Coil Weight Calculator: Width × Thickness Formula
Struggling with inaccurate coil weight estimates that lead to budget overruns and project delays? Imagine ordering stainless steel based on a rough guess, only to find you’re short on material, halting production, or overstocked, tying up valuable capital. Mastering the fundamental width × thickness formula1 is your first step toward precision.
The width × thickness formula is the starting point for calculating a coil's weight. These two dimensions determine the material's cross-sectional area. This area is then multiplied by the coil's total length and the specific density of the steel grade to yield an accurate theoretical weight.
This calculation is more than just a mathematical exercise; it's a cornerstone of effective project management, inventory control, and logistical planning. While the formula itself seems simple, its real-world application requires an understanding of material properties, manufacturing tolerances, and consistent units. In this guide, I'll walk you through each step, drawing on my experience at MFY helping clients navigate these complexities to ensure their supply chains are as efficient and resilient as possible.
As the Global Business Director for MFY, I’ve seen firsthand how a small miscalculation can ripple through an entire project. It's not just about the numbers; it’s about understanding the material science behind them. For instance, the density difference between a 300-series austenitic stainless steel and a 400-series ferritic grade2 is a critical variable that a basic calculator might miss. This guide moves beyond simple formulas to provide a professional framework for calculation, incorporating the nuances that separate a rough estimate from a reliable, actionable figure. We will explore how factors like industry standards and production tolerances impact the final weight, empowering you to make more informed procurement decisions.
How to begin calculating coil weight using width and thickness?
Feeling overwhelmed by complex formulas and variables? Jumping into a calculation without a clear starting point often leads to errors, rework, and frustration. The most reliable way to begin is by isolating and verifying the two most fundamental inputs: the coil’s specified width and thickness.
To begin calculating coil weight, you must first secure the precise nominal width and thickness from the material's specification sheet or Mill Test Certificate (MTC). These two dimensions are multiplied to find the cross-sectional area, which is the foundational building block for the complete weight formula.
In my years of working with clients across India and Southeast Asia, I've learned that the most common errors often happen at this initial stage. I recall a case with a manufacturing client in Vietnam who was setting up a new production line for kitchen appliances. Their junior procurement officer placed an order based on verbal confirmation of the thickness. However, the actual material delivered was within tolerance but on the lower end of the specification, resulting in a 4% variance in total weight. While seemingly small, this discrepancy disrupted their automated feeding system, which was calibrated for a specific weight per meter. This experience underscores why at MFY, we emphasize starting with certified documentation. Once you have these two verified dimensions—width and thickness—you have established the bedrock of your calculation. This solid foundation is essential before you can move on to consider other critical variables like coil length and material density, which we will explore next. It transforms the task from guesswork into a methodical process, ensuring every subsequent step is built on accuracy and reliability.
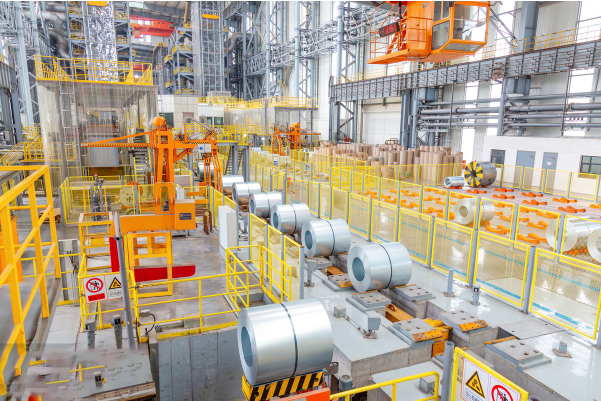
The initial step of gathering width and thickness data is far more nuanced than it appears. It involves understanding the distinction between what is specified and what is physically delivered, the importance of the cross-sectional area, and the reliability of different data sources. For our clients, who range from large-scale construction contractors to precision equipment integrators, mastering this first step is non-negotiable for project success. A deep dive into these aspects reveals why a professional approach to this foundational stage is critical. At MFY, our integrated supply chain model is built on providing this level of precision from the very first specification, ensuring our clients start their projects with confidence and clarity.
Understanding Nominal vs. Actual Dimensions
The first critical concept to grasp is the difference between "nominal" and "actual" dimensions. When you order a stainless steel coil with a 1.0mm thickness, this is the nominal, or named, thickness. However, manufacturing processes are subject to slight variations. International standards, such as those from ASTM (American Society for Testing and Materials) or EN (European Norms), define acceptable tolerance ranges for these variations. For example, a 1.0mm thick coil might have a tolerance of ±0.05mm, meaning the actual thickness at any given point could range from 0.95mm to 1.05mm.
In my experience, this is a crucial detail for engineering and construction contractors. We worked with a client in the Middle East responsible for fabricating architectural cladding for a high-profile skyscraper. The structural engineering calculations depended on a precise weight per square meter to stay within the building's load-bearing limits. A 5% deviation in thickness, while within standard tolerance, would have resulted in a significant weight difference across thousands of square meters, potentially requiring a costly redesign. We worked closely with them, providing coils from our advanced cold-rolling facilities that offered tighter-than-standard tolerances, giving them the predictability they needed.
