Duplex 2205 Chloride Resistance: Spec & Savings
Struggling with material degradation in high-chloride environments? The relentless attack of chlorides on standard stainless steel leads to costly failures and downtime. This isn't just a maintenance issue; it's a threat to your operational integrity and bottom line, forcing you to accept constant repairs. Duplex 2205 stainless steel1 offers a robust solution engineered to withstand these harsh conditions.
Duplex 2205 stainless steel offers superior chloride resistance due to its dual-phase microstructure of austenite and ferrite. This composition, enriched with chromium, molybdenum, and nitrogen, provides exceptional protection against pitting and crevice corrosion, making it a reliable and cost-effective choice for harsh industrial environments and critical applications.
The choice of material can make or break a project, especially when chlorides are a key factor. In my years at MFY, I've seen countless projects pivot from conventional 300-series stainless steels2 to Duplex 2205, not just for superior performance but for the significant long-term savings it unlocks. This shift represents a move towards smarter, more resilient engineering. Let's delve into why this material is a game-changer for your operations.
While many engineers default to standard 304 or 316L grades3, they often overlook the hidden, compounding costs of corrosion in chloride-rich settings—a classic case of short-term savings leading to long-term pain. The critical question isn't just "what material works?" but "what material provides the best life-cycle value?" A study by NACE International estimates the global cost of corrosion at a staggering $2.5 trillion annually. Duplex 2205 addresses this head-on by offering a performance profile that traditional austenitic steels simply cannot match in these specific environments, bridging the gap between elite performance and economic feasibility. This isn't just an upgrade; it's a strategic investment in reliability.
What challenges does chloride exposure pose to materials?
Are your critical projects plagued by unexpected material failures? Chloride ions are invisible aggressors, silently attacking conventional metals and compromising structural integrity. This leads to pitting, crevice corrosion, and stress corrosion cracking, causing system failures that halt production and inflate maintenance budgets. Understanding these specific corrosion mechanisms is the first step toward selecting a material truly engineered to resist them.
Chloride exposure poses significant challenges by initiating localized corrosion, such as pitting and crevice corrosion, which can lead to rapid material failure. It also promotes stress corrosion cracking (SCC), where tensile stress and a corrosive environment combine to cause sudden, brittle fractures in susceptible materials.
In my experience working with clients in the desalination and chemical processing sectors, the impact of chloride-induced corrosion is a constant, pressing concern. I recall a client in Southeast Asia operating a coastal chemical plant who initially specified 316L stainless steel for their piping systems, believing it offered sufficient protection. Within just a few years, they faced persistent leaks due to severe pitting corrosion, a problem exacerbated by the region's warm, humid, and saline atmosphere. Their maintenance costs skyrocketed, and the unscheduled downtime was crippling their production targets. This is not an isolated incident; it's a common narrative across various industries where chloride concentrations are high. The danger is that the damage isn't always visible until it's too late. Pitting can start microscopically but will penetrate deep into the material, creating a hidden pathway for catastrophic failure. This insidious threat is why a reactive maintenance strategy is both dangerous and expensive. Proactively selecting a material designed for these conditions isn't just a best practice; it's an essential risk management strategy. We must move beyond meeting minimum material specifications and start thinking about the total cost of ownership over an asset's entire lifecycle.
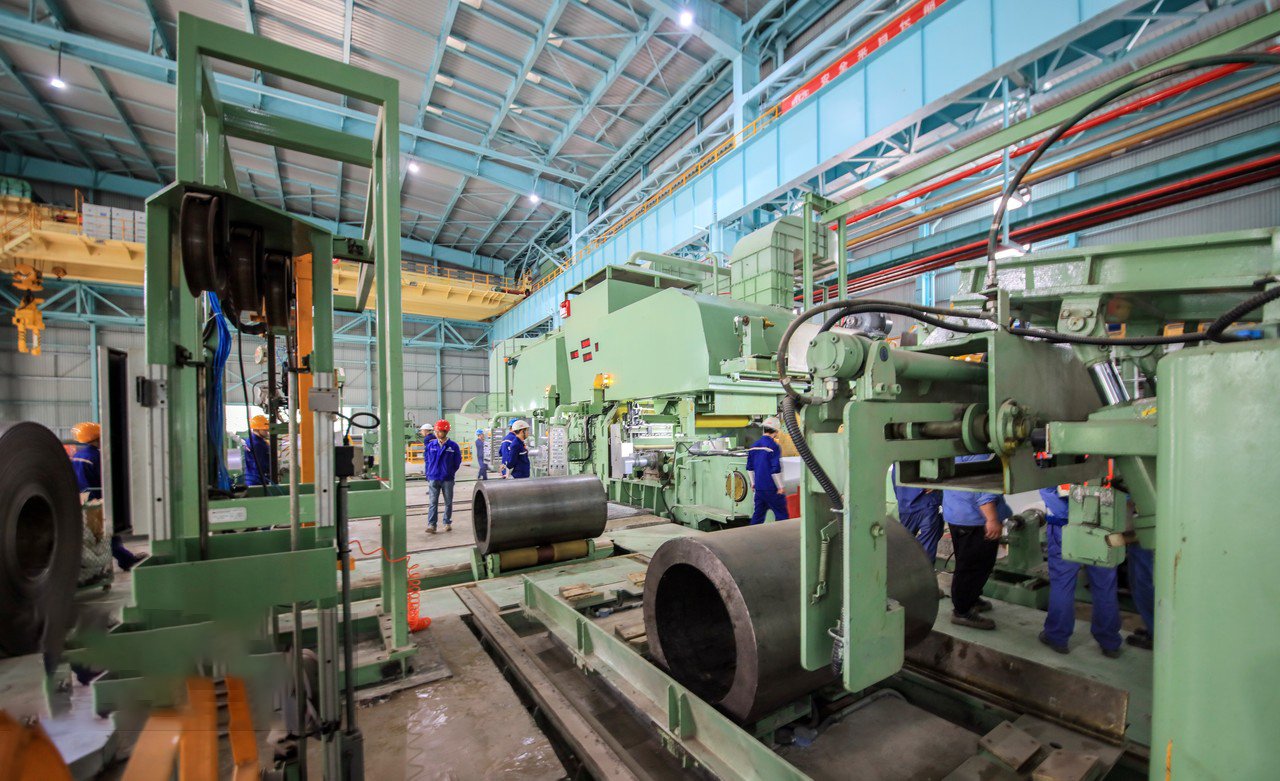
The challenges posed by chloride ions are multifaceted and attack susceptible metals through several distinct, yet often interconnected, mechanisms. For engineers and asset managers, understanding these threats is paramount to ensuring long-term structural integrity and operational reliability. Failure to account for them during the material selection phase can lead to premature failure, significant financial loss, and serious safety risks. The primary forms of attack—pitting, crevice corrosion, and stress corrosion cracking—each have unique characteristics that make them particularly destructive in chloride-rich environments. At MFY, we frequently consult with clients who have learned this lesson the hard way, and our goal is to provide the knowledge and materials to prevent these issues from the outset. By examining each failure mechanism in detail, we can build a compelling case for why a more robust material like Duplex 2205 is not just a preference but a necessity in these demanding applications.
