Нержавеющие трубы 304 и 316: Руководство по коррозии и стоимости
Facing the critical choice between 304 and 316 stainless steel pipes1? The price difference is tempting, but you're worried that opting for the cheaper Grade 304 could lead to catastrophic corrosion failure and costly downtime. Making the wrong call is a high-stakes gamble.
The primary difference between 304 and 316 stainless pipe is that Grade 316 contains molybdenum, an alloying element that significantly enhances its corrosion resistance, particularly against chlorides and acidic solutions. Grade 304 is a general-purpose, lower-cost option suitable for less corrosive environments.
As the Global Business Director at MFY, I’ve guided hundreds of clients through this exact decision. It's often the single most important material specification they'll make, impacting everything from budget adherence to the long-term operational integrity of their facility. This guide cuts through the technical jargon to give you the practical framework you need.
I want to move beyond simple data sheets and share the real-world financial and operational implications of this choice. We will dissect the role of alloying elements in both corrosion resistance and cost, explore industry-specific applications, and provide a clear methodology for making a decision that ensures both fiscal responsibility and the physical longevity of your piping systems.
What are the key differences in corrosion resistance between 304 and 316 stainless steel pipes?
Afraid that a hidden environmental factor will cause your pipes to fail prematurely? You know corrosion is the enemy, but the technical differences between 304 and 316 feel abstract, making it hard to justify the higher cost of 316 until it's too late and a leak occurs.
The key difference in corrosion resistance lies in Grade 316's addition of molybdenum (2-3%). This element provides superior protection against pitting and crevice corrosion, especially in environments containing chlorides (like seawater, de-icing salts) and various industrial acids.
This isn't just a theoretical difference; it has massive real-world consequences. I recall working with a client, let's call them "AquaTech Engineering," a promising firm in Southeast Asia designing a small-scale water purification system. They initially specified 304 stainless pipe for the entire system to keep their bid competitive. However, their raw water source was brackish, with fluctuating salinity levels. I felt compelled to intervene, explaining that while 304 is robust, the chloride ions in the brackish water would inevitably attack the passive layer of the steel, leading to pitting corrosion. Pitting is insidious; it can perforate the pipe wall with very little visible surface corrosion, leading to unexpected system failures. We analyzed the water chemistry and calculated the Pitting Resistance Equivalent Number (PREN) needed. The data was unequivocal: 316 was not just a recommendation, it was a requirement for reliable operation. This shifted their thinking from winning the bid to delivering a durable, low-risk system for their end-user.
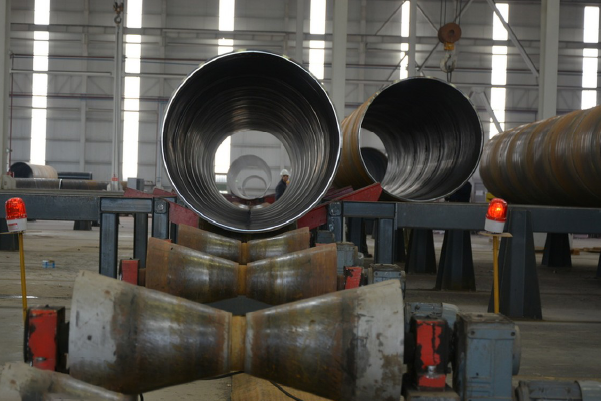
The choice between these two grades is a foundational engineering decision rooted in the science of metallurgy and corrosion. It’s a proactive risk assessment. While both 304 and 316 are "stainless," they behave very differently when challenged. Understanding the specific types of corrosion they are susceptible to is crucial for anyone specifying piping for critical applications. The presence of molybdenum in 316 steel fundamentally changes its molecular defense mechanism against the most common and aggressive forms of localized corrosion. To make an informed choice, we must delve deeper into how this single element fortifies the steel, exploring the mechanisms of general corrosion, the specifics of pitting and crevice corrosion, and the risk of stress corrosion cracking. This knowledge transforms the choice from a guess into a calculated, defensible decision.
General Corrosion vs. Localized Corrosion
First, it's important to understand the concept of the "passive layer." Both 304 and 316 stainless steels owe their "stainless" properties to a microscopic, invisible, and chemically inert layer of chromium oxide that forms on the surface when exposed to oxygen. This passive layer is incredibly thin but very robust, and it instantly reforms when scratched. General corrosion, or uniform corrosion, occurs when this passive layer is broken down evenly across the entire surface, typically by strong acids or bases that are aggressive enough to dissolve the chromium oxide shield. In many common environments, both 304 and 316 exhibit excellent resistance to general corrosion. For example, in applications involving potable water or most food products, the passive layer on both grades remains stable, and the rate of general corrosion is negligible.
The real battleground, however, is localized corrosion. Unlike general corrosion, which is predictable and slow, localized corrosion is treacherous because it attacks the steel at specific points, often hidden from view, and can cause failure much more rapidly. This is where the differences between 304 and 316 become starkly apparent. The two most common and dangerous forms of localized corrosion for stainless steel pipes are pitting corrosion and crevice corrosion. These are typically initiated by chloride ions, which are abundant in marine environments, de-icing salts, and many industrial process fluids.
These chloride ions are small and aggressive, and they have the ability to penetrate the passive layer at weak points, such as microscopic inclusions or surface imperfections. Once through, they create a tiny, localized acidic environment that prevents the passive layer from reforming. This creates a self-sustaining corrosion cell—a pit—that can rapidly burrow through the pipe wall. Grade 304 is particularly vulnerable to this form of attack. Grade 316's secret weapon, molybdenum, significantly enhances the stability and strength of the passive layer, making it far more difficult for chlorides to initiate a breach. This is the single most important distinction in their corrosion performance.
