Mirror Finish Stainless Sheet: Polishing Steps + QC
Struggling to achieve that flawless, liquid-like mirror finish on stainless steel sheets? Imperfections are glaringly obvious on such a surface, leading to costly rejections and project delays. This comprehensive guide breaks down the essential polishing steps and quality control measures, helping you master this demanding yet rewarding finish.
Achieving a No. 8 mirror finish on stainless steel sheets involves a meticulous, multi-stage grinding and polishing process using progressively finer abrasives and specialized compounds. Stringent quality control at each step is crucial to ensure a defect-free, highly reflective, and uniform surface.
The allure of a mirror finish stainless steel is undeniable, often chosen to impart a sense of luxury, precision, and high quality in architectural designs, upscale appliances, and sanitary applications. As Global Business Director at MFY, I’ve seen our MFY 304 and 316L sheets1 transformed into stunning reflective surfaces by skilled fabricators. This journey from a standard sheet to a flawless reflection is both an art demanding patience and a science requiring meticulous process control.
A true No. 8 mirror finish, as defined by standards like ASTM A480/A480M, is more than just "shiny." It signifies a highly reflective, non-directional surface, free of scratches, haze, cloudiness, or any visual distortion, akin to a high-quality glass mirror. This premium finish often commands a significant price uplift, sometimes 50-100% or more compared to a standard 2B or even a BA (Bright Annealed) finish, due to the intensive labor and material removal involved – potentially 0.05mm to 0.1mm of the surface. For instance, high-end architectural firms in Dubai, regular clients of MFY, specify our prime quality 316L sheets for producing mirror-finished facade elements on prestigious towers, where aesthetic perfection is paramount. Achieving this requires not only skill but also starting with impeccable base material, as research from material science institutes consistently shows a direct correlation between substrate quality and the final mirror polish outcome. The slightest imperfection in the base material can become a glaring flaw once magnified by the polishing process.
What are the initial preparations for polishing mirror finish stainless sheets?
Ever dived into polishing, only to find stubborn scratches or embedded contaminants ruining your mirror finish? This common frustration wastes time, valuable materials, and significant effort. Proper groundwork is non-negotiable for achieving that perfect, defect-free shine and meeting client expectations for a premium product.
Initial preparations for polishing mirror finish stainless sheets critically involve selecting high-quality, defect-free base material (typically a No. 2B or BA finish), followed by thorough degreasing and cleaning to remove all surface contaminants, and a meticulous inspection for any pre-existing imperfections.
The old adage "fail to prepare, prepare to fail" is exceptionally true when aiming for the pristine surface of a mirror finish on stainless steel. At MFY, when we supply our MFY 304 or 316L BA (Bright Annealed) sheets – often the preferred starting point due to their inherently smoother, cleaner surface (typically with an Ra value < 0.1 µm) compared to a standard 2B finish – to specialized polishing houses or high-end fabricators, we consistently emphasize the paramount importance of this initial phase. I recall a client, a manufacturer of luxury yacht fittings in Southeast Asia, who initially struggled with "comet tails" (streaks emanating from a point defect) and persistent fine scratches in their mirror-polished components. The investigation revealed the root cause wasn't their polishing technique itself, but inadequate initial cleaning and inspection of incoming sheets sourced from a previous, less reliable supplier. They were inadvertently trying to polish over microscopic contaminants and subtle surface imperfections that then became glaringly magnified under the intense scrutiny of a mirror polish. After switching to our MFY BA finish sheets, which undergo stringent surface quality checks at our facilities, and implementing a more rigorous pre-cleaning protocol (including ultrasonic cleaning for smaller parts), their rework rate plummeted from nearly 18% down to below 3%. This experience vividly illustrates that the foundation laid during preparation directly dictates the final quality. It's not merely about surface cleaning; it's about meticulously creating a flawless canvas before the first abrasive even touches the steel.
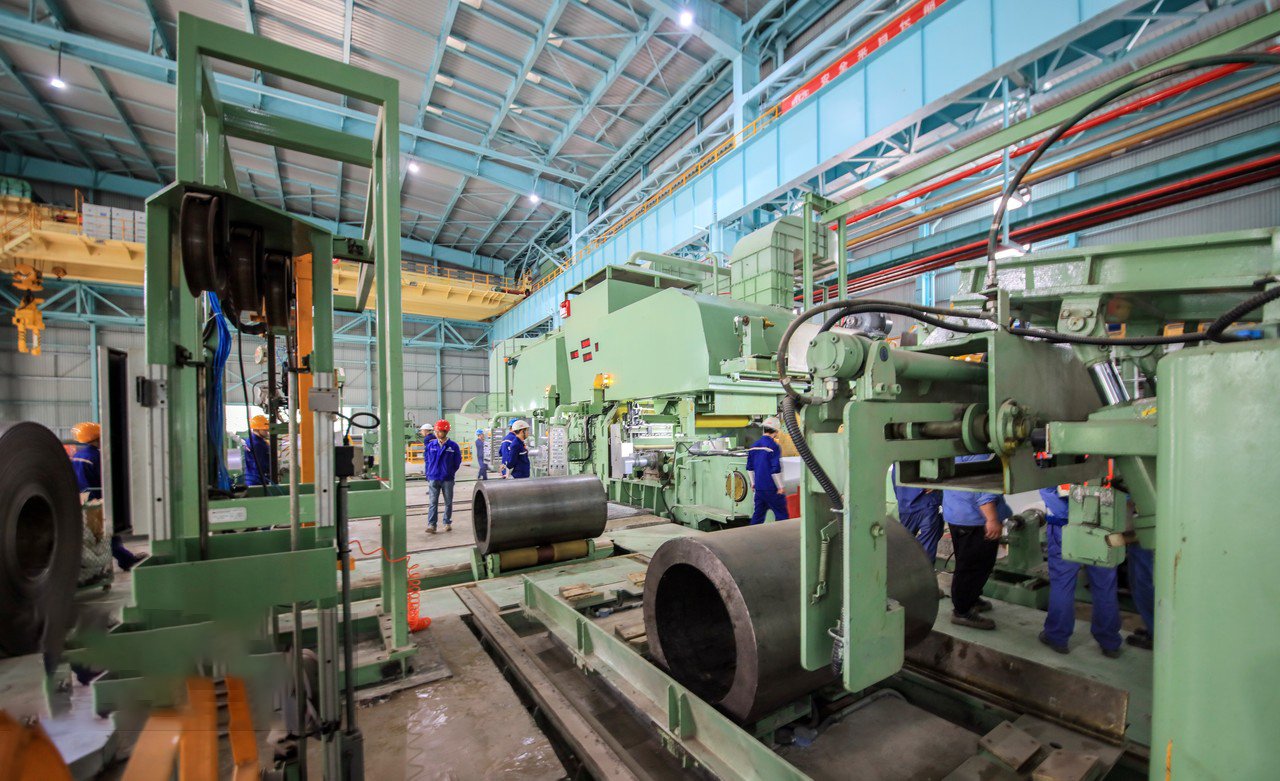
Selecting the Ideal Base Material: The Foundation of a Flawless Mirror
The journey to a perfect No. 8 mirror finish begins with the uncompromising selection of the base stainless steel sheet. While it's possible to achieve a mirror finish from a standard No. 2B cold-rolled sheet, starting with a Bright Annealed (BA) finish is often preferred by professionals. A BA finish, produced by annealing in a controlled, oxygen-free atmosphere, results in a smoother, brighter, and more reflective surface with a typical surface roughness (Ra) value often below 0.1 micrometers (µm). This means less aggressive initial grinding is required, saving time, labor, and consumables, and reducing the risk of introducing deeper scratches that are hard to remove later. At MFY, our BA finish 304 and 316L sheets are specifically processed to provide an excellent starting point for such critical applications, ensuring minimal inherent surface defects. We aim for Ra values on our BA sheets that are consistently in the 0.05-0.08 µm range.
The grade of stainless steel also plays a role. Austenitic stainless steels like Type 304 (UNS S30400) and Type 316L (UNS S31603) are commonly used for mirror polishing due to their good formability and corrosion resistance. Type 316L, with its added molybdenum content, offers superior corrosion resistance, making it ideal for marine environments or applications involving corrosive chemicals, which is why our yacht-fitting client uses MFY 316L BA sheets. Beyond the grade, the specific chemical composition, particularly sulfur content, can impact polishability. Low-sulfur grades (typically <0.005% S) are known to yield better results, as sulfur inclusions can cause "stringers" or pitting during polishing. MFY maintains strict control over the chemistry of the raw materials we use in our production, ensuring our "polish-ready" grades meet these tighter compositional requirements, leading to a more consistent and defect-free polishing experience for our clients.
