Coil vs Sheet Stainless Steel: Cost, Yield, & Handling
Are you struggling to decide between stainless steel coils and sheets for your production line? This choice seems straightforward, but it profoundly impacts your project's cost, efficiency, and logistics. Making the wrong call can lead to inflated material waste, higher labor expenses, and ultimately, a compromised bottom line.
The primary difference is that stainless steel coils offer a lower per-ton cost and higher material yield, ideal for high-volume automated production. In contrast, sheets, which are cut from coils, provide easier handling and are better suited for smaller-scale or custom fabrication projects despite a higher initial price.
This decision is far more than a simple procurement choice; it's a strategic move that reverberates through your entire operational workflow. From the moment the material arrives at your facility to the final product assembly, the format of your stainless steel dictates processing methods, storage requirements, and even your labor structure. As the Global Business Director for MFY, I’ve guided countless clients through this exact decision-making process, helping them look beyond the price tag to see the bigger picture of total cost and efficiency.
The debate between coil and sheet isn’t a simple matter of one being universally better than the other. It’s a nuanced decision that balances upfront investment against long-term operational savings. Coils are the undisputed champions for mass production, but they demand significant capital for decoiling, straightening, and feeding equipment—a barrier that can be too high for smaller enterprises. Sheets, while more expensive per kilogram, offer unparalleled flexibility and a lower barrier to entry. I recall a client in the construction sector who initially relied on sheets for their manageability on-site. As their projects scaled, we helped them analyze the break-even point for investing in mobile processing units, enabling a strategic shift to coils that dramatically lowered their material costs and project timelines. This is the kind of critical, long-term thinking we foster at MFY, ensuring your supply chain is not just a cost center, but a competitive advantage1.
What are the cost differences between stainless steel coils and sheets?
Trying to pin down your material budget but getting tripped up by the price gap between stainless steel coils and sheets? The per-ton invoice price is merely the opening chapter of the full cost story, not the conclusion. Ignoring the downstream costs can lead to budget overruns.
Fundamentally, stainless steel coils are less expensive per unit of weight than sheets. This cost advantage stems from the fact that sheets require additional processing steps, including cutting-to-length, flattening, and shearing from a master coil, all of which add labor and machine time to the final cost.
The initial purchase price is a critical factor, but it’s a deceptive one if viewed in isolation. True cost-effectiveness is revealed when you calculate the Total Cost of Ownership (TCO), which encompasses the entire journey of the steel through your facility. This includes the labor needed to handle it, the capital tied up in processing equipment, the value of the material lost to scrap, and the logistics of storage and transport. At MFY, we always encourage our partners to adopt this holistic view. I remember working with a kitchen sink manufacturer in Southeast Asia. They were laser-focused on the per-ton price of sheets because their production volume didn't seem to justify a full coil-fed line. However, once we mapped out their costs for handling individual sheets, the high scrap rate from stamping circular sink bowls, and the associated labor, the financial picture changed dramatically. The slightly higher upfront cost of narrower, custom-slit coils quickly became the more economical option2 by dramatically reducing waste and streamlining their stamping process. This is where a strategic supplier adds value—by helping you see the hidden costs and opportunities within your own operations.
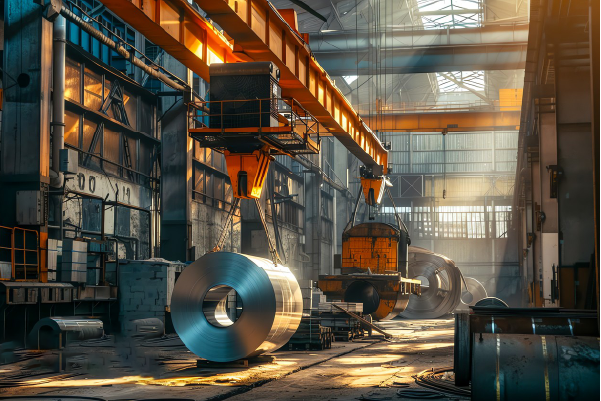
To truly grasp the cost implications, you have to look deep into the production and operational lifecycle of both formats. The price you see on an invoice is just the tip of the iceberg. The real drivers of cost are rooted in how the material is made, how you have to handle it, and how efficiently you can turn it into a finished product. For my clients, understanding these underlying factors is the first step toward building a more resilient and profitable supply chain. It’s about shifting the mindset from simply buying steel to strategically investing in a raw material format that aligns perfectly with your business model, whether you're a massive automotive OEM in India or a custom fabrication shop in the Middle East.
The Economics of Mill Production: Why Coils Cost Less
The fundamental reason for the price difference originates at the steel mill. Stainless steel is produced in a continuous process, emerging from the rolling mill as a long, wound coil. This is the most efficient and basic form of the product. The process is highly automated and runs uninterrupted, maximizing throughput and minimizing the energy and labor cost per ton. Every subsequent action taken on that coil adds cost.
