reference chart (like the one provided earlier) that lists the standard densities for common stainless steel grades.
- Check the MTC: For high-precision or large-tonnage orders, request the Material Test Certificate (MTC) from your supplier. This document provides the most accurate chemical composition from which a precise density can be derived. At MFY, providing the MTC is a standard part of our quality guarantee.
Error 3: Ignoring the Product's True Form and Tolerances
This mistake involves a failure of geometric and practical understanding. A buyer might use the simple (L × W × T) formula for a product that isn't a simple plate, like a checkered plate, a perforated sheet, or a pipe. Checkered plates, for example, have a raised pattern that adds weight beyond the base plate thickness. Perforated sheets, conversely, have material removed, making them lighter.
Equally important is ignoring manufacturing tolerances. A client might calculate the weight of 1,000 plates based on the nominal thickness of 5mm. However, if the manufacturing tolerance allows the actual thickness to be up to 5.2mm, the actual shipped weight will be higher than their estimate. While this is a normal part of the industry, failing to account for it in budgeting can lead to confusion and perceived cost overruns.
How to Avoid It:
- Use the Correct Formula: Ensure you are using the right geometric formula for the product's shape (plate, pipe, bar, etc.).
- Account for Modifications: For non-standard items like checkered or perforated plates, consult with the supplier for the correct weight per square meter, as a simple volume calculation won't work.
- Discuss Tolerances: Have a clear conversation with your supplier about manufacturing tolerances. Understand the potential variance between nominal weight and actual weight, and factor this potential difference into your project budget as a contingency. A good supplier will be transparent about these industry standards.
What tools and formulas are recommended for precise weight calculation of stainless steel?
Tired of manual calculations and the risk of human error? In today's fast-paced industry, relying on pen and paper is inefficient and risky. Leveraging specialized tools and standardized formulas is the professional’s choice for achieving both speed and unerring accuracy in every calculation.
For precise weight calculation, it is recommended to use validated online weight calculators or integrated ERP software, combined with standardized formulas. The key formulas are: (L × W × T × ρ) for sheets, and ((OD - WT) × WT × C) for pipes, where C is a grade-specific constant.
In the modern supply chain, efficiency and accuracy are competitive advantages. While understanding the manual formulas is crucial for foundational knowledge, day-to-day operations demand faster and more reliable solutions. At MFY, we've integrated sophisticated weight calculation logic directly into our digital platforms, from our internal ERP to the client-facing portals on our website, www.mfysteel.com. This removes the burden of manual calculation and minimizes the risk of human error for our customers. For example, a distributor can configure a complex order of multiple grades and forms (coils, sheets, pipes) and receive an instantaneous, accurate total weight and cost estimate. This automation not only speeds up the procurement process but also provides a level of precision that is difficult to achieve manually, especially for large and complex orders. These tools are no longer a luxury; they are a necessity for efficient global trade.
