Orbital Welding Stainless Tube: ISO 14732 Guide
Struggling to achieve consistent, high-purity welds in your stainless steel tubing projects? The slightest imperfection can lead to catastrophic failures, costly rework, and a damaged reputation. This is a constant pressure point in industries where precision is not just a goal, but a strict requirement.
The solution lies in a standardized approach. ISO 14732 provides a comprehensive framework for the approval of welding operators for fusion welding and resistance weld setters for fully mechanized and automatic welding of metallic materials, ensuring every weld meets the highest standards of quality and repeatability.
As the Global Business Director for MFY, I’ve seen firsthand how projects can be delayed or derailed by inconsistent welding quality. Adopting a universally recognized standard isn't just about compliance; it's about building a foundation of trust with your clients and ensuring the long-term integrity of your work. We'll explore how this standard transforms your operations.
Diving deeper into ISO 14732 reveals it's more than just a set of rules; it's a paradigm shift in how we approach automated welding. It moves the focus from the welder's manual skill to the operator's competence in managing a sophisticated, automated system1. This is crucial in sectors like pharmaceuticals, aerospace, and food processing, where the cost of a single failed weld can be astronomical. For instance, a study by the Welding Institute (TWI) highlighted that automated processes like orbital welding can reduce defect rates by over 50% compared to manual methods. This standard ensures that the personnel operating these advanced systems are fully qualified, directly impacting safety, efficiency, and your bottom line by building a process that is predictable and repeatable every single time.
What is the significance of ISO 14732 in orbital welding for stainless tubes?
Are you concerned that your welding processes lack the verifiable quality your clients demand? Without a recognized standard, you risk inconsistent results and diminished credibility. This uncertainty can jeopardize high-stakes projects where failure is not an option, making compliance a critical business necessity.
ISO 14732 is significant because it establishes a global benchmark for qualifying welding operators and setters for automated processes like orbital welding. It ensures that personnel possess the necessary knowledge and skills to manage the equipment, guaranteeing weld integrity, safety, and process repeatability for critical applications.
I recall a project with a new client in the semiconductor industry, a sector where particle contamination from a single bad weld can ruin millions of dollars in product. They were hesitant to source from a new supplier, given the stringent purity requirements for their gas delivery systems. Their previous supplier had provided materials that, while certified, failed to perform consistently under their automated orbital welding process, leading to micro-fissures and costly delays. By demonstrating our rigorous adherence to standards that complement ISO 14732 at the material supply level—ensuring consistent chemical composition and dimensional tolerance in our stainless steel tubes—we provided the foundation they needed. We explained that superior materials are the starting point, but the process is only as strong as its execution, which is where a standard like ISO 14732 becomes indispensable for the end-user. It provides a shared language of quality, a verifiable assurance that the operators managing the sophisticated welding process are certified experts. This conversation shifted their focus from mere material cost to the total cost of ownership, including process reliability and risk mitigation. They understood that our quality control, combined with their certified welding operations, would create a truly resilient supply chain.
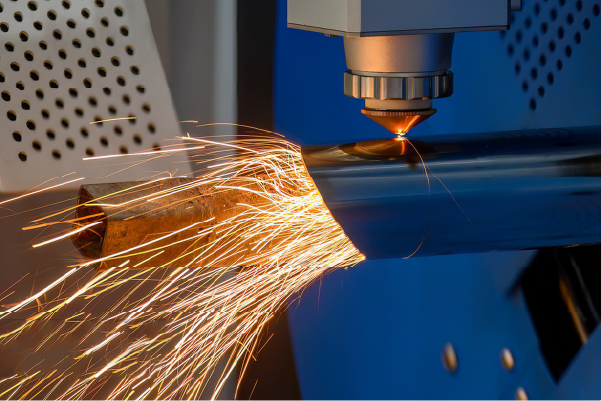
ISO 14732 is not merely a procedural checklist; it is a foundational pillar supporting the entire structure of modern industrial manufacturing where automated welding is employed. It redefines accountability, shifting the emphasis from the manual dexterity of a welder to the technical proficiency of an operator overseeing a complex, automated system. This distinction is vital. In orbital welding, the machine executes the weld with precision far exceeding human capability, but it is the operator who sets the parameters, monitors the process, and ensures the system functions within the strict confines of the Welding Procedure Specification (WPS)[^2]. The standard’s significance lies in its power to codify the knowledge required for this oversight, transforming welding from an art form into a science. It mandates a deep understanding of metallurgy, gas flow, amperage, and equipment calibration. This ensures that every operator, regardless of their geographic location or the company they work for, meets a universal standard of competence. This global benchmark is what allows a company like MFY to confidently supply stainless steel tubes to a contractor in Russia or an engineering firm in Southeast Asia, knowing that if the client is compliant with ISO 14732, the welding process will honor the quality of our materials. It creates a seamless chain of quality that begins with raw material and ends with a certified, flawless final product. This level of standardization de-risks projects, accelerates timelines, and ultimately builds a more interconnected and reliable global industrial ecosystem.