The Insidious Nature of Pitting and Crevice Corrosion
Pitting corrosion is a localized form of corrosion that leads to the creation of small holes, or "pits," in the metal. This process is initiated when chloride ions break down the passive protective layer of standard stainless steels at specific points. Once a pit forms, the local environment inside it becomes highly acidic and concentrated with chlorides, creating an autocatalytic process that accelerates corrosion and causes the pit to deepen rapidly. This "boring" type of corrosion can perforate a vessel or pipe wall with minimal overall loss of material, making it difficult to detect with visual inspection alone before a leak occurs.
Crevice corrosion operates on a similar principle but occurs in shielded areas, such as under gaskets, washers, bolt heads, and in lap joints. In these stagnant zones, a differential aeration cell is created. The area inside the crevice becomes depleted of oxygen, making it anodic, while the area outside the crevice with free access to oxygen becomes cathodic. Chloride ions migrate into the crevice to maintain charge neutrality, leading to a highly aggressive, acidic environment that rapidly corrodes the metal. This form of attack is particularly treacherous because it happens in areas that are hidden from view and routine inspection.
A compelling example comes from a client of ours in the Middle East who constructed a large-scale seawater cooling system using 316L stainless steel. Within 18 months of operation, they reported multiple leaks. Our investigation revealed severe crevice corrosion under pipe clamps and at gasket seals, precisely where stagnant seawater and high chloride levels created a perfect storm for corrosion. The cost of repairs and the associated downtime amounted to nearly 30% of the initial installation cost. Research published in the Journal of Materials Engineering and Performance4 has shown that in warm seawater, 316L can experience pit propagation rates of up to 1 mm per year, confirming that it is simply not suitable for long-term service in such conditions.
Stress Corrosion Cracking (SCC): The Silent Killer
Stress Corrosion Cracking, or SCC, is arguably the most dangerous form of corrosion because it can lead to sudden, brittle, and catastrophic failure of a component with little to no warning. It occurs due to the combined action of three factors: a susceptible material, a specific corrosive environment (in this case, one containing chlorides), and the presence of tensile stress (which can be applied stress from service loads or residual stress from manufacturing processes like welding or bending). The failure happens at stress levels far below the material's nominal yield strength, making it unpredictable and exceptionally hazardous.
Standard austenitic stainless steels, such as Grades 304 and 316, are notoriously susceptible to chloride-induced SCC. This vulnerability is significantly amplified at temperatures above approximately 60°C (140°F). The cracks that form are typically fine and branched (transgranular or intergranular), propagating quickly through the material once initiated. Because there is often no obvious sign of corrosion on the surface, a pipe or vessel can appear perfectly sound right up until the moment it fractures, releasing its contents and potentially causing a major safety or environmental incident.
I recall a case involving a pulp and paper mill we worked with in India. They experienced a catastrophic failure of a large bleach plant vessel that was constructed from 316L stainless steel. The subsequent investigation determined the cause to be SCC, initiated by a combination of residual welding stresses and the high concentration of chlorides present in the bleaching process fluid. The incident led to weeks of lost production and a costly replacement project, underscoring the critical need for materials that are inherently resistant to SCC in these types of applications. The ASM Handbook, Volume 13A, Corrosion: Fundamentals, Testing, and Protection, provides extensive data that consistently documents the vulnerability of standard austenitic grades to SCC in a wide range of chloride-containing environments.
Quantifying the Economic Impact of Chloride-Induced Failure
The costs associated with chloride-induced corrosion extend far beyond the direct expenses of repair and replacement. While direct costs—including new materials, labor for removal and installation, and equipment needed for the job—are significant, they often pale in comparison to the indirect costs. These indirect costs encompass lost revenue from production downtime, potential penalties for failing to meet contractual obligations, the cost of environmental cleanup, potential litigation, and immeasurable damage to a company's reputation.
The NACE International "IMPACT" study provides a stark financial perspective, estimating the global annual cost of corrosion at $2.5 trillion. However, the study also offers a path forward, suggesting that implementing corrosion prevention best practices could save between 15% and 35% of this cost. This represents a potential global savings of $375 to $875 billion annually. This saving is achieved by moving from a reactive "fix-it-when-it-breaks" approach to a proactive strategy centered on life cycle costing and selecting the right materials from the start.
To illustrate this, consider a simplified life cycle cost analysis comparing 316L and Duplex 2205 for a critical piping system in a high-chloride environment. This comparison highlights why the initial purchase price is a misleading metric for making sound engineering and financial decisions.
Фактор стоимости | Standard 316L in High-Chloride Service | Duplex 2205 in High-Chloride Service |
---|---|---|
Initial Material Cost | Lower (Index: 1.0) | Higher (Index: 1.5-1.8) |
Estimated Lifespan | 5-10 лет | 25+ лет |
Maintenance/Repair Frequency | High (Annual inspections/repairs) | Low (Minimal intervention needed) |
Risk of Production Downtime | От умеренного до высокого | Очень низкий |
Total Lifecycle Cost (25 years) | High (3.0-4.0x initial cost) | Lower (1.6-2.0x initial cost) |
As the table demonstrates, while Duplex 2205 has a higher upfront cost, its significantly longer lifespan, drastically reduced maintenance needs, and near-elimination of unscheduled downtime result in a substantially lower total cost of ownership. This is the crucial calculation that procurement and engineering teams must embrace to build truly resilient and cost-effective infrastructure.
Duplex 2205 resists pitting corrosionПравда
Its dual-phase microstructure with chromium and molybdenum provides superior resistance to chloride-induced pitting compared to standard stainless steels.
316L is immune to chloride SCCЛожь
316L is highly susceptible to stress corrosion cracking in chloride environments, especially at temperatures above 60°C, as demonstrated by multiple industry failures.
Why is Duplex 2205 particularly resistant to chloride-induced corrosion?
Tired of materials that promise resistance but fail under pressure? Standard steels often fall short in the real-world conditions of chloride-rich environments. This gap between expectation and reality leads to budget overruns, operational risks, and constant maintenance headaches. You need a material whose superior performance is backed by solid science, and Duplex 2205's unique microstructure and alloy chemistry provide precisely that.
Duplex 2205's exceptional chloride resistance stems from its balanced two-phase microstructure of austenite and ferrite. This structure, combined with high levels of chromium (22%), molybdenum (3%), and nitrogen (0.14%), provides superior defense against pitting, crevice corrosion, and stress corrosion cracking.