To create sheets, that master coil must be unspooled and fed into a cut-to-length (CTL) line. This line contains a flattener or leveler to remove coil memory, followed by a shear that cuts the steel into sheets of a specified dimension. These sheets are then stacked, packaged, and prepared for shipment. Each of these steps—uncoiling, leveling, shearing, stacking—requires machinery, energy, and labor, which are all factored into the final price of the sheet.
This added processing cost can be significant. Depending on the material grade (e.g., 304, 316L), thickness, and the precision of the cut, the conversion from coil to sheet can add anywhere from 5% to 15% to the material's base cost. At MFY, our integrated production capabilities, which include our own cold-rolling and processing centers, allow us to manage these costs effectively, but they are an unavoidable reality of the physics of steel processing.
Factoring in Secondary Processing and Labor
Beyond the mill, the next layer of cost is determined by your own operational setup. To process coils, a manufacturer needs a significant upfront capital investment in equipment: decoilers to unwind the steel, straighteners to ensure it's flat, and feeders to introduce it into a press or laser cutter. This machinery is expensive and represents a substantial barrier to entry. In contrast, sheets can often be handled with much less sophisticated equipment, like a simple shear, and loaded into machines with standard forklifts or even manually for smaller jobs.
However, for high-volume production, the labor equation flips. An automated coil-fed stamping line can run continuously with minimal human intervention, requiring only skilled operators for setup and monitoring. This results in a very low labor cost per part. A sheet-fed operation, on the other hand, might require one or more workers to manually load each sheet, a process that is slower and inherently more labor-intensive. I worked with an automotive parts supplier in India that manufactured thousands of small brackets daily. Their initial sheet-fed process was a bottleneck. After a thorough cost-benefit analysis, they invested in a new coil-fed press line. The result? They reduced their labor cost per unit by 40% and increased throughput by over 150%, achieving a full return on their investment in just 18 months.
The Hidden Costs: Logistics and Inventory
Finally, consider the costs associated with getting the material into your facility and storing it. Coils are incredibly dense and offer a significant advantage in storage footprint. A single 20-ton coil occupies far less floor space than 20 tons of stacked sheets. However, moving that coil requires a heavy-duty overhead crane with a specialized C-hook or other lifting apparatus. Sheets, while taking up more space, can be managed with a standard forklift, offering greater handling flexibility. This can be a critical distinction for facilities with limited crane capacity. Transportation logistics also differ. Coils must be properly secured on specialized cradles during shipping to prevent rolling or damage. While seemingly more complex, shipping a single large coil is often more efficient than packaging and protecting multiple stacks of sheets, which are more susceptible to surface scratches and edge damage if not handled carefully.
Feature | Stainless Steel Coil | Stainless Steel Sheet |
---|---|---|
Initial Purchase Price | Lower per ton | Higher per ton |
Required Equipment | High initial investment (Decoilers) | Lower initial investment (Shears, Forklifts) |
Labor Cost (High Volume) | Lower (Automated lines) | Higher (Manual handling) |
Storage Footprint | Smaller, more dense | Larger, requires more surface area |
Logistical Handling | Requires heavy-duty cranes | Can be handled with standard forklifts |
Coils cost less per tonTrue
Stainless steel coils have lower base costs because they require less processing than sheets, which need additional cutting and flattening steps.
Shears are cheaper than decoilersFalse
While shears are less expensive than full decoiling systems, the total cost of sheet processing (including labor and waste) often exceeds coil processing costs at scale.
How does the yield of stainless steel coils compare to sheets?
Are you concerned that hidden material waste is silently eroding your profitability? The physical form of your stainless steel feedstock is one of the biggest factors determining how much usable product you get for your money, directly impacting your bottom line.
Stainless steel coils consistently provide a higher material yield compared to pre-cut sheets. This advantage comes from the ability to "nest" parts more efficiently along a continuous strip of metal, which significantly minimizes the scrap generated between cuts and at the material's edge.
In manufacturing, yield is everything. Every square centimeter of steel left on the factory floor as scrap is money wasted. It's a direct reduction of your potential profit. The difference in yield between using coils and sheets isn't a minor rounding error; it can be a substantial figure that determines the financial viability of a project. The combination of modern nesting software with automated, coil-fed machinery is a paradigm shift for fabricators. I often share the story of a client in the Middle East who specializes in large-scale HVAC systems for commercial buildings. For years, they used standard sheets to fabricate ducting components, accepting a scrap rate of nearly 25% as a cost of doing business. We worked with them to transition to slit coils that were customized to the specific widths needed for their primary components. By optimizing the input material size and nesting their cuts along a continuous coil, they slashed their scrap rate to below 10%. This didn't just save them money on raw materials; it also reduced their disposal costs and improved their overall production speed, making their bids more competitive.
