Slitting Stainless Coil: Burr Control & Tolerance
Are you struggling with inconsistent quality from your slitting operations? Burrs, poor tolerance, and surface defects can compromise your final product, leading to waste and customer complaints. Mastering the slitting process by controlling these variables is crucial for efficiency and maintaining a competitive edge in the market.
Slitting stainless steel coils to control burrs and maintain tight tolerances involves a precise combination of factors. Primarily, it requires optimizing the slitting machine's setup, including correct knife clearance, sharp and high-quality tooling, and appropriate tension settings, all tailored to the specific grade and thickness of the stainless steel.
This balance is often easier said than done. It’s a delicate interplay between the machinery, the material, and the operator's skill. Achieving that perfect, clean edge consistently requires more than just following a textbook guide; it demands a deep understanding of the nuances of metal behavior under stress. It's a craft we've honed over years of production at MFY.
In my years leading MFY's global business, I've seen how slitting is often underestimated. It's not merely cutting a large coil into smaller ones; it's a foundational process that dictates the quality of subsequent manufacturing stages. A seemingly minor issue like a burr can cause major downstream problems, from damaging forming dies to creating safety hazards on an assembly line. This guide moves beyond simple definitions, offering a critical look at the mechanics of slitting, backed by industry data and practical experience1, to help you achieve the precision your operations demand.
What are the common challenges associated with slitting stainless steel coils?
The path from a master coil to perfectly slit strips is filled with potential pitfalls. These challenges, from burrs to camber, can disrupt production schedules and inflate costs. Overcoming them requires a proactive approach to diagnostics and process control, turning a potential liability into a competitive advantage.
Common challenges in slitting stainless steel coils include managing burr formation, maintaining strict width and thickness tolerances, preventing surface defects like scratches and coil marks, and controlling coil-induced stresses that lead to shape issues such as camber, crossbow, and wavy edges, which impact downstream processes.
Recognizing these challenges is the first step, but truly understanding their root causes and interplay is where operational excellence begins. Many manufacturers treat these issues in isolation, fixing one only to find another has worsened. For instance, increasing slitting speed to boost output might exacerbate burr formation or induce more stress, leading to camber. A client of ours, a large-scale producer of automotive components in India, faced this exact dilemma. They were trying to meet higher production targets, but their rejection rate skyrocketed due to slit edges not meeting the stringent requirements for automated welding lines. The burrs were causing misalignment and inconsistent welds. This experience taught us that a holistic view is essential. You cannot address tolerance without considering burr control, nor can you ignore material properties when setting up your machinery. Each element is a piece of a larger puzzle. In the following sections, we will dissect these challenges, exploring not just what they are, but why they occur and how they are interconnected, providing a comprehensive framework for troubleshooting and optimization.
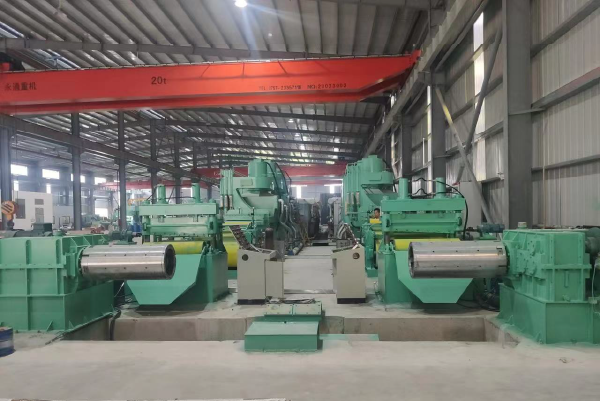
The Hidden Costs and Dangers of Burr Formation
Burrs are more than just a cosmetic flaw; they represent a significant financial and operational risk. In my experience, many businesses initially underestimate the cascading impact of burr formation. A typical burr height limit for precision applications might be as low as 10% of the material's thickness. For a 1mm thick 304 stainless steel strip, this means burrs must be under 0.1mm. Exceeding this can lead to a domino effect of problems. For example, in automated assembly lines, sharp burrs can snag on guides, rollers, and other components, causing costly jams and downtime. We worked with a manufacturer of commercial kitchen equipment whose automated panel bending machines were constantly being misaligned by burred edges, leading to unacceptable panel gaps in their final products.
Beyond the machinery, burrs pose a serious safety risk. Slit stainless steel edges are already sharp, but burrs make them razor-like and unpredictable, leading to a higher incidence of lacerations for handlers, packers, and assemblers. This increases liability and can negatively impact team morale and productivity. The hidden costs also accumulate in material waste. If a portion of a coil is deemed out of spec due to excessive burrs, it often has to be scrapped or re-processed, both of which erode profit margins. This is particularly costly with higher-value stainless steel grades, where every meter of scrap represents a significant loss.
The final, and perhaps most critical, cost is to a company's reputation. Delivering a product with inconsistent or dangerous edges signals poor quality control. For our clients in sectors like medical devices or high-end electronics, where precision and safety are non-negotiable, a burred edge is not just a defect—it's a dealbreaker. It reflects poorly on the entire supply chain, and as a supplier, we at MFY understand that the quality of our slit coil directly impacts our customers' final product and their standing in the market.