The secret to the remarkable performance of Duplex 2205 isn't magic; it's the result of meticulous metallurgical engineering. At MFY, we often collaborate with engineering contractors specifying materials for critical infrastructure like offshore platforms5 or chemical processing plants. They approach us seeking a material that offers more than just baseline compliance; they need a built-in "safety factor" against the unpredictable and harsh conditions of the real world. I remember a project for a coastal bridge in Southeast Asia where the client was initially considering a coated carbon steel solution. We walked them through the science of Duplex 2205's microstructure, explaining how the ferrite phase provides high strength and resistance to stress corrosion cracking, while the austenite phase delivers excellent toughness and general corrosion resistance. It is this synergistic "best of both worlds" combination, further enhanced by key alloying elements, that makes it so formidable against chlorides. Understanding the science behind the material gives clients the confidence to invest in a long-term, reliable solution rather than a temporary fix. It facilitates a crucial shift from a purely cost-centric to a value-centric procurement model.
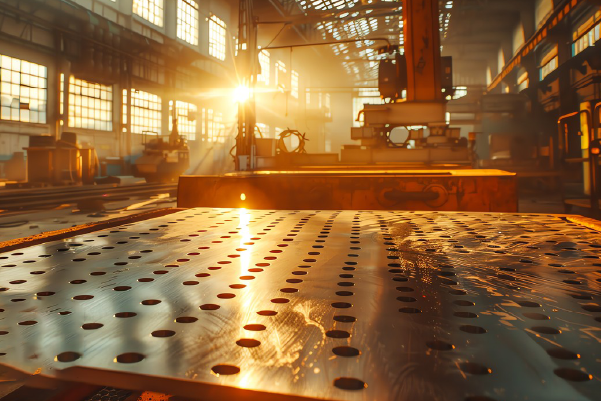
The exceptional resilience of Duplex 2205 in chloride-containing environments is not a coincidence but a direct result of its sophisticated and intentionally engineered design. Its superiority over conventional austenitic stainless steels like 316L can be attributed to three core factors: its unique dual-phase microstructure, the strategic enrichment with specific alloying elements, and its resulting inherent immunity to stress corrosion cracking in most industrial scenarios. This combination doesn't just offer incremental improvement; it provides a step-change in performance that fundamentally alters the reliability and lifecycle economics of assets operating in corrosive conditions. As a supplier, we at MFY believe that educating our clients on these metallurgical principles is key to helping them make informed decisions. When an engineer understands the "why" behind the performance, they can specify Duplex 2205 with confidence, knowing they are deploying a scientifically optimized solution.
The Power of a Dual-Phase Microstructure
The defining characteristic of Duplex 2205 is its balanced microstructure, which consists of approximately 50% austenite and 50% ferrite. This two-phase structure combines the most desirable properties of both ferritic and austenitic steels. The ferrite phase, which has a body-centered cubic (BCC) crystal structure, is responsible for the material's high mechanical strength and its outstanding resistance to stress corrosion cracking. The austenite phase, with its face-centered cubic (FCC) crystal structure, contributes excellent toughness, ductility, and good general corrosion resistance.
The synergy between these two phases is what provides such robust protection. The fine-grained, interdispersed structure creates a tortuous path for any potential crack. A crack that might initiate in one phase is quickly arrested when it encounters the boundary of the other phase, significantly impeding its ability to propagate through the material. This mechanism is the primary reason for its excellent SCC resistance. Furthermore, this dual-phase structure disrupts the formation of the large, deep pits that can plague single-phase austenitic steels, distributing the corrosive attack more evenly and slowing its progression.
A key metric used to quantify a material's resistance to pitting corrosion is the Pitting Resistance Equivalent Number (PREN), calculated using the formula: PREN = %Cr + 3.3 %Mo + 16 %N. For a typical 316L stainless steel, the PREN is around 24. For Duplex 2205 (UNS S32205)6, the PREN is approximately 35. This significantly higher value provides a quantitative measure of its superior ability to resist the initiation of pitting corrosion. A PREN value above 32 is generally considered the minimum requirement for reliable long-term performance in seawater applications, a threshold that 316L fails to meet.
The Role of Key Alloying Elements: Cr, Mo, and N
While the dual-phase structure provides the foundation, it is the specific alloying elements within Duplex 2205 that activate its high-performance characteristics. The three most critical elements are chromium, molybdenum, and nitrogen. Chromium (Cr) is the primary element responsible for the corrosion resistance of all stainless steels. It forms a very thin, tenacious, and invisible chromium-oxide passive film on the surface of the steel. This film protects the underlying metal from the environment and has the ability to self-heal if scratched. Duplex 2205 contains around 22% chromium, compared to about 18% in 316L, which results in a more robust and faster-healing passive layer.
Molybdenum (Mo) is a vital addition for resisting localized corrosion, particularly pitting and crevice corrosion in chloride-rich media. Molybdenum strengthens the passive film, making it much more resistant to breakdown by aggressive chloride ions. At a nominal 3%, Duplex 2205 contains a significantly higher concentration of molybdenum than 316L, which typically has 2-2.5%. This enhancement is a major contributor to its high PREN value and its reliability in environments like seawater or chemical process streams.
Nitrogen (N) is a powerful and synergistic alloying addition. It serves multiple functions: it acts as an austenite stabilizer to help maintain the critical 50/50 phase balance during welding, it significantly increases the material's mechanical strength, and it powerfully enhances resistance to pitting corrosion. Nitrogen works in concert with molybdenum to further fortify the passive layer, especially in acidic chloride solutions. Extensive research published in journals like Corrosion Science has demonstrated that nitrogen additions can substantially delay the onset of pitting and improve the repassivation potential of the steel.
Superiority in Stress Corrosion Cracking (SCC) Resistance
The most critical performance differentiator between Duplex 2205 and standard 300-series austenitic steels is resistance to chloride-induced Stress Corrosion Cracking (SCC). As previously discussed, grades like 304 and 316 are highly susceptible to SCC, especially at temperatures exceeding 60°C (140°F). In contrast, Duplex 2205 is considered virtually immune to chloride SCC in the vast majority of industrial applications at temperatures up to around 150°C (300°F). This provides an enormous margin of safety and reliability.
This immunity is a direct result of its duplex microstructure. The ferrite phase is inherently resistant to SCC, and the austenite/ferrite phase boundaries act as effective barriers to crack propagation. A client of ours, a major equipment integrator for the food and beverage industry, faced a critical challenge when designing a large, heated brine tank. The warm, high-chloride solution created a perfect storm for SCC, making 316L a high-risk choice. By specifying Duplex 2205 for the tank and all associated piping, they completely eliminated the risk of a sudden, catastrophic failure. This decision not only ensured the long-term reliability of the equipment but also protected the client from significant liability and ensured food safety compliance.
The combination of SCC immunity, higher pitting resistance, and greater mechanical strength makes Duplex 2205 a superior engineering choice, as summarized below.
