PVC-Coated Stainless Coil: Scratch-Free Fabrication
Are you constantly battling scratches on your stainless steel components during fabrication? These imperfections lead to costly rework, rejected parts, and project delays, ultimately compromising the quality of your final product. Fortunately, a simple, proactive solution can protect your surfaces and ensure a flawless finish.
To achieve scratch-free stainless steel fabrication, you must protect the material's surface throughout the entire process. The most reliable method is using a temporary protective film, like a PVC coating, which shields the steel from mechanical abrasions, handling marks, and workshop debris from start to finish.
These seemingly minor surface flaws can escalate into significant financial and reputational headaches. Before we explore the ultimate solution, it's crucial to understand the journey a stainless steel coil1 takes through fabrication and identify its many vulnerabilities. This understanding is the first step toward implementing a truly effective strategy for protecting your investment and delivering a perfect end product.
In my years as Global Business Director at MFY, I’ve witnessed how a single deep scratch can halt an entire production run. The problem is far more complex than a simple handling mistake; it's a systemic challenge in modern manufacturing. From the moment a coil is unwound, it faces a gauntlet of potential threats: guide rollers, slitting blades, press brakes, and transport. Industry data from the Metal Processing Institute2 suggests that surface defects can account for up to 7% of material waste in high-finish applications. This is a direct blow to profitability, making a proactive "protect-it-now" strategy essential.
What challenges are faced in fabricating stainless coils without causing scratches?
Striving to maintain the pristine, reflective finish of a stainless steel coil throughout fabrication can feel like an uphill battle. Every step, from initial handling to final assembly, poses a significant risk of scratches that diminish the product's aesthetic appeal and value, requiring a robust preventative strategy.
The primary challenges in preventing scratches during stainless coil fabrication include abrasive contact from machinery and tools, improper handling and storage protocols, friction during forming and bending, and contamination from workshop debris. These factors can easily mar the delicate surface, causing cosmetic and potentially functional defects.
The journey of a stainless steel coil from our warehouse to a client’s finished product is fraught with peril for its surface. As an integrated supplier, we at MFY have seen it all. Imagine a typical fabrication line: the coil is unwound, leveled, slit or laser-cut, bent on a press brake, and then assembled. Each stage is a potential "scratch zone." Guide rollers can harbor abrasive particles. Press brake tooling can leave impressions. Even a worker's glove, if contaminated with metal filings, can cause irreparable damage. It's a battle fought on multiple fronts. I once worked with a client in the high-end home appliance industry who was facing a 5% rejection rate on polished stainless steel panels due to fine scratches. The cost was staggering, not just in wasted material but in lost production time. This experience highlighted that simply being careful isn't enough; a physical barrier of protection is necessary. Understanding the specific nature of these challenges is the only way to formulate a truly effective defense for the steel's surface.
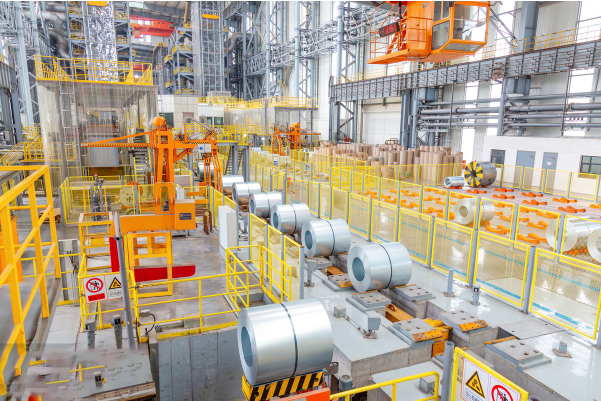
The path to a flawless finish requires a deep understanding of the nuanced challenges that arise at every stage of the fabrication process. It's a combination of mechanical, human, and environmental factors that all conspire against the pristine surface of the stainless steel. Protecting this surface requires a multi-faceted approach that addresses each of these threats directly.
The Hidden Dangers in Automated Processing Lines
Many of our clients in the manufacturing sector invest heavily in automation for metal fabrication3 to boost output and ensure precision. However, these high-speed systems, with their numerous rollers, guides, clamps, and feeders, create multiple points of contact where constant pressure and friction can easily mar a delicate stainless steel surface. A single misaligned roller or a worn-out tension pad can create a continuous scratch along hundreds of meters of coil, turning a high-value asset into scrap material in a matter of minutes. The speed of these lines means that by the time a defect is spotted, significant waste has already occurred.
I remember working with a major appliance manufacturer in India who was seeing consistent, fine scratches on their 430-grade stainless steel refrigerator doors. After an audit of their process, we pinpointed the source: their automated decoiling and leveling line. Minute metal filings had become embedded in the polyurethane guide rollers, essentially turning them into fine-grit sandpaper that abraded the steel's surface as it passed through. According to a 2024 report by the Sheet Metal & Fabrication Journal, over 60% of persistent, linear scratching defects in automated lines are caused by the contamination of contact surfaces.
