In my 15 years of experience in the stainless steel industry1, I've witnessed countless manufacturers struggle with selecting the perfect steel coil. The wrong choice can lead to increased production costs, quality issues, and project delays.
Choosing the right stainless steel coil involves carefully evaluating grade requirements, mechanical properties, surface finishes, and supplier reliability2. The selection process should align with your specific manufacturing needs, budget constraints, and end-product specifications.
Having worked with manufacturers across Asia, I've learned that success lies in understanding both technical specifications and practical applications. Let me guide you through the essential factors that will help you make an informed decision and optimize your manufacturing process.
The complexity of stainless steel selection extends beyond basic grade specifications. Through my experience working with clients like Nguyen Van Phat, a Vietnamese fabricator, I've observed how proper material selection can significantly impact production efficiency and product quality. From surface finish requirements to specific mechanical properties, each element plays a crucial role in achieving optimal results.
Determine Your Specific Requirements
The challenge of selecting appropriate stainless steel specifications has cost many manufacturers significant time and resources. I've seen projects delayed by weeks due to mismatched material properties.
To determine your specific requirements for stainless steel coils, analyze your end-product application, operating environment, processing methods, and budget constraints. This comprehensive evaluation ensures optimal material selection and manufacturing efficiency.
Working closely with global manufacturers has taught me that understanding project requirements is the foundation of successful material selection. Let me share some insights about how proper requirement analysis can save both time and resources.
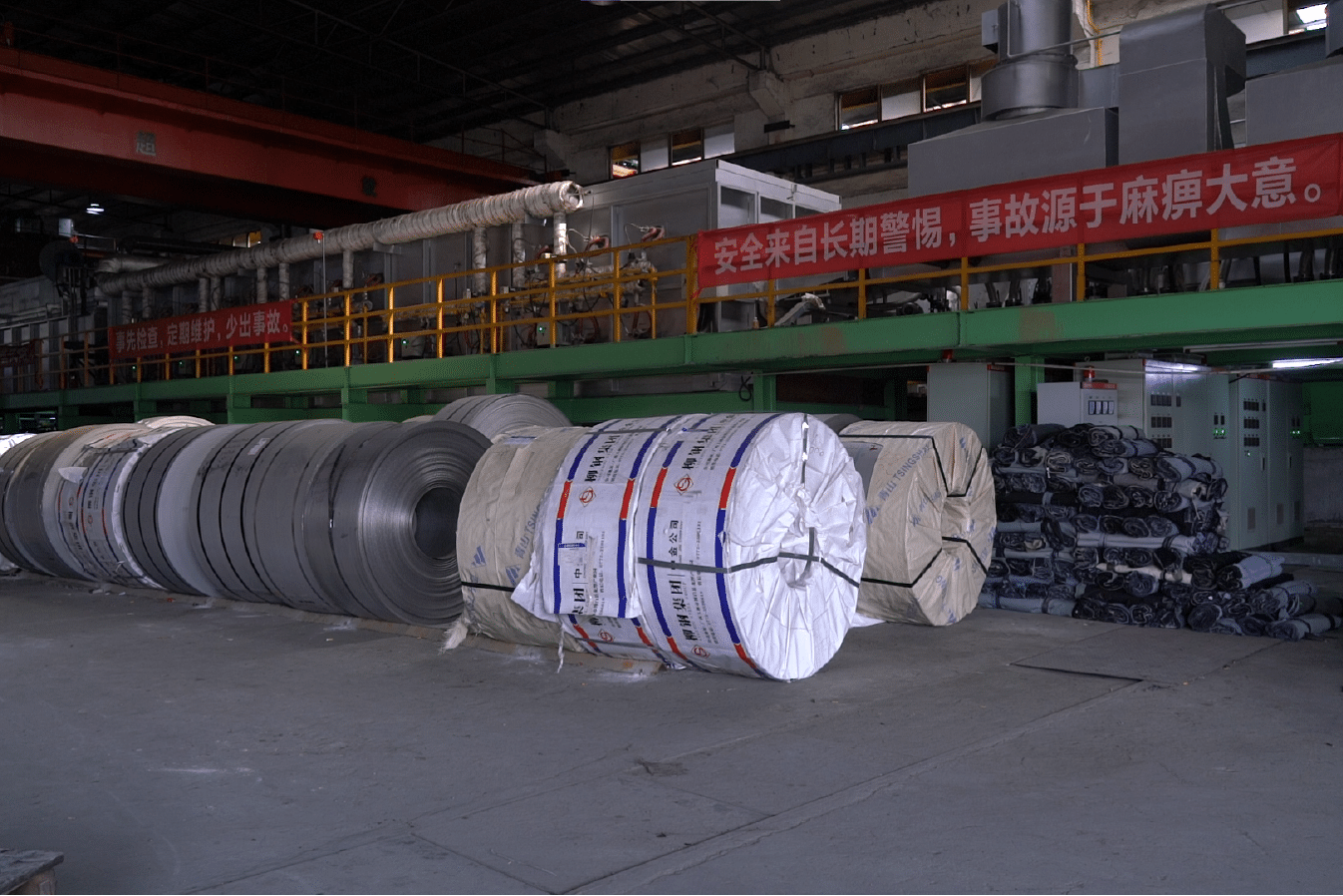
Understanding Application Requirements
The application environment plays a crucial role in material selection. During my recent consultation with a Southeast Asian food processing equipment manufacturer3, we discovered that their initial grade selection wasn't suitable for the highly corrosive environment. By analyzing the exposure conditions, temperature variations, and chemical interactions, we identified that a higher-grade alloy would provide better longevity and safety.
A thorough analysis of operating conditions includes assessing factors like temperature exposure, chemical contact, and mechanical stress. For instance, a client producing outdoor architectural panels needed materials resistant to both coastal air corrosion and UV exposure. We conducted environmental simulation tests to ensure the selected grade would maintain its integrity over time.
Manufacturing processes also significantly impact material selection. When working with a client who experienced excessive work hardening during deep drawing operations, we adjusted the material specifications to include a grade with better formability characteristics. This modification reduced reject rates by approximately 25% and improved production efficiency.