Недвижимость | Austenitic 316L | Дуплекс 2205 | Advantage of Duplex 2205 |
---|---|---|---|
Chloride SCC Resistance (at 80°C) | Poor / Susceptible | Excellent / Highly Resistant | Prevents sudden, brittle failure, ensuring safety. |
Pitting Resistance (PREN) | ~24 | ~35 | Significantly higher margin of safety against leaks. |
Yield Strength (approx.) | 290 MPa (42 ksi) | 450 MPa (65 ksi) | Allows for thinner walls, saving weight and cost. |
The higher yield strength is a particularly important feature. It allows designers to use thinner walls for pressure vessels and piping systems while maintaining the same pressure rating. This reduction in material thickness can lead to significant weight and cost savings, which can partially or even fully offset the higher per-kilogram cost of the Duplex material, making it an even more compelling financial proposition.
Duplex 2205 has dual-phase microstructureПравда
The material contains roughly equal parts austenite and ferrite phases, which synergistically enhance corrosion resistance.
316L has better PREN than Duplex 2205Ложь
Duplex 2205's PREN (~35) significantly exceeds 316L's (~24), making it far superior for chloride environments.
How does using Duplex 2205 translate to cost savings in industrial applications?
Is your budget being eroded by the endless cycle of maintenance, repair, and replacement of corroded assets? Focusing only on the initial material cost is a common but costly mistake. The real financial drain comes from the hidden costs of downtime and unexpected failures. The solution is to adopt a Life Cycle Costing (LCC) approach, revealing the true long-term value of a superior material like Duplex 2205.
Duplex 2205 translates to significant long-term cost savings by dramatically extending asset life, minimizing maintenance requirements, and preventing costly production shutdowns. This results in a much lower Total Cost of Ownership (TCO) compared to conventional steels, despite a higher initial purchase price.
I often speak with procurement managers who are, quite understandably, focused on the upfront capital expenditure of a project. The higher price tag of Duplex 2205 compared to 316L can cause initial hesitation. I remember one client, an engineering contractor for a water utility, who was reluctant to specify Duplex 2205 for a coastal water intake pipeline due to budget constraints. We sat down and developed a comprehensive 30-year Total Cost of Ownership model. The model factored in not just the initial cost, but also the projected cost of replacing the 316L pipe twice during that period, plus the frequent maintenance and high risk of service interruptions. The data was clear: the Duplex 2205 option, while more expensive initially, was projected to save them over 40% in total costs over the asset's life. Seeing the numbers transformed their perspective from "How can we afford this?" to "How can we afford not to use this?" It’s a powerful illustration of how strategic material selection is a direct investment in long-term financial health.
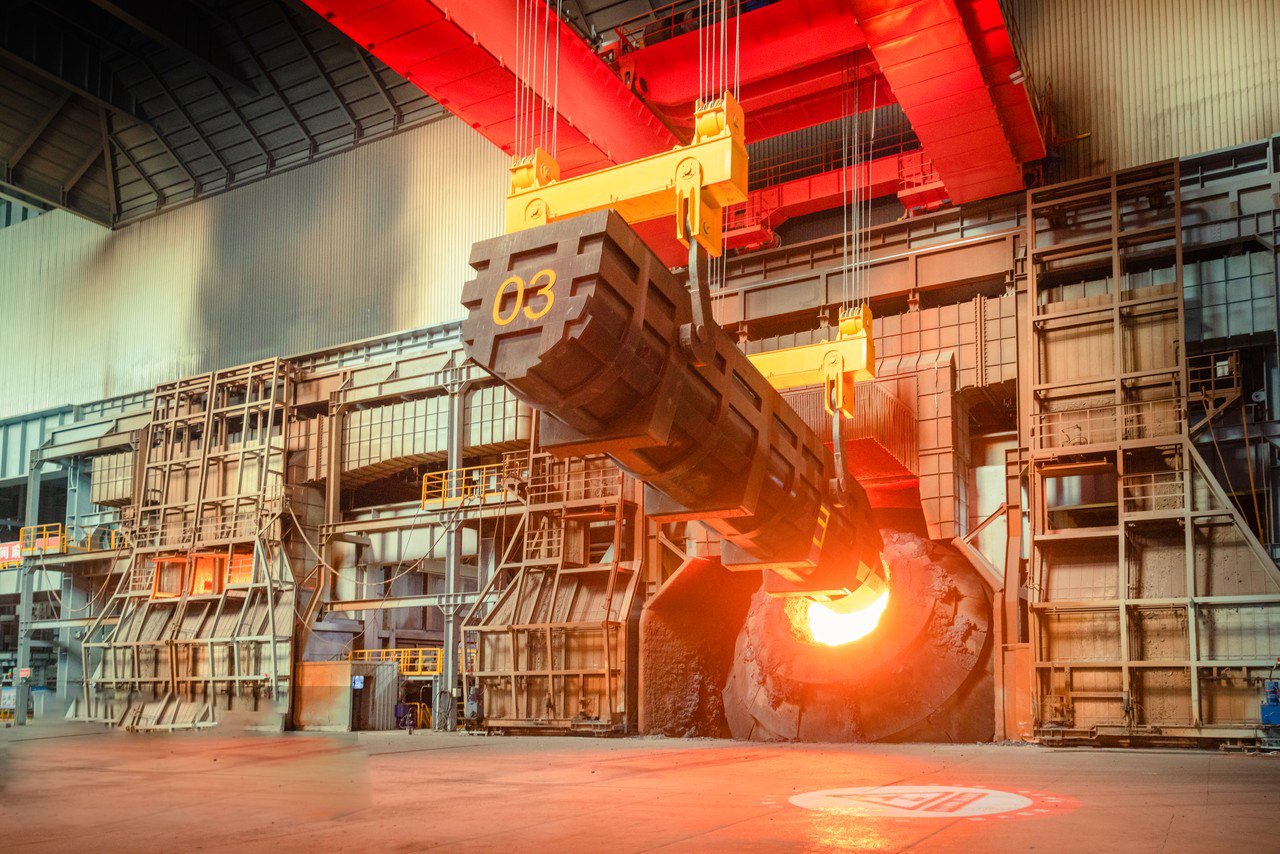
The financial argument for using Duplex 2205 in chloride-rich environments is one of the most compelling aspects of its value proposition. While its performance characteristics7 are technically superior, it is the tangible, quantifiable impact on the bottom line that drives its adoption in savvy, forward-thinking organizations. The cost savings are not theoretical; they are realized through a combination of dramatically extended asset lifespan, significantly reduced operational and maintenance burdens, and the opportunity for more efficient engineering design. Moving beyond a myopic focus on the initial purchase price to a holistic view of an asset's entire economic life is the key to unlocking these savings. At MFY, our role often extends beyond simply supplying steel; we act as partners, helping our clients analyze these long-term financial benefits to make the most strategic and profitable decisions for their projects.
