Навигация по гигантам: Путеводитель по 10 крупнейшим производителям рулонов нержавеющей стали в Китае
Struggling to find a reliable stainless steel coil supplier in China's vast market can be daunting. You're facing inconsistent quality and unpredictable delivery times, putting your projects and reputation at risk. I understand this frustration, as finding a trustworthy partner is crucial for success.
Navigating the Chinese stainless steel coil market requires identifying top-tier manufacturers known for quality, capacity, and reliability. The leading producers are distinguished by their integrated supply chains, advanced technology, and adherence to international standards, ensuring consistent product quality and dependable delivery for global clients.
In my years as a Global Business Director, I’ve seen countless companies grapple with these sourcing challenges. The sheer number of suppliers makes it difficult to distinguish the true industry leaders from the rest. This guide is designed to cut through that noise. I'll provide you with the insights I've gained to help you identify partners who can truly strengthen your supply chain.
This article will go beyond a simple list. We will delve into the nuances of the Chinese stainless steel market, exploring the current landscape and the giants who command it. I'll offer a critical analysis of the challenges these manufacturers face, from overcapacity to tightening environmental regulations1, and discuss the innovative strategies they are employing to stay ahead. We will examine data from industry bodies like the World Stainless Association and look at real-world case studies to understand the practical implications of these market dynamics. This deeper exploration will equip you with a comprehensive understanding, empowering you to make more strategic sourcing decisions that align with your long-term business goals.
Overview of China's Stainless Steel Manufacturing Industry
Are you finding it difficult to grasp the true scale and complexity of China's stainless steel industry? The market's immense size and rapid evolution can feel overwhelming, making it hard to identify real opportunities. I've guided many partners through this landscape, helping them see clarity amidst the complexity.
China's stainless steel industry is the world's largest, characterized by massive production capacity, dominated by a few major players, and undergoing significant transformation. Its focus is shifting from pure volume to higher-value products, driven by technological innovation, domestic demand, and strict environmental policies, shaping global market dynamics.
To truly succeed in this market, a surface-level view isn't enough. You need to understand the fundamental forces at play. For instance, according to data from the World Stainless Association, China's output consistently accounts for over half of the global total, reaching approximately 39.44 million tonnes recently. This staggering volume creates both immense opportunity and significant challenges, including intense competition and price volatility. We've worked with clients, like an automotive parts manufacturer in India, who were initially attracted by low prices but struggled with inconsistent quality from smaller mills. Their challenge wasn't just finding a supplier, but finding a partner who could navigate the industry's intricacies to provide consistent, high-grade material. By partnering with an integrated supplier like us, they gained access to a stable supply of 400-series coils that met their exacting specifications, eliminating production bottlenecks. This experience highlights a critical lesson: understanding the industry's structure is the first step toward building a resilient and efficient supply chain. It's about looking beyond the price tag to see the whole picture—the technology, the capacity, and the commitment to quality that defines the industry leaders.
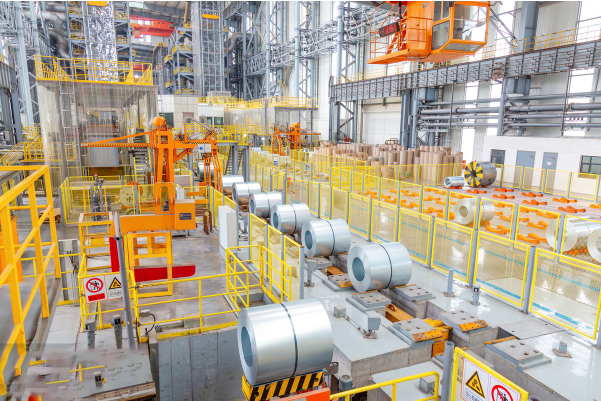
The sheer scale of China's stainless steel sector is a double-edged sword. While it offers unparalleled sourcing options, it also creates an environment where quality and reliability can vary dramatically. For international buyers, the primary challenge is not a lack of choice but an excess of it, compounded by a lack of transparency. Many of my clients, before working with us, have shared stories of navigating a fragmented market of countless trading companies and smaller mills, each making bold claims but few delivering consistently. This fragmentation often leads to a race to the bottom on price, which invariably compromises material quality, grade accuracy, and delivery schedules. The result for the end-user is often project delays, budget overruns, and, in worst-case scenarios, product failure. Understanding this dynamic is crucial for any business looking to source from China. It’s about recognizing that the most sustainable strategy involves partnering with manufacturers who have vertically integrated operations, from raw material procurement to final product processing. These are the players who can truly guarantee quality control at every stage.
The Dominance of Integrated Production Models
At the heart of the most reliable segment of China's stainless steel industry is the integrated production model. Unlike smaller, non-integrated mills that often rely on sourcing semi-finished products from various suppliers, integrated manufacturers control the entire production lifecycle. This starts from the melting and casting of raw materials like nickel and chromium into crude steel, followed by hot rolling, and then precision cold rolling to produce the final coils. This end-to-end control is the bedrock of quality assurance. For example, a leading manufacturer can ensure the precise chemical composition of an alloy from the very first stage, something a non-integrated producer simply cannot guarantee.
This control extends to every subsequent process. When a client requires a specific finish, such as a 2B or BA finish, an integrated mill has the in-house equipment and expertise to execute it flawlessly. I recall a case with an engineering contractor in the Middle East working on a major desalination plant. They required a large quantity of 316L coils with a very specific surface roughness to maximize corrosion resistance. Sourcing from a non-integrated supplier would have meant relying on third-party processors, introducing multiple points of potential failure. By working with an integrated producer, we were able to manage the entire process, from melt to final polish, providing them with test certificates and full traceability for every coil, ensuring the project's long-term integrity.
