Export Packaging for Stainless Steel Coils: Checklist
Shipping thousands of dollars worth of pristine stainless steel coils across oceans, only to have them arrive rusted, dented, or scratched? The fear of a rejected shipment and catastrophic financial loss is a constant worry for any global business. Don't let poor packaging undermine your product quality.
Export packaging for stainless steel coils involves a multi-layered system including quality inspection, anti-corrosion measures like VCI paper and desiccants, robust physical protection with materials like kraft paper, plastic film, and steel wrapping, clear labeling, and secure container loading to prevent damage during transit.
As the Global Business Director for MFY, I’ve overseen countless shipments to demanding markets in India, Southeast Asia, and beyond. The difference between a happy, repeat customer and a costly insurance claim almost always comes down to the discipline and precision of the packaging process. It's a science we've perfected over years of experience.
This checklist is more than a set of instructions; it's a framework for risk mitigation. I want to guide you through the critical checkpoints our own teams use, from the initial coil preparation to the final container seal. We'll explore the materials, the methods, and the documentation that form a fortress around your valuable assets, ensuring they arrive in factory-perfect condition, every time.
What are the preliminary steps to prepare stainless steel coils for export packaging?
Rushing to wrap a coil without proper prep work is like building a house on a weak foundation. If you miss a surface defect, a documentation error, or an unstable core, the best packaging in the world won't prevent a potential problem thousands of miles away.
Preliminary steps involve a thorough quality inspection of the coil for surface defects, verification of the coil's specifications against the order, and securing the inner diameter (the "eye") to provide a stable foundation for the subsequent layers of protective packaging.
Before any wrapping material touches a coil at MFY, a rigorous pre-packaging protocol is initiated. I remember a case with a new manufacturing client in India who was extremely sensitive to surface finish. Our pre-packaging inspection caught a minor oil stain, invisible to an untrained eye, on one of the coils. We were able to clean and re-verify the coil before it was wrapped. This small, disciplined step prevented a potential quality claim and solidified the client's trust in our process. It’s this unseen diligence that forms the bedrock of a reliable supply chain.
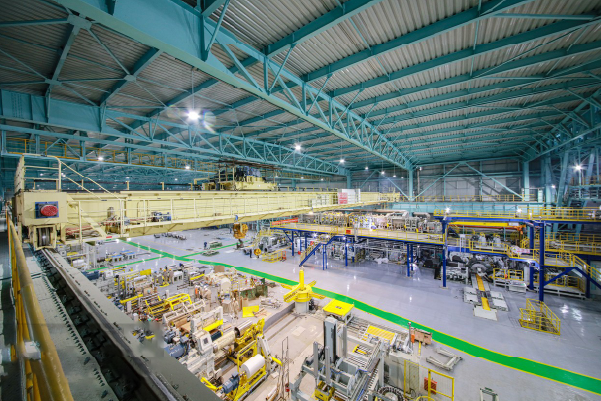
These initial steps are not mere formalities; they are the most critical quality gate in the entire logistics process. Skipping or rushing this stage introduces unnecessary risk that cascades through every subsequent step. A coil that is improperly documented, has an unseen defect, or is not structurally ready for transport is a liability waiting to happen. The entire philosophy of export packaging rests on starting with a perfect, well-documented, and stable product. To truly understand this foundation, we need to break it down into three distinct phases of preparation: the meticulous physical inspection of the coil itself, the crucial cross-verification of the product against the paperwork, and the often-overlooked but vital task of securing the coil’s core to ensure structural integrity from the inside out. Each phase is a critical checkpoint that ensures the packaging process begins on solid ground.
Quality Inspection and Surface Verification
The very first step is to treat the unwrapped stainless steel coil as a final product undergoing its last quality control check. This is the last opportunity to view the entire surface of the steel before it is concealed by layers of protective wrapping. Our teams at MFY are trained to perform a detailed visual inspection under proper lighting. They look for any potential surface imperfections that could have occurred during the final stages of production or handling. This includes checking for scratches, dents, roll marks, oil stains, or any discoloration. The standards for this inspection are dictated by the client's order; a coil destined for decorative architectural use, for example, will have a much higher standard for surface finish than one destined for industrial tank fabrication.
This inspection is not just a passive glance. It involves verifying the finish itself. For instance, if the order is for a No. 4 brushed finish, the inspector confirms the uniformity and direction of the grain. If it’s a 2B finish, they look for the characteristic smooth, reflective surface free from anomalies. We keep control samples from the production batch to compare against, ensuring absolute consistency. A digital surface roughness tester might even be used to provide a quantitative measure of the finish if required by the client's technical specifications.
Documenting this final check is paramount. The inspector signs off on a quality checklist for that specific coil ID, often taking high-resolution digital photographs of the surface. This creates a clear record of the coil's pristine condition before it was packaged. I recall a situation with a shipment to a distributor in the Middle East where minor surface marks were reported upon arrival. By providing our time-stamped, pre-packaging photos showing a flawless surface, we were able to help the client identify that the damage occurred during their own unpacking process, protecting both MFY from an unjust claim and helping the client improve their internal handling procedures.
Cross-Referencing with Order and Production Data
Once the physical coil has been verified, the next critical step is to ensure it is the correct coil for the order. This is a meticulous cross-referencing process that connects the physical product to its digital and paper trail. Every coil produced by MFY has a unique identification number. This ID is the key that unlocks all associated data. The packaging team leader will pull up the client's purchase order and the internal production order.
