Plasma vs Laser vs Waterjet: Best Way to Cut Plate
Struggling to choose between plasma, laser, and waterjet cutting for your metal plates? Making the wrong decision can lead to costly material waste, project delays, and compromised quality, directly impacting your bottom line. This guide will help you navigate the options and make an informed choice.
The best method for cutting plate—plasma, laser, or waterjet—depends entirely on your specific requirements. Plasma cutting excels in speed for thick conductive metals, laser cutting offers unmatched precision for thin to medium materials, while waterjet provides a cold-cutting process suitable for nearly any material without thermal distortion.
As the Global Business Director at MFY, I've spent years advising clients, from large construction contractors in the Middle East to specialized manufacturers in Southeast Asia, on their stainless steel processing needs. The "best" cutting method isn't just a technical question; it's a strategic business decision that affects everything from production speed to final product quality and cost-per-part. Let's explore this further.
The debate over plasma, laser, and waterjet often centers on isolated metrics like speed or cost. However, a more holistic view is essential. The optimal choice is one that integrates seamlessly into your supply chain, enhances your competitive edge, and delivers the best return on investment. For instance, a client in India's automotive sector might prioritize the high-speed, high-precision capabilities of a fiber laser to meet demanding production schedules. Conversely, a client fabricating custom architectural elements from thick 316L stainless steel might find that the slower, but heat-free, waterjet process1 eliminates costly secondary finishing, making it the more efficient choice overall. This critical thinking is at the core of how we at MFY help clients build resilient and agile supply chains.
What are the key features of plasma, laser, and waterjet cutting technologies?
Understanding the fundamental technology behind each cutting method feels overwhelming with all the technical jargon. This confusion can lead to misapplication, where a chosen technology is fundamentally unsuited for the job, causing rework and financial loss. Let's demystify the core principles of each method.
Each technology uses a unique principle: plasma cutting utilizes a high-velocity jet of ionized gas (plasma) to melt and expel material. Laser cutting employs a highly focused, high-energy beam of light to melt or vaporize the material. Waterjet cutting uses an ultra-high-pressure stream of water, often mixed with an abrasive garnet, to erode the material away.
In my experience, a foundational understanding prevents costly errors. I recall a client in the construction industry who was sourcing pre-cut stainless steel stiffeners. They initially specified plasma cutting due to its low cost, not realizing the heat-affected zone (HAZ) would compromise the material's structural properties for their specific application. This oversight nearly led to a significant project delay. After we walked them through the core differences, they switched to waterjet cutting, which, despite a higher initial quote, saved them from potential structural failures and expensive post-processing. This illustrates why grasping the "how" behind each method is not just an academic exercise; it's a crucial step in operational planning and risk management. It allows you to ask the right questions and challenge assumptions, ensuring the technology you choose is perfectly aligned with your material, design, and performance requirements. We will now dive deeper into the mechanics, advantages, and limitations of each of these powerful cutting technologies.

The Workhorse: How Plasma Cutting Operates
Plasma cutting is fundamentally a thermal process. It works by sending an electric arc through a gas (like oxygen, nitrogen, or argon) that is passed through a constricted opening, or nozzle. This process elevates the gas to a fourth state of matter—plasma—at incredibly high temperatures, around 20,000°C. This superheated, electrically conductive plasma jet is then directed at the workpiece. It melts the metal, and the high-velocity gas stream simultaneously blows the molten material away, creating the cut. This method is exclusively for electrically conductive materials, making it a perfect fit for stainless steel, carbon steel, and aluminum.
The primary advantage of plasma is its exceptional speed on medium to thick plates. For a heavy equipment manufacturer in Russia we supply, cutting 20mm thick 304 stainless steel plates for machinery frames is a daily task. For them, plasma is the undisputed champion. It can cut through this thickness at a rate far exceeding laser or waterjet, making it incredibly cost-effective for high-volume production of parts where ultra-fine precision isn't the main priority. The technology has also evolved significantly with high-definition plasma systems, which now offer improved edge quality and reduced bevel, narrowing the gap with other methods.
However, its thermal nature is also its main drawback. The intense heat creates a Heat-Affected Zone (HAZ) along the cut edge, which can alter the metallurgy of the material. For certain grades of stainless steel, this can affect corrosion resistance or hardness, potentially requiring secondary processes like grinding or heat treatment to restore the material's properties. Furthermore, the cut edge typically has a slight bevel, and the process generates dross (resolidified metal) on the underside of the cut, which often needs to be removed. These are critical considerations that must be factored into the total production time and cost.
The Artist: The Precision of Laser Cutting
Laser cutting operates on a completely different principle of concentrated light energy. The two main types used in industry are CO2 and fiber lasers. A CO2 laser generates a beam by exciting CO2 gas molecules, while a fiber laser creates it within an optical fiber. In both cases, this intense beam of light is focused through a lens onto a tiny spot on the material. The sheer energy density at this point melts, burns, or vaporizes the material, and an assist gas (like nitrogen or oxygen) is used to blow the molten material out of the kerf, or cut path.
