How to Pack Stainless Pipes for Export: 5 Steps
Are you worried about your stainless steel pipes arriving at their international destination damaged and corroded? This common problem can lead to costly project delays, budget overruns, and a damaged reputation. The solution lies in a meticulous, professional packing process that protects your investment from start to finish.
Stainless steel pipe export packing involves cleaning and drying the pipes, applying surface protection, bundling them securely, and placing them in a transport container like a wooden crate. Key steps include using end caps, wrapping bundles, securing them with strapping, and adding dunnage to prevent movement.
As the Global Business Director at MFY, I’ve seen firsthand how an overlooked detail in packing can jeopardize a multi-million dollar project. It’s more than just putting pipes in a box; it’s about delivering on a promise of quality and reliability. In this guide, I’ll walk you through the exact steps we use to ensure our stainless steel products arrive in perfect condition, every time.
This process isn't just about logistics; it’s a core part of our business strategy. In an industry where supply chain disruptions can cost up to 2% of annual revenue, robust packing1 is a powerful competitive advantage. It's a tangible expression of our commitment to quality that our clients in manufacturing, construction, and distribution have come to rely on. By investing in superior packing, we're not just protecting steel; we're safeguarding our clients' projects, timelines, and bottom lines, reinforcing our vision to be a leading brand in the global stainless steel trade.
How to prepare stainless pipes for packing?
Ever had a shipment arrive with surface stains or scratches that happened before it was even packed? Failing to prepare pipes properly negates any packing effort that follows. A thorough preparation stage is the critical first step to ensuring the final product is flawless upon arrival.
To prepare stainless pipes for packing, first conduct a thorough visual inspection and cleaning to remove any contaminants. Then, apply appropriate surface protection like plastic film or VCI paper. ly, segregate and bundle the pipes by size, grade, and length for stability and handling efficiency.
Preparation is the foundation of effective export packing. It’s a disciplined process that prevents the most common and avoidable types of product degradation. Simply cleaning the pipes is not enough; we must also protect their surfaces and organize them for safe handling. I remember a case with a new client in India who was building a large-scale water treatment facility. They had previously sourced from a supplier whose pipes arrived with residual grease marks and minor surface corrosion from condensation trapped under loose wrapping. This caused minor, yet costly, delays as each pipe needed to be manually cleaned on-site. When they switched to MFY, the first thing they noted was the pristine condition of our pipes upon unboxing. This wasn't an accident. It was the result of a multi-step preparation protocol that ensures every pipe is inspected, cleaned, protected, and properly organized before it ever sees the inside of a crate. This initial phase sets the standard for the quality we deliver and prevents the small issues that create big headaches for our clients down the line. It transforms packing from a mere logistical task into an integral part of our quality assurance promise.
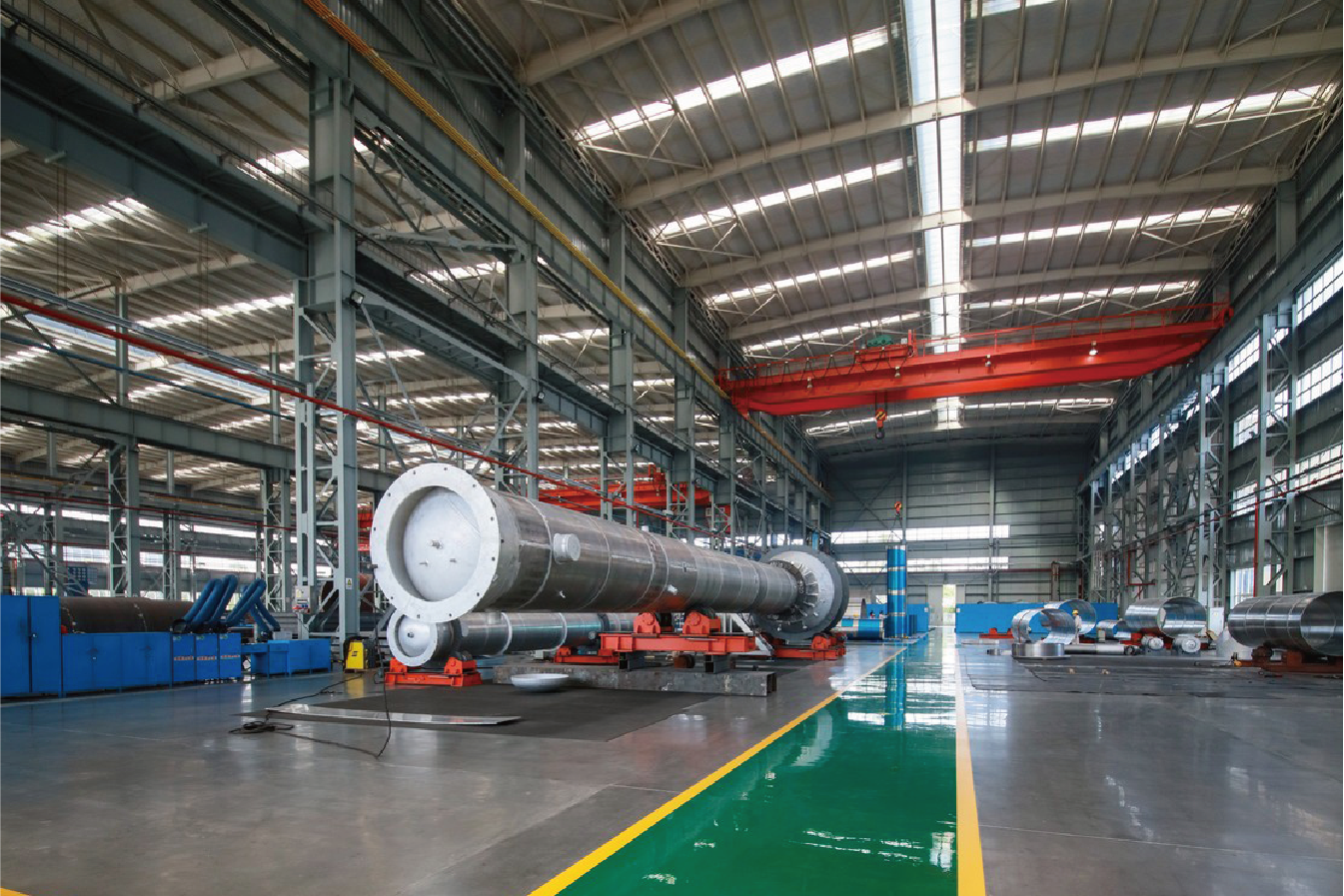
The preparation stage is far more nuanced than a simple wipe-down. It's a systematic approach to quality preservation that begins the moment the pipes leave the production line. At MFY, we view this as the first line of defense in maintaining the integrity of our products throughout their journey. The goal is to create a perfect "blank slate" so that the subsequent packing steps can be maximally effective. This involves not just cleaning, but a strategic assessment of each pipe's condition and requirements before it is bundled.