The Intricate Battle for Dimensional Accuracy
Achieving precise dimensional accuracy in slitting is a constant battle against the inherent properties of the metal and the limitations of the machinery. The three primary demons we fight are camber, crossbow, and width deviation. Camber, the tendency of a slit strip to curve edge-wise like a banana, is often caused by non-uniform internal stresses within the master coil or uneven pressure from the slitting knives. A study by the Metals Service Center Institute (MSCI)2 indicated that even a slight variation in hardness across the width of a master coil can induce enough stress during slitting to cause significant camber, especially in thinner gauge materials. For a client producing long, narrow channels for window frames, excessive camber meant the strips wouldn't feed correctly into their roll-forming machines, causing massive production delays.
Crossbow, the transverse arching of a strip, is another stress-related issue, often stemming from the coiling process itself. When the coil is slit, these trapped stresses are released unevenly, causing the material to warp. Width tolerance is perhaps the most obvious metric, but it is incredibly sensitive. Factors like knife wobble, arbor deflection, and even thermal expansion during a long run can cause deviations. For a 25mm wide strip, a typical commercial tolerance might be ±0.15mm, but for high-precision applications like stamping electronic connectors, clients may demand ±0.05mm or less.
Maintaining these tight tolerances requires a slitting line that is not only precise but also incredibly rigid and stable. The quality of the machine build, the rigidity of the arbors, and the precision of the tensioning system are paramount. At MFY, our investment in state-of-the-art slitting lines is a direct response to this challenge. We’ve found that using computer-controlled tensioners and knife-positioning systems3 provides a level of consistency that manual setups simply cannot match. It’s an ongoing process of measurement, feedback, and adjustment to counteract the natural tendencies of the steel.
Preserving a Flawless Finish: Surface Integrity
For many applications, particularly in architectural and consumer products, the aesthetic finish of stainless steel is its primary selling point. The slitting process, however, is fraught with risks that can mar this finish. The most common surface defects introduced during slitting are scratches, scuffs, and pressure marks. Scratches can be caused by contact with inadequately polished or worn-out tooling, guides, or even debris embedded in the separator arms of the recoiler. Even the smallest chip on a slitting knife can create a faint but continuous scratch along the entire length of a coil, rendering it useless for a decorative application.
Pressure marks or "coil breaks" are another concern. These are subtle, transverse ridges caused by improper tensioning or bending the material too sharply. When slitting, the tension applied between the uncoiler and the recoiler must be carefully controlled. Too little tension and the slit strips may not track straight, leading to width variations. Too much tension, especially on softer austenitic grades like 304, can stretch the material beyond its elastic limit, causing permanent deformation and altering its mechanical properties. This is a delicate balancing act that requires sophisticated tension control systems.
To mitigate these risks, a multi-faceted approach is necessary. We often use protective PVC or PE films on the stainless steel surface4, which are applied before slitting and remain on until the final fabrication stage. This provides a robust barrier against mechanical damage. Furthermore, the choice of tooling and equipment is critical. Using highly polished separator discs made from materials like Delrin® or felt-covered steel can prevent scratching on the recoiled strands. The table below outlines some common slitting defects and their mitigation strategies, illustrating the systematic approach required.
Defect Type | Common Cause(s) | Impact on Product | Mitigation Strategy |
---|---|---|---|
Burr | Incorrect knife clearance; dull knives. | Safety hazard; poor fit-up; tool damage. | Optimize clearance (8-12% of thickness); regular knife sharpening. |
Camber | Uneven internal stress; non-parallel knives. | Feeding issues in automated lines. | Use stress-relieved coils; precise machine alignment. |
Scratches | Worn/damaged tooling; debris. | Poor aesthetic appearance; corrosion point. | Use polished tooling; apply protective film; regular cleaning. |
Coil Breaks | Excessive tension; small bending radii. | Surface imperfections; altered properties. | Implement precise tension control; use larger diameter rollers. |
Why do burrs form during the slitting process of stainless steel coils?
You've identified burrs as the problem, but do you know why they truly appear? It's not random. This uncontrolled tearing of metal is a direct result of process parameters clashing with material properties. Understanding this fundamental conflict is the key to preventing it from happening in the first place.
Burrs form during slitting because the process is a combination of shearing and fracturing metal. When the clearance between the upper and lower knives is incorrect, or if the blades are dull, the metal is pushed and bent rather than cleanly sheared, causing an uncontrolled fracture that results in a burr.
The formation of a burr is a microscopic event with macroscopic consequences. It's a clear signal that the slitting process is not optimized. Many operators fall into the trap of addressing the symptom—the burr—by making arbitrary adjustments. They might tighten the clearance or speed up the line, hoping for a quick fix. However, without understanding the underlying mechanics, these changes can be counterproductive, potentially leading to excessive tool wear, increased internal stress in the material, or even new defects5. I recall a case with a new operator who, frustrated with burrs on a batch of 430-grade stainless steel, kept reducing the knife clearance. This actually work-hardened the edge of the strip, created secondary shear (a shiny, smeared edge), and ultimately caused the knives to chip. The science of it is fascinating and critical. The process involves creating a deliberate, controlled fracture. When that control is lost, the burr is born. In the next section, we'll delve into the physics of this shear-fracture zone and explore the three variables that absolutely must be mastered: clearance, tooling, and material behavior.