This scenario underscores a critical lesson for modern fabricators: automation does not eliminate risk; it simply changes its nature and amplifies the consequences of minor issues. Relying solely on machine maintenance schedules is a reactive strategy that leaves your materials vulnerable. The most robust and reliable solution is to apply a physical barrier to the steel itself before it enters this automated gauntlet. This proactive defense ensures that the pristine surface is never directly exposed to the inherent risks of high-speed processing, safeguarding your material from the very first step.
Human Factor and Handling Vulnerabilities
Despite the rise of automation, the human element remains a critical and often unpredictable part of the fabrication process. Manual handling is unavoidable during quality inspections, transfer between workstations, loading and unloading machines, and final assembly. Each of these touchpoints introduces a high degree of variability and risk. A moment of carelessness, such as placing a tool on the steel's surface or dragging a sheet across a contaminated workbench, can result in deep, costly scratches.
I recall a visit to a partner in Southeast Asia specializing in architectural cladding for luxury hotels. They were experiencing random, non-linear scratches on large, high-polish panels, and they couldn't identify a consistent source. Our joint investigation revealed the issue wasn't with their machinery but with their handling procedures. Workers, under pressure to meet deadlines, were occasionally placing tool belts on stacks of finished panels and using improper separators during storage. The cost wasn't just in the rejected panels but in the significant man-hours spent trying to buff out the damage, which often distorted the finish and made the problem worse.
This highlights the limitations of relying solely on training and procedural controls. While essential, these measures are always susceptible to human error. A physical protective film on the steel surface acts as a constant, reliable safeguard. It serves as both a physical barrier against accidental damage and a visual reminder to handlers that the surface beneath is valuable and delicate. It transforms the protection strategy from one based on hope and vigilance to one based on physical certainty.
Environmental and Contamination Risks
The fabrication environment itself is a silent but potent adversary in the fight against scratches. Airborne particles, such as dust, grit, and metal shavings from nearby grinding or cutting operations, can settle on the surface of the stainless steel. When the steel is subsequently stacked, moved, or processed, these seemingly insignificant specks of debris are pressed or dragged across the surface, acting as powerful abrasive agents that cause pits and scratches.
A client in the elevator manufacturing sector in the Middle East faced a perplexing issue with "pitting" on their brushed-finish stainless steel cabin panels. The defects were not linear scratches but small, indented marks that ruined the aesthetic. The cause was traced to fine, abrasive dust from a nearby concrete flooring project settling on the steel sheets before they were sent to the press brake. The immense pressure of the press would embed these hard particles directly into the stainless steel surface. This demonstrates that the challenge extends beyond direct tool contact and includes the ambient cleanliness of the entire operational facility.
Let's compare the risk exposure in a typical workshop environment.
Risk Factor | Unprotected Coil | PVC-Coated Coil |
---|---|---|
Airborne Abrasive Dust | High risk of embedding/scratching upon pressure. | Debris settles on the disposable PVC film, not the steel. |
Accidental Tool Contact | Direct impact or drag causes a deep scratch. | The PVC layer absorbs minor impacts and prevents scratches. |
Stacking & Storage | Metal-on-metal contact creates friction and scuffing. | Smooth PVC-on-PVC contact allows for low-friction stacking. |
This analysis makes it clear that a PVC coating does more than protect against obvious mechanical damage; it isolates the valuable steel surface from the ambient environmental hazards of a busy workshop. It ensures that the quality of the finish is not left to chance or the daily fluctuations in workshop cleanliness.
Why do stainless steel coils get scratched during fabrication?
Are you frustrated by discovering scratches on your stainless steel after it has already been processed? This common issue often stems from a series of overlooked causes throughout the production line, turning your high-quality raw material into a compromised final product and eroding your profit margins.
Stainless steel coils get scratched during fabrication primarily due to mechanical abrasion from machinery, tooling, and handling. This includes contact with contaminated rollers, friction during bending and forming, improper storage without separators, and dragging sheets across abrasive surfaces, all of which compromise the steel's protective passive layer.
The vulnerability of stainless steel lies in its prized finish. Whether it's a mirror-like polish or a delicate brushed texture4, the surface is susceptible to damage from the very first step of fabrication. When a coil is unwound, the tension and guide systems can be a source of linear scratches if not perfectly maintained. Then, as the sheet goes through slitting or laser cutting, small burrs or sharp edges on the material itself can scratch adjacent surfaces when stacked. During press brake forming, immense pressure is applied, and any debris on the die or the steel's surface will be pressed into the material, creating permanent indentations. Even the simple act of transporting a sheet from one station to another is a risk. A client producing commercial kitchen countertops found that most of their defects came from sliding sheets off a stack, where tiny trapped particles acted like sandpaper. Understanding these root causes is not about placing blame; it's about identifying every point where the integrity of the surface is at risk so that a comprehensive protective strategy can be implemented.