Initial Inspection and Cleaning
The very first step is a meticulous visual and physical inspection. Each stainless steel pipe is examined for any surface imperfections, such as scratches or dents, that may have occurred during manufacturing or internal transit. More importantly, we inspect for any residues. Manufacturing processes can leave behind oils, lubricants, or dust. If not removed, these substances can interfere with protective coatings and even trap moisture, creating a breeding ground for localized corrosion. According to a study by the Materials Technology Institute, over 30% of premature stainless steel failures can be traced back to surface contaminants that were present before the material was even put into service.
Our process involves using industry-approved, non-chlorinated solvents to gently remove any grease or oil without harming the steel's passive layer. This is followed by a thorough drying process, as any remaining moisture is a significant risk, especially for shipments crossing different climate zones. We train our teams to understand that a pipe that looks "clean" to the naked eye may still hold microscopic contaminants, making this a critical, non-negotiable step. For a client in the food and beverage industry, for whom hygiene is paramount, this level of cleaning isn't just a best practice—it's a contractual requirement that we fulfill with precision.
Surface Protection Application
Once a pipe is certified clean and dry, the next step is to apply a layer of surface protection. The type of protection depends on the grade of the stainless steel, the duration and conditions of the transit, and the client's specific requirements. For short-term transport or pipes that are less sensitive, a simple, durable polyethylene (PE) film might suffice. This film acts as a physical barrier against dust, scuffs, and minor scratches. However, for long-haul sea freight, especially to humid regions like Southeast Asia or the Middle East, we take it a step further.
We often use Volatile Corrosion Inhibitor (VCI) paper or film. This advanced material releases a harmless, odorless vapor that forms a microscopic, corrosion-inhibiting layer on the surface of the steel. This layer is self-replenishing and protects the metal even in areas that aren't in direct contact with the paper. This is particularly crucial for protecting the vulnerable pipe ends and interiors. This proactive anti-corrosion measure is a key part of our value proposition, ensuring that a client in, for example, a coastal region of Russia receives pipes as pristine as the day they were made, preventing costly surface finishing work upon arrival.
Segregation and Bundling Strategy
The final preparation step is strategic segregation and bundling. Packing a mix of different pipe diameters, wall thicknesses, and lengths together without a clear system is a recipe for disaster. It creates instability, increases the risk of pipes knocking against each other, and makes handling at the destination inefficient and unsafe. Our protocol dictates that pipes be sorted by their key specifications. This organized approach forms the basis for creating stable, uniform bundles.
We then bundle these segregated pipes into hexagonal or square shapes, which are inherently more stable and space-efficient than simple round bundles. The method we choose depends on the pipe diameter and quantity. For smaller diameter pipes, a hexagonal bundle secured with steel strapping is often ideal. For larger, heavier pipes, we might create a square bundle strapped to a custom-built wooden cradle. This pre-bundling strategy is critical. It simplifies the final packing process, optimizes space within the shipping crate or container, and most importantly, minimizes internal movement. By creating tight, stable units, we drastically reduce the forces exerted on individual pipes during transit.