Most importantly, the initial surface quality of the sheet must be as close to perfect as possible. It must be free from visible scratches, pits, roll marks, embedded scale, "orange peel" texture, or any other defects originating from the steel mill or subsequent handling. Any such imperfection, if not entirely removed during the initial, most aggressive grinding stages, will become highly visible and often magnified by the mirror polishing process. This means that opting for a slightly cheaper, lower-quality base sheet can be a false economy, as the additional labor, time (potentially adding hours per sheet for defect removal), and consumables required to rectify these initial flaws can far outweigh the initial savings. I’ve consulted with a fabricator client in India, producing high-end retail displays, who switched from a generic 2B sheet to our MFY "Prime BA" sheets. They reported a 20% reduction in overall polishing time and a 10% decrease in rejection rates, directly attributing this to the superior starting surface of our material. This illustrates that investing in a higher-quality base material is a critical first step.
Meticulous Surface Cleaning and Degreasing: Creating a Pristine Canvas
Once a suitable base sheet is selected, the next crucial preparatory step is meticulous surface cleaning and degreasing. Any contaminants left on the surface – such as oils, grease from handling or previous processing, shop dirt, adhesive residues from protective films, fingerprints, or even microscopic iron particles from nearby carbon steel work – will interfere with the polishing process. These contaminants can clog abrasive belts or pads, cause uneven polishing, create unsightly smears or stains, or become embedded into the surface, leading to defects like "comet tails" or localized corrosion initiation points later on. For instance, a patch of residual grease can prevent the abrasives from uniformly cutting the surface, resulting in a dull or uneven spot that is very difficult to correct without re-polishing the entire area.
Several cleaning methods can be employed, and the choice depends on the type and extent of contamination. Solvent cleaning using appropriate organic solvents like acetone, isopropyl alcohol (IPA), or specialized stainless steel cleaners is common for removing oils, grease, and some adhesive residues. It's vital to ensure the chosen solvent is compatible with stainless steel and does not leave any residue itself. Safety precautions, including adequate ventilation and use of personal protective equipment (PPE), are paramount when handling solvents. For more stubborn or widespread contamination, alkaline cleaning, often involving immersion in heated (e.g., 60-80°C) solutions of alkaline detergents (e.g., sodium hydroxide based formulations) for 5-15 minutes, can be very effective. This is followed by thorough rinsing with clean water. At MFY, we often advise clients to use deionized (DI) water for the final rinse, especially for high-purity applications, to prevent water spots caused by dissolved minerals. Emulsion cleaners, which combine solvent and detergent properties, can also be used. Whatever method is chosen, the goal is a chemically clean surface.
After cleaning and rinsing, the stainless steel sheets must be thoroughly dried before any polishing begins. Residual moisture can cause water spots, interfere with oil-based polishing compounds, or even promote localized corrosion if left for extended periods. Effective drying methods include using clean, dry compressed air (passed through oil and water filters), wiping with new, lint-free cloths (microfiber cloths are excellent), or using warm air ovens. If warm air ovens are used, the temperature should be kept relatively low (e.g., below 70°C) to avoid any potential distortion of the sheet, especially for thinner gauges. I remember a case with an architectural fabricator client in the Middle East who was experiencing faint, almost invisible streaking on their large mirror-polished panels. The issue was eventually traced back to insufficient drying after cleaning, where trace amounts of residual moisture were interacting with the initial polishing compounds. Implementing a more rigorous drying step, verified by ensuring no visible moisture or condensation, completely resolved their problem.
Thorough Inspection and Pre-emptive Defect Rectification: Addressing Issues Early
Before commencing the actual polishing sequence, a final, thorough inspection of the cleaned and dried stainless steel sheet is indispensable. This inspection should be conducted under strong, angled lighting (e.g., >1000 lux) which helps to reveal subtle surface defects that might not be visible under diffuse ambient light. Using magnification, such as a 5x or 10x loupe, can also be beneficial for examining suspicious areas. It's important to inspect the entire surface systematically, paying attention to both sides if both are to be polished, and also checking for overall flatness, as significant waviness or distortion can lead to uneven polishing, particularly on large sheets where consistent pressure from polishing heads can be challenging to maintain. At MFY, our internal QA for sheets destined for polishing clients includes such detailed surface checks.
This inspection aims to identify any common pre-existing defects that may have been missed earlier or were inherent in the sheet. These can include deeper scratches that are beyond what the initial coarse grinding stage of polishing can easily remove, small dents or dings from handling, isolated pits (which could be signs of minor prior corrosion or material inclusions), or embedded particles. The inspector needs to differentiate between superficial blemishes that will be removed in the first polishing step and more significant flaws that require pre-emptive action. For example, a light surface scuff might be acceptable, but a scratch that can be felt with a fingernail (typically >0.025mm deep) will likely persist through several polishing stages unless specifically addressed. This is why our "Prime BA" sheets supplied by MFY undergo an additional level of visual scrutiny before being designated as "polish-ready," often involving comparison against calibrated defect limit samples.
If minor, isolated defects are found, a decision must be made whether to rectify them locally before starting the overall polishing sequence or to reject the sheet if the defects are too severe or widespread. Localized rectification might involve carefully using finer grit abrasive tools (e.g., a small orbital sander with a 120 or 180 grit disc, or even hand sanding with appropriate abrasive paper) on the specific spot to blend it out. However, this must be done with extreme care, as over-grinding can create a "dished" area or a localized pattern that will be difficult to blend with the rest of the polished surface. The cost-benefit of rectification versus rejection is a key consideration. A client of ours, an equipment integrator for the pharmaceutical industry in Europe, has a strict protocol: any scratch deeper than 0.05mm on a sheet designated for a product-contact surface results in rejection of that sheet for that specific application, as the risk of a lingering crevice is unacceptable. Industry data suggests that attempting to polish out deep pre-existing defects (e.g., >0.1mm) can increase polishing time for that specific sheet by 30-50%, often making it uneconomical.
Preparation Stage | Key Action | MFY Recommendation / Product Link | Potential Issue if Skipped |
---|---|---|---|
Base Material Selection | Choose high-quality BA or defect-free 2B finish; check grade & composition. | MFY Prime 304/316L BA sheets with controlled low sulfur content. | Longer polishing time, more defects, inconsistent final finish. |
Surface Cleaning | Degrease thoroughly using appropriate solvents or alkaline cleaners. | Consult MFY for compatible cleaning agents; ensure full residue removal. | Clogged abrasives, uneven polish, embedded contaminants, "comet tails". |
Rinsing & Drying | Rinse with clean (ideally DI) water; dry completely with lint-free methods. | Use filtered air or clean microfiber cloths. Avoid water spots. | Streaking, water spots, interference with polishing compounds. |
Final Inspection | Inspect under strong, angled light for scratches, dents, pits, waviness. | Establish clear acceptance criteria; use magnification. | Polishing over existing defects, leading to magnified flaws. |
Defect Rectification | Address minor, isolated defects locally with care, or reject sheet if severe. | Consult MFY on repairability; avoid creating new issues like "dishing". | Persistent defects in final mirror finish, high rework/rejection rates. |
BA finish is better than 2B for mirror polishingTrue
Bright Annealed (BA) finish has smoother surface (Ra <0.1µm) than standard 2B finish, requiring less initial grinding and reducing defect risks.
Any solvent can clean stainless steelFalse
Only compatible solvents (like acetone or IPA) should be used - some may leave residues or damage the surface, compromising polish quality.
How to apply polishing compounds for optimal shine?
Are your polishing efforts falling short of that brilliant, deep mirror shine? The secret often lies in the selection and application of polishing compounds. Using the wrong type or an improper technique can lead to a hazy, swirled finish, or even damage the surface.
For optimal shine, select polishing compounds appropriate for each stage, from cutting to final coloring. Apply them sparingly to the buffing wheel or surface, ensuring even distribution to prevent buildup, overheating, and to achieve a consistent, high-gloss mirror finish on stainless steel.
