Duplex Pipe vs 316L: Stop Cl⁻ Stress Cracking
Struggling with pipeline failures? Chloride-induced stress corrosion cracking (Cl⁻ SCC)1 is a silent killer for standard stainless steels like 316L stainless steel2 in demanding environments. This can lead to unexpected downtime and costly repairs, jeopardizing your operations and creating significant safety risks that can't be ignored.
Duplex stainless steel pipe offers superior resistance to chloride-induced stress corrosion cracking (Cl⁻ SCC) compared to 316L due to its dual-phase microstructure of austenite and ferrite. This structure provides higher strength and enhanced corrosion resistance, making it the more reliable choice for harsh, chloride-rich environments.
As Global Business Director for MFY, I’ve seen countless projects where the right material choice at the outset prevented years of future headaches. While 316L stainless steel has been a trusted workhorse in many industries, its vulnerability to Cl⁻ SCC is a critical Achilles' heel. This isn't just a technical detail; it's a factor that can determine the long-term profitability and safety of your entire operation. Let's move beyond a simple comparison and explore the strategic implications of this choice.
The decision between 316L and duplex stainless steel is far more than a simple line item on a procurement sheet; it's a foundational strategic choice that impacts risk management, lifecycle cost, and operational resilience. In industries from chemical processing to marine engineering, the assumption that 316L is "good enough" has led to costly, and sometimes catastrophic, failures. For instance, the NACE International standard3 for the oil and gas industry (MR0175/ISO 15156) sets strict limits on the use of austenitic steels like 316L in chloride environments precisely because of this risk. Choosing the right material isn't about buying a commodity; it's about investing in certainty and partnering with a supplier who understands the complex interplay between material science and real-world performance.
What are the key differences between duplex pipe and 316L stainless steel?
Are you confused by the technical jargon differentiating stainless steel grades? Choosing between duplex and 316L can feel like navigating a complex maze, where a wrong turn leads to poor performance, unexpected costs, or even catastrophic failure, putting your entire project's integrity on the line.
The primary differences lie in their microstructure and properties. Duplex steel has a mixed austenite-ferrite structure, giving it higher strength and superior stress corrosion cracking resistance. In contrast, 316L is fully austenitic, offering excellent formability and general corrosion resistance but is vulnerable to chloride SCC.
For decades, 316L has been the default choice for corrosion-resistant applications, and for good reason. It's versatile, widely available, and performs admirably in a vast range of environments. However, as industries push for higher temperatures, increased efficiency, and operations in more aggressive settings like coastal or chemical plants, the limitations of 316L become starkly apparent. The development of duplex stainless steels wasn't an accident; it was a direct response by metallurgists to solve the inherent weaknesses of austenitic steels, particularly their susceptibility to Cl⁻ SCC. I remember consulting for a client in Southeast Asia whose new heat exchanger, specified with 316L, failed in less than two years. They had underestimated the combined effect of moderate temperature and brackish cooling water. The switch to duplex wasn't just a repair; it was an upgrade in their engineering philosophy. Understanding the fundamental differences we are about to explore is the first step toward making that same forward-thinking decision for your own applications and avoiding similar costly lessons.
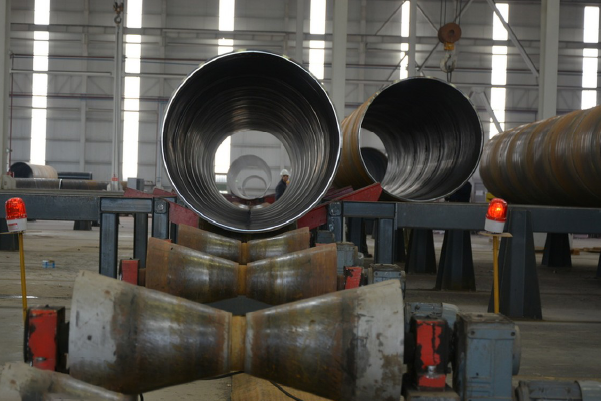
Duplex stainless steel represents a significant evolution in materials science, offering a blend of properties that neither austenitic nor ferritic steels can achieve alone. Its unique character is engineered from the atomic level up, designed specifically to overcome the challenges that plague traditional grades in demanding service. This requires a deeper look into the core science that defines these materials—their microstructure, mechanical capabilities, and inherent resistance to various forms of corrosion. For engineers and project managers, moving beyond a surface-level familiarity with these steels is essential for optimizing design, ensuring safety, and achieving the lowest total cost of ownership. The choice is not merely about selecting from a catalog; it's about applying a sophisticated understanding of material performance to real-world operational challenges.
Microstructure and Chemical Composition: The Foundation of Performance
The performance of any stainless steel begins with its microstructure. Type 316L is a fully austenitic steel, meaning its crystal structure is a face-centered cubic (FCC) lattice. This structure is what gives 316L its renowned ductility and excellent formability, making it relatively easy to bend, shape, and weld. Its chemical composition, featuring around 17% chromium, 12% nickel, and 2.2% molybdenum, provides a robust passive layer that delivers good general corrosion resistance in many environments. This combination has made it a reliable standard for decades.
In sharp contrast, duplex stainless steel, as its name implies, features a two-phase microstructure containing roughly equal parts of austenite (FCC) and ferrite (a body-centered cubic, or BCC, lattice). This engineered combination is the key to its enhanced properties. The ferritic phase contributes high strength and resistance to stress corrosion cracking, while the austenitic phase provides toughness and general corrosion resistance. This dual nature means you get the best of both worlds, creating a material that is fundamentally more robust.