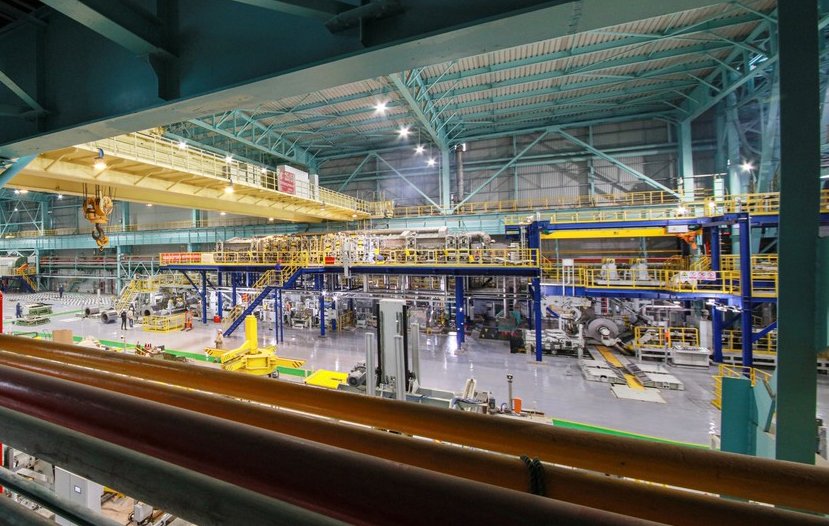
The Mechanics: Deconstructing the Shear-Fracture Zone
To control burrs, one must first visualize what happens to the steel at the point of contact with the knives. The slitting action is not a simple cut like with scissors. It's a rapid, high-pressure event that happens in two distinct phases: shearing and fracture. In the first phase, as the sharp, rotating knives penetrate the material, they displace the steel in a plastic deformation zone. This is the 'shear' phase. A clean shear is characterized by a shiny, burnished surface on the edge of the slit strip, typically extending through 10% to 40% of the material's thickness. This is the ideal portion of the cut.
The second phase is the 'fracture'. Once the stress induced by the knives exceeds the material's ultimate tensile strength, the remaining material fractures apart. The goal of precision slitting is to make this fracture as clean and predictable as possible. A burr is essentially an uncontrolled fracture. It's the lip of metal that gets pushed and torn away instead of breaking off cleanly. The size and characteristics of the burr are dictated by how these two zones are managed. An optimized process results in a very small fracture zone with a minimal burr, while a poorly controlled process results in a small shear zone and a large, ragged fracture zone, creating a significant burr.
Understanding this two-phase process is crucial for diagnostics. By examining the edge of a slit coil, an experienced operator can "read" the cut. A large burnished area might indicate the clearance is too tight, while a very rough, granular edge with a heavy burr points to excessive clearance. We train our technicians at MFY to analyze the slit edge profile as a primary indicator of process health, allowing for rapid adjustments before an entire coil is compromised. This microscopic analysis prevents macroscopic failures.
The Cardinal Rule: Mastering Horizontal and Vertical Knife Clearance
If there is one parameter that governs burr formation above all others, it is the clearance between the slitting knives. This clearance exists in two dimensions: horizontal and vertical6. Horizontal clearance is the gap between the edges of the top and bottom knives. This is the most critical setting. If the clearance is too small, the knives will create a secondary shear, essentially pinching and wiping the edge, which can lead to rapid tool wear and a work-hardened edge. If the clearance is too large, the metal is effectively bent until it snaps, resulting in a large fracture zone and a correspondingly large burr. The rule of thumb for stainless steel is to set the horizontal clearance at approximately 8-12% of the material's thickness. However, this is not a fixed law.
This percentage needs to be adjusted based on the steel's properties. For instance, softer austenitic grades like 304 might require slightly more clearance than harder martensitic grades like 420. We use precise gauges and even microscopic analysis to set our clearances, as even a hundredth of a millimeter can make a difference. Vertical clearance, or the degree of overlap between the top and bottom knives, is also critical. Insufficient overlap will not generate enough force to complete the fracture, while excessive overlap increases the lateral forces on the knives, which can cause them to deflect and lead to inconsistent burr and width variations.
The challenge is that the ideal clearance is a moving target. It is influenced not just by material thickness and grade, but also by the condition of the tooling and the rigidity of the slitting head. As knives wear, their sharp edges become rounded, which effectively changes the shearing dynamic and may require a clearance adjustment to compensate. This is why a "set it and forget it" mentality is the enemy of quality slitting. It requires constant vigilance and a data-driven approach, where settings are documented, and results are meticulously tracked.
Beyond Clearance: The Influence of Tooling and Material Properties
While clearance is king, the condition of the tooling and the intrinsic properties of the stainless steel itself are powerful co-conspirators in burr formation. The sharpness of the knives cannot be overstated. A dull knife does not shear; it plows. It pushes and deforms the metal with brute force rather than slicing it with precision. This plowing action dramatically increases the bending moment before fracture, which is a primary driver of burr height. We maintain a strict regimen for our tooling, where knives are inspected and sharpened or replaced based on the volume and type of material they have processed, not just on a fixed time schedule.