Once your stainless steel sheet is impeccably prepared, the next critical phase is the selection and masterful application of polishing compounds. This is where the true artistry and science of mirror finishing converge to coax out that breathtaking, liquid-metal reflectivity. At MFY, while we supply the foundational high-quality stainless steel sheets like our MFY 304 BA, we also work closely with clients, such as manufacturers of high-end architectural fixtures in Russia or producers of luxury automotive trim in Southeast Asia, who have honed their polishing processes to perfection. I've seen how the subtle differences in compound choice – solid bar versus liquid, grease-based versus greaseless, specific abrasive types like alumina or chromium oxide – and application technique can make the difference between a merely shiny surface and a truly flawless, deep mirror. For instance, one client producing custom stainless steel sculptures initially struggled with a slight haze on their final polish. The solution involved switching to a finer final coloring compound with a different lubricant system and adjusting the amount applied to their soft cotton mops. This seemingly small change elevated their work to a new level of brilliance, significantly enhancing the perceived value of their pieces. Understanding the nuances of these compounds is key to unlocking the ultimate shine.
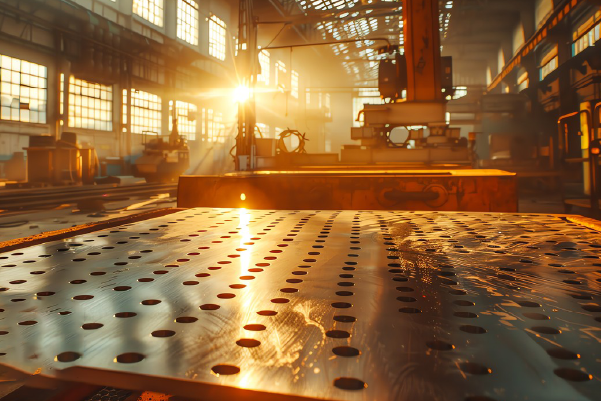
Understanding Polishing Compound Types and Their Roles
The journey to a mirror finish involves a sequence of polishing stages, each requiring a specific type of polishing compound paired with an appropriate buffing wheel. These compounds consist of abrasive powders (like aluminum oxide, silicon carbide, chromium oxide, or jeweler's rouge/iron oxide) suspended in a binder, typically a grease or wax base for bar compounds, or a liquid carrier for liquid compounds. The "cut" refers to the aggressiveness of the compound in removing material, while the "color" or "finish" refers to its ability to produce shine and reflectivity. Generally, you start with coarser "cutting" compounds to remove scratches from previous abrasive steps and level the surface, then progress to finer "coloring" or "finishing" compounds to achieve high gloss.
For stainless steel, a typical progression might involve:
- Cutting Compounds (Coarse to Medium): These are used after initial grinding (e.g., with abrasive belts down to 320 or 400 grit). They contain coarser abrasives like emery or tripoli (for softer metals, but sometimes used in initial stages on stainless) or more commonly, aggressive grades of aluminum oxide. Their primary role is to remove the grinding lines and achieve a uniform, smooth, but still dull or satin surface. For example, a sisal buffing wheel paired with a grey or black cutting compound (often containing ~100-180 grit equivalent abrasives) would be a common first step after abrasive belt sanding.
- Intermediate Polishing Compounds (Medium to Fine): These bridge the gap between heavy cutting and final finishing. They use finer aluminum oxide abrasives and are often applied with treated cotton or spiral-sewn cotton buffing wheels. The goal is to refine the surface further, remove any marks from the cutting stage, and start developing a higher luster. A typical compound might be a "brown tripoli" (though less common for stainless) or a white/green compound specifically designed for stainless steel, often with ~240-320 grit equivalent abrasives.
- Finishing/Coloring Compounds (Fine to Ultra-Fine): These are crucial for achieving the final mirror shine. They contain very fine abrasives, such as green chromium oxide (Cr₂O₃, renowned for its excellent coloring properties on stainless steel) or fine grades of calcined alumina. These are typically applied with soft, loose cotton mops, flannel buffs, or microfiber wheels. The objective here is minimal material removal and maximum surface smoothing to create high reflectivity. Jeweler's rouge (iron oxide, Fe₂O₃), while excellent for precious metals, is sometimes used as a final step on stainless for an ultra-high gloss, though green chromium oxide is generally preferred. At MFY, we've seen clients who specialize in mirror-finishing our MFY 316L sheets for marine hardware achieve exceptional results using a two-stage finishing process2: first with green chromium oxide, then a final pass with an even finer proprietary white coloring compound.
Understanding the binder is also important. Grease-based compounds adhere well to the buff and provide lubrication, which helps prevent overheating and dragging. Greaseless compounds are essentially dry abrasives with a glue binder, applied to the buff and allowed to dry, creating an abrasive "head" – these are more akin to flexible grinding wheels. Liquid compounds, often used in automated polishing systems for consistency and ease of application, can offer better control over the amount applied and can be formulated for specific cutting or coloring actions. The choice between bar and liquid often depends on the scale of operation and equipment. For instance, a small custom fabrication shop might prefer bars for their versatility, while a high-volume manufacturer of, say, stainless steel sinks (though usually not full mirror) might use automated liquid compound applicators.
Best Practices for Applying Compounds to Buffing Wheels
The technique used to apply polishing compound to the buffing wheel is critical for achieving optimal results and ensuring the longevity of both the compound and the wheel. Applying too much compound is a common mistake; it doesn't improve the finish but rather wastes material, can cause the workpiece to overheat, lead to excessive residue buildup (which is hard to clean), and can even create a "muddy" or hazy finish. Applying too little compound means the buff is essentially running dry, leading to poor cutting/coloring action, potential burnishing, and increased wear on the buff.
For bar compounds, the compound should be applied to the rotating buffing wheel sparingly and for only a few seconds at a time (e.g., 2-3 seconds). The friction between the bar and the moving wheel will melt a small amount of the wax/grease binder, transferring the abrasive to the wheel's surface. A properly "headed" or "charged" buff will have a light, even coating of compound. You should be able to see the fibers of the buff through the compound layer. It's better to apply small amounts more frequently than a large amount infrequently. When I visited a client in India who manufactures high-quality stainless steel cookware, their experienced polishers demonstrated this art: a quick touch of the bar to the spinning mop every few minutes was all that was needed to maintain a perfect cutting action.
The speed of the buffing wheel (Surface Feet Per Minute - SFPM) is also a crucial parameter. Different compounds and buff types have optimal SFPM ranges. For stainless steel, typical speeds range from 5,000 to 7,500 SFPM (e.g., a 10-inch diameter buff running at 1900-2800 RPM). Running too fast can burn the compound or the workpiece; running too slow reduces efficiency. The direction of buff rotation is also important – it should generally run off an edge rather than into it to prevent snagging. For liquid compounds, automated spray systems are often used, which can be precisely calibrated to deliver the optimal amount of compound at the right intervals, ensuring consistency, especially in large-scale production by clients like our automotive parts manufacturers.
Ensuring Even Distribution and Avoiding Common Pitfalls
Achieving an even distribution of the polishing compound on the workpiece itself, via the buff, is key to a uniform finish. This requires consistent pressure, movement, and overlap as the operator moves the workpiece across the buffing wheel (or moves the buff across a stationary workpiece). Uneven pressure can lead to high and low spots, or areas that are more polished than others. The operator should use smooth, overlapping strokes, working systematically across the entire surface. For large sheets, this often involves multiple passes in different directions (e.g., first pass north-south, second pass east-west) to ensure all areas are equally worked and to help eliminate any directional lines from previous steps.
Common pitfalls to avoid include:
- Overheating: Stainless steel has relatively low thermal conductivity, meaning heat can build up quickly during polishing. Overheating can cause discoloration ("heat tint" or "blueing"), warping (especially on thinner sheets), and can even alter the metallurgical properties of the surface layer. Using appropriate lubrication (from the compound itself), not dwelling too long in one spot, and using correct buff speeds and pressures are essential. Some operations use air cooling jets directed at the contact point.
- Contamination: Using the same buffing wheel for different compounds (especially moving from a coarser to a finer compound without thorough cleaning or "raking" the buff) is a recipe for disaster, as coarser abrasive particles will get trapped and cause scratches. Each compound should ideally have its own dedicated buff. Similarly, keeping the work area scrupulously clean to prevent airborne dust or grit from settling on the workpiece or buff is vital.
