Duplex vs Austenitic Stainless: Strength & Cost Wins
Struggling to choose the right stainless steel for your project? The wrong decision can lead to overspending, premature material failure, and costly operational delays. Understanding the fundamental differences between duplex and austenitic stainless steel grades1 empowers you to optimize for both performance and your budget.
Duplex stainless steel generally offers superior strength and stress corrosion cracking resistance compared to austenitic grades. While initial material costs can be similar, duplex's strength allows for thinner, lighter designs, often resulting in significant overall project cost savings and enhanced long-term durability.
This decision is more than just a simple comparison of technical datasheets; it's a strategic choice that directly impacts your project's longevity, safety, and bottom line. Over my years as Global Business Director at MFY, I’ve personally seen clients save millions by making a well-informed switch. Let’s explore how these materials truly stack up so you can make the most intelligent choice for your next critical project.
The debate between duplex and austenitic stainless steel is a classic engineering dilemma that my team and I navigate with our clients every week. On the surface, austenitic grades like Нержавеющая сталь 304 и 3162 are the familiar workhorses of the industry—reliable, versatile, and well-understood. However, the evolution of duplex stainless steel presents a compelling alternative that demands a more critical evaluation. A study by the Nickel Institute highlighted that using duplex grades in structural applications could reduce weight by up to 50% compared to austenitic steel. This isn't just a material swap; it's a fundamental shift in design philosophy, enabling more efficient, cost-effective, and durable solutions, especially in the demanding environments our clients in the chemical processing and marine industries operate in.
What are the key properties of duplex stainless steel compared to austenitic stainless steel?
Are you confused by the technical jargon surrounding steel properties like "microstructure" or "pitting resistance"? Misinterpreting these terms can lead to selecting a material that ultimately fails under pressure, jeopardizing your entire project. Let’s break down the fundamental properties in simple, practical terms.
Duplex stainless steel possesses a mixed microstructure of austenite and ferrite, providing a unique combination of properties. Key differences from austenitic steel include higher strength, superior resistance to stress corrosion cracking (SCC), and generally better pitting and crevice corrosion resistance while maintaining good weldability.
These properties are not just abstract concepts; they translate directly into real-world performance and reliability. I recently worked with a client in the Middle East who was designing a critical piping system for a new desalination plant. Their initial specification was for Grade 316L (austenitic), a standard choice for such applications. However, given the high-chloride environment and elevated operating temperatures, their design was at significant risk for Stress Corrosion Cracking (SCC), a notorious and often sudden failure mode for austenitic steels under tension in these conditions.
During our consultation, I explained how the ferritic phase in a duplex steel like 2205 actively resists this type of cracking. The mixed microstructure isn't a metallurgical curiosity; it’s a built-in defense mechanism that protects the integrity of the asset. By switching to duplex pipes, which we supplied from our extensive inventory at MFY, they didn't just procure a more reliable material. They engineered a system with a significantly longer service life and lower maintenance costs, effectively designing out the risk of a catastrophic failure. This experience underscores why a deeper dive into the "why" behind these properties is essential for any engineer or project manager.
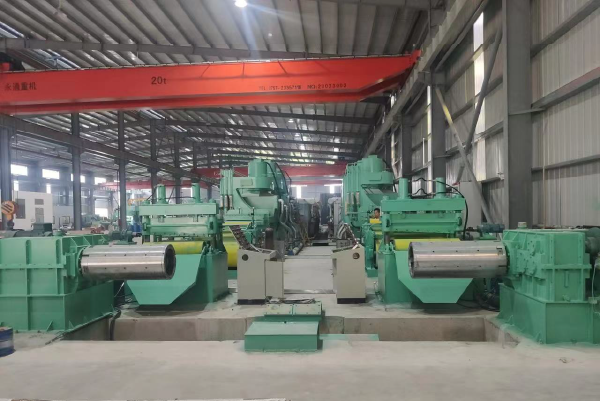
The Two-Phase Microstructure: A Best-of-Both-Worlds Approach
The defining characteristic of duplex stainless steel is its two-phase microstructure3, which is typically a balanced 50/50 mix of austenite and ferrite. To put it simply, austenitic steels have a face-centered cubic (FCC) crystal structure, which gives them excellent toughness and formability. Ferritic steels have a body-centered cubic (BCC) structure, providing higher strength and resistance to stress corrosion cracking. Duplex steel combines these two phases in a single material, creating a composite-like structure at the microscopic level. This is fundamentally different from the single-phase structure of a standard austenitic grade like 304 or 316.
This unique structure directly impacts the material's performance. The interfaces between the austenite and ferrite grains act as barriers that impede the propagation of cracks, which is the core reason for its superior resistance to SCC. The ferritic phase provides the backbone of strength, while the austenitic phase ensures the material doesn't become brittle, maintaining good toughness and ductility. This synergistic relationship is what allows duplex steel to outperform its single-phase counterparts in so many demanding applications.