The defining feature of laser cutting is its incredible precision and speed, particularly on thin materials. We work with an equipment integrator in India that produces intricate control panels from 1.5mm 316 stainless steel sheets. They rely exclusively on fiber laser cutting, which can achieve tolerances of ±0.1mm and produce clean, sharp edges with a minimal kerf width. This precision allows for complex designs and tight nesting of parts, maximizing material utilization and minimizing scrap. For stainless steel up to about 15mm, a fiber laser often provides the perfect balance of speed, precision, and edge quality.
The limitations of laser cutting become apparent with thicker or more reflective materials. While modern high-power fiber lasers can cut thicker stainless steel, the process becomes much slower and more energy-intensive, often making plasma a more economical choice. Highly reflective materials like aluminum or copper can pose a challenge as they can reflect the laser beam, potentially damaging the machine's optics, although modern fiber lasers are much better at handling these materials than older CO2 systems. Like plasma, laser cutting is a thermal process and creates a small HAZ, though it is typically much smaller and less significant than that of plasma.
The Universal Soldier: The Versatility of Waterjet Cutting
Waterjet cutting is a unique mechanical erosion process. It starts with an ultra-high-pressure pump that pressurizes water to extreme levels—typically between 40,000 and 90,000 PSI. This water is then forced through a tiny orifice made of ruby or diamond, creating a fine, powerful stream. For cutting soft materials like foam or rubber, pure water is sufficient. For hard materials like stainless steel, stone, or composites, an abrasive substance, usually garnet, is mixed into the water stream in a mixing chamber just before the nozzle. This abrasive-laden jet exits the nozzle at nearly three times the speed of sound, eroding the material rather than melting it.
The single most important feature of waterjet cutting is that it is a cold-cutting process. Since no heat is generated, there is absolutely no HAZ, no thermal distortion, and no change to the material's intrinsic properties. This is a non-negotiable requirement for many industries. For instance, a client of ours in the Middle East who fabricates components for the aerospace industry must use waterjet for cutting certain titanium and nickel alloys. Any thermal stress from laser or plasma would compromise the material's integrity, making the parts unusable. This ability to cut virtually any material—from metal and stone to glass and composites—without thermal damage makes it incredibly versatile.
The trade-offs for this versatility are primarily speed and cost. Waterjet cutting is generally the slowest of the three methods, especially on thick metals. The operational costs can also be high due to the consumption of expensive garnet abrasive and the high-maintenance nature of the ultra-high-pressure pumps. However, for applications where edge quality is paramount and secondary finishing must be avoided, waterjet often proves more cost-effective in the long run. The edge finish is smooth and satin-like, and with taper compensation control, it can produce parts with virtually no bevel.
Feature | Plasma Cutting | Laser Cutting | Waterjet Cutting |
---|---|---|---|
Mechanism | Thermal (Ionized Gas) | Thermal (Focused Light) | Mechanical (Abrasive Erosion) |
Suitable Materials | Conductive Metals (Steel, Aluminum) | Most Metals, some Plastics, Wood | Virtually Any Material |
Key Advantage | High speed on thick metals | High precision & speed on thin/medium materials | No Heat-Affected Zone (HAZ), cuts any material |
Primary Limitation | Lower precision, significant HAZ | Thickness limitations, struggles with reflective materials | Slower speed, high consumable (abrasive) cost |
Plasma cutting is fastest for thick metalsTrue
The article states plasma cutting excels in speed for thick conductive metals, making it the fastest option for such applications.
Waterjet creates heat-affected zonesFalse
Waterjet is a cold-cutting process that produces no heat-affected zone (HAZ), unlike plasma and laser cutting which are thermal processes.
How do plasma, laser, and waterjet cutting methods compare in terms of precision and speed?
Business owners often face the dilemma of choosing between speed and precision. Sacrificing precision for speed can lead to poor product quality and customer dissatisfaction, while prioritizing precision at the expense of speed can create production bottlenecks and hurt profitability. Let's analyze this critical trade-off.
In general, fiber laser cutting offers the best combination of high speed and excellent precision on thin to medium-gauge metals. Waterjet cutting provides the highest precision with no thermal distortion but at a slower cutting speed, while plasma offers the fastest speeds on thick metals but with the lowest precision.
This comparison, however, is not just about the numbers on a spec sheet. True operational efficiency, what I call the "throughput matrix," considers the entire process from start to finish. I once consulted for a manufacturing client who was frustrated with their production times. They were using a fast plasma cutter for 10mm stainless steel parts but were spending hours on secondary operations like grinding the edges to meet the required tolerances. We ran a trial with a waterjet supplier. Although the cutting time per part was 30% longer, the elimination of all secondary finishing work meant their total production time per batch was reduced by half. This is why a deeper dive into how speed, precision, and edge quality interact is essential for making the most profitable decision.