This difference is further magnified by the chemical composition. A common grade like Duplex 2205 (UNS S32205) typically contains around 22% chromium, 3% molybdenum, and 5% nickel. The higher chromium and molybdenum content, along with the addition of nitrogen, significantly boosts its resistance to pitting and crevice corrosion. This is quantified by the Pitting Resistance Equivalent Number (PREN), where PREN = %Cr + 3.3 %Mo + 16 %N. For 316L, the PREN is about 25, whereas for Duplex 2205, it's around 36. This higher PREN is a direct indicator of superior resistance to localized corrosion, which is often the precursor to more severe failures like SCC.
Mechanical Strength and Toughness: A Tale of Two Materials
One of the most significant practical advantages of duplex stainless steel is its superior mechanical strength. The yield strength—the point at which a material begins to deform permanently—is a critical design parameter. For 316L, the typical yield strength is approximately 240 MPa (35 ksi). Duplex 2205, however, boasts a yield strength of around 450 MPa (65 ksi), nearly double that of 316L. This has profound implications for design and cost.
This superior strength means that for a pipe designed to handle a specific internal pressure, a duplex pipe can have a much thinner wall than a 316L pipe. This leads to a substantial reduction in the total weight of the material required for a project. I recently worked with a client in the Middle East designing a new water treatment plant. Their initial specification called for 316L piping. By presenting a comparative analysis, we demonstrated that switching to Duplex 2205 would allow them to reduce the pipe wall thickness by nearly 30%. This significant weight saving not only helped offset the higher per-kilogram cost of duplex steel but also led to cascading benefits, including lower shipping costs, reduced structural support requirements, and easier on-site installation.
While duplex steel excels in strength, it's important to consider other mechanical properties like ductility. 316L is more ductile, meaning it can be stretched and formed more easily without fracturing. However, while duplex has lower elongation values, it still possesses excellent toughness and is far from brittle. Modern fabrication and welding techniques are well-adapted for duplex materials, and while they require more precise control over factors like heat input compared to 316L, the procedures are well-established and routinely executed by qualified fabricators.
Property | 316L Stainless Steel | Duplex 2205 Stainless Steel |
---|---|---|
Yield Strength (0.2% Offset) | ~240 MPa (35 ksi) | ~450 MPa (65 ksi) |
Tensile Strength | ~515 MPa (75 ksi) | ~655 MPa (95 ksi) |
Elongation | ~40% | ~25% |
PREN (Typical) | 25 | 36 |
Corrosion Resistance Beyond the Basics
While 316L is known for its good "general" corrosion resistance, its primary vulnerability is Chloride Stress Corrosion Cracking (Cl⁻ SCC). This failure mechanism requires the simultaneous presence of three factors: a susceptible material (like 316L), tensile stress (from pressure, welding, or fabrication), and a specific corrosive environment (containing chlorides). When these conditions are met, especially at temperatures above 60°C (140°F), 316L can fail suddenly and without warning.
Duplex stainless steel was specifically designed to combat this weakness. The reason for its superior performance lies in its two-phase microstructure. Cracks that might initiate in the more susceptible austenite phase are unable to easily propagate through the harder ferrite phase. The ferrite grains act as "crack arrestors," effectively blocking the path of the crack and preventing it from growing to a critical size. This intrinsic mechanism provides a powerful, built-in defense against SCC.
The enhanced performance is backed by extensive data and real-world experience. In chloride-containing environments, 316L is generally considered at high risk for SCC at temperatures above 60°C. In contrast, standard duplex grades like 2205 can often be used safely in similar environments at temperatures up to 150°C (300°F) or even higher, depending on the specific chloride concentration and pH level. This dramatically wider operating window is precisely why duplex has become the material of choice for demanding applications in chemical processing, desalination, and offshore platforms, where reliability is not just desired but essential.
Duplex steel resists chloride SCC betterTrue
The dual-phase microstructure of duplex steel provides inherent resistance to stress corrosion cracking in chloride environments, unlike 316L's vulnerable austenitic structure.
316L has higher yield strengthFalse
Duplex 2205's yield strength (~450 MPa) is nearly double that of 316L (~240 MPa), allowing thinner pipe walls and weight savings in designs.
How does Cl⁻ stress cracking affect 316L stainless steel pipes?
Have you ever witnessed a pipe that looked perfectly fine on the outside fail suddenly? This is the danger of Chloride Stress Corrosion Cracking (Cl⁻ SCC), an insidious failure mechanism that can compromise your 316L pipelines4 without any obvious warning signs, turning a reliable asset into a sudden liability.
Chloride stress corrosion cracking (Cl⁻ SCC) causes fine, branching cracks in 316L pipes under the combined influence of tensile stress and a chloride environment. These cracks propagate rapidly and can lead to sudden, brittle-like failure, even though the material itself appears ductile and uncorroded.
The insidious nature of SCC is what makes it so dangerous. It’s not like general corrosion, which gradually thins the pipe wall over time and can often be monitored. SCC is a silent killer. I recall a case with a food processing client who used 316L for their hot brine lines—a seemingly standard choice. For nearly two years, the system operated flawlessly. Then, almost overnight, a series of pinhole leaks and fine cracks appeared, forcing a complete production halt during their busiest season. The investigation pointed directly to Cl⁻ SCC, a phenomenon their team hadn't fully accounted for in the initial design phase. This experience was a stark reminder for me, and for them, that understanding the precise how and why of a potential failure mechanism is just as critical as knowing a material's general specifications. It underscored the need to look beyond the datasheet and analyze the true operational environment.