This highlights why relying solely on the nominal value for critical calculations can be misleading. For precise project costing and engineering, it is essential to consult the supplier about their specific manufacturing tolerances or, even better, to reference the actual measurements provided on the Mill Test Certificate (MTC) that accompanies the shipment. This document provides the certified, measured data for the specific coil you receive.
The Foundational Role of Cross-Sectional Area
Once you have the width and thickness, you calculate the cross-sectional area (Area = Width × Thickness). This value represents the area of the "face" of the steel strip if you were to cut through it. Why is this so important? Because it directly determines how much material is packed into every linear meter of the coil. Two coils with the same outer diameter can have vastly different weights if their cross-sectional areas differ. A wider or thicker strip naturally contains more mass per unit of length.
This concept is central to our production philosophy at MFY. Our cold-rolling and processing lines are designed to achieve exceptional consistency in both width and thickness. For our clients in the automotive parts manufacturing sector, for instance, a consistent cross-sectional area is vital. Their stamping and forming machinery is calibrated to process strips with specific dimensions. Any significant deviation can lead to tool damage, production stoppages, and a higher rate of defective parts.
Therefore, when you begin your calculation, think of it not just as multiplying two numbers, but as defining the fundamental substance of your material. This cross-sectional area becomes the constant that, when multiplied by the strip's total length and density, gives you the final weight. Focusing on getting this area right is the most effective way to minimize errors from the outset.
Sourcing and Verifying Dimensional Data
The reliability of your calculation depends entirely on the quality of your source data. In the stainless steel trade, information can come from several places, each with a different level of accuracy. A quotation or a product catalog will typically list nominal dimensions, which are great for initial estimates but not for final calculations. The packing list or the label on the coil itself will often provide more specific details, but the ultimate source of truth is the Mill Test Certificate (MTC).
At MFY, we treat the MTC as a pact of quality with our client. It's a formal document that certifies the coil's exact properties, including its precise dimensions and weight as measured at our facility. I always advise our clients, especially distributors and traders who manage large inventories, to build their internal systems around the data from the MTC. This practice eliminates ambiguity and provides a traceable record for quality control.
Here is a comparison of common data sources:
Data Source | Type of Data | Reliability for Calculation | Best Use Case |
---|---|---|---|
Supplier Quote | Nominal | Low | Budgetary Estimates, Initial Inquiry |
Packing List | Nominal / Actual | Medium | Logistics, Receiving Checks |
Product Label | Nominal / Actual | Medium | Warehouse Identification |
Mill Test Certificate (MTC) | Certified Actual | High | Final Calculation, Quality Assurance, Engineering |
By insisting on the MTC as the primary source for your width and thickness inputs, you are adopting a best practice that aligns with the highest standards of industrial procurement and ensures your calculations are as accurate as possible.
Width × thickness = cross-sectional areaTrue
Multiplying width by thickness gives the cross-sectional area, which is fundamental for weight calculation.
Nominal dimensions equal actual dimensionsFalse
Nominal dimensions are specifications while actual dimensions may vary within manufacturing tolerances.
What measurement units are required for accurate coil weight calculation?
Have your calculations ever been thrown off by a simple unit mismatch? Confusing millimeters with inches or kilograms with pounds is a common pitfall that can completely invalidate your results, leading to significant procurement and logistical errors. Standardizing your units before you begin is the crucial solution.
For an accurate coil weight calculation, all dimensional inputs—width, thickness, and length—must be in a consistent measurement system, either metric (e.g., meters) or imperial (e.g., inches). The material's density unit (e.g., kg/m³ or lb/in³) must also align with the chosen system to ensure a correct result.
This isn't just a matter of academic rigor; it has profound real-world consequences. I remember a complex project involving a partnership between a Southeast Asian fabricator and their European client. The designs were specified in metric, but the fabricator's team was more accustomed to working with imperial units for some of their local sourcing. This led to confusion where a requirement for 2-inch material was misinterpreted, causing a significant over-order of stainless steel pipes. The financial loss and project delay were considerable. As a global supplier, MFY operates at the intersection of these systems every day. Our documentation and support teams are trained to bridge these gaps, providing clarity for clients in over 20 countries. We ensure that whether you work in millimeters or inches, the data you receive from us is clear, consistent, and tailored to your needs. This dedication to clarity is vital because once units are standardized, you can confidently apply them to the weight formula, which involves not just dimensions but also the critical factor of material density.