They will verify, point by point, that the physical coil matches the documentation. This includes checking the grade (e.g., 304, 316L), the dimensions (thickness and width), the weight, the finish (e.g., 2B, No. 4, BA), and any specified standards (ASTM, JIS, EN). For example, if the order specifies a coil of ASTM A240 Grade 316L with a 2B finish, a thickness of 1.2mm, and a width of 1219mm, the team confirms every single one of these parameters against the coil's production record. This eliminates the risk of shipping a correctly packaged but incorrect product—an error that can be incredibly costly to rectify once it has arrived at a foreign port.
This step also involves verifying the coil's Mill Test Certificate (MTC). The MTC is the material's birth certificate, detailing its exact chemical composition and mechanical properties. The team ensures the MTC corresponds to the correct coil ID and that it is ready to be included with the shipping documents. This meticulous administrative check ensures that what the client ordered is exactly what is being packaged, guaranteeing full traceability and compliance with their technical requirements.
Securing the Coil Eye for Structural Stability
With the quality and specifications confirmed, the final preliminary step focuses on the structural integrity of the coil itself. A stainless steel coil is essentially a very heavy, tightly wound spring. Its stability during transport depends on it remaining tightly wound. The center of the coil, known as the "eye," is the key to this stability. The packaging process begins at the eye.
Depending on the client's preference and the coil's size, the coil can be positioned with its eye to the sky (vertical) or eye to the side (horizontal). For eye-to-sky orientation, which is very common, the coil is placed on a specially designed pallet or skid. For eye-to-side, it is placed in a cradle. Regardless of orientation, the inner diameter must be protected and secured. This is typically done by fitting plastic or cardboard core plugs or protectors into the eye. These protectors prevent the inner wraps of the steel from being damaged or collapsing inward.
More importantly, strapping is often fed through the eye to secure the coil to its pallet or cradle. This is called circumferential strapping. These straps, typically made of high-strength polyester or steel, are tensioned and sealed, effectively locking the coil onto its base. This prevents the coil from shifting or unravelling from the inside out. It creates a stable, unified base unit upon which all the subsequent layers of protective wrapping will be built. Without this foundational step, the entire packaging structure would lack the necessary internal stability to withstand the dynamic forces of ocean transit.
Pre-packaging inspection prevents quality claimsTrue
The example shows how catching an oil stain during inspection prevented a potential rejection, demonstrating the value of thorough pre-packaging checks.
Coil orientation doesn't affect packagingFalse
The text specifies that eye-to-sky (vertical) and eye-to-side (horizontal) orientations require different handling and securing methods, making orientation a critical factor.
How to choose the appropriate packaging material for stainless steel coils?
Choosing packaging materials based on cost alone is a false economy. A cheap, flimsy paper might save pennies upfront, but it offers little protection against the humidity of ocean transit or the rough handling at a port, leading to thousands of dollars in damages. The material itself is your first line of defense.
Appropriate materials are chosen in a layered approach: soft, non-abrasive materials like VCI paper for direct contact; moisture barriers like plastic film; absorbent materials like kraft paper; and robust outer protection like hardboard and galvanized steel sheets.
The material selection is a science tailored to the journey. For a shipment to a humid market like Southeast Asia, we would never rely on kraft paper alone. We always mandate a layer of VCI (Vapor Corrosion Inhibitor) paper1 as the first wrap, followed by a waterproof plastic film. I once had a prospective client who was skeptical about the added cost of VCI. I showed them two small steel samples, one wrapped in standard paper and one in VCI, which we had left in our factory's humid outdoor environment for a month. The difference was stark: one was rust-free, the other was stained. This simple demonstration instantly proved the value of investing in the right protective material.