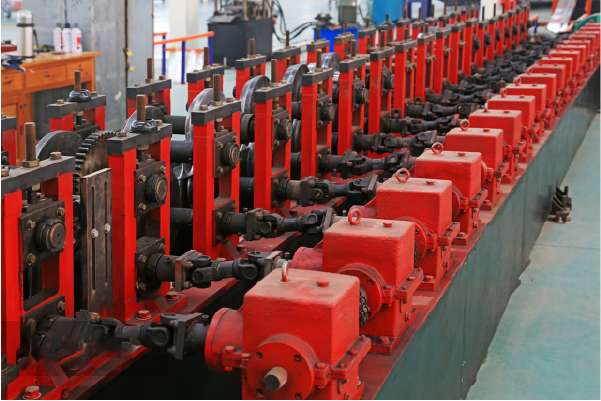
To effectively prevent a problem, you must first understand its roots. The failure of 316L pipes due to Chloride Stress Corrosion Cracking5 is a classic example of a material being pushed beyond its operational limits. It's a textbook case in materials science, driven by a specific combination of conditions that transform a ductile, reliable material into one that is susceptible to sudden, brittle-like fracture. Unpacking this mechanism reveals why simply specifying "stainless steel" is not enough. It requires a nuanced approach that considers the interplay of mechanical forces, chemical environment, and material science. Let’s dissect the three core components that must align for this type of failure to occur and explore how they conspire to undermine the integrity of 316L piping systems.
The Three Pillars of SCC: Stress, Environment, and Material
For Cl⁻ SCC to occur in 316L, three conditions must be met simultaneously. The first is the presence of tensile stress. This is often misunderstood as only the stress from internal pressure (hoop stress). In reality, residual stresses are often the main culprit. These are locked-in stresses from the manufacturing and fabrication process, particularly from welding, where uneven heating and cooling create significant internal tension. Bending pipes, cold forming, and even improper fit-up can also introduce substantial residual stresses that are more than sufficient to initiate SCC.
The second pillar is a specific corrosive environment, with chloride ions (Cl⁻) being the primary aggressor. Chlorides are ubiquitous in many industrial settings. They are found in seawater, brackish water, many process chemicals, food products like brine, and even de-icing salts. A critical factor is temperature; the risk of SCC in 316L increases dramatically at temperatures above approximately 60°C (140°F). Even in environments with low chloride levels, evaporation at hot surfaces can concentrate chlorides in crevices or under deposits, creating a localized but highly aggressive environment that triggers cracking.
The third and final pillar is a susceptible material. Austenitic stainless steels, including both 304 and 316L, are inherently susceptible to Cl⁻ SCC. While the chromium-oxide passive layer on the surface provides excellent protection against general corrosion, it is vulnerable to localized breakdown by chloride ions. Once this protective layer is breached, the underlying steel is exposed to the corrosive environment, setting the stage for crack initiation and a rapid path to failure.
The Mechanism of Crack Initiation and Propagation
The process of Cl⁻ SCC begins at a microscopic level. A chloride ion attacks and breaks down the passive layer at a susceptible point on the steel's surface, forming a tiny pit. This pit acts as a stress riser, meaning the tensile stress in the material becomes highly concentrated at the bottom of the pit. This combination of a concentrated stress field and an aggressive local chemistry is what initiates the crack.
Once initiated, the crack begins to propagate. The environment at the crack tip is extremely harsh. It becomes shielded from the bulk environment, allowing chloride ions to concentrate and the local pH to drop, becoming highly acidic. This creates a self-sustaining, or "autocatalytic," process. The metal at the crack tip rapidly corrodes, causing the crack to advance. This exposes fresh, unpassivated metal to the aggressive environment, which in turn corrodes, and the cycle continues, often at a surprisingly fast rate.
The resulting cracks have a distinct appearance under a microscope. They are typically transgranular, meaning they cut directly through the grains of the metal, and have a fine, branching, tree-root-like structure. This morphology is a classic signature of SCC. Because the cracks are so fine and the bulk of the material is unaffected, they are extremely difficult to detect with routine inspection methods like visual checks or standard ultrasonic testing until they have grown through the pipe wall, resulting in a leak or sudden rupture.
Real-World Consequences and Mitigation Failures
The practical consequences of Cl⁻ SCC can be severe. I worked with a coastal chemical plant that specified 316L for a heat exchanger system using seawater as a coolant. Despite operating within the pressure limits, they experienced multiple tube failures within 18 months of commissioning. A detailed failure analysis confirmed Cl⁻ SCC, initiated by the combination of the seawater's chlorides, operating temperatures around 70-80°C, and residual stresses from manufacturing. The cost of the emergency shutdown, lost production, and replacement of the tube bundle with a duplex material far exceeded the initial savings from choosing 316L.
Condition | Risk Level for 316L SCC |
---|---|
Temp < 50°C + Low Chlorides (<200 ppm) | Low |
Temp > 60°C + Low Chlorides (<200 ppm) | Medium |
Temp < 50°C + High Chlorides (>1000 ppm) | Medium |
Temp > 60°C + High Chlorides (>200 ppm) | High |
Any Temp/Chloride + Crevices or Wet-Dry Cycles | High |
Some engineering teams attempt to mitigate the risk by controlling the operational parameters—for instance, by strictly limiting operating temperatures or implementing costly systems to remove chlorides from process streams. However, this approach turns the operation into a precarious balancing act. An unexpected temperature spike or a minor process upset can suddenly push the 316L material into the SCC danger zone. While stress-relief heat treatments can reduce residual stresses, they are often impractical and prohibitively expensive for large, complex piping systems. Ultimately, when the three pillars of SCC are unavoidably present, the most reliable and cost-effective solution is not to manage the risk, but to eliminate it by selecting a material, like duplex stainless steel, that is inherently resistant to the failure mechanism.
Cl⁻ SCC requires three conditionsTrue
Chloride stress corrosion cracking only occurs when tensile stress, chloride environment, and susceptible material are all present simultaneously.