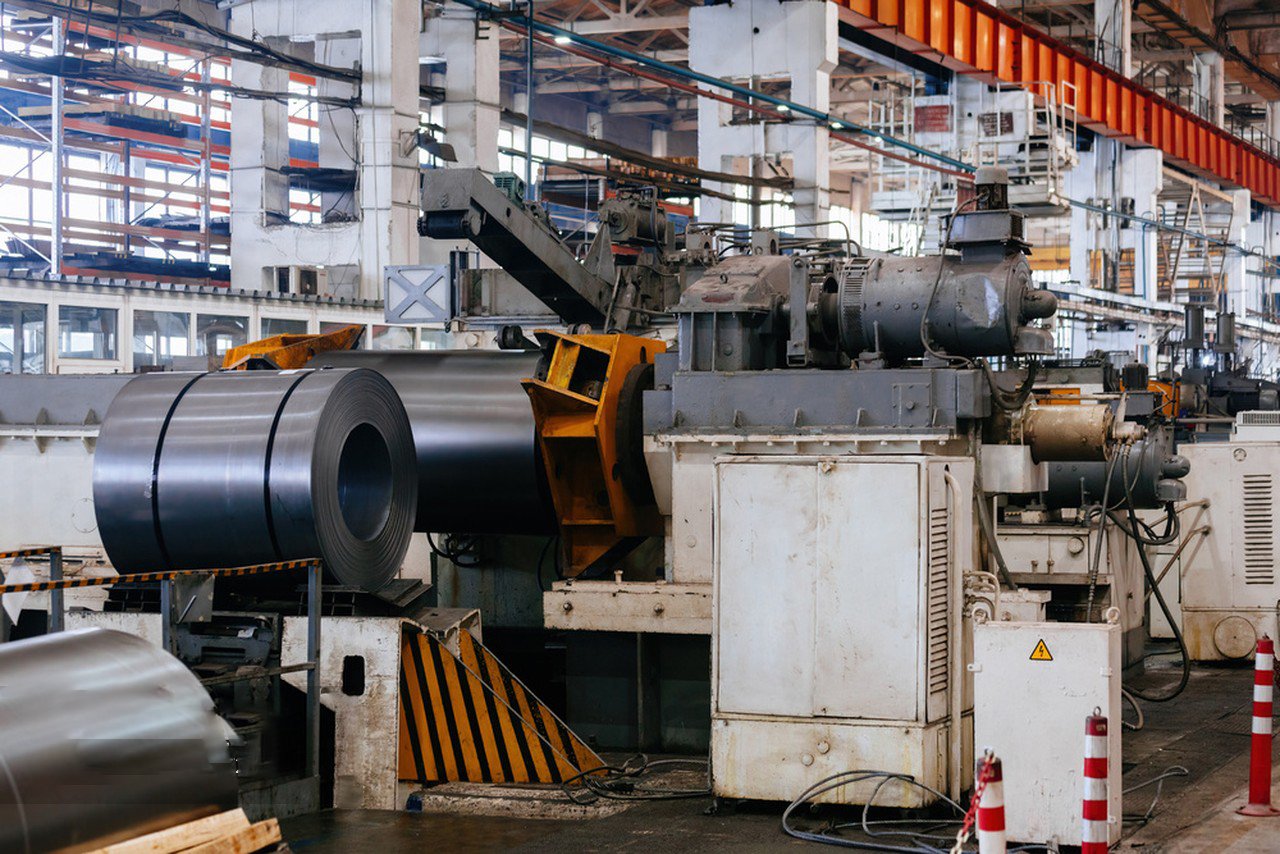
Ensuring unit consistency is a fundamental discipline in engineering and international trade. The global steel market, while increasingly standardized, still contends with the legacy of different measurement systems. For any company involved in sourcing or using stainless steel coils, understanding how to navigate these systems is key to avoiding costly errors. At MFY, our experience in exporting to diverse markets like Russia, India, and the Middle East has reinforced the importance of meticulous unit management. It’s a core component of our service, protecting our clients from the hidden risks of miscalculation and ensuring seamless integration of our products into their projects.
The Metric System (SI Units): The Global Standard
In the international steel industry, the metric system, or International System of Units (SI), is the undisputed standard. Dimensions are typically specified in millimeters (mm)1, length in meters (m), and weight in kilograms (kg) or metric tons (t). This standardization is a massive advantage for global trade, as it creates a common language for suppliers, engineers, and clients across different countries. For MFY's key export markets in Asia and the Middle East, the metric system is the default for all technical specifications and commercial transactions.
When you begin your calculation, converting all inputs to a consistent metric base is the most reliable approach. For instance, if you have a width of 1219mm, a thickness of 1.2mm, and a length of 2500m, all your units are already aligned. The corresponding density for stainless steel2 should then be used in a compatible format, such as kilograms per cubic meter (kg/m³). Before performing any multiplication, a crucial first step is to convert all millimeter dimensions into meters (e.g., 1219mm = 1.219m and 1.2mm = 0.0012m). This prevents astronomical errors in the final volume calculation.
Our production processes at MFY are entirely metric-based. From our cold-rolled processing lines to our tube manufacturing facilities, all machinery and quality control systems are calibrated to SI units. This ensures that the data on our MTCs is precise and directly usable for our clients who operate within this global standard, eliminating the need for conversions and reducing the risk of error.
Navigating Imperial Units and Cross-Border Challenges
While the metric system dominates, the imperial system—using inches, feet, and pounds—remains prevalent in some markets, most notably the United States. This can create significant challenges for international projects. A US-based engineering firm might specify a coil with a width of 48 inches and a thickness of 0.0478 inches (18 gauge). A manufacturer in another country must convert these dimensions to metric to align with their production capabilities and then convert them back for reporting purposes.