Bundling Method | Best For | Advantages | Disadvantages |
---|---|---|---|
Hexagonal Bundle | Small to medium diameter pipes (e.g., < 4 inches) | Highly stable, space-efficient, self-supporting shape. | Can be complex to assemble without proper equipment. |
Square/Rectangular Bundle | Medium to large diameter pipes | Easy to stack, stable base, simple to secure. | Less space-efficient than hexagonal bundles. |
Cradled Bundle | Very large or heavy-walled pipes | Provides maximum support, prevents rolling, ideal for lifting. | Requires custom wooden cradles, increasing cost and weight. |
Loose Loading | Not Recommended for Export | - | High risk of damage, inefficient use of space, unsafe handling. |
Inspection prevents corrosionTrue
Thorough inspection and cleaning remove contaminants that could lead to corrosion during transit, as mentioned in the article.
VCI paper is optionalFalse
VCI paper is crucial for long-haul sea freight to humid regions, forming a protective layer against corrosion, as explained in the article.
What materials are necessary for packing stainless pipes?
Using the wrong packing materials is like building a house on a weak foundation. You might think a generic wooden box and some plastic wrap are enough, but this approach often leads to failure. Selecting the right, high-quality materials is essential for creating a truly protective shipping solution.
Essential materials for packing stainless pipes include plastic end caps to protect pipe ends, bubble wrap or VCI paper for surface protection, and steel or polyester strapping for bundling. For transport, use ISPM 15 compliant wooden crates, metal cages, or cradles, with dunnage for stabilization.
The choice of materials is where theory meets practice. Each material in our packing process serves a specific, vital function in a multi-layered defense system. It’s not about using the most expensive options, but the correct options for the job. From the humble end cap to the robust wooden crate, every component works in concert to absorb shock, prevent corrosion, and maintain structural integrity. I recall a shipment for a construction contractor in the Middle East. The project involved high-grade polished pipes for an architectural feature. The client was extremely concerned about surface scratches. Instead of standard wrapping, we used a soft, non-woven fabric wrap under a layer of bubble wrap for each pipe. We used custom-molded plastic end caps that friction-fit perfectly. The pipes were then bundled and placed in a plywood-lined wooden crate. This tailored material selection ensured that the aesthetic quality, which was just as important as the structural quality for this project, was perfectly preserved over a 4,000-mile journey. This demonstrates our philosophy: understand the risks and the client's needs, then engineer a material solution to match. It’s a deliberate, thoughtful process.
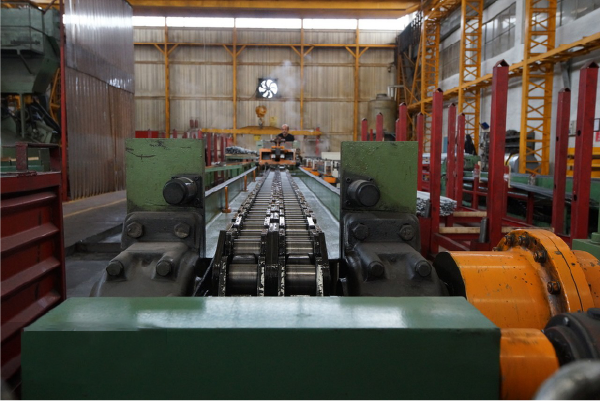
Selecting the right packing materials is a science in itself, balancing protection, cost, weight, and regulatory compliance. At MFY, our material selection process is rigorous and is based on decades of experience in exporting to diverse and challenging markets. We consider the entire journey of the pipe, from our factory floor to the client's final storage location. This holistic view ensures that our multi-layered protection strategy is robust enough to handle the stresses of international shipping, including handling, vibration, and climatic changes. Our goal is to create a self-contained environment for the pipes that preserves their condition regardless of external factors.
Primary Protective Materials
These are the materials that come into direct contact with the stainless steel pipes, forming the first and most critical layer of defense. The most basic and non-negotiable component is the plastic end cap. Pipe ends are particularly vulnerable to impact damage and distortion, which can render a pipe unusable. We use heavy-duty, tightly fitting plastic caps to seal both ends, preventing physical damage and also keeping contaminants and moisture out of the pipe's interior. This is especially crucial for pipes intended for fluid or gas transport, where internal cleanliness is paramount.
The next material is the surface wrap. As mentioned, this could be polyethylene (PE) film, bubble wrap, or VCI paper. For general-purpose pipes, a PE film provides adequate protection against dust and scratches. For pipes with polished or sensitive finishes, or for clients in high-humidity zones, bubble wrap offers cushioning while VCI paper provides active corrosion prevention. We recently fulfilled an order for a major equipment integrator in Southeast Asia. Knowing the shipment would spend weeks at sea and potentially sit in a humid port, we used VCI-impregnated bubble wrap, combining physical cushioning with chemical protection. This dual-function material added minimal cost but provided maximum peace of mind, preventing any possibility of surface rust.