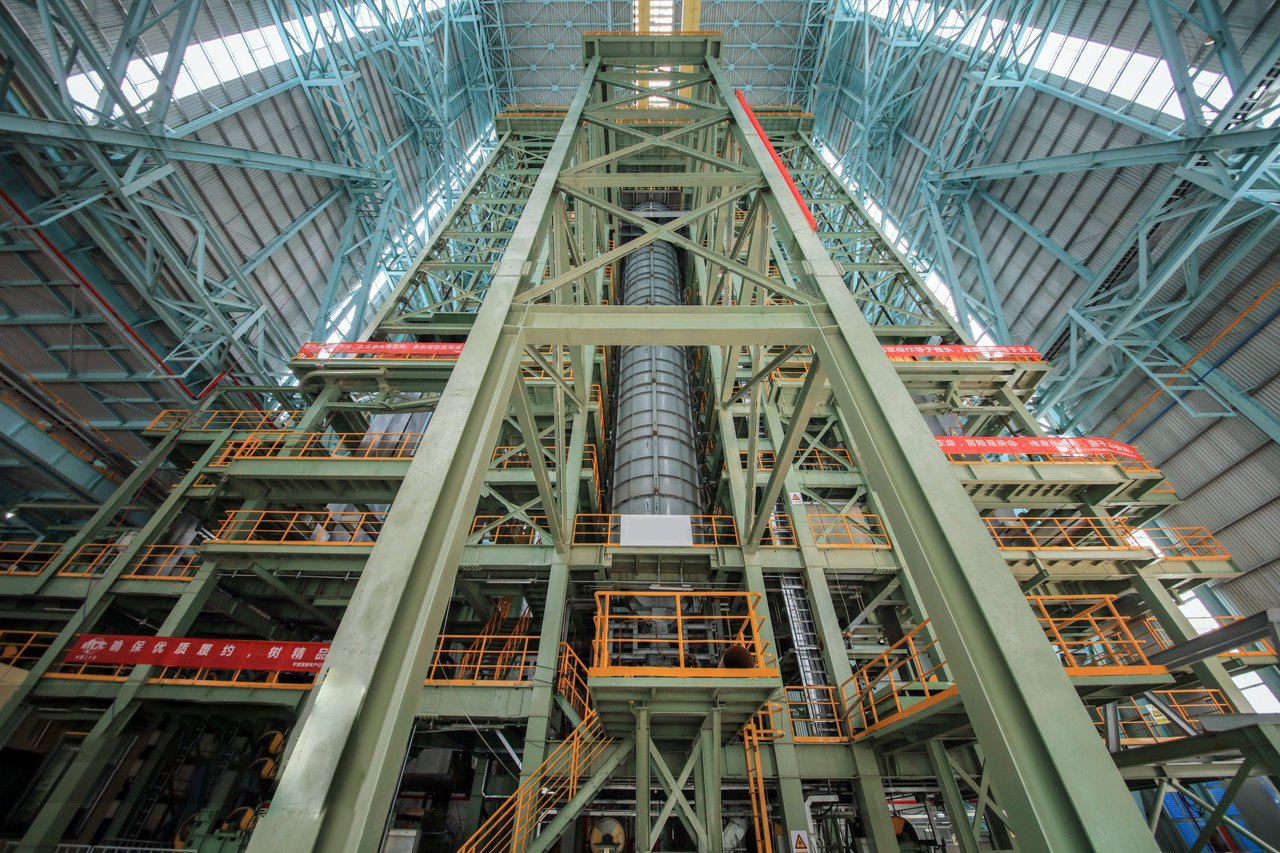
The selection of packaging materials is not a one-size-fits-all process. It is a carefully engineered system where each material plays a specific and complementary role. Think of it as dressing the coil for a long and arduous journey. You need a soft, breathable base layer against the skin, insulating mid-layers for cushioning and moisture management, and a tough, waterproof, and impact-resistant outer shell. The goal is to create a micro-environment inside the package that keeps the stainless steel coil in the exact same condition it was in when it left the factory floor. This requires a deep understanding of the properties of various materials and how they work together to combat the dual threats of physical damage and environmental corrosion. We will explore this system by examining the critical inner layers, the structural and impact-absorbing layers, and the final outer shield that faces the world.
The Inner Layers: Anti-Corrosion and Surface Protection
The materials that come into direct contact with the stainless steel surface are arguably the most critical. Their primary job is twofold: to provide a final barrier against corrosion and to ensure the pristine surface finish is not scratched or marred. The first layer applied is almost always a specialized anti-corrosion paper. At MFY, we exclusively use VCI (Vapor Corrosion Inhibitor) paper. This is not ordinary paper; it is impregnated with chemical compounds that sublimate (turn from a solid to a gas) within the enclosed space of the package. These vapor-phase inhibitors are drawn to the metal surface, forming a microscopic, invisible layer that disrupts the electrochemical process of corrosion. This is an active, ongoing protection that is essential for long sea voyages through varying temperatures and humidity levels.
Following the VCI paper, a layer of neutral kraft paper is often wrapped around the coil. Kraft paper is strong and absorbent, providing an additional layer of cushioning and, more importantly, a medium to absorb any potential condensation that might form inside the package despite the outer waterproofing. It acts as a blotting layer. This is then typically followed by a wrap of high-density polyethylene (HDPE) or similar plastic film. This layer serves as the primary waterproof barrier, preventing external moisture from ever reaching the inner layers and the steel surface.
The selection of these inner materials must be precise. The VCI paper must be fresh and from a reputable supplier to ensure its chemical potency. The kraft paper must be pH neutral to avoid any chemical reaction with the steel. The plastic film must be thick and durable enough to resist punctures. For coils with extremely delicate surfaces, like a mirror or bright annealed finish, an additional layer of soft, non-woven fabric might be used as the very first wrap before the VCI paper, providing an extra degree of soft cushioning against abrasion.
The Structural Layers: Cushioning and Impact Absorption
Once the sensitive surface is protected and sealed against moisture, the next layers are added to provide structural integrity and protection from physical impacts. These materials are designed to absorb and distribute the force from bumps, drops, or collisions that can occur during handling and transit. The most common material used for this purpose is hardboard or fiberboard. Thick, custom-cut discs of hardboard are placed on the inner and outer diameters (the ID and OD) of the coil. These act as rigid shields, protecting the vulnerable edges of the steel coil from being dented or deformed.
Around the circumference of the coil, several layers of corrugated cardboard or similar wrapping are applied. This provides a circumferential cushion. If the coil is positioned eye-to-sky on a pallet, this outer wrapping protects the sides from being scraped or impacted by other cargo or the container walls. The edges of the coil are particularly vulnerable. To protect them, molded plastic or thick cardboard edge protectors are often applied to the four "corners" (the inner and outer edges on both sides) of the coil before the final metal wrapping.