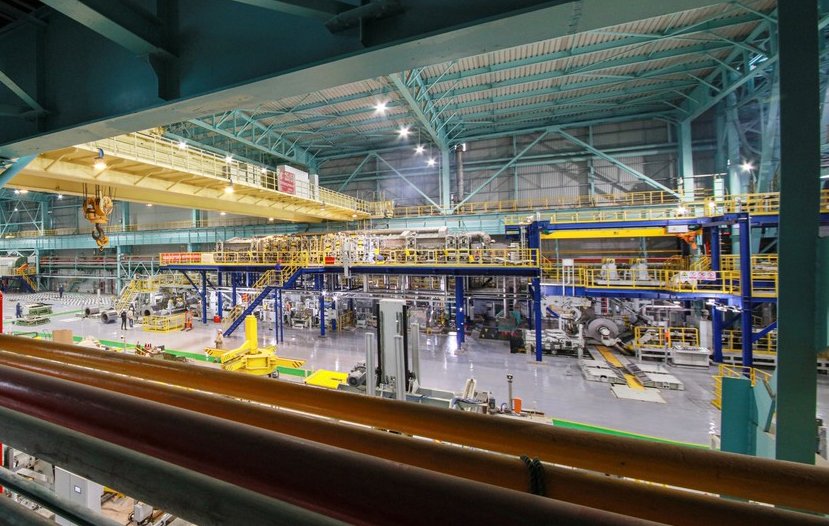
Uncovering the specific reasons for scratching is the first step toward creating a truly resilient fabrication process. The causes are often a combination of factors related to machinery interaction, material properties, and workshop practices. By dissecting these core issues, we can move from merely reacting to defects to proactively preventing them from ever occurring, ensuring that the inherent value of the stainless steel is preserved.
Mechanical Abrasion from Tooling and Machinery
The most frequent cause of scratches is direct, forceful contact with the tools and machines designed to shape the steel. Every metallic surface that touches the stainless steel coil is a potential source of damage. Guide rollers, press brake dies, stamping tools, and even measuring calipers can leave their mark. The problem is often exacerbated by wear and tear on the equipment and lack of regular inspection protocols5. A small chip on a forming die or a hardened buildup of residue on a roller creates a high-pressure point that will consistently damage every piece of steel that passes over it.
For instance, a customer of ours in the automotive parts sector in Russia was experiencing a high rejection rate for a stamped 304-grade component. The scratches were identical on every rejected part. An inspection of their stamping press revealed that a small piece of metal shaving had become welded to the die surface. This tiny imperfection was effectively engraving a scratch onto every single part during the stamping cycle. Data from manufacturing analytics firm Pro-Met Consult shows that approximately 40% of repeatable surface defects are traced back to tooling that is either damaged, worn, or contaminated.
This is where a protective PVC film becomes an invaluable insurance policy. The film provides a compressible, sacrificial layer that stands between the tooling and the steel surface. When the press comes down, the film absorbs the pressure from minor imperfections on the die, distributing the force and preventing the hard tool surface from digging into the softer stainless steel. It effectively neutralizes the threat posed by less-than-perfect tooling.
Friction and Galling During Forming Processes
Stainless steel, particularly austenitic grades like 304 and 316, is known for its tendency to gall during forming operations6. Galling is a severe form of adhesive wear that occurs when two surfaces slide against each other under heavy pressure. During processes like deep drawing or tight-radius bending, the friction between the steel and the die can cause the surfaces to momentarily weld together. As the materials pull apart, they tear chunks from each other, resulting in significant surface damage, including deep scratches and gouges.
We worked with an engineering contractor in the Middle East who was fabricating complex architectural panels with intricate bends. They were fighting a constant battle with galling on the bend lines, which was not only an aesthetic issue but also a potential site for corrosion. They tried various lubricants, which were messy, difficult to clean, and only partially effective. The lubricants also created issues with subsequent welding and finishing processes, adding steps and costs to their workflow.
A PVC-coated coil offers a superior solution. The polymer film acts as a clean, dry lubricant barrier that physically separates the stainless steel from the tool surface. This prevents the metal-to-metal contact that is the prerequisite for galling. The film's low coefficient of friction allows the stainless steel to slide smoothly over the die during the forming operation, even under extreme pressure. This eliminates the need for messy lubricants, streamlining the entire production process and resulting in a clean, scratch-free bend every time.
Contamination and Improper Handling Practices
Often, the source of scratching is not the primary machinery but the surrounding environment and handling protocols. As we've discussed, airborne contaminants like dust and metal filings are a major threat. However, improper handling practices are equally damaging. Stacking sheets without protective interleaving, dragging coils across concrete floors, or using un-deburred clamps and grips can all introduce deep, random scratches that are impossible to polish out.
A classic example comes from a distributor client who also performed basic slitting services. Their end-customers were complaining about scratches found deep within the newly slit coils. The cause was traced back to the recoiling process. As the slit strips were being wound into a new coil, small, sharp burrs created during the slitting process on the edge of one strip would scratch the pristine surface of the strip being wound next to it. The tight winding pressure ensured this damage was consistent throughout the coil.