To quantify one of its key benefits, the industry uses the Pitting Resistance Equivalent Number (PREN)4. Calculated as PREN = %Cr + 3.3 %Mo + 16 %N, this value provides a quick, objective measure of a material's resistance to localized pitting corrosion. For example, Grade 316L has a typical PREN of around 25. In contrast, Duplex 2205 has a PREN of about 35, while super duplex grades can exceed 40. This tangible metric is a critical tool our clients use to compare materials and select the most durable option for corrosive service.
Corrosion Resistance: Beyond the Basics of 316L
When discussing corrosion, we must look beyond general resistance. Duplex steel's primary advantage lies in its exceptional performance against specific, aggressive forms of corrosion. The most significant of these is Коррозионное растрескивание под напряжением (SCC)5, a phenomenon that can cause sudden, brittle failure in austenitic steels when they are exposed to a combination of tensile stress, chlorides, and temperatures typically above 60°C (140°F). This is the silent killer responsible for countless failures in heat exchangers, piping, and tanks in industries from chemical processing to indoor swimming pools.
Beyond SCC, the higher chromium, molybdenum, and nitrogen content in duplex steels provide robust defense against pitting and crevice corrosion. I worked with a chemical processing client in Mumbai who was experiencing premature failures in their 316L storage tanks due to pitting from a chloride-rich solution. After analyzing their failure reports, it was clear that the material was simply not robust enough for the service environment. We supplied them with Duplex 2205 sheets from our coil processing center, and the switch completely eliminated this recurring maintenance headache. The higher PREN was not just a number on a spec sheet; it was the direct solution to their costly operational problem.
Of course, no material is perfect. It is critical to understand the limitations. Duplex steels can be susceptible to embrittlement if held for extended periods at temperatures above 300°C (570°F) due to the formation of undesirable intermetallic phases. This is a crucial consideration where certain high-temperature austenitic grades might have an advantage. It highlights the importance of application-specific material selection, a process where our technical team at MFY provides critical guidance to our partners.
Mechanical Properties and Weldability: A Practical Comparison
The most striking mechanical property of duplex stainless steel is its strength. Standard duplex grades have roughly double the yield strength of common austenitic grades. This is not an incremental improvement; it is a transformative advantage that has profound implications for design and cost. The table below gives a clear comparison of the minimum specified yield strengths for several common grades.
Класс | Type | Minimum Yield Strength (MPa) | Minimum Yield Strength (ksi) |
---|---|---|---|
304L | Аустенитные | 170 | 25 |
316L | Аустенитные | 170 | 25 |
2205 | Дуплекс | 450 | 65 |
2507 | Super Duplex | 550 | 80 |
This higher strength allows for a direct reduction in material thickness without compromising safety or performance. I recently advised an engineering contractor in Vietnam who was designing a pedestrian bridge near the coast. By substituting Duplex 2205 for the originally specified 316L, they were able to reduce the thickness of the main structural members by nearly 30%. This not only yielded direct savings on material costs but also cascaded into lower transportation expenses and a reduced load on the bridge's foundations.
A common concern that arises is weldability. It is true that welding duplex steels requires more control over heat input and the use of appropriate filler metals to ensure the finished weld maintains the correct 50/50 phase balance in the weld zone. However, this should be viewed not as a disadvantage but as a required best practice. With modern welding procedures and proper training, achieving high-quality, reliable welds is a straightforward process. At MFY, we see it as part of our service to provide our clients with comprehensive welding guidelines and technical support, ensuring they can confidently fabricate with duplex and unlock its immense performance benefits.
Duplex steel has higher yield strength than austeniticПравда
Duplex grades like 2205 have ~450MPa yield strength versus 170MPa for standard austenitic grades, enabling thinner designs.
316L is better than duplex for all chloride environmentsЛожь
Duplex steels outperform 316L in chloride-rich environments due to higher PREN values and SCC resistance.
How does the strength of duplex stainless steel compare to that of austenitic stainless steel?
Are you potentially over-engineering your projects with unnecessarily thick and heavy materials? This common practice wastes capital, increases structural weight, and complicates logistics, all because the design is based on a weaker steel. Let's quantify the strength advantage of duplex and see how it translates into tangible design efficiencies.
Duplex stainless steels, such as Grade 2205 stainless steel, typically possess a minimum yield strength of around 450 MPa (65 ksi). This is more than double the strength of common austenitic grades like 304L and 316L stainless steel, which have yield strengths of approximately 170 MPa (25 ksi).