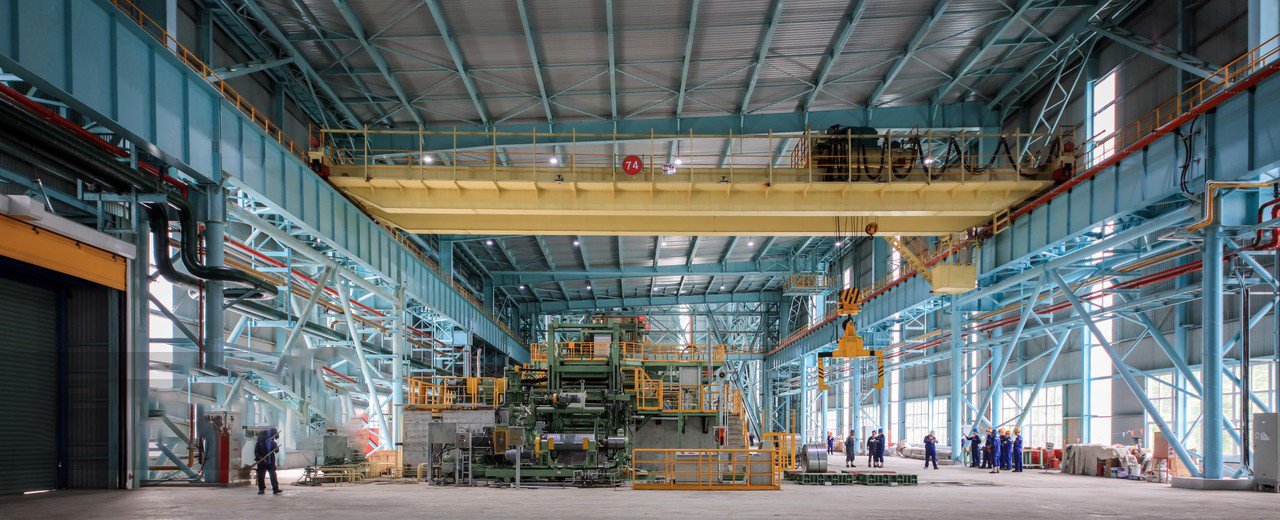
The concept of yield optimization is central to modern, lean manufacturing. It’s not just about reducing waste; it’s about maximizing the value extracted from every single kilogram of steel you purchase. The choice between coil and sheet lies at the very heart of this principle. While the initial cost discussion revolves around the purchase price, the yield discussion is about the effective price you pay for the material that actually ends up in your final product. For our clients at MFY, ranging from massive equipment integrators to specialty component manufacturers, a deep dive into yield calculations often reveals the most compelling argument for structuring their supply chain around a specific material format. It's a conversation that moves beyond simple procurement into the realm of strategic process engineering3.
Maximizing Material Usage Through Nesting
Yield, in the context of metal fabrication, is the percentage of the raw material that becomes part of the finished product. The primary reason coils offer superior yield is the effectiveness of a process called "nesting." Nesting is the art and science of arranging the shapes to be cut on a piece of raw material in the most compact way possible to minimize waste. When you're working with a continuous coil, your nesting possibilities are virtually infinite along its length. Advanced software algorithms can analyze part geometries and arrange them in incredibly tight configurations, almost like a puzzle, ensuring the absolute minimum amount of steel is left between them.
Contrast this with sheets. A sheet has four fixed edges, creating a finite boundary. No matter how cleverly you nest your parts, you are constrained by these dimensions. This often leads to awkward, unused sections of material, particularly near the edges or when cutting non-rectangular shapes. The flexibility of the coil format eliminates these restrictive boundaries along the length axis, giving the nesting software a much larger canvas to work with.
As a practical example, imagine stamping a large number of circular parts. On a coil, these circles can be nested in a staggered pattern that interlocks tightly, achieving a material utilization rate that can exceed 85%. Trying to cut the same parts from a standard 1219x2438mm sheet would force a more rigid, grid-like layout, potentially dropping the yield to below 75% simply because of the wasted material4 at the start and end of the sheet and the inefficient use of space.
The Impact of Skeletons and Edge Trim
The waste material left over after parts are cut is often called the "scrap skeleton." With sheet-fed operations, you are invariably left with a large, web-like skeleton from each sheet, which must be handled and removed. While this scrap has recovery value, its price is a small fraction of the initial material cost. The goal is to minimize its creation in the first place. Coil processing inherently produces a more streamlined form of scrap—typically two continuous strips from the edges, which are easier to handle, chop, and recycle.
Furthermore, consider edge trim. A master coil from the mill often has a slightly rougher edge that needs to be trimmed for precision applications. This is done in a slitting operation. While this does create a small initial loss, once you have a slit coil of a precise width, the edge waste is defined. With sheets, every single sheet has four edges. If your part is small relative to the sheet size, you are dealing with the cumulative waste from these four edges over and over again. A key service we provide at MFY is custom slitting, where we cut a master coil into several narrower coils based on a client's specific needs. A client manufacturing electrical enclosures, for instance, might need a 300mm wide strip. By ordering a 300mm slit coil from us instead of cutting it from a 1219mm wide sheet, they eliminate a massive amount of structural scrap, dramatically improving their yield before the first part is even stamped.
Calculating and Comparing True Yield
The financial impact of yield can be quantified with a simple formula: Yield % = (Weight of Finished Parts / Total Weight of Raw Material) x 100. Let's run a hypothetical scenario. A company needs to produce 50,000 stamped components, each weighing 0.2 kg. The total weight of the finished parts is 10,000 kg, or 10 metric tons.