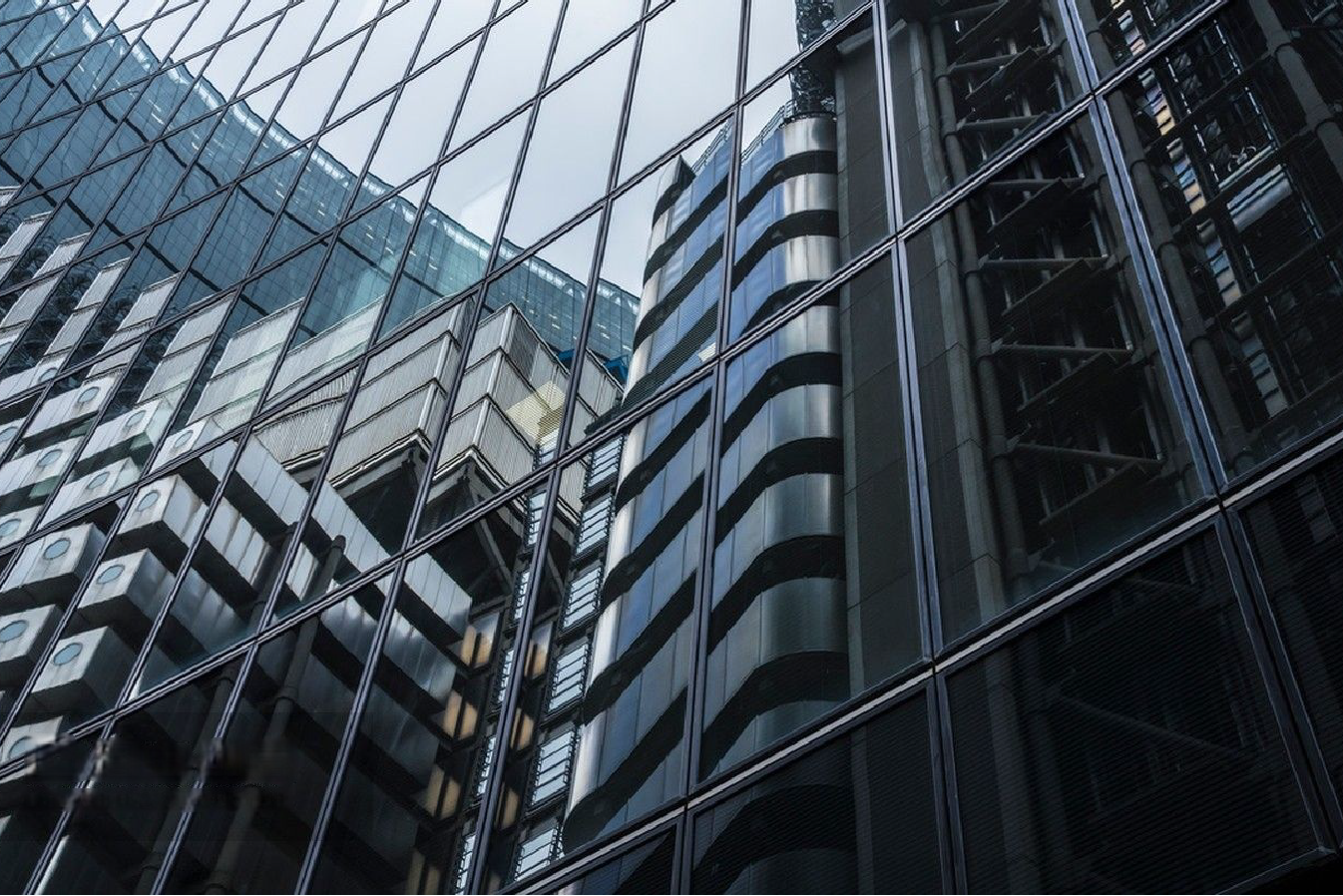
Adopting the right tools is about more than convenience; it’s a strategic decision to de-risk your procurement process. The ideal toolkit combines the power of digital automation with a solid understanding of the underlying mathematical principles. Relying solely on a “black box” calculator without knowing how it works can be dangerous, while sticking to manual methods is inefficient. The optimal approach is a synthesis of the two: using trusted digital tools for execution while retaining the knowledge to validate their outputs8 and understand their parameters. This creates a robust system that is both fast and transparent.
Essential Formulas for Common Product Forms
Every professional in the steel industry should have a firm grasp of the core formulas for the most common product shapes. These formulas are the engine inside every weight calculator. Knowing them allows you to perform quick estimates, double-check a tool’s output, and understand how different variables impact the final weight.
1. For Stainless Steel Sheets and Plates:
The most straightforward calculation.
- Formula:
Weight (kg) = Length (m) × Width (m) × Thickness (m) × Density (kg/m³)
- Example: For a 304 grade sheet (ρ ≈ 7930 kg/m³) of 2.5m × 1.25m × 0.002m:
Weight = 2.5 × 1.25 × 0.002 × 7930 = 49.56 kg
2. For Stainless Steel Pipes and Tubes:
This requires a specific formula that accounts for the circular cross-section. A widely used industry shortcut simplifies the complex geometry.
