Таблица соотношения калибров и миллиметровых листов: Бесплатно скачать PDF
Затрудняетесь со сложными пересчетами калибров листового металла в миллиметры? Неточные расчеты могут привести к катастрофическим и дорогостоящим ошибкам в производстве и строительстве, срывая сроки и бюджеты проектов. Представьте себе, что вы заказали нержавеющую сталь неправильной толщины, что привело к целому каскаду проблем. Именно поэтому я предоставляю четкую и надежную таблицу перевода калибров в миллиметры в формате PDF для бесплатного скачивания.
Таблица пересчета калибров в миллиметры - это справочная таблица, которая переводит стандартные номера калибров (например, US Standard Gauge для стали) в точные миллиметровые (мм) и дюймовые измерения. Этот важный инструмент помогает инженерам, изготовителям и менеджерам по закупкам обеспечить точную спецификацию материалов, предотвращая дорогостоящие ошибки и обеспечивая выполнение требований проекта.
Правильный выбор толщины является основополагающим в любом проекте, связанном с нержавеющей сталью. Поскольку во всем мире используются различные системы измерения толщины, часто возникает путаница. За годы работы в компании MFY я видел, как это простое преобразование может сделать или разрушить проект. Это руководство не только предоставит вам бесплатный инструмент, который можно скачать, но и расскажет, как эффективно его использовать, чтобы ваши спецификации всегда были точными.
Хотя таблица пересчета кажется простой, ее важность часто недооценивают. Расхождение между различными стандартами калибровки (например, Колея проводов по британскому стандарту в сравнении с колеей по американскому стандарту1) - это исторический артефакт, который до сих пор вызывает значительные трения в мировой торговле. Например, клиент из Индии, использующий британский стандартный калибр проволоки (SWG), может указать материал, который должен быть получен на основе американского стандарта. Без четкого пересчета итоговый лист из нержавеющей стали может отличаться на критически малую величину, что повлияет на целостность конструкции или производственные допуски. Речь идет не только о цифрах, но и о преодолении коммуникационных разрывов в глобализованной цепочке поставок. Понимание этих нюансов - ключ к освоению международных закупок.
Где можно бесплатно скачать PDF-файл с таблицей соотношения калибров и мм?
Поиск надежной таблицы пересчета калибров в миллиметры в Интернете часто приводит к путанице или неточным источникам. Вам нужен надежный инструмент, к которому вы можете обратиться в любое время. Трата времени на поиск информации на сомнительных сайтах или использование некачественных таблиц может нарушить спецификации вашего проекта и привести к дорогостоящим ошибкам в работе с материалами. Чтобы решить эту проблему, я предлагаю прямое бесплатное скачивание профессионально составленной таблицы соотношения калибров и миллиметров от MFY прямо здесь.
Вы можете свободно скачать полную таблицу соотношения калибров и миллиметровых листов в формате PDF прямо с сайта MFY. Мы составили четкую и точную таблицу, охватывающую стандартный калибр США для стали, который широко используется в промышленности. Просто нажмите на ссылку ниже, чтобы получить мгновенную копию и обеспечить себя надежным справочником.
Занимая должность директора по глобальному бизнесу в компании MFY, я ежедневно общаюсь с клиентами из Индии, Юго-Восточной Азии и Ближнего Востока. В наших разговорах постоянно звучит тема необходимости четкой, стандартизированной информации. Однажды руководитель проекта в Дубае рассказал историю о важном строительном проекте, где субподрядчик заказал сталь на основе устаревшей и некорректной онлайн-таблицы. Расхождение составило всего доли миллиметра, но в результате панели не подошли, что привело к недельной задержке и значительным затратам на переделку. Этот опыт подчеркивает важный момент: источник информации имеет огромное значение. Дело не только в том, чтобы найти a график; это поиск справа диаграмма. Именно поэтому мы в MFY решили создать свою собственную схему и поделиться ею. Это не просто маркетинговая уловка; это практический инструмент, родившийся из реальных проблем, с которыми сталкиваются наши партнеры. Предоставляя этот ресурс, мы стремимся устранить одну из наиболее распространенных точек трения при международных закупках нержавеющей стали. Мы хотим предоставить нашим клиентам - будь то крупные производственные компании или местные дистрибьюторы - инструменты, необходимые для достижения успеха.