- Using Coils: With optimized nesting on a coil-fed line, they achieve a 91% yield. The total raw material required would be 10 tons / 0.91 = 10.99 tons.
- Using Sheets: Due to the part's irregular shape and the constraints of standard sheet sizes, their yield is only 77%. The total raw material required would be 10 tons / 0.77 = 12.99 tons.
In this scenario, choosing coils saves 2 metric tons of stainless steel. Even if the per-ton cost of the coil was slightly higher due to a special width, the massive reduction in required tonnage makes it the overwhelmingly cheaper option. This is the type of analysis we guide our clients through at MFY. We don't just sell steel; we provide the data and insight needed to make the most economically sound and sustainable procurement decisions.
Coils offer higher yield than sheetsTrue
Continuous coil format allows more efficient nesting of parts, minimizing scrap between cuts and at edges.
Sheets provide infinite nesting optionsFalse
Sheets have four fixed edges that limit nesting possibilities, unlike coils which offer continuous length for optimization.
What are the handling characteristics of stainless steel coils versus sheets?
Are you evaluating your facility's logistical capabilities and safety protocols? The physical form of your steel dictates everything from the equipment you need to the workflow on your factory floor, and overlooking these handling characteristics can lead to dangerous inefficiencies.
Stainless steel coils are extremely heavy and dense, requiring specialized equipment like overhead cranes and C-hooks for safe handling. Sheets are individually lighter and more manageable, allowing for transport with standard forklifts, but they carry a higher risk of surface damage during handling.
The conversation about handling goes far beyond simple logistics; it's fundamentally about safety, efficiency, and the preservation of material quality. A 15-ton coil is a concentrated, powerful object that demands respect and the right equipment. Dropping or improperly handling it isn't just a financial loss; it's a major safety hazard. Sheets, while seemingly less intimidating, have their own set of challenges. Their large, flat surfaces are susceptible to scratches, dings, and dents that can render a piece unusable for aesthetic applications. I once visited a client's facility where their sheet storage area was a major bottleneck. Stacks were disorganized, leading to excessive forklift movement, accidental damage to top sheets, and wasted time searching for the right gauge and finish. After reviewing their workflow, we helped them implement a better system, but it highlighted how something as basic as handling can create or destroy value. At MFY, we ensure our products are packaged for optimal protection and handling, but the client's internal processes are just as crucial in maintaining that quality from the receiving dock to the final product.
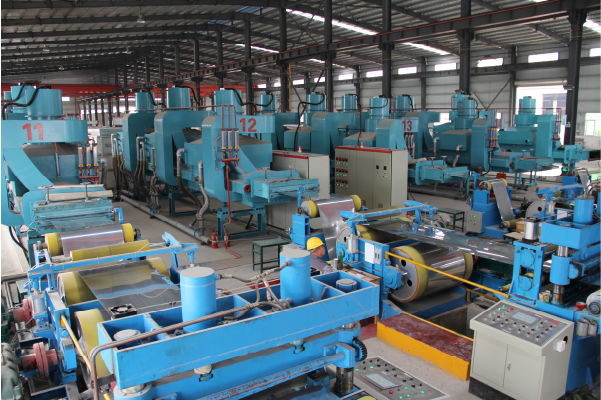
Evaluating the handling characteristics of coils versus sheets is a critical exercise in aligning your material choice with your facility's physical and operational reality. The most cost-effective, highest-yield material in the world is useless if you can't move it safely and efficiently through your production process. This assessment requires a candid look at your equipment, your floor space, your workforce's training, and the flow of materials through your plant. As a supplier, our responsibility extends to helping our clients think through these practicalities. We can provide the world's best stainless steel, but if it creates logistical chaos for the client, we haven't delivered a true solution.
The Demands of Coil Handling: Equipment and Safety
A standard stainless steel coil can weigh anywhere from 5 to 25 metric tons5. Moving such an object is a serious engineering task. The primary tool is a high-capacity overhead bridge crane. This crane must be fitted with a specialized attachment, such as a C-hook that cradles the coil from its inner diameter, or a vertical eye-grab that grips it securely. The capacity of the crane and the entire building structure must be sufficient to handle these loads. Furthermore, the factory floor itself must have the load-bearing capacity to support not only the static weight of a stored coil but also the dynamic loads during transport.
Safety protocols are paramount. Coil storage areas, often called "saddles" or "cradles," must be designed to prevent rolling. Personnel must be rigorously trained in proper lifting procedures and to maintain a safe distance during movement. In addition to cranes, facilities often use coil cars or turnstiles to load coils onto decoilers. This is all heavy-duty, specialized equipment that represents a significant investment and requires dedicated, well-trained personnel to operate safely and effectively. For our clients running 24/7 manufacturing operations, the reliability and safety of their coil handling equipment is a cornerstone of their productivity.
The Flexibility and Risks of Sheet Handling
Sheets offer a completely different handling paradigm. While a full pallet of sheets can still be very heavy, individual sheets or small stacks can be managed with a standard forklift, a piece of equipment present in nearly every industrial facility. This accessibility is a major advantage for smaller shops or facilities without the infrastructure for heavy cranes. For some applications, single sheets can even be moved or positioned manually, offering a degree of flexibility that is impossible with coils.