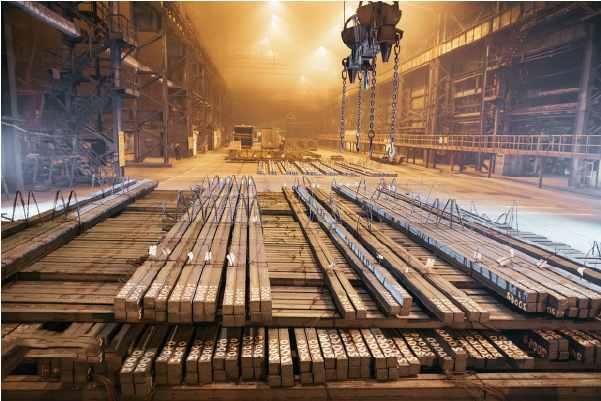
The Speed Equation: Inches Per Minute vs. Total Throughput
When comparing cutting speeds, it's easy to get lost in metrics like inches per minute (IPM) or meters per minute (m/min). A high-power fiber laser2 cutting 1mm stainless steel can achieve speeds over 20 m/min, a rate that plasma and waterjet cannot hope to match. This makes laser the clear winner for high-volume production of thin sheet metal parts, common in the electronics and appliance industries. However, the equation changes dramatically as material thickness increases. At 25mm thickness, a plasma cutter becomes significantly faster than a laser, whose beam struggles to penetrate efficiently. Waterjet is typically the slowest in a direct IPM comparison across most metal thicknesses.
However, a focus on cutting speed alone is misleading. The more important metric is total throughput, which accounts for the entire workflow. This includes setup time, programming, cutting, and any necessary secondary operations. For example, while a plasma cutter might finish cutting a batch of parts first, if those parts then require an hour of manual grinding to remove dross and smooth the edges, the overall process might be slower than a waterjet that produces a finished edge straight off the machine. At MFY, we encourage our clients to time the entire process—from raw plate to finished, usable part—to understand the true speed of each technology in their specific context.
This holistic view also includes factors like machine uptime and maintenance. A waterjet's high-pressure pump requires more frequent and complex maintenance than a robust plasma system, which can impact available production hours. Conversely, dialing in the perfect settings on a laser for a new material can sometimes take longer than programming a waterjet. True speed is a measure of finished parts per shift, not just the velocity of the cutting head.
The Precision Frontier: Tolerances and Kerf Width
Precision is a multi-faceted metric, encompassing part accuracy (dimensional tolerance), cut angle (bevel), and kerf width. Laser cutting is the champion of precision in most common industrial applications. A well-maintained fiber laser can consistently achieve tolerances of ±0.1mm or even tighter, with a very narrow kerf width (often less than 0.5mm). This narrow kerf is a significant advantage, as it allows for intricate contours and enables parts to be nested closer together on a plate, maximizing material utilization and reducing scrap—a direct cost saving.
Waterjet cutting can achieve even higher tolerances, sometimes reaching ±0.05mm, and modern systems with 5-axis heads can actively compensate for taper to produce perfectly square edges. This makes it the go-to method for applications where absolute precision is non-negotiable, such as in aerospace components or medical implants. Its kerf is slightly wider than a laser's but still allows for efficient part nesting. Plasma cutting has the lowest precision of the three, with typical tolerances in the range of ±0.5mm. The kerf is also the widest, and the edge often has a noticeable bevel, although high-definition plasma systems have significantly improved on these fronts.
For a distributor client of ours who provides parts for architectural projects, the precision of laser cutting is essential. They fabricate decorative stainless steel panels with intricate patterns. The tight tolerances of the laser ensure that all the pieces fit together perfectly during on-site installation, avoiding costly adjustments. For them, the slightly higher cost of laser cutting is easily justified by the guarantee of perfect fit and finish, which upholds their reputation for quality.
A Practical Comparison: The Heat-Affected Zone (HAZ) Factor
The Heat-Affected Zone (HAZ) is a critical, and often overlooked, aspect of precision that directly results from the cutting process. Both plasma and laser cutting are thermal processes, meaning they use intense heat to melt the metal. This heat inevitably conducts into the surrounding material, creating a zone where the metal's microstructure and properties have been altered. In plasma cutting, this zone can be quite large, potentially affecting the hardness, strength, and corrosion resistance of materials like stainless steel. The HAZ from a laser is significantly smaller but still present.
This is where waterjet's "cold-cutting" nature provides an unparalleled advantage. Because it's a mechanical erosion process, it imparts no heat into the workpiece. There is zero HAZ. This is not just a minor benefit; it is a critical requirement for performance-sensitive applications. When cutting pre-hardened steels, the heat from a laser or plasma would soften the edge, ruining the material's properties. When fabricating parts from certain stainless steel grades for corrosive environments, the HAZ can become a preferential site for rust and corrosion to begin.
The presence of a HAZ often necessitates secondary processing. Edges may need to be machined or ground away to remove the affected material, adding time, labor, and cost to the production cycle. Therefore, when comparing precision, one must ask if the precision achieved by the laser is sufficient, or if the complete absence of thermal effects from a waterjet is required to maintain the material's integrity. For many general fabrication jobs, the small HAZ from a modern laser is perfectly acceptable. For high-performance applications, the "true precision" of a waterjet—delivering a part with unchanged material properties—is the only viable option.
Metric | Plasma Cutting | Laser Cutting | Waterjet Cutting |
---|---|---|---|
Typical Speed (10mm Steel) | High (~2 m/min) | Medium (~1.5 m/min) | Low (~0.4 m/min) |
Typical Precision | ±0.5 mm | ±0.1 mm | ±0.05 mm |
Kerf Width | Wide | Narrow | Medium |
Heat-Affected Zone (HAZ) | Significant | Minimal | None |
Laser offers best speed-precision balanceTrue
Fiber lasers provide optimal combination of cutting speed and precision for thin-to-medium metals, as shown in the throughput matrix analysis.