- Excessive Pressure: Applying too much pressure does not speed up the polishing process effectively and can lead to overheating, excessive compound consumption, rapid buff wear, and can even "drag" or "smear" the surface instead of cutting or coloring it cleanly. Light to moderate pressure is generally best, letting the compound and the buff do the work. The goal is to "flow" the surface material at a microscopic level, especially in the final coloring stages.
- Skipping Grits/Compounds: Each step in the abrasive/compound sequence is designed to remove the scratches from the previous step. Attempting to jump from a very coarse grit directly to a fine finishing compound will leave deep scratches visible in the final finish. A methodical progression is essential. For example, jumping from a 120-grit abrasive belt directly to a green chromium oxide finishing compound will not yield a mirror finish; intermediate steps with 240 grit, 320 grit, and possibly a finer intermediate compound would be necessary. This systematic approach is something we at MFY always reinforce when discussing finishing processes with our fabrication clients.
Chromium oxide creates mirror shineTrue
Green chromium oxide (Cr₂O₃) is specifically mentioned as the preferred ultra-fine abrasive for achieving high reflectivity on stainless steel during final polishing stages.
More compound equals better shineFalse
The text explicitly states that applying excessive compound causes overheating, residue buildup, and hazy finishes - the opposite of achieving optimal shine.
What techniques ensure uniformity in the polishing process?
Achieving a consistent, flawless mirror finish across an entire stainless steel sheet, especially large ones, can be incredibly challenging. Are you struggling with patchiness, uneven reflectivity, or visible transition lines? These issues can lead to rejected parts and significant rework, undermining your efforts.
Uniformity in mirror polishing stainless steel is ensured by consistent operator technique (pressure, speed, overlapping strokes), proper buffing wheel maintenance (dressing/raking), controlled compound application, optimal machine parameters (SFPM), and, for large surfaces, using automated or semi-automated polishing equipment.
Ensuring that every square inch of a stainless steel sheet reflects with the same flawless clarity is perhaps the ultimate test of a polisher's skill and process control. It's one thing to achieve a small patch of mirror finish, but quite another to scale that perfection across large architectural panels or critical-aesthetic components. As Global Business Director at MFY, I've seen the impressive results achieved by clients who have mastered this uniformity, such as an engineering firm in the Middle East that produces large, mirror-polished MFY 316L column claddings for luxury hotel lobbies where even the slightest inconsistency would be unacceptable. They achieve this not just through skilled artisans, but through rigorously standardized procedures, meticulous equipment maintenance, and sometimes, the strategic use of automation. I recall another client, a manufacturer of high-end catering equipment in Europe, who initially faced challenges with "cloudiness" and subtle variations in reflectivity on larger surfaces. By refining their buffing patterns, ensuring consistent wheel speeds across different machines, and implementing stricter compound management, they dramatically improved their product's visual appeal and reduced their internal rejection rate for aesthetic flaws by over 10%. This pursuit of uniformity is paramount for high-value applications.
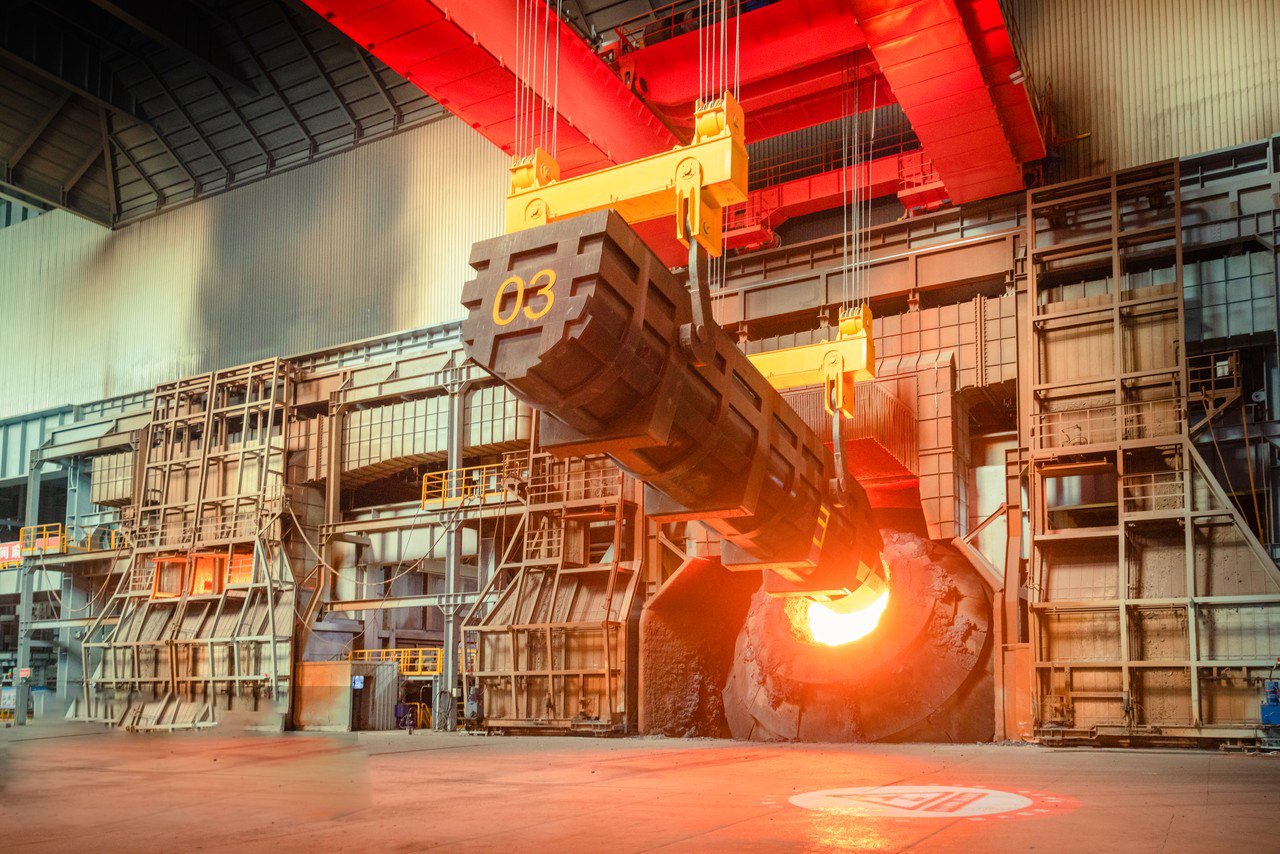
Mastering Operator Technique for Consistent Results
Even with the best materials and equipment, the skill and consistency of the operator are paramount in manual or semi-manual polishing operations, which are still common for custom or complex shapes. Uniformity begins with consistent pressure application. The operator must learn to apply just the right amount of pressure between the workpiece and the buffing wheel, and maintain that pressure evenly across the entire surface. Too little pressure results in inefficient polishing and a lack of "cut" or "color," while too much can cause overheating, dragging, or gouging. This "feel" is often developed through extensive experience. Training programs for polishers often involve exercises to develop muscle memory for consistent pressure and movement, sometimes using pressure sensors on practice setups to provide feedback. For MFY clients who are setting up or refining their polishing departments, we sometimes connect them with experienced consultants or training providers.
Consistent speed and motion are equally critical. The operator should move the workpiece (or the polishing head) across the surface at a steady, controlled speed. Rushing or dwelling too long in one area will lead to uneven results. Smooth, overlapping strokes are essential to avoid visible lines or patches. A common technique is to use a "cross-hatch" pattern, where successive passes are made at approximately 90 degrees to each other (or 45 degrees for more complex blending). This helps to ensure that all areas are worked equally and helps to eliminate any directional lines left from previous polishing stages. For example, if the previous abrasive belt sanding was done north-south, the first buffing stage might be done east-west, followed by a diagonal pass. The amount of overlap between strokes (typically 25-50% of the buff width) must also be consistent. Some of our most successful clients, like a manufacturer of bespoke stainless steel furniture in India, have developed highly detailed work instructions and visual aids for their polishing staff, specifying stroke patterns and speeds for different component types.