The logistical advantages of this model are equally significant. An integrated supply chain minimizes dependencies on external parties, drastically reducing the risk of delays. Production schedules are more predictable, and lead times are often shorter. For businesses operating on tight project timelines, this reliability is invaluable. It transforms the supplier relationship from a simple transaction into a strategic partnership, where the manufacturer becomes an extension of the client's own operations, committed to their success.
Regional Clusters and Specializations
The Chinese stainless steel industry is not monolithic; it is geographically concentrated in specific provinces, each with its own ecosystem and specializations. The two most prominent clusters are in Guangdong (particularly the Foshan area) and Jiangsu (around Wuxi). These are not just production hubs; they are complete industrial ecosystems encompassing production, processing, logistics, and trading. Foshan, for instance, is renowned for its vast market of decorative stainless steel, offering an incredible variety of finishes and patterns. Wuxi, on the other hand, is a major center for industrial-grade stainless steel, with a focus on coils and sheets for manufacturing and construction.
Understanding these regional strengths is key to efficient sourcing. A client looking for high-end, architectural-grade sheets for a skyscraper facade would be best served by the specialists in Guangdong, while a manufacturer of industrial tanks would find their ideal partners in the Jiangsu region. We often advise our clients on this, helping them connect with the right production base for their specific needs, even if it's within our own diversified network.
These clusters also foster intense competition and innovation. The proximity of numerous producers drives them to constantly improve efficiency, develop new products, and adopt new technologies. This creates a dynamic environment for buyers, but it also necessitates a discerning eye. The presence of so many players means that due to diligence is paramount. A savvy buyer will leverage the strengths of these clusters while carefully vetting potential partners to ensure they meet stringent quality and ethical standards.
The Role of Government Policy and Environmental Scrutiny
Government policy is a powerful and often unpredictable force shaping the industry. In recent years, Beijing has implemented stringent environmental protection laws and production capacity controls aimed at curbing pollution and consolidating the industry. These policies have had a profound impact, forcing the closure of smaller, less efficient, and highly polluting mills. While this has caused some short-term supply disruptions, the long-term effect is positive. It is driving the industry towards a more sustainable and high-quality future, favoring the larger, more technologically advanced producers who can afford to invest in green technologies and comply with strict regulations.
For our clients, this trend provides an extra layer of assurance. Working with a manufacturer that is compliant with these government mandates means a lower risk of production stoppages due to environmental audits. I remember a period a few years ago when sudden government-enforced shutdowns in a major steel-producing region left many international buyers scrambling as their suppliers went dark overnight. Our operations, being fully compliant with national environmental standards, continued without interruption, reinforcing our clients' supply chain security.
This policy-driven shift is also accelerating the move towards "green steel." Manufacturers are increasingly investing in technologies like Electric Arc Furnaces (EAFs), which use recycled scrap and consume significantly less energy than traditional Blast Furnaces. As global markets place a greater emphasis on sustainability, sourcing from these forward-looking Chinese producers will become not just a preference but a competitive necessity.
Характеристика | Integrated Manufacturer | Non-Integrated Mill/Trader |
---|---|---|
Контроль качества | End-to-end control from melt to finish | Variable; dependent on third-party suppliers |
Прослеживаемость | Full material traceability available | Often limited or non-existent |
Последовательность | High consistency in chemistry & mechanics | Can vary significantly between batches |
Lead Times | More predictable and often shorter | Prone to delays from external dependencies |
Customization | High capability for custom grades/finishes | Limited by third-party processing capabilities |
Risk | Lower risk of supply chain disruption | Higher risk of delays and quality issues |
China leads global stainless productionПравда
China produces over 50% of the world's stainless steel, with output reaching 39.44 million tonnes annually.
Small mills guarantee better qualityЛожь
Integrated manufacturers with full production control consistently deliver higher quality than fragmented small mills.
Current Leaders in the Chinese Stainless Steel Coil Market
Pinpointing the truly elite manufacturers in China's crowded market feels like an impossible task. You're bombarded with names, but how do you know which ones represent real quality and reliability? This uncertainty can paralyze your sourcing decisions, costing you time and money.
The leaders of the Chinese stainless steel coil market are large, state-owned or publicly-listed conglomerates like Baosteel, TISCO, and Tsingshan. These giants are defined by their vast production capacities, integrated supply chains, extensive R&D, and global reach, setting the industry benchmarks for quality and innovation.
Navigating this top tier requires understanding what sets them apart. It's not just about size; it's about a relentless commitment to excellence that permeates their entire operation. I once worked with a German engineering firm that was building a high-tech chemical processing facility. They needed absolute certainty in their material's performance under extreme conditions. Their initial supplier, a smaller mill, couldn't provide the rigorous testing data and certifications required. We connected them with one of China's top-tier producers. The difference was night and day. They received comprehensive mill test reports (MTRs), full batch traceability, and material that not only met but exceeded international standards. This experience underscores a simple truth: the industry leaders don't just sell steel; they sell certainty. Their reputation is built on a foundation of proven performance, advanced technology, and a deep understanding of their customers' most critical needs.