The Power of Molybdenum and PREN
To quantify this enhanced resistance, engineers use the Pitting Resistance Equivalent Number, or PREN. This is a calculated value based on the alloy's chemical composition, providing a relative measure of its resistance to pitting corrosion. The formula is generally calculated as: $PREN = \%Cr + 3.3 \times \%Mo + 16 \times \%N$. While there are variations of this formula, they all highlight the powerful influence of Molybdenum (Mo), which is weighted 3.3 times more heavily than Chromium (Cr). Nitrogen (N) also contributes, but molybdenum is the key differentiator between 304 and 316.
Let's look at the numbers. A typical Grade 304 stainless steel, with no deliberate addition of molybdenum, will have a PREN value in the range of 18-20. In contrast, a standard Grade 316, with its 2-3% molybdenum content, will have a PREN value of 23-28. This is not a small difference; it represents a significant leap in performance. As a general rule of thumb in engineering, a PREN value below 32 is not considered suitable for direct contact with seawater. While 316 doesn't meet that threshold for full immersion, its PREN value demonstrates why it is vastly superior to 304 in any chloride-containing environment. For the AquaTech Engineering project, the brackish water had a chloride concentration that put it squarely in the zone where Grade 304 would fail, while 316 provided a necessary margin of safety.
Crevice corrosion is a related form of localized corrosion that occurs in tight, shielded areas, such as under gaskets, washers, or in unsealed threaded connections. In these crevices, the stagnant fluid can become depleted of oxygen, preventing the passive layer from reforming. Chloride ions concentrate in the crevice, creating a highly aggressive local environment that rapidly corrodes the metal. Here again, the molybdenum in Grade 316 plays a crucial role. It enhances the steel's ability to "repassivate" even in low-oxygen, high-chloride conditions, providing a level of protection that Grade 304 simply cannot offer in such geometries.
Susceptibility to Stress Corrosion Cracking (SCC)
Another important failure mode to consider is Stress Corrosion Cracking (SCC). SCC is a particularly dangerous form of corrosion because it can lead to sudden, brittle failure of a pipe that may appear perfectly fine on the outside. It occurs under a specific combination of three conditions: a susceptible material, a corrosive environment, and tensile stress (the stress of being pulled or stretched). Standard austenitic stainless steels like the 300 series are most susceptible to chloride-induced SCC, particularly at elevated temperatures (typically above 60°C or 140°F).
In this context, there is not a dramatic difference in the inherent resistance of 304 and 316 to SCC. Both grades are considered susceptible under the right conditions. The addition of molybdenum in 316 offers only a slight improvement in SCC resistance. For the AquaTech project, while their water wasn't heated, this was a key point of discussion for future-proofing. If they were to add a heated cleaning cycle to their system, the risk of SCC would increase significantly for either grade.
When SCC is a primary concern—for example, in hot water systems containing chlorides—engineers must look beyond standard 304 and 316. Alternative materials, such as ferritic stainless steels (like Grade 444) or duplex stainless steels (like 2205), offer vastly superior resistance to chloride SCC. These materials have a different crystalline structure that is inherently less prone to this type of failure. However, they come with their own distinct cost and fabrication considerations. For most ambient temperature applications, the primary decision remains focused on 316's superior defense against pitting and crevice corrosion.
Тип коррозии | Grade 304 Performance | Grade 316 Performance | Key Influencing Factor |
---|---|---|---|
Общая коррозия | Excellent in most atmospheric and mild chemical environments. | Excellent; slightly better than 304 in more acidic environments. | Содержание хрома |
Точечная коррозия | Susceptible in environments with >100 ppm chlorides. | Resistant in environments with up to ~1000 ppm chlorides. | Molybdenum content |
Щелевая коррозия | Highly susceptible in chloride-containing crevices. | Significantly more resistant than 304 due to better repassivation. | Molybdenum content |
Коррозионное растрескивание под напряжением (SCC) | Susceptible at temperatures >60°C in chloride environments. | Susceptible (only slightly better than 304) at temperatures >60°C. | Tensile Stress + Chlorides + Heat |
316 содержит молибденПравда
Grade 316 stainless steel contains 2-3% molybdenum, which significantly enhances its corrosion resistance compared to 304.
304 resists all chloridesЛожь
Grade 304 is susceptible to pitting corrosion in environments with chloride concentrations above 100 ppm, unlike 316 which can handle ~1000 ppm.
How does the alloy composition impact the cost of 304 and 316 stainless steel pipes?
You know 316 pipe is the safer bet for corrosion, but your project budget is tight. The significant price premium for 316 makes you question if it's truly necessary, forcing you to weigh a tangible upfront cost against a potential, uncertain future failure.
The higher cost of 316 stainless steel pipe is directly due to its alloy composition, specifically the addition of molybdenum and a typically higher nickel content. These elements are expensive commodities, and their market prices add a significant surcharge to the material's cost.
I spend a great deal of my time at MFY explaining cost structures to procurement managers. The price of stainless steel isn't arbitrary; it's tied directly to the global commodities market. I often use an analogy: buying Grade 304 is like buying a standard car model. Buying Grade 316 is like adding the premium "all-weather performance package." That package includes expensive components (molybdenum and more nickel), and the final price reflects that. For AquaTech Engineering, their initial budget was based on the lower cost of 304. When we re-quoted with 316, the 20-25% price increase was a shock. My task was to break down that cost, showing them that the premium wasn't profit margin, but the tangible cost of the molybdenum and extra nickel required to protect their investment from their specific environmental threat.