Furthermore, operator ergonomics and fatigue management play a subtle but important role in maintaining consistency, especially during long shifts. A well-designed workstation, proper lighting (non-glare, but bright enough to see the surface detail), and regular breaks can help operators maintain the high level of concentration and physical control needed for uniform polishing. Some companies implement job rotation to prevent repetitive strain and maintain operator alertness. This focus on the human element is crucial because any lapse in consistency, even for a moment, can mar a large, expensive sheet of mirror-polished stainless steel, potentially requiring hours of rework.
The Role of Buffing Wheel Maintenance and Selection
The condition of the buffing wheel (or "mop") is a major factor in achieving a uniform finish. Proper buffing wheel maintenance, including regular "dressing" or "raking," is essential. Over time, the buffing wheel can become loaded with old compound, metallic fines, and worn abrasive particles. This buildup, known as "glazing" or "loading," reduces the buff's cutting efficiency and can cause scratches or a smeared, uneven finish. A buff rake (a tool with sharp, hardened steel teeth) is used to remove this loaded layer from the face of the rotating buff, exposing fresh, clean fibers and restoring its cutting/coloring ability. Raking should be done frequently, sometimes every few minutes of use, depending on the type of compound and the material being polished. A clean, well-dressed buff will accept fresh compound more effectively and deliver a more consistent finish.
The selection of the right buffing wheel for each stage is also critical for uniformity. Buffs come in various materials (sisal, treated cotton, standard cotton, flannel, microfiber), constructions (spiral sewn, bias cut, loose, pleated), and densities.
- Sisal buffs: Made from stiff natural fibers, these are aggressive and used with cutting compounds for initial surface leveling and removing deeper scratches (e.g., from 180-240 grit sanding).
- Treated cotton buffs (e.g., mill-treated): These are stiffer than untreated cotton and offer a good cut with less fraying. Used with cutting or intermediate compounds.
- Spiral sewn cotton buffs: Multiple layers of cotton cloth sewn together in a spiral pattern. These are general-purpose buffs, offering a good balance of cutting ability and flexibility. Used with medium cutting to initial coloring compounds. The closer the sewing, the harder the buff and the more cut it provides.
- Loose cotton buffs (or "color mops"): Made from layers of cotton discs only sewn together at the center. They are very soft and flexible, ideal for final coloring operations with fine compounds like green chromium oxide, as they conform well to surfaces and produce a high gloss with minimal pressure.
- Bias cut buffs: Constructed from cotton material cut at a 45-degree angle to the weave. This design allows for better flexibility, cooler running, and longer life. They often have a steel center and can be pleated for even better cooling. These are versatile for both cutting and coloring.
Using a buff that is too hard for a finishing operation can leave fine scratches or a "streaky" appearance. Using a buff that is too soft for a cutting operation will be inefficient and wear out quickly. MFY often advises clients to consult with buff and compound manufacturers to select the optimal combination for their specific grade of stainless steel (e.g., 304 vs. 316L, which have slightly different hardness) and desired finish. Ensuring consistent buff diameter and density across all polishing stations performing the same step is also key for process uniformity.
Automation and Process Control for Scalability and Precision
For achieving high levels of uniformity, especially on large flat sheets or in high-volume production, automation or semi-automation plays an increasingly important role. Automated polishing machines, such as flatbed polishers with traversing heads or robotic polishing cells3, can provide a level of consistency in pressure, speed, and motion that is very difficult for even the most skilled human operator to replicate over extended periods or large surface areas. These machines can be programmed with specific polishing paths, head pressures, spindle speeds, and compound application rates. For instance, a client of MFY who manufactures large architectural panels (e.g., 2m x 4m) from our MFY 316L BA sheets uses a multi-head automated flatbed polisher. This machine has a series of polishing heads, each equipped with the appropriate buff and compound for a specific stage, moving systematically across the sheet. This ensures that every part of the sheet receives exactly the same treatment, resulting in exceptional uniformity of gloss and reflectivity (e.g., variations of less than ±5 GU across the entire surface).
Even in semi-automated setups, where an operator might guide a polishing head mounted on an articulated arm, process control parameters are critical. This includes:
- Consistent Spindle Speeds (RPM/SFPM): Ensuring that the RPM of the polishing lathes or machines is accurately set and maintained. Variations in RPM will directly affect the Surface Feet Per Minute (SFPM), which impacts the cutting/coloring action. Using tachometers to periodically verify spindle speeds is good practice.
- Controlled Compound Application: If using liquid compounds with spray systems, the nozzle type, spray duration, frequency, and pressure must be precisely controlled and regularly checked for consistency. For bar compounds, establishing standard operating procedures (SOPs) for how often and how much compound to apply is important.
- Environmental Controls: Maintaining a relatively stable ambient temperature and humidity in the polishing area can help ensure consistent compound performance and drying times. Good dust extraction systems are vital not only for operator health and safety but also to prevent airborne particles from contaminating the workpiece or buff and causing scratches, thus ensuring a more uniform surface.
- Workpiece Fixturing: For consistent results, especially with automated or semi-automated systems, the stainless steel sheet must be securely and flatly fixtured to prevent movement or vibration during polishing. Any chatter or vibration can translate into visible marks on the finished surface. Vacuum tables are often used for holding large sheets flat.
By implementing these techniques and controls, industries can significantly improve the uniformity of their mirror-polished stainless steel products, meeting the highest aesthetic standards demanded by clients for applications ranging from decorative architectural elements to precision optical components.
Operator technique affects finish uniformityTrue
Consistent pressure, speed, and overlapping strokes are crucial for achieving uniform mirror finishes on stainless steel.
Buffing wheels never need maintenanceFalse
Buffing wheels require regular dressing/raking to remove built-up compound and metal particles for consistent performance.
Which steps are crucial for conducting Quality Control checks?
Just completed polishing a stainless steel sheet to a mirror finish, but how can you be sure it meets the required standards? Skipping rigorous Quality Control can lead to shipping defective products, resulting in costly rejections, unhappy clients, and damage to your reputation.
Crucial QC steps for mirror finish stainless steel include meticulous visual inspection under specific lighting for defects (scratches, haze, distortion), quantitative measurement of gloss and reflectivity using calibrated instruments, and verification of surface cleanliness and uniformity against approved standards or samples.
After the intensive labor and meticulous care invested in polishing a stainless steel sheet to a No. 8 mirror finish, the final and arguably most critical stage is Quality Control (QC). This is where the product is rigorously evaluated to ensure it meets the exacting aesthetic and functional standards expected of such a premium finish. At MFY, we understand that our clients, whether they are architectural fabricators in Dubai specifying our MFY 316L sheets for a landmark project or manufacturers of luxury appliances in Europe, rely on flawless surface quality. A robust QC process is non-negotiable. I've seen situations where insufficient QC led to a shipment of mirror-polished components having subtle but unacceptable variations in reflectivity, causing significant delays and cost overruns for the end-user. For instance, a client producing high-end retail display cases found that inconsistent final inspection under variable lighting conditions led to customer complaints about "patchiness" that wasn't caught in their own facility. Implementing a standardized QC protocol, including defined lighting conditions and acceptance criteria based on master samples, helped them achieve over 99% acceptance rates from their discerning customers. Effective QC is the gatekeeper of quality, ensuring that only perfect products reach the market.