This problem is elegantly solved by using PVC-coated coils from the outset. When a coated coil is slit, the PVC film remains on the surface. During recoiling, the sharp burr from one edge only comes into contact with the PVC film on the adjacent strip, not the steel itself. The film is tough enough to resist being punctured by these small burrs, preserving the integrity of the steel surface beneath. This simple, built-in protection saves time, reduces waste, and guarantees that the customer receives a flawless product.
Cause of Scratch | How Unprotected Steel is Damaged | How PVC Coating Prevents Damage |
---|---|---|
Tool Imperfections | A chip in a die directly engraves the steel surface. | PVC film cushions the impact, preventing the flaw from reaching the steel. |
Forming Friction | Metal-on-metal contact under pressure causes galling and tearing. | PVC acts as a dry lubricant, allowing steel to slide smoothly. |
Slitting Burrs | Sharp edges on a slit strip scratch the surface of the next layer in the coil. | The burr scratches the disposable PVC film, not the valuable steel. |
Handling/Debris | Dragging or stacking with debris creates abrasive scratches. | The film takes the abrasion, protecting the steel surface underneath. |
How do scratches on stainless steel coils impact product quality and performance?
Thinking that a few scratches are just a minor cosmetic issue? This misconception can be incredibly costly. Scratches on stainless steel are far more than skin deep; they directly impact product value, structural integrity, and your brand's reputation, leading to customer rejections and financial losses.
Scratches on stainless steel coils severely impact quality by creating aesthetic defects that lead to product rejection. More critically, they compromise the material's passive layer, creating nucleation sites for corrosion, which reduces the product's long-term performance, durability, and hygienic properties.
The moment a stainless steel surface is scratched, two things happen. First, its visual appeal is immediately compromised. For applications like architectural panels, high-end appliances, or decorative trim, the aesthetic is the primary feature. A scratch is not just a flaw; it's a failure. I have seen entire shipments for luxury construction projects rejected because of visible scratches on the cladding, causing massive delays and financial penalties for our client. Second, and more insidiously, a scratch damages the chromium oxide passive layer7 that gives stainless steel its signature corrosion resistance. This microscopic damage breaks the protective shield. In environments with moisture, salt, or chemicals, this small scratch becomes the focal point for rust and pitting corrosion, undermining the very reason stainless steel was chosen. For industries like food processing or medical equipment, where hygiene is paramount, a scratched surface can harbor bacteria, creating a safety hazard. Therefore, a scratch is a direct assault on both the form and function of the final product.
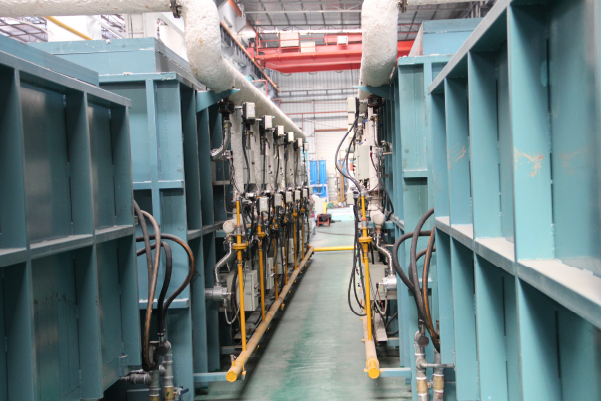
The consequences of a scratched surface ripple outward, affecting everything from customer perception to the product's physical lifespan. It's a compound problem where an initial aesthetic flaw can evolve into a significant performance failure. Delving deeper into these impacts reveals why maintaining a perfect surface finish is not a luxury but a fundamental requirement for quality manufacturing.
Compromised Corrosion Resistance and Structural Integrity
The primary value proposition of stainless steel is its exceptional resistance to corrosion. This property is not inherent in the bulk metal itself but comes from a very thin, invisible, and self-healing layer of chromium oxide on its surface, known as the "passive layer." When a scratch occurs, it physically cuts through this protective film, exposing the raw iron-containing alloy underneath to the environment.
While the passive layer can reform, a deep scratch creates a crevice with a different microenvironment. This area can trap moisture, chlorides, and other contaminants, preventing proper repassivation and creating a perfect nucleation site for localized corrosion, such as pitting or crevice corrosion. A 2023 study in the Journal of Materials Engineering and Performance showed that the corrosion rate at the base of a 50-micrometer deep scratch on 304 stainless steel in a saline environment was over 100 times higher than on the undamaged surface. For a client in the marine industry, we saw this firsthand when a series of scratched railings failed inspection after only a few months in service due to visible rust originating directly from the fabrication marks.
This is not just a cosmetic issue of rust stains. Pitting corrosion can propagate deep into the material, creating stress concentration points that can eventually lead to cracking and catastrophic structural failure, especially in load-bearing applications or pressurized systems. Therefore, a scratch directly undermines the long-term durability and safety of the product.