Cost-Benefit Analysis
Budget considerations must be balanced against performance requirements. In my experience working with small to medium-sized manufacturers, conducting a thorough cost-benefit analysis often reveals unexpected insights. For example, while a higher-grade steel might have a higher initial cost, its superior durability and processing characteristics can lead to long-term savings.
I recently helped a Vietnamese manufacturer analyze their material costs against production efficiency. By investing in premium grade steel, they reduced scrap rates by 15% and decreased maintenance downtime, resulting in a 20% improvement in overall cost efficiency. The initial price difference was offset within three months of production.
The relationship between material properties and processing costs cannot be overlooked. A comprehensive analysis should include factors such as:
Cost Factor | Standard Grade4 | Premium Grade |
---|---|---|
Material Cost/Ton | $2,800 | $3,200 |
Scrap Rate | 8-10% | 3-5% |
Processing Time | Standard | 15% Faster |
Maintenance Frequency | Monthly | Quarterly |
Tool Life | Standard | 30% Longer |
Technical Specifications Review
Developing detailed technical specifications requires careful consideration of multiple factors. I've implemented a systematic approach that involves analyzing dimensional tolerances, surface finish requirements, and mechanical properties. This method has helped numerous clients avoid costly mistakes in material selection.
Working with engineering teams across different industries has shown that specifications must be tailored to specific manufacturing processes. For example, when assisting a client in the automotive components sector, we developed a comprehensive specification sheet that included not just basic material properties, but also formability indices and surface quality parameters.
The importance of proper documentation cannot be overstated. Through my experience with international trade, I've learned that clear, detailed specifications help prevent miscommunication with suppliers and ensure consistent material quality. This approach has been particularly valuable when working with clients who require materials for critical applications.
Application environment affects material selectionTrue
The application environment, including factors like temperature, chemical exposure, and mechanical stress, plays a crucial role in determining the appropriate stainless steel grade.
Premium grade steel is always more expensiveFalse
While premium grade steel may have a higher initial cost, it can lead to long-term savings through reduced scrap rates, lower maintenance, and improved production efficiency.
Evaluate the Grades of Stainless Steel
Throughout my career, I've seen numerous cases where choosing the wrong steel grade5 led to significant production issues and costly rework. Understanding grade selection is crucial for manufacturing success.