Establishing a Baseline for Quality and Safety
The primary function of ISO 14732 is to establish an unambiguous baseline for what constitutes a competent welding operator. In industries like nuclear, pharmaceutical, or aerospace, a faulty weld is not just a defect; it's a potential safety hazard of immense proportions. The standard directly addresses this by requiring documented proof of an operator's ability to produce welds that are free from defects and meet stringent mechanical and structural properties. This isn't a one-time test but a validation of their deep understanding of the entire welding ecosystem.
This baseline extends beyond the operator to the process itself. By standardizing operator qualification, companies can achieve unprecedented process control. For a client of ours manufacturing high-pressure hydraulic systems in India, batch-to-batch consistency is paramount. Their adoption of ISO 14732-qualified operators meant they could guarantee that the 1,000th weld was identical to the first. This level of repeatability, validated by a globally recognized standard, is a powerful selling point and a critical factor in ensuring the safety and reliability of their end products.
Furthermore, this standardization has a cascading effect on the entire supply chain. When fabricators and contractors adopt ISO 14732, it signals to material suppliers like us at MFY that they are serious about quality. It prompts us to ensure our stainless steel tubes offer consistent weldability, with controlled chemical compositions (e.g., sulfur content) and precise dimensional tolerances that facilitate perfect joint fit-up. This synergy between a certified operator and high-quality material is where true manufacturing excellence is born, creating a system where quality and safety are ingrained at every step.
The Role of Welding Personnel Qualification
ISO 14732 fundamentally redefines the role of welding personnel in an automated environment. It moves beyond the traditional "welder" title to that of a "welding operator" or "setter," a technician responsible for managing a sophisticated manufacturing process. The qualification process is rigorous, covering both theoretical knowledge and practical application. An operator must demonstrate proficiency not just in running the equipment but in understanding the underlying metallurgy, interpreting the Welding Procedure Specification (WPS), and performing essential quality checks.
Consider a typical customer of ours, an equipment integrator for the food and beverage industry in the Middle East. They use our 316L stainless steel tubes to build pasteurization systems. For them, every internal weld must be perfectly smooth to prevent microbial growth. Under ISO 14732, their operators are tested on their ability to set up the orbital welder to achieve specific weld profiles with controlled heat input, ensuring the corrosion-resistant properties of the stainless steel are not compromised. The qualification is tangible proof that the operator can deliver a sanitary weld every single time.
This focus on personnel qualification builds a culture of accountability and expertise. It empowers operators by providing them with a certified skill set that is recognized globally. It also provides management with the assurance that their most critical processes are in the hands of proven experts. This reduces the reliance on subjective assessments of skill and replaces it with objective, verifiable evidence of competence, which is essential for risk management and continuous improvement in any high-stakes manufacturing environment.
Global Market Access and Client Trust
In today's globalized marketplace, standards are the language of international trade. Compliance with ISO 14732 is not just an internal quality metric; it's a passport to new markets and a critical tool for building client trust. When a manufacturing company can state that its welding operators are certified to this standard, it immediately elevates their credibility. It tells potential clients that their processes are robust, repeatable, and aligned with global best practices.
I've personally seen this in action. A potential client, a large engineering contractor, was evaluating suppliers for a major desalination plant project. The project specifications demanded strict adherence to multiple ISO standards. Our ability to supply certified stainless steel products was a given, but their main concern was the fabrication process on-site. The contractor that won the bid had made ISO 14732 compliance a cornerstone of their proposal, showcasing their team of certified operators as a key strength. This assurance of quality was a decisive factor, proving more valuable than a slightly lower price.
This trust is self-perpetuating. As more leading companies demand ISO 14732 compliance, it becomes a de facto requirement for participation in premier projects. It creates a clear distinction in the market between those who can provide certified quality and those who cannot. For companies looking to expand their footprint, particularly in export markets like those MFY serves, adopting this standard is a strategic investment in their brand reputation and their long-term growth. It's a clear, powerful signal that they are a world-class operator.
How to prepare for orbital welding in compliance with ISO 14732?
Feeling overwhelmed by the stringent preparation required for certified orbital welding? The complexity of material handling, equipment setup, and joint preparation can seem daunting. A single misstep can lead to failed tests and costly project delays, creating significant pressure to get it right from the start.
To prepare for orbital welding under ISO 14732, focus on three core areas: meticulous material control, precise equipment calibration, and flawless joint preparation. This involves verifying material certificates, calibrating the welding machine against a known standard, and ensuring tube ends are perfectly square, clean, and contaminant-free.
From my experience at MFY, the most successful projects are those where preparation is treated with the same importance as the weld itself. We once worked with a construction contractor on a large-scale chemical processing plant. They were struggling with weld test failures despite having top-of-the-line orbital welding equipment. When we visited the site, the issue wasn't the machine or the operator's skill, but the pre-weld preparation. Their storage of our stainless steel tubes was inadequate, allowing for surface contamination, and their tube-facing tools were worn, resulting in slightly angled ends. This created an inconsistent gap, which the automated system couldn't reliably compensate for. We helped them implement a stringent pre-weld protocol: a dedicated clean storage area for tubes, a regular maintenance schedule for their facing tools, and a final, multi-step cleaning process using specified solvents. By focusing intensely on these preparatory steps, their first-pass weld success rate jumped from under 80% to over 99%, saving them weeks on their project schedule. It’s a powerful lesson that meticulous preparation is the non-negotiable foundation for automated welding success.