The material of the knives7 is also a key variable. High-carbon, high-chromium tool steels like D2 are a common choice, offering a good balance of hardness and toughness. However, for high-volume slitting of abrasive or hard stainless steel grades, carbide-tipped knives are often a better investment. Though more brittle and expensive, their superior wear resistance means they hold a sharp edge for much longer, providing greater consistency and reducing burr formation over the course of a long production run.
Finally, the work-hardening characteristic of the stainless steel itself8 plays a huge role. Austenitic grades, such as 304 and 316, are notoriously prone to work hardening. During the slitting process, the deformation caused by the knives hardens the material almost instantly. This means that a dull knife or incorrect clearance will not only create a burr but also a hardened edge that can be problematic for subsequent forming or machining operations. This is why slitting stainless steel is so much more challenging than slitting plain carbon steel—the material actively fights back against the cutting process.
How does burr formation affect the quality and tolerance of the final product?
A small burr might seem like a trivial imperfection, but its impact ripples through the entire manufacturing chain. This seemingly minor flaw can compromise dimensional accuracy, jeopardize safety, and ultimately tarnish the quality of your finished product. Ignoring it is not an option for any high-performance application.
Burr formation directly degrades product quality by creating sharp, hazardous edges that interfere with assembly and handling. It also compromises tolerance, as the burr height can effectively alter the strip's functional width and thickness, leading to poor fit-up in automated processes and dimensional rejection of the final part.
The relationship between burrs, quality, and tolerance9 is intimate and unforgiving. Think of the burr as an uncontrolled variable that throws off all subsequent measurements and processes. For example, when measuring the width of a slit strip, does the measurement include the burr? If so, the strip might appear to be within tolerance, but the usable, burr-free width is actually smaller. This discrepancy is a common source of conflict between suppliers and customers. A client of ours in the electronics sector, who produces precision-stamped enclosures, had to reject an entire shipment from a previous supplier because the burrs, though small, were preventing the components from seating correctly in their high-speed stamping dies. This led to intermittent jamming and damage to their multi-thousand-dollar tooling. This illustrates that the true measure of quality is not just meeting a number on a caliper but ensuring the material is fit for its intended purpose. The burr is a direct impediment to that fitness for purpose.
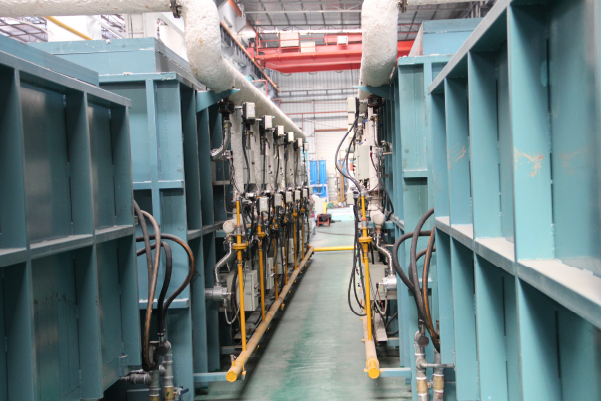
Interference in Automated Processes and Assembly
In the age of Industry 4.0 and lean manufacturing10, automated systems are the backbone of efficiency. These systems, however, are built for precision and consistency; they are not designed to accommodate random imperfections like burrs. When a burred stainless steel strip is fed into a roll-forming line, a stamping press, or an automated welding station, a cascade of problems can occur. The burr can snag on guides, causing the material to misfeed and jam the entire line. This leads to immediate production losses and requires manual intervention, defeating the purpose of automation.
I visited a customer's facility in Southeast Asia where they manufacture stainless steel tubing. The slit strip they were using had a significant burr, and this burr was scratching the inside of the forming dies as the strip was shaped into a tube. Over time, these scratches on the die transferred to the outside of the tube, creating an unacceptable cosmetic defect. Furthermore, in the subsequent orbital welding process, the burr created an inconsistent gap between the edges, resulting in weak or incomplete welds, a critical failure for a product designed to carry fluids under pressure. The problem wasn't the welding or the tube mill; the root cause was the poor edge quality of the initial slit coil.
This demonstrates how a burr acts as a source of dimensional "noise" and tolerance stack-up11. It prevents parts from fitting together correctly, a phenomenon known as "tolerance stack-up." In a complex assembly with multiple components, even a tiny burr on each part can accumulate, leading to significant misalignment in the final product. For manufacturers of everything from appliances to aerospace components, where fit and finish are paramount, a burr-free edge is not a luxury—it is a fundamental requirement for process stability and product integrity.
Compromising Dimensional Tolerance and Measurement
Burrs create a significant ambiguity in dimensional measurement, which directly impacts tolerance compliance. When an inspector measures the width of a slit strip with a caliper or micrometer, the presence of a burr can easily lead to an inaccurate reading. If the jaws of the caliper press against the burr, the measured width will be larger than the actual functional width of the strip. Conversely, if the operator tries to avoid the burr, the measurement might not capture the true maximum dimension. This inconsistency makes quality control a nightmare. According to a quality control report from a major metal service center, disputes over width measurements due to burrs account for over 15% of all quality claims related to slit coils.