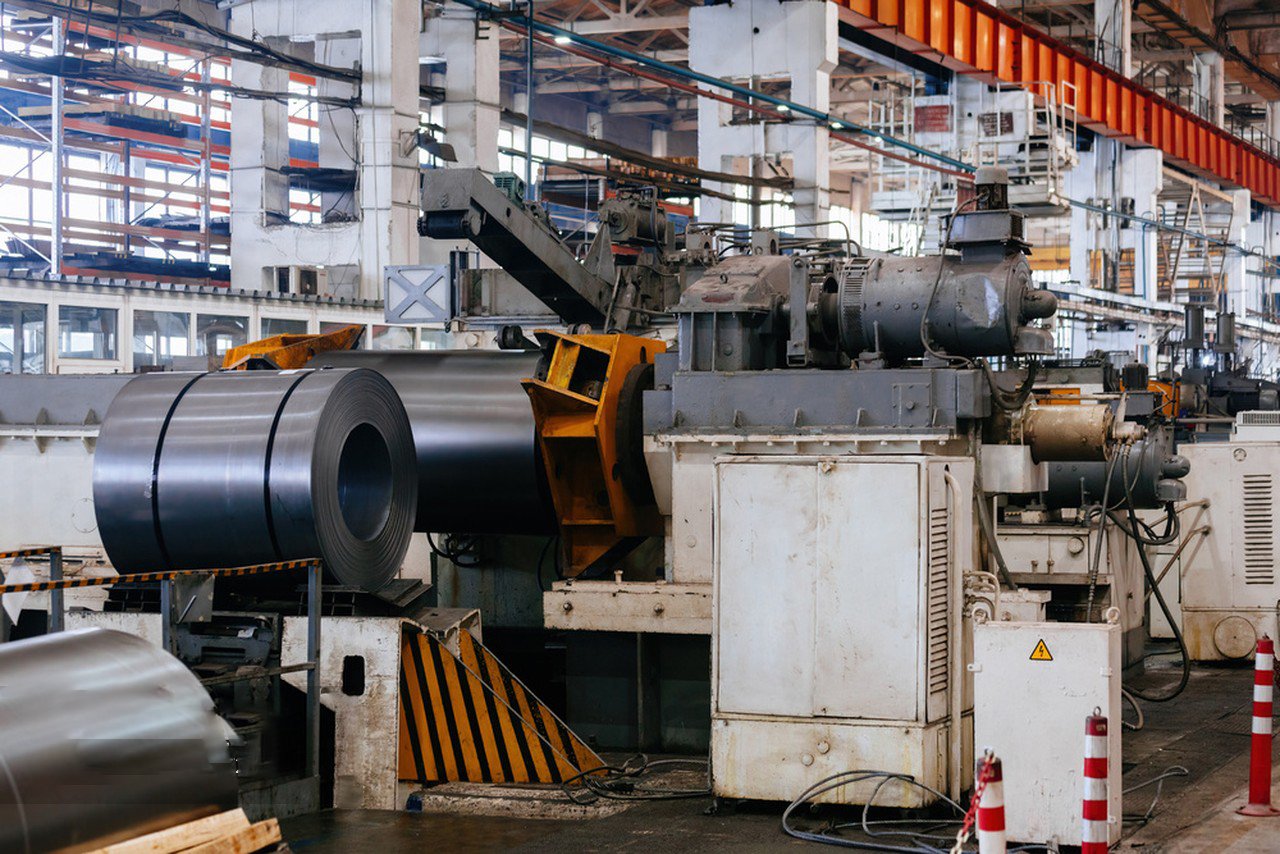
The landscape of China's stainless steel industry is dominated by a handful of colossal players whose names are synonymous with scale and influence. Companies like the Baowu Steel Group and Tsingshan Holding Group2 are not just national leaders; they are global powerhouses. Their annual production figures are measured in the tens of millions of tonnes, and their influence extends across the entire supply chain, from owning nickel mines in Indonesia to operating sophisticated processing centers around the world. For any business sourcing from China, understanding the profiles of these giants is essential. They are the market makers, their production decisions and pricing strategies ripple across the entire industry, affecting smaller mills and distributors alike. Sourcing from these leaders often means higher initial costs, but it provides an unparalleled level of quality assurance, technological sophistication, and supply chain stability that smaller players simply cannot match. For critical applications in sectors like aerospace, medical devices, or energy, the peace of mind that comes with sourcing from a top-tier manufacturer is often a non-negotiable requirement.
The State-Owned Behemoths: Baowu and TISCO
The China Baowu Steel Group Corporation, parent of the famed Baosteel, stands as the undisputed world leader in steel production. Its stainless steel division is a cornerstone of its operations, known for producing a vast range of high-quality products, including precision coils for the automotive and home appliance industries. As a state-owned enterprise (SOE), Baowu benefits from significant government backing, enabling massive investments in research and development. This allows them to pioneer new alloys and production techniques, staying at the forefront of the industry. Their commitment to quality is institutional, with rigorous control systems that are often modeled on the world's most demanding standards.
Similarly, TISCO (Taiyuan Iron & Steel Co.) has a long and storied history as one of China's first and most important stainless steel producers. Based in Shanxi province, TISCO has built a reputation for its expertise in specialized products, including high-grade stainless steel for the railway, petrochemical, and nuclear power industries. Sourcing from an SOE like Baosteel or TISCO means engaging with a massive, structured organization. While this can sometimes mean less flexibility in negotiations compared to smaller mills, it offers unmatched reliability.
For a construction contractor we supplied in Southeast Asia working on a landmark public transport system, the requirement was for thousands of tonnes of 304L coils with extremely tight thickness tolerances. The project's specifications were rigid, and penalties for delays were severe. By sourcing through the state-owned system, we could guarantee not only the material quality but also a locked-in production and delivery schedule. This level of certainty, backed by the full faith and credit of a state-owned giant, was the critical factor that won them the bid.
The Private Sector Titan: Tsingshan Holding Group
In stark contrast to the state-owned giants, Tsingshan Holding Group represents the dynamic power of China's private sector. In a remarkably short period, Tsingshan has grown to become the world's largest stainless steel producer by volume, a feat achieved through aggressive vertical integration and relentless cost control. Their most strategic move was the massive investment in nickel pig iron (NPI) production facilities in Indonesia, giving them direct control over the single most important raw material in stainless steel manufacturing. This has allowed them to fundamentally reshape the cost structure of the global industry.
Tsingshan's business model is built on scale and efficiency. They focus on producing large volumes of standard-grade stainless steel (primarily 200 and 300 series) at a cost that few competitors can match. This has made them a dominant force in markets like India and Southeast Asia, where price sensitivity is high. Working with Tsingshan offers a different value proposition than working with an SOE. The focus is less on bespoke, highly specialized products and more on delivering reliable, commodity-grade steel at an extremely competitive price point.