However, this flexibility comes with risks, primarily to the material's surface finish. Stainless steel sheets, especially those with polished or decorative finishes like No. 4 or Mirror, are highly susceptible to scratching. A drag from a forklift tine, improper stacking without interleaving paper, or careless manual handling can easily damage the surface, making the sheet unusable for architectural or appliance applications. Stacking also presents challenges. Sheets must be stacked flat and on a level surface to prevent warping. Accessing a specific sheet in the middle of a tall stack can be a time-consuming and potentially hazardous task, requiring the unstacking and restacking of all the material on top of it.
Case Study: Facility Layout and Workflow Integration
The choice between coil and sheet has a profound impact on the entire layout and workflow of a facility. I worked with an equipment integrator who was expanding their production line for manufacturing commercial kitchen equipment. Their old facility was exclusively designed for sheet metal. As they moved to a new, larger building, they had a critical decision to make.
Their analysis showed that about 70% of their steel usage was for standard-sized frames and panels, while 30% was for custom, one-off components. Continuing with a sheet-only process was familiar but inefficient for their high-volume parts. Moving to a coil-only process would streamline the standard parts but make the custom work cumbersome. The solution was a hybrid layout. We helped them design a receiving and production area with two distinct workflows. One area featured a new overhead crane and a compact coil-fed laser cutting line dedicated to the high-volume components. The adjacent area was set up for sheet handling with forklifts, feeding a press brake and turret punch press for the custom, low-volume work. By investing in this dual capability, they matched the raw material format to the specific production demand, optimizing efficiency, safety, and flexibility across their entire operation. This is the essence of a strategic approach to handling.
Coils require overhead cranesTrue
Stainless steel coils' extreme weight and density necessitate specialized lifting equipment like overhead cranes with C-hooks for safe handling.
Sheets are safer than coilsFalse
While sheets are lighter, they present unique safety risks like surface damage and stacking hazards that require careful handling protocols.
What are the implications of choosing coils over sheets for specific applications?
Have you considered how your choice of steel format directly enables or hinders your specific application's success? Selecting the right raw material form is not just a technical detail; it is a strategic decision that aligns your supply chain with your market's demands.
The implications are significant: for high-volume, repetitive manufacturing like automotive parts or appliances, steel coils are essential for achieving the necessary speed, consistency, and cost-efficiency. For custom, project-based work like architectural fabrication or prototyping, steel sheets provide the necessary flexibility and low barrier to entry.
The application is the ultimate arbiter in the coil versus sheet debate. The ideal raw material format for a company making millions of identical automotive stampings is completely different from that for a firm creating a one-of-a-kind architectural façade. A mismatch can be disastrous. Imagine trying to supply a high-speed automotive line with individual sheets—the line would be starved for material, and the labor costs would be astronomical. Conversely, forcing a custom metal art studio to invest in a full coil processing line for their unique projects would be financially ruinous. As a supplier, understanding our clients' end applications is non-negotiable. It's the only way we can provide true value. When an engineering contractor for a major infrastructure project in India contacts us, our conversation starts with their application: Are they forming long, continuous profiles for cable trays, or are they cutting custom gusset plates? The answer determines our recommendation, ensuring we support their operational reality, not just sell them a product.