This is where a knowledgeable supplier becomes a critical partner. We recently assisted an equipment integrator client in India who was building a complex machine for export to the US. The end-user's specifications were entirely in imperial units. Our team at MFY worked with them to meticulously translate every material requirement into our metric production system, ensuring the 316L stainless steel coils we supplied met the precise dimensional and weight requirements. We provided dual-unit documentation (MTCs and packing lists showing both mm/kg and in/lb) to facilitate smooth customs clearance and final assembly in the US.
The key conversion factors to always have on hand are:
- 1 inch = 25.4 millimeters
- 1 foot = 0.3048 meters
- 1 kilogram = 2.20462 pounds
Failing to apply these conversions correctly is one of the quickest ways to derail a project budget.
Density Units: The Silent Culprit of Miscalculation
The most subtle, yet critical, aspect of unit consistency is density. Density is a measure of mass per unit of volume (Mass/Volume). The unit you use for density must correspond to the units you used for your dimensions. If you calculate the coil's volume in cubic meters (m³), you must use a density value expressed in kilograms per cubic meter (kg/m³). If you work in imperial and calculate the volume in cubic inches (in³), your density must be in pounds per cubic inch (lb/in³).
This is a frequent point of error. A user might correctly calculate the volume in cubic meters but then mistakenly use a density value they found online in grams per cubic centimeter (g/cm³), leading to a result that is off by a factor of one million. At MFY, we provide clear density specifications for all our products.
Here’s a table showing the approximate densities of common stainless steel grades in both metric and imperial units, which is essential for accurate calculations:
Steel Grade | Density (kg/m³) | Density (g/cm³) | Density (lb/in³) |
---|---|---|---|
SS 304/304L | 8000 | 8.00 | 0.289 |
SS 316/316L | 8000 | 8.00 | 0.289 |
SS 430 | 7700 | 7.70 | 0.278 |
SS 201 | 7800 | 7.80 | 0.282 |
As you can see, not only do the units matter, but the grade itself impacts the density. Using the wrong density value is as significant an error as using the wrong dimensions. Always verify both the unit and the value for the specific grade of steel you are using.
Metric system is global standardTrue
The international steel industry predominantly uses SI units (mm, m, kg) for standardization across global trade.
Density units don't affect calculationsFalse
Density units must match dimensional units (kg/m³ with m³ or lb/in³ with in³) to avoid calculation errors.
How do you apply the width × thickness formula in coil weight calculation?
You have the formula's components, but do you know how to assemble them for a real-world coil calculation? Knowing the inputs is one thing, but applying them in the correct sequence is what transforms raw data into a reliable weight estimate, preventing costly procurement mistakes.
To apply the width × thickness formula, first calculate the cross-sectional area. This area is then multiplied by the total length of the steel strip in the coil. Finally, this resulting volume is multiplied by the material's specific density to arrive at the total coil weight.
The full, practical formula is Weight = Width × Thickness × Length × Density. However, a coiled strip3 presents a unique challenge: its "Length" is not a simple, measurable dimension. This is where many people get stuck. You cannot just take a tape measure to a 20-ton coil. The length must be calculated from the coil's geometry—specifically, its Outer Diameter (OD) and Inner Diameter (ID). This step is what elevates a basic calculation into a true engineering estimate. In my role at MFY, I often guide clients through this process, showing them how to derive the length accurately. This skill is particularly valuable for distributors and service centers who need to calculate the weight of partial coils remaining in their inventory. It empowers them to provide quick, accurate quotes and manage their stock with precision. Understanding how to unlock this "hidden" length is the key to applying the formula correctly.
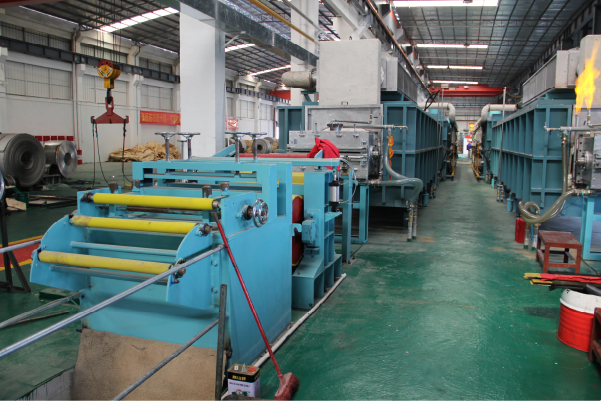
Moving from the theoretical formula to a practical application requires a methodical, step-by-step approach4. The process involves more than just plugging numbers into a simple equation; it requires an understanding of geometric principles to first determine the coil's length. This is a critical skill for anyone in the steel industry, from procurement managers to warehouse supervisors. At MFY, we believe in empowering our clients with this knowledge, as it fosters a deeper understanding of the product and leads to more efficient operations. By breaking down the calculation into manageable steps, we can demystify the process and ensure anyone can achieve an accurate result.
Step 1: Calculating the Total Length of the Unrolled Strip
The first and most complex part of the application is determining the total length of the steel strip. Since the strip is wound into a coil, its length is a function of its thickness and the diameters of the coil. The formula to calculate this length is derived from the principle that the volume of the material is the same whether it's coiled or flat.