Structural and Bundling Materials
Once the pipes are individually protected, we move to materials that create secure, handleable units. Steel or high-tensile polyester strapping is used to bind the pipes into tight, stable bundles. Steel strapping offers superior strength and rigidity, ideal for heavy-walled pipes. However, polyester strapping is often preferred as it has a slight elasticity to absorb shocks without breaking, and it won't rust or stain the pipe surfaces if the primary wrap is somehow breached. The choice depends on the bundle's weight and the shipping method.
The primary transport packaging is typically a wooden crate. These aren't just any wooden boxes. All wood used for our export crates must be heat-treated or fumigated according to the International Standards for Phytosanitary Measures No. 15 (ISPM 15). This regulation prevents the international transport of pests and is a strict requirement for customs clearance in most countries, including all our key markets in India, the Middle East, and Russia. Our crates are custom-built to the dimensions of the pipe bundle, minimizing empty space. Inside the crate, we use dunnage—materials like wood blocks, foam, or air bags—to brace the bundle and prevent any movement, which is the primary cause of in-transit damage.
Environmental Considerations and Material Innovations
As a forward-thinking company, we are also deeply invested in the sustainability of our packing materials. While providing maximum protection is our priority, we actively seek out and test environmentally friendly alternatives. For instance, we are exploring the use of recycled or biodegradable plastics for our end caps and wrapping films. We also work with our wood suppliers to ensure they source from sustainably managed forests.
Furthermore, we conduct a continuous cost-benefit analysis of new materials on the market. Innovations like reinforced fiber straps, which offer the strength of steel at a fraction of the weight, can lead to lower shipping costs for our clients. We also offer packaging consolidation services for our distributor clients, designing packaging systems that are not only protective for export but also efficient for their local storage and distribution needs. This commitment to material science and sustainability is part of our mission to build efficient, resilient, and responsible supply chains for our global partners.
Dunnage prevents in-transit movementTrue
Dunnage materials like wood blocks or foam brace the pipe bundle to prevent movement, which is a primary cause of damage.
Standard PE film is sufficient for polished pipesFalse
Polished or sensitive pipes require bubble wrap or VCI paper for extra protection, not just standard PE film.
How to ensure the safety and integrity of stainless pipes during packing?
You've prepared the pipes and have the right materials. But what if the packing process itself causes damage? A dropped pipe or an improperly handled bundle can undo all your careful preparation. Ensuring safety and integrity during the packing operation requires disciplined procedures and a vigilant team.
To ensure safety and integrity, implement a multi-point quality check system throughout the packing process. Use proper handling equipment, like nylon slings instead of steel chains, to prevent surface damage. Meticulously document each step, creating a traceable record for quality assurance and accountability.
Ensuring safety and integrity during the packing process is about transforming a manual task into a controlled, repeatable procedure. It's where human skill and systemic checks intersect to guarantee a flawless outcome. This isn't just about avoiding dents and scratches; it's about embedding quality into every action. At MFY, every member of our packing team is a trained quality assurance agent. They aren't just packing pipes; they are upholding our brand promise. For a large engineering and construction contractor2 working on a critical infrastructure project, receiving a single damaged pipe can have a domino effect on their timeline. They rely on us not just for the steel itself, but for the certainty that it will arrive ready for immediate installation. I once visited a client's site where they showed me a "graveyard" of damaged materials from other suppliers—a stark reminder of the cost of carelessness. This is why our internal motto is "handle every pipe as if it's the final product." This mindset is supported by a robust framework of checks, proper equipment, and detailed documentation, ensuring that our commitment to integrity is reflected in every package we ship.