We have a long-standing relationship with a large distributor in India whose business model relies on high volume and fast turnover. For them, Tsingshan's consistent output and cost-effective pricing are a perfect match. They can place large, regular orders for standard-sized coils and be confident in both the price and the availability, allowing them to effectively manage their inventory and serve their broad customer base of smaller fabricators and manufacturers. This demonstrates how different leaders in the Chinese market cater to different segments of global demand.
Emerging Leaders and Specialized Producers
Beyond the top three, there is a dynamic tier of other significant manufacturers who are leaders in their own right, often focusing on specific niches or regions. Companies like Yongjin, Delong Stainless Steel, and Hongwang Group have carved out substantial market share through specialization and technological prowess. Yongjin, for example, is highly regarded for its specialization in precision cold-rolled stainless steel strip, catering to the demanding electronics and IT sectors where ultra-thin and highly uniform materials are required.
These emerging leaders are often more agile and flexible than the state-owned behemoths. They are quick to adopt new technologies and can be more responsive to custom requests for smaller or medium-sized orders. For a client of ours in the medical device industry, who needed a specific grade of 316L stainless steel with a mirror finish for surgical instruments, a specialized producer was the ideal choice. They had the technical expertise and the willingness to handle a smaller, highly specialized production run that might not have been a priority for a larger, volume-focused mill.
This tier of the market demonstrates the depth and diversity of China's manufacturing capabilities. While the giants define the broad trends, these specialized players provide the critical components for a vast array of industries. For a discerning buyer, identifying these niche leaders can unlock significant value and provide a competitive edge. It requires a deeper level of market intelligence, moving beyond just the big names to understand the unique strengths of the entire manufacturing ecosystem.
Производитель | Ownership | Key Strengths | Primary Products |
---|---|---|---|
Baowu Steel (Baosteel) | State-Owned | R&D, High-End Products, Quality Control | Automotive, Appliance, High-Grade Coils |
TISCO | State-Owned | Specialized Alloys, Heavy Industry Focus | Railway, Petrochemical, Nuclear-Grade Steel |
Tsingshan Holding Group | Private | Vertical Integration, Cost Leadership, Volume | Commodity 200/300 Series Coils, NPI |
Yongjin | Private | Precision Cold-Rolling, Niche Expertise | Ultra-thin Gauge Strip for Electronics |
Delong / Hongwang | Private | Regional Strength, Flexibility, Modern Mills | General Purpose Coils and Sheets |
Baowu is state-ownedПравда
Baowu Steel Group is a state-owned enterprise that receives significant government backing.
Tsingshan focuses on custom productsЛожь
Tsingshan specializes in high-volume commodity-grade steel rather than bespoke products.
Key Challenges Faced by Chinese Stainless Steel Coil Manufacturers
Are you concerned that your Chinese supplier might suddenly face production halts or unexpected price hikes? The industry is fraught with challenges like overcapacity and trade tensions, creating volatility that can disrupt your supply chain. I've helped clients navigate this uncertainty by building resilient sourcing strategies.
Chinese stainless steel manufacturers face significant challenges, including structural overcapacity leading to intense price competition, rising raw material costs, and increasing international trade friction through tariffs and anti-dumping duties1. Furthermore, stringent domestic environmental regulations demand costly operational and technological upgrades to ensure compliance.
These are not abstract problems; they have real-world consequences for your business. The constant pressure on margins from overcapacity can tempt some mills to cut corners on quality. I saw this firsthand with a construction client in the Middle East. Their previous supplier, under intense price pressure, started substituting a lower-grade material, which was only caught during on-site testing, causing costly delays and rework. This incident highlights the critical need to partner with manufacturers who have the financial stability and ethical commitment to maintain quality standards, even in a challenging market. The most resilient manufacturers are those who are not just competing on price, but are investing in efficiency, innovation, and sustainability to build a business that can weather these industry storms.
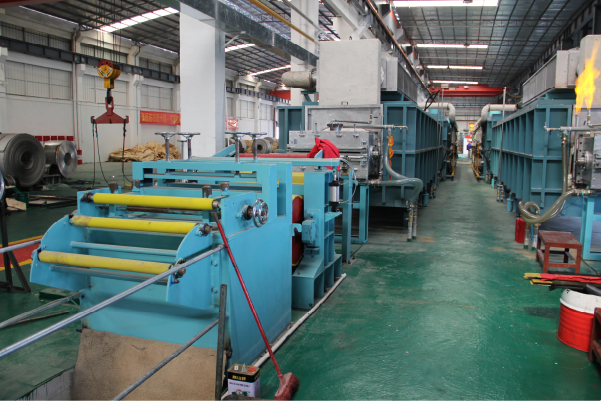
While China's stainless steel industry is a global titan, it is not without its vulnerabilities. Operating within this complex market requires a clear-eyed understanding of the significant headwinds that manufacturers face daily. These challenges range from internal structural issues to external geopolitical pressures, and they directly impact pricing, availability, and the long-term viability of suppliers. The most pressing of these is the persistent issue of overcapacity2. For years, rapid expansion, fueled by both government incentives and market speculation, led to a production capacity that far outstrips domestic demand. This fundamental imbalance creates a hyper-competitive environment where manufacturers are constantly under pressure to lower prices to maintain market share and keep their mills running. For an international buyer, this might seem like an advantage, leading to lower procurement costs. However, it's a double-edged sword. This relentless downward pressure on prices can erode profit margins to unsustainable levels, forcing some producers to compromise on quality, delay investments in new technology, or even face bankruptcy, creating significant risks for their clients' supply chains.