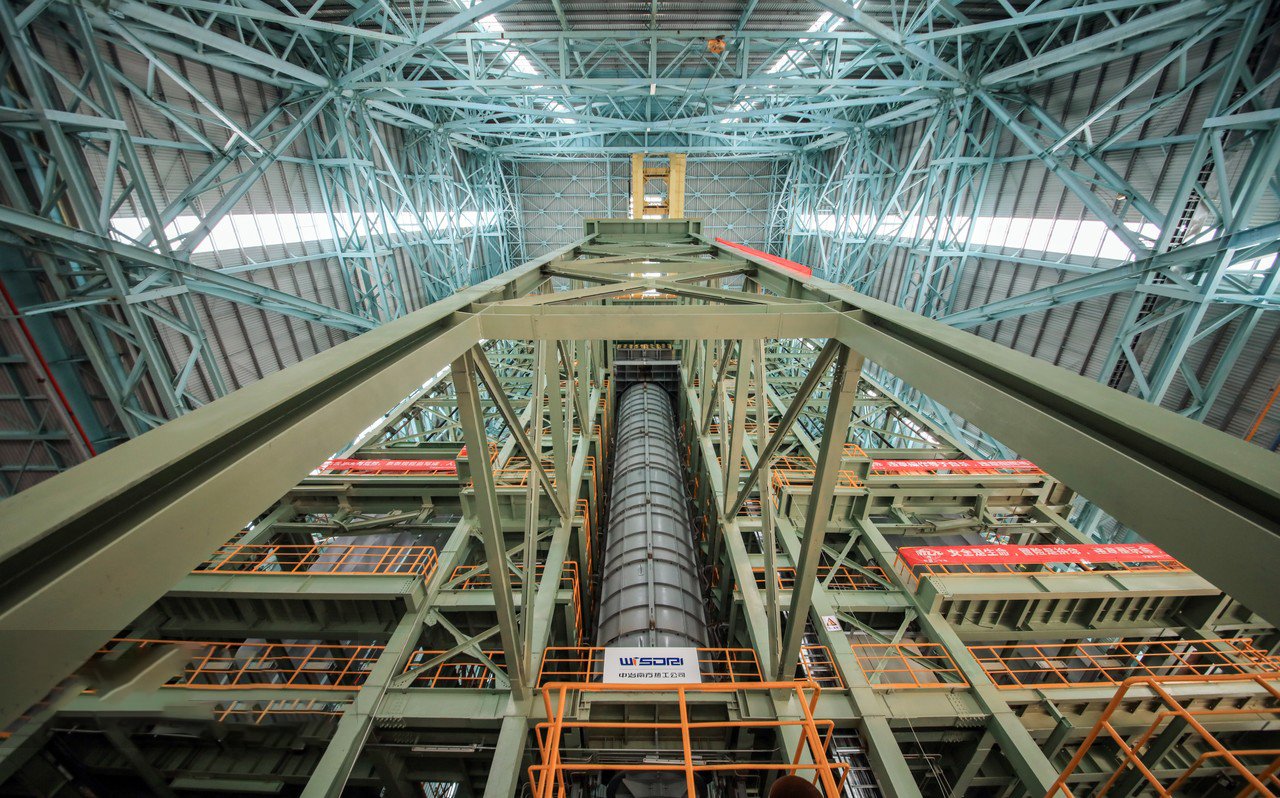
Establishing Comprehensive Visual Inspection Protocols
The cornerstone of QC for mirror-finished stainless steel is a comprehensive visual inspection protocol. While seemingly subjective, visual inspection by trained personnel is highly effective when standardized. This involves examining 100% of the polished surface under controlled lighting conditions.
- Lighting: The type and angle of lighting are critical. Diffuse overhead lighting alone is often insufficient. A combination of bright, directional lighting (e.g., from halogen or LED spotlights positioned at a low angle, typically 15-45 degrees to the surface) and diffuse lighting is recommended to reveal different types of defects. Some standards might specify illuminance levels (e.g., 1000-2000 lux at the inspection surface). The color temperature of the light (e.g., D65 daylight simulator) should also be consistent to ensure accurate color perception and detection of any subtle yellowing or blueing.
- Viewing Distance and Angle: Define the standard viewing distance (e.g., 0.5 to 1 meter) and angles from which the surface will be inspected. The inspector should examine the surface from multiple angles to catch defects that may only be visible from a specific perspective.
- Defect Classification: Develop a clear understanding and classification of potential defects. Common defects include:
- Scratches: Linear marks of varying depth and length. Note if they are isolated, clustered, or directional.
- Haze or Cloudiness: A milky or dull appearance, lacking sharp reflectivity.
- Orange Peel: A mottled or textured surface resembling the skin of an orange, often resulting from coarse grain structure or improper forming/polishing.
- Pinholes or Pits: Small depressions or voids in the surface.
- Buffing Lines or Swirl Marks: Fine circular or directional marks left by the buffing process.
- Distortion: Lack of flatness in the reflection, indicating the surface itself is not perfectly flat or has an uneven polish.
- Stains or Residue: Discoloration from leftover compound, cleaning agents, or fingerprints.
- Reference Standards: Use approved master samples or limit samples that represent the minimum acceptable quality and illustrate borderline or unacceptable defects. These provide a physical benchmark for inspectors, reducing subjectivity. MFY often provides such reference samples to clients purchasing our sheets for high-end polishing applications, ensuring alignment on quality expectations from the outset. For example, a "limit sample" might show the maximum allowable density of extremely fine pinprick haze permissible in a non-critical area.
Training inspectors is crucial. They need to understand the types of defects, their potential causes, and the acceptance criteria. Regular calibration meetings among inspectors can also help maintain consistency in their judgments. Documenting findings, often with photographs of any defects and mapping their location on the sheet, is essential for traceability and for providing feedback to the polishing department. Some companies use digital imaging systems to capture and analyze surface characteristics against a pre-defined standard.
Implementing Quantitative Measurements for Objectivity
While visual inspection is primary, quantitative measurements provide objective data to supplement and validate subjective assessments, especially for critical applications or when disputes arise.
- Gloss Measurement: A gloss meter measures the specular reflection of a surface. For mirror finishes, measurements are typically taken at 20 degrees (for high gloss surfaces >70 GU at 60 degrees) or 60 degrees (for medium gloss). ASTM D523 is a common standard for gloss measurement. The gloss meter should be regularly calibrated using traceable standards. Acceptance criteria for gloss units (GU) should be established (e.g., >800 GU at 20 degrees for a high-quality No. 8 mirror). Multiple readings should be taken across the sheet to check for uniformity. For instance, a quality-conscious client of MFY producing mirror-finish trim for luxury automobiles specifies a minimum gloss of 850 GU at 20 degrees, with a maximum variation of ±20 GU across any single component.
- Reflectivity Measurement: While related to gloss, reflectivity specifically measures the ratio of reflected light to incident light. Specialized instruments like reflectometers or spectrophotometers (which can also measure color) can provide this data. This is particularly important for applications where the optical performance is critical, such as solar reflectors or optical mirrors4, though less common for purely decorative mirror finishes.
- Surface Roughness (Ra): Although a No. 8 mirror finish is primarily defined by its visual appearance, a very low surface roughness (Ra value) is implicit. While not typically measured as a routine QC check on every mirror-polished sheet (as the profilometer stylus could scratch the surface), Ra measurements (e.g., using non-contact optical profilometers if available, or on sacrificial test coupons polished alongside the main batch) can be used during process development or for troubleshooting. A true No. 8 mirror finish should have an Ra value significantly below 0.05 µm, often in the range of 0.01-0.02 µm.
- DOI (Distinctness of Image) / Haze Measurement: More advanced instruments can measure DOI, which quantifies the sharpness of a reflected image, and haze, which quantifies the "milkiness" or scattering of light adjacent to the main reflected beam. ASTM D5767 (DOI) and ASTM D1003 (Haze) are relevant standards. These parameters are crucial for high-end automotive or optical applications where clarity of reflection is paramount. A high DOI value (e.g., >90) and low haze value (e.g., <10) indicate a superior mirror finish.
Using these instruments requires proper calibration, trained operators, and standardized measurement procedures. The data collected should be recorded and tracked over time to monitor process consistency and identify any drifts in quality. This data-driven approach allows for more objective decision-making and continuous improvement.
Final Cleanliness Checks and Protective Packaging Protocols
After passing visual and instrumental QC, the final steps involve ensuring the polished surface is scrupulously clean and then properly protected for handling, storage, and shipment.
- Final Cleaning: Any remaining polishing compound residue, fingerprints, or dust must be removed. This is often done using clean, soft, lint-free microfiber cloths and a high-quality stainless steel cleaner or a volatile solvent like isopropyl alcohol (IPA). The cleaning motion should be light and follow the (imperceptible) grain if any, or be in gentle circular motions. Ensure no streaks or residues are left behind. For critical applications, this final cleaning might be done in a controlled environment (e.g., a cleanroom or a designated clean area with filtered air) to prevent re-contamination.
- Inspection for Cleanliness: After cleaning, the surface should be inspected again under good lighting to confirm it's free of any smudges, smears, or residues. Sometimes, a "water break test" can be used on a test coupon (if appropriate) to check for residual oils: a perfectly clean surface will hold a continuous film of water, whereas oily spots will cause the water to bead up.