Diminished Aesthetic Value and Brand Reputation
In a vast number of applications, stainless steel is chosen specifically for its clean, modern, and high-end appearance. From the gleaming façade of a skyscraper to the flawless finish of a commercial-grade refrigerator or the polished surface of a luxury watch, the aesthetic is inextricably linked to the product's perceived quality and value. A scratch, no matter how small, shatters this perception. It communicates carelessness and poor quality control.
Consider the highly competitive consumer appliance market. A customer purchasing a premium stainless steel dishwasher expects perfection. A visible scratch on the door panel, discovered upon unboxing, will almost certainly lead to a product return. This has a multi-layered cost for the manufacturer: the cost of the returned unit, the logistics of handling the return, the cost of repair or replacement, and most importantly, the damage to brand reputation. A negative customer experience can quickly multiply through online reviews and word-of-mouth.
At MFY, we supply coils to manufacturers of elevator interiors, a market where aesthetics are paramount. One of our clients quantifies the cost of a single rejected panel at over five times the material cost, once labor, rework, and project delay penalties are factored in. This demonstrates that for high-visibility products, the surface finish is the product in the eyes of the end-user. Protecting that finish is equivalent to protecting the brand's promise of quality.
Hygiene and Cleanability Concerns in Sanitary Applications
In industries such as food and beverage processing, pharmaceuticals, and healthcare, stainless steel is the material of choice due to its non-porous surface and excellent cleanability. A smooth, unbroken surface prevents the buildup of bacteria, biofilms, and other contaminants, ensuring a sterile environment. A scratch fundamentally compromises this critical hygienic property.
A scratch, gouge, or crevice creates a microscopic trench where bacteria can shelter from cleaning and sterilization agents. This can lead to the formation of difficult-to-remove biofilms, posing a serious contamination risk. Regulatory bodies like the FDA and standards such as 3-A Sanitary Standards have stringent requirements for surface finishes on food-contact equipment, often specifying a maximum surface roughness (Ra). A scratch is a significant deviation from the specified Ra value.
We once consulted for a dairy processing equipment manufacturer who was facing sanction from a food safety auditor. The issue was traced back to scratched surfaces inside a processing tank, which were found to harbor microbial colonies even after a full clean-in-place (CIP) cycle. The root cause was damage during the tank fabrication and welding process. Switching to PVC-coated coils for the raw material eliminated this initial damage, ensuring a smooth interior surface that met strict hygiene standards. This protected them from regulatory action and upheld their reputation for supplying safe, high-quality equipment.
Impact Area | Consequence of an Unprotected, Scratched Surface | Benefit of a Scratch-Free, PVC-Coated Surface |
---|---|---|
Performance | Damaged passive layer leads to localized corrosion and potential failure. | Intact passive layer ensures maximum corrosion resistance and longevity. |
Aesthetics | Visible flaws lead to product rejection and diminished brand value. | Flawless finish commands premium value and reinforces brand quality. |
Hygiene | Scratches harbor bacteria, creating safety risks in sanitary applications. | Smooth, unbroken surface ensures superior cleanability and meets regulatory standards. |
What solutions can prevent scratching in stainless steel coil fabrication?
Tired of seeing valuable stainless steel damaged during the fabrication process? Simply hoping for the best is not a strategy. The good news is that there are proven, practical solutions that can be implemented to protect your material from start to finish, saving you time, money, and frustration.
The most effective solution to prevent scratching is using stainless steel coils with a factory-applied protective PVC coating. This is complemented by maintaining clean and well-aligned machinery, implementing proper handling and storage protocols, and using non-abrasive tooling where possible.
While a holistic approach is best, the single most impactful solution is starting with a protected raw material. A PVC-coated coil8 from MFY arrives at your facility with a durable barrier already in place. This film acts as a shield throughout your entire workflow—decoiling, slitting, forming, and even light assembly. It absorbs the impacts, scuffs, and abrasions that would otherwise damage the steel. I've seen clients transform their production lines with this single change. For instance, a manufacturer of architectural elements reduced their surface-defect rejection rate by over 90% simply by switching to PVC-coated coils. This primary solution, when combined with secondary best practices like regular machine inspection and training staff on proper handling techniques, creates a nearly foolproof system for producing scratch-free products and maximizing profitability.
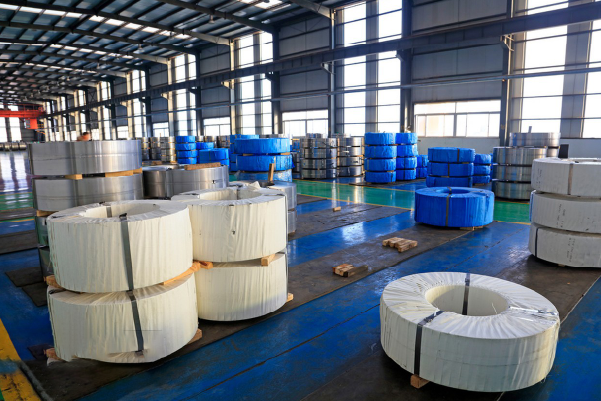
Implementing a robust strategy to prevent scratches is an investment in quality and efficiency that pays for itself many times over. It involves moving from a reactive mindset of fixing defects to a proactive one of preventing them entirely. Let's explore the hierarchy of solutions, from the most fundamental and effective to the supporting practices that create a truly comprehensive system of protection.