This dramatic difference in strength is often the single most impactful factor for our clients. It's not an incremental improvement; it's a complete game-changer. I recall working with a manufacturer of pressure vessels for the oil and gas sector in Russia. They were constrained by strict road transportation weight limits for their modules. Their standard design using 316L was simply too heavy to ship. By redesigning the vessel with Duplex 2205, they leveraged its superior strength to significantly reduce the wall thickness. This simple change brought the entire module within the legal weight limit, solving a critical logistical bottleneck that had threatened the entire project's viability. The strength wasn't just a number on a material certificate; it was the key that unlocked the project.
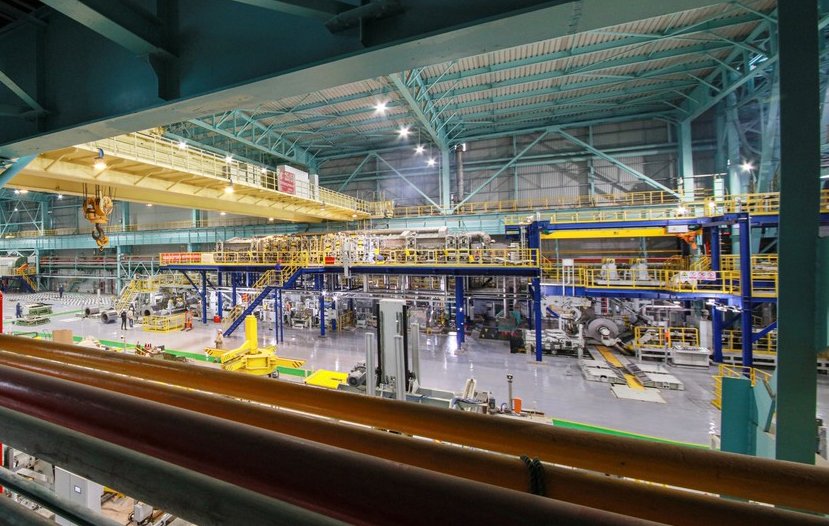
Quantifying the Yield Strength Advantage: A Numbers-Driven Look
In engineering design, particularly for structural components and pressure-containing equipment, yield strength is the most critical mechanical property. It represents the point at which a material begins to permanently deform under load. While tensile strength indicates the ultimate breaking point, yield strength dictates the practical design limit. For a material to be considered safe and reliable, the stresses it experiences in service must remain well below this point.
The numbers speak for themselves. As noted, common austenitic grades like 304L and 316L have a minimum specified yield strength of around 170 MPa. In sharp contrast, a standard duplex grade like 2205 offers a minimum yield strength of 450 MPa—a 2.6-fold increase. For even more demanding applications, super duplex grades like 2507 push this value to 550 MPa. This isn't a minor difference; it's a fundamental leap in performance capacity that designers can and should leverage.
This advantage is formally recognized and codified in major international design standards, such as the ASME Boiler and Pressure Vessel Code6 and the Eurocode standards for structural design. These codes explicitly permit the use of higher allowable design stresses for materials with higher specified yield strengths. This means that designing with duplex steel is not a workaround or a niche technique; it is a safe, accepted, and highly efficient engineering practice that allows for the creation of stronger, lighter, and more optimized structures.
From Strength to Savings: The Thinner, Lighter, Cheaper Reality
The direct consequence of higher strength is the ability to use less material to do the same job. This is best understood through the concept of the strength-to-weight ratio, a key metric where duplex steels excel. A higher ratio means you get more structural performance for every kilogram of steel you purchase. This translates directly into designs with thinner walls, smaller profiles, and reduced overall weight.
Consider a practical example I often share with clients: a large storage tank. If a tank designed with 316L requires a wall thickness of 10mm, a redesigned tank using Duplex 2205 to hold the same pressure could potentially require a wall thickness of only 6-7mm. This represents an immediate material weight reduction of 30-40%. At MFY, we see this play out in our order book every day. Clients who once ordered thick austenitic sheets are now ordering thinner gauge duplex coils for the same applications, realizing significant direct material savings.
The economic benefits do not stop at the material purchase order. This weight reduction creates a cascade of savings throughout the project lifecycle. Lighter materials mean lower freight and shipping costs, especially for international projects. On-site, lighter components can be handled and installed with smaller, less expensive cranes. Furthermore, the reduced dead load of the structure can lead to smaller and less substantial foundations, resulting in significant savings in civil engineering works. These downstream savings often dwarf the initial material cost difference, reducing the Total Installed Cost of the project.
Strength Under Duress: Fatigue and Toughness Considerations
A common misconception is that higher-strength materials are inherently more brittle. While this can be true for some materials, duplex stainless steels defy this assumption. Thanks to the austenitic phase in their microstructure, which imparts excellent toughness and ductility, duplex steels maintain high impact strength, even at low temperatures (down to -50°C or -58°F). This makes them a reliable choice for applications in cold climates or where sudden impacts are a risk, a key advantage over purely ferritic steels which can become brittle at low temperatures.