Plasma is always fastest methodFalse
While plasma excels on thick metals, fiber lasers are significantly faster for thin materials (20+ m/min on 1mm steel).
What are the cost implications of using plasma, laser, and waterjet for plate cutting?
Focusing solely on the initial machine purchase price is a trap many businesses fall into. This narrow view ignores the substantial ongoing operational costs which can slowly erode your profitability, turning a seemingly good investment into a long-term financial burden. Let's perform a complete financial analysis.
The total cost of ownership is the most critical metric. Plasma has the lowest initial investment, laser has the highest, and waterjet sits in the middle. However, operational costs vary significantly, with plasma having high consumable usage, laser having high power and gas costs, and waterjet having high abrasive and maintenance expenses.
I often share the story of a manufacturing client in Vietnam who was expanding their capabilities. They were tempted by the low entry price of a plasma system to cut 5mm stainless steel sheets. We sat down and modeled their total cost per part. We factored in the higher electricity and consumable costs of plasma, plus the added labor for dross removal. We compared this with a fiber laser. Despite the laser's much higher initial price tag, its faster speed, lower labor requirement, and superior material utilization through nesting resulted in a 20% lower cost-per-part and a projected ROI that was 18 months faster. This is the level of detail required to make a sound financial decision.
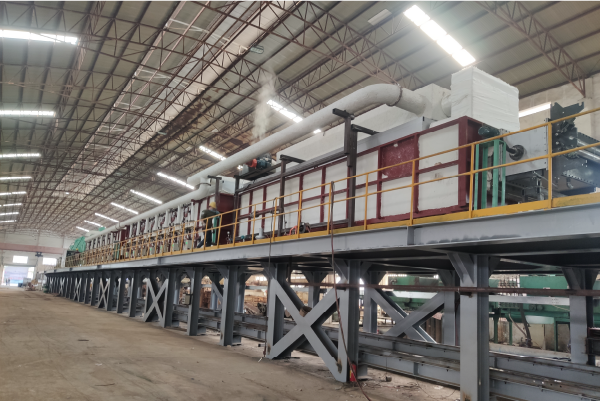
Upfront Investment: The Capital Expenditure (CapEx) Breakdown
The initial purchase price, or Capital Expenditure (CapEx), is the most visible cost and varies dramatically between the three technologies. A standard air plasma system suitable for a small fabrication shop can be acquired for as little as $20,000, while a large, gantry-style high-definition plasma machine can exceed $100,000. These systems represent the lowest barrier to entry for in-house metal cutting.
Waterjet systems occupy the middle ground. A basic machine might start around $60,000, but a more typical industrial setup with a reliable high-pressure pump, a large cutting bed, and features like taper compensation will generally fall in the $100,000 to $250,000 range. The price is heavily influenced by the pump pressure (PSI) and the sophistication of the cutting head.
Laser cutters, particularly high-power fiber lasers, represent the highest initial investment. An entry-level machine might be found for around $150,000, but the majority of industrial-grade systems that our clients at MFY consider are in the $300,000 to $1,000,000+ range. This cost is driven by the laser's power (kilowatts), the size of the cutting table, and the inclusion of automation features like load/unload systems, which are crucial for maximizing throughput in a 24/7 production environment.
Operational Costs (OpEx): The Hidden Financial Drain
Operational Expenditure (OpEx), or the cost to run the machine per hour, is where the true financial picture emerges. This is a complex calculation involving utilities, consumables, and routine maintenance. For plasma, the primary costs are electricity, compressed air, and a steady supply of consumables like electrodes, nozzles, and swirl rings, which wear out relatively quickly.
Laser cutting's OpEx is dominated by two factors: extremely high electricity consumption, especially for high-power units, and the cost of assist gases (like nitrogen for a clean cut on stainless steel or oxygen for faster cutting of carbon steel). While consumables like lenses and nozzles last longer than plasma's, they are also more expensive to replace. The overall hourly cost for a laser can often be the highest of the three.
Waterjet's main operating cost is the abrasive. Garnet is consumed continuously during cutting and can account for 60-70% of the hourly running cost. Other significant costs include electricity to power the high-pressure pump, the water itself (though often recycled), and the frequent replacement of high-wear components in the pump and nozzle assembly (seals, orifices, mixing tubes). Neglecting a proper maintenance schedule for a waterjet pump can lead to catastrophic and very expensive failures.
Calculating True ROI: Cost-Per-Part and Beyond
The ultimate goal of this financial analysis is to determine the cost-per-part, which is the key to calculating your true Return on Investment (ROI). This metric synthesizes CapEx and OpEx into a practical, decision-making figure. To calculate it, you must consider all contributing factors: labor cost per hour, machine cutting time per part, material cost (including waste generated from the kerf), and the cost of any required secondary operations.
Let's imagine a scenario: cutting a part from a 10mm stainless steel plate. Plasma might be the fastest (lowest cutting time) but has a wide kerf (more material waste) and requires a 5-minute deburring process per part (high labor cost). Laser is faster than waterjet, has a narrow kerf (low material waste), but a very high hourly running cost. Waterjet is the slowest (highest cutting time) but produces a perfect edge (zero secondary labor) and has a moderate hourly cost.