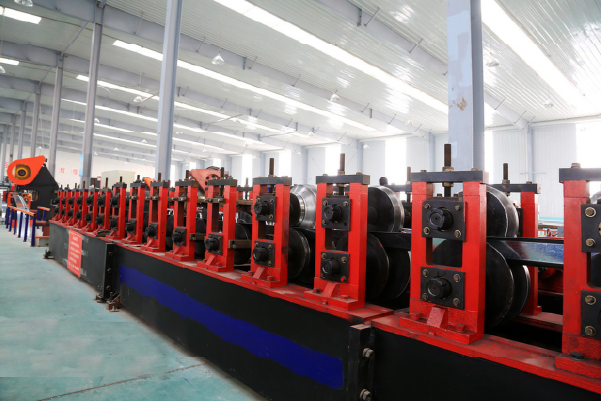
Compliance with ISO 14732 orbital welding qualification begins long before the welding arc is ever initiated. The preparation phase is a meticulous, multi-faceted process that sets the stage for success or failure. It is here that the operator’s diligence and adherence to the Welding Procedure Specification (WPS) are first put to the test. This phase is about controlling every possible variable to ensure that the automated system can perform its task under ideal and repeatable conditions. It encompasses the entire journey of the material, from receiving and inspection to the final moment before it's clamped into the weld head. A lapse in this stage, such as using an incorrect grade of stainless steel or failing to properly purge the tube of oxygen, cannot be corrected by even the most advanced welding machine. Therefore, the standard implicitly demands a culture of precision and cleanliness. A client in the biopharmaceutical sector once shared that they consider their pre-weld cleanroom environment as critical as their production cleanrooms. They use our electropolished 316L tubes, and to protect that pristine surface, they implement a rigorous protocol that includes dedicated tooling, lint-free wipes, and specific cleaning agents to prevent any form of contamination. This level of rigor is what ISO 147322 aims to standardize, ensuring that the final weld is a reflection of a controlled, predictable, and thoroughly documented preparatory process.
Material Selection and Handling
The foundation of a compliant weld is the material itself. Preparation begins with rigorous verification of the stainless steel tubes. This means cross-referencing the material test certificates (MTCs)3 with the project's WPS requirements, confirming the grade (e.g., 304L, 316L), heat number, and chemical composition. At MFY, we ensure every shipment comes with comprehensive documentation for precisely this reason. An operator must confirm they have the correct material before a single cut is made.
Once verified, material handling becomes paramount. Stainless steel must be protected from contamination, particularly from carbon steel. This requires dedicated storage racks, handling equipment (e.g., nylon slings instead of steel chains), and tools. I’ve seen projects compromised because a grinder used on carbon steel was subsequently used to bevel a stainless tube, impregnating the surface with ferrous particles that led to corrosion at the weld site. A proper preparatory environment includes separate workstations and color-coded tools to prevent such cross-contamination.
Furthermore, the tubes themselves must be inspected for any surface imperfections, scratches, or ovality that could interfere with the welding process. Any deviation must be addressed according to the specified procedures. This scrupulous attention to the material from the moment it arrives on-site is a core tenet of building a reliable welding process compliant with international standards.
Equipment Calibration and Setup
An orbital welding system is a precision instrument, and its accuracy is contingent on proper calibration and setup. ISO 14732 requires that the operator be competent in this area, as the machine's output must be verifiable and consistent. The process starts with calibrating the power supply. This often involves using a calibrated multimeter to verify that the displayed amperage and voltage match the actual output, a process sometimes referred to as "calibrating the meters." This ensures that a programmed 100 amps is truly 100 amps.
Next, the setup of the physical components is critical. This includes selecting the correct weld head, collets for the specific tube diameter, and, crucially, the tungsten electrode preparation for orbital welding4. The electrode must be the correct type, diameter, and ground to a precise angle and tip geometry as specified in the WPS. A poorly prepared electrode can lead to arc wander, an unstable arc, and an inconsistent weld bead. The table below illustrates common tungsten preparation issues and their impact.
Electrode Issue | Description | Impact on Weld Quality |
---|---|---|
Contaminated Tip | Tip touched the weld pool or filler wire. | Causes arc instability and potential weld contamination. |
Incorrect Tip Angle | Angle is too sharp or too blunt. | Affects arc shape and heat concentration, leading to poor penetration or excessive melt-through. |
Improper Grinding | Grinding lines are circumferential, not longitudinal. | Can cause the arc to wander, resulting in an inconsistent and uneven weld bead. |
Split or Worn Tip | The tip is fractured or has lost its point. | Leads to a diffuse, unstable arc and difficulty in controlling the weld pool. |
ly, gas flow rates for both the shield gas (protecting the outside of the weld) and the purge gas (protecting the inside) must be set and verified with a calibrated flowmeter. An incorrect flow rate can lead to atmospheric contamination and a porous, weak weld. The operator's ability to meticulously execute this entire setup sequence is a key part of their qualification.
Joint Design and Pre-Weld Cleaning
The final preparatory step is the "fit-up" of the joint itself. For orbital tube welding, this almost universally means a square butt joint. The tube ends must be prepared using a specialized tube facing or squaring tool to ensure they are perfectly perpendicular to the tube's centerline. A non-square end will create a variable gap around the circumference, leading to inconsistent penetration and potential defects. The goal is a "zero-gap" fit-up where the two tube ends touch uniformly.