The higher strength of duplex steel also translates into superior fatigue performance. For components subjected to cyclic loading—such as pump shafts, agitators, or structural elements in vibrating machinery or bridges—fatigue resistance is critical to ensuring a long service life. I worked with an equipment integrator in our Southeast Asian market who was experiencing premature shaft failures in a series of high-vibration industrial pumps. The 316L shafts were failing due to fatigue cracking. By manufacturing new shafts from Duplex 2205 bar stock, they completely resolved the issue, as the duplex material's higher endurance limit could withstand the cyclic stresses indefinitely.
It's also important to acknowledge the trade-offs. Austenitic steels exhibit higher uniform elongation, meaning they can be stretched more significantly before fracturing. This property makes them exceptionally well-suited for applications requiring extreme formability, such as deep-drawn kitchen sinks or complex architectural panels. In these specific cases, the superior ductility of an austenitic grade might be the deciding factor. The key is to match the material’s specific set of strengths to the primary demands of the application.
Duplex steel is stronger than austeniticПравда
Duplex 2205 has a yield strength of 450 MPa, more than double that of common austenitic grades like 316L (170 MPa).
Higher strength means thicker wallsЛожь
Higher strength actually allows for thinner walls - a 316L tank needing 10mm walls could use 6-7mm duplex for equivalent strength.
What are the cost differences between duplex stainless steel and austenitic stainless steel?
Is the initial price tag of duplex stainless steel making you hesitate? Focusing solely on the per-kilogram cost is a common trap that can blind you to massive lifecycle savings, potentially leading you to select a solution that is far more expensive in the long run. Let’s perform a more honest analysis of the true cost.
While the per-kilogram price of duplex stainless steel can be comparable to or slightly different from austenitic grades, its higher strength allows for thinner sections. This frequently leads to a lower total material cost, reduced fabrication expenses, and a significantly lower Total Installed Cost (TIC).
The cost conversation is one I have every single day at MFY, and it's perhaps the most misunderstood aspect of selecting high-performance materials. A distributor partner of ours in the UAE once told me, "Cosmos, my customers just look at the price per tonne, and duplex looks expensive." We sat down and reframed the calculation. Instead of looking at the cost per tonne of steel, we calculated the cost per meter of a specific pipeline. When we factored in the thinner wall thickness and reduced weight per meter that duplex allowed, the cost per meter was actually 15% lower than its 316L counterpart. This simple shift in perspective transformed his entire sales strategy. It’s a powerful reminder that true value is found not in the sticker price but in the efficiency a material creates.
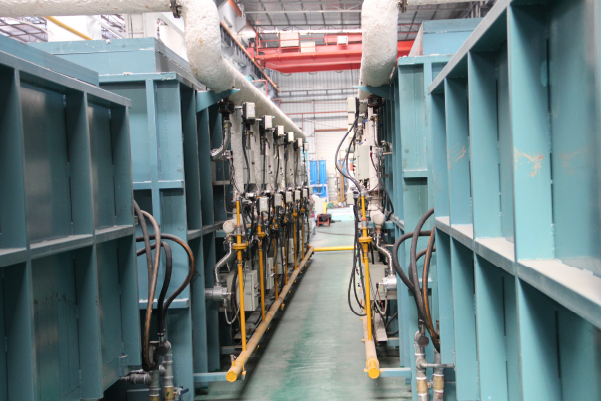
The Price-per-Kilogram Myth: Deconstructing Material Costs
A primary driver of stainless steel cost is the blend of alloying elements. Austenitic grades like 304 and 316L are characterized by a high nickel content (typically 8-12%). Duplex grades, by design, contain significantly less nickel (usually in the 3-7% range) but have higher amounts of chromium and additions of nitrogen, which contribute to their strength and corrosion resistance. Historically, nickel has been one of the most volatile and expensive commodities on the metals market.
This difference in alloy content has a direct impact on pricing and stability. The lower nickel content means that duplex steel prices are often less susceptible to the wild swings of the nickel market. During periods of high nickel prices, duplex grades can even be significantly cheaper per kilogram than 316L. As a key player in the global supply chain, we at MFY help our clients navigate this volatility. Our deep market integration and large-scale purchasing power allow us to offer stable, forward-looking pricing that helps de-risk our clients' procurement strategies.
Ultimately, the key takeaway is that the direct material cost is not a simple, static equation. It's a dynamic variable. However, the more important part of the story is that even if the per-kilogram price is slightly higher, you are almost always buying fewer kilograms. The focus must shift from the cost of the raw material to the cost of the finished component.
Total Installed Cost (TIC): The True Economic Benchmark
Experienced project managers and CFOs know that the material purchase order is just one line item in a much larger budget. The most accurate measure of a project's upfront expense is the Total Installed Cost (TIC), which is the sum of all direct costs required to get a component in place and operational. A comprehensive TIC calculation includes: Material Cost + Fabrication & Welding Cost + Transportation Cost + Installation Cost.