- Formula:
Weight per Meter (kg/m) = (Outer Diameter (mm) - Wall Thickness (mm)) × Wall Thickness (mm) × C
Where ‘C’ is a constant that depends on the material’s density. For austenitic stainless steel (304/316), C ≈ 0.02466. For ferritic stainless steel (430), C is slightly lower, around 0.0243. - Example: For a 316 pipe (C ≈ 0.02466) with 60mm OD and 3mm WT:
Weight/m = (60 - 3) × 3 × 0.02466 = 57 × 3 × 0.02466 = 4.22 kg/m
3. For Stainless Steel Bars (Round/Square):
- Round Bar Formula:
Weight (kg) = π × (Diameter (m)/2)² × Length (m) × Density (kg/m³)
- Square Bar Formula:
Weight (kg) = Side (m)² × Length (m) × Density (kg/m³)
Leveraging Online Weight Calculators
For quick, reliable calculations without the risk of manual error, online weight calculators9 are an invaluable resource. Many reputable steel suppliers, including MFY, offer these tools on their websites. A good online calculator provides a user-friendly interface where you can simply select the material grade, the product form, and input the dimensions.
The key advantages of using a trusted online calculator are:
- Speed: It provides instantaneous results.
- Accuracy: It uses pre-programmed, grade-specific densities and correct formulas, eliminating guesswork.
- User-Friendliness: It handles unit conversions automatically, reducing the primary source of manual error.
As a case in point, we often direct our clients—from large engineering contractors to smaller distributors—to the calculator on our website (www.mfysteel.com). This not only empowers them to independently estimate costs for various scenarios but also ensures that when they come to us with a request for quotation, their preliminary numbers are already aligned with our own, making the entire process smoother and more transparent. When choosing a calculator, ensure it is from a reputable industry source to guarantee the data and formulas it uses are up-to-date and accurate.
The Ultimate Tool: Integrated ERP and Quoting Systems
For businesses that procure steel regularly, the most powerful tool is a sophisticated Enterprise Resource Planning (ERP) system with integrated material calculation capabilities. This is the solution we employ internally at MFY and represents the gold standard for industrial supply chain management.
An integrated system connects the entire workflow. When our sales team enters a client’s request, they select the product, grade, and dimensions. The system automatically pulls the correct density, applies the appropriate formula, and calculates the precise weight. This data then flows seamlessly through the entire process:
- Quotation: Generates an accurate quote based on weight.
- Inventory: Deducts the correct tonnage from our available stock.
- Logistics: Creates a packing list with precise weights for shipping and customs.
- Invoicing: Bills the client for the exact amount of material shipped.
This level of integration eliminates data entry errors, ensures consistency across all departments, and provides a single source of truth for every transaction. For our clients, this means faster response times, highly accurate documentation, and a level of reliability that builds lasting partnerships. It transforms weight calculation from a simple task into a strategic component of a fully digitized and efficient supply chain.
Conclusion
Ultimately, mastering stainless steel weight calculation is a function of precision. By using grade-specific densities, correct formulas for each product form, and leveraging reliable digital tools, you can eliminate costly errors and ensure your project's budget and logistics are built on a foundation of accuracy.
-
Learn why precise weight impacts both logistics budgeting and structural safety in projects ↩
-
Find practical examples of errors and savings when using or omitting real density data ↩
-
Learn how density affects stainless steel weights and its impact on your procurement accuracy ↩
-
Understand real logistics considerations when shipping large quantities of stainless steel ↩
-
Learn how dimensional tolerances impact large-order steel weight and cost planning ↩
-
Understand the standards shaping accurate calculation processes for different stainless steel products ↩
-
Learn about how unit and density errors can disrupt stainless steel weight calculations and accuracy. ↩
-
Learn the value of combining digital automation with manual formula understanding for accuracy and transparency ↩
-
Discover key characteristics of reputable and precise weight calculation tools for the steel industry ↩
Have Questions or Need More Information?
Get in touch with us for personalized assistance and expert advice.