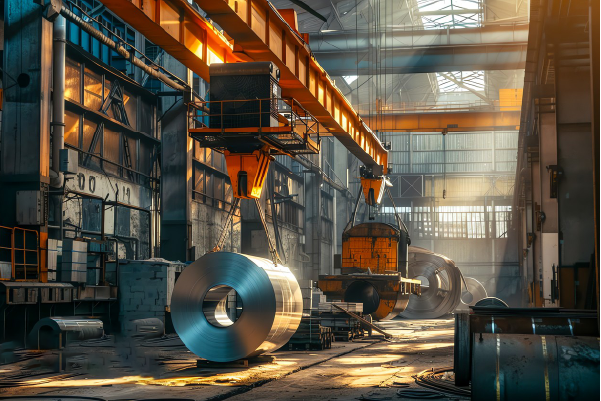
Понимание различных стандартов манометров: Почему одного графика недостаточно
Термин "калибр" не является универсальным, что является основным источником путаницы в мировой торговле. Для разных материалов и регионов существуют разные стандарты. Для стальных изделий наиболее распространенным стандартом в международной торговле является стандартный калибр производителя (MSG), также известный как стандартный калибр США (USG). Однако если вы работаете с цветными металлами, такими как алюминий или медь, вам придется использовать American Wire Gauge (AWG) или Brown & Sharpe Gauge, где значения толщины для одного и того же номера калибра совершенно разные. Кроме того, в Великобритании и странах, исторически находившихся под ее влиянием, таких как Индия, до сих пор используется стандартный калибр проводов (SWG) или британский стандартный калибр.
Эти системы имеют исторические корни, часто происходящие из процесса волочения проволоки, где каждый проход через фильеру - "волочение" - уменьшал диаметр и увеличивал номер калибра. Это объясняет контринтуитивный принцип: более высокий номер калибра означает более тонкий лист или проволоку. В то время как эта система была логичной для своей эпохи, сейчас она представляет собой минное поле потенциальных ошибок. Проектировщик в Европе может указать материал для проекта в Юго-Восточной Азии, используя сталь из Китая, и неправильное толкование стандарта калибра может привести к критическому сбою. Вот почему точная, четко обозначенная таблица пересчета - это не просто удобство, а необходимость.
Я вспоминаю ситуацию с нашим клиентом, интегратором оборудования в России, который запросил нержавеющую сталь 16-го калибра для сосуда высокого давления. Мой опыт заставил меня обратиться за разъяснениями. Оказалось, что они ссылались на стандарт SWG, что соответствует примерно 1,626 мм. Если бы мы исходили из более распространенного стандарта USG, мы бы поставили сталь толщиной 1,519 мм. Хотя разница кажется незначительной, эти десятые доли миллиметра были критическим фактором для безопасности и номинального давления сосуда. Этот случай подчеркивает, почему в нашем загружаемом PDF-файле четко указано, что он предназначен для стандартного калибра стали США, что исключает двусмысленность для наших партнеров.
Важнейшая роль централизованного проверенного ресурса
Интернет перенасыщен информацией, но большая ее часть не имеет подтверждения. Многие бесплатные таблицы пересчета публикуются на форумах или неспециализированных сайтах без перекрестных ссылок на официальные стандарты. Полагаться на такие непроверенные источники - серьезный риск для любого специалиста в области производства или строительства. Ошибка во втором знаке после запятой в миллиметре может легко вылиться в серьезные проблемы с подгонкой на сборочной линии или нарушить структурную целостность строительного элемента. Это авантюра, которую не может позволить себе ни один серьезный бизнес.
В компании MFY мы решаем эту проблему, создавая единый источник правды для наших внутренних команд и клиентов. Наш технический отдел тщательно сверяет данные, приведенные в таблице, с публикациями международных организаций по стандартизации, таких как ASTM International (Американское общество по испытаниям и материалам). Такая тщательность гарантирует точность и актуальность значений. Это больше, чем просто предоставление PDF-файла; это создание основы для доверия в работе. Когда дистрибьютор в Малайзии использует нашу таблицу для размещения заказа, он делает это с уверенностью, что полученные им рулоны нержавеющей стали будут соответствовать его спецификациям с точностью до микрона.
Рассмотрим более широкие последствия для цепочки поставок. Крупному производителю бытовой техники необходимо закупать листы нержавеющей стали марки 304 у нескольких поставщиков для удовлетворения производственных потребностей. Если каждый поставщик использует немного отличающуюся таблицу пересчета, конечная продукция может иметь несоответствующую толщину панелей, что негативно сказывается на качестве продукции и подрывает репутацию бренда. Предоставляя стандартизированную таблицу MFY всем заинтересованным сторонам, от менеджеров по закупкам до начальников цехов, мы помогаем нашим клиентам обеспечить последовательность и строгий контроль качества на всех этапах производства, защищая ценность их бренда.
Интеграция PDF в рабочий процесс для максимальной эффективности
Скачивание PDF-файла - это первый важный шаг, но его реальная ценность раскрывается, когда он должным образом интегрирован в вашу повседневную деятельность. Мы настоятельно рекомендуем нашим клиентам, особенно инженерным и строительным подрядчикам, принять нашу таблицу в качестве стандартного справочного документа в своих стандартных операционных процедурах (СОПах). Это означает, что она должна быть назначена официальным инструментом для всех запросов на закупку, инженерных спецификаций и проверок качества. Для обеспечения всеобщего доступа и контроля версий документ должен храниться на общем сервере компании или облачном диске, а не на отдельных рабочих станциях, где он может стать фрагментарным или устаревшим.