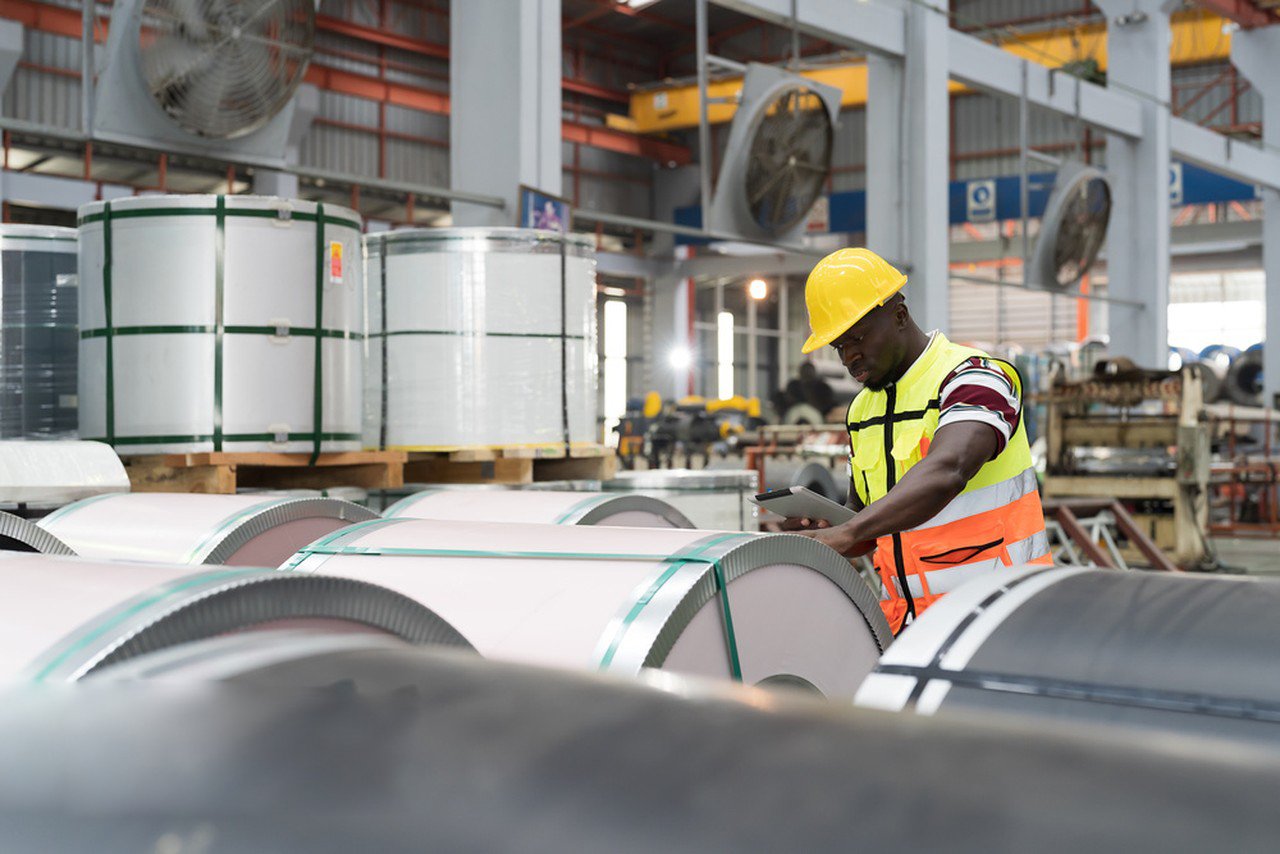
Moving beyond generic cost and yield calculations, the true wisdom in selecting between coils and sheets emerges when you analyze the specific demands of your industry and product. The material format you choose should be a direct reflection of your production philosophy, your customers' expectations, and your competitive landscape. At MFY, we serve a diverse range of clients across numerous sectors, and this experience has given us a unique perspective on how this single choice can define operational success. From the relentless pace of automotive manufacturing to the bespoke precision of architectural projects, the raw material is the first and most critical building block.
High-Volume Manufacturing: Automotive and Appliances
In sectors like automotive manufacturing and home appliance production, the name of the game is speed, consistency, and cost per part. Production lines run continuously, churning out thousands or millions of components that must be identical. For these applications, the stainless steel coil is not just the best choice; it is the only feasible choice. Automated stamping presses and roll-forming lines are fed directly from coils, allowing for uninterrupted production runs that can last for hours or even days.
The consistency of a coil is also a critical advantage. A single coil from one heat (a single batch of molten steel) offers extremely uniform metallurgical properties, thickness tolerance, and surface finish from its beginning to its end. This is vital for applications like deep drawing (forming a shape like a kitchen sink) or for parts that require a perfect cosmetic finish, as in a stainless steel refrigerator door. Using sheets would introduce variability from sheet to sheet and from batch to batch, increasing the risk of defects and process adjustments. For our clients in these industries, we focus on providing high-quality coils with just-in-time (JIT) delivery to keep their high-stakes production lines moving without interruption.
Project-Based Work: Construction and Architecture
The world of construction and architectural metalwork operates on a completely different set of principles. Here, every project can be unique, and customization is the norm rather than the exception. Production volumes are lower, and the work is often performed either in a job shop or directly on the construction site. For these applications, stainless steel sheets are often the superior choice. Their primary advantage is flexibility and accessibility. A contractor can easily transport a few sheets to a job site in the back of a truck, and they can be cut, bent, and welded using portable equipment.
Consider the fabrication of custom flashing, decorative panels, or support brackets for a building façade. The quantities are small, and the designs are bespoke. Forcing this type of work through a coil-based process would be incredibly wasteful and inefficient. I recall a project we supplied in Dubai, which involved creating thousands of unique, laser-cut decorative panels for a hotel lobby. Each panel was slightly different. Our client, a specialized architectural fabricator, relied on our cut-to-length sheets as their feedstock. It allowed them to program their laser cutters for each unique design without the complexity and scrap associated with starting and stopping a coil line for every single part.
The Hybrid Approach: Equipment Integrators and Job Shops
Many businesses live between these two extremes. Consider a company that integrates custom equipment, like food processing machinery or pharmaceutical packaging lines. These companies have a mix of needs. They may produce a line of standard machine frames or enclosures in relatively high volumes, but each final machine is customized with unique brackets, chutes, and guards. For these clients, a hybrid approach to material sourcing is often the most effective strategy.