These structural layers must be robust. The thickness and density of the hardboard are chosen based on the weight and size of the coil—a heavier coil requires a more substantial shield. The entire system is held together by circumferential and radial straps made of high-tensile polyester. These straps are tensioned to compress the packaging layers tightly against the coil, creating a single, solid, and stable unit. This prevents any internal shifting of the packaging materials, which could lead to abrasion.
The Outer Shell: The Metallic Shield
The final layer of defense is the outer shell, which provides the ultimate protection against the elements and the rigors of shipping. This is almost always a full metal jacket. The entire packaged coil—now wrapped in VCI, paper, plastic, and hardboard—is encased in a final layer of thin-gauge galvanized steel sheet or, in some cases, a thick, durable plastic wrap. This outer steel wrapping provides a tough, puncture-proof, and fully waterproof barrier. It is the coil's armor.
This outer metal shell is meticulously applied. The hardboard discs at the ID and OD are covered with fitted galvanized steel caps. The circumference is wrapped with a long sheet of galvanized steel, with the edges interlocking and sealed to create a continuous barrier. This metallic shell ensures that even if the container is exposed to heavy rain or sea spray, no water can penetrate the package. It also provides a high degree of resistance to punctures from forklifts or other equipment.
This final layer is what the outside world sees and interacts with. It must be strong enough to withstand being stacked upon (within specified limits) and to resist the constant vibration and movement of a ship at sea. The choice of galvanized steel is deliberate; its zinc coating provides its own layer of corrosion resistance, ensuring that the packaging itself does not rust and stain other cargo or the container floor. Once this final metal shell is in place and strapped, the coil is fully protected and ready for labeling.
Packaging Layer | Material Example | Primary Function |
---|---|---|
Layer 1 (Contact) | VCI (Vapor Corrosion Inhibitor) Paper | Active Corrosion Prevention: Releases vapor that coats the steel surface. |
Layer 2 (Moisture) | Kraft Paper & Plastic Film (HDPE) | Moisture Barrier & Absorption: Prevents external water ingress and absorbs internal condensation. |
Layer 3 (Impact) | Hardboard Discs & Edge Protectors | Impact Resistance: Protects vulnerable edges and flat surfaces from dents and deformation. |
Layer 4 (Cushion) | Corrugated Cardboard Wrapping | Cushioning: Provides a circumferential buffer against side impacts and scrapes. |
Layer 5 (Strapping) | High-Tensile Polyester Straps | Unitization: Compresses all layers into a single, stable unit, preventing internal shifting. |
Layer 6 (Outer Shell) | Galvanized Steel Sheets/Caps | Armor & Waterproofing: Provides a final, puncture-proof, and fully waterproof exterior shield. |
VCI paper prevents corrosionTrue
VCI paper releases vapor-phase inhibitors that form a protective layer on stainless steel, actively preventing corrosion during transit.
Kraft paper is waterproofFalse
Kraft paper is absorbent and helps manage condensation, but it requires an additional plastic film layer for waterproofing.
Which protective measures should be taken to prevent corrosion during transit?
You've wrapped your coil perfectly, but an invisible enemy is lurking inside: humid air. Trapped moisture can condense as the shipment moves through different climate zones, causing rust and stains to form on the steel, rendering your meticulous packaging useless.
To prevent corrosion, a multi-faceted approach is required: first, wrap the coil in VCI (Vapor Corrosion Inhibitor) paper for active chemical protection, then seal it in waterproof film, and finally, add desiccant bags strategically to absorb any trapped residual moisture.
This combination is our standard protocol at MFY. I once had to explain this to an engineering contractor in a dry region who questioned the need for both VCI and desiccants. I explained that their coil would travel for weeks on a ship crossing the humid equator. The temperature fluctuations would create a "breathing" effect, causing condensation. The VCI provides the primary shield for the metal, while the desiccants act as "lungs," absorbing the moisture before it can cause damage. It's a belt-and-suspenders approach that is essential for international sea freight.
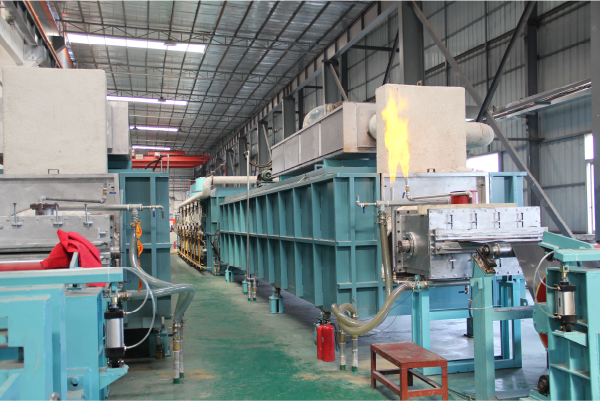
Preventing corrosion during a weeks-long ocean voyage is a battle fought on a microscopic level against an ever-present enemy: humidity. The air inside a sealed package is not inert; it contains water vapor. As a container ship travels from a temperate climate like Northern China to a tropical one like India, the temperature and humidity inside the container can fluctuate dramatically. This "container rain2" phenomenon, where moisture condenses on the coolest surfaces, is a primary cause of damage. Therefore, an effective anti-corrosion strategy cannot rely on a single solution. It must be a robust, multi-layered defense system that actively inhibits the chemical reaction of rust, provides a physical barrier to moisture, and aggressively removes any water vapor that is trapped inside. We will now delve into the science behind this threat and the specific technologies we use to defeat it.