В качестве примера передовой практики можно привести одного из наших ключевых партнеров, крупного строительного подрядчика на Ближнем Востоке, который встроил прямую ссылку на нашу таблицу калибров MFY в свое программное обеспечение для закупок. Когда инженер указывает калибр стали в новом заказе, система автоматически вводит соответствующее значение в миллиметрах непосредственно из нашей проверенной таблицы, что значительно сократило вероятность ошибок при ручном вводе данных. Эта простая, но мощная интеграция позволила оптимизировать процесс закупок и практически исключить дорогостоящие ошибки, связанные с неправильной толщиной материала.
Чтобы дать вам представление о ясности и полезности, которые вы можете ожидать, ниже приведен образец нашей загружаемой таблицы, посвященной распространенным калибрам нержавеющей стали. Обратите внимание на то, как четко представлен номер калибра вместе с его эквивалентом в дюймах и миллиметрах, что устраняет любую возможность догадок или неправильного толкования. Этот удобный формат специально разработан для быстрого и безошибочного использования в быстро меняющейся профессиональной среде.
Манометр (USG) | Дюймы (дюймы) | Миллиметры (мм) |
---|---|---|
10 калибр | 0.1345 | 3.416 |
12 калибр | 0.1046 | 2.657 |
14 калибр | 0.0747 | 1.897 |
16 калибр | 0.0598 | 1.519 |
18 калибр | 0.0478 | 1.214 |
20 калибр | 0.0359 | 0.912 |
Более высокие номера калибра означают более тонкие листыПравда
Этот контринтуитивный принцип берет начало в исторических процессах волочения проволоки, когда каждый проход через фильеру уменьшал диаметр и увеличивал номер калибра.
Все системы манометров используют одинаковые измеренияЛожь
В разных стандартах (USG, SWG, AWG) для одного и того же номера калибра используются совершенно разные измерения, поэтому использование правильной таблицы очень важно.
Как использовать таблицу перевода калибров в миллиметры для определения толщины листа?
Получив номер калибра с чертежа, вы когда-нибудь испытывали чувство неуверенности при поиске его точного миллиметрового эквивалента на графике? Удивительно легко ошибиться или неверно истолковать данные под давлением. Простая ошибка, например, взгляд не на ту строку или колонку, может привести к заказу неправильных материалов, что вызовет задержку проекта и значительные финансовые потери. Я проведу вас через простой пошаговый процесс, чтобы вы точно читали диаграмму и уверенно пересчитывали любой калибр в точную толщину в миллиметрах каждый раз.
Чтобы воспользоваться таблицей перевода калибров в миллиметры, сначала найдите нужный номер калибра в колонке "Калибр". Затем переместитесь по горизонтали вдоль этой же строки в колонку "Миллиметры (мм)", чтобы найти точную толщину. Всегда проверяйте, что вы используете правильную таблицу для вашего материала (например, USG для стали).
Использование таблицы пересчета может показаться необъяснимым, но, как и в случае с любым профессиональным инструментом, правильная техника имеет решающее значение для точности. Я отчетливо помню ошибку в начале своей карьеры: я торопился и быстро взглянул на таблицу для нескольких материалов, случайно использовав значение для алюминия вместо нержавеющей стали. Материал прибыл на объект нашего клиента и был немедленно забракован. Это был неловкий и дорогой урок того, как важно быть внимательным и обращать внимание на детали. Цель состоит не только в том, чтобы найти a число; это для того, чтобы найти правильно число с абсолютной уверенностью, каждый раз. Этот процесс призван выработать привычку к точности, потому что в отрасли, где допуски измеряются микронами, "достаточно близко" никогда не будет достаточно хорошо. За годы работы я разработал простой метод проверки, которому я обучаю свою команду и наших клиентов, и здесь я поделюсь им с вами.