They might use slit coils to efficiently produce their standard components, benefiting from the high yield and automation. Simultaneously, they will order various gauges and finishes of sheets for their custom fabrication department. This allows them to leverage the efficiency of coils for the "80%" of their production and retain the flexibility of sheets for the "20%" that requires customization. At MFY, we are uniquely positioned to serve these clients because our integrated supply chain allows us to be a single source for all their needs. We can deliver a 10-ton coil of 304 stainless steel for their main production line and, on the same order, include a pallet of specialized 316L mirror-finish sheets for the components that require high corrosion resistance and a cosmetic appearance. This simplifies their procurement and allows them to optimize every aspect of their production.
Coils ensure production line continuityTrue
Coils allow uninterrupted feeding of automated stamping presses in high-volume manufacturing, preventing production stoppages.
Sheets suit one-off architectural projectsFalse
Actually sheets are ideal for architectural projects as they offer flexibility for custom fabrication and easy transport to job sites.
What recommendations can be made for selecting between stainless steel coils and sheets?
Are you ready to make a final decision but feeling caught between the competing benefits of coils and sheets? The path to the right choice isn't about finding a single "best" answer, but about following a clear framework to find the best answer for you.
To select the right format, perform a thorough analysis of your production volume, available capital for equipment, facility logistics, and labor capabilities. High-volume, automated producers should choose coils for cost and yield, while low-volume or custom fabricators will benefit from the flexibility of sheets.
Making the right recommendation requires moving beyond a simple product comparison and into a collaborative analysis of your entire operation. The best choice is one that holistically integrates with your business goals, your financial realities, and your production floor. Over my years at MFY, I've found that the most successful outcomes happen when we act less like a supplier and more like a strategic partner. It begins with asking the right questions. It's not just "What do you want to buy?" but "What are you trying to achieve?" Are you trying to lower your cost per part, increase your production throughput, reduce material waste, or gain the flexibility to enter new markets? The answers to these strategic questions will illuminate the path forward and transform the choice between a coil and a sheet from a tactical nuisance into a powerful lever for business growth. Let's walk through the framework we use to guide our clients to the optimal solution.
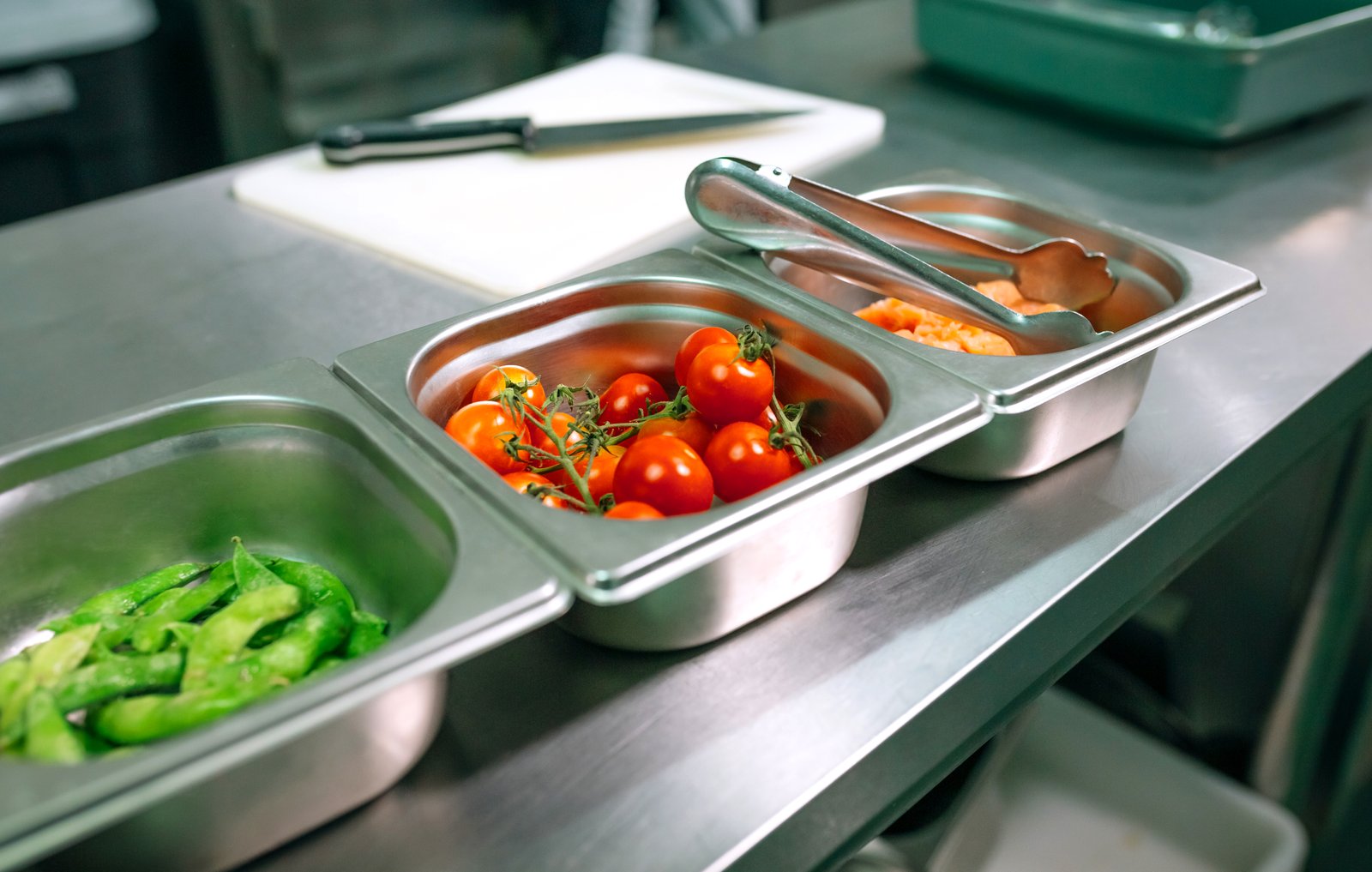
The final decision on whether to base your production around stainless steel coils or sheets is one of the most significant you'll make for your fabrication process. It’s a choice with long-term consequences for your capital expenditure, operational efficiency, and overall profitability. To navigate this decision effectively, a structured approach is essential. It requires a blend of quantitative financial analysis and a qualitative assessment of your operational capabilities. Rushing this decision based on incomplete data is a recipe for inefficiency. Instead, by methodically working through the key variables, you can arrive at a conclusion that not only makes sense today but also supports your company's growth in the future.