The higher strength of duplex steel positively influences each of these subsequent factors. In fabrication, for example, welding a thinner duplex component often requires less filler metal and fewer welding passes than joining a thicker austenitic one, saving both time and consumables. While duplex requires more careful control of welding parameters, the overall reduction in welding volume for heavy-section fabrications is often a net financial win.
The most significant savings, however, are often realized in logistics and installation. Let's revisit the example of the Vietnamese pedestrian bridge. The lighter duplex components not only reduced shipping costs from our port in China but also enabled the use of smaller, more agile cranes on a congested construction site. This reduced equipment rental costs and labor hours. Furthermore, the lighter overall structure decreased the load on the foundations, allowing for a less expensive civil works package. These are real, quantifiable savings that can add up to tens or even hundreds of thousands of dollars, completely eclipsing any minor difference in the initial material price.
Life Cycle Costing (LCC): The Long-Term Value Proposition
For asset owners, the analysis cannot stop at installation. The true economic performance of a material is revealed over its entire service life. Life Cycle Costing (LCC) provides this long-term perspective. The LCC equation is: TIC + Lifetime Maintenance & Repair Costs + Operational Costs - End-of-Life Salvage Value. For critical infrastructure, this is the ultimate measure of financial efficiency.
This is where the superior corrosion resistance of duplex stainless steel creates immense value. By resisting SCC, pitting, and crevice corrosion more effectively than austenitic grades, duplex components require less frequent inspection, maintenance, and replacement. Consider a chemical plant that must shut down its operations to repair or replace a corroded tank or heat exchanger. The cost of lost production during that downtime can be astronomical, often far exceeding the original cost of the equipment. A study by a major chemical company found that switching from 316L to Duplex 2205 for their heat exchangers extended the service life from 5 years to over 15 years, resulting in an LCC reduction of over 60%.
This long-term reliability and durability is the hidden value proposition of duplex steel. When we at MFY supply high-quality duplex coils, sheets, or pipes for a critical application, we are not just selling a commodity. We are providing our clients with operational certainty, enhanced safety, and a superior long-term financial return. It is a strategic investment in resilience, not just a purchase.
Duplex allows thinner sections than austeniticПравда
Duplex stainless steel's higher strength enables thinner material sections while maintaining performance, reducing overall material costs.
Nickel content determines all cost differencesЛожь
While nickel content affects price, total cost depends on multiple factors including fabrication, installation, and lifecycle savings.
In what applications does duplex stainless steel offer advantages over austenitic stainless steel?
Are you unsure where duplex steel truly shines in the real world? Using it in the wrong application is wasteful, but ignoring it in the right one means missing out on significant performance, safety, and cost benefits. Let’s pinpoint the specific applications where duplex steel is the undisputed champion.
Duplex stainless steel excels in applications requiring both high strength and superior corrosion resistance, particularly against chloride stress corrosion cracking. Key areas include oil and gas infrastructure, chemical processing plants, desalination facilities, pulp and paper manufacturing, and structural components in marine environments.
The list of ideal applications is growing every year as more engineers and designers recognize this powerful value proposition. A few years ago, I visited a construction site for a large architectural project in Southeast Asia. They were building a stunning coastal walkway constantly exposed to salt spray. The original specification called for mirror-polished 316L. I pointed out the long-term risks of both SCC from residual stresses and unsightly "tea-staining," a common form of surface corrosion on austenitic steels in marine atmospheres. We worked with their engineers to specify a lean duplex grade. Not only did it provide far better corrosion assurance, but its higher strength allowed for a more slender, elegant support structure, which actually enhanced the architect's original vision. This is a perfect example of how the right material can elevate a project from good to great.
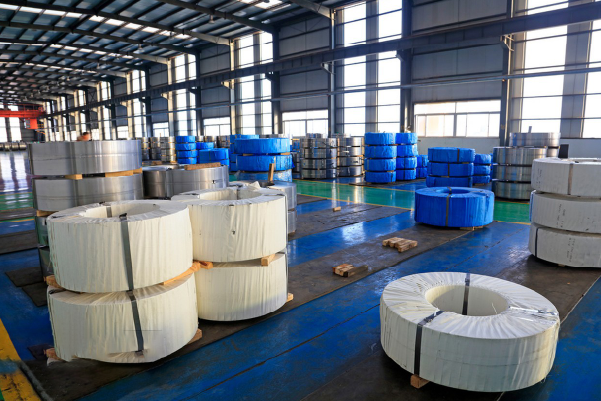
The Marine and Oil & Gas Frontier: Conquering Harsh Environments
The primary challenge in marine and offshore oil and gas environments is the relentless attack of chloride-induced corrosion. Seawater is a perfect storm: high in chlorides, rich in oxygen, and often at elevated temperatures, creating an environment where austenitic steels are highly vulnerable to SCC, pitting, and crevice corrosion. This is the domain where duplex and super duplex steels are not just an option, but often a necessity.