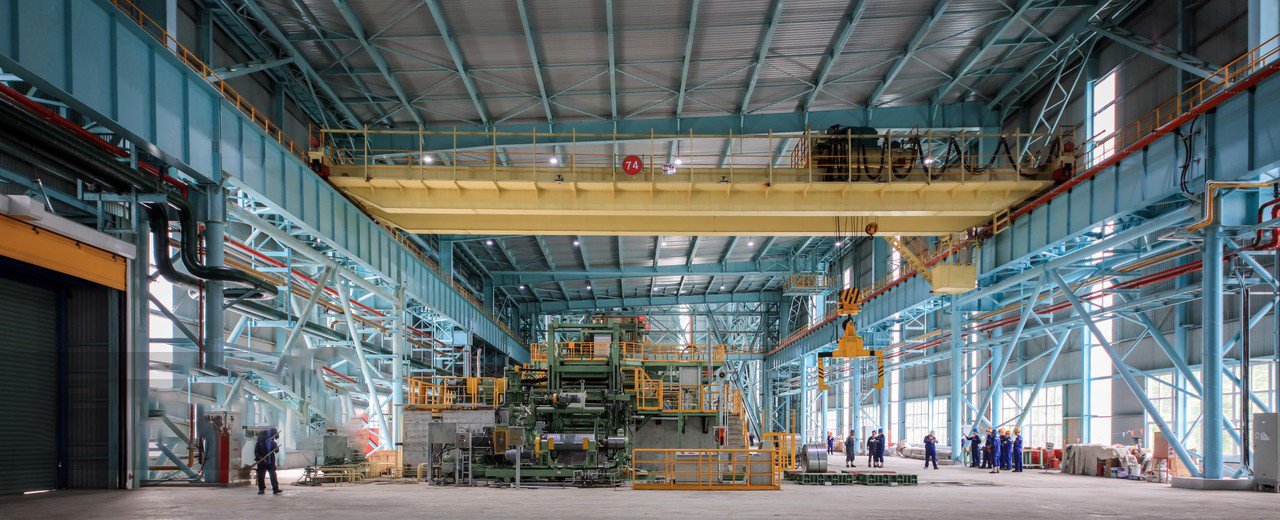
Пошаговое руководство по чтению таблицы пересчета
Точный перевод калибров в миллиметры - процесс методичный и требует тщательного подхода. Он начинается с четкого определения номера калибра, который необходимо перевести. Эта важная информация обычно содержится в спецификации проекта, инженерных чертежах или официальном запросе на поставку. Например, в техническом чертеже для проекта санитарно-технического оборудования может быть указан "лист из нержавеющей стали 316L 18 калибра", что является обычным требованием в отраслях, требующих высокой коррозионной стойкости. Это ваша отправная точка.
Once you have the gauge number, open our MFY Gauge-to-mm PDF. The table is designed for clarity, with the first column typically labeled "Gauge" or "Gauge (USG)." Scan down this column with your finger or cursor until you find the exact number you're looking for—in this case, "18." This physical act of tracing helps prevent your eyes from skipping and is a simple habit that enhances accuracy, especially when working with extensive tables or complex documents.
After you have confidently located your gauge number, "18," follow that specific row horizontally to the right. The table will present several columns, including the material's thickness in both inches and millimeters to cater to different regional and engineering preferences. Find the column explicitly labeled "Millimeters (mm)." The numerical value in that cell is the direct and precise conversion of your gauge number. For 18 gauge steel, you will find the value is 1.214 mm. While the process itself is straightforward, the key to error-free execution lies in moving slowly, deliberately tracing the line, and giving the task your full attention to prevent simple but costly mistakes.
Common Pitfalls and How to Avoid Them
One of the most frequent and costly errors in material specification is confusing different gauge standards. As I've emphasized, the thickness for "14 gauge" steel is fundamentally different from that of "14 gauge" aluminum. Our downloadable MFY chart is specifically calibrated for steel, using the US Standard Gauge (USG). It is critical to always confirm your material type before consulting any chart. For projects involving multiple materials, a best practice is to use separate, clearly labeled conversion charts for each to eliminate any possibility of a mix-up. This simple organizational step can save you from major procurement headaches.
Another common human error is transposition—inadvertently flipping digits when transcribing the value from the chart to another document, for example, writing 1.124 mm instead of the correct 1.214 mm. To combat this, I have instilled a "read-back" verification method within my team at MFY. After finding a value on the chart, you should pause, read it out loud, and then double-check it against the source. If possible, have a colleague perform a quick second check. This simple two-step verification process acts as a powerful safety net and catches a surprising number of minor errors before they can become major problems.
I recall a case with a client, a skilled fabricator for the food and beverage industry in Thailand, who was consistently ordering material that was slightly off-spec. The deviations were minor but enough to cause issues in their high-precision welding processes. After a diagnostic call, we discovered one of their junior engineers was working from a low-resolution screenshot of a chart saved on his phone. The blurry text made "1.519" appear as "1.619." The solution was simple: we provided them with our crystal-clear, high-resolution PDF and advised them to use it on a proper computer monitor. The issue was resolved immediately. The lesson here is profound: the quality and clarity of the tool you use are just as important as the process you follow.
Practical Application: From Blueprint to Purchase Order
Let's trace the complete journey of a specification to see how the table functions in a real-world scenario. An engineer is designing a series of commercial kitchen exhaust hoods and specifies 20 gauge Grade 304 stainless steel for the main panels due to its optimal balance of formability and durability. This specification, "20 ga SS304," is then officially noted on the project blueprints, which serve as the master document for the build. The project's procurement officer then receives a copy of these blueprints to begin the sourcing process.
The procurement officer’s first critical task is to translate this imperial-based gauge number into a precise metric value, as they will be ordering from an international supplier like MFY, which operates on the metric system. They open the official MFY gauge-to-mm conversion table, navigate down the "Gauge" column to find "20," and follow the row across to the "Millimeters (mm)" column. They find the corresponding thickness: 0.912 mm. With this, they have the exact metric specification required for the purchase order.