The Persistent Problem of Overcapacity
The issue of overcapacity is arguably the most significant structural challenge for the industry. Estimates suggest that China's stainless steel production capacity exceeds its actual domestic consumption by a substantial margin, forcing producers to rely heavily on exports. This fierce competition for orders, both domestically and internationally, leads to chronic price wars. The resulting low-profit environment makes it difficult for companies to invest in crucial areas like research and development, employee training, and environmental upgrades. It creates a cycle where cutting costs becomes the primary focus, rather than improving quality or innovation.
I have seen the direct impact of this on the ground. A client, an equipment integrator for the food processing industry, began experiencing quality issues with their supplier. The finish on the 304 coils was inconsistent, and there were variations in thickness beyond the specified tolerance. Upon investigation, it became clear their supplier was struggling with profitability and had cut back on their quality control personnel and maintenance schedules. The client had to switch partners mid-project. This case serves as a stark reminder that while a low price is attractive, the stability and financial health of your supplier are far more critical in the long run. A healthy, profitable manufacturer is one that can afford to uphold its promises of quality.
This oversupply also means that inventories, both at the mills and with distributors, can swell to high levels, as seen in recent industry reports showing historically high stock levels. This puts even more pressure on producers to offload material at discounted prices, further destabilizing the market. For buyers, this volatility can make long-term planning difficult, as prices can fluctuate dramatically in short periods.
Navigating Geopolitical Tensions and Trade Barriers
The global political climate has become a major source of uncertainty. Chinese stainless steel exports are increasingly being targeted by anti-dumping measures3 and countervailing duties in key markets like the European Union, the United States, and even emerging economies like India. These trade barriers are designed to protect local industries from what they see as unfairly priced imports. For Chinese manufacturers, these tariffs can effectively close off entire markets or render their products uncompetitive overnight. A recent example is the escalation of US tariffs, which not only targets primary steel products but also downstream goods that use Chinese steel.
This forces manufacturers to constantly adapt their export strategies. They may need to pivot to new markets in Southeast Asia, the Middle East, or South America, which can involve navigating unfamiliar regulations, logistics, and business cultures. This strategic shift requires agility and significant resources. We worked with a manufacturer who had a large portion of their exports going to Europe. When anti-dumping duties were imposed, they had to quickly find new customers. As their partner, we helped them leverage our network in the Middle East, reformulating their product offerings and marketing to meet the specific needs of that region.
The risk for buyers is that a supplier heavily dependent on a single export market can face sudden financial distress if that market imposes tariffs. A diversified export strategy is a key indicator of a manufacturer's resilience. When vetting a potential partner, it's crucial to ask about their primary export markets and their contingency plans for dealing with trade disputes.
The Green Mandate: Environmental Regulations and Costs
The Chinese government's "war on pollution" has placed the heavy industry under intense scrutiny. Steel manufacturing is an energy-intensive process, and Beijing has implemented strict environmental standards to reduce emissions and improve air and water quality. This "green mandate" requires manufacturers to make substantial capital investments in new technologies, such as flue-gas desulfurization systems, advanced water treatment facilities, and upgrading to cleaner production processes like Electric Arc Furnaces4 (EAF).
These investments are non-negotiable, and the cost of compliance is significant. For smaller, less profitable mills, these costs can be prohibitive, forcing them to either shut down or operate illegally, risking sudden closures by regulators. The larger, more established players like Baowu and TISCO have the capital to invest in these green technologies, which further consolidates the market in their favor. This environmental push is ultimately beneficial for the industry's long-term sustainability and for the planet.
However, these costs are inevitably passed on through the supply chain. For buyers, it's important to understand that the push for "green steel" comes with a price tag. A supplier who is fully compliant with environmental regulations will likely have a higher cost base than one who is not. I always advise my clients that paying a slight premium for steel from an environmentally responsible and compliant producer is a form of risk management. It ensures your supply chain won't be disrupted by environmental shutdowns and aligns your own business with global sustainability goals, which is increasingly important for brand reputation in Western markets.
Вызов | Impact on Manufacturer | Risk for International Buyer |
---|---|---|
Overcapacity | Intense price competition, low profitability | Inconsistent quality, supplier instability, price volatility |
Trade Barriers | Loss of key export markets, need for strategic shifts | Sudden supply disruption if supplier is over-exposed |
Raw Material Volatility | Unpredictable production costs, margin squeeze | Rapid price fluctuations, potential for contract renegotiation |
Environmental Regulations | High cost of compliance, risk of shutdowns | Supply chain disruption from non-compliant suppliers |
Overcapacity leads to price warsПравда
Chinese stainless steel production capacity far exceeds domestic demand, forcing manufacturers into intense price competition.
Trade barriers benefit Chinese exportersЛожь
Anti-dumping duties make Chinese exports less competitive in key markets, forcing manufacturers to find new buyers.
Strategies for Overcoming Challenges in the Stainless Steel Coil Industry
Worried about your supply chain being fragile and exposed to market shocks? Relying on a single supplier or strategy can be risky in a volatile market. I've built my career on developing robust, multi-faceted strategies that create resilience and a competitive edge for my partners.
To overcome industry challenges, successful manufacturers are embracing digital transformation for efficiency, focusing on product innovation to enter high-margin niches, and diversifying their export markets to mitigate geopolitical risks. This proactive approach turns challenges into opportunities for growth and differentiation.
A purely reactive approach is a recipe for failure. The most forward-thinking companies are actively shaping their own destiny. For example, instead of just accepting volatile raw material prices, some manufacturers are using sophisticated hedging strategies or, like Tsingshan, integrating backward into raw material production5. I worked with a mid-sized producer who implemented a full-scale digital inventory management system linked directly with their key customers. This transparency allowed both parties to optimize stock levels, reduce holding costs, and improve forecasting accuracy, effectively insulating them from minor market shocks. This is the kind of strategic thinking that separates the leaders from the laggards.