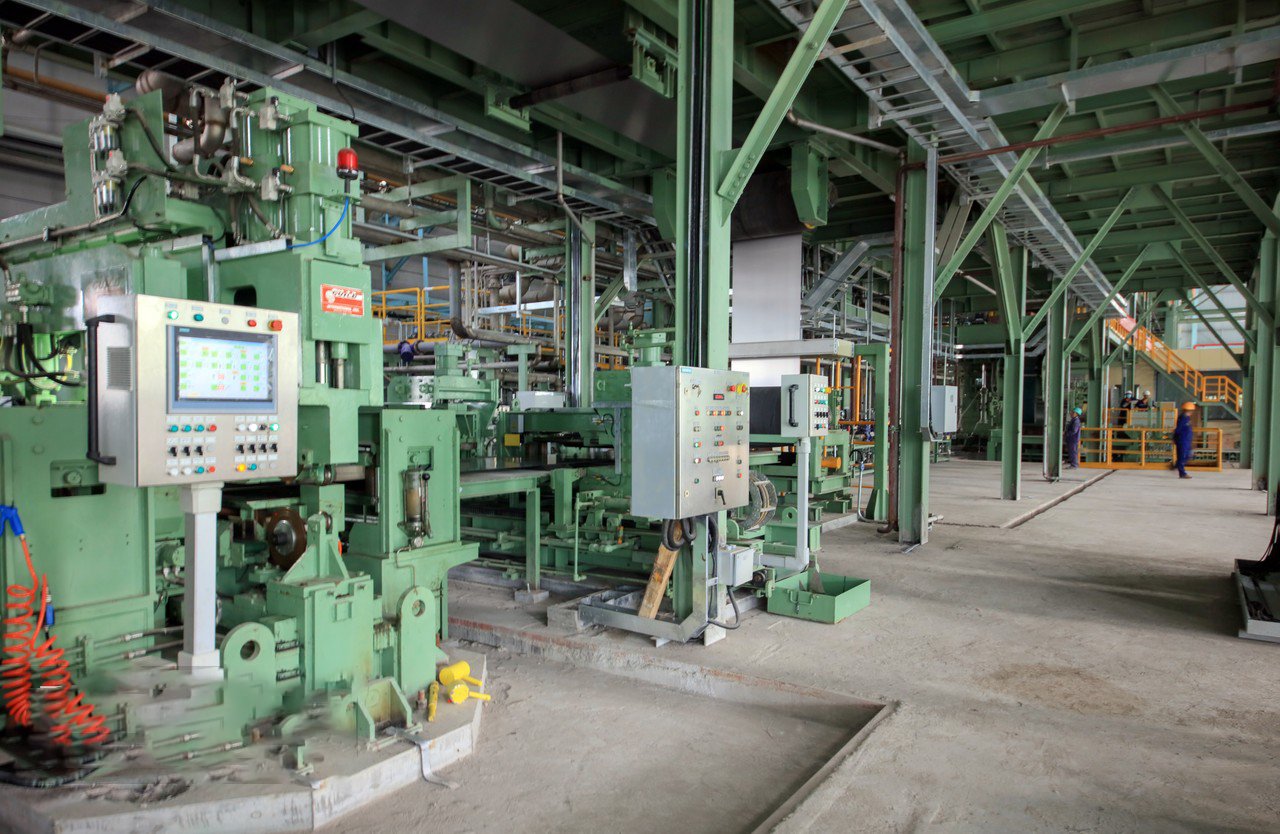
The packing area at MFY is not just a logistics hub; it’s a zero-tolerance zone for error. We have engineered a systematic process that minimizes risk at every touchpoint. Ensuring the safety and integrity of the pipes during the packing phase is a dynamic process that combines trained personnel, specialized equipment, and a rigorous verification system. This operational excellence is what allows us to confidently ship high-value, sensitive stainless steel products across the globe, knowing they are protected from our door to the client's.
Implementing a Multi-Point Check System
A foundational element of our process is the multi-point check system. Quality isn't just inspected at the end; it's verified at every stage. The first check happens during preparation, as discussed. A second check occurs after the primary wrap is applied, ensuring complete coverage and proper sealing. A third check is performed after bundling, verifying the tension of the straps and the stability of the bundle. A final, critical inspection happens just before the crate is sealed. A supervisor signs off on a detailed checklist that confirms the bundle is properly braced, dunnage is correctly placed, and all required documentation (like packing lists and VCI indicators) is included.
This systematic checking process creates multiple opportunities to catch and correct any potential issues before they become problems. For example, a strap that is too tight could damage the wrapping and the pipe surface, while a strap that is too loose could lead to bundle failure. Our calibrated tensioning tools and trained operators, combined with supervisory checks, mitigate this risk. A report from the Logistics Bureau3 suggests that implementing such process-based quality checks can reduce error rates by over 50%, a figure we have validated through our own internal metrics.
Proper Handling Techniques and Equipment
The physical handling of heavy, and often long, stainless steel pipes presents a significant risk of damage. Dropping a bundle or scraping it against a hard surface can cause irreparable harm. To prevent this, we exclusively use handling equipment designed for surface protection. Instead of bare steel forks or chains, our forklifts are fitted with rubber or polyurethane guards. When lifting bundles with cranes, we use wide, soft nylon slings rather than steel cables. These slings distribute the load over a larger surface area and eliminate the risk of metal-on-metal contact that can scratch, gouge, or compromise the steel's passive layer.
Our teams undergo regular training on safe handling procedures, including proper lifting techniques and communication protocols. For a client supplying sanitary pipes4 to the pharmaceutical industry, even a minor surface scratch can create a potential site for bacterial growth, rendering the pipe useless. Our meticulous handling procedures are not just a best practice; they are essential for serving clients in high-stakes industries where material perfection is a functional necessity.
Case Study: Preventing In-Transit Corrosion for a Southeast Asian Client
A powerful illustration of our process is a case involving a large distributor in a coastal city in Southeast Asia, where atmospheric humidity regularly exceeds 85%. They had placed a significant order for 304-grade stainless steel pipes, which, while corrosion-resistant, can be susceptible to surface staining and pitting in persistently moist, saline environments if not packed correctly. Their previous international supplier had packed the pipes in standard wooden crates with simple plastic sheeting. Upon arrival, a significant percentage of the pipes showed signs of superficial "tea staining" from condensation that had formed and been trapped during the long sea voyage.