Visual inspection detects early SCCFalse
SCC cracks are microscopic and branching, making them undetectable by visual inspection until failure occurs.
Why is duplex pipe more resistant to Cl⁻ stress cracking compared to 316L?
Are you seeking a "set it and forget it" solution for your most demanding pipelines? Relying on standard materials in corrosive environments can feel like a constant gamble against failure, forcing you into expensive, frequent inspection cycles and leaving you perpetually worried about the next unexpected leak.
Duplex pipe's superior resistance stems from its two-phase microstructure. The ferrite phase interrupts the path of cracks that typically propagate through the austenite phase, effectively acting as a "crack arrester." This, combined with its optimized chemical composition, provides robust protection against Cl⁻ SCC.
The superior performance of duplex stainless steel6 isn't magic; it's the result of deliberate and sophisticated material science. It was designed from the ground up to provide a solution where austenitic steels fall short. After the food processing client I mentioned earlier experienced their costly 316L failure, we worked with them to replace the critical hot brine lines with Duplex 2205. It has now been over five years, and the system has operated without a single SCC-related issue, saving them from repeated downtime and ensuring consistent production. This success wasn't due to luck. It was based on a solid understanding of the fundamental scientific principles that give duplex steel its remarkable resilience. Let's explore the core mechanisms that provide engineers and asset managers with such a powerful and reliable tool against one of corrosion's most destructive forms.
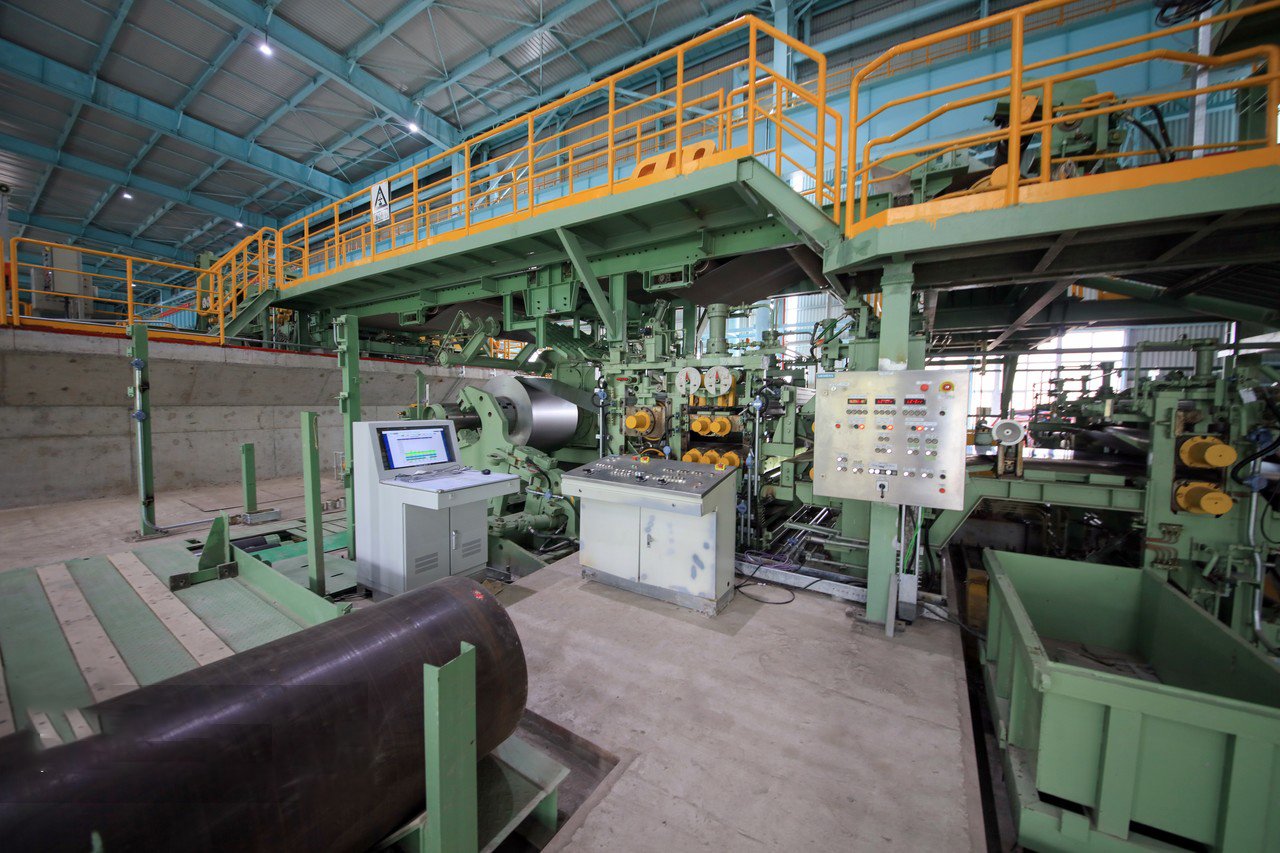
The exceptional resistance of duplex stainless steel to Cl⁻ SCC is not attributable to a single factor, but rather to a powerful synergy between its unique microstructure and its carefully balanced chemical composition. This combination creates a multi-layered defense system against the initiation and propagation of stress corrosion cracks. While 316L relies solely on its passive surface layer for protection—a layer that is vulnerable to chlorides—duplex steel has an intrinsic structural advantage that provides a second, more robust line of defense. Understanding this dual-protection mechanism is key to appreciating why duplex is not just a marginal improvement, but a transformative leap in material reliability for critical applications.