The standard formula for the length of a coiled strip is:
Length = [π × (OD² - ID²)] / (4 × Thickness)
Let's break down each variable:
- π (Pi): A mathematical constant, approximately 3.14159.
- OD (Outer Diameter): The full diameter of the coil from edge to edge.
- ID (Inner Diameter): The diameter of the hollow center of the coil (the eye).
- Thickness: The thickness of the steel strip.
It is absolutely critical that all these inputs are in the same unit (e.g., all in meters or all in millimeters) before you start. Let's take a practical example for a typical MFY stainless steel coil. Suppose we have a coil with an OD of 1500mm, an ID of 508mm, and a thickness of 1.0mm. First, we convert all units to meters: OD = 1.5m, ID = 0.508m, Thickness = 0.001m.
Applying the formula:
Length = [3.14159 × (1.5² - 0.508²)] / (4 × 0.001)
Length = [3.14159 × (2.25 - 0.258064)] / 0.004
Length = [3.14159 × 1.991936] / 0.004
Length = 6.2578 / 0.004
Length ≈ 1564.45 meters
This calculated length is the crucial missing piece of our primary weight formula.
Step 2: Assembling the Full Weight Formula
Now that we have calculated the length, we can return to our main weight formula and assemble all the components.
The formula is: Weight = Width × Thickness × Length × Density
Let's continue with our example. We have a coil with the following properties:
- Width: 1219mm = 1.219 m
- Thickness: 1.0mm = 0.001 m
- Length: 1564.45 m (calculated in the previous step)
- Density: For Grade 304 stainless steel, we'll use 8000 kg/m³
Now, we multiply these values together:
Weight = 1.219 m × 0.001 m × 1564.45 m × 8000 kg/m³
First, calculate the volume: Volume = 1.219 × 0.001 × 1564.45 = 1.9071 m³
Then, calculate the weight: Weight = 1.9071 m³ × 8000 kg/m³
Weight ≈ 15,256.8 kg or 15.26 metric tons
This step-by-step process, starting with the length calculation and then integrating it into the main weight formula, provides a highly accurate theoretical weight for the coil. It's the same methodology our technical team at MFY uses when planning production runs and providing estimates to our clients.
Practical Application: A Distributor's Inventory Management
This calculation method is not just for full coils; it's an invaluable tool for inventory management, especially for our distributor clients. I worked with a large steel distributor in Russia who regularly sold partial coils to smaller fabricators. Their challenge was determining the weight—and therefore the value—of the remaining partial coils in their warehouse without having to use a scale for every transaction.
We helped them implement a system based on this formula. When a partial coil was returned to stock, their warehouse team would simply measure the new Outer Diameter (OD). Since the ID, width, and thickness were known constants for that coil, they could quickly recalculate the remaining length and weight. This allowed them to update their inventory records in real-time, generate accurate invoices for the material sold, and provide quick quotes for the remaining stock.
Here's a simplified example of how they used this for validation:
Coil ID | Original Weight (MTC) | Measured New OD | Calculated Remaining Weight | Actual Scale Weight | Variance |
---|---|---|---|---|---|
MFY-304-001 | 15,257 kg | 1100 mm | 7,615 kg | 7,630 kg | -0.2% |
MFY-316-005 | 12,110 kg | 950 mm | 5,144 kg | 5,155 kg | -0.21% |
MFY-430-009 | 18,450 kg | 1300 mm | 12,388 kg | 12,420 kg | -0.26% |
As the table shows, the calculated weight was consistently within a fraction of a percent of the actual scale weight. This level of accuracy empowered them to operate more efficiently, reduce handling time, and improve the speed and reliability of their sales process. It's a perfect example of how applying the formula correctly can deliver tangible business benefits.
Length is calculated firstTrue
The length of the coiled strip must be calculated using geometric principles before applying the weight formula.
OD and ID can be in different unitsFalse
All measurements (OD, ID, thickness) must be in the same unit before calculation to ensure accuracy.
What additional factors should be considered when calculating coil weight?
Is your calculated weight still slightly different from the actual scale weight? This frustrating gap often comes from overlooking subtle but important real-world variables that are not included in the basic formula. Let's explore these hidden factors to refine your calculations to a professional level.
Beyond the basic formula, you must consider the specific steel grade's density variations between series (e.g., 304 vs. 430). Additionally, manufacturing tolerances for width and thickness, as permitted by standards like ASTM, and the weight of packaging materials will affect the final gross weight.
These factors represent the difference between an academic calculation and a professional, commercially-reliable estimate. In my early career, I learned a valuable lesson about density. We were quoting a large project that allowed for either 304 or 430 grade stainless steel. I ran the calculations using the standard 304 density, not realizing the client ultimately chose the 430 grade. The density of 430 is about 3.75% less than 304, and on a multi-container shipment, this resulted in a significant total weight difference that impacted shipping costs and the client's budget. This experience taught me that precision lies in the details. It's not enough to know the formula; you must account for material science, manufacturing realities, and even the logistics of packaging. At MFY, this comprehensive approach is standard practice, ensuring our clients receive a product that aligns perfectly with their expectations, both in dimension and in weight.