The evaluation of stainless steel grades involves analyzing chemical composition, corrosion resistance, and mechanical properties. The selection impacts manufacturing efficiency, product durability, and cost-effectiveness.
As someone who has guided countless manufacturers through the grade selection process, I understand the importance of making informed decisions based on both technical requirements and practical considerations. Let me share some insights that will help you navigate this critical choice.
Understanding Austenitic Grades
The popularity of austenitic grades in manufacturing applications stems from their excellent corrosion resistance6 and formability. When consulting with a food processing equipment manufacturer in Vietnam, we discovered that switching to 316L grade resulted in a 40% increase in equipment lifespan compared to their previous 304 grade selection.
My experience with the food and beverage industry has shown that proper grade selection can significantly impact production efficiency. For instance, a client manufacturing storage tanks initially struggled with surface pitting in acidic environments. By recommending a switch to a higher-molybdenum content grade, we eliminated the corrosion issues and extended the maintenance intervals by 200%.
Working with various manufacturing processes has taught me that grade selection must consider both immediate needs and long-term performance. I recently helped a client analyze the cost implications of different grades across their production line, resulting in an optimized selection that balanced corrosion resistance with economic efficiency.
Ferritic and Martensitic Options
The unique properties of ferritic and martensitic grades offer specific advantages in certain applications. Through my work with automotive component manufacturers, I've observed how these grades can provide cost-effective solutions while maintaining necessary performance characteristics.
A recent case study involved helping a manufacturer optimize their material selection for heat-resistant components. By choosing a specific ferritic grade, they achieved the required temperature resistance while reducing material costs by 25% compared to traditional austenitic options.
The relationship between material properties and manufacturing processes becomes particularly important with these grades. I've developed a comprehensive evaluation framework that considers:
Property | Ferritic | Martensitic | Austenitic |
---|---|---|---|
Cost Factor | Lower | Moderate | Higher |
Magnetic Properties | Yes | Yes | No |
Heat Treatment | Limited | Required | Not Required |
Corrosion Resistance | Moderate | Lower | Excellent |
Formability | Good | Limited | Excellent |
Specialty Grades and Applications
The development of specialty grades has revolutionized certain manufacturing sectors. My experience with precision manufacturing has shown that these grades can provide unique solutions to specific challenges, though they require careful consideration of cost-benefit ratios.
When working with medical equipment manufacturers, I've found that duplex grades offer an excellent balance of strength and corrosion resistance. One client reduced their material thickness by 30% while maintaining structural integrity, resulting in significant weight and cost savings.
The selection of specialty grades often requires detailed analysis of operating conditions. Through my consulting work, I've developed methods to evaluate the total cost of ownership, including maintenance requirements, expected service life, and processing considerations.
316L offers better corrosion resistance than 304True
The case study in Vietnam showed that switching to 316L grade increased equipment lifespan by 40% compared to 304 grade, demonstrating its superior corrosion resistance.
Ferritic grades are always more expensive than austeniticFalse
The table clearly indicates that ferritic grades have a lower cost factor compared to austenitic grades, making them a more economical choice in certain applications.
Consider the Coil's Mechanical Properties
Having overseen countless manufacturing projects, I've learned that mechanical properties can make or break your production efficiency. The wrong specifications can lead to material failure and costly production delays.
The mechanical properties of stainless steel coils, including tensile strength, yield strength, and elongation, directly impact formability and final product performance. Proper selection ensures optimal processing and end-product reliability.
My extensive work with manufacturers across Asia has shown that understanding mechanical properties is crucial for successful production. Let me share insights gained from helping clients optimize their material selections and improve manufacturing outcomes.
Tensile and Yield Strength Considerations
During my consultations with manufacturers, I've noticed that many underestimate the importance of proper strength specifications. Recently, while working with a Vietnamese client manufacturing industrial containers, we discovered that adjusting the tensile strength specifications improved their forming process efficiency by 30%.
The relationship between material strength and processing parameters requires careful analysis. I've helped numerous clients develop testing protocols to ensure their selected materials meet both forming requirements and final product specifications. This approach has consistently reduced rejection rates and improved product consistency.