In the final purchase order (PO) sent to MFY, the officer demonstrates best practice by including both values for maximum clarity and to eliminate any potential for misinterpretation. The line item reads: "Stainless Steel Sheet, Grade 304, 20 Gauge (0.912 mm)." This dual-specification approach is something we highly recommend to all our partners. It instantly confirms to our sales and production teams that the client has performed the conversion correctly and that we are all perfectly aligned on the specification. It builds a crucial, redundant layer of verification directly into the purchasing workflow, ensuring the right material is delivered every time.
Gauge standards vary by materialПравда
A 14 gauge steel sheet has a different thickness than a 14 gauge aluminum sheet, which is why material-specific charts are essential.
All gauge charts are universalЛожь
Gauge charts are material-specific (e.g., USG for steel), and using the wrong chart will yield incorrect thickness values.
Каковы основные преимущества использования таблицы перевода калибров в миллиметры?
Are you still estimating sheet thickness or relying on memory? This can introduce unacceptable risks into your projects. Without a standardized reference, you're exposed to costly procurement errors, communication breakdowns with suppliers, and potential structural failures. The consequences of imprecision are steep. By consistently using a reliable gauge-to-mm conversion table, you can eliminate these risks, ensuring accuracy, efficiency, and quality in every project you undertake.
The key benefits of using a gauge-to-mm conversion table include ensuring procurement accuracy, reducing material waste and costs, streamlining communication between engineering and purchasing teams, and guaranteeing that the final product meets precise design and engineering specifications for optimal performance and safety.
A standardized conversion table is more than just a reference; it's a foundational tool for operational excellence. In my experience at MFY2, the companies that thrive are those that systematize precision. A simple tool like this, when adopted across an organization, creates a common language. It ensures that the engineer in the design office, the procurement manager negotiating with a supplier in China, and the fabricator on the workshop floor are all working from the exact same data. This alignment is the bedrock of an efficient and resilient supply chain. It minimizes friction, prevents rework, and ultimately protects your bottom line and your reputation for quality. When every stakeholder is on the same page regarding material specifications, projects move forward smoothly, on time, and on budget. That is the true power of this simple document.
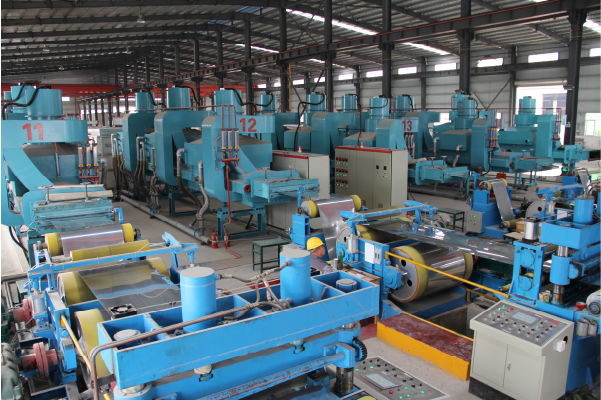
Enhancing Procurement Accuracy and Reducing Costs
The most immediate and tangible benefit of using a standardized gauge-to-mm table is the dramatic improvement in procurement accuracy. When a purchase order is created based on a precise millimeter value derived from a verified chart, the risk of ordering the wrong material is virtually eliminated. This precision is not just about getting the order right; it’s a powerful cost-control measure. Ordering the wrong thickness of stainless steel leads to a cascade of expensive problems, including shipping costs for the incorrect material, return logistics, project delays waiting for the right material, and rush order fees for the replacement. These costs can quickly erode, and even erase, a project's profit margin.
Consider a client of ours, a large-scale manufacturing company that produces automotive components. They operate on a just-in-time inventory system where precision is paramount. Before they standardized their process using our chart, they experienced a recurring issue where batches of 14 gauge steel would occasionally be ordered incorrectly, resulting in a thickness that was incompatible with their stamping dies. This would halt a production line, causing thousands of dollars in losses per hour of downtime. By making our MFY chart the single source of truth for their procurement team, they have since eliminated this issue entirely. This has not only saved them money but has also improved their production efficiency and reliability.
Furthermore, accurate specification prevents material waste. If a sheet is too thick for an application, you have paid for material you don't need, directly impacting the project's bottom line. Conversely, if the sheet is too thin, it may not meet structural or safety requirements, leading to a complete rejection of the material and the need to reorder. A reliable conversion table ensures you order exactly what is required—no more, no less. This optimization of material usage is a key principle of lean manufacturing and sustainable business practice, directly contributing to financial health and resource efficiency.
Streamlining Communication Across Global Teams
In today's globalized economy, projects often involve teams spread across different continents. An architect might be in London, the engineer in Mumbai, the procurement team in Dubai, and the material supplier, like MFY, in China. In such a distributed environment, clear and unambiguous communication is essential. The different measurement systems (imperial vs. metric) and legacy standards (USG vs. SWG) create natural barriers to this clarity. A standardized gauge-to-mm conversion table acts as a universal translator, bridging these gaps.