- Application of Protective Film: A high-quality, non-staining, strippable protective film is almost always applied to mirror-finished stainless steel sheets immediately after final inspection and cleaning. The film protects the delicate surface from scratches, abrasions, fingerprints, and contamination during subsequent handling, fabrication, transit, and installation.
- The type of film is crucial. It should have an adhesive that does not react with the stainless steel or leave residue upon removal, even after prolonged storage or exposure to moderate temperature fluctuations. Low-tack acrylic adhesives are often preferred.
- The film should be applied smoothly, without air bubbles or creases, as these can sometimes transfer a pattern to the stainless surface over time. Automated film applicators are often used for large sheets to ensure consistent application.
- For applications involving laser cutting, a special laser-cuttable protective film must be used.
- Packaging: Beyond the protective film, careful packaging is essential. Sheets should be packaged to prevent movement and contact with abrasive materials during transit. This might involve interleaving with soft, non-abrasive paper or foam sheets, then crating or palletizing securely. For export, MFY ensures robust seaworthy packaging for products like our mirror-polished sheets, often using wooden crates with internal supports and desiccant bags to prevent moisture damage.
By rigorously implementing these multi-faceted QC checks, from detailed visual scrutiny to objective instrumental measurements and meticulous final preparation for shipment, manufacturers can confidently deliver mirror-finished stainless steel products that meet the highest expectations of quality and aesthetic perfection.
QC Check Aspect | Critical Step/Technique | MFY Client Benefit / Example (e.g., Architectural Firm) |
---|---|---|
Visual Inspection | Standardized lighting (type, angle, intensity), viewing distance; defect classification. | Ensures consistent aesthetic quality across all panels for a facade, preventing mismatched appearances (e.g., no visible scratches from 1m). |
Reference Standards | Use approved master/limit samples for defects (haze, scratches, orange peel). | Provides objective benchmark, reduces disputes, ensures MFY supplied base material allows for achieving the target finish consistently. |
Gloss Measurement | Calibrated gloss meter (20°/60°); multiple readings for uniformity (e.g., target >800 GU @ 20°). | Guarantees high reflectivity demanded for luxury interiors/exteriors; verifies uniformity across large surfaces (e.g., max ±20 GU variation). |
DOI/Haze (Advanced) | Instrument measurement for image clarity and light scatter. | Critical for high-specification projects where reflection sharpness is paramount (e.g., feature walls in corporate HQs). |
Final Cleanliness | Inspection for residue, smudges after final cleaning with approved agents. | Prevents issues with coating adhesion if further treated, ensures pristine appearance on delivery to site. |
Protective Film/Pkg | Application of high-quality, non-staining, strippable film; robust packaging. | Protects the perfect MFY mirror finish during transit and on-site handling, reducing risk of costly damage before installation. |
Visual inspection requires controlled lightingTrue
Standardized lighting conditions (type, angle, intensity) are essential for effective visual inspection of mirror finishes to reveal defects consistently.
Gloss meters measure at 90° angleFalse
Gloss meters for mirror finishes typically measure at 20° or 60° angles, not 90°, as these acute angles are more sensitive to high-gloss surfaces.
How to maintain and preserve the mirror finish over time?
Achieved a stunning mirror finish on your stainless steel project, but worried about keeping it pristine? Everyday exposure can quickly dull its brilliance. Scratches, fingerprints, and environmental contaminants can tarnish that perfect reflection if not managed correctly, diminishing its value.
Maintain mirror finish stainless steel by regular cleaning with soft microfiber cloths and mild, chloride-free detergents or specialized stainless steel cleaners. Avoid abrasive materials or harsh chemicals. For long-term preservation, periodic application of a protective wax or sealant can help repel dirt.
The breathtaking allure of a mirror-finished stainless steel surface is an investment in aesthetics and quality. However, preserving that flawless, liquid-like reflection requires ongoing care and attention, especially in demanding environments. As Global Business Director at MFY, I've seen our MFY 316L mirror-polished sheets used in prestigious architectural installations in coastal cities like Mumbai5 or Dubai6, where salt-laden air poses a constant threat, and in high-traffic commercial interiors where fingerprints and scuffs are daily challenges. Simply achieving the finish is only half the battle; maintaining it is crucial for long-term client satisfaction and preserving the integrity of the design. I recall a luxury hotel client who had stunning mirror-finished MFY stainless steel features in their lobby. Initially, their housekeeping staff used standard all-purpose cleaners, which, over time, led to a subtle hazing and fine scratching. By switching to a recommended pH-neutral, chloride-free cleaner and training staff on proper techniques (e.g., wiping with the 'grain' even if imperceptible), they restored and successfully maintained the original brilliance, safeguarding their significant investment. Understanding these maintenance protocols is key to ensuring the longevity of this premium finish.
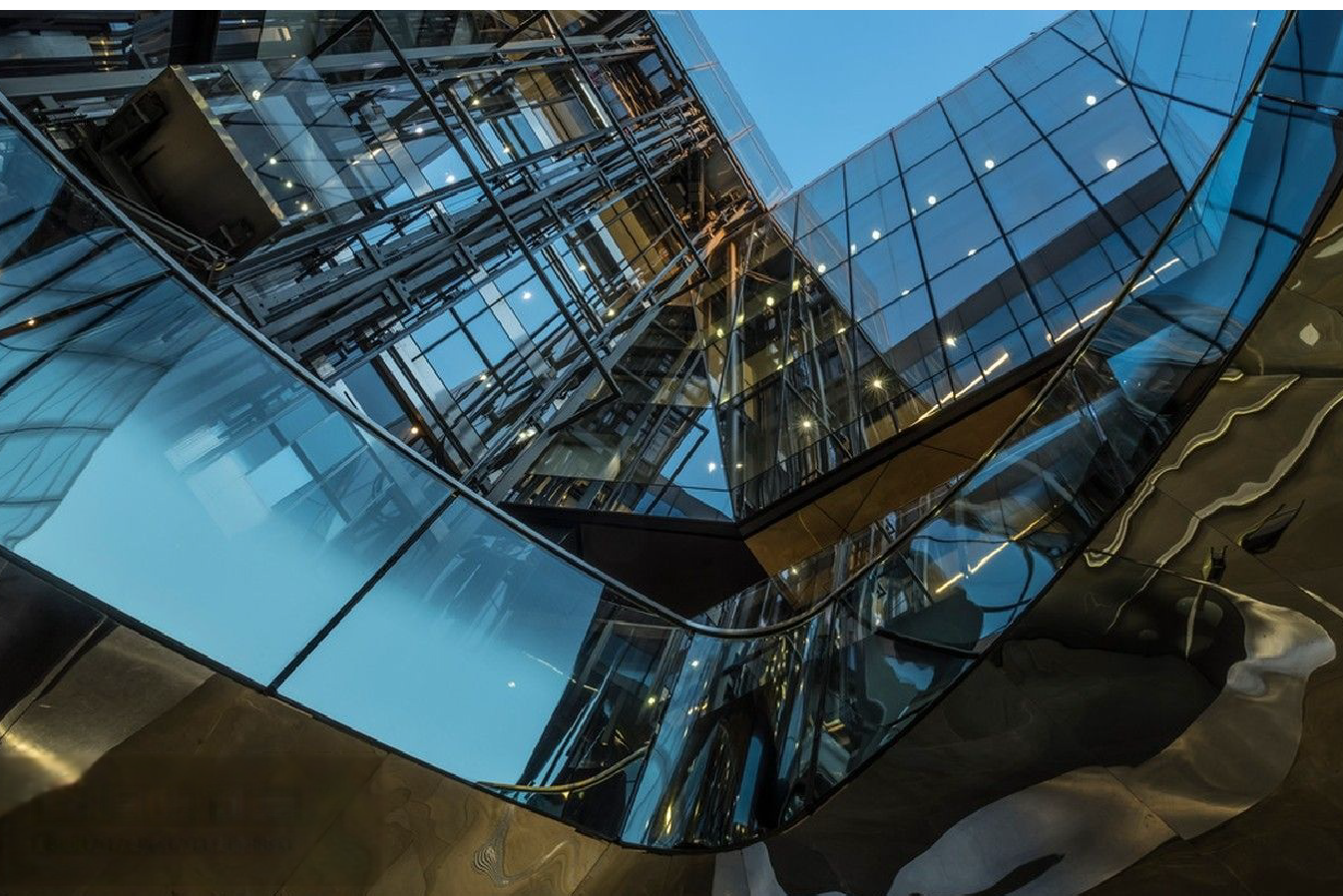
Routine Cleaning: Best Practices for Daily and Regular Care
The most important aspect of maintaining a mirror finish is routine cleaning to remove dust, fingerprints, water spots, and other superficial contaminants before they have a chance to become ingrained or cause damage. The frequency of cleaning will depend on the location and level of exposure. High-traffic interior areas or exterior applications in corrosive environments will require more frequent attention than low-traffic, protected interior surfaces. For many applications using MFY’s mirror-finished sheets, such as decorative panels in commercial buildings or high-end appliance facias, a simple cleaning regime is often sufficient.