The Primary Solution: Factory-Applied PVC Coating
The most direct, reliable, and cost-effective method to prevent scratches is to use stainless steel coils that have a protective PVC (polyvinyl chloride) film applied at the source. This is the cornerstone of any serious scratch-prevention program. The film is applied by the steel supplier (like MFY) under clean, controlled conditions, ensuring perfect adhesion and coverage before the coil ever faces the rigors of transport and fabrication. This film acts as a durable, sacrificial "skin" for the steel.
The beauty of this solution lies in its simplicity and effectiveness. The PVC film remains on the steel throughout the entire fabrication process—from uncoiling and laser cutting to bending and forming. It withstands the immense pressures of press brakes and the friction of guide rollers. The laser can even cut directly through the film and steel simultaneously without issue. The film is only removed at the very end of the process, often just before final inspection or shipping, revealing a perfectly pristine, untouched surface beneath.
We worked with a large-scale producer of commercial kitchen equipment who was spending significant labor hours on post-fabrication polishing to remove scratches. By switching their procurement to our PVC-coated 304 coils, they eliminated the entire polishing department. The ROI was realized in under three months, factoring in labor savings, reduced abrasive consumable costs, and increased throughput. This is the power of a primary, built-in solution.
Secondary Solution: Process and Machinery Optimization
While PVC coating is the primary defense, optimizing your fabrication process and equipment9 provides a crucial second layer of protection. This involves meticulous maintenance and careful selection of the machinery and tooling that comes into contact with your material. Even when using a PVC-coated coil, reducing the overall stress and abrasive forces on the material is a best practice that extends tool life and prevents the film itself from being excessively damaged.
Key practices include regular inspection and cleaning of all contact surfaces, such as rollers, guides, and clamps, to ensure they are free of debris and metal filings. Aligning machinery properly minimizes unnecessary friction. When possible, using "non-marring" tooling, such as urethane inserts or polished and hardened dies, can make a significant difference, especially in high-pressure forming applications. For example, using nylon lifting clamps instead of bare steel clamps for moving sheets can prevent deep gouges.
A client manufacturing precision electronic enclosures found that even with PVC film, they were getting pressure marks during a deep-draw stamping process. We advised them to pair the PVC-coated material with a highly polished tool steel die (D2 grade) that had a micro-finish. The combination of the slick PVC surface and the ultra-smooth die eliminated the pressure marks and allowed them to increase their production speed, as the material flowed more easily into the die.
Tertiary Solution: Enhanced Handling and Workshop Discipline
The final, yet essential, piece of the puzzle is establishing a culture of careful material handling and workshop discipline. This human element can undermine even the best material and machinery solutions if not properly managed. This involves both formal training and creating a workshop environment that is conducive to quality.
This includes implementing clear protocols for storage, such as using proper dunnage and never stacking unprotected sheets directly on top of one another. It means designating "clean zones" for high-finish materials, away from grinding or welding sparks. It also involves training personnel on how to lift and move sheets correctly—lifting, not dragging—and ensuring they don't place tools, parts, or other objects on the valuable surfaces.
To support our clients, MFY often provides handling guidelines with our coated coil shipments. We saw a powerful example of this with a distributor in Southeast Asia. They were experiencing damage during the de-crating and warehousing process. We worked with them to implement a simple color-coded system: red zones on the floor where no material could be placed, and a strict "tools-on-bench" policy. Combined with training on how to handle the PVC-coated sheets, their internal damage rate dropped by over 75%. This demonstrates that technology and process must be supported by people to achieve a zero-defect goal.
Solution Tier | Description | Key Actions | Impact |
---|---|---|---|
Primary | Using factory-applied PVC-coated coils. | Procure coils with the protective film already applied. | Prevents 90%+ of all surface scratches throughout fabrication. |
Secondary | Optimizing machinery and tooling. | Regular cleaning, alignment, use of non-marring tools. | Reduces stress on material and film, prevents severe defects. |
Tertiary | Improving handling and workshop culture. | Training, designated clean zones, proper storage protocols. | Eliminates random damage from human error and environment. |
What are the best practices for using PVC coating in scratch-free coil fabrication?
You've made the smart choice to use PVC-coated stainless steel. But are you maximizing its potential? To truly guarantee a scratch-free result, you need to follow a few key best practices for handling, processing, and removing the film. This ensures the coating does its job perfectly.
Best practices for using PVC coating include selecting the correct film type and thickness for your process, ensuring it's compatible with laser cutting or forming applications, processing within the film's shelf life, and peeling it off correctly at a low angle post-fabrication.