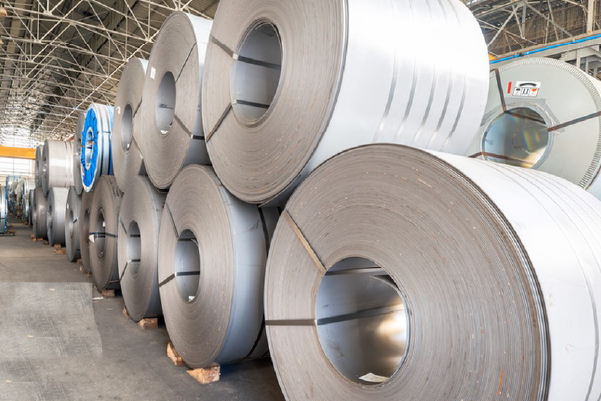
Achieving true accuracy in coil weight calculation requires moving beyond pure mathematics and into the realms of material science and manufacturing practice. The theoretical weight is an excellent baseline, but professionals must account for the variables that influence the final, real-world weight of a delivered coil. These factors—density variations, dimensional tolerances, and packaging—are where a knowledgeable supplier like MFY can provide immense value. By understanding and communicating these nuances, we help our clients in manufacturing, construction, and distribution to mitigate risks, control costs, and execute their projects with a higher degree of certainty.
The Critical Role of Material Density
The density of steel is not a universal constant. It varies based on the chemical composition of the alloy. The addition of different elements like chromium, nickel, and molybdenum—which define the grade and its properties—alters the material's mass per unit of volume. This is one of the most frequently overlooked factors in weight calculation. While many austenitic grades like 304 and 316 have similar densities, ferritic grades like 430 are noticeably less dense.
This has significant commercial implications. Consider a client in the appliance manufacturing industry producing refrigerator doors. They need panels of a specific size. If they switch from Grade 304 to Grade 430 (a common choice for cost-effectiveness in non-corrosive environments), they get more surface area per ton of steel because Grade 430 is lighter. Specifically, the density of SS 430 is around 7700 kg/m³, while SS 304 is 8000 kg/m³. This is a difference of 3.75%. For a company purchasing thousands of tons per year, this translates into a substantial increase in yield and a corresponding reduction in cost per unit produced.
At MFY, we provide detailed technical datasheets for all our products, clearly stating the nominal density for each grade. We consult with clients to ensure they are using the correct density in their calculations, especially when they are considering alternative materials for their applications. Below is a table illustrating this critical data:
Steel Grade | Key Alloying Elements | Primary Use Case | Nominal Density (kg/m³) |
---|---|---|---|
SS 201 | Mn, N (low Ni) | Decorative, Indoor | ~7800 |
SS 304 | Cr, Ni | General Purpose, Food Grade | ~8000 |
SS 316L | Cr, Ni, Mo | Marine, Chemical Processing | ~8000 |
SS 430 | Cr (low C) | Appliances, Automotive Trim | ~7700 |
Using the correct density is a simple check that adds a layer of professional accuracy to any weight calculation.
Navigating Manufacturing Tolerances
No manufacturing process is perfect. As discussed earlier, there will always be a slight variation in the width and thickness of a steel strip. Reputable producers like MFY operate within the strict tolerance bands defined by international standards (e.g., ASTM A480/A480M for flat-rolled stainless steel). These standards specify the permissible deviation from the nominal dimension. For example, for a 1219mm wide coil, the width tolerance might be +4mm / -0mm. For a 1.0mm thickness, the tolerance could be ±0.05mm.
So how does this impact weight calculation? While you should use the nominal dimensions for your primary calculation, understanding the tolerance range is crucial for risk management. A coil produced at the upper end of both width and thickness tolerances will be heavier—and costlier—than one produced at the lower end. For projects with very strict weight budgets, such as in the aerospace or high-performance automotive sectors, this variation matters.
This is where MFY's investment in advanced technology provides a competitive edge. Our state-of-the-art cold-rolling mills utilize computer-controlled sensors to maintain exceptionally tight tolerances, often much stricter than the standard requires. We provide our clients with a "capability report" showing the measured consistency of our production runs. This gives an engineering contractor, for example, the confidence that the 100 tons of steel they order will not unexpectedly come in at 103 tons, disrupting their structural calculations and budget.
Accounting for Packaging and Coil Build-up
The final factor to consider is everything that isn't steel. When you receive a coil, its total (gross) weight includes packaging materials designed to protect it during transit. This can include a wooden or steel skid (pallet), cardboard or plastic ID/OD protectors, plastic wrapping, and steel strapping. The weight of this packaging can range from 50 kg to over 200 kg depending on the size of the coil and the required level of protection for export shipping. The weight on your supplier's invoice and packing list will be broken down into "Gross Weight" and "Net Weight." Your theoretical calculation gives you the Net Weight; the Gross Weight is what you'll see on the shipping documents and what freight costs are based on.