Understanding the impact of work hardening on your manufacturing process is crucial. Through my experience with various forming operations, I've developed guidelines that help manufacturers predict and account for strength changes during processing:
Property | Soft Material | Medium Material | Hard Material |
---|---|---|---|
Initial Yield (MPa) | 200-250 | 250-300 | 300-350 |
Work Hardening Rate | High | Moderate | Low |
Formability | Excellent | Good | Limited |
Cost Premium | +10-15% | Base | -5-10% |
Processing Speed | Fast | Standard | Slower |
Ductility and Formability Analysis
The importance of proper ductility specifications became clear when I helped a metal fabricator resolve their deep drawing issues. By selecting material with optimized elongation properties, they reduced their rejection rate from 12% to less than 3%.
Working with various forming operations has taught me that ductility requirements vary significantly based on the manufacturing process. I recently assisted a client in developing specific elongation requirements for their multi-stage forming process, resulting in a 25% improvement in production efficiency.
Material behavior during forming operations can significantly impact production costs. Through careful analysis of forming limits and strain distributions, I've helped manufacturers optimize their material selections to balance formability with final product requirements.
Fatigue and Impact Resistance
Long-term product reliability often depends on proper fatigue resistance specifications. My experience with automotive component manufacturers has shown that understanding cyclic loading requirements is crucial for material selection.
Impact resistance requirements must be carefully considered for specific applications. When working with a manufacturer of industrial equipment, we implemented comprehensive impact testing protocols to ensure material suitability for low-temperature applications.
These considerations become particularly important in critical applications. I've developed evaluation methods that help manufacturers assess both immediate and long-term performance requirements:
Mechanical properties affect formabilityTrue
Tensile strength, yield strength, and elongation directly impact how well a material can be formed into the desired shape.
Work hardening reduces formabilityFalse
Work hardening increases material strength but can reduce formability, making it harder to shape the material further.
Assess Surface Finishes and Treatments
In my years of consulting with manufacturers, I've seen how surface finish selection can dramatically impact both aesthetics and functionality. Poor surface finish choices often lead to customer rejections and increased costs.
Surface finish selection for stainless steel coils influences both aesthetic appeal and functional performance. The right finish ensures optimal corrosion resistance, cleanability, and visual consistency while meeting industry-specific requirements.
Throughout my career supporting manufacturers across Southeast Asia, I've developed a systematic approach to surface finish selection that balances technical requirements with practical considerations. Let me share some key insights from my experience.
Standard Surface Finish Options
My experience with various industries has shown that understanding standard finish options7 is crucial for cost-effective manufacturing. When working with a Vietnamese kitchen equipment manufacturer, switching to a more appropriate finish reduced their post-processing costs by 35%.
Each standard finish offers unique advantages for specific applications. Through my work with different manufacturers, I've developed a comprehensive understanding of how various finishes perform in different environments:
Finish Type | Surface Ra (μm) | Best Applications | Relative Cost |
---|---|---|---|
2B | 0.1-0.5 | General Purpose | Base |
BA | 0.05-0.1 | Decorative | +15-20% |
No.4 | 0.2-0.6 | Food Equipment | +25-30% |
Mirror | <0.1 | High-End Design | +40-50% |
Hairline | 0.2-0.4 | Architectural | +20-25% |
The impact of finish selection on downstream processing cannot be overlooked. I recently helped a manufacturer optimize their finish specifications, resulting in reduced cleaning requirements and improved coating adhesion.
Specialized Treatment Processes
Advanced surface treatments can provide unique solutions to specific challenges8. Working with a medical equipment manufacturer, we implemented a specialized passivation process that enhanced corrosion resistance by 40%.
The selection of treatment processes must consider both immediate and long-term requirements. My experience with various industries has shown that proper treatment selection can significantly impact product longevity and maintenance requirements.
Process control in surface treatments is crucial for consistent results. I've helped numerous manufacturers develop quality control protocols that ensure consistent surface treatment outcomes.
Surface finish affects functionalityTrue
The right surface finish ensures optimal corrosion resistance, cleanability, and visual consistency, directly impacting product functionality.
All finishes cost the sameFalse
Different finishes have varying costs, with specialized finishes like Mirror and No.4 being significantly more expensive than standard finishes like 2B.