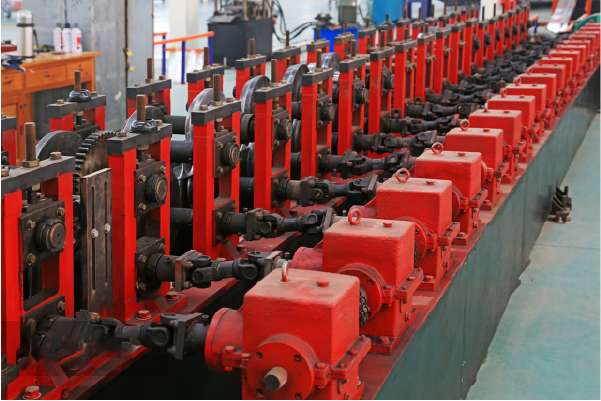
Understanding this cost difference is not just for budget approval; it’s about making a sound financial investment. The price tag on a length of pipe is a direct reflection of the valuable metals mixed into the steel. The global prices for elements like nickel and molybdenum are volatile, fluctuating based on mining output, geopolitical events, and industrial demand. This is why the price gap between 304 and 316 is not fixed; it changes over time. To truly grasp the financial implications, one must look beyond the final invoice and understand the components of the cost. We will explore the role of alloy surcharges, specifically how nickel and molybdenum drive the price, and then reframe the conversation from upfront cost to the far more important metric of Total Cost of Ownership (TCO).
Base Cost vs. The Alloy Surcharge
The price of any stainless steel product is typically broken into two main components: the base cost and the alloy surcharge. The base cost covers the iron, chromium, the energy used in melting, and the costs of manufacturing, labor, and logistics. This portion of the cost is relatively stable and is similar for both 304 and 316 pipe produced in the same facility. It represents the fundamental cost of turning raw materials into a finished pipe product.
The variable and most significant part of the cost, especially for higher grades, is the alloy surcharge. This surcharge is a mechanism used by mills to account for the fluctuating market prices of the key alloying elements beyond iron and chromium. For austenitic stainless steels like 304 and 316, the most significant drivers of the surcharge are nickel (Ni) and molybdenum (Mo)2. The surcharge is typically calculated monthly based on the average commodity prices from the previous month. This is why a quote for stainless steel pipe is often only valid for a short period.
When you compare 304 and 316, the difference in the alloy surcharge is stark. Grade 304 typically contains about 8-10.5% nickel and no molybdenum. Grade 316 contains more nickel, typically 10-14%, и the crucial 2-3% of molybdenum. Since nickel and molybdenum are far more expensive than iron and chromium, the surcharge for 316 is always substantially higher than for 304. This surcharge directly reflects the added value and cost of the enhanced chemical composition you are purchasing.
The Molybdenum and Nickel Premium
Molybdenum is the single biggest driver of the cost difference between 304 and 316. It is a refractory metal that is less abundant and more expensive to mine and refine than nickel or chromium. Its price can be highly volatile, directly impacting the 316 surcharge. When global demand for high-strength or corrosion-resistant alloys increases (for example, from the aerospace or energy sectors), the price of molybdenum can spike, widening the price gap between 304 and 316 pipe. As a supplier, we have to pass this commodity cost directly on to the customer.
Nickel also plays a critical role. Grade 316 specifications require a higher minimum nickel content than 304. Nickel is essential for forming the tough, ductile austenitic crystal structure and contributes to overall corrosion resistance. Like molybdenum, nickel is traded on global markets (primarily the London Metal Exchange), and its price can fluctuate wildly. The higher nickel content in 316 adds another layer of cost on top of the molybdenum premium.
Therefore, when a procurement manager from a company like AquaTech sees a 25% price increase for 316, it's not arbitrary. If, for example, nickel is at $20,000/tonne and molybdenum is at $45,000/tonne, the added cost of just those raw materials for a tonne of 316 steel can be several thousand dollars more than for a tonne of 304. This is the tangible cost of the enhanced corrosion performance. It's a direct investment in a more resilient and durable alloy.
Calculating the Total Cost of Ownership (TCO)
Focusing solely on the initial purchase price is a common but critical mistake. A much more powerful financial metric is the Total Cost of Ownership (TCO). TCO considers not only the upfront procurement cost but also all associated costs over the entire lifecycle of the piping system. This includes the cost of installation, maintenance, downtime, repair, and eventual replacement. When viewed through the lens of TCO, the more expensive Grade 316 often emerges as the more economical choice in demanding environments.
Let's revisit the AquaTech Engineering scenario. Let's say the 304 piping system cost $80,000 and the 316 system cost $100,000—a $20,000 difference. If they install the 304 system and it begins to fail from pitting corrosion after five years, what are the costs? There's the cost of the replacement pipe, but more importantly, there's the cost of emergency labor, the operational downtime of their water purification system (lost revenue), the potential damage caused by leaks, and the reputational damage with their client. A single failure event could easily cost well over the initial $20,000 savings.
Conversely, the 316 system, while more expensive upfront, might perform reliably for 20+ years with only routine maintenance. The TCO is simply the initial $100,000 plus minimal maintenance costs. The TCO of the 304 system is the initial $80,000 plus the massive, unplanned costs of failure and replacement. This analysis proves that choosing the correct material is a risk management strategy. The higher upfront cost of 316 is an insurance premium paid to avoid a much larger, unpredictable future cost. This TCO calculation was the final piece of evidence that convinced AquaTech's management that 316 was the only responsible financial choice for their project.
Компонент затрат | Grade 304 Pipe | Grade 316 Pipe | Primary Driver of Difference |
---|---|---|---|
Base Material Cost | Iron, Chromium, Manufacturing | Iron, Chromium, Manufacturing | Minimal difference |
Nickel (Ni) Content | ~8% | ~10% | Nickel is an expensive commodity; 316 has more. |
Molybdenum (Mo) Content | 0% | ~2% | Molybdenum is a very expensive commodity. |
Alloy Surcharge | Нижний | Significantly Higher | Reflects the market price of Ni and Mo. |
Первоначальная покупная цена | Базовый уровень | ~20-40% Higher | The combined cost premium for Nickel and Molybdenum. |
Общая стоимость владения (TCO) | Potentially very high in corrosive environments due to failure/replacement costs. | Higher initial cost but lower lifecycle cost in corrosive environments. | Long-term performance and reliability. |
316 содержит молибденПравда
Grade 316 stainless steel includes 2-3% molybdenum, which significantly enhances its corrosion resistance but increases cost.