A less obvious factor is the "coil build-up" or "profile." An ideally wound coil is perfectly flat on its faces. However, minor variations in strip thickness can lead to a slightly crowned or uneven profile. This can make getting an accurate OD measurement with a simple tape measure difficult and can introduce small errors into the length calculation. At MFY, our coiling process is carefully controlled to ensure a tight, stable, and flat coil profile. This not only makes the coil safer to handle and process but also ensures that the measured OD is a reliable input for weight verification calculations.
Steel density varies by gradeTrue
Different steel grades like 304 and 430 have different densities, which must be accounted for in weight calculations.
Packaging weight is negligibleFalse
Packaging materials can add 50-200kg to the gross weight, which impacts shipping costs and must be considered.
How can you validate the accuracy of your coil weight calculation?
You have performed the calculation, but how can you be certain it's correct? Relying solely on your own math without a system of checks and balances can be a risky approach, potentially masking errors that only become apparent when it's too late.
To validate your coil weight calculation, you should first compare your result against the certified net weight provided on the supplier's Mill Test Certificate (MTC). The most definitive validation method is to physically weigh the coil on a properly calibrated industrial scale upon receipt.
Validation is not just a final check; it's a fundamental part of a robust quality assurance and procurement process. At MFY, we view this as a collaborative effort. We provide the certified data, but we also encourage our clients to understand the underlying calculations. This transparency builds trust and empowers them to manage their operations more effectively. For a manufacturing client, for example, validating the weight of incoming raw materials against the MTC and their own calculations allows them to immediately identify any discrepancies and adjust their inventory and production planning accordingly. It transforms the supplier-client relationship from a simple transaction into a partnership focused on precision and reliability. This proactive approach ensures there are no surprises, fostering a seamless flow from raw material receipt to finished product. This dual-pronged approach, combining documentation review with physical verification, is the hallmark of professional inventory management.
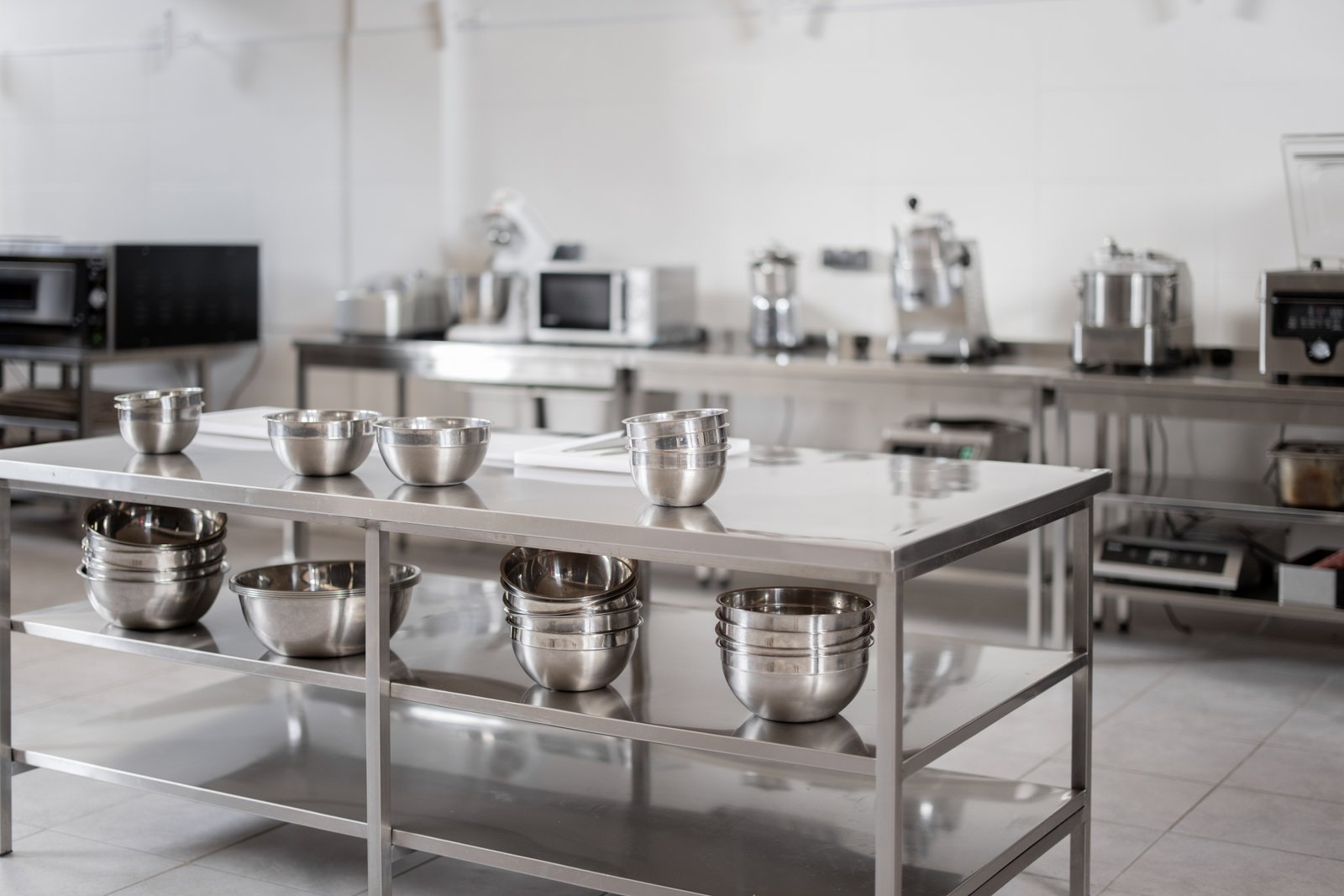
In any business process, what isn't measured cannot be managed. The same principle applies to steel procurement. Validating your coil weight calculation is the final and most crucial step in ensuring you have received exactly what you ordered and that your financial and material planning is sound. It’s a process of cross-referencing and verification that protects against errors, whether they originate from a miscalculation, a data entry mistake, or a supplier discrepancy. As a company committed to the entire stainless steel supply chain, MFY champions rigorous validation practices because they underpin the integrity and efficiency our clients depend on.