Beyond the Initial Purchase Price: A Life Cycle Costing (LCC) Perspective
Life Cycle Costing (LCC) is a critical management accounting tool that evaluates the total cost of an asset over its entire life. This includes not only the initial capital investment (material purchase and installation) but also all subsequent costs, such as energy consumption, operational expenses, routine maintenance, scheduled and unscheduled repairs, and eventual decommissioning or disposal. When comparing materials like 316L and Duplex 2205 using an LCC framework, the results are often striking.
Consider a heat exchanger in a coastal chemical processing plant, operating with seawater as the cooling medium. A unit fabricated from 316L might have a lower initial cost, but its susceptibility to pitting and crevice corrosion in this service means it will likely require major repairs or a full replacement within 7 to 10 years. Furthermore, it would necessitate annual shutdowns for inspection to monitor corrosion progression. In contrast, a heat exchanger made from Duplex 2205, while carrying a higher upfront price, can be reasonably expected to last for the entire 25- to 30-year design life of the plant with only minimal maintenance.
When you factor in the cost of one or two full replacements of the 316L unit—including new material, fabrication, and the massive cost of lost production during the extended downtime—the financial scales tip overwhelmingly in favor of Duplex 2205. The initial premium paid for the superior material is effectively an insurance policy against much larger future expenditures.
Reduced Maintenance and Inspection Demands
The exceptional corrosion resistance of Duplex 2205 directly translates into lower operational expenditures (OPEX). Assets built with conventional materials in aggressive environments require a rigorous and costly regimen of inspection and maintenance to ensure their integrity. This can include frequent visual inspections, non-destructive testing (NDT) like ultrasonic thickness measurements or dye penetrant testing, and preventative repairs. Each of these activities carries costs for labor, equipment, and, most significantly, production downtime.
A distributor we work with who supplies components to the marine industry shared a powerful anecdote. Their customers who build propeller shafts and rudder stocks from Duplex 2205 report drastically lower maintenance burdens compared to those who stick with traditional marine-grade stainless steels like 316L or Aquamet. The Duplex 2205 components resist crevice corrosion at the bearing points and pitting from seawater exposure, requiring little more than routine cleaning. In contrast, the 316L shafts often need to be pulled for inspection and polishing to remove corrosion sites, a labor-intensive and costly exercise.
The value of this reliability cannot be overstated. For an industrial plant, a single scheduled shutdown for inspection can cost tens or even hundreds of thousands of dollars per day in lost production revenue. By designing with Duplex 2205, engineers can confidently extend inspection intervals, and in some cases, eliminate the need for certain types of inspection altogether. Avoiding just one major maintenance shutdown over the life of an asset can more than pay for the initial material cost difference.
The Value of Weight Reduction and Design Optimization
A frequently overlooked but significant cost-saving advantage of Duplex 2205 is its superior mechanical strength. Its specified minimum yield strength is approximately 450 MPa (65 ksi), which is nearly double that of austenitic grades like 316L (approx. 290 MPa / 42 ksi). This higher strength allows engineers to perform "value engineering" by designing components with reduced wall thickness while still meeting the required pressure ratings and structural loads as per design codes like ASME B31.3 or the ASME Boiler and Pressure Vessel Code.
This ability to use less material has a cascading effect on cost reduction. Firstly, it directly reduces the total tonnage of steel required for a project, which lowers the material purchase cost. Secondly, the lighter components are cheaper to transport to the project site. Thirdly, the reduced weight translates to lower fabrication and welding costs (less weld metal required) and easier handling and installation. Finally, the overall lighter weight of the system can lead to savings in the cost of structural supports, foundations, and ancillary equipment. While the fabrication of duplex steels requires more careful control than austenitic steels, these costs are often more than offset by the material savings.
Характеристика | Austenitic 316L | Дуплекс 2205 | Impact on Cost |
---|---|---|---|
Предел текучести | ~290 МПа (42 кси) | ~450 MPa (65 ksi) | Allows for ~30-40% wall thickness reduction in pressure applications. |
Weight per Unit | Higher (for same pressure rating) | Нижний | Reduces material purchase, shipping, and handling costs. |
Fabrication Cost | Стандартные процедуры | Requires more control (can be slightly higher) | Higher labor cost often offset by reduced material and weld volume. |
Total Installed Cost | Базовый уровень | Often comparable or slightly higher | The difference is quickly recouped through operational savings. |
Life Cycle Cost | Высокий | Significantly Lower | The ultimate measure of economic value. |
This multi-faceted approach to cost savings—combining extreme longevity, minimal maintenance, and design optimization—is what makes Duplex 2205 a truly intelligent financial choice for any application involving chlorides. At MFY, we often assist our clients' engineering teams with these comparative calculations to demonstrate the tangible, long-term financial benefits.
Duplex 2205 reduces total cost of ownershipПравда
Despite higher initial cost, Duplex 2205's extended lifespan and lower maintenance needs result in significant long-term savings.
316L requires less frequent inspectionsЛожь
316L actually requires more frequent inspections due to its higher susceptibility to corrosion compared to Duplex 2205.
What solutions does Duplex 2205 offer for environments with high chloride levels?
Are you searching for a reliable, long-term material solution for the most extreme chloride environments? In sectors like desalination and offshore oil & gas, material failure is not an option. The operational and safety stakes are simply too high for compromise. Дуплекс 22058 is not just an alternative; it is the proven, specified material of choice, offering a robust and lasting solution where others fail.
Duplex 2205 provides robust solutions for high-chloride environments like desalination plants, offshore platforms, and chemical processing by offering superior resistance to pitting, crevice corrosion, and SCC, ensuring long-term operational integrity and safety where standard materials would predictably fail.
Over the years, MFY has supplied Duplex 2205 pipes, plates, and coils for an incredibly diverse range of demanding projects, from desalination plants in the Middle East to chemical facilities in India and infrastructure projects across Southeast Asia. Its versatility is one of its greatest strengths. I recall a project for an offshore gas platform in Russia, where the client needed a material that could not only withstand the highly corrosive seawater cooling systems but also maintain its toughness in the frigid arctic temperatures. Standard austenitic steels become brittle in such cold, while Duplex 2205 maintains good ductility and impact strength. It was the only material that could reliably solve both challenges simultaneously, showcasing its broad problem-solving capabilities. It's this ability to perform under a confluence of extreme conditions that makes it an indispensable tool for modern engineering.