When all parties involved in a project agree to use a single, standardized chart, it creates a common language for material specification. The term "16 gauge" is no longer ambiguous; it is universally understood to correspond to exactly 1.519 mm (per the USG standard). This removes guesswork and the potential for misinterpretation that can arise from verbal or email communications. The chart becomes the central point of reference, ensuring alignment from the initial design concept to the final delivery of goods.
I've personally seen this benefit a major engineering and construction contractor we work with on projects across Southeast Asia. Their teams are multinational, with engineers from India, the Philippines, and Europe. Initially, they faced constant friction due to differing interpretations of gauge specifications. By implementing the MFY conversion chart as a mandatory project document, they created a unified standard. Now, when a blueprint calls for a specific gauge, everyone on the project, regardless of their native country or training, understands the exact metric thickness required. This has streamlined their request-for-quotation (RFQ) process, reduced clarification emails by over 50%, and significantly accelerated their procurement cycle.
Ensuring Engineering and Manufacturing Integrity
Ultimately, the most critical benefit of using an accurate gauge-to-mm table is the assurance of engineering and manufacturing integrity. The thickness of a stainless steel sheet is rarely an arbitrary choice; it is a calculated engineering decision that impacts the structural strength, load-bearing capacity, corrosion resistance, and overall safety and performance of the final product. Whether it's a structural beam in a building, a pressurized tank in a chemical plant, or a panel on a piece of medical equipment, using the correct material thickness is non-negotiable.
A deviation of even a fraction of a millimeter can have serious consequences. A sheet that is too thin might fail under stress, leading to catastrophic equipment failure or safety hazards. A sheet that is too thick can add unnecessary weight, increase costs, and create problems during fabrication processes like bending or welding. The conversion table is the first line of defense in ensuring that the engineer's design intent is perfectly translated into the physical product. It guarantees that the material's properties, which are directly linked to its thickness, are precisely what the application demands.
For example, we supply stainless steel pipes to a company that integrates systems for water treatment facilities. The wall thickness of these pipes is a critical parameter determined by calculations involving pressure ratings and flow dynamics. Their quality control process begins with our conversion chart. When they order a specific gauge of pipe, they use the chart to know the exact target wall thickness in millimeters. Upon delivery, they use digital calipers to verify that our product matches this specification within a tight tolerance. This rigorous process, anchored by the reliable data from the conversion table, ensures the safety, longevity, and efficiency of the public infrastructure they build. It's a clear example of how a simple tool supports the highest standards of engineering excellence.
Conversion tables prevent procurement errorsПравда
Standardized gauge-to-mm tables eliminate guesswork by providing exact thickness measurements, ensuring correct material orders.
Gauge numbers are universal worldwideЛожь
Different regions use different gauge standards (e.g., USG vs. SWG), making conversion tables essential for global projects.
Как проверить точность результатов преобразования из таблицы?
You have a conversion table, but how can you be certain it's accurate? Placing trust in an unverified document is a significant risk. An incorrect chart is worse than no chart at all, as it creates a false sense of security that can lead to major procurement mistakes. These errors can jeopardize project integrity, cause budget overruns, and damage your professional credibility. To operate with confidence, you need a robust method for verifying that the numbers you rely on are correct, precise, and trustworthy.
To verify the accuracy of a conversion table, cross-reference its values against official industry standards published by bodies like ASTM. Additionally, you can use calibrated digital calipers to physically measure a sample piece of known gauge, and implement a "dual-specification" method in purchase orders.
In the steel industry, trust is built on verification. At MFY, we never take data for granted. While we are confident in the chart we provide, I always encourage our clients to cultivate a mindset of "trust, but verify." This isn't about second-guessing your partners; it's about establishing a professional discipline that safeguards your operations. Verifying your tools is a hallmark of a mature and resilient organization. The methods I'll share are straightforward and can be easily integrated into your quality assurance procedures. They provide the peace of mind that comes from knowing your foundational data is rock-solid, allowing you to make critical decisions with confidence. This is how you build quality into your process from the ground up.
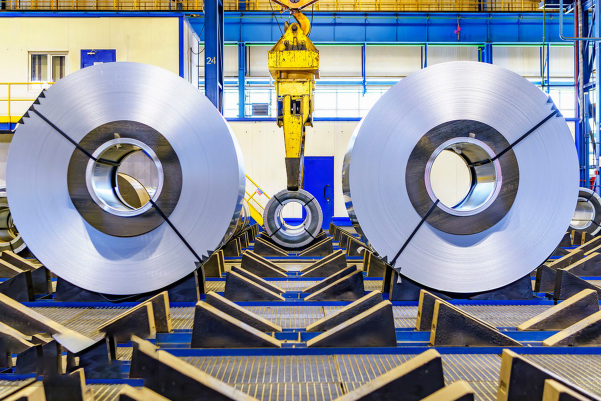
Cross-Referencing with Official Industry Standards
The most authoritative method for verifying a conversion table is to cross-reference it with documents published by internationally recognized standards organizations. For steel, the primary body in North America and widely respected globally is ASTM International. ASTM A480/A480M, for example, is a standard specification that covers the general requirements for flat-rolled stainless and heat-resisting steel plate, sheet, and strip. These documents contain the official, legally recognized tolerances and nominal thicknesses corresponding to specific gauge numbers for steel.