A Quantitative Framework: The Break-Even Analysis
At its core, the financial part of this decision is a break-even analysis. You need to determine the production volume at which the higher initial capital cost of a coil processing line is offset by the savings from lower material cost and higher yield.
First, calculate the Total Cost of Production using sheets. This is relatively straightforward: (Cost per ton of sheets x Tons required) + (Labor costs). The tons required must account for your current scrap rate. Then, calculate the Total Cost of Production using coils. This is more complex: (Cost per ton of coils x Tons required) + (Labor costs) + (Amortized monthly cost of new equipment). The key here is that the "Tons required" will be lower due to better yield, and the "Labor costs" will likely be lower for high volumes. The "Amortized equipment cost" is the total price of the decoiler, feeder, etc., divided by its expected lifespan in months.
By plotting these two costs against production volume, you will find a break-even point. Below this volume, sheets are more economical. Above this volume, the investment in coil processing equipment begins to pay for itself and becomes the more profitable option. We often help clients run these numbers, modeling different scenarios to give them a clear financial picture of their investment.
A Qualitative Assessment: The Operational Checklist
Numbers alone don't tell the whole story. You must also conduct a frank assessment of your facility's operational readiness. Ask your team the following questions:
- Tonnage & Volume: What is your realistic monthly consumption of a specific grade and thickness? Is it consistent, or does it fluctuate wildly? Consistent, high-volume demand points toward coils.
- Handling & Infrastructure: Do you have an overhead crane with the necessary capacity? Is your floor strong enough to store heavy coils safely? If the answer is no, the infrastructure costs must be added to your quantitative analysis.
- Workforce Skills: Is your team trained to operate and maintain an automated coil-fed line? Or are they more experienced with manual, sheet-based fabrication? Training is an additional, but crucial, investment.
- Scrap & Yield: What is your current, measured scrap rate with sheets? A high scrap rate (above 15-20%) is a strong indicator that you could see significant benefits from the improved yield of coils.
- Supplier Relationship: Does your current supplier have the flexibility to offer both coils and sheets? Can they provide value-added services like slitting or cut-to-length processing that could offer a "hybrid" solution?
Partnering with Your Supplier for the Right Solution
Ultimately, you don't have to make this decision in a vacuum. A true supply chain partner should function as a consultant. At MFY, this is a core part of our identity. Our goal is to align our supply capabilities with your operational reality. Because we are a fully integrated group—from raw material trading and cold-rolling to custom processing and export—we have the flexibility to offer the perfect solution for you.
For a client just starting out, we can supply high-quality sheets to support their growth. As their volume increases, we can transition them to custom-slit coils that improve their yield without requiring a full decoiling line. And for our large-scale manufacturing clients, we are a reliable source of high-tonnage master coils delivered to their precise specifications. The best recommendation is one that comes from a deep, collaborative understanding of your unique needs. We invite you to have that conversation with us.
Coils suit high-volume productionTrue
Coils offer cost and yield advantages for automated, high-volume manufacturers due to economies of scale.
Sheets always cost lessFalse
Sheets only cost less below the break-even volume; above that threshold, coils become more economical despite higher initial equipment costs.
Conclusion
Ultimately, the choice between stainless steel coils and sheets is a strategic trade-off. It balances the lower material cost and superior yield of coils against the handling flexibility and lower upfront capital investment of sheets. A thorough analysis of your production volume, capabilities, and applications is essential.
-
Discover how material choice impacts competitive edge and operational efficiency ↩
-
Explore how custom-slit coils can reduce waste and streamline production ↩
-
Explore how strategic process engineering can optimize manufacturing yield and efficiency ↩
-
Understand the impact of material waste on production efficiency when using sheets ↩
-
Explore typical weights and handling requirements for standard coils in industrial settings. ↩
Have Questions or Need More Information?
Get in touch with us for personalized assistance and expert advice.