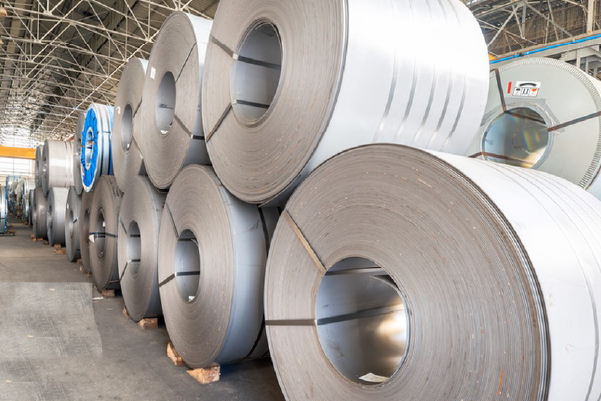
In a market defined by intense competition and constant change, survival and success depend on more than just production capacity. The leading Chinese stainless steel manufacturers are actively deploying a range of sophisticated strategies to navigate the challenges of overcapacity, trade barriers, and environmental regulations. These strategies are not merely defensive; they are proactive initiatives designed to build resilience, create new value, and secure a competitive advantage in the global marketplace. For international buyers, understanding these strategies is crucial. It allows you to identify forward-thinking partners who are not just surviving but thriving, ensuring your own supply chain is anchored by a supplier that is built for the future. The core of these strategies revolves around three key pillars: technological and digital transformation, a renewed focus on product innovation and value-added services, and the strategic diversification of export markets to de-risk and capture new growth.
Embracing Digital Transformation and Smart Manufacturing
The Fourth Industrial Revolution is reshaping heavy industry, and stainless steel is no exception. Leading manufacturers are making significant investments in digitalization and "Smart Manufacturing" (Industry 4.0) technologies to boost efficiency, reduce costs, and improve quality. This involves creating a fully connected production environment where data from sensors on the production line is collected and analyzed in real-time. This allows for predictive maintenance, preventing costly equipment failures before they happen. It also enables precise monitoring of every stage of the coil production process, from temperature and pressure in the furnaces to the exact tension and speed of the cold-rolling mills.
This data-driven approach leads to a dramatic improvement in product consistency. For a client of ours in the automotive sector, consistent mechanical properties in the stainless steel coils they use for exhaust systems are critical for their automated welding and forming processes. Even slight variations can lead to production line stoppages. By sourcing from a "smart factory," they receive coils with exceptionally low variance from batch to batch, which has increased their production uptime by over 15%. This is the tangible benefit of digitalization.
Furthermore, digital platforms are transforming the customer experience. Companies like MFY are developing sophisticated digital systems that allow clients to track their orders in real-time, access quality control documents instantly, and manage their logistics from a single dashboard. This level of transparency and control builds trust and transforms the traditional supplier-customer relationship into a seamless digital partnership.
Shifting Focus to High-Value Products and Innovation
Faced with shrinking margins in the commodity-grade market, the most astute manufacturers are shifting their focus towards high-value, specialized products. Instead of competing solely on price for standard 304 coils, they are investing in R&D to develop proprietary alloys and products for demanding, high-margin industries. This includes producing ultra-lightweight, high-strength steels for the aerospace and electric vehicle sectors, developing superior corrosion-resistant alloys for the marine and chemical processing industries, and creating specialized antibacterial stainless steels for medical and food-grade applications.
This strategy of "moving up the value chain" is a direct response to the challenge of overcapacity. It allows manufacturers to differentiate themselves based on technical expertise rather than price alone. I recently facilitated a partnership between a Chinese specialty mill and a European manufacturer of high-performance surgical tools. The mill had developed a specific grade of martensitic stainless steel that could hold an exceptionally sharp edge while also being highly resistant to sterilization processes. This innovation allowed the European client to create a superior product and command a premium in their market.
This focus on innovation extends to services as well. Leading suppliers are no longer just selling steel; they are providing comprehensive solutions. This includes offering in-house processing services like cut-to-length, slitting, and polishing, as well as providing technical consultation to help clients select the optimal material for their application. This service-oriented approach creates stickier customer relationships and provides a hedge against the commoditization of the core product.
Strategic Market Diversification and Supply Chain Integration
The rise of global trade protectionism has made market diversification an essential survival strategy. Relying too heavily on a single export market, such as the US or the EU, is now seen as an unacceptable risk. Intelligent manufacturers are actively cultivating a balanced portfolio of export destinations, with a strong focus on high-growth regions that are less likely to impose punitive tariffs. The Belt and Road Initiative has been a key enabler of this strategy, opening up new infrastructure and construction markets for Chinese steel in Central Asia, Africa, and the Middle East.
We at MFY have been at the forefront of this trend, establishing strong partnerships with distributors and contractors in India, Southeast Asia, and Russia. This not only spreads risk but also provides valuable insights into the unique demands and specifications of different markets. For example, our work in Southeast Asia has led us to develop specific product lines that are particularly resistant to the hot and humid climate of the region.
Beyond geographic diversification, deep supply chain integration is another key strategy. This is exemplified by Tsingshan's move to control its own nickel supply in Indonesia. By integrating backward into raw material production, they have gained an unparalleled level of cost control and supply security. While not all manufacturers can afford to buy their own mines, the principle of securing the supply chain is being adopted in other ways, such as forming long-term strategic alliances with raw material suppliers, investing in logistics and warehousing infrastructure, and even developing proprietary software to manage the entire supply chain more efficiently. This end-to-end control is the ultimate strategy for delivering reliability in an uncertain world.