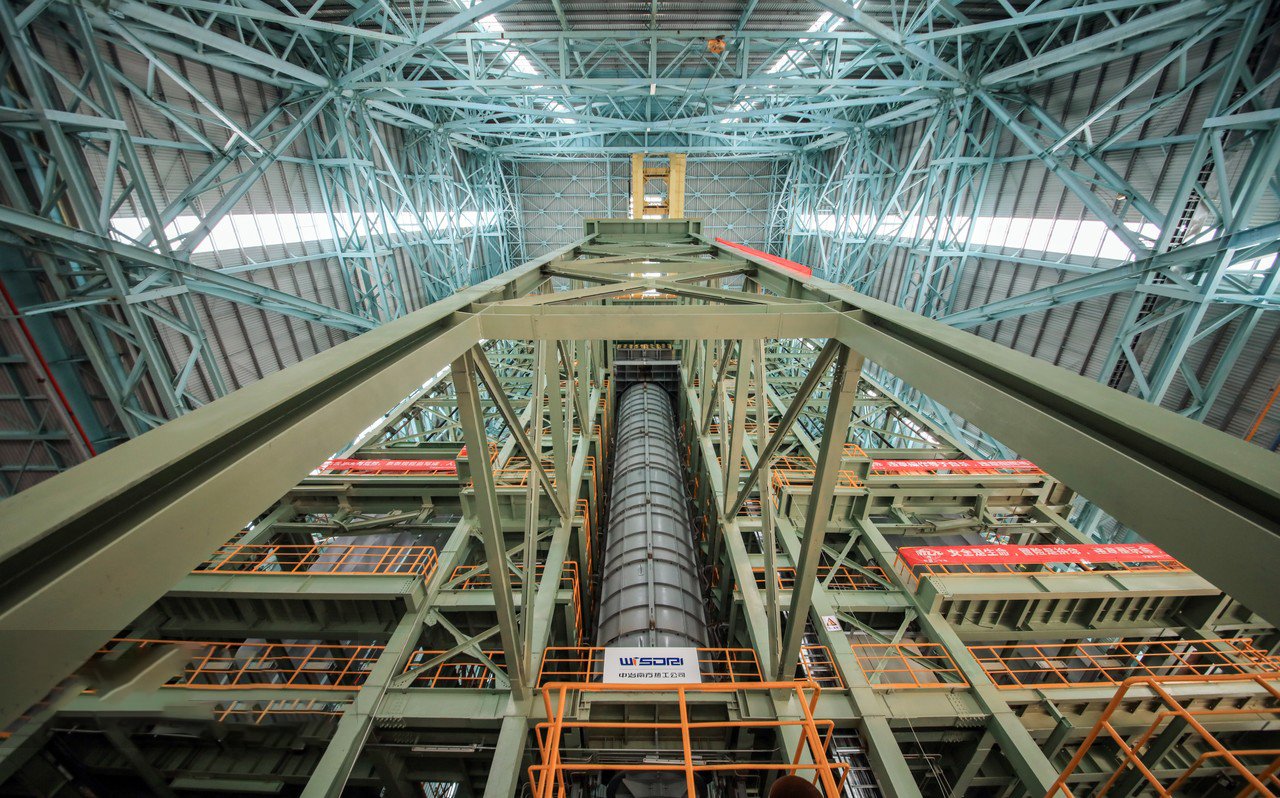
Duplex 2205 stainless steel is more than just a corrosion-resistant alloy; it is a versatile engineering solution that has become the benchmark material for some of the world's most challenging industrial environments. Its unique combination of high strength, excellent corrosion resistance, and good fabricability allows it to solve complex problems where single-phase materials fall short. From the hyper-saline brines of modern desalination plants to the punishing conditions of offshore platforms and the aggressive chemical streams in processing industries, Duplex 2205 provides a level of reliability that underpins the safety and economic viability of these critical operations. As we explore these specific applications, it becomes clear that Duplex 2205 is not a niche product but a cornerstone of modern industrial infrastructure.
Desalination Plants: The Ultimate Chloride Challenge
Modern desalination plants, particularly those using Reverse Osmosis (RO) technology, represent one of the most aggressive chloride environments imaginable. These facilities process seawater or brackish water at very high pressures, resulting in a concentrated brine stream that is extremely corrosive. Standard stainless steels like 316L simply cannot survive in this service; they are highly susceptible to rapid pitting and crevice corrosion, leading to frequent leaks and costly shutdowns.
Дуплекс 22059 has become the industry-standard material for many critical components in desalination plants. It is extensively used for high-pressure piping that carries the seawater and brine, as well as for pressure vessels, pump casings, and valve bodies. Its high PREN value (~35) gives it the necessary resistance to pitting and crevice corrosion, while its immunity to SCC provides the safety assurance needed in these high-pressure systems.
MFY has proudly contributed to this sector by supplying high-quality Duplex 2205 pipes and sheets to major desalination projects in the Middle East and India. In one such project, the engineering firm specified Duplex 2205 for the entire high-pressure RO train after a previous facility built with 316L experienced major corrosion failures within three years of commissioning. By choosing Duplex 2205 from the outset, they designed for a 25-year service life, ensuring a reliable and sustainable supply of fresh water. Data from the International Desalination Association (IDA) consistently highlights proper material selection as one of the most critical factors for the long-term success and economic feasibility of desalination projects.
Offshore Oil & Gas Platforms
The offshore oil and gas industry operates in a relentlessly corrosive environment. Platforms are constantly exposed to saline atmospheric conditions, sea spray (the "splash zone"), and direct immersion in seawater for cooling systems. Furthermore, the process fluids themselves often contain produced water with high levels of chlorides. On top of this, structural weight is a critical design constraint, as every extra kilogram of topside weight adds significant cost to the supporting structure (the "jacket") and foundations.
Duplex 2205 is an ideal solution for these multifaceted challenges. Its excellent resistance to seawater corrosion makes it perfect for seawater lift pumps, firewater systems, and cooling water piping. Its high strength-to-weight ratio is a major advantage, allowing for the design of lighter piping systems and pressure vessels, which directly translates to topside weight savings. A lighter platform is a cheaper platform to build, transport, and install.
For example, a major engineering, procurement, and construction (EPC) contractor we work with for projects in Southeast Asia now specifies Duplex 2205 as their default material for all seawater-handling systems on offshore platforms. They found that while 316L systems had a typical lifespan of only 5-7 years before requiring major overhauls, the Duplex 2205 systems are designed for the full 25-year life of the platform, dramatically reducing life cycle cost and improving operational safety and reliability. In some cases, Duplex 2205 also offers adequate resistance to the mild sour service (H2S) conditions found in some process streams, further expanding its utility.
Chemical Processing and Pulp & Paper Industries
The chemical process industries (CPI) handle a vast array of aggressive substances, many of which contain chlorides. Duplex 2205 offers a robust solution for tanks, reactors, heat exchangers, and piping that handle chloride-containing process streams, especially at elevated temperatures where 316L would be at high risk of SCC. It provides reliable service in the production of organic and inorganic chlorides and in processes involving acidic chloride solutions.
The pulp and paper industry is another key user. Bleach plants, which use chlorine dioxide and other chloride-containing chemicals to whiten pulp, are notoriously corrosive environments. The combination of hot, wet conditions and high chloride levels makes this a classic application for SCC failure in austenitic stainless steels. Duplex 2205 has been used with great success for bleach plant washers, drums, and piping, offering a significantly longer service life and preventing the costly, unscheduled shutdowns that plague mills using inferior materials.
The table below summarizes the suitability of Duplex 2205 in these key applications compared to 316L.