Once the joint is mechanically prepared, cleaning is the last, critical action. The area to be welded, both internally and externally, must be completely free of oils, grease, dirt, cutting fluids, and any other contaminants. This is typically a multi-step process. First, a mechanical cleaning with a dedicated stainless steel wire brush may be required. This is followed by a chemical cleaning using a specified solvent, such as acetone or isopropyl alcohol, applied with a clean, lint-free cloth.
The operator must be trained on the correct cleaning procedures and the safety precautions associated with the solvents. They must understand that even a fingerprint can introduce enough contamination to cause a weld defect. This final, painstaking cleaning ensures that the only materials fused during the welding process are the parent metals themselves, creating the pure, integral bond that high-stakes applications demand.
What are the essential steps in the orbital welding process according to ISO 14732?
Facing the live welding process can be nerve-wracking. You've done the prep work, but now you have to execute perfectly. There's a real fear that a wrong parameter or a missed step will undo all your careful preparation, forcing you back to square one.
The essential steps under ISO 14732 orbital welding process involve three key actions: programming the exact parameters from the certified WPS into the power supply, performing a test coupon weld to verify the setup, and then executing the production weld while monitoring the system for any deviations.
In my role, I often emphasize that the orbital welding process itself should be the most predictable part of the job if the preparation is done right. The machine simply executes the commands it's given. A client manufacturing medical gas pipelines learned this well. Initially, their operators were tweaking program parameters on the fly based on what they "felt" was right, leading to inconsistent results that failed quality control. We worked with them to enforce a strict "lockdown" on the Welding Procedure Specification (WPS)5. The essential process became: 1. The certified operator selects the pre-approved program number corresponding to the WPS without any modification. 2. They run a sample coupon, which is then visually inspected. 3. Only after the coupon is approved do they clamp the head onto the production pipes and press "start." This rigid, non-deviating sequence transformed their process, making it systematic and consistently compliant. The machine’s automation became their greatest asset, but only once they committed to a standardized, hands-off execution process.
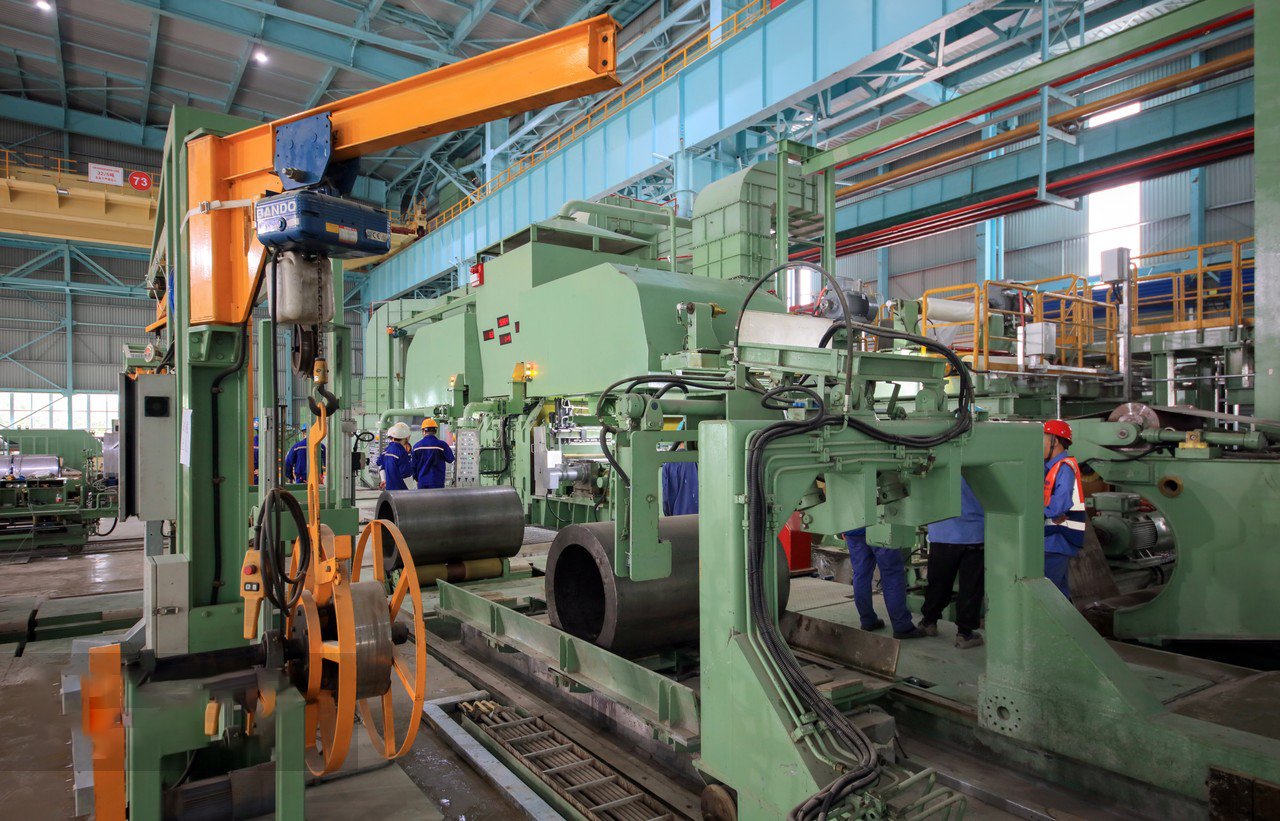
The actual orbital welding process for high purity piping6, when viewed through the lens of ISO 14732, is the systematic execution of a pre-approved and scientifically validated procedure. It is the culmination of all prior preparation. The standard requires that the operator demonstrate not just the ability to press a button, but the ability to manage a controlled manufacturing event. This means they must load the correct, certified Welding Procedure Specification (WPS) into the power supply, a document that dictates every critical variable: peak and background amperage, pulse rates, travel speed, and gas flow timings. There is no room for improvisation or guesswork. The operator’s role is one of verification and oversight, ensuring the machine’s environment and setup perfectly mirror the conditions under which the WPS was qualified. They are the guardians of the procedure. For example, a client fabricating piping for a UHP (Ultra-High Purity) water system knows that the WPS for their thin-wall stainless steel tubes is designed to minimize heat input and prevent any internal discoloration or "sugaring." The operator's primary job during the weld is to ensure the automated sequence runs exactly as programmed, as any deviation could compromise the sanitary integrity of the entire system. This disciplined, procedure-driven execution is the core of the ISO 14732 philosophy.