Think of the PVC film as a critical tool, not just a wrapper. Its performance depends on using it correctly. The first step is selecting the right film for the job. A heavy-duty forming process requires a thicker, more robust film than a simple laser-cutting application. At MFY, we consult with clients to match the PVC specification to their specific fabrication needs. For example, a client doing deep drawing needs a high-adhesion, highly ductile 80-100 micron film, whereas a client doing only laser cutting might use a 50-micron film. Following this, proper storage away from direct UV light is crucial to prevent the adhesive from hardening. Lastly, the "grand reveal"—removing the film—should be done smoothly and at an angle to avoid leaving adhesive residue. Proper removal technique10 ensures the PVC coating delivers on its promise of a perfect finish.
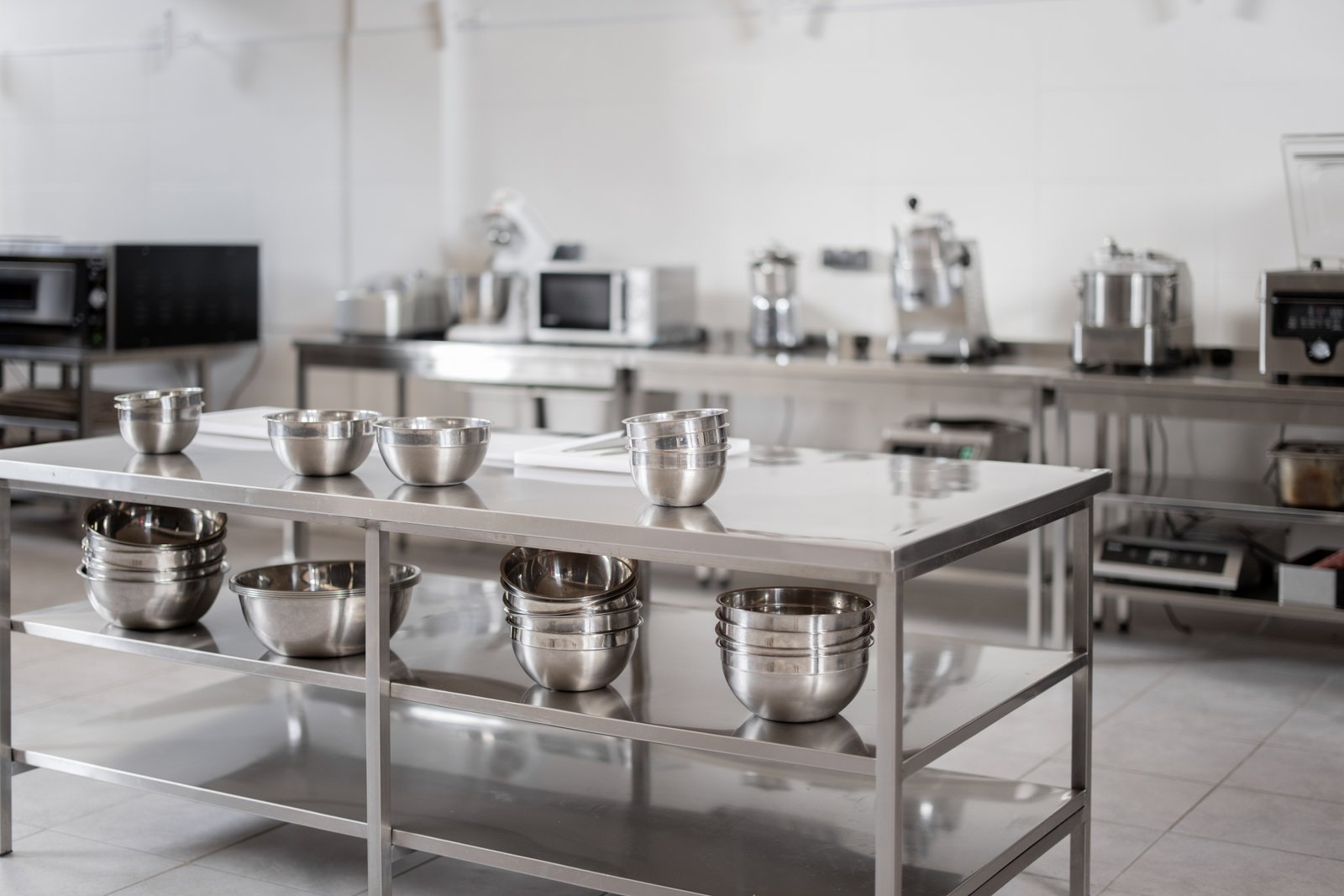
Adopting PVC-coated coils is the most significant step toward scratch-free fabrication, but refining your technique unlocks its full potential. By treating the protective film with the same care and precision as the steel itself, you can create an infallible system. This involves a deeper look into the lifecycle of the film, from selection before it even reaches your factory to its final removal, ensuring every stage is optimized for success.