304 and 316 have identical nickel contentЛожь
316 typically contains 10-14% nickel versus 304's 8-10.5%, making 316 more expensive due to higher nickel requirements.
What are the practical implications of using 304 vs 316 stainless steel pipes in various industries?
Theory and data are useful, but you need to know what's standard practice in your specific industry. Choosing a material that deviates from the norm can raise questions from clients and regulators, or worse, lead to failures that others in your field have already learned to avoid.
In practice, 304 stainless pipe is the workhorse for industries with mild corrosive environments like food and beverage or architectural applications. 316 stainless steel is mandated in high-corrosion industries like marine, chemical processing, and pharmaceuticals where chloride or acid exposure is common.
This decision has direct operational and regulatory consequences. A client in the dairy industry, a classic user of 304 pipe, once considered "upgrading" to 316 for a new milk processing line. After a discussion, we concluded it was unnecessary. Milk is not highly corrosive, and standard Clean-In-Place (CIP) procedures don't use harsh chlorides. Specifying 316 would have added significant, unrecoverable cost without providing any meaningful performance benefit or meeting any regulatory requirement. Conversely, for a pharmaceutical client producing saline solutions, 316L was the only option on the table; using 304 would have been an immediate compliance failure.
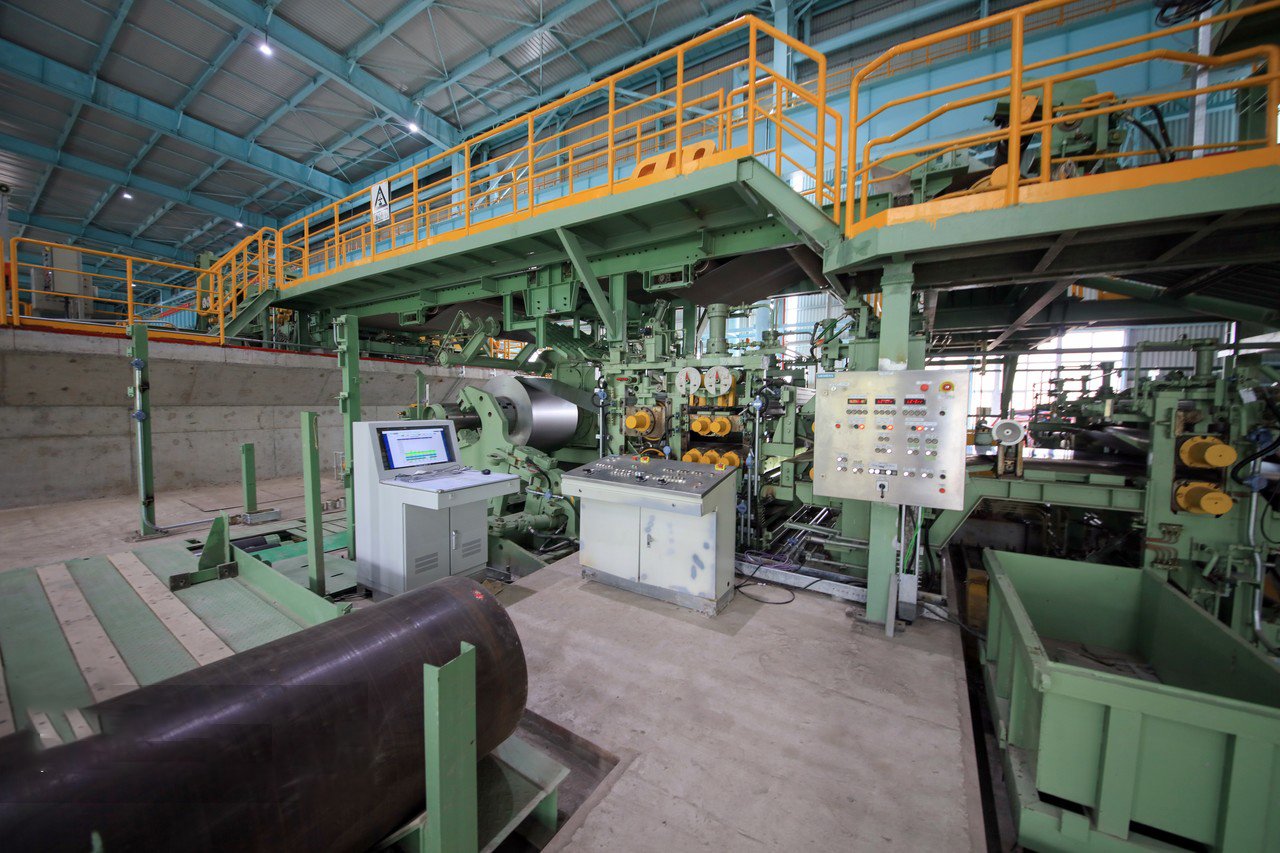
The choice between 304 and 316 is not made in a vacuum; it’s dictated by the unique chemistry, regulations, and operational realities of each industry. What is considered a standard, reliable choice in one field could be a recipe for disaster in another. The practical implications extend beyond mere corrosion resistance to include factors like product purity, regulatory compliance, and the expected lifecycle of the equipment. As a supplier, we see these patterns clearly. Certain industries have established norms based on decades of collective experience with what works and what doesn't. To illustrate this, let's explore the typical material choices and reasoning within three key sectors: the food and beverage industry, the high-purity world of pharmaceuticals, and the extremely demanding environments of marine and chemical processing.
Food & Beverage: The Realm of 304
The food and beverage industry is one of the largest consumers of stainless steel pipe, and Grade 304 is overwhelmingly the material of choice. It is used for transporting everything from milk and beer to sauces and soft drinks. The reason for its dominance is simple: it provides the perfect balance of corrosion resistance, cleanability, and cost-effectiveness for most food-related applications. Most food products are relatively mild in terms of corrosivity, with pH levels that do not aggressively attack the passive layer of 304.