The "Crack Arrestor" Effect of the Duplex Microstructure
The primary defense of duplex steel against SCC lies in its composite microstructure, which consists of an interwoven matrix of approximately 50% austenite and 50% ferrite. We know that Cl⁻ SCC in austenitic-ferritic materials preferentially initiates in and propagates through the softer, more susceptible austenite phase. In a fully austenitic material like 316L, once a crack starts, it has an uninterrupted path to grow through the continuous network of austenite grains.
In duplex steel, this continuous path is broken. When a stress corrosion crack travelling through an austenite grain encounters a boundary with a ferrite grain, its progress is halted. The ferrite phase has a different crystal structure (BCC) and electrochemical potential, making it inherently more resistant to SCC and creating a formidable barrier to crack propagation. The energy driving the crack is dissipated at this interface, effectively blunting the crack tip and arresting its growth.
To visualize this, imagine a wildfire (the crack) spreading rapidly through a dry, grassy field (the austenite phase). The ferrite phase acts like a series of wide, paved firebreaks or rivers woven throughout the landscape. The fire may start in a patch of grass, but it cannot easily jump across these barriers. This "crack arrestor" mechanism is the most critical feature behind the superior SCC resistance of duplex steel. It is not just a theoretical concept; it is consistently observed in metallographic analysis of failed or tested components, proving its real-world effectiveness.
The Synergistic Role of Chemical Composition
The robust microstructure of duplex steel is further enhanced by an optimized chemical recipe. Key alloying elements are present in proportions specifically designed to maximize corrosion resistance. First, higher levels of Chromium (Cr) and Molybdenum (Mo)—around 22% and 3% respectively in Duplex 2205—create a more tenacious and rapidly-repairing passive layer than that of 316L. Molybdenum is particularly effective at resisting pitting corrosion, which is the critical first step in the initiation of SCC.
Second, the deliberate addition of Nitrogen (N) is a hallmark of modern duplex steels. Nitrogen acts as a strong austenite stabilizer, ensuring the proper phase balance is achieved during production. More importantly, it significantly increases the steel's strength and, as reflected in the PREN formula, dramatically improves its resistance to pitting corrosion. This makes the initial breakdown of the passive layer—the event that starts the entire SCC process—far less likely to occur in the first place.
Finally, duplex steels contain significantly less Nickel (Ni) than their 316L counterparts. While nickel is an essential austenite former, it is well-documented that austenitic alloys with nickel content in the 8-15% range (where 316L sits) are in the "peak" of susceptibility to Cl⁻ SCC. By reducing the nickel content to around 5%, duplex steels move out of this high-risk zone, further contributing to their overall immunity to this failure mechanism. This carefully balanced chemistry works in concert with the microstructure to provide a multi-faceted defense.
Performance Under Pressure: Industry Data and Standards
The superior performance of duplex steel is not just a laboratory curiosity; it is codified in major international standards and proven by decades of field data. For example, NACE MR0175/ISO 15156, the globally recognized standard for selecting materials for use in H₂S-containing environments for oil and gas production, provides detailed environmental limits for various alloys. The approved operating envelopes for duplex and super duplex steels in terms of temperature and chloride concentration are significantly wider and less restrictive than those for austenitic steels like 316L.
Feature | 316L Stainless Steel | Duplex 2205 Stainless Steel | Rationale for Superiority |
---|---|---|---|
Microstructure | 100% Austenite | ~50% Austenite / 50% Ferrite | Ferrite phase acts as a "crack arrestor" |
Yield Strength | ~240 MPa | ~450 MPa | Higher strength reduces stress concentration |
PREN | ~25 | ~36 | Higher resistance to pitting initiation |
Max Temp (Seawater) | ~50-60°C | >100°C | Wider and safer operating window |
The offshore oil and gas industry serves as a powerful case study. In the past, 316L was frequently used for seawater handling and cooling systems, but it was plagued by frequent failures due to Cl⁻ SCC. Today, the industry has almost universally transitioned to duplex and super duplex stainless steels for these critical systems. This shift has resulted in a dramatic increase in reliability and a significant reduction in maintenance costs and unplanned shutdowns. This long-term, large-scale industrial application provides undeniable proof of the superior performance and long-term value of duplex materials in the exact environments where 316L is most vulnerable.
Ferrite phase stops crack propagationTrue
The ferrite phase in duplex steel has a different crystal structure that interrupts and arrests stress corrosion cracks traveling through the austenite phase.
316L has better SCC resistance than duplexFalse
316L is actually more susceptible to chloride stress corrosion cracking due to its fully austenitic microstructure and lower PREN value compared to duplex steels.
What are the cost implications of using duplex pipe over 316L in environments prone to Cl⁻ stress cracking?
Is the higher upfront price tag of duplex stainless steel holding you back? Focusing solely on the initial material cost is a common but misleading mistake. This narrow view completely ignores the cascading hidden costs of maintenance, inspection, downtime, and premature replacement associated with a less-resistant material.
While duplex pipe has a higher initial cost per kilogram, its superior strength allows for thinner walls, reducing material weight and cost. The most significant savings come from a total lifecycle perspective: reduced maintenance, fewer inspections, and avoidance of catastrophic failure and downtime in SCC-prone environments.
As a business director, my focus is always on return on investment and long-term value, and material selection should be viewed through the same lens. It's easy for a procurement manager to see a 30% higher price per ton for duplex steel and opt for the cheaper 316L7. However, a plant manager, an operations director, or a CFO must consider the bigger picture. I once consulted with a large chemical manufacturer in India facing this exact dilemma. Their engineers specified Duplex 2205 for a critical cooling loop, but the procurement team pushed back hard on the initial cost. We helped them build a comprehensive lifecycle cost model. When they quantified the cost of just one potential week of unplanned production downtime due to an SCC failure in a 316L system, the upfront premium for duplex suddenly seemed trivial. This is the analysis that matters.