Selecting the Appropriate PVC Film Specification
Not all PVC films are created equal. The most critical best practice begins before the coil even arrives at your facility: selecting the right type of film for your specific application. The choice depends on the severity of the fabrication processes the coil will undergo. Key parameters to consider are film thickness (measured in microns), adhesive strength, and film color.
For light-duty processes like laser cutting or simple bending, a standard 40-60 micron film is often sufficient. However, for more demanding applications like deep drawing, roll forming, or heavy stamping, a thicker film of 80-120 microns is necessary to withstand the extreme pressure and friction without tearing. The adhesive strength is also crucial. It must be strong enough to stay in place during fabrication but not so strong that it becomes difficult to remove or leaves residue. We worked with a client who was having issues with film tearing during a roll-forming process. They were using a standard 50-micron film. We recommended they switch to an 80-micron, high-tack film designed for forming. This simple change completely resolved the issue and eliminated the defects.
Furthermore, some PVC films are specifically designed for fiber laser cutting11, featuring properties that minimize melting or bubbling around the cut edge. At MFY, we offer a range of film options and provide expert consultation to ensure our clients receive a product that is perfectly tailored to their production line, preventing problems before they can start.
Proper Handling, Storage, and Processing
Once the correctly specified coil arrives, its protective film must be treated with care. While durable, the PVC film has its own vulnerabilities. The most significant environmental threat is prolonged exposure to direct sunlight or UV radiation. UV rays can degrade the plasticizers in the film and cure the adhesive, making the film brittle and causing it to bond permanently to the steel surface. This can turn removal from a simple peel into an impossible task that damages the underlying surface. Therefore, coated coils should always be stored indoors, away from windows.
The shelf life of the adhesive is also a factor. Most films are designed to be removed within 3-6 months of application. Using coils that have been in storage for too long can lead to removal issues. We advise clients to follow a "First-In, First-Out" (FIFO) inventory system to ensure they are always processing material that is well within its recommended shelf life.
During processing, it's important to be mindful of heat. While the film can withstand the instantaneous heat of a laser, prolonged exposure to high temperatures, such as in a baking or curing cycle for paint, should be avoided unless the film is specifically rated for high temperatures. If such processes are necessary, the film should be removed beforehand.
The Art of Film Removal
The final step is perhaps the most satisfying: peeling back the film to reveal the flawless stainless steel surface. However, even this step has a best practice. Ripping the film off quickly or at a 90-degree angle can increase the likelihood of "adhesive transfer," where small amounts of glue are left behind on the steel. This residue is difficult to clean and can mar the final appearance.
The recommended technique is to start at a corner and peel the film back on itself, maintaining a low angle (less than 45 degrees). Pull steadily and smoothly, rather than in short, sharp jerks. This technique minimizes the stress on the adhesive bond and promotes a clean release. The ideal temperature for removal is room temperature (around 15-25°C). Trying to remove the film when the material is very cold can make the adhesive more brittle, while removing it when very hot can make the adhesive gummy.
A client manufacturing stainless steel balustrades scheduled the film removal as the very last step after the entire structure was installed on-site. This protected the components during transport and installation. Their teams were trained to use this low-angle peeling technique, ensuring a perfect, residue-free finish and a very happy end customer. This final touchpoint of care guarantees that all the preceding efforts result in the intended perfection.
Best Practice | Description | Why It's Important |
---|---|---|
Film Selection | Choose film thickness and adhesive based on the fabrication process. | Prevents film tearing during severe forming and ensures it stays put. |
Proper Storage | Store coils indoors, away from direct UV/sunlight. | Prevents adhesive from curing, which makes removal difficult or impossible. |
FIFO Inventory | Use coils within their 3-6 month shelf life. | Ensures the adhesive performs as designed for clean removal. |
Correct Removal | Peel film at a low, steady angle after fabrication is complete. | Minimizes the risk of leaving adhesive residue on the final product. |
Conclusion
Ultimately, scratches are a preventable threat in stainless steel fabrication. Embracing PVC-coated coils is not an extra expense but a strategic investment in quality, efficiency, and brand integrity. It’s the most reliable way to deliver a flawless product from our factory to your end customer.
-
Get a detailed overview of the stages and risks during stainless steel coil processing. ↩
-
Verify industry data and gain insight into defect-related waste in stainless steel manufacturing. ↩
-
Understand how automation can both help and harm stainless steel surface integrity and how to manage. ↩
-
Learn about finish types and which are most vulnerable to scratches during handling or processing. ↩
-
See real-world examples and best practices regarding equipment maintenance and surface protection. ↩
-
Understand the science of galling and strategies for its prevention in forming operations. ↩
-
Learn how the passive layer is critical for stainless steel's corrosion resistance. ↩
-
Understand the application, removal, and industry use cases for PVC-coated stainless coils ↩
-
Explore measures to optimize machines and tools for less material damage during production ↩
-
See step-by-step guidance for residue-free film removal after fabrication ↩
-
Discover specialized protective films that prevent melting or bubbling during laser cutting ↩
Have Questions or Need More Information?
Get in touch with us for personalized assistance and expert advice.