Consider the critical application of subsea flowlines and umbilical tubing, which transport corrosive well fluids under immense external pressure. Super duplex grades like 2507 are now the industry standard for these components. Their immense strength easily resists the crushing pressures of the deep sea, while their PREN of over 40 ensures exceptional resistance to the corrosive fluids both inside and out. At MFY, we regularly supply high-quality duplex and super duplex coils and pipes that form the backbone of these demanding offshore projects in key markets like the Middle East and Russia.
Desalination plants are another core application area. Processes like Multi-Stage Flash (MSF) and Reverse Osmosis (RO) create highly concentrated, hot brine solutions that are extremely aggressive to most materials. Duplex and super duplex steels are the materials of choice for high-pressure piping, pumps, valves, and evaporator vessels, where a material like 316L would have a very short and unreliable service life. The operational reliability of the world's freshwater supply in many arid regions hinges on the performance of these advanced steels.
Chemical Processing and Pulp & Paper: Resisting Aggressive Media
The chemical process industries (CPI) handle a vast and complex array of corrosive substances. Duplex stainless steels provide a versatile and cost-effective solution for tanks, pressure vessels, reactors, and heat exchangers that must handle media containing chlorides, various acids, and caustic solutions. In many cases, duplex can effectively replace more expensive high-nickel alloys, offering a sweet spot of performance and cost.
I worked directly with a pulp and paper mill in India that was facing constant production interruptions due to corrosion in their bleaching equipment, which uses aggressive chemicals like chlorine dioxide. Their existing 316L components were failing at an alarming rate, posing both safety and financial risks. By collaborating with their engineering team, we helped them upgrade the critical components to Duplex 2205. The switch dramatically increased the plant's uptime and safety. The unique combination of duplex's chemical resistance and high strength made it the ideal technical and commercial solution.
In heat exchanger applications, the benefits are twofold. The superior corrosion resistance extends the equipment's life, but the higher strength also allows for the use of thinner-walled tubes. Thinner tubes not only save on material costs but also improve thermal efficiency, allowing for more effective heat transfer. This leads to direct operational savings in energy consumption, a subtle but significant benefit that process engineers highly value.
Architecture, Building, and Infrastructure (ABI): Strength Meets Aesthetics
In the world of Architecture, Building, and Infrastructure (ABI), the unique combination of high strength, exceptional corrosion resistance, and low life cycle cost is driving a rapid adoption of duplex stainless steels. This is especially true for landmark projects and critical public infrastructure where longevity and minimal maintenance are paramount. Iconic structures like the Helix Bridge in Singapore and the Stonecutters Bridge in Hong Kong famously utilized duplex stainless steel for critical structural and aesthetic elements.
My personal experience with the coastal walkway project in Southeast Asia is a prime example of this trend. By choosing duplex, the client not only saved money on the total installed cost and achieved a more graceful, slender design, but they also secured a structure with a design life of over 100 years with minimal expected maintenance. This combination is an incredibly powerful value proposition for public infrastructure projects where long-term costs are a major concern for governments and taxpayers.
A rapidly growing application in this sector is the use of duplex stainless steel for concrete reinforcement rebar. In bridges, coastal flood defenses, and marine structures, traditional carbon steel rebar is prone to corrosion, which causes the surrounding concrete to crack and spall, leading to costly repairs and a shortened lifespan. The exceptional corrosion resistance of duplex rebar prevents this degradation, dramatically extending the life and safety of the concrete structure. MFY is actively involved in supplying material for this forward-thinking application, helping build infrastructure that is truly designed to last for generations.
Duplex steel resists chloride stress corrosionПравда
Duplex stainless steel has superior resistance to chloride stress corrosion cracking compared to austenitic steels, making it ideal for marine applications.
316L is better for desalination plantsЛожь
Duplex and super duplex steels are preferred in desalination plants due to their ability to withstand highly concentrated, hot brine solutions that would quickly degrade 316L.
What are the best practices for choosing between duplex and austenitic stainless steel?
Are you feeling overwhelmed by the choice between two excellent but very different materials? Making a decision based on habit or incomplete information can lock your project into a suboptimal design for decades. To avoid this, let's walk through a systematic, best-practice approach to ensure you make the right choice, every time.
Best practices for choosing involve a holistic evaluation. First, rigorously analyze the service environment, specifically temperature and chloride levels. Second, assess the mechanical strength requirements to identify opportunities for weight and cost savings. Finally, conduct a life cycle cost analysis that moves beyond initial price.