Understanding the Threat: Humidity, Salinity, and Condensation
The primary mechanism for the corrosion of stainless steel is the presence of an electrolyte, which allows for the flow of ions in an electrochemical cell. For export shipments, that electrolyte is almost always water. The amount of water vapor in the air is measured as relative humidity (RH). When the RH reaches the dew point—the temperature at which air becomes saturated with water vapor—condensation will form on any surface at or below that temperature. A steel coil, with its high thermal mass, is often one of the last things to warm up inside a container, making it a prime target for condensation. This moisture, on its own, can be enough to initiate surface staining.
The threat is magnified tenfold by the presence of chlorides. The air in a marine environment is naturally laden with microscopic salt particles. If this salty, humid air is trapped inside the package, the resulting condensation will be a saline solution. As discussed in previous articles, chlorides are the arch-nemesis of stainless steel's passive layer, capable of causing localized pitting corrosion3 that is far more damaging than simple surface rust. Even if the coil is wrapped at a factory far from the coast, the container will spend weeks at sea, and there is always a risk of this marine air ingressing if the packaging is not perfectly sealed.
Therefore, the anti-corrosion strategy must assume the worst-case scenario: that the coil will be subjected to a 100% humidity environment with potential chloride contamination for an extended period. The protective measures must be robust enough to keep the steel surface completely isolated from this hostile environment from the moment it leaves our facility until the moment the end-user unpacks it.
The Active Shield: How VCI Technology Works
The first and most important line of active defense is Vapor Corrosion Inhibitor, or VCI, technology. As mentioned before, VCI paper or film is infused with a proprietary blend of chemical compounds. These compounds are specially selected to have a high vapor pressure, meaning they slowly and continuously sublimate, releasing molecules into the air inside the sealed package. This creates a protective, saturated vapor environment.
These VCI molecules are polar, meaning they are attracted to the charged surface of the metal. They travel through the air and land on every exposed surface of the stainless steel coil, including the hard-to-reach edges and crevices. Once there, they form a very thin, invisible monomolecular layer. This layer acts as a barrier, preventing moisture and oxygen—the key ingredients for rust—from coming into contact with the steel. It effectively passivates the surface and disrupts the electrochemical pathway that defines the corrosion process.
The beauty of VCI technology is that it is self-healing. If the protective vapor barrier is temporarily disturbed (for example, by a change in air pressure), the VCI compounds in the paper will continue to sublimate until the protective atmosphere is replenished. It provides active, ongoing protection for the entire duration of the transit. At MFY, we consider VCI to be a non-negotiable component of our export packaging standard. It is the most effective technology available for preventing corrosion on metal products during shipment.
The Physical Defense: Desiccants and Waterproofing
While VCI provides the active chemical shield, it works best in concert with a robust physical defense against moisture. This defense has two components: sealing out external moisture and absorbing any internal moisture. The first is achieved by wrapping the coil in a waterproof material, typically a heavy-duty polyethylene (HDPE) film. This layer is carefully applied after the VCI paper, and the seams are overlapped and securely taped to create a sealed bag or cocoon around the coil. This barrier's primary job is to prevent the humid, often salty, air from the container environment from entering the package.
However, no matter how carefully you wrap the coil, some ambient air from the factory will always be trapped inside. This air contains a certain amount of humidity. This is where desiccants come in. Desiccants are hygroscopic substances—materials that have a strong affinity for water and readily attract and hold water molecules. Small bags of desiccant, typically containing clay, silica gel, or calcium chloride, are placed strategically inside the package before the final sealing of the waterproof film.
These desiccant bags act like sponges, aggressively pulling the trapped water vapor out of the enclosed air. This drastically lowers the relative humidity inside the package, keeping it well below the dew point and preventing condensation from ever forming on the steel coil. The number and size of the desiccant bags are calculated based on the volume of the package and the expected duration of the voyage. The combination is powerful: the waterproof film keeps external moisture out, the desiccants remove internal moisture, and the VCI provides a final fail-safe shield directly on the metal surface.
VCI paper provides active corrosion protectionTrue
VCI paper releases protective chemicals that form an invisible barrier on metal surfaces to prevent rust formation.
Desiccants alone can prevent all corrosionFalse
While desiccants absorb moisture, they can't prevent all corrosion and must be used with VCI and waterproofing for complete protection.
What labeling and documentation are necessary for the export of stainless steel coils?
A perfectly packaged coil can still turn into a logistical nightmare if its labels are wrong or its documents are missing. A simple typo on a label can send a shipment to the wrong warehouse, while a missing certificate can leave it stranded in customs for weeks, accumulating fees and risking damage.
Essential labeling includes clear shipping marks with consignee details, port of discharge, and handling symbols. Necessary documentation comprises a commercial invoice, packing list, bill of lading, certificate of origin, and a Mill Test Certificate (MTC) for traceability.
This isn't just bureaucracy; it's the language of global trade. I recall a shipment to a large distributor in Russia where their import process required the net weight, gross weight, and coil number to be stenciled in a specific format and location on the package. Our team's adherence to this precise labeling instruction ensured the coil cleared customs in a single day. In contrast, another supplier's shipment was held for over a week due to incorrect label formatting. Details matter immensely.