Приложение | 316L Stainless Steel | Дуплекс 2205 | Reason for Duplex 2205 Choice |
---|---|---|---|
RO Desalination High-Pressure Piping | Unsuitable (rapid pitting/crevice corrosion) | Превосходно | High PREN value and SCC resistance ensure long-term integrity. |
Offshore Platform Seawater Systems | Limited Lifespan (5-7 years) | Standard Choice (25+ years) | High strength (weight savings) and superior corrosion resistance. |
Pulp Bleach Plant Washer | Highly Susceptible to SCC | Highly Resistant | Immunity to SCC in hot chloride environments prevents sudden failure. |
Food Processing Brine Tank (>60°C) | High Risk of SCC | Превосходно | Ensures product safety and operational reliability by preventing SCC. |
This demonstrates that Duplex 2205 is not just a material, but a versatile and powerful problem-solver, providing reliable, long-term solutions across a wide spectrum of critical and demanding industries.
Duplex 2205 resists pitting in chloride environmentsПравда
With a PREN value of ~35, Duplex 2205 offers superior resistance to pitting corrosion in high-chloride environments like seawater.
316L is better than Duplex 2205 for desalinationЛожь
316L fails rapidly in desalination plants due to pitting, while Duplex 2205 is the industry standard for long-term performance.
What best practices ensure the optimal use of Duplex 2205 in chloride environments?
You’ve made the smart choice and specified Duplex 2205 stainless steel10. But even the best material can be compromised by poor handling. Improper fabrication, welding, or design can introduce weaknesses that negate your investment and lead to premature failure. Following established best practices is not optional; it is essential to unlock the full performance and longevity of this high-performance alloy.
To ensure the optimal performance of Duplex 2205, best practices include using proper welding procedures to maintain the balanced phase ratio, correct heat treatment, designing to minimize crevices, and partnering with a reputable supplier who guarantees material quality and full traceability.
The importance of execution cannot be overstated. I once consulted on a project where a chemical storage tank fabricated from Duplex 2205 began showing signs of corrosion near the welds just months after being commissioned. The material itself was perfectly on-spec. The investigation revealed that the fabrication shop, inexperienced with duplex steels, had used incorrect welding parameters and failed to perform proper post-weld cleaning. This created a compromised microstructure in the heat-affected zone, which became the weak point. It was a costly lesson for the client: the success of a project depends just as much on the "how" as it does on the "what." This is why at MFY, we see our role as not just supplying material, but also sharing the critical knowledge needed to use it correctly.
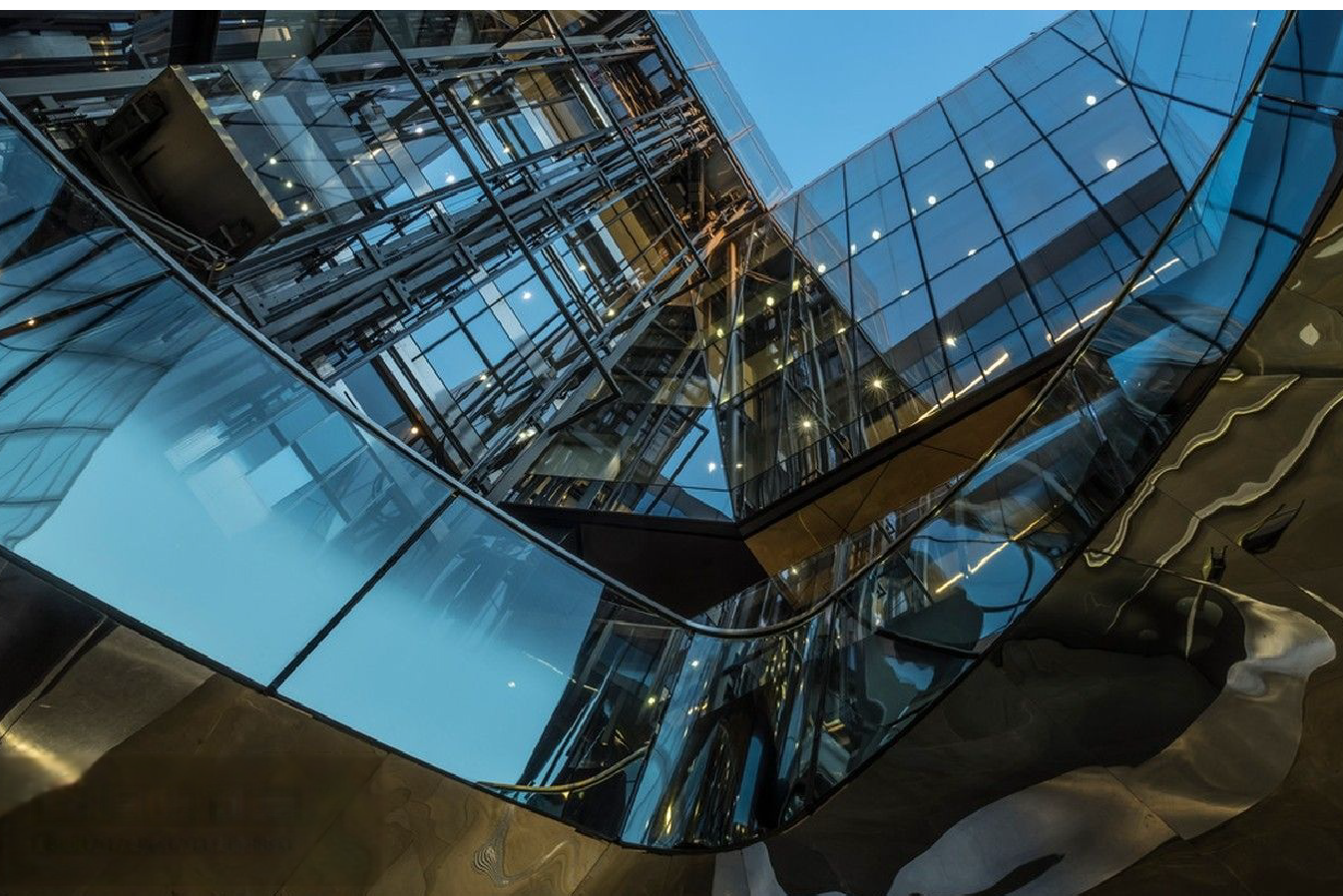
Maximizing the exceptional benefits of Duplex 2205 stainless steel requires more than just selecting it from a catalog. It demands a holistic approach that encompasses precise fabrication techniques, thoughtful design considerations, and, most importantly, rigorous quality assurance in material sourcing. The unique metallurgical properties that give Duplex 2205 its strength and corrosion resistance also mean that it requires a higher degree of control during manufacturing and welding compared to conventional austenitic steels. Overlooking these critical best practices is a false economy that can lead to the very failures the material was chosen to prevent. Partnering with an experienced supplier and knowledgeable fabricators is the final, crucial step in translating the potential of Duplex 2205 into guaranteed real-world performance and reliability.