This problem is magnified in applications requiring tight tolerances. Consider a manufacturer of gaskets or shims, where thickness and width must be controlled to within a few microns. The height of the burr itself can be greater than the entire tolerance band for the part. For example, if a 0.5mm thick shim has a width tolerance of ±0.02mm, a burr of just 0.03mm height makes it impossible to verify if the part is dimensionally correct. The part is, by definition, out of spec the moment the burr is formed.
At MFY, we address this by defining edge quality as a specific parameter on our certificates of analysis. We don't just provide a width measurement; we provide a guarantee of burr control, often specifying a maximum allowable burr height (e.g., <0.05mm). This removes ambiguity and ensures our clients receive material that is not only dimensionally accurate on paper but is also functionally perfect for their application. True tolerance control is not just about hitting a number; it's about delivering a clean, usable edge.
Safety Hazards and Downstream Surface Damage
Beyond the technical and dimensional aspects, burrs are a critical safety issue12. The sharp, jagged edge of a burr on a stainless steel strip is a significant laceration hazard for anyone who handles the material, from the slitting line operator to the parts assembler on the factory floor. This increases the risk of workplace injuries, which carries direct costs in the form of medical expenses and lost workdays, as well as indirect costs like higher insurance premiums and lower employee morale. Companies with strong safety cultures place a high premium on sourcing burr-free material as a proactive measure to protect their teams.
Furthermore, the burr can cause damage to the product itself. During the recoiling process after slitting, the burr on one wrap of the coil can press into the finished surface of the wrap below it. This can create a line of indentations or scratches along the entire length of the coil, a defect known as "burr-scratching." This is especially problematic for stainless steel with decorative finishes, such as a No. 4 brushed or No. 8 mirror finish. A single burr can ruin the aesthetic value of an entire coil.
We once had to troubleshoot an issue for a client making high-end elevator interiors. They were experiencing faint, repetitive line marks on their brushed stainless steel sheets. After a thorough process audit, we traced the problem back to their slitting process. A slightly worn knife was creating a small but consistent burr, and during recoiling, this burr was embossing a "scar" onto the next layer of steel. By implementing a stricter tool maintenance schedule and optimizing the slitting parameters, we eliminated the burr and resolved the surface damage issue. This case was a powerful reminder that the quality of an edge has a direct impact on the quality of the surface.
What strategies can be employed to minimize burrs during slitting?
Actively minimizing burrs isn't about finding a single magic bullet. It's about implementing a systematic strategy that addresses the core causes of their formation. From tooling to tension, every element must work in harmony. This proactive control is what separates average results from exceptional quality.
To minimize burrs, a multi-faceted strategy is essential. This includes maintaining optimal horizontal and vertical knife clearance tailored to the material, using sharp, high-quality tool steel or carbide knives, ensuring machine rigidity, and applying precise tension control to ensure the stainless steel strip is stable throughout the slitting process.
Moving from a reactive to a proactive approach in burr control marks a significant step up in operational maturity. Instead of simply inspecting and rejecting bad coils, the focus shifts to creating a process that is inherently incapable of producing significant burrs. This involves a deep dive into the entire slitting ecosystem. It’s not just about the operator turning a dial; it’s about the quality of the raw material, the maintenance schedule for the equipment, and the engineering of the tooling. I often tell my team that a perfect slit edge is a reflection of a healthy and well-managed production system. We once helped a customer in the pipe manufacturing industry reduce their burr-related rejection rate by over 80%. We didn't just adjust their slitter; we helped them implement a comprehensive program covering knife management, clearance standards for different steel grades, and operator training13. This holistic strategy is what delivers sustainable, long-term results, which we will explore in detail now.
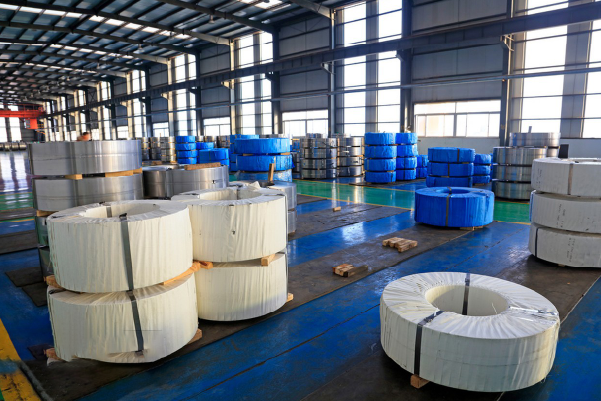
The Foundation: Precision Tooling and Rigorous Maintenance
The frontline defense against burrs is the tooling itself. This strategy begins with the selection of the right slitting knives. While D2 tool steel is a common workhorse, its performance can be insufficient for challenging materials like the work-hardening 300 series stainless steels or very thin-gauge products. In these cases, investing in powdered metal (PM) tool steels or tungsten carbide knives14 can provide a significant return. According to a study by the Fabricators & Manufacturers Association (FMA), carbide knives can maintain a sharp cutting edge up to 10 times longer than D2 steel in certain applications, drastically reducing burr formation over a production run. This longevity ensures process consistency and reduces downtime for tool changes.