Programming the Welding Parameters
The first active step in the welding process is translating the written WPS into a machine-executable program. The qualified operator must be able to navigate the welding power supply's interface and accurately input or select the correct parameters. Modern orbital welding systems allow for the storage of hundreds of programs, so selecting the precise one that matches the tube diameter, wall thickness, and material grade is a critical responsibility. A simple mistake, like choosing the program for a 0.065" wall tube instead of a 0.049" wall, will result in a failed weld.
This step involves more than just selecting a program number. The operator must verify that the parameters displayed on the screen—such as primary amperage, pulse frequencies, rotational speed, and gas pre-flow/post-flow times—are an exact match for those listed on the approved WPS documentation. Some procedures may even require the operator to enter a unique ID or have a supervisor authorize the program selection. This creates a digital audit trail, linking a specific weld to a specific operator and the exact program used, which is invaluable for welding quality assurance and traceability7.
At MFY, we often advise clients to create a physical checklist that the operator must complete during this programming phase. This double-check mechanism, requiring the operator to physically tick off each parameter as they verify it against the WPS, minimizes the risk of human error. It reinforces the discipline that ISO 14732 demands, ensuring the machine is perfectly configured before the cycle begins.
Executing the Test Weld (Coupon Test)
Before committing to welding on expensive, production-level materials, a test weld is almost always performed. This is commonly known as a "coupon test." The operator will take two short pieces of the exact same material (from the same heat lot, if required) that will be used in production, prepare them identically, and perform a complete weld cycle. This coupon serves as the final proof that the material, the machine calibration, the program, and the operator's setup are all working in harmony.
Once the coupon weld is complete, it is subjected to immediate inspection. The first step is a thorough visual examination. The operator, trained in weld inspection, looks for tell-tale signs of problems: uniform bead width, proper penetration (often checked on the inside of the tube), correct color (indicating proper gas shielding), and the absence of any surface defects like porosity or undercut. In many high-purity applications, the coupon is cut open to allow for a full inspection of the internal weld bead profile.
This test weld is a critical data point. If it passes inspection, it gives the operator and the quality inspector the confidence to proceed with the actual production welds. If it fails, all work stops. The operator must then troubleshoot the issue—was it a gas flow problem? An electrode issue? A programming error?—and repeat the entire setup and coupon test process until a perfect weld is achieved. This step prevents the costly mistake of creating a series of bad welds on the final product.
The Live Production Welding Cycle
With a successful coupon test completed, the operator can now move to the live production weld. The process is identical: the weld head is mounted onto the production tubes, which have been meticulously prepared and fitted. The operator ensures the head is seated correctly and that all cables and gas lines are clear and unobstructed. Then, they initiate the automated weld cycle.
During the few minutes the weld is being performed, the operator’s role shifts to one of active monitoring. They are not idle. They watch the machine's display for any error messages or fluctuations in parameters. They listen for the consistent, steady hum of a good weld and look at the arc and weld pool (through appropriate safety glasses) for any signs of instability. This monitoring is a key skill outlined in ISO 14732; the operator must be able to recognize the signs of a developing problem during the cycle itself.
Upon completion, the automated cycle will manage the post-purge gas flow to protect the cooling weld. The operator waits for this cycle to finish before removing the weld head. The freshly completed production weld is then immediately subjected to the same initial visual inspection as the test coupon, and it is marked with an identifier for traceability. This disciplined, repeatable sequence of Program-Test-Execute is the very essence of reliable automated welding under ISO 14732.
How to ensure quality control and monitoring during orbital welding under ISO 14732?
How can you be absolutely certain that every weld is perfect, especially when many defects are invisible to the naked eye? This doubt can be a major source of anxiety, as relying on visual inspection alone leaves you vulnerable to latent flaws that can cause failures later.