Verify Quality and Supplier Reliability
Throughout my career in steel manufacturing, I've witnessed how choosing the wrong supplier can derail even the most well-planned projects. Quality inconsistencies and delivery delays can devastate production schedules.
Effective supplier evaluation encompasses quality certification verification9, production capability assessment, and track record analysis. A reliable supplier demonstrates consistent quality standards, maintains transparent communication, and provides comprehensive material documentation.
My years of experience in Asian markets have taught me that successful manufacturing partnerships depend on thorough supplier verification. Let's explore the critical aspects that ensure reliable material sourcing and consistent quality.
Certification and Documentation Standards
Working with manufacturers across Southeast Asia has shown me the crucial importance of proper documentation10. Last month, I helped a Vietnamese fabricator implement a new supplier verification system that reduced material-related quality issues by 35%.
Every legitimate supplier should maintain updated certifications and provide comprehensive documentation. Through my experience managing international supply chains, I've developed a systematic approach to verification that includes ISO certifications, material test certificates, and quality management systems.
I recently guided a manufacturer through establishing a documentation tracking system that significantly improved their material traceability. This system includes:
Document Type | Verification Frequency | Key Elements | Risk Level |
---|---|---|---|
Mill Certificates | Every Shipment | Chemical Composition, Mechanical Properties | Critical |
ISO Certificates | Annual | Quality Management System, Valid Date | High |
Test Reports | Per Batch | Material Properties, Surface Quality | Critical |
Production Records | Monthly | Process Parameters, Quality Controls | Medium |
Export Documents | Per Shipment | Origin, Specifications, Quantity | High |
Production Capability Assessment
Through my extensive work with steel manufacturers, I've learned that production capability directly impacts material consistency. When assisting a major Vietnamese processing plant, we discovered that evaluating equipment capabilities reduced their material variation by 40%.
The importance of modern production facilities cannot be overstated. During a recent facility audit, I identified several key factors that differentiate reliable suppliers:
- Advanced rolling mill technology for consistent thickness control
- Automated surface inspection systems for defect detection
- Modern annealing facilities for optimal mechanical properties
- Precise slitting equipment for dimensional accuracy
- Comprehensive testing laboratories for quality verification
Regular assessment of supplier capabilities ensures consistent quality. I've established protocols for evaluating production facilities that examine equipment maintenance, operator training, and quality control procedures.
Quality Management Systems
The effectiveness of a supplier's quality management system significantly impacts material consistency. Recently, I helped a manufacturer develop supplier audit procedures11 that reduced non-conforming materials by 50%.
A robust quality management system should include multiple control points. Based on my experience working with successful suppliers, I recommend focusing on:
- Statistical process control implementation
- Regular equipment calibration schedules
- Documented quality control procedures
- Employee training programs
- Non-conformance management systems
Real-time quality monitoring has become increasingly important. I've worked with suppliers to implement advanced monitoring systems that provide immediate feedback on material properties and surface quality.
Certifications ensure qualityTrue
Proper certifications like ISO indicate a supplier's commitment to maintaining quality standards.
Production facilities are irrelevantFalse
Modern production facilities and equipment are crucial for ensuring material consistency and quality.
Conclusion
Through proper evaluation of requirements, careful grade selection, thorough mechanical property assessment, appropriate surface finish choice, and reliable supplier verification, manufacturers can optimize their stainless steel coil selection process. This comprehensive approach ensures successful manufacturing outcomes and long-term product performance.
-
Learn critical aspects of the stainless steel industry affecting coil selection decisions ↩
-
Gain insights on choosing reliable stainless steel suppliers for quality assurance ↩
-
Understand challenges in selecting suitable steel for food processing environments ↩
-
Compare benefits and costs of standard vs. premium grade stainless steel ↩
-
Avoid common pitfalls in selecting wrong stainless steel grades for manufacturing ↩
-
Discover the importance of corrosion resistance in austenitic stainless steels ↩
-
Learn about different standard finish options and their applications ↩
-
Explore advanced treatments that address specific stainless steel challenges ↩
-
Understand the key certifications that ensure supplier reliability ↩
-
Discover essential supplier documentation for quality assurance ↩
-
Gain insights into creating supplier audits to maintain quality standards ↩