By plugging in your specific labor, material, and utility costs, you can build a spreadsheet to compare the true cost-per-part for each technology. A business cutting thousands of identical parts might find the laser's speed and automation provide the lowest cost, justifying the high CapEx. A custom job shop doing low-volume, high-precision work might find the waterjet's elimination of secondary processing makes it the most profitable, despite its slow speed. This detailed analysis moves beyond simple cost comparisons to reveal the most financially sound path for your specific business.
Cost Factor | Plasma Cutting | Laser Cutting | Waterjet Cutting |
---|---|---|---|
Initial Cost (CapEx) | Low ($) | High ($$$) | Medium ($$) |
Electricity Cost | Medium | Very High | High |
Consumables Cost | High (Nozzles, Electrodes) | Medium (Gases, Optics) | Very High (Abrasive Garnet) |
Maintenance Cost | Low | Medium | High (Pump Maintenance) |
Secondary Operations | Often Required (Dross Removal) | Minimal | None |
Plasma has lowest initial costTrue
Plasma systems have the lowest upfront purchase price among the three cutting technologies, starting at $20,000.
Laser has lowest operational costFalse
Laser cutting actually has very high operational costs due to electricity and assist gases, often making it the most expensive to operate hourly.
What are the environmental considerations for plasma, laser, and waterjet cutting methods?
In today's global market, sustainability is no longer an optional extra; it's a critical business consideration. Ignoring the environmental impact of your operations can lead to regulatory penalties, harm your brand's reputation, and alienate an increasingly eco-conscious customer base. Let's assess the green footprint of each method.
Waterjet cutting is generally the most environmentally friendly option as it produces no hazardous fumes or gases, and its primary waste—abrasive sludge—is often non-hazardous and can be recycled. Plasma and laser cutting are thermal processes that generate harmful fumes, requiring robust ventilation and filtration systems.
At MFY, we are committed to helping our clients build not just efficient but also responsible supply chains. This conversation is becoming more frequent, especially with our partners in Europe and North America who face stringent environmental regulations. Choosing a cutting technology is now intertwined with corporate social responsibility (CSR) goals. The decision impacts workplace safety, waste disposal costs, and a company's overall carbon footprint. A "cheaper" technology that incurs heavy environmental compliance costs or poses risks to employee health is a false economy. Let's delve into the specific environmental impacts you need to consider.
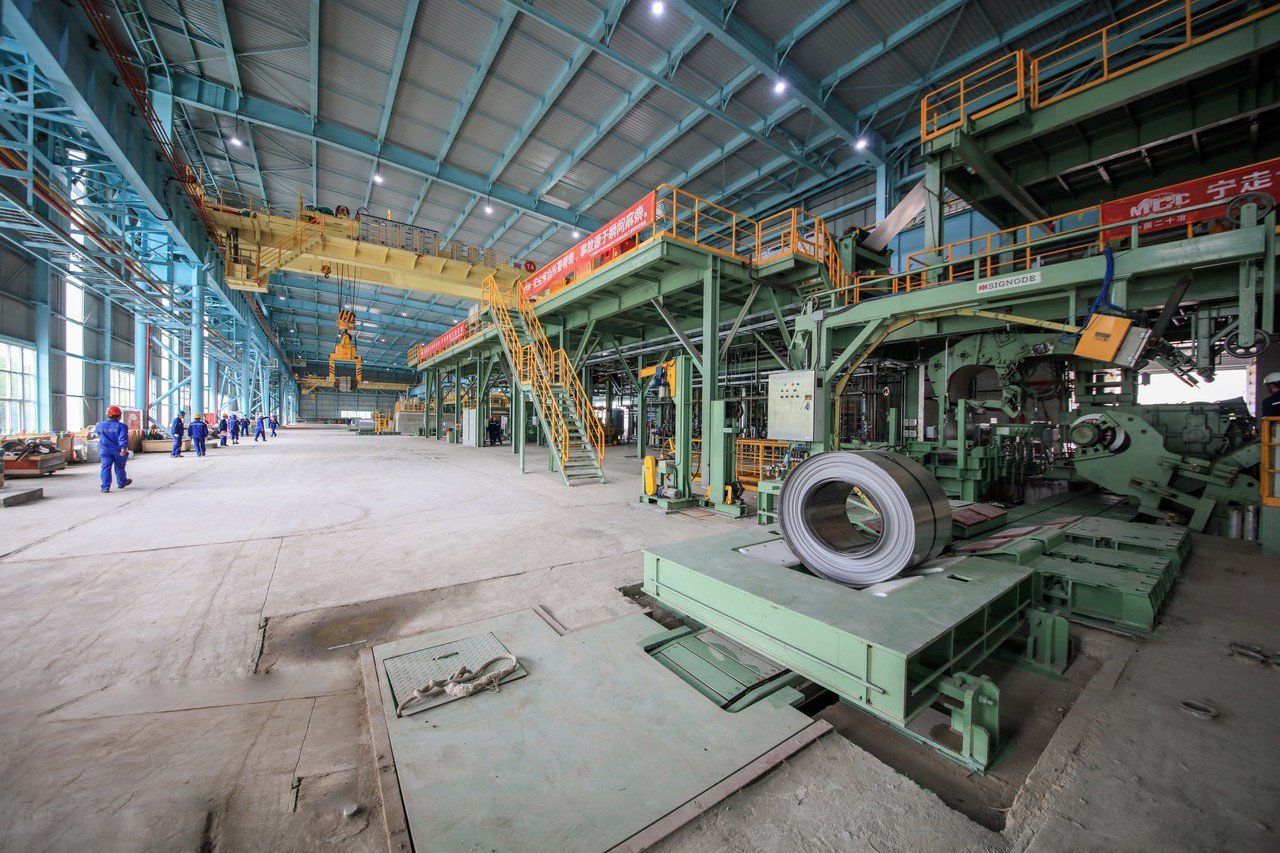
Energy Consumption and Carbon Footprint
The energy required to power these industrial machines is a major contributor to their environmental footprint. High-power fiber lasers3 are notoriously energy-hungry. The process of generating the laser beam and powering the necessary cooling systems (chillers) results in significant electricity consumption per hour of operation. This directly translates to a higher carbon footprint, especially in regions where the electrical grid relies heavily on fossil fuels.