To ensure quality under ISO 14732, a multi-layered approach is used: real-time data logging during the weld], followed by rigorous visual inspection and, most importantly, the application of appropriate Non-Destructive Testing (NDT) methods to uncover any subsurface defects and validate weld integrity.
This is a topic I discuss frequently with clients, particularly those in the energy sector who rely on our stainless steel pipes for critical applications. A client who was constructing a natural gas processing facility provides a perfect example. While their operators were certified and their visual inspections were thorough, their end-client required 100% radiographic testing (a form of NDT) on all critical welds. Initially, they viewed this as a costly, time-consuming hurdle. However, after the first week, the NDT reports provided invaluable feedback. They revealed minor, intermittent internal porosity that wasn't visually apparent, which they traced back to an inconsistent purge gas regulator. The data logging from the welder confirmed the pressure fluctuations. By integrating real-time monitoring with NDT results, they were able to correct a systemic issue, dramatically improving their overall weld quality and passing the stringent final validation with ease. It proved that robust QC isn't a barrier, but a tool for refinement.
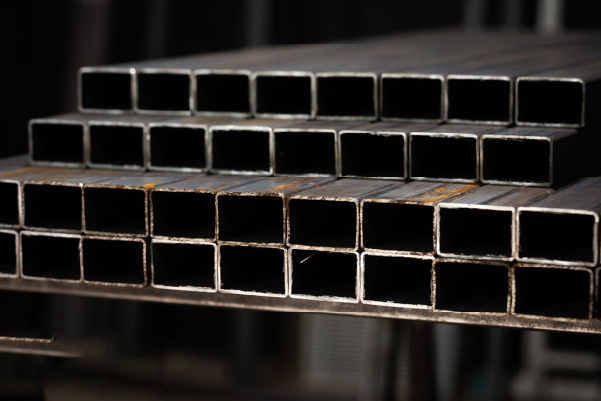
Quality control within the ISO 14732 framework is not a post-production afterthought; it is an integrated and continuous process that occurs before, during, and after the weld is made. The standard mandates a system where quality is actively managed and documented at every stage. It moves beyond the simple "pass/fail" visual check to a more holistic and data-driven approach to quality assurance. The core principle is that if the inputs are controlled (certified operator, calibrated machine, correct WPS, verified material) and the process is monitored, the output will be consistently high quality. However, the framework still demands verification. This is where a robust monitoring and testing plan becomes indispensable. For a client like MFY supplies in the aerospace sector, this is non-negotiable. They use our high-strength stainless steel tubes for hydraulic lines, where a weld failure could be catastrophic. Their quality plan, aligned with ISO 14732, includes real-time data logging for every single weld, a 100% visual inspection by a certified inspector, and a statistically significant percentage of welds undergoing further NDT like radiography or ultrasonic testing. This creates a powerful feedback loop, allowing them to spot any potential process drift long before it results in a systemic problem, ensuring the highest possible level of safety and reliability.
Real-Time Data Logging and Monitoring
Modern orbital welding power supplies are also sophisticated data-logging devices. A key aspect of advanced quality control is leveraging this capability. During every weld, the machine can record a complete set of data in real-time, including amperage, voltage, travel speed, and gas flow for every second of the process. This creates a unique digital "birth certificate" for each weld.
The qualified operator, as part of their monitoring duties, must be aware of the expected data ranges. An alarm on the power supply might indicate if a parameter drifts outside the limits specified in the WPS. This allows for immediate intervention or flagging of the weld for further inspection. After the project is complete, these data logs provide an invaluable audit trail. If a question ever arises about a specific weld, one can pull up the data log and prove that it was made within the specified parameters.
For industries requiring high levels of traceability, like nuclear or pharmaceutical, this data logging is not just good practice; it's often a contractual requirement. It provides objective, quantitative evidence that the welding process was under control, shifting quality assurance from a subjective visual assessment to a verifiable, data-backed conclusion.
Non-Destructive Testing (NDT) Methods
While visual inspection is the first line of defense, it can only assess the external surface of the weld. Non-Destructive Testing (NDT) methods are a family of analysis techniques used to evaluate the properties of a material or component without causing damage. For orbital welds, NDT is crucial for detecting subsurface defects like lack of fusion, porosity, or cracking.
Several NDT methods are commonly used. Radiographic Testing (RT), which uses X-rays or gamma rays, provides a film image of the weld's internal structure, clearly showing voids or inclusions. Ultrasonic Testing (UT) uses high-frequency sound waves to detect internal flaws. For high-purity tube welds, Borescope/Videoscope Inspection is also a form of NDT, allowing an inspector to view the inside (ID) of the weld bead in high magnification to check for color, profile, and any signs of oxidation or "sugaring."
The choice of NDT method depends on the application, material, and client specifications. An ISO 14732 qualified operator isn't necessarily an NDT expert, but they must understand why NDT is performed and how to produce a weld that will pass the specified inspection criteria. This knowledge reinforces the need for meticulous technique, as they know their work will be scrutinized on a microscopic level.
Visual Inspection Criteria and Documentation
The most immediate form of quality control is a thorough visual inspection, performed by a trained and often certified welding inspector (CWI). This inspection is guided by a clear set of acceptance criteria, often defined by a standard like ISO 5817. The inspector examines the weld for a range of potential discontinuities.