Стратегия | Objective | Ключевые действия | Benefit for Buyer |
---|---|---|---|
Digital Transformation | Improve Efficiency & Quality | Real-time data monitoring, predictive maintenance | Higher product consistency, greater transparency |
Product Innovation | Increase Margins & Differentiate | R&D in specialty alloys, new finishes | Access to cutting-edge materials, competitive edge |
Market Diversification | Reduce Geopolitical Risk | Cultivate new export markets (e.g., SE Asia, Middle East) | More stable and resilient supplier partner |
Supply Chain Integration | Enhance Control & Reliability | Long-term supplier alliances, investment in logistics | Greater supply security, more predictable pricing |
Digital transformation improves product consistencyПравда
Smart manufacturing technologies enable precise monitoring of production parameters, leading to more consistent stainless steel coil quality between batches.
Standard 304 coils offer highest profit marginsЛожь
Commodity-grade products like standard 304 coils actually face shrinking margins, while specialized alloys for aerospace/medical applications command premium pricing.
Future Trends in the Chinese Stainless Steel Coil Market
Are you preparing your business for the next wave of change in the steel industry? The market of tomorrow will be driven by sustainability and advanced technology. Positioning your supply chain now is critical to staying ahead of the curve and maintaining a competitive advantage.
The future of the Chinese stainless steel market will be defined by two dominant trends: the push for "green steel" production to meet decarbonization goals and the development of advanced high-performance alloys. These trends are driven by both government policy and evolving demands from high-tech industries.
This isn't a distant future; the transition is already underway. The pressure for decarbonization is mounting globally, and China, as the world's largest producer, is at the center of this shift. I'm already in conversations with clients who are facing new ESG (Environmental, Social, and Governance) requirements from their own customers. They are actively seeking partners who can supply steel produced with a lower carbon footprint. Manufacturers who invest in green technologies like Electric Arc Furnaces and hydrogen-based production will become the preferred suppliers for global brands, turning sustainability into a powerful commercial advantage.
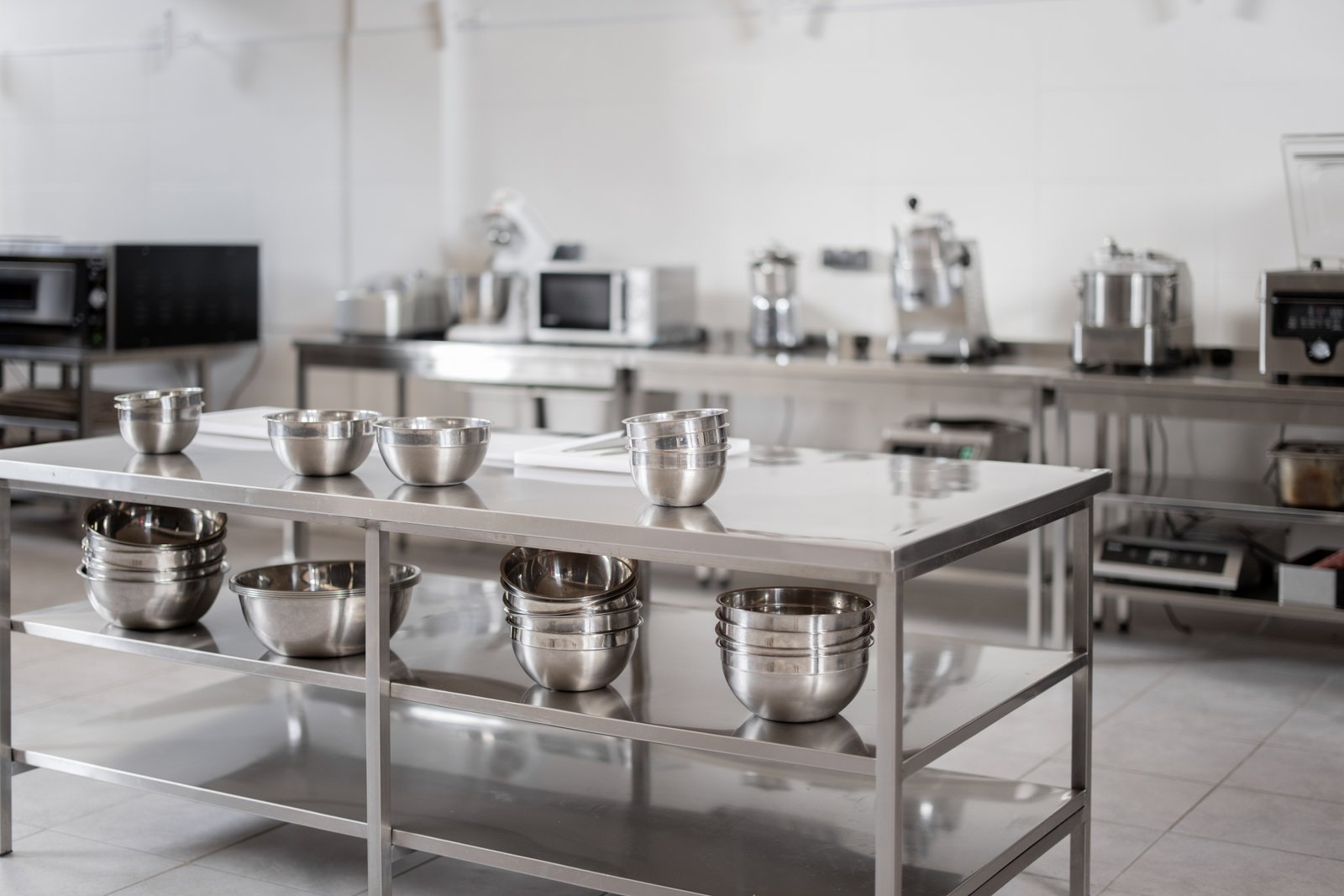
Looking ahead, the Chinese stainless steel industry is on the cusp of a profound transformation. The era of growth at any cost is over, replaced by a strategic pivot towards sustainability, technological sophistication, and high-quality development. Two interconnected trends will dominate the landscape for the next decade: the rise of "green steel" and the accelerating demand for advanced and intelligent materials. These trends are not occurring in a vacuum; they are a direct response to both domestic policy pressures, such as China's 2060 carbon neutrality goal, and the evolving needs of the global market. For international businesses, aligning sourcing strategies with these future trends will be essential for building resilient, responsible, and competitive supply chains. Partnering with manufacturers who are leading this transition will offer not just superior products, but also a share in the brand value that comes with sustainability and innovation.