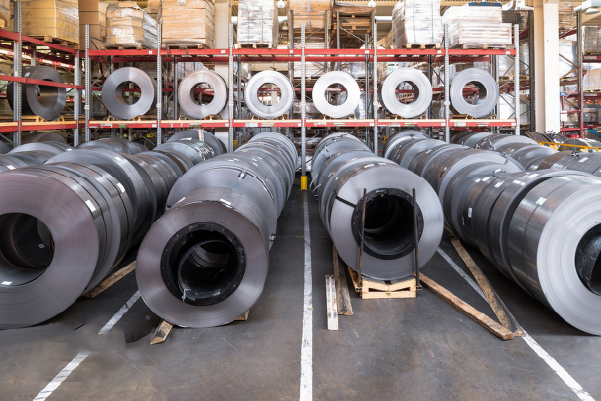
Labeling and documentation are the voice of your shipment. They communicate vital information to every person who will interact with the package, from the freight forwarder and port handler to the customs officer and the final recipient. This information needs to be clear, accurate, and standardized to ensure a smooth and efficient transit through the complex global supply chain. Any ambiguity or error in this communication can lead to significant delays, added costs, and frustrated customers. A well-executed packaging job is rendered incomplete without a perfect execution of this final, critical administrative step. To ensure perfection, we must focus on three distinct areas of information: the external shipping marks for logistics, the formal export documents for customs and commerce, and the internal traceability marks for quality assurance.
The Anatomy of a Standard Shipping Mark
The shipping mark is the main label stenciled or adhered to the outside of the packaged coil. It is the package's primary ID for the entire logistics chain. While specific requirements can vary by country and customer, a standard international shipping mark contains several key pieces of information. First and foremost are the consignee details: the name and address of the company that is to receive the goods. This must be written exactly as it appears on the commercial invoice and bill of lading.
Next is the port of discharge, which is the destination seaport where the container will be unloaded from the ship. This is critical for ensuring the container is sorted correctly at transshipment hubs. The mark will also include the final destination city if it is different from the port city. A package number is also essential, written as "Package 1 of 5," "2 of 5," etc. This ensures that all parts of a single shipment are kept together. The country of origin ("Made in China") is also a mandatory declaration for customs purposes.
ly, the shipping mark includes internationally recognized handling symbols. These are simple pictograms that transcend language barriers. For a heavy steel coil, the most important symbols are "Use No Hooks," "Keep Dry" (an umbrella), and often "Sling Here" to indicate the correct lifting points. The weight of the package (both Gross Weight and Net Weight in kilograms) must also be clearly displayed. All of this information is typically stenciled in large, clear, waterproof black ink in at least two prominent locations on the package.
The Essential Suite of Export Documents
While the shipping mark guides the physical package, the export documents are what allow it to legally cross borders. This suite of documents is the commercial and legal foundation of the transaction. The Commercial Invoice is the bill for the goods, detailing the seller, buyer, product description, quantities, unit price, and total value. This document is used by customs authorities to determine the duties and taxes owed. Accuracy is paramount; the value declared must be true and correct.
The Packing List is a detailed breakdown of the shipment's contents. For a shipment of steel coils, it will list each package, its corresponding coil ID number, its net weight (the weight of the steel only), its gross weight (the weight of the steel plus all packaging materials), and its dimensions. This document allows customs and the end-user to verify the contents of the shipment without having to unpack every single item.
The Bill of Lading (B/L) is the most important document in sea freight. It is a contract between the shipper (MFY) and the carrier (the shipping line). It serves three purposes: it is a receipt for the goods, it is evidence of the contract of carriage, and it is a document of title, meaning whoever holds the original B/L has the right to take possession of the goods. ly, the Certificate of Origin is a document certified by a chamber of commerce that attests to the country in which the goods were produced. This is often required by the importing country to qualify for preferential tariff rates.
Internal Traceability: The Coil ID and MTC
The final piece of the documentation puzzle connects the external package back to the specific product inside. This is the coil's unique identification number and its associated Mill Test Certificate (MTC). As discussed previously, the coil ID is referenced on the packing list. This allows the end-user to know exactly which coil is in which package. Upon unpacking, they can match the ID stenciled on the coil's inner wrap with the packing list.
This coil ID is the key to traceability. It links the physical product directly to its MTC. The MTC is a formal quality assurance document issued by the mill that produced the steel. It provides a complete "chemical fingerprint" of the coil, listing the exact percentages of all alloying elements (Chromium, Nickel, Molybdenum, etc.). It also details the results of mechanical property tests, such as tensile strength, yield strength, and elongation.
This document is crucial for our clients in engineering and manufacturing. It provides them with absolute proof that the material they have received meets the technical standards (like ASTM or EN) they specified in their order. At MFY, we provide a full set of original documents, including the MTC for every coil, ensuring our clients have the complete quality assurance and traceability they need for their own production processes and quality records.