Choosing the right steel is less like picking an item off a menu and more like a medical diagnosis. You must understand all the symptoms—the environmental conditions, the structural loads, the budget constraints, the fabrication methods—before prescribing the optimal solution. I remember a client who came to us for a large order of 316L pipe for a food processing plant in India. It was a standard, "safe" choice. I asked a few simple questions about their Clean-in-Place (CIP) cycle, which involved hot, chloride-based sanitizing solutions. It quickly became clear that Stress Corrosion Cracking7 was a very real risk. We ran a quick cost-benefit analysis, showing that a lean duplex grade would offer total immunity to SCC in their specific process for a negligible increase in initial cost. They made the switch and avoided a potential product recall or catastrophic plant shutdown. This consultative approach is key.
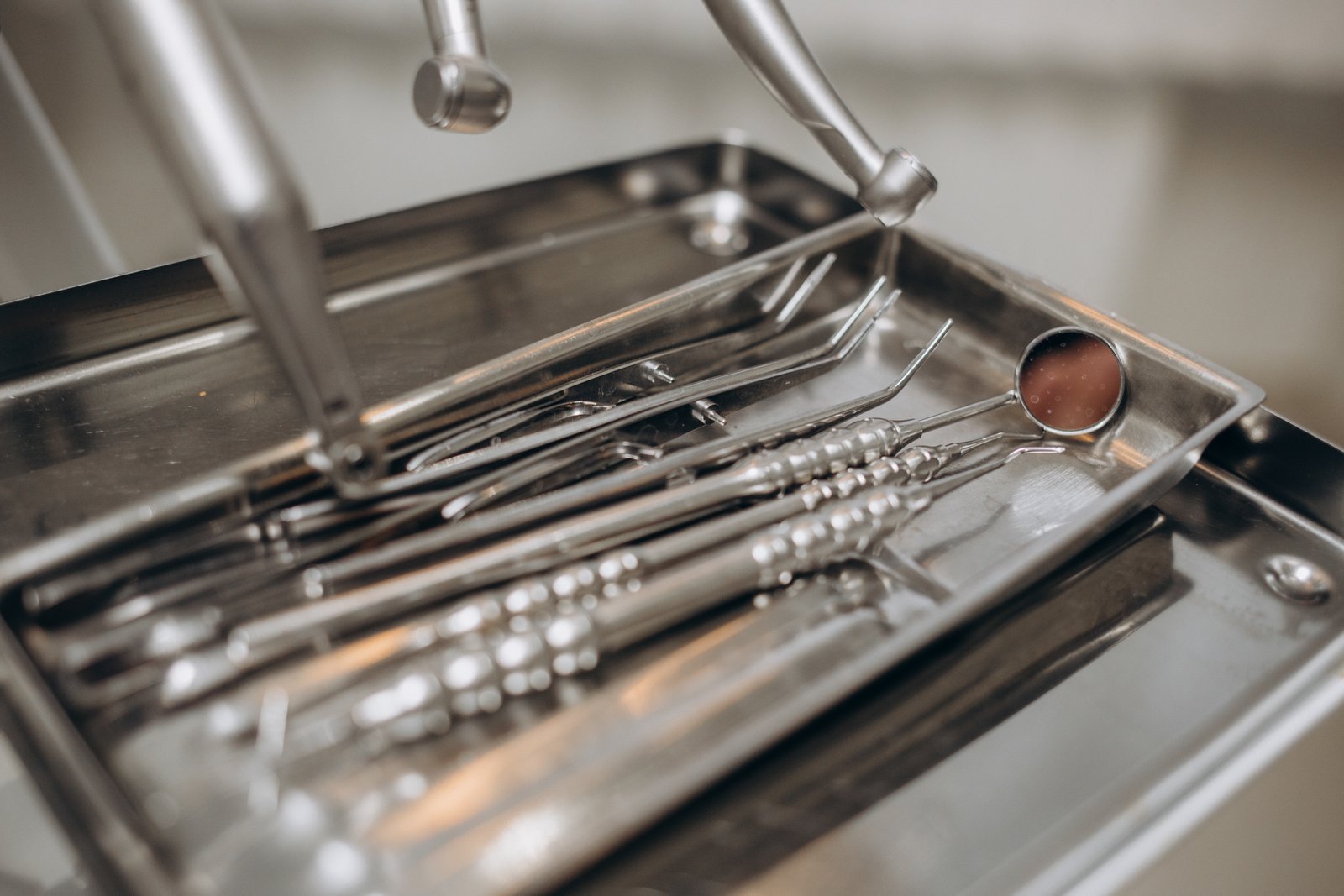
Step 1: A Rigorous Environmental and Mechanical Audit
The selection process must begin with a thorough audit of the application's demands. Start with the service environment. What is the maximum continuous operating temperature? What is the concentration of chlorides, sulfides, or other specific corrosive agents in the process stream or atmosphere? A simple decision tree can be helpful here: if the operating temperature is consistently above 60°C (140°F) and chlorides are present, the risk of SCC for austenitic steels becomes significant, and duplex grades should be strongly considered as the baseline option.