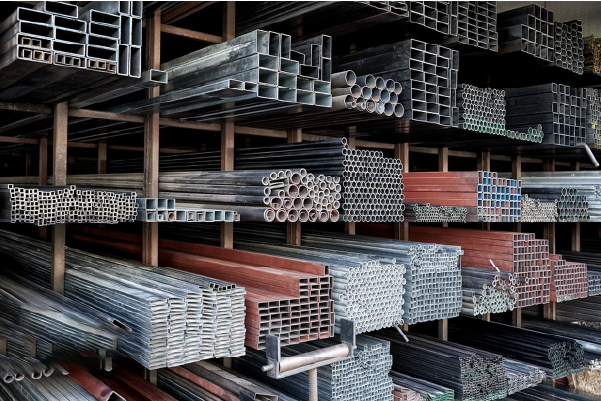
The conversation about cost must evolve from "price" to "value." A simple comparison of the cost per kilogram between 316L and duplex stainless steel is a flawed metric because it overlooks two critical factors: design efficiency and total cost of ownership (TCO). Duplex steel's superior properties allow for smarter, more efficient designs, while its durability dramatically reduces long-term operational expenditures and risks. A truly comprehensive cost analysis reveals that in applications where Cl⁻ SCC is a tangible threat, choosing the cheaper material upfront can often be the most expensive decision in the long run. Let's break down the components of a proper cost evaluation to see how the initial premium for duplex steel often translates into significant long-term savings.
Deconstructing the Initial Investment: Beyond Price Per Kilogram
The first point to address is the sticker price. Yes, on a per-kilogram or per-ton basis, duplex stainless steel is typically more expensive than 316L. This is a direct result of its more complex production process and its higher content of valuable alloying elements like chromium, molybdenum, and nitrogen8. This is the figure that often dominates preliminary cost discussions and can create a bias toward the seemingly cheaper option.
However, this initial price comparison is misleading because it ignores the strength-to-weight advantage. As we've established, duplex steel has nearly double the yield strength of 316L. In practical terms, this means a duplex pipe can safely handle the same pressure with a significantly thinner wall. This reduction in required wall thickness directly translates to a reduction in the total weight of material needed for the project.
Let's consider a practical example. A 6-inch pipe system designed to a specific pressure rating might require a Schedule 40S wall thickness if made from 316L, which weighs approximately 28.3 kg per meter. Due to its higher strength, the same system using Duplex 2205 might only require a Schedule 10S wall, weighing just 11.3 kg per meter. Even if the duplex material is 50% more expensive per kilogram, the total cost per meter of pipe is actually lower by more than 20%. At MFY, we frequently perform these types of weight-saving calculations for our clients, demonstrating that the "more expensive" material can often lead to a lower initial project cost.
The Total Cost of Ownership (TCO): Where Duplex Shines
The true economic advantage of duplex steel becomes undeniable when you analyze the Total Cost of Ownership (TCO) over the lifetime of a project. TCO encompasses not just the initial purchase price, but also all associated costs, including installation, operation, inspection, maintenance, and the monetized risk of failure. In an environment prone to Cl⁻ SCC, the TCO of a 316L system can spiral out of control.
Consider the hidden costs associated with using 316L in a high-risk application. Inspection costs are higher because you need more frequent and more sophisticated non-destructive testing (NDT) to search for the fine, branching cracks of SCC. Maintenance costs increase due to the higher likelihood of needing patches, repairs, or premature replacement of entire sections. The most significant factor, however, is downtime. An unplanned shutdown of a critical process line can result in losses ranging from tens of thousands to millions of dollars per day.
In contrast, the TCO profile for a duplex system is heavily front-loaded at the initial investment stage. Because of its inherent resistance to SCC, the long-term operational costs are dramatically lower. Inspection intervals can be safely extended, maintenance needs are minimal, and the risk of sudden, costly failure is virtually eliminated. This provides operational certainty and budget predictability, which are invaluable assets for any plant manager. You're not just buying pipe; you're investing in uninterrupted operation.
Factoring in Fabrication and Long-Term Market Stability
A common historical concern regarding duplex steel was its perceived difficulty in fabrication and welding. While it's true that duplex requires different procedures than 316L—such as tighter control of welding heat input and the use of appropriate filler metals to maintain the correct phase balance—these procedures are now well-understood and standardized. With modern welding equipment and properly trained fabricators, welding duplex steel is a routine and reliable process. As a responsible supplier, we provide our clients with comprehensive technical support and guidelines to ensure successful fabrication.
Another strategic financial consideration is price stability. The cost of 316L is heavily influenced by the price of nickel, which is known for its market volatility. Duplex steels, with their significantly lower nickel content, tend to have more stable and predictable pricing. For large-scale, long-term projects, this price stability can be a significant advantage in budgeting and financial planning, reducing exposure to volatile commodity markets.
Cost Factor | 316L (in SCC Environment) | Duplex 2205 | Rationale |
---|---|---|---|
Initial Material Cost | $100,000 | $130,000 | Higher alloy content in Duplex |
Weight-Saving Reduction | N/A | -$40,000 | Duplex's higher strength allows thinner walls |
Inspection & Maintenance (10yr) | $50,000 | $5,000 | Reduced need for frequent, specialized NDT |
Risk-Adjusted Cost of Downtime | $250,000+ | ~$0 | High risk of SCC failure vs. inherent resistance |
10-Year Total Cost of Ownership | $400,000+ | $95,000 | Duplex offers vastly superior long-term value |
(Note: Costs are illustrative examples for comparison)
Duplex allows thinner wallsTrue
Duplex steel's higher strength enables thinner wall designs while maintaining pressure ratings, reducing material weight and cost.