Document / Label | Primary Purpose | Key Information Included |
---|---|---|
Shipping Mark | Logistics & Handling | Consignee Name, Port of Discharge, Package Number, Handling Symbols (e.g., Keep Dry), Gross/Net Weight. |
Commercial Invoice | Commerce & Customs | Seller/Buyer Info, Product Description, Value of Goods (for duty calculation). |
Packing List | Content Verification | Detailed breakdown of each package's contents, individual coil IDs, weights, and dimensions. |
Bill of Lading (B/L) | Contract & Title | Contract of carriage between shipper and carrier; serves as a document of title to the goods. |
Certificate of Origin | Tariff & Trade Policy | Certifies the country of manufacture (e.g., "Made in China") for customs purposes. |
Mill Test Certificate (MTC) | Quality Assurance | The coil's "birth certificate" detailing its exact chemical composition and mechanical properties. |
Shipping marks include handling symbolsTrue
Standard shipping marks contain internationally recognized handling symbols like "Keep Dry" and "Sling Here" to ensure proper handling.
Bill of Lading is optionalFalse
The Bill of Lading is a mandatory document for sea freight that serves as receipt, contract, and title document.
How to ensure the secure loading and transportation of stainless steel coils?
Your coil is perfectly packaged and labeled, but the most dangerous part of its journey is about to begin. An improperly loaded, 15-ton coil can become a battering ram inside a container, destroying itself, other cargo, and potentially causing a major safety incident.
To ensure secure loading, the container must first be inspected for integrity. The coils must then be securely blocked and braced using heavy-duty timber and strapping to prevent any movement, with careful consideration given to proper weight distribution inside the container.
Securing cargo is a non-negotiable safety responsibility. I personally witnessed the aftermath of a poorly loaded container at a port. A coil had broken free from its restraints, punched through the front wall of the container, and was sitting halfway out onto the truck's chassis. The financial loss was secondary to the immense safety risk it created. This is why at MFY, our loading crews are rigorously trained, and we use a specific, engineered blocking and bracing plan for every shipment. There is no room for improvisation when it comes to securing heavy cargo4.
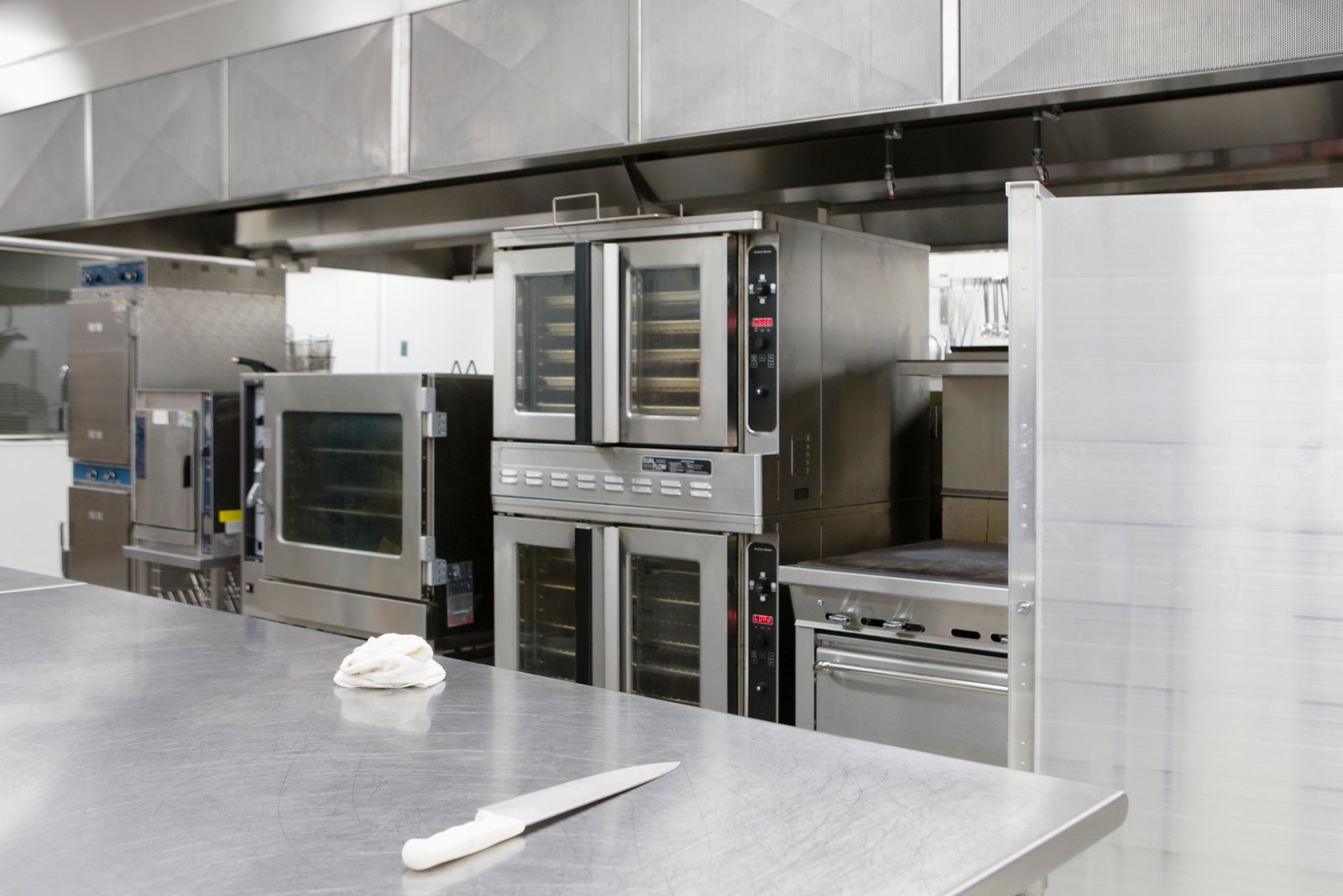
The final stage of the export process is the physical act of loading and securing the coils into a shipping container. This is where the meticulous work of packaging is put to the ultimate test. A standard 20-foot shipping container will be lifted, tilted, and subjected to constant, multi-directional g-forces from the rolling and pitching of a ship at sea. Any movement of the cargo inside is unacceptable. It can lead to damage to the coil, damage to the container, and can even compromise the stability of the entire stack of containers on the vessel. Therefore, the process of loading is a discipline of engineering and physics, focused on immobilizing the cargo and ensuring the container is balanced and safe for transport. This critical process involves three key stages: preparing the container, building the restraints, and managing the overall weight distribution.