Precision in Welding and Fabrication
The primary challenge in welding Duplex 2205 is maintaining the balanced 50/50 austenite-ferrite microstructure in the weld metal and the heat-affected zone (HAZ). The thermal cycle of welding can easily disrupt this balance. For example, excessively high heat input or very slow cooling rates can lead to the formation of excessive ferrite and the precipitation of detrimental intermetallic phases, such as the sigma phase11. The sigma phase is very hard and brittle, and it severely reduces both the corrosion resistance and toughness of the steel.
To prevent these issues, fabricators must adhere to strict best practices. This includes using a filler metal with a slightly higher nickel content (e.g., 2209) to promote the reformation of austenite upon cooling. Heat input must be carefully controlled within the range recommended by the material manufacturer, typically between 0.5 and 2.5 kJ/mm. The interpass temperature—the temperature of the workpiece between weld passes—must also be limited, usually to below 150°C (300°F), to prevent the buildup of heat. Proper shielding gas (typically an argon-based mixture with small amounts of CO2 or N2) is essential to protect the molten weld pool from atmospheric contamination. Finally, post-weld cleaning is not optional; it is a critical step. All heat tint (oxide scale) must be removed mechanically or chemically (through pickling with a hydrofluoric/nitric acid paste or gel), followed by passivation to restore the chromium-oxide protective layer.
At MFY, we understand these complexities and always provide our clients with detailed welding guidelines that align with international standards like ASME Section IX or AWS D1.6. We strongly recommend that all fabrication be performed by certified welders who have documented experience with duplex stainless steels.
Design Considerations and Surface Finish
Good engineering design can significantly enhance the corrosion performance of any material, and Duplex 2205 is no exception. The primary goal is to minimize opportunities for chlorides to concentrate and initiate localized corrosion. This means designing systems to be free-draining, avoiding stagnant areas where water and contaminants can collect. Most importantly, designers should strive to eliminate or minimize crevices wherever possible. This can be achieved by using welded joints instead of bolted flanges where practical, and by specifying full-penetration butt welds instead of lap joints. When gaskets are necessary, they should be of a non-absorbent material and designed to minimize the crevice area.
The surface finish of the final component also plays a crucial role. A smooth, clean surface is inherently more resistant to corrosion initiation than a rough or contaminated one. Any surface damage from handling, grinding, or machining can create sites for pitting to begin. Therefore, specifications should call for all surfaces, especially those in contact with the corrosive medium, to be smooth and free from contamination. After any fabrication work, a final pickling and passivation treatment is the best way to ensure the entire surface has a clean, fully formed passive layer, ready for service.
I worked with a construction contractor on a water treatment plant who consulted our technical team during the design phase. By working together, we helped them optimize their piping layout to eliminate dozens of unnecessary flanges and several "dead legs" in the system. This proactive design modification, made at no extra cost, significantly reduced the long-term risk of crevice corrosion and simplified future maintenance.
The Critical Role of Material Sourcing and Quality Assurance
All the best practices in design and fabrication are meaningless if the starting material is not what it claims to be. The global market is unfortunately plagued by counterfeit and off-spec materials. The only way to guarantee you are getting the full performance benefits of Duplex 2205 is to ensure the material you purchase is fully compliant with the relevant international standards, such as UNS S32205 (or its lean duplex S31803 equivalent) and ASTM/EN specifications.
This is why partnering with a reputable and trustworthy supplier is arguably the most critical step in the entire process. A quality supplier will provide a comprehensive quality assurance package for every piece of material they sell. This starts with a Mill Test Certificate (MTC) to EN 10204 3.1 or 3.2, which is a formal document from the original steel mill that certifies the material's exact chemical composition (showing the critical Cr, Mo, and N levels) and its mechanical properties (yield strength, tensile strength, elongation) Benefits of Mill Test Certificate12.
Furthermore, a reliable supplier must demonstrate full traceability, meaning they can track a specific plate, pipe, or coil all the way back to the original heat or batch from the mill. This ensures accountability and confirms the material's pedigree. At MFY, this is our standard practice. We maintain rigorous internal quality control, conduct our own verification tests when necessary, and provide our clients with a complete documentation package that gives them absolute confidence in the material they are receiving.
Supplier Quality Checklist | Почему это важно | How MFY Addresses It |
---|---|---|
Certified MTC (EN 10204 3.1) | Provides certified proof of the material's chemical and mechanical properties. | A complete, certified MTC is provided with every single shipment, without exception. |
Full Traceability | Allows tracking of the material's entire history, ensuring quality control at every stage. | Our rigorous internal system links every product to its original mill heat number. |
Adherence to International Standards | Guarantees the material meets globally recognized specifications for performance. | Our production and testing protocols strictly follow standards like ASTM A240, A790, etc. |
Supplier Reputation and Audits | Verifies that the supplier has robust quality systems and a proven track record of reliability. | We have a long history of serving global clients and welcome customer audits of our facilities. |
Ultimately, your material is only as good as your supplier. Choosing a partner like MFY is the final and most important best practice to ensure your investment in Duplex 2205 delivers the long-term, trouble-free performance your project demands.
Welding affects microstructureПравда
The thermal cycle of welding can disrupt the balanced 50/50 austenite-ferrite microstructure in Duplex 2205, potentially forming detrimental phases like sigma phase.
Post-weld cleaning is optionalЛожь
Post-weld cleaning is critical for Duplex 2205 to remove heat tint and restore the protective chromium-oxide layer through pickling and passivation.
Заключение
Duplex 2205 is more than just a material; it's a strategic investment in reliability. Its superior chloride resistance, high strength, and significantly lower lifecycle cost make it the definitive choice for demanding applications, safeguarding your operations and delivering unparalleled long-term value where other materials inevitably fail.
-
Learn why Duplex 2205 is ideal for resisting chloride-induced corrosion and cost-effective over time. ↩
-
Discover why Duplex 2205 is often preferred over 300-series in harsh environments. ↩
-
Understand the additional costs associated with using standard steels in corrosive environments. ↩
-
Study evidence showing 316L's limitations in seawater conditions for long-term use. ↩
-
Understand the suitability and benefits of Duplex 2205 in harsh marine conditions. ↩
-
Learn how PREN quantifies pitting resistance compared to other steel grades. ↩
-
Discover the technical benefits of using Duplex 2205 in harsh environments ↩
-
Discover how Duplex 2205 outperforms other steels in saline conditions ↩
-
Understand its corrosion resistance and weight-saving advantages for platforms ↩
-
Discover why Duplex 2205 offers superior corrosion resistance in challenging conditions ↩
-
Learn how the sigma phase affects corrosion resistance and toughness of duplex stainless steel ↩
-
Ensure material meets standards with certified chemical composition and properties ↩
У вас есть вопросы или нужна дополнительная информация?
Свяжитесь с нами, чтобы получить индивидуальную помощь и квалифицированный совет.