However, the best knives in the world are useless if they are not sharp and perfectly maintained. A documented and rigorously enforced knife management program is non-negotiable. This program should include scheduled inspections, sharpening based on usage (e.g., total meters cut or tonnage processed), and precise sharpening protocols. The cutting edge of a slitting knife should have a fine, polished finish, as any grinding marks can transfer to the material. At MFY, our tool room uses specialized grinding machines that ensure the correct angle and surface finish, and every sharpened knife is microscopically inspected before being returned to service.
Furthermore, the setup of the tooling assembly is just as critical as the knives themselves. The spacers that sit between the knives must be ground to an exceptional level of precision; any variation in their thickness will cause the knives to wobble, leading to inconsistent width and burrs. Using a "shimless" tooling setup, where the spacers and knives are ground as a matched set, is a best practice for high-precision slitting. This eliminates the errors and inconsistencies that can arise from using thin, flimsy shims to make adjustments, ensuring the entire tooling arbor is as rigid and accurate as possible.
Dynamic Process Control: Mastering Tension and Speed
Once the tooling is optimized, the next strategic layer is the dynamic control of the slitting process itself, primarily through tension and speed management. The tension applied to the strip as it travels from the uncoiler, through the knives, and to the recoiler is a critical factor in maintaining stability. The goal is to create a "tension bridle," a stable system that pulls the material taut and flat as it enters the slitting head. If the tension is too low, the strip can flutter or wander, causing the knives to engage with the material at an inconsistent angle, which generates burrs. If the tension is too high, it can stretch the material, reduce its thickness, and induce stress that leads to shape defects like camber.
Modern slitting lines employ [sophisticated tension control systems](How do advanced tension control systems work in modern slitting lines to reduce burrs?)15. These often use a "drag generator" on the uncoiler and a variable-speed motor on the recoiler, linked by a control loop that measures and adjusts tension in real-time. A common and effective method is the "pull-through" slitting mode, where the slitting head itself is not powered. The strip is pulled through the stationary knives by the force of the recoiler. This isolates the cutting action from drive-train vibrations and allows for very precise tension control, which is highly effective at minimizing burrs, especially in thin or sensitive materials.
Slitting speed must also be managed strategically. While it is tempting to run the line as fast as possible to maximize throughput, excessive speed can be detrimental to edge quality. Higher speeds generate more heat and vibration, which can accelerate tool wear and cause instability in the strip. The optimal speed is a balance between productivity and quality. For high-strength or thick-gauge stainless steel, a slower speed allows the metal more time to shear cleanly, reducing the fracture component of the cut and thus minimizing the burr. We often advise clients to run trials at different speeds and measure the resulting burr height to find the empirical "sweet spot" for each specific product.
The Role of the Machine: Rigidity and Alignment
The third pillar of this strategy is the slitting machine itself. The most advanced tooling and process controls will be ineffective if the machine they are on is not fundamentally sound. Machine rigidity is paramount. The slitting head, the arbors that hold the tooling, and the machine frame must be incredibly stiff to resist the immense forces generated during slitting. Any deflection or vibration in the machine structure will be transferred directly to the cut, resulting in burrs and tolerance issues. A well-built slitter will have oversized arbors, robust bearing housings, and a heavy, vibration-dampening base.
A key metric for arbor quality is its deflection under load. A high-quality slitting machine might specify a maximum arbor deflection of less than 0.02mm under full load. This ensures that the horizontal clearance set by the operator remains constant during the actual cut. This rigidity is what allows for the use of shimless tooling and the maintenance of extremely tight tolerances. Regular maintenance and alignment checks are essential to preserve this designed-in precision. The parallel alignment of the uncoiler, slitting head, and recoiler must be verified periodically. Any misalignment can cause the strip to track improperly, inducing stress and leading to camber and poor edge quality.
ly, the design of the slitting head itself is a factor. Many modern machines feature interchangeable heads, allowing for tooling to be set up offline while the machine is still running another job. This not only boosts productivity but also allows for more careful and precise tooling setups in a dedicated, controlled environment. Features like "turret" or "cassette-style" slitting heads enable these quick changes. Investing in a machine with high rigidity and features that promote precision setup is a cornerstone of any effective burr minimization strategy.
What are the best practice guidelines for maintaining tolerance in slitting operations?
Maintaining tight tolerances in slitting isn't a matter of luck; it's the result of disciplined adherence to best practices. When every part of the process, from setup to execution, is governed by precision, consistent quality becomes the standard. This discipline is the bedrock of reliable manufacturing.
Best practices for maintaining slitting tolerance include using high-precision, shimless tooling on rigid, low-deflection arbors, implementing meticulous setup procedures with calibrated gauges, controlling strip tension precisely, and conducting regular machine alignment and maintenance checks to ensure consistent performance and minimize cumulative error.