The golden rule for cleaning mirror-finished stainless steel is to use the mildest cleaning method that will effectively do the job. Start with clean, soft cloths – microfiber cloths are ideal as they are highly absorbent, non-abrasive, and lint-free. For light dust or fresh fingerprints, often a dry microfiber cloth or one slightly dampened with clean warm water is enough. Wipe gently, and if there's any perceptible "grain" from the original polishing direction (even on a No. 8 finish, there can be an almost invisible microscopic lay), it's best to wipe parallel to it. Avoid harsh rubbing or circular scrubbing motions unless using a specialized polish designed for such application. After wiping with a damp cloth, it's good practice to dry the surface thoroughly with another clean, dry microfiber cloth to prevent water spots, which can be particularly noticeable on a mirror finish.
For more stubborn dirt, smudges, or oily fingerprints, a mild, chloride-free detergent (like a gentle dish soap) mixed with warm water can be used. Apply with a soft cloth, rinse thoroughly with clean water, and then dry completely. It is absolutely critical to avoid cleaners containing chlorides (chlorine bleach, hydrochloric acid, many muriatic acids, or even some household scouring powders), as chlorides are the nemesis of stainless steel’s passive layer and can cause pitting corrosion, even on resistant grades like 316L, especially if left in contact for extended periods. Also, avoid abrasive cleaners (scouring powders, steel wool, abrasive pads, or wire brushes of any kind other than stainless steel for specific, aggressive cleaning which is NOT for mirror finishes) as these will undoubtedly scratch and dull the mirror surface. We always advise our MFY clients, particularly those in food service or coastal construction who use our mirror-finished products, to develop very specific cleaning protocols for their staff, listing approved cleaners and techniques.
Addressing Specific Stains and Minor Imperfections
Occasionally, a mirror-finished stainless steel surface may encounter more stubborn stains or minor imperfections that require targeted attention. It’s crucial to address these carefully to avoid damaging the surrounding finish.
- Stubborn Water Spots or Mineral Deposits: These can sometimes be removed by applying a solution of equal parts white vinegar (a mild acetic acid) and water. Apply with a soft cloth, let it sit for a few minutes (but don't let it dry on the surface), then rinse thoroughly with clean water and dry. Test in an inconspicuous area first, especially on lower grades of stainless steel if unsure.
- Adhesive Residues: If adhesive from labels or old protective film remains, it can often be softened and removed by applying a mild solvent like isopropyl alcohol (IPA), acetone (use with caution and test first, as it's a strong solvent), or a specialized citrus-based adhesive remover. Apply the solvent to a cloth, gently rub the residue, and then clean the area as usual. Avoid scraping with metal tools.
- Minor Scratches: Unfortunately, removing scratches from a true mirror finish without affecting the surrounding area is extremely difficult and often requires re-polishing the entire affected panel or section by a professional. For very fine, superficial scuffs, sometimes a high-quality stainless steel polish specifically designed for mirror finishes (often a very fine abrasive paste or liquid) applied with a microfiber cloth might help to blend them, but results can vary greatly, and there's a risk of creating a larger, slightly different-looking area. Attempting to use abrasive compounds by hand on an established mirror finish is generally not recommended for amateurs. For MFY clients with high-value installations, we usually recommend they establish a relationship with a specialist metal polishing service for any necessary repairs. Data from maintenance companies indicates that improper scratch removal attempts are a common cause of further damage to mirror finishes.
- Grease and Oil: Heavy grease or oil can be pre-cleaned with an organic solvent or an alkaline degreaser (again, chloride-free and suitable for stainless steel) before routine cleaning.
Always remember the principle of "test in an inconspicuous area first" when trying any new cleaning agent or technique. This is particularly important for a delicate and valuable finish like a No. 8 mirror. Documentation provided by MFY for its specialized finishes often includes a section on recommended cleaning and maintenance procedures, tailored to the specific grade and finish.
Long-Term Preservation Strategies and Protective Measures
Beyond routine cleaning, certain long-term preservation strategies can help maintain the beauty and integrity of a mirror-finished stainless steel surface, especially in more challenging environments.
- Protective Waxes or Sealants: Applying a thin, even coat of a high-quality, non-abrasive wax (e.g., carnauba-based automotive wax or a specialized stainless steel wax/sealant) can provide a temporary barrier against fingerprints, smudges, water spots, and mild atmospheric contaminants. The wax fills microscopic pores in the surface, making it smoother and more hydrophobic, causing water to bead up and run off. This can also enhance the depth of the shine. The wax will need to be reapplied periodically (e.g., every few months for interior applications, more frequently for exteriors), as it wears off with cleaning and exposure. Before applying wax, ensure the surface is perfectly clean and dry. Buff gently with a clean microfiber cloth after application. Some architectural clients of MFY in coastal regions have reported good results using marine-grade waxes on exterior MFY 316L mirror-finished elements, extending the intervals between more intensive cleaning.
- Avoiding Contact with Corrosive Substances: Educate users and maintenance staff about substances that are harmful to stainless steel. This includes strong acids (hydrochloric, sulfuric, nitric – though dilute nitric is used for passivation, concentrated or prolonged contact can be harmful), chlorides (bleach, de-icing salts, some sterilizing solutions), and even prolonged contact with carbon steel (which can cause embedded iron particles leading to rust spots). In environments where such substances might be present, design considerations (e.g., preventing pooling of liquids, ensuring good drainage) are also important.
- Managing Environmental Factors: For exterior applications, consider the orientation of the mirror-finished surfaces. Surfaces sheltered from direct rain or salt spray may require less frequent cleaning. In areas with high pollution, regular rinsing with clean water can help remove acidic deposits. Indoors, maintaining good ventilation can help reduce condensation.
- Periodic Professional Care: For very large or critical installations, consider periodic inspection and maintenance by a professional metal maintenance service. They have the expertise and equipment to deep clean, re-passivate if necessary (though rarely needed for well-maintained mirror finishes unless corrosion has started), and address any minor damage that may have occurred. This can be a worthwhile investment to protect the significant cost of the mirror finish itself. Some studies on life-cycle costing of architectural materials show that while stainless steel has a higher initial cost, its longevity and low maintenance needs (if properly cared for) make it very cost-effective over time. A mirror finish, while requiring more careful cleaning, shares this longevity if these protocols are followed.
By adopting these maintenance practices, the stunning visual appeal of mirror-finished stainless steel can be preserved for many years, ensuring it remains a testament to quality and sophisticated design.
Microfiber cloths are ideal for cleaningTrue
Microfiber cloths are non-abrasive, highly absorbent, and lint-free, making them perfect for maintaining mirror finishes without scratching.
Chloride cleaners are safe for stainless steelFalse
Chlorides in cleaners can damage stainless steel's passive layer and cause pitting corrosion, especially on mirror finishes.
Conclusion
Achieving and maintaining a flawless mirror finish on stainless steel demands meticulous preparation, precise polishing techniques, stringent QC, and diligent care. By mastering these steps, from base material selection to long-term preservation, industries can deliver exceptionally beautiful and durable products that truly reflect excellence.
-
Discover why MFY's stainless steel products are ideal for high-quality mirror finishes ↩
-
Explore advanced techniques for superior mirror-finishing results ↩
-
Discover the precision and efficiency of robotic cells in polishing ↩
-
Understand their role in focusing light and improving energy efficiency in optics ↩
-
Understand environmental factors affecting stainless steel maintenance in coastal areas. ↩
-
Learn about the unique environmental challenges for stainless steel in Dubai. ↩
Have Questions or Need More Information?
Get in touch with us for personalized assistance and expert advice.