To prevent this, we executed our full protective packing protocol. After cleaning, each pipe was wrapped in VCI paper. The bundles were strapped with polyester bands to avoid any potential galvanic reaction. Inside the ISPM 15-stamped, plywood-lined wooden crate, we placed several large desiccant bags to absorb any ambient moisture that might penetrate the container. We also placed a humidity indicator card inside the crate, which provides a visual confirmation upon arrival that the internal humidity remained below the risk threshold. The result? The pipes arrived in flawless condition. The client was able to immediately stock and resell the products without costly and time-consuming cleaning or refinishing. This success solidified our partnership and demonstrated that investing in the right materials and procedures is a direct investment in the client’s success and our own reputation.
Nylon slings prevent surface damageTrue
Nylon slings distribute weight evenly and eliminate metal-on-metal contact that could scratch pipes.
Steel chains are safer than nylonFalse
Steel chains can cause surface damage through scraping and galvanic reactions, unlike protective nylon slings.
What are the steps to secure stainless pipes in transport packaging?
Packing pipes in a crate is only half the battle. If the contents can shift, slide, or vibrate during transit, they will arrive damaged. The violent forces inside a shipping container on rough seas are immense. Securing the load properly is the crucial final step to ensure it remains static.
To secure stainless pipes, first place the bundled pipes into a custom-fit crate. Then, use blocking and bracing techniques with wooden dunnage to eliminate all empty space. Secure the bundle with lashing or strapping, and ensure the crate's weight is distributed evenly for safe transport.
Securing the load within the transport packaging is a matter of physics and foresight. We are essentially creating a rigid, monolithic block out of what started as a collection of individual pipes. The goal is to make the contents and the container move as one single unit, eliminating the destructive energy of internal impacts. An unsecured or poorly secured load is one of the top causes of cargo damage claims in the logistics industry. I've heard horror stories from freight forwarders about containers opening to reveal what looks like a pile of scrap metal5 that started as high-value pipes. A construction contractor working on a tight schedule for an LNG plant in Russia cannot afford such a failure. A delay in receiving usable pipes can halt a critical phase of construction, costing them hundreds of thousands of dollars per day. That is why our securing process is so rigid. We analyze the weight, dimensions, and center of gravity of each bundle to engineer a specific bracing plan that will counteract the forces of acceleration, braking, and lateral movement during its entire journey, whether by truck, rail, or ocean vessel.

The process of securing stainless steel pipes within their transport packaging—be it a crate or a full container—is a critical engineering task. It's about anticipating the dynamic forces of transit and systematically neutralizing them. At MFY, we treat this stage with the same precision as our manufacturing processes. An improperly secured load can lead to catastrophic failure, damaging not only the product but also the transport vehicle and posing a safety risk to personnel. Our methodology is built on established principles of cargo securing and is tailored to the specific characteristics of stainless steel pipes6.
The Art of Blocking and Bracing
Once a bundle of pipes is placed inside its wooden crate, the primary goal is to eliminate any free space where movement could begin. This is achieved through blocking and bracing. Blocking involves using pieces of wood (dunnage) nailed or screwed to the crate floor and walls to prevent the bundle from sliding or shifting. Bracing involves using larger timber structures to support the load and transfer forces to the strongest parts of the crate. We build a custom "cage" of wood around the bundle.
The key is to ensure these braces are snug against the load, leaving no gaps. For a 20-ton bundle of pipes, the forces generated during an emergency brake or a ship's roll can be immense. According to the IMO's Code of Safe Practice for Cargo Stowage and Securing, cargo can be subjected to forces equivalent to its entire weight in multiple directions. Our bracing is designed to withstand these peak forces. We use specific wood densities and nail patterns, calculated to provide the necessary strength without adding excessive weight. This meticulous internal construction ensures the bundle remains completely immobilized from our factory to the client's destination.
Correct Application of Strapping and Lashing
In addition to blocking and bracing, internal strapping or lashing can be used to anchor the bundle to the crate itself. While the bundle is already strapped, these secondary lashings provide an extra layer of security. We might use heavy-duty polyester lashing straps, anchored to reinforced points within the crate. The tension applied to these straps is critical and is measured with a tensioner to ensure it is within the specified range—tight enough to prevent movement, but not so tight as to damage the bundle or the crate structure.
For particularly heavy or high-value shipments, we often use a combination of techniques. For example, a large-diameter pipe bundle might be settled into a custom-built wooden cradle (a form of bracing), then blocked at both ends, and finally lashed down to the crate floor. This multi-modal approach ensures redundancy. If one securing element were to fail under extreme stress, the others would continue to hold the load in place. This is part of our risk mitigation strategy that gives clients, especially those in the project-critical engineering and construction sectors, confidence in our delivery capabilities.