Plasma cutting systems also consume a substantial amount of electricity to generate the plasma arc. While generally less than a high-power laser, it is still a significant energy draw. The efficiency of the power supply and the thickness of the material being cut heavily influence the overall consumption.
Waterjet systems, powered by their large electric-motor-driven pumps, are also high energy consumers. However, their energy profile can be different. The pump runs continuously, but the actual energy used to cut can sometimes be lower per part for very thick materials compared to a laser struggling at its limit. A comprehensive energy audit should compare the kilowatt-hours (kWh) consumed per part produced, not just the hourly rating of the machine, to get a true picture of the carbon footprint associated with each technology.
Waste Generation and Disposal
Each cutting method produces a unique stream of waste that must be managed responsibly. Plasma and laser cutting create metallic dust and dross (resolidified molten metal). More importantly, they generate fumes containing fine particulates and potentially hazardous compounds depending on the material being cut. When cutting stainless steel, these fumes can contain hexavalent chromium4 and nickel oxides, which are known carcinogens and require specialized, high-efficiency filtration and ventilation systems to protect workers and the environment. The captured dust and used filters must then be disposed of as hazardous waste, adding complexity and cost.
Waterjet cutting's primary waste product is a sludge composed of used garnet abrasive, water, and fine particles of the material that was cut. For most applications, this sludge is classified as non-hazardous and can be disposed of in a standard landfill, making management simpler and cheaper. Furthermore, there are now advanced recycling systems available that can separate the used garnet, wash it, and reclaim a significant percentage for reuse, drastically reducing both new abrasive purchases and waste output. This "closed-loop" potential makes waterjet an attractive option from a waste reduction standpoint.
Workplace Safety and Air Quality
Protecting the health and safety of operators is a paramount environmental and ethical concern. The thermal processes of plasma and laser cutting present significant air quality challenges. As mentioned, the fumes generated can be highly toxic. Without proper engineering controls, such as downdraft tables and high-capacity fume extraction systems, the concentration of harmful particulates in the air can easily exceed safe occupational exposure limits. In addition to fume hazards, operators must be protected from the intense UV radiation generated by the plasma arc and the risk of eye damage from stray laser reflections.
Waterjet cutting eliminates the risk of toxic fumes and UV radiation. The primary hazards are related to the extreme high pressure of the water stream and the high noise levels generated during cutting, which can exceed 100 decibels. These risks are managed through robust machine enclosures, safety interlocks, and the use of personal protective equipment (PPE) like ear and eye protection. While all industrial machinery presents risks, the nature of the waterjet's hazards—noise and high pressure—are often considered more straightforward to mitigate through physical guarding and standard PPE compared to the invisible and insidious danger of toxic airborne fumes.
Environmental Factor | Plasma Cutting | Laser Cutting | Waterjet Cutting |
---|---|---|---|
Airborne Emissions | Hazardous Fumes (e.g., Hexavalent Chromium) | Hazardous Fumes and Particulates | None (Water Vapor) |
Energy Consumption | High | Very High | High |
Solid Waste | Metallic Dross, Used Consumables | Metallic Dross, Used Optics | Abrasive/Material Sludge (Often Non-Hazardous) |
Recycling Potential | Low (Scrap Metal Only) | Low (Scrap Metal Only) | High (Abrasive can be recycled) |
Primary Safety Hazard | Toxic Fumes, UV Radiation | High-Energy Light Beam, Fumes | High-Pressure Water, High Noise Levels |
Waterjet cutting produces non-hazardous wasteTrue
Waterjet cutting primarily generates abrasive sludge that is typically classified as non-hazardous and can often be recycled.
Laser cutting has the lowest energy consumptionFalse
High-power fiber lasers are actually the most energy-intensive option, requiring significant electricity for both the laser generation and cooling systems.
How to choose the best plate cutting method for different industrial applications?
After analyzing the technology, performance, cost, and environmental impact, making the final decision can still seem complex. The key is to realize there is no universal "best" method; the right choice is the one that best aligns with your specific operational reality. A misguided decision at this stage can hamstring your entire production process. I'll now provide a practical framework to guide your choice.