Adherence to best practice guidelines transforms slitting from a variable art form into a repeatable science. It creates a framework that minimizes human error and machine variability, ensuring that the first meter of a coil is identical to the last. We once worked with a client in the construction industry who was experiencing inconsistent widths on slit coils for steel studs. This was causing significant fit-up issues on job sites. The root cause wasn't a single major failure, but a series of small deviations from best practices: operators were using worn shims, the tooling wasn't set up with a micrometer, and machine tension was set by "feel." By helping them implement a formal best-practice checklist for every setup16, we were able to bring their width variation down to well within the required ±0.2mm tolerance. This proves that excellence lies in the consistent execution of fundamentals. These fundamentals form the basis of a truly capable process.
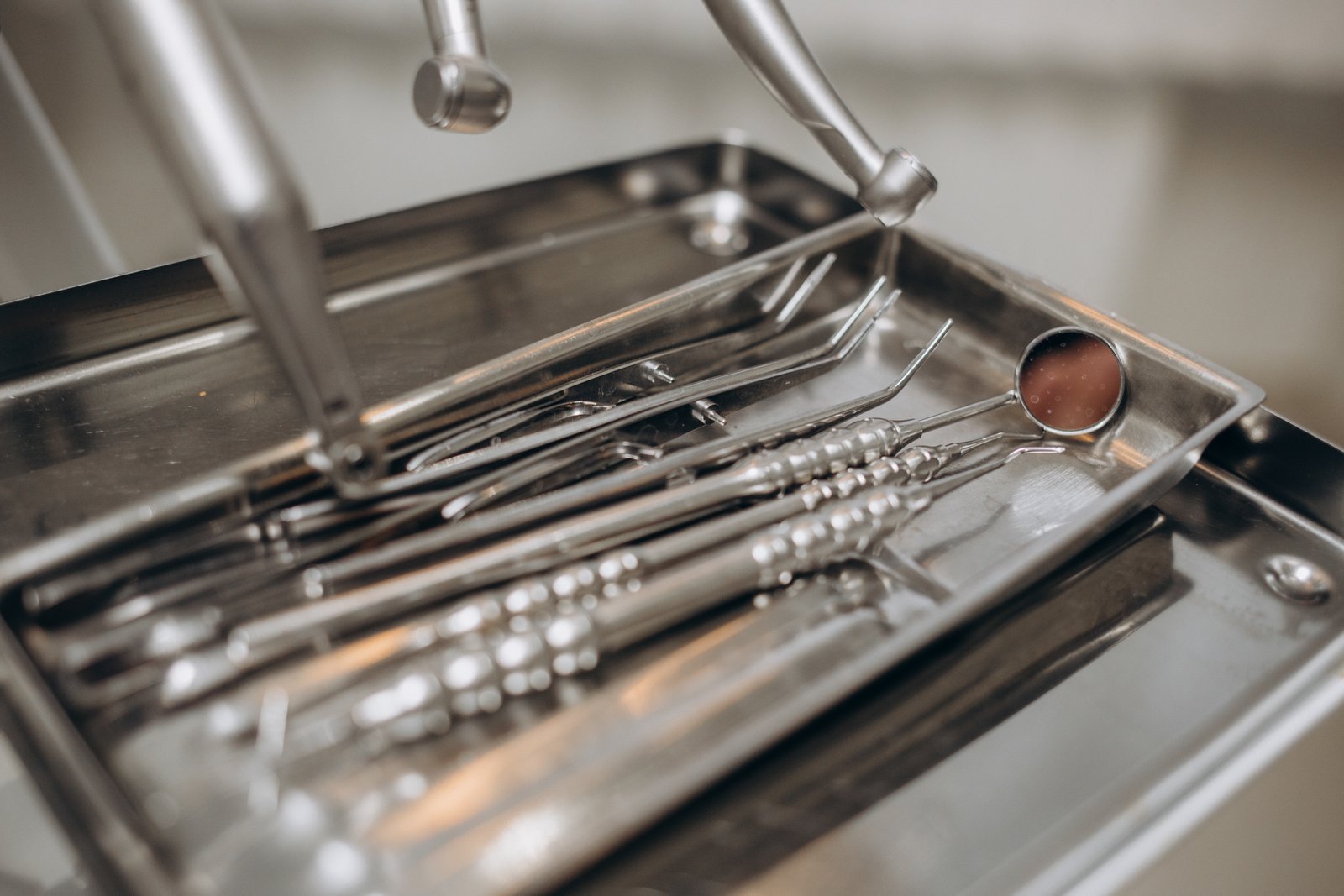
The Sanctity of the Setup: Measurement and Documentation
The foundation of tolerance control is laid before the machine ever starts running. The setup procedure must be treated as a critical, high-precision process. Best practice dictates the use of a dedicated, clean, and well-lit area for tooling assembly. All components—knives, spacers, and arbors—must be meticulously cleaned and inspected for wear or damage before each setup. The use of calibrated, high-precision measuring instruments, such as micrometers or digital calipers, is not optional; it is mandatory. Relying on tape measures or visual estimation is a recipe for failure.