These include external issues like incorrect weld size, undercut (a groove melted into the base metal), excessive reinforcement (too much weld metal), surface porosity, and arc strikes. They also assess the weld color. On stainless steel, a shiny, silver or light straw color indicates proper shielding gas coverage, while a dark blue, gray, or black color signifies excessive heat or loss of shielding gas, which compromises the material's corrosion resistance.
Every inspection, whether it passes or fails, must be meticulously documented. This documentation is a critical component of the quality control process. A weld map is often created for the entire project, with each weld numbered. Inspection reports are then tied to these numbers, recording the date, operator, inspection results, and any NDT performed. This creates a complete quality record, providing traceability and proving that the project was completed in full compliance with the required standards.
What are the final steps for validation and certification in accordance with ISO 14732?
You've completed the welding and quality checks, but how do you formally prove compliance? The final stage of validation and certification can feel like a bureaucratic maze. Without a clear understanding of the documentation and auditing process, you risk having your hard work invalidated on a technicality.
The final steps involve compiling a comprehensive documentation package, including the Welding Procedure Specification (WPS) and qualification records, and often submitting to a third-party audit. This process culminates in the formal certification of the welding operators, validating their competence according to the ISO 14732 standard.
This final validation is the moment of truth. I often tell my team at MFY that the quality of our stainless steel is ultimately proven when our clients' projects get certified. I recall a major infrastructure project where a client used our duplex stainless steel pipes. The project's success hinged on passing a final audit by an international certification body. Their entire project book, which we helped them prepare the material sections for, was scrutinized. The auditors didn't just look at the final NDT reports; they meticulously reviewed the operator qualification records under ISO 14732, the WPS documentation for each joint type, and the material traceability certificates8 we provided. It was the complete, unbroken chain of documentation—from our steel mill to their final weld—that earned them the final certification. It’s a powerful reminder that the final stamp of approval is earned through diligence at every single step.
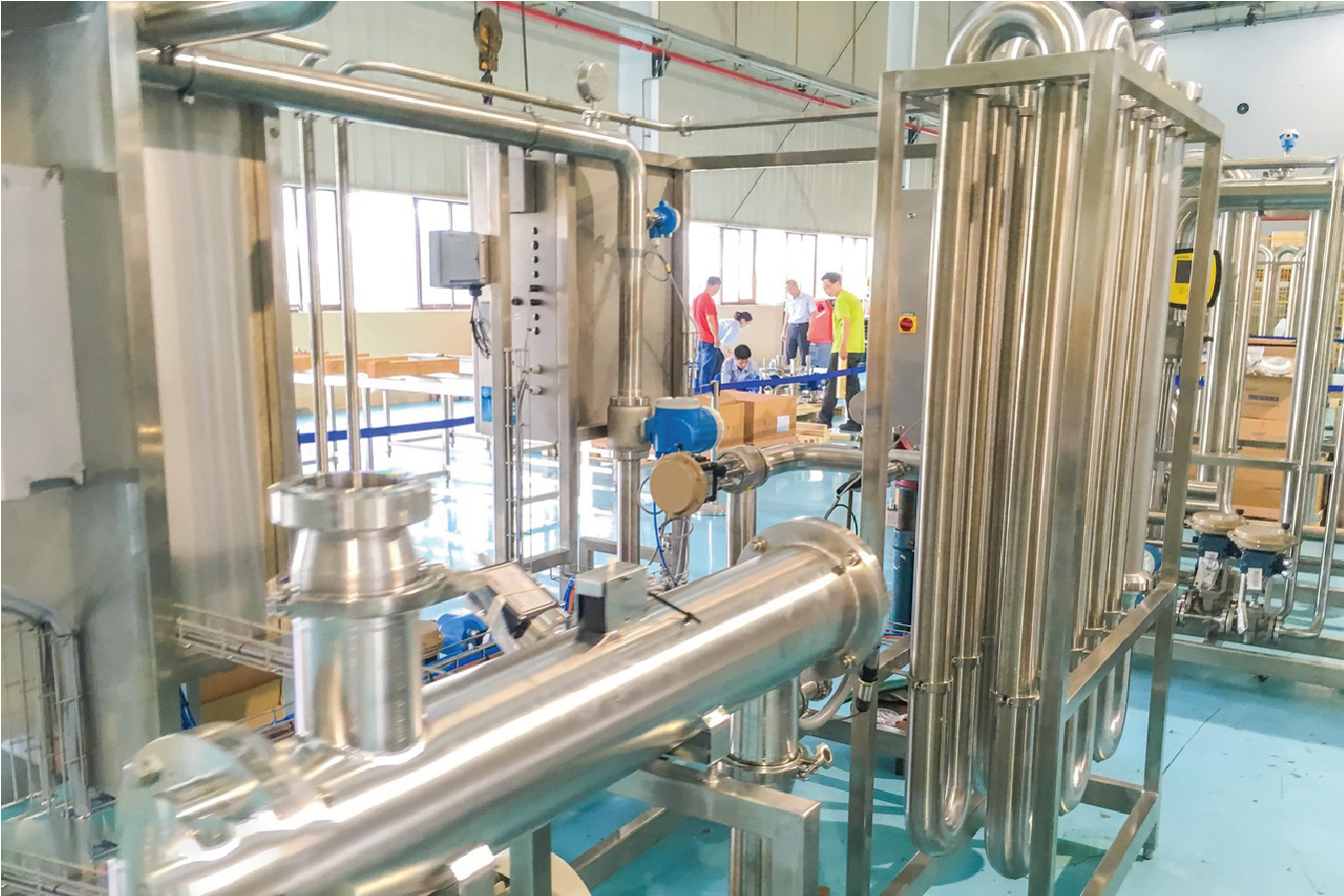
The culmination of the entire orbital welding process under ISO 14732 is the formal validation and certification. This is the final, official confirmation that the procedures are sound and the personnel are competent. It's the point where all the meticulous preparation, precise execution, and rigorous quality control are synthesized into a recognized qualification. This stage is not merely about paperwork; it is the cornerstone of trust and accountability in high-stakes industries. It provides the asset owner, regulators, and insurers with irrefutable proof that the welding operations have met a global standard of excellence. For a company to achieve this certification, it must demonstrate a mastery of the entire process, showcasing a system that is not only capable of producing perfect welds but is also robust, repeatable, and thoroughly documented. This final step transforms operational capabilities into a certified, marketable, and bankable asset. For contractors and manufacturers, this certification is a powerful differentiator, opening doors to projects that are inaccessible to those without such formal qualifications. It is the ultimate testament to their commitment to quality and safety, turning their operational processes into a tangible competitive advantage.