To choose the best method, evaluate your primary material, thickness range, required precision, production volume, and budget. For thick, conductive metals where speed trumps precision, plasma is ideal. For high-volume, high-precision cutting of thin to medium metals, choose laser. For any material requiring no thermal distortion, choose waterjet.
As a partner to global businesses, my role at MFY is often to act as a consultant, helping clients see the bigger picture. I recently worked with an Engineering & Construction contractor who was sourcing parts for a single large project that involved thick structural steel components, intricate stainless steel architectural panels, and some sensitive composite materials. Instead of trying to find one supplier5 who used a single "do-it-all" method, we helped them develop a multi-sourcing strategy. They used a fabricator with high-def plasma for the structural parts, a specialist with a fiber laser for the panels, and a waterjet shop for the composites. This strategic approach, matching the right technology to the right task, ensured optimal quality, cost, and lead time for every component of their project.
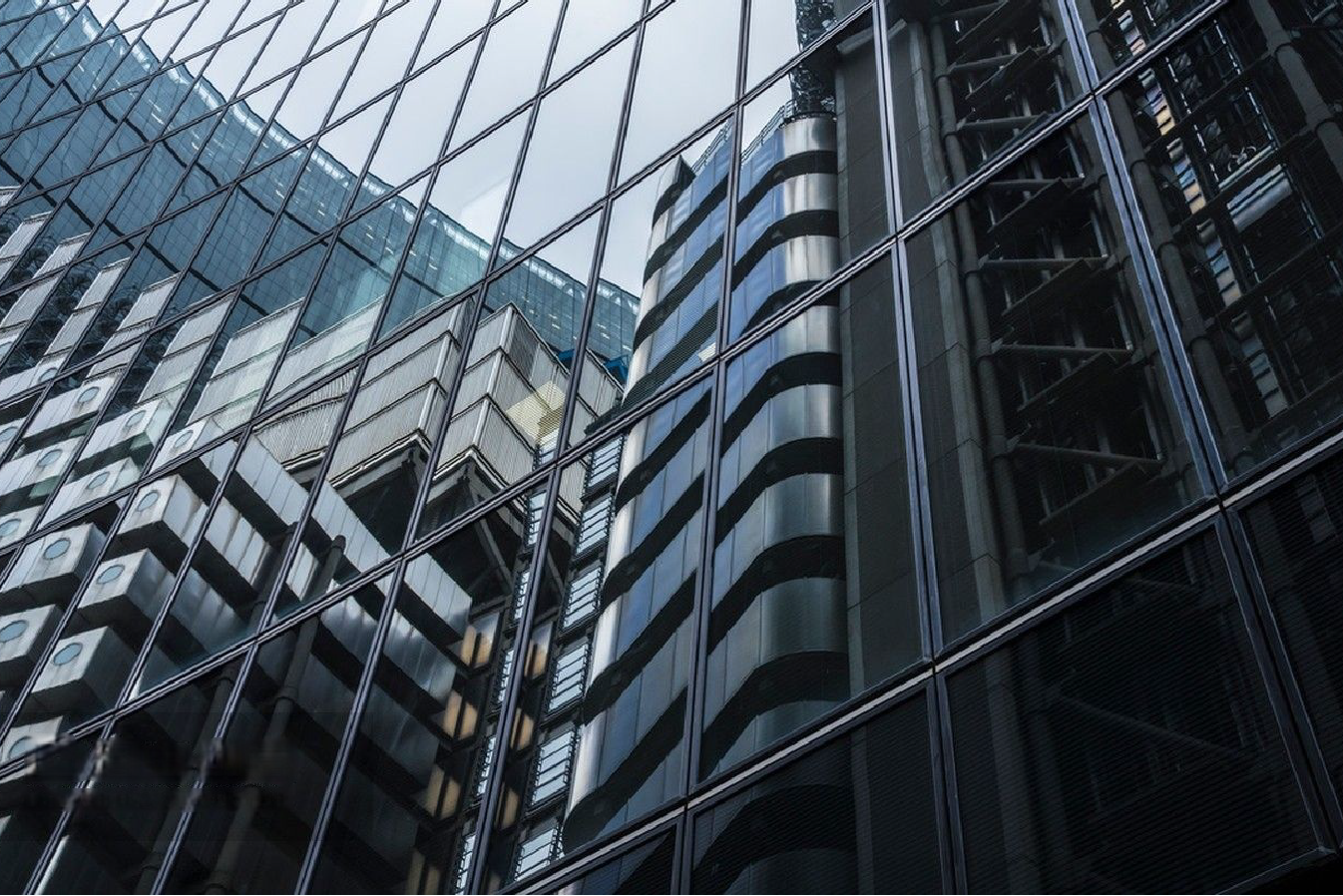
Application-Specific Scenarios: Matching Technology to Task
The best way to begin is by looking at established industry practices, as they are often based on years of optimization. For heavy manufacturing sectors like shipbuilding, railcar production, or heavy equipment fabrication, where thick carbon steel plates (e.g., 20mm to 100mm) are the norm, plasma cutting is the dominant technology. Its high speed and low capital cost make it unbeatable for processing large volumes of thick plate where minor edge bevel and a larger HAZ are acceptable.