A setup chart17 should be created and followed for every job. This document details the exact combination of knives and spacers required to achieve the target slit width. Each component of the tooling stack should be measured individually, and the total calculated width should be verified against the job specification. This documented setup provides traceability and accountability. In the event of a quality issue, this chart is the first piece of evidence in the investigation, allowing a team to confirm whether the tooling was assembled correctly.
Furthermore, the practice of "touching off" the knives, where the operator brings the upper and lower arbors together to check for a uniform gap, is a crucial final step. This simple visual and tactile check can reveal issues like a chipped knife, a deformed spacer, or arbor misalignment that might not be apparent from measurements alone. Investing time in a meticulous, documented setup process prevents countless hours of wasted production and tons of scrapped material. It is the most cost-effective quality control measure in the entire slitting operation.
Data-Driven Process Validation and In-Run Monitoring
Once the machine is running, best practices shift from setup to validation and monitoring. It is not enough to assume the setup is correct; it must be verified. The first few meters of the slit coil, known as the "first article," must be carefully measured and inspected. This should include not only the width of multiple strips across the arbor but also an assessment of edge quality (burr) and shape (camber). These first-article inspection results must be documented and signed off before the full production run is authorized to continue.
During the run, periodic checks are essential. Relying solely on the first-article inspection is risky, as factors like thermal expansion in the machine and tool wear can cause dimensions to drift over time. Best practice involves taking measurements at set intervals, for example, at the beginning, middle, and end of each master coil. Many modern slitting lines are being equipped with in-line, non-contact measuring systems, such as laser gauges18. These systems can monitor the width of every slit strip in real-time and can be programmed to alert the operator or even stop the line if any dimension trends outside the tolerance band.
This data-driven approach removes guesswork and provides a rich source of information for continuous improvement. By analyzing tolerance data over time, patterns can emerge. For example, if a certain slit width consistently drifts after 2,000 meters, it may indicate a specific tool wear pattern or a thermal issue with the machine. This allows maintenance and engineering teams to move from reactive problem-solving to proactive process optimization, building a more robust and capable slitting operation.
A Culture of Quality: Operator Training and Equipment Maintenance
Ultimately, maintaining tolerance is not just about machines and procedures; it's about people and culture. The most sophisticated equipment is only as good as the operator running it. A best-in-class operation invests heavily in training its personnel. Operators should not just be taught which buttons to press; they need to understand the "why" behind the procedures. They should be trained to understand the fundamentals of burr formation, the importance of clearance, how to properly handle and inspect tooling, and how to interpret the quality of the slit edge. An empowered and knowledgeable operator is the first line of defense against quality issues.
This culture of quality must be supported by a rigorous equipment maintenance program. As discussed previously, machine rigidity and alignment are critical for tolerance. A preventative maintenance schedule should be in place to regularly check and adjust key parameters. This includes checking the parallel alignment of the arbors, inspecting bearings for wear, calibrating tensioning systems, and verifying the accuracy of all measuring equipment. The machine must be treated as a precision instrument.
This holistic view, which combines meticulous setups, data-driven validation, thorough training, and proactive maintenance, creates a robust system for tolerance control. It's an ecosystem where each part supports the others. For us at MFY, this isn't just a set of guidelines; it's the operational philosophy that allows us to confidently supply high-precision slit coils to the most demanding markets around the globe. It’s the commitment behind every coil that carries our name.
Conclusion
Ultimately, achieving superior burr control and tight tolerance in stainless steel slitting is a holistic discipline. It requires integrating precision tooling, data-driven process control, and rigorous maintenance. Mastering these elements ensures consistent quality, enhances safety, and provides a critical competitive advantage in today's demanding market.
-
Discover expert-backed insights and technical explanations about the mechanics of the slitting process. ↩
-
See research-based data connecting material hardness variation to coil camber during metal slitting. ↩
-
Explore the benefits of automated tension and knife adjustment systems for high-precision slitting. ↩
-
Find best practices and application tips for using protective films on stainless steel during slitting. ↩
-
Find out the potential issues caused by incorrect adjustments in the slitting process. ↩
-
Understand the two types of knife clearance and their impact on cutting performance. ↩
-
See which knife materials are commonly chosen for durability and cut quality in slitting lines. ↩
-
Explore why work hardening complicates stainless steel slitting and subsequent manufacturing steps. ↩
-
Learn how burrs impact quality control, tolerance, and cause supplier-customer disputes in manufacturing. ↩
-
Discover why automated systems cannot handle burrs and how this affects production efficiency. ↩
-
Understand how burrs cause accumulation of dimensional errors in complex assemblies. ↩
-
Identify the safety risks posed by burrs and strategies to reduce workplace injuries. ↩
-
Learn the key components of an end-to-end burr reduction program for coil processing ↩
-
Compare tool material performance for burr-resistance and durability in slitting lines ↩
-
Discover how technology helps control tension and improve edge quality in steel slitting ↩
-
See examples of industry-accepted setup checklists that prevent common slitting tolerance errors ↩
-
Discover how proper documentation supports troubleshooting and continuous improvement in slitting ↩
-
Understand the benefits of real-time, automated inspection for slitting process control ↩
Have Questions or Need More Information?
Get in touch with us for personalized assistance and expert advice.