Assembling the Welding Procedure Specification (WPS)
The foundational document for any welding operation is the Welding Procedure Specification (WPS). Before an operator can even be tested, a WPS must be established and qualified. A preliminary WPS (pWPS) is first written, detailing all the variables for a specific weld material grade and thickness, joint design, welding position, and all machine parameters (amperage, voltage, travel speed, gas, etc.). This pWPS is then used to perform a procedure qualification record (PQR) test weld.
The PQR weld is subjected to extensive destructive and non-destructive testing to prove that the procedure can produce a weld that meets the required mechanical properties (e.g., tensile strength, bend tests). Once the PQR passes, the pWPS is formally approved and becomes the official WPS. This certified WPS is the "recipe" that all subsequent production welds must follow.
For ISO 14732 operator qualification, the candidate will perform their test weld strictly following a certified WPS. Their ability to understand and perfectly adhere to this document is a key part of what is being tested. The final documentation package for the project will include copies of all relevant WPS and supporting PQR documents.
The Role of Third-Party Inspection and Audits
While internal quality control is essential, independent, third-party verification provides the highest level of assurance. For many critical projects, a third-party inspection agency or a certified welding inspector (CWI) is engaged to oversee the qualification process and audit the results. This third party acts as an impartial authority, ensuring that the company is adhering strictly to the ISO 14732 standard.
During an audit, the inspector will review all documentation: the WPS/PQR, material certificates, equipment calibration records, and quality control reports. They will witness the operator qualification tests, watching the operator perform the setup and execute the test coupon weld. They will then independently verify the results of the visual inspection and any NDT performed on the test piece.
This independent oversight is crucial for eliminating any potential conflicts of interest and providing the end client with maximum confidence. Passing a third-party audit for ISO 14732 demonstrates that a company's welding quality system is robust and that their personnel are qualified to an internationally recognized benchmark. It’s a rigorous but invaluable process for proving capability.
Maintaining Certification and Continuous Improvement
Certification under ISO 14732 is not a one-time event. The standard requires periodic re-validation to ensure that an operator's skills remain sharp and that they stay current with the procedures. Typically, a welding operator's qualification is valid for a set period (e.g., three years), provided they are continuously working within the scope of their qualification.
Companies must maintain detailed records to prove this continuity of work for each operator. If an operator has not performed any welding for a period (e.g., more than six months), a re-test is required. This system ensures that the certification remains a relevant and accurate indicator of current competence.
Furthermore, the entire quality system should be subject to a process of continuous improvement. Data from weld logs, inspection reports, and NDT results should be analyzed to identify trends or opportunities for refinement. This might lead to adjustments in training programs or updates to a WPS. This commitment to maintaining and improving upon the certified standards is the hallmark of a world-class manufacturing organization.
Conclusion
Ultimately, embracing ISO 14732 for orbital welding stainless tubes is about risk mitigation and quality assurance. It standardizes operator competence, guarantees process repeatability, and provides the documented proof of excellence that critical industries and global markets demand in today's competitive landscape.
-
Discover how operator competence affects automated welding outcomes in regulated industries ↩
-
Understand the role of WPS in maintaining consistency and quality in industrial welding ↩
-
Discover how ISO 14732 sets international preparation and documentation standards ↩
-
See what data to verify in MTCs before welding as per global standards ↩
-
Get practical guidelines for ensuring consistent arc stability and weld quality ↩
-
Understand the definition, purpose, and criticality of WPS in welding automation ↩
-
Discover applications and industry practices for orbital welding in high purity systems ↩
-
Find out the benefits of electronic traceability and its impact on weld quality and accountability ↩
Have Questions or Need More Information?
Get in touch with us for personalized assistance and expert advice.