Furthermore, Grade 304 is exceptionally easy to clean and sanitize, which is a paramount concern in preventing microbial growth and ensuring food safety. Its smooth surface, especially when polished, leaves no place for bacteria to hide. Standard industry cleaning protocols, known as Clean-In-Place (CIP) systems, typically use caustic and acid washes that are formulated to be effective without being overly aggressive to 304 stainless steel. The material is considered sanitary and non-reactive, meaning it will not leach any elements into the food product or impart any off-flavors, ensuring product purity.
There are, however, exceptions where 316 is required. These are niche applications involving products with very high salinity (like brines for curing meats or pickling), or those containing aggressive acids like tomato sauce, which has high chloride and acid content. In these specific cases, the risk of pitting corrosion in 304 pipe is significant enough to warrant the upgrade to 316. But for the vast majority of piping in a brewery, dairy, or food processing plant, 304 remains the cost-effective and technically sound industry standard.
Pharmaceutical & Biotech: Purity Demands 316/316L
When we move to the pharmaceutical and biotechnology industries, the baseline for material selection immediately shifts to Grade 316 and, more specifically, 316L. The "L" denotes a low carbon content (typically <0.03%). This is critical because when stainless steel is welded, the carbon can combine with chromium to form chromium carbides at the grain boundaries, which depletes the area of chromium and makes it susceptible to intergranular corrosion. The low carbon content of 316L minimizes this effect, preserving corrosion resistance in the "as-welded" condition.
In these industries, the primary concerns are preventing product contamination and resisting corrosion from highly pure water systems and various process chemicals. Water for Injection (WFI), a staple of pharmaceutical manufacturing, is extremely pure and, because of its lack of ions, can be surprisingly corrosive. More importantly, many processes involve saline solutions or other chloride-containing compounds where 304 would be completely inadequate. The enhanced resistance of 316 to pitting and crevice corrosion is not just a preference; it is a necessity for maintaining the sterile and non-reactive environment required by regulatory bodies like the FDA.
The surface finish is also paramount. Pharmaceutical-grade pipe is often electropolished, a process that removes a microscopic layer from the surface, leaving it incredibly smooth, clean, and with enhanced chromium content for superior corrosion resistance. This ultra-smooth surface minimizes the risk of biofilm formation and ensures complete drainability of the system. In this context, the higher cost of 316L electropolished pipe is simply a non-negotiable cost of doing business, essential for ensuring patient safety and product efficacy.
Marine & Chemical Processing: The Gauntlet for 316
The marine and chemical processing industries represent some of the most challenging environments for any material. Here, Grade 316 is the absolute minimum requirement, and often, even more exotic alloys are needed. In marine environments, any stainless steel exposed to salt spray, salt fog, or direct immersion in seawater is under constant attack from chlorides. Grade 304 would fail rapidly in these conditions, showing significant rust and pitting in a matter of months. Grade 316, with its molybdenum content, provides the necessary defense to withstand this onslaught, making it the standard for everything from boat railings and hardware to piping on offshore oil and gas platforms.
The chemical processing industry presents an even wider array of corrosive challenges. Pipes are used to transport a vast spectrum of acids, alkalis, solvents, and catalysts, often at elevated temperatures and pressures. While Grade 316 has good resistance to many chemicals, its suitability must be evaluated on a case-by-case basis. For example, it performs well with sulfuric acid at low concentrations but is rapidly attacked at high concentrations. It is resistant to many organic acids but can be vulnerable to certain halogenated compounds.
This is where detailed corrosion charts and expert consultation become critical. For many aggressive chemical streams, engineers must specify even higher-performance alloys. This can include duplex stainless steels (which have superior strength and stress corrosion cracking resistance), "Super Austenitic" grades with 6% or more molybdenum, or even nickel-based alloys. In this world, 316 is seen as a robust and versatile starting point, but the specific chemical cocktail being handled will always dictate the final material selection. Using 304 is almost entirely out of the question for any process-contacting surface.
Промышленность | Primary Grade Used | Key Justification | Example Application |
---|---|---|---|
Продукты питания и напитки | 304 / 304L | Cost-effective, excellent cleanability, sufficient corrosion resistance for most food products. | Milk transfer lines, beer fermentation tanks, beverage piping. |
Архитектура | 304 | Good aesthetic, adequate atmospheric corrosion resistance in non-coastal areas. | Interior railings, decorative elements. |
Фармацевтика | 316 / 316L | Purity, resistance to cleaning agents and saline solutions, regulatory compliance (FDA). | Water for Injection (WFI) systems, process fluid piping. |
Морской | 316 | Essential resistance to chloride-induced pitting and crevice corrosion from saltwater. | Boat hardware, piping on offshore platforms, coastal structures. |
Химическая обработка | 316 (as a baseline) | Resistance to a wide range of acidic and chemical process fluids. | Chemical transport piping, reactor vessels. |
304 is standard for food industryПравда
304 stainless steel is the industry standard for food processing due to its cost-effectiveness and sufficient corrosion resistance for most food products.
316 is optional for pharmaceuticalsЛожь
316L is mandatory in pharmaceutical applications due to regulatory requirements and its superior resistance to saline solutions and pure water systems.
How can companies choose the right stainless steel pipe material for their corrosion needs and budget considerations?
You've seen the data and the industry standards, but your project has unique conditions. How do you synthesize all this information into a final, defensible decision? You're caught between the fear of over-engineering (and over-spending) with 316 and under-engineering (and risking failure) with 304.
To choose the right pipe, companies must conduct a formal risk assessment of the service environment, analyze the total cost of ownership instead of just the purchase price, and partner with a knowledgeable supplier who can provide technical guidance and material traceability.