316L has lower TCOFalse
In Cl⁻ environments, 316L's higher inspection, maintenance and downtime costs make its total cost of ownership far exceed duplex.
What recommendations can be made for selecting between duplex and 316L pipes for specific applications?
Feeling overwhelmed by the choice between duplex stainless steel9 and 316L? Making the right decision requires a clear, logical framework, but the technical details can seem complex. Guessing or simply sticking with what's familiar can lead to overspending on an unnecessary alloy or, far worse, risking failure.
For general-purpose applications with low chlorides and temperatures below 60°C, 316L is a cost-effective choice. For any application involving chlorides, temperatures above 60°C, high mechanical stress, or where failure is not an option (e.g., chemical processing, marine environments), 316L stainless steel is strongly recommended.
Ultimately, the best recommendation is one that is perfectly tailored to your project's unique operational reality. There is no universal "right" answer. As a material solutions provider, our role at MFY extends beyond simply selling steel; we see ourselves as partners in our clients' success, helping them navigate these critical decisions. I have seen clients in one part of the world use 316L successfully for years in their potable water systems, while other clients in coastal regions saw the same grade fail rapidly in brackish water cooling systems. The key variable was not the material itself, but the specific demands of the application—namely, the chloride concentration and operating temperature. To help you avoid costly trial-and-error, let's establish a practical decision-making framework based on sound engineering principles.
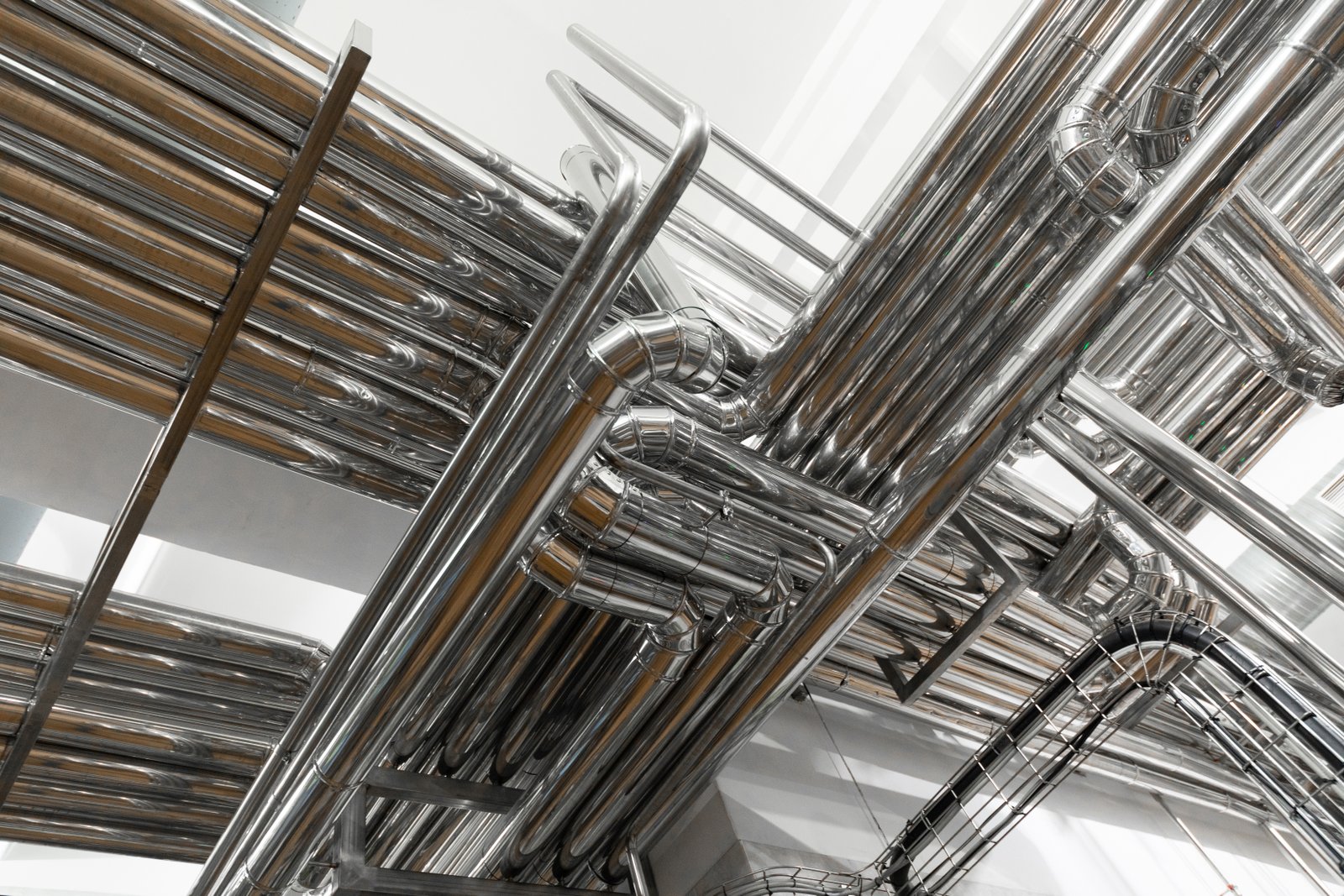
Selecting the optimal material is a process of risk assessment. The goal is to match the material's capabilities with the service environment's demands in the most economically efficient way. This doesn't have to be an overly complicated exercise. By asking a series of targeted questions about your application, you can quickly determine which material falls into the "safe and cost-effective" category and which falls into the "unnecessary risk" category. The framework below is designed to guide you through this thought process, ensuring that your choice is based on data and logic rather than habit or incomplete information. Let's walk through the ideal applications for each material and then combine them into a simple decision-making tool.