Weight Distribution and Center of Gravity
ly, securing is not just about preventing movement inside the crate, but also about ensuring the crate itself is stable and safe to handle. Before sealing the crate, we confirm that the weight is distributed as evenly as possible. An off-balance load can be extremely dangerous to lift with a forklift or crane and can cause instability during transit. The center of gravity is kept as low and as central as possible.
When loading multiple crates into a shipping container, the same principles apply on a larger scale. We create a loading plan that distributes weight evenly across the container floor. Heavier crates are placed on the bottom, and the entire load is blocked and braced against the container walls. We use inflatable dunnage bags to fill any larger voids between crates. This meticulous attention to weight distribution ensures compliance with road and maritime safety regulations and is the final step in our end-to-end process for securing our clients' valuable assets for their journey across the world.
Blocking prevents pipe movementTrue
Wooden dunnage is nailed to crate walls/floor to eliminate sliding space.
Straps alone secure heavy pipesFalse
High-value shipments require combined blocking, bracing AND lashing for redundancy.
How to label stainless pipe packages for export?
What good is perfectly packed pipe if it gets lost, delayed at customs, or mishandled by the freight company? Improper or incomplete labeling is a simple mistake that can cause massive logistical nightmares. Clear, accurate, and durable labeling is the silent guide for your shipment's journey.
To label stainless pipe packages for export, include the shipper's and consignee's details, country of origin, port of loading/discharge, net/gross weight, and dimensions. Also, add handling symbols (ISO 780), a packing list, and any required regulatory marks like the ISPM 15 stamp.
Labeling is the voice of the package. It communicates critical information to every person who will interact with it—from our warehouse team to freight forwarders, customs officials, and the client's receiving crew. A missing detail can bring a shipment to a grinding halt. I remember an urgent shipment for a manufacturing client in India that was held up in customs for a week simply because a previous supplier had forgotten to include the gross weight on the documentation, creating a discrepancy. This delay nearly shut down their production line. At MFY, we've developed a standardized, digitally integrated labeling system to prevent such errors. Our labels are designed for clarity, durability, and compliance. They contain multiple layers of information, from human-readable text to machine-scannable barcodes, ensuring that the package can be identified, handled correctly, and processed efficiently at every single checkpoint on its way to the client. This system transforms the label from a simple sticker into a key component of a resilient and transparent supply chain.
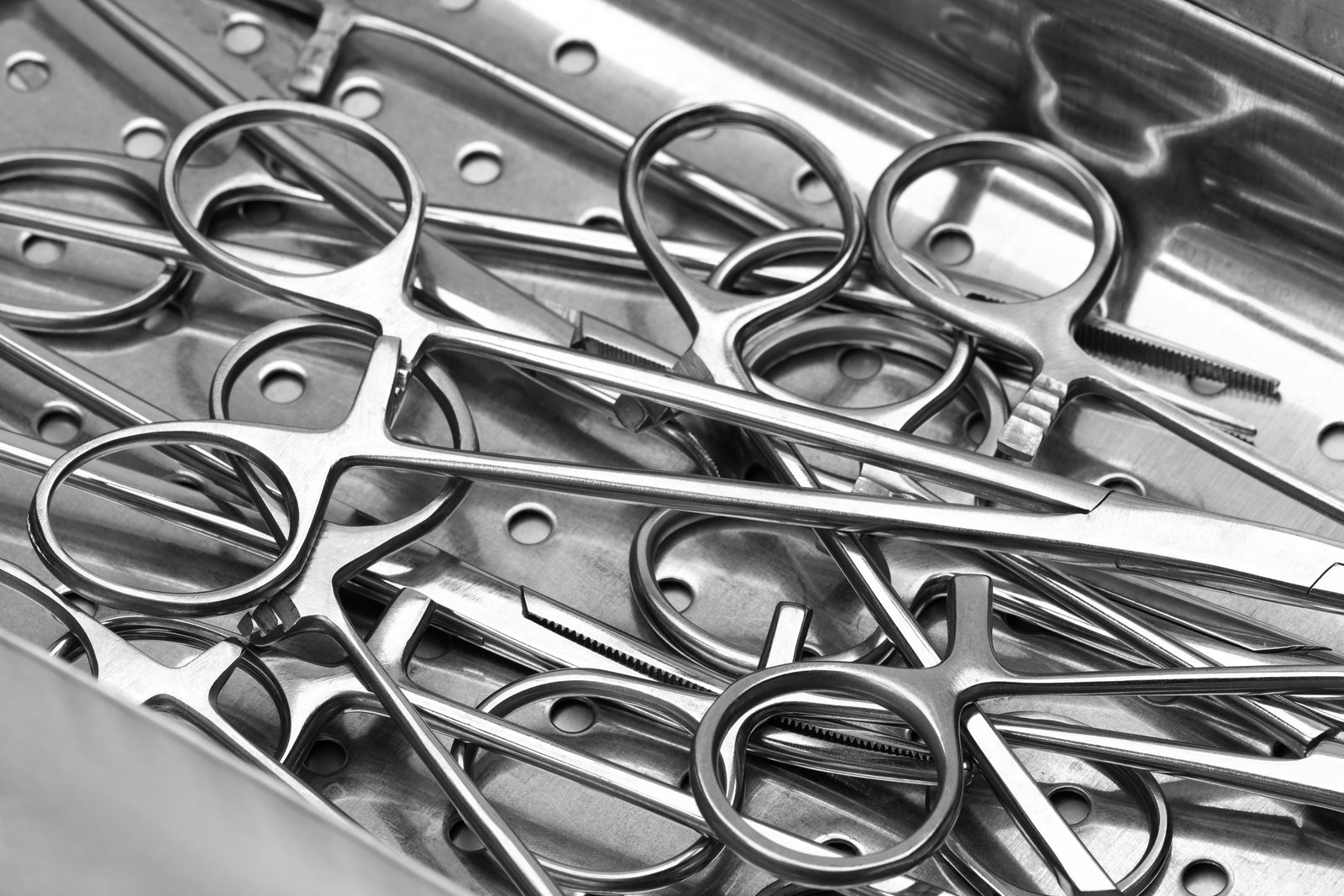
Export labeling is a discipline of precision and compliance. It goes far beyond a simple "To/From" address. Each element on the label serves a legal, logistical, or safety purpose. A well-executed labeling strategy is indispensable for a smooth customs clearance process and ensures the safe and efficient handling of the cargo. At MFY, our labeling protocol is a comprehensive system designed to meet international standards, leverage digital technology, and provide our clients with complete visibility from dispatch to delivery.
Meeting International and Customs Standards
The foundation of our labeling process is compliance with international regulations. Every crate is clearly marked with essential information required by customs authorities worldwide. This includes the full name and address of the shipper (MFY) and the consignee (the client), the final destination country, and the port of loading and discharge. We specify the net weight (product only) and gross weight (product plus packaging) in both kilograms and pounds, as well as the external dimensions of the crate in meters and feet. A unique package number (e.g., "1 of 5") is critical for keeping multi-crate shipments together.