This is the strategic process I walk my clients through every day. For AquaTech Engineering, we moved beyond a simple "304 vs. 3163" debate. We created a decision matrix. We listed all the variables: chloride levels, operating temperature, pressure, client expectations, and lifecycle cost. We assigned a risk score to each. The matrix visually demonstrated that the corrosion risk in their specific application far outweighed the upfront cost savings of using 304. This structured approach removed emotion and provided a clear, data-driven justification for selecting 316, satisfying both their engineering and financial teams.
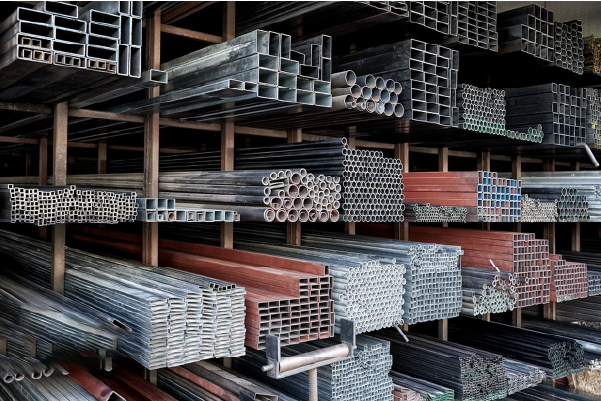
Making the optimal choice is a balancing act, a methodical process that marries technical requirements with financial realities. It’s about replacing uncertainty with a structured evaluation. A hasty decision based on purchase price alone is the most common path to long-term regret. A robust decision-making process, however, builds confidence and ensures the selection is sound from every angle—engineering, finance, and operations. This process can be broken down into three essential steps. First, performing a thorough corrosion risk assessment4 tailored to your specific application. Second, moving beyond the sticker price to conduct a realistic financial analysis of upfront versus lifecycle costs. And third, leveraging the expertise of your supply chain partner to validate your choice and ensure material quality.
Conducting a Corrosion Risk Assessment
The cornerstone of any material selection process is a comprehensive risk assessment. This is not a generic exercise; it must be specific to the intended service conditions of the pipe. The first step is to meticulously document the "what, where, and how." What specific fluid will be flowing through the pipe? This includes not just the primary product but also any cleaning agents (like CIP solutions), potential contaminants, or process additives. You need to know the chemical composition, pH level, and, most importantly, the concentration of chloride ions in parts per million (ppm).
Next, document the operational parameters. What is the expected temperature range, including any spikes during cleaning cycles? As we've seen, temperatures above 60°C can introduce the risk of Коррозионное растрескивание под напряжением (SCC)5. What is the operating pressure? And what is the external environment? A pipe in a climate-controlled indoor facility faces a very different challenge than one on an outdoor coastal rack exposed to salt spray.
With this data in hand, you can begin to quantify the risk. Use corrosion data tables and the PREN formula6 as guides. If your fluid contains more than 100 ppm of chlorides, Grade 304 immediately becomes a high-risk choice for pitting corrosion. If the environment is marine or involves de-icing salts, 316 is the minimum baseline. This systematic approach forces you to confront the specific threats your piping system will face, moving the decision from a vague feeling to a data-supported conclusion.
Financial Analysis: Upfront Cost vs. Lifecycle Cost
With a clear technical risk assessment, the next step is to perform a realistic financial analysis. As we've discussed, this means calculating the Total Cost of Ownership (TCO), not just comparing the initial purchase price. The first step is to get firm quotes for both 304 and 316 options from your supplier to understand the real-world upfront cost difference, which we'll call the "investment premium" for 316.
Now, you must quantify the potential cost of failure if you choose the lower-grade material. This is the "cost of risk." What would be the financial impact of a significant leak? This includes the cost of replacement material and labor, the cost of lost production during downtime, potential penalties for late orders, the cost of cleaning up any spills, and potential safety incidents. Even if the probability of failure in a year is only 5%, multiplying that probability by the high cost of failure reveals a significant "risk-adjusted" annual cost associated with choosing the cheaper option.
When you compare the certain, one-time investment premium for 316 against the potential, recurring annual cost of risk for 304, the financial picture becomes much clearer. For the AquaTech project, the $20,000 premium for 316 was a known quantity. The potential cost of a system failure was estimated at over $50,000 per event. Even a low probability of that event made the $20,000 investment look like a very smart insurance policy. This TCO mindset shifts the conversation from "How much can we save now?" to "What is the smartest long-term investment?"
The Role of a Supplier Partnership
Lastly, do not underestimate the value of a strong partnership with a knowledgeable and reputable material supplier. A good supplier is more than just a company that takes your order and ships your pipe; they are an extension of your technical team. They have broad experience across multiple industries and can provide invaluable insights and validation for your decision-making process. At MFY, we see ourselves as consultants first and foremost. When a client comes to us with a specification, we make it a point to ask about the application. This allows us to act as a second check.
A quality supplier provides two critical things: technical guidance and quality assurance. They can review your risk assessment and provide feedback based on their experience with similar applications. They might suggest a nuance you hadn't considered, like the specific grade of cleaning chemical being used, or point you toward a more cost-effective solution if you are over-engineering.
Most importantly, a trusted supplier guarantees the quality and traceability of the material you purchase. Every pipe should be delivered with a Сертификат об испытании мельницы (MTC)7, the material's "birth certificate" that documents its exact chemical composition and mechanical properties. This is your ultimate proof that the 316 pipe you paid for actually contains the required percentage of molybdenum and nickel. This assurance of quality is the final, critical link in the chain, ensuring that your carefully made decision is fully realized in the physical product you install.