Next, conduct an audit of the mechanical requirements. What is the primary load on the component? Is it static, like the internal pressure in a storage tank, or is it dynamic and cyclic, like the load on a bridge or a pump shaft? Identify the design-limiting property: is it yield strength (for resisting deformation), tensile strength (for resisting fracture), or fatigue life (for resisting cyclic loads)? If the design is strength-driven, duplex steel immediately presents an opportunity for optimization that should be fully explored.
Finally, be honest about fabrication requirements. What level of forming and welding is needed? Does the component require severe deep drawing or stretching, a process that favors the high ductility of austenitic steel? Or is it primarily constructed from plate, pipe, and structural profiles, which are applications where duplex is easily fabricated? A candid assessment of your or your contractor's fabrication capabilities is crucial. At MFY, we help bridge any experience gaps by providing our clients with comprehensive technical support and best-practice welding guidelines along with our material deliveries.
Step 2: The Economic Analysis - Total Cost of Ownership
Once the technical requirements are understood, the economic analysis can begin. It is essential to move beyond the simplistic and often misleading metric of price-per-kilogram. The most effective approach is to create a simple comparison model to estimate the Total Installed Cost (TIC) for both the austenitic and duplex options. This model should include line items for the required material volume (calculated based on the different required thicknesses), the resulting material cost, estimated welding consumables and labor, transportation costs, and installation expenses. This exercise will provide a much clearer picture of the true upfront cost.
For asset owners and long-term operators, the analysis must be extended to the full Life Cycle Cost (LCC). Add factors to your model for estimated annual inspection and maintenance costs (which will be lower for the more corrosion-resistant option), the expected service life before major replacement is needed, and any operational gains (like improved heat transfer). A slightly higher TIC for a duplex solution can be paid back many times over through decades of reduced maintenance, increased uptime, and superior reliability.
As part of this financial analysis, a savvy procurement manager should also consider market dynamics. As I mentioned previously, the lower nickel content of duplex steels can insulate your project budget from the price volatility of the nickel market8, which heavily influences austenitic grade pricing. This price stability is a strategic advantage that provides greater cost certainty during the project planning and execution phases.
Step 3: Partnering with Your Supplier for Expert Guidance
Your material supplier should be far more than a transactional vendor; they should serve as a technical partner in your project's success. An expert supplier doesn't just know their product catalog; they understand your applications, challenges, and goals. When a new or existing client approaches my team at MFY, our first objective is always to understand the project's unique technical and commercial drivers.
You should leverage your supplier's expertise. At MFY, we have access to a wealth of performance data and case studies from thousands of successful applications across a diverse range of industries and geographic regions, from manufacturing in India to infrastructure in Russia. We can share anonymized performance data, fabrication best practices, and insights into the subtle differences between various grades—for instance, advising when a cost-effective lean duplex is sufficient versus when a robust super duplex is necessary. This is a level of detail you simply cannot find on a generic technical data sheet.
Ultimately, the final material selection should be a collaborative decision. It should be an informed synthesis of your team's intimate knowledge of the project's requirements and your supplier's deep, specialized knowledge of material science and performance. This partnership-based approach de-risks the entire process, ensuring that the final choice is not just technically sound, but also commercially optimal and strategically brilliant for the long-term success of your asset.
Duplex resists SCC betterПравда
Duplex stainless steels offer superior resistance to stress corrosion cracking (SCC) in chloride environments compared to austenitic grades.
Price-per-kg is sufficientЛожь
Material selection requires total cost of ownership analysis including fabrication, maintenance, and lifecycle costs, not just initial price.
Заключение
Ultimately, duplex stainless steel presents a compelling value proposition. Its superior strength and corrosion resistance often translate into lower total project costs and enhanced longevity, despite a sometimes similar initial price. The right choice hinges on a holistic analysis of the environment, strength needs, and life cycle costs.
-
Learn about the unique advantages and applications of duplex versus austenitic stainless steel. ↩
-
Discover the characteristics and standard uses of 304 and 316 stainless steel. ↩
-
Understand the impact of microstructure on strength and corrosion resistance in duplex steels. ↩
-
Gain insight into using PREN to evaluate corrosion resistance in stainless steel. ↩
-
Learn about the causes and prevention strategies for SCC in stainless steels. ↩
-
Get insights on how the ASME Code supports efficient and safe design engineering ↩
-
Understand the risks of stress corrosion cracking in stainless steel and its impact on material choice. ↩
-
Discover how fluctuations in the nickel market influence stainless steel costs and investment stability. ↩
У вас есть вопросы или нужна дополнительная информация?
Свяжитесь с нами, чтобы получить индивидуальную помощь и квалифицированный совет.