To perform this check, you would obtain the relevant ASTM standard (or a similar standard from ISO, DIN, or another body relevant to your region) and compare the values directly. For instance, you can look up the nominal thickness for 16 gauge steel in the ASTM standard and see if it matches the 1.519 mm (or 0.0598 inches) listed in your conversion table. Any significant discrepancy would be a major red flag, indicating that your chart is unreliable. This method is the gold standard for verification as it relies on the same source documents that manufacturers and regulators use.
While accessing these standards can sometimes require a subscription or purchase, they are an invaluable investment for any company serious about quality control. We at MFY base our own internal standards and our public-facing chart on these documents. When you use our PDF, you are leveraging data that has already been verified against these primary sources. This process of referencing foundational industry standards is the bedrock of engineering and manufacturing confidence, ensuring that the data guiding your decisions is not just a convenient number, but a certified fact.
Using Digital Calipers for Physical Measurement
A practical, hands-on method for verification is to use a calibrated measuring tool to check a physical sample. Digital calipers are an inexpensive and essential tool for anyone working with sheet metal. If you have a piece of stainless steel sheet that you know for certain is, for example, 18 gauge, you can directly measure its thickness with the calipers. The reading should closely match the value for 18 gauge in your conversion table (1.214 mm).
It's important to use a properly calibrated and high-quality caliper for this task. Before measuring, ensure the caliper is zeroed out correctly. Take measurements at several different points on the sheet to account for any minor variations in thickness allowed by manufacturing tolerances. The average of these measurements should align very closely with the table's value. A significant deviation could indicate either an issue with your sample piece or, more critically, an error in your conversion chart.
This physical verification method is particularly useful for teams on the workshop floor or for quality control personnel receiving goods. We had a client, a distributor in India, who used this method to resolve a dispute with one of their local customers. The customer claimed the 20 gauge sheet we supplied was too thin. Our client used their digital calipers to measure the sheet on-site, showing a consistent reading of ~0.91 mm, perfectly matching the MFY conversion chart they both had. It turned out the end customer was using an old, inaccurate SWG chart. The physical measurement, backed by our verified chart, resolved the issue instantly and educated the customer.
The "Dual-Specification" Method in Official Documentation
A powerful procedural method for ensuring ongoing accuracy is what I call the "dual-specification" approach. This involves including both the gauge number and its corresponding millimeter (or inch) equivalent in all official documentation, especially purchase orders and technical specifications. For example, instead of just writing "12 Gauge Stainless Steel Sheet," your purchase order should read "12 Gauge (2.657 mm) Stainless Steel Sheet." This practice serves as a built-in, continuous verification system.
When we at MFY receive a purchase order with this dual specification, it immediately allows us to cross-check the client's numbers against our own standard chart. If there's a discrepancy—for instance, if a client writes "12 Gauge (2.750 mm)"—it instantly raises a red flag. Our sales team is trained to immediately contact the client to clarify the requirement before the order is processed. This simple step prevents a potentially massive error from ever entering the production and logistics chain. It forces both the buyer and the seller to confirm they are aligned and working from the same data.
This method transforms a static document into an active verification tool. It fosters a shared responsibility for accuracy between the supplier and the customer. Over time, it helps to educate all parties and reinforces the correct values, reducing the likelihood of future errors. We have recommended this practice to all our major clients, from large construction contractors to equipment integrators. Those who have adopted it have reported a near-total elimination of thickness-related order errors, proving that a simple change in documentation habits can yield significant improvements in supply chain reliability.
ASTM standards verify gauge chartsПравда
ASTM International publishes official thickness specifications that serve as the gold standard for verifying conversion tables.
Digital calipers are unreliableЛожь
Properly calibrated digital calipers provide accurate physical measurements that can validate conversion table values when used correctly.
Что следует учитывать при применении таблицы перевода калибров в миллиметры?
You've downloaded an accurate chart and know how to use it, but how do you ensure it's applied consistently and effectively across your entire organization? Without established best practices, even the best tools can be misused or ignored. Individual team members might revert to old habits, use outdated versions, or create their own conflicting references, leading to the very same errors you're trying to prevent. To truly capitalize on the benefits, you need a strategy to embed the tool into your company's DNA.