Decision Factor | Low Risk (Favors 304) | High Risk (Favors 316) | Key Question to Ask |
---|---|---|---|
Воздействие хлоридов | < 100 ppm; controlled, non-coastal environment. | > 100 ppm; brackish water, coastal or marine environment, de-icing salts. | What is the maximum chloride concentration the pipe will ever see? |
Acidity (pH) | Neutral pH (6-8); mild food products. | Low pH (<5); acidic process chemicals, some acidic foods. | What is the full pH range of the process and cleaning fluids? |
Температура | Ambient; consistently below 50°C (122°F). | Elevated; frequent or sustained operation above 60°C (140°F). | What is the peak temperature during operation or cleaning cycles? |
Lifecycle Cost | Low consequence of failure; non-critical system, easy to repair/replace. | High consequence of failure; critical system, major downtime costs. | What is the true business cost of an unplanned shutdown? |
Regulatory/Purity | Standard industrial or architectural use. | Pharmaceutical, biotech, or high-purity food grade where purity is paramount. | Are there any industry or government regulations dictating material choice? |
316 is better than 304 for high chloride environmentsПравда
316 contains molybdenum which provides superior resistance to chloride-induced pitting corrosion compared to 304.
Initial cost is the most important factorЛожь
Total cost of ownership including potential failure costs should be considered, not just purchase price.
What are the best practices for maintaining 304 and 316 stainless steel pipes to ensure longevity?
You've invested in the right material and installed it correctly. But your job isn't over. Without a proper maintenance plan, even the mighty Grade 316 can fall victim to contamination and corrosion, jeopardizing your investment and the integrity of the entire system.
Best practices for maintaining stainless steel pipes include initial passivation to enhance the chromium-rich layer, implementing a routine cleaning schedule with non-chloride agents, and strictly avoiding contact with carbon steel to prevent iron contamination and galvanic corrosion.
Ensuring longevity is about proactive care. A chemical processing client once called me about unexpected surface rust appearing on their new 316 piping. After investigation, we discovered the installation crew had used carbon steel wire brushes to clean the welds. This deposited iron particles onto the surface, which then rusted, initiating corrosion on the otherwise resistant pipe. We had to implement a costly repassivation procedure. This experience taught them a valuable lesson: material purity must be maintained throughout the pipe's entire life.
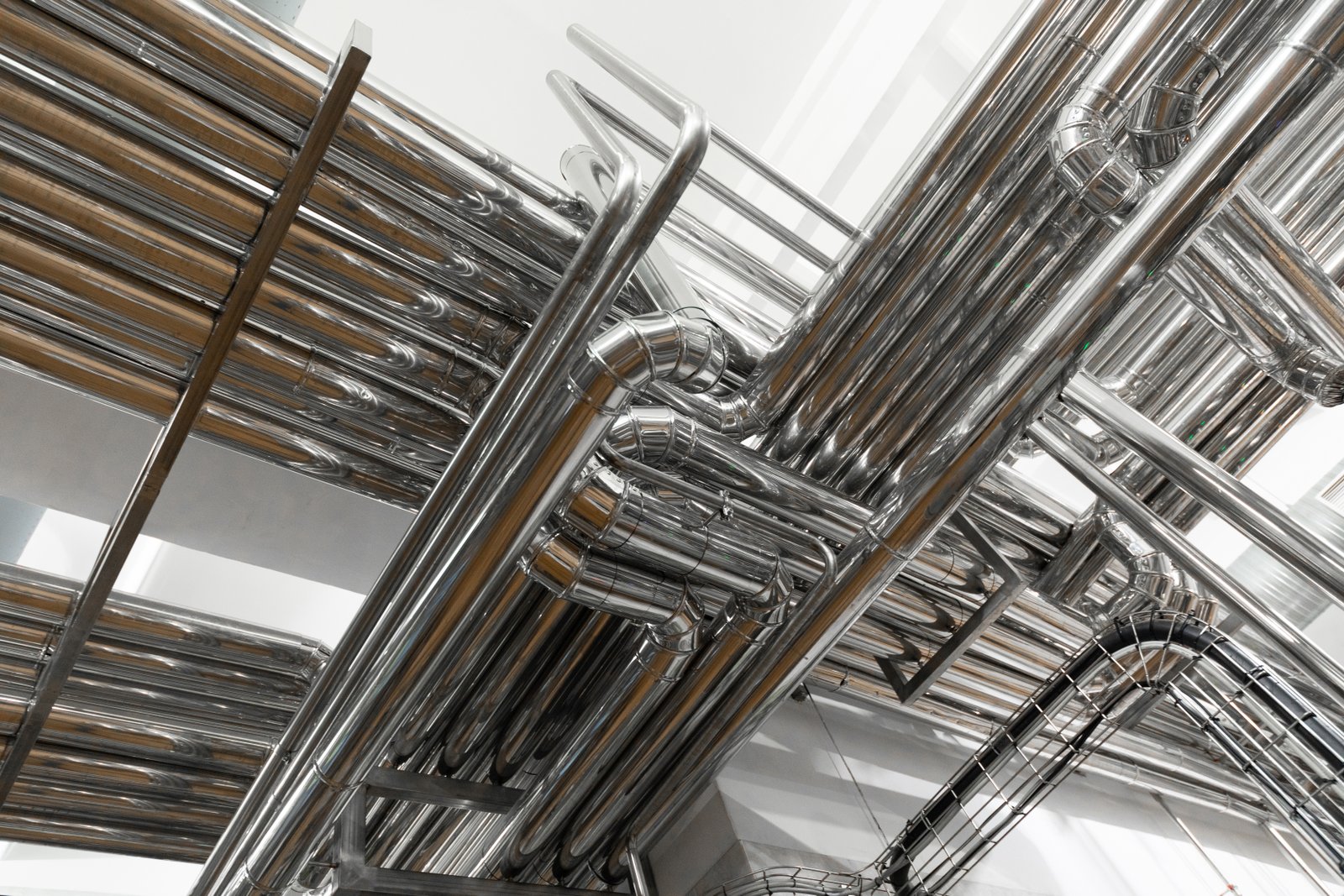
The selection of the correct alloy is the first step toward a long service life, but it is not the last. Maintenance is the ongoing process that preserves the material's inherent corrosion resistance. Proper care ensures the passive layer—the steel's protective shield—remains healthy, intact, and free from contaminants. The best practices for maintenance are not complex or expensive, but they do require diligence and an understanding of what helps the steel versus what harms it. The strategy can be divided into three key phases: the critical first step of initial passivation after installation, the development of a smart routine cleaning and inspection protocol, and the disciplined practice of avoiding cross-contamination throughout the pipe's lifecycle. These three pillars will ensure your piping system delivers the long, trouble-free service life you designed it for.