The Gold Standard: Weighing on a Calibrated Industrial Scale
The most reliable and indisputable method for validating a coil's weight is to weigh it physically. Most warehouses, ports, and manufacturing facilities are equipped with large, calibrated industrial scales (weighbridges or floor scales) for this purpose. When a shipment arrives, weighing a representative sample of coils (or all of them, depending on the application's criticality) provides a definitive "actual" weight.
This physical weight serves as the ultimate benchmark against which all other data—your calculation and the supplier's documents—should be compared. It is important to ensure the scale itself is properly calibrated and certified. An uncalibrated scale can be a source of error in itself. At MFY, every single coil that leaves our facility is weighed on a calibrated scale as part of our final quality control and logistics process. This certified weight is recorded and becomes part of the official shipping documentation, providing our clients with a reliable figure from the moment of dispatch.
I always recommend to our clients, especially those in the construction sector where material weight directly impacts structural integrity, that they make weighing coils upon receipt a standard operating procedure. This simple step provides peace of mind and an immediate, factual basis for inventory records.
Leveraging Supplier Documentation (MTC and Packing Lists)
Before the coil even arrives, you have a powerful validation tool in your hands: the supplier's documentation. The two key documents are the Packing List and the Mill Test Certificate (MTC). The Packing List provides logistical information, including the gross and net weight of each coil in the shipment. The MTC goes a step further by providing the certified net weight linked to the coil's specific heat number and chemical/physical properties.
The MTC is the supplier's formal certification of the product's quality and specifications. Comparing your calculated theoretical weight to the certified net weight on the MTC is the most important "paper" validation you can perform. The two numbers should be very close, typically within 1% of each other, with any small variance attributable to the slight difference between nominal and actual tolerances. If there is a significant discrepancy, it should be investigated immediately.
Here is a sample of how weight information might be presented on an MFY MTC, demonstrating the clarity we provide:
Certificate Section | Parameter | Value |
---|---|---|
Coil Identification | Coil No. | CHN-MFY-24-0811 |
Heat No. | H304L-9982A | |
Dimensions | Thickness | 1.20 mm |
Width | 1219 mm | |
Weight Information | Net Weight (kg) | 9,854 kg |
Gross Weight (kg) | 9,986 kg |
By cross-referencing your calculation with this document, you are validating your method against the manufacturer's certified measurement.
Cross-Referencing with Theoretical Weight Calculators
As a final sanity check, you can use online theoretical weight calculators, like the one we plan to host on our website, www.mfysteel.com. These digital tools provide a quick and easy way to run the numbers without performing the manual calculations. You simply input the dimensions and select the steel grade, and the tool provides an estimated weight.
However, it is critical to use these tools with a degree of professional skepticism. A public calculator will almost always use the standard nominal density for a given grade and will not account for specific manufacturing tolerances or the exact certified dimensions of your coil. Therefore, it should be used for quick estimates or to double-check the order of magnitude of your own calculation, not as the single source of truth.
The best practice is a three-tiered approach:
- Perform your own detailed calculation using the formulas discussed.
- Compare your result to the supplier's MTC for a certified paper trail.
- Physically weigh the coil upon receipt for ultimate real-world validation.
This comprehensive validation process eliminates uncertainty and ensures that the foundation of your project—your raw material—is precisely what you planned for.
MTC provides certified net weightTrue
The Mill Test Certificate contains the manufacturer's certified net weight measurement for each coil.
Online calculators are definitiveFalse
Online weight calculators should only be used for estimates, as they don't account for manufacturing tolerances.
Conclusion
Mastering the width × thickness formula is foundational, but true accuracy in coil weight calculation comes from considering material density, manufacturing tolerances, and consistent validation. This comprehensive approach empowers you to manage steel procurement with precision, control costs, and ensure your project's success from the start.
-
Understand the basic formula that helps estimate coil weight accurately ↩ ↩
-
Learn how density variations affect weight calculations in stainless steel grades ↩ ↩
-
Explore the geometric principles needed to understand coil weight calculation. ↩
-
Learn how inventory management utilizes coil weight calculation for efficiency. ↩
Have Questions or Need More Information?
Get in touch with us for personalized assistance and expert advice.