Container Inspection and Floor Preparation
Before any cargo enters the container, the container itself must be thoroughly inspected. The loading crew must verify that it is structurally sound5 and suitable for the cargo. This involves checking for any holes or cracks in the walls, roof, and floor that could let in water. They inspect the door seals to ensure they are intact and will provide a watertight closure. The interior must be clean, dry, and free from any debris or residue from previous cargo that could damage or contaminate the stainless steel packages. Any container that fails this inspection is rejected, and a new one is ordered.
The container floor is the foundation upon which the entire load will be secured. While container floors are strong, a steel coil concentrates an immense amount of weight onto a very small footprint. To distribute this load and to provide a solid base for bracing, the floor is often lined with dunnage—typically wooden planks or sheets of plywood. This spreads the pressure from the coil's pallet or cradle across multiple cross-members of the container's understructure.
This preparation also involves inspecting the lashing points. These are strong metal loops welded to the container's floor and side rails. The loading crew confirms that these lashing points are present, secure, and not overly rusted or damaged. These points will be the primary anchors for the straps and wires used to tie down the cargo, and their integrity is critical to the safety of the load.
Blocking, Bracing, and Lashing Techniques
With the container prepared, the coils are loaded using a forklift or an overhead crane. Once positioned, the process of immobilization begins. This is achieved through a combination of blocking, bracing, and lashing. Blocking involves placing heavy-duty wooden blocks or lumber directly against the cargo's base to prevent it from sliding. For a heavy coil, this means building a robust wooden frame around the pallet or cradle it sits on, nailing it securely to the container's wooden floor.
Bracing refers to using larger timber structures to fill empty spaces and transfer forces from the cargo to the container's strong structural walls. For example, if a coil is placed in the center of the container, wooden braces will be built from the coil's base out to the container's side walls, creating a rigid, load-bearing structure. These braces are cut to fit snugly, ensuring there is zero room for the cargo to gain momentum.
Lashing is the final step, where high-tensile steel wire or heavy-duty polyester straps are used to tie the cargo down. The straps are looped over the coil (using protective material to prevent scratching the metal packaging) and tightened using tensioning tools. They are anchored to the container's lashing points. A typical securement plan for a heavy coil will involve multiple lashings in different directions—some to prevent forward and backward movement, and others to prevent side-to-side shifting. This combination of blocking, bracing, and lashing creates a redundant safety system that holds the coil firmly in place.
Weight Distribution and Center of Gravity Management
ly, a secure load is also a balanced load. The placement of the coils within the container is carefully planned to ensure proper weight distribution. A single, heavy coil is typically placed in the center of the container, over the keel line, to maintain a balanced center of gravity. If multiple coils are being loaded, their weights must be distributed evenly to prevent the container from becoming top-heavy, side-heavy, or end-heavy. An imbalanced container can be dangerous to lift and can cause handling problems for trucks, cranes, and the ship itself.
There are strict regulations regarding the maximum payload of a container, and also often road weight limits in the destination country that must be adhered to. The total gross weight of the cargo must not exceed the maximum payload specified on the container's CSC (Convention for Safe Containers) plate. Our logistics team at MFY plans the load meticulously, calculating the total weight and planning the precise placement of each coil to ensure the final loaded container is both legal and stable.
Before the doors are closed and sealed with a high-security bolt seal, the loading supervisor takes several photographs of the completed securement. This serves as a record of our due diligence and proves that the cargo was loaded and secured according to best practices. This final checkpoint ensures that we have done everything possible to protect the cargo and ensure its safe arrival.
Container inspection is mandatoryTrue
Containers must be inspected for structural integrity and cleanliness before loading to prevent damage or contamination.
Coils can be loaded without dunnageFalse
Dunnage (wooden planks) is essential to distribute the coil's concentrated weight across container floor cross-members.
Conclusion
Effective export packaging for stainless steel coils is a system of proactive risk management. It demands a meticulous checklist approach: from pre-inspection and multi-layered wrapping with VCI and desiccants, to precise documentation and engineered container securement. This discipline ensures product integrity and builds ultimate client trust.
-
Understand the scientific principle behind VCI paper's effectiveness ↩
-
Discover how climate variations cause moisture condensation in shipping containers ↩
-
Understand the impacts of pitting corrosion on stainless steel surfaces, especially in marine environments ↩
-
Explore methods for safely securing heavy cargo to prevent damage during transport. ↩
-
Understand how to assess container stability and suitability for transporting goods. ↩
Have Questions or Need More Information?
Get in touch with us for personalized assistance and expert advice.