The Inevitable Rise of Green Steel
The most significant trend shaping the future is the industry-wide push for decarbonization. Steelmaking is traditionally a carbon-intensive process, and as the world's largest producer, China's industry is central to the global fight against climate change. The government's ambitious climate goals are forcing a rapid shift away from traditional Blast Furnace-Basic Oxygen Furnace (BF-BOF) production towards cleaner methods. The primary technology leading this charge is the Electric Arc Furnace (EAF). EAFs use recycled stainless steel scrap as their primary raw material and are powered by electricity, which can increasingly come from renewable sources. This process can reduce CO2 emissions by up to 75% compared to the traditional route.
This transition is capital-intensive and presents a monumental challenge. Wood Mackenzie estimates that a large portion of China's blast furnace capacity will need major overhauls by 2030, presenting a critical choice: reline the old furnaces or replace them with EAFs. While the EAF route is currently more expensive, rising carbon prices and government incentives are expected to close that gap. We are already seeing major players like Baowu announce significant investments in EAF capacity and research into breakthrough technologies like hydrogen-based steelmaking6, which could virtually eliminate carbon emissions.
For our clients, especially those in Europe and North America where carbon-border adjustment mechanisms (CBAMs) are becoming a reality, sourcing low-carbon steel is quickly moving from a "nice-to-have" to a "must-have." We are actively working to build a portfolio of green steel products to meet this future demand, ensuring our clients' products remain competitive in a carbon-conscious world.
Demand for High-Performance and Specialized Alloys
As global technology advances, so does the demand for materials with extraordinary properties. The future of stainless steel is not just in standard grades but in highly engineered alloys designed for specific, high-performance applications. The rapid growth of the electric vehicle (EV) industry, for example, is creating huge demand for lightweight, high-strength stainless steels for battery enclosures and structural components. The global energy transition requires advanced, corrosion-resistant alloys for wind turbines, solar panel frames, and hydrogen fuel cells.
Chinese manufacturers are investing heavily in R&D to capture these emerging markets. This involves moving beyond simply adding chromium and nickel to developing complex alloys with elements like molybdenum, titanium, and nitrogen to achieve specific properties. I recently visited the R&D lab of a partner facility that was testing a new duplex stainless steel designed for subsea pipelines, capable of withstanding immense pressure and highly corrosive environments. This is where the future lies: in solving complex engineering challenges with advanced material science.
For businesses in high-tech sectors, this trend means that China will increasingly become a source not just for cost-effective coils but for cutting-edge materials that enable new product development. Building relationships with these innovative producers now is a strategic move to secure access to the materials that will define the next generation of technology.
The Integration of AI and Smart Steel
The concept of "smart manufacturing" will evolve into "smart materials." The future will see the integration of Internet of Things (IoT) sensors and AI directly into the steel itself and the supply chain that manages it. Imagine stainless steel components in a bridge or building embedded with microscopic sensors that can report on stress, strain, and corrosion in real-time. This "smart steel" could revolutionize structural health monitoring, enabling predictive maintenance and enhancing safety.
While this technology is still in its early stages, the underlying principles are already being applied to the supply chain. AI-driven logistics platforms are becoming more common, capable of optimizing shipping routes, predicting demand fluctuations, and managing inventory with unprecedented accuracy. These systems can analyze vast datasets, including weather patterns, port congestion, and market trends, to make supply chains more resilient and efficient.
For my clients, this means a future where supply chain disruptions are minimized and predictability is maximized. It means having a digital twin of your inventory, knowing precisely where your materials are at all times, and using AI-powered insights to make smarter purchasing decisions. As a company like MFY that integrates digital innovation into our core business, we are actively developing these capabilities to provide our partners with a supply chain that is not just strong, but intelligent.
Future Trend | Key Drivers | Impact on Products | Implication for Buyers |
---|---|---|---|
Green Steel | Government Decarbonization Goals, CBAMs | Low-carbon steel produced via EAF, Hydrogen | Need to source from certified green producers |
High-Performance Alloys | EV, Renewable Energy, Advanced Tech | Lightweight, high-strength, corrosion-resistant steels | Access to materials for cutting-edge applications |
Smart Steel & AI | Industry 4.0, IoT, Big Data | Sensor-embedded materials, AI-optimized logistics | Hyper-efficient, transparent, and resilient supply chains |
Green steel uses EAF technologyПравда
Electric Arc Furnaces (EAF) are a key technology for producing low-carbon steel by using recycled scrap and renewable energy.
Traditional BF-BOF is more sustainableЛожь
Blast Furnace-Basic Oxygen Furnace (BF-BOF) production is carbon-intensive, while EAF and hydrogen-based methods are cleaner alternatives.
Заключение
Navigating China's stainless steel market requires partnering with resilient manufacturers. Success hinges on identifying leaders who embrace digital innovation, focus on high-value products, and pursue green technologies. This strategic approach ensures a reliable, high-quality, and future-proof supply chain for your business's continued growth.
-
Learn how China's environmental policies are shaping industry practices and standards. ↩ ↩
-
Learn about their global influence and how they shape pricing and supply chains ↩ ↩
-
Understand how these measures impact international trade dynamics ↩
-
Discover benefits of implementing EAF technology in sustainable steel manufacturing ↩
-
Understand Tsingshan's backward integration strategy for better supply chain control ↩
-
Understand the potential of hydrogen-based processes in reducing carbon emissions. ↩
У вас есть вопросы или нужна дополнительная информация?
Свяжитесь с нами, чтобы получить индивидуальную помощь и квалифицированный совет.