In contrast, industries like automotive manufacturing, electronics, and medical devices rely heavily on laser cutting. An automotive supplier mass-producing chassis components from high-strength steel sheets requires the speed, repeatability, and precision that only a laser can provide. Similarly, a medical device company cutting small, intricate parts from thin stainless steel tubing needs the clean, burr-free edge and minimal HAZ of a laser. At MFY, many of our manufacturing clients fall into this category, leveraging laser cutting for its balance of speed and precision on stainless steel sheets and coils up to 15mm.
Waterjet cutting carves its niche in specialized and high-value applications. The aerospace industry uses it to cut heat-sensitive titanium and nickel-based superalloys without altering their metallurgical properties. Architectural firms and custom fabricators use it to cut not only thick metals with a perfect edge finish but also materials that laser and plasma cannot touch, like glass, stone, marble, and advanced composites. Distributors and traders who serve a wide variety of customers often benefit from having access to waterjet services to handle unique and unpredictable requests.
The Material and Thickness Matrix
A simple decision matrix based on material and thickness can quickly narrow down your options. This is the first filter you should apply. First, identify the material. Is it electrically conductive? If not (e.g., glass, plastic, stone, wood), your only option is waterjet. If it is conductive, you can consider all three.
Next, consider the primary thickness range you will be working with. If your work consists almost exclusively of metal plates thicker than 25mm, plasma is almost certainly your most cost-effective and fastest choice. If your core business involves cutting sheet metal or plates under 15mm, a fiber laser will likely provide the best balance of speed, precision, and cost-per-part. Waterjet is the most versatile across the thickness spectrum; it can cut materials as thin as foil and as thick as 300mm or more, but its slow speed makes it less economical for high-volume work in the ranges where plasma and laser excel.
Think of it as a spectrum. On the thin end (<1mm), laser dominates. In the middle range (1mm-20mm), laser and high-def plasma compete, with the choice depending on the required precision. On the thick end (>25mm), plasma takes over for speed, while waterjet is the choice for precision or for materials that cannot be heated. By identifying where 80% of your work falls on this spectrum, you can make a much more targeted decision.
Building a Business Case: A Final Checklist
To synthesize everything, you must build a comprehensive business case tailored to your company. Move beyond a simple price comparison and ask yourself the following critical questions. Answering them honestly will illuminate the best path forward and ensure your investment aligns with your strategic goals.
- Primary Application: What specific parts will I be making? What is their end-use? (e.g., structural beams, intricate panels, machine components).
- Material & Thickness: What material types and thickness ranges will constitute 80% of my cutting volume?
- Precision & Edge Quality: What dimensional tolerances are required? Is a Heat-Affected Zone (HAZ) acceptable? Is a smooth, burr-free edge required to avoid secondary operations?
- Volume & Speed: What is my expected production volume? Is minimizing cut time per part (speed) or minimizing total process time per part (throughput) more important?
- Budgetary Constraints: What is my realistic budget for the initial capital investment (CapEx)? More importantly, what is my projected budget for hourly operational costs (OpEx), including consumables, power, and maintenance?
- Workforce & Facility: Do I have operators with the skills to run and maintain the machine? Do I have the necessary space and infrastructure (e.g., power supply, ventilation, foundation) for the system?
- Environmental & Safety: What are the local environmental regulations I must comply with? What is the cost of fume extraction and waste disposal? How does each technology align with my company's safety culture?
By systematically working through this checklist, you transform a confusing technical choice into a clear, data-driven business decision. The "best" cutting method is the one that provides the most profitable and efficient solution for your unique set of answers.
Priority | Best Choice: Plasma | Best Choice: Laser | Best Choice: Waterjet |
---|---|---|---|
Highest Speed | On thick (>20mm) conductive metals | On thin-to-medium (<15mm) metals | N/A (Generally slowest method) |
Highest Precision | Good (with HD systems) | Excellent (±0.1mm) | Superior (±0.05mm, no taper) |
Lowest Initial Cost | Yes | No | No |
Material Versatility | Conductive Metals Only | Most Metals, some organics | Virtually Any Material |
No Heat-Affected Zone | No (Significant HAZ) | No (Minimal HAZ) | Yes (Cold-cutting process) |
Best for Thick Metal | Yes (For Speed & Cost) | No (Limited & Slow) | Yes (For Precision & Material Integrity) |
Plasma is best for thick metalsTrue
Plasma cutting excels in speed and cost-effectiveness for conductive metals over 25mm thick, as mentioned in the material matrix section.
Waterjet is fastest methodFalse
The comparison table clearly shows waterjet is generally the slowest method, though it offers superior precision and material versatility.
Conclusion
Ultimately, there is no single best way to cut a plate. The optimal choice among plasma, laser, and waterjet is a strategic decision that hinges on a careful balance of your specific material, thickness, and precision requirements against your budget, production volume, and operational goals.
-
Understand how waterjet cutting's cold process avoids heat distortion in stainless steel ↩
-
Discover the technology behind high-speed fiber laser cutting for improved production rates ↩
-
Discover the electricity demands and environmental impact of using fiber lasers. ↩
-
Understand the health risks and protective measures related to hexavalent chromium fumes. ↩
-
Learn how combining suppliers with different technologies optimizes project outcomes ↩
Have Questions or Need More Information?
Get in touch with us for personalized assistance and expert advice.