Crucially, our wooden crates bear the ISPM 15 stamp. This is a permanent, visible mark indicating that the wood packaging material has been treated to international standards, a mandatory requirement for entry into most countries. We also use standardized pictorial handling symbols (ISO 780). Symbols like "Sling Here," "Keep Dry," and "Center of Gravity" transcend language barriers, ensuring that cargo handlers in any country understand how to manage the crate safely without having to read text. This universal language is vital for protecting the integrity of the shipment.
Internal Tracking and Identification
Beyond international requirements, our labels incorporate features for our own and our clients' tracking systems. Each crate is assigned a unique tracking number, which is represented as a barcode and a QR code. This code is the key that unlocks a wealth of digital information. When scanned, it links to our central database, providing instant access to the detailed packing list, material test certificates, the manufacturing date, and the full order details.
This digital integration is a core part of our competitive strength. For our distributor and trader clients, this provides a powerful tool for inventory management. When a shipment arrives, they can scan the QR code to automatically populate their warehouse management system with all the necessary product data, saving time and eliminating manual entry errors. This digital handshake between our system and our client's system is a perfect example of our commitment to leveraging technology to build more efficient supply chains.
Placement and Durability of Labels
A label is useless if it falls off or becomes illegible during transit. Shipments are exposed to rain, sun, friction, and handling, so label durability is paramount. We use industrial-grade, weather-resistant labels with permanent adhesive. For critical information like the ISPM 15 stamp, the mark is heat-branded or stenciled directly onto the wood itself.
Placement is equally important. We follow the standard practice of placing main labels on at least two adjacent sides of the crate. This ensures that the information is visible regardless of how the crate is stacked or positioned in a container or warehouse. A securely attached, weatherproof document pouch is also affixed to the crate, containing a hard copy of the detailed packing list and any other required shipping documents. This redundancy ensures that even if there is a digital systems failure at a port, the essential paperwork is still available with the physical goods, providing a final layer of security for a smooth and timely delivery.
ISPM 15 stamp is mandatoryTrue
The ISPM 15 stamp indicates wood packaging has been treated to international standards, required by most countries.
Labels go on one side onlyFalse
Labels should be placed on at least two adjacent sides for visibility regardless of crate orientation.
Conclusion
Ultimately, meticulous export packing is not a cost but a vital investment. It is the final, crucial step in fulfilling our quality promise, ensuring that our stainless steel pipes arrive safely and on time. This commitment to excellence protects our clients' projects and builds lasting trust.
-
Discover how robust packing can minimize risks and maintain product integrity in transit ↩
-
Learn the impact of damaged materials on project timelines and costs. ↩
-
Discover how systematic checks reduce error rates in the logistics industry. ↩
-
Understand how scratches can compromise sanitary standards and product usability. ↩
-
Learn about common factors leading to cargo damage in transit and prevention methods ↩
-
Discover the unique characteristics that affect the securing process for stainless steel pipes ↩
Have Questions or Need More Information?
Get in touch with us for personalized assistance and expert advice.