The "Go-To" Zone for 316L Stainless Steel
Type 316L stainless steel remains an excellent and highly cost-effective choice for a wide range of applications, provided it is used within its well-defined operational limits. The ideal conditions for 316L are those with low chloride levels (generally below 200 ppm, although this is highly dependent on other factors), operating temperatures that remain consistently below 60°C (140°F), and moderate mechanical stress. When these conditions are met, 316L will provide a long and reliable service life.
Specific applications where 316L is often the appropriate and economical choice include:
- Food and Beverage: Piping for products like milk, wine, and beer, as long as cleaning-in-place (CIP) cycles do not involve hot, high-chloride sanitizing agents.
- Pharmaceuticals: Systems for high-purity water (WFI) and other processes where chloride contamination is negligible.
- Architectural Applications: Structural and decorative elements like handrails and facades in inland environments where exposure to salt spray is not a concern.
- General Water and Wastewater: Potable water distribution and municipal water treatment in regions with low natural chloride content in the water supply.
The critical caveat is certainty. The designer must be confident that the operational envelope will not be breached. If there is a possibility of process upsets leading to temperature excursions, or if conditions like wet-dry cycling could lead to the concentration of chlorides on the steel surface, the risk of SCC with 316L increases exponentially. Diligent process control and a thorough understanding of all potential operating conditions are essential when specifying 316L.
The Critical Zone Demanding Duplex Stainless Steel
Duplex stainless steel becomes the necessary and prudent choice as soon as the environment becomes more aggressive. It should be considered the default option for any new project where the three pillars of SCC—tensile stress, chlorides, and elevated temperature—are present. The superior strength and inherent SCC resistance of duplex steel provide a level of safety and reliability that 316L simply cannot match in these conditions.
Applications where duplex steel is strongly recommended or even mandatory include:
- Oil & Gas: Seawater injection lines, cooling systems, process piping, and flowlines, especially in offshore and coastal facilities. For more severe sour service conditions, super duplex grades are often required.
- Chemical Processing: Equipment for producing or handling chlorides, acids, and other corrosive chemicals. This includes reactors, heat exchangers, storage tanks, and associated piping.
- Marine Environments: Any system exposed to seawater or salt spray. This is particularly critical for desalination plants (especially in high-temperature evaporators and brine handling), shipbuilding, and infrastructure on or near the coast.
- Pulp and Paper Industry: Equipment in the bleach plant and other areas where chloride-based chemicals are used at elevated temperatures.
I can share a compelling case from a manufacturing client MFY supplied in India. Their new plant was located near the coast and designed to use brackish water for process cooling. Their initial specification, based on old company standards, was 316L. After reviewing the water analysis and operating temperatures, we strongly advised them of the extremely high risk of SCC and recommended they upgrade to Duplex 2205. They took our advice. A competing facility built nearby at the same time with 316L experienced major leaks in their cooling system within two years, forcing a costly and disruptive replacement project. Our client's investment in the right material from day one paid for itself many times over by avoiding that failure.
A Practical Decision-Making Matrix
To simplify the selection process, you can use a simple decision matrix. By answering a few key questions about your application, you can quickly identify the most appropriate material.
Operating Condition | Recommendation for 316L | Recommendation for Duplex | Primary Rationale |
---|---|---|---|
Temp < 60°C & Low Chlorides (<200ppm) | Suitable | Over-specified | 316L is safe and cost-effective in mild conditions. |
Temp > 60°C & Low Chlorides (<200ppm) | Use with Caution | Recommended | Elevated temperature increases SCC risk even with low chlorides. |
Any Temp & High Chlorides (>200ppm) | High Risk | Strongly Recommended | High chloride concentration is the primary driver for SCC. |
Any Temp & Seawater/Brine | Not Recommended | Mandatory | Seawater is a highly aggressive SCC environment for 316L. |
High Consequence of Failure | Evaluate Risk Carefully | Strongly Recommended | For critical systems, the reliability of duplex justifies the cost. |
This matrix serves as a starting point. The most critical question to ask is: "What are the consequences of a failure?" If a leak or rupture would pose a safety hazard, cause environmental damage, or result in significant economic loss from downtime, the conservative and correct engineering choice is to use the material that is inherently resistant to the most likely failure mode. In chloride-containing environments, that material is duplex stainless steel.
316L is suitable for low-chloride applicationsTrue
316L is cost-effective for environments with chloride levels below 200ppm and temperatures under 60°C, such as food processing or inland water systems.
Duplex is only needed for oil & gasFalse
Duplex is essential for any chloride-rich environment including marine, chemical processing, and high-temperature applications beyond just oil & gas.
Conclusion
The choice between 316L and duplex pipe is a critical strategic decision. While 316L is a reliable workhorse for mild conditions, duplex steel's superior strength and near-immunity to chloride stress corrosion cracking make it the safer, more cost-effective choice for demanding, long-term applications.
-
Learn about the impact of Cl⁻ SCC on stainless steel durability in various environments ↩
-
Discover the characteristics and uses of 316L stainless steel in industry ↩
-
Understand the material standards protecting against corrosion in oil and gas applications ↩
-
Learn about the impact of Cl⁻ SCC on 316L pipeline reliability and safety. ↩
-
Understand the process initiating crack formation in stainless steel due to Cl⁻ SCC. ↩
-
Better understand the material design advantages of duplex stainless steel for corrosive environments. ↩
-
Understand the constraints of 316L in environments prone to chloride-induced stress cracking ↩
-
Discover how alloying elements improve duplex stainless steel properties ↩
-
Discover why duplex stainless steel is favored in aggressive environments ↩
Have Questions or Need More Information?
Get in touch with us for personalized assistance and expert advice.