For best practices, you should establish a single, standardized gauge-to-mm chart as the official reference for the entire organization, integrate the conversion process into digital workflows like ERP systems, and conduct regular training to ensure all technical and procurement team members apply it consistently and accurately.
Implementing best practices is about moving from having a tool to building a system. At MFY, we've seen firsthand that the most successful companies are those that prioritize process over individual preference. When you make the gauge-to-mm conversion table a non-negotiable part of your workflow, you create a culture of precision. It ceases to be a matter of choice and becomes "the way we do things here." This removes ambiguity, empowers employees with clear guidelines, and builds a resilient operational framework where quality is not an accident, but a guarantee. Let's explore how to make this a reality in your business.

Establishing a Standardized Chart Across the Organization
The cornerstone of best practice is standardization. It is absolutely critical that everyone in your organization—from engineering and design to procurement and quality control—uses the exact same gauge-to-mm conversion chart. The existence of multiple, conflicting charts within a single company is a direct path to confusion and errors. The first step is to formally designate one chart, like the MFY downloadable PDF, as the sole, official reference for the entire company.
This designated chart should be stored in a centralized, easily accessible location, such as a shared network drive or a company intranet portal. This prevents the "desktop" problem, where individuals save local copies that can become outdated or modified. All employees should be directed to this central location whenever they need to perform a conversion. Any old charts, saved bookmarks, or physical wall posters should be removed and discarded to eliminate any chance of accidental use.
I worked with a manufacturing client in the Middle East to implement this. They were struggling with inconsistent material specifications between their design team in Europe and their production facility locally. We helped them establish our MFY chart as their global standard. They uploaded it to their corporate SharePoint and sent out a company-wide memo announcing it as the only approved reference. This simple act of standardization immediately synchronized their teams, ensuring that a "14 gauge" specification from the European design office was interpreted correctly as 1.897 mm on the factory floor in Dubai.
Integrating Conversion into Digital Workflows and ERP Systems
To elevate best practices to the next level, you should look for opportunities to integrate the conversion process directly into your digital workflows. Manual data entry is a known source of human error. By automating the conversion within your existing software, you can significantly reduce this risk. Many Enterprise Resource Planning (ERP) systems, procurement platforms, or even custom spreadsheets can be configured to perform this function automatically.
For example, you could create a dropdown menu in your procurement software where an employee selects the gauge number. The system would then automatically populate the corresponding millimeter field based on a master data table that you've pre-loaded with the values from your standardized chart. This removes the need for the employee to manually look up and type the value, thus eliminating the possibility of transposition errors or other typos. It makes the correct process the easiest process.
A forward-thinking equipment integrator we partner with has taken this approach. They have built a small custom tool within their ERP system. When a project manager configures a bill of materials, they select the required steel gauge, and the system instantly shows the millimeter equivalent, the calculated weight, and the estimated cost based on data fed from our supply chain. This level of integration not only ensures accuracy but also accelerates their quoting and planning process, giving them a competitive edge. It's a prime example of how a simple conversion table can become a powerful component of a larger digital strategy.
Regular Training and Knowledge Sharing for Technical Teams
A tool is only as good as the person using it. Therefore, ongoing training and knowledge sharing are essential components of best practice. You cannot assume that everyone understands the nuances of gauge systems or the importance of using the standardized chart correctly. Regular, brief training sessions should be conducted for all relevant personnel, including new hires and existing staff in technical, procurement, and quality assurance roles.
These training sessions should cover not only how to use the chart but also почему it is so important. Use real-world examples, like some of the client stories I've shared, to illustrate the costly consequences of getting it wrong. Explain the difference between various gauge standards (e.g., USG vs. SWG) to deepen their understanding. Reinforce the company policy of using only the official, centralized chart and the dual-specification method in documentation. This creates a knowledgeable workforce that is invested in maintaining quality.
At MFY, we practice this internally. Our sales and technical support teams have quarterly refreshers on material standards. This ensures they can confidently and accurately advise our clients. We encourage our partners to adopt a similar model. A distributor in Russia, after a minor ordering mix-up, implemented a "Toolbox Talk" series. Once a month, their team leaders spend 15 minutes reviewing a key technical document, and they started with the gauge conversion chart. This proactive approach to knowledge sharing has empowered their team, reduced errors, and strengthened their own customer relationships.
Standardization prevents conversion errorsПравда
Using a single standardized chart across all departments eliminates conflicting references that could lead to measurement errors.
Manual conversions are more accurateЛожь
Manual conversions are prone to human error; integrating the process into digital workflows significantly improves accuracy.
Заключение
A reliable gauge-to-mm table is more than a tool; it’s your key to procurement accuracy, cost control, and project success. By downloading our free, verified PDF and adopting these professional best practices, you can eliminate costly errors and streamline your entire stainless steel supply chain with confidence.
У вас есть вопросы или нужна дополнительная информация?
Свяжитесь с нами, чтобы получить индивидуальную помощь и квалифицированный совет.