Passivation and Initial Cleaning
Once a new piping system is installed, it should not be put into service immediately. The process of cutting, welding, and handling can leave the surface compromised. Welding heat can create heat tint (oxide scale), and tools can leave behind iron particles or other contaminants. The single most important post-installation step is a thorough cleaning followed by passivation. Passivation is a chemical process, typically using a nitric or citric acid solution, that is designed to remove contaminants and, more importantly, to chemically enhance the passive chromium oxide layer, making it thicker, more uniform, and more resistant to corrosion than it would be naturally.
The process begins with degreasing and cleaning to remove any oils, grease, or dirt from installation. Following this, the passivation solution is circulated through the piping system for a specified time and temperature. This acid bath dissolves any free iron and other contaminants from the surface while simultaneously promoting the growth of a high-quality passive layer. This isn't just a cleaning process; it's a conditioning process that maximizes the inherent corrosion resistance of the alloy you selected.
For the chemical client who experienced rusting on their 316 pipes, the root cause was iron contamination from carbon steel tools. Had they performed a proper passivation procedure immediately after installation, the acid would have removed those iron particles before they had a chance to rust and initiate corrosion sites. Performing this crucial first step sets the stage for a long and trouble-free service life, essentially unlocking the full potential of the stainless steel.
Routine Maintenance and Inspection Protocols
Once the system is passivated and in service, a routine maintenance and inspection plan is the key to longevity. The intensity and frequency of this plan will depend on the service environment. A 316 pipe carrying saline solution8 will require more frequent attention than a 304 pipe carrying potable water. The goal of routine cleaning is to prevent the buildup of deposits that could create crevices or harbor corrosive substances. Cleaning should always be done with tools that will not damage the steel. This means using soft cloths, nylon brushes, or non-metallic pads. Never use steel wool or carbon steel brushes.
The choice of cleaning agent is critical. The guiding principle is to use the mildest cleaner that will do the job. For most applications, warm water and a mild detergent are sufficient. For more stubborn deposits, a solvent may be used. It is absolutely essential to avoid cleaners that contain chlorides, especially hydrochloric acid. Many commercial cleaners, particularly those for masonry, contain chlorides and can cause catastrophic damage to stainless steel. After any cleaning procedure, the system should be thoroughly rinsed with clean water to remove any residue of the cleaning agent.
Visual inspection should be a part of the routine. Periodically inspect the piping, paying close attention to welds, joints, and any areas where fluid might stagnate. Look for any signs of discoloration, staining, or pitting. Early detection is key. A small spot of tea staining on an exterior 316 pipe can often be easily cleaned, but if left for years, it can develop into more serious pitting. A formal protocol ensures that this diligence is maintained consistently over the life of the facility.
Avoiding Cross-Contamination
Perhaps the most insidious and avoidable threat to stainless steel is cross-contamination from carbon steel. As highlighted by my client's experience, this is a very common problem on construction sites and in fabrication shops. When a carbon steel tool—a grinder, a wire brush, a wrench, even a dirty work glove—comes into contact with stainless steel, it can embed microscopic particles of iron onto the surface. This is called "free iron" contamination. These iron particles are not protected by a passive layer. When exposed to moisture, they rust. This rust can not only stain the stainless surface but also break down the passive layer beneath it, creating a site for localized corrosion of the stainless steel itself.
To prevent this, strict fabrication and handling protocols are necessary. Ideally, there should be a dedicated area and dedicated tools used only for working with stainless steel. Tools used on carbon steel should never be used on stainless steel without being thoroughly cleaned and decontaminated. This includes grinding wheels, wire brushes, and clamps. When systems of mixed metals are necessary, the two materials should be electrically isolated using non-conductive gaskets and washers to prevent galvanic corrosion, where the less noble metal (carbon steel) will corrode preferentially when in contact with the more noble metal (stainless steel) in the presence of an electrolyte.
This discipline extends to storage as well. Stainless steel pipes should be stored off the ground and away from areas where they might be contaminated by carbon steel dust from nearby grinding or cutting operations. These practices might seem overly cautious, but they are fundamental to preserving the integrity of the material. The "stainless" quality of the steel is entirely dependent on its clean, uncontaminated surface. Maintaining that purity is the essence of effective long-term maintenance.
Passivation enhances chromium layerПравда
Passivation chemically thickens the chromium oxide layer, improving corrosion resistance.
Steel wool is safe for cleaningЛожь
Steel wool can embed iron particles, causing contamination and corrosion.
Заключение
The choice between 304 and 316 pipe is a strategic decision balancing cost against performance. While 304 is a reliable workhorse, 316's molybdenum content provides essential chloride resistance that justifies its higher price in demanding environments, making it a long-term investment in operational reliability.
-
Discover how molybdenum in 316 enhances protection against corrosive environments ↩
-
Understand how nickel and molybdenum affect the pricing of stainless steel products ↩
-
Evaluating the choice between 304 and 316 for project specifics ↩
-
Understanding a detailed corrosion risk assessment process for informed decision-making ↩
-
Understanding SCC risks related to stainless steel applications ↩
-
Learn how to evaluate pitting resistance using PREN for better material choice ↩
-
Authenticate stainless steel's quality and traceability through MTC insights ↩
-
Understand the impact of saline on stainless steel maintenance needs. ↩
У вас есть вопросы или нужна дополнительная информация?
Свяжитесь с нами, чтобы получить индивидуальную помощь и квалифицированный совет.