316 vs 304 Stainless Plate: Marine Strength Test
Choosing the right stainless steel for harsh marine environments can be a daunting task, often leading to costly premature failures or unnecessary over-specification. The relentless assault of saltwater, constant moisture, and chloride ions demands a material that can truly withstand the elements. Imagine confidently selecting the optimal stainless steel plate, ensuring longevity and performance for your marine application.
A marine strength test for 316 vs 304 stainless plates evaluates their comparative corrosion resistance, particularly against pitting and crevice corrosion induced by chlorides, and their ability to maintain mechanical integrity over time in saltwater environments, with 316 generally outperforming 304.
The decision between 304 and 316 stainless steel for marine use is pivotal, directly impacting the durability and safety of structures and equipment. As Global Business Director at MFY, I've seen countless projects where this choice was critical. This article will dissect their differences, explore their performance under marine conditions, and guide you in making an informed decision.
The maritime industry, with its unique and demanding operational conditions, has long relied on stainless steel for its blend of strength and corrosion resistance. However, not all stainless steels are created equal, especially when facing the relentless corrosive power of seawater. The selection process must go beyond generic specifications, delving into the nuances of alloy composition and real-world performance data. At MFY, supplying stainless steel plates to manufacturers of marine equipment and engineering contractors involved in coastal projects across India, Southeast Asia, and the Middle East, we emphasize the importance of understanding these distinctions. Industry studies, like those from NACE International1 (now AMPP), consistently highlight chloride-induced corrosion as a primary failure mechanism in marine environments. Our experience aligns with this, showing that while 304 might suffice in milder atmospheric marine conditions, 316, with its molybdenum content, offers a significant leap in protection for direct seawater contact or splash zones. This guide aims to provide clarity, drawing on established material science and MFY's practical insights.
What are the key differences between 316 and 304 stainless plates in terms of composition and properties?
Are you puzzled by why 316 stainless steel is often preferred over 304 in marine settings, despite their visual similarity? This confusion can lead to selecting a less-than-optimal material, risking corrosion and reduced service life. Understanding their fundamental makeup is key to demystifying this.
The primary difference is that 316 stainless steel contains molybdenum (typically 2-3%), which 304 lacks. This addition significantly enhances 316's corrosion resistance, especially against chlorides and pitting. Both are austenitic, with good formability, but 316 offers superior durability in aggressive environments.
The subtle yet significant variations in the chemical makeup of 304 and 316 stainless steel plates dictate their distinct performance characteristics, particularly when subjected to corrosive forces. While both grades belong to the austenitic family, renowned for their excellent formability and general corrosion resistance, the inclusion of molybdenum in 316 is a game-changer for more aggressive environments. As we at MFY advise our clients, from boat builders to offshore equipment manufacturers, this isn't just a minor elemental tweak; it translates into a tangible difference in longevity and reliability. For instance, a higher Pitting Resistance Equivalent Number (PREN) for 316 (typically ~24-26) compared to 304 (typically ~18-20) quantitatively demonstrates this enhanced resistance. This section will delve deeper into their elemental compositions, explore how these elements influence crucial properties like corrosion resistance, strength, and weldability, and explain why these differences are so critical when considering applications for MFY stainless steel plates in challenging conditions. Understanding these fundamentals will empower you to appreciate why one might be a more prudent investment over the other for specific scenarios.

The distinction between 304 and 316 stainless steel plates, while seemingly specific, is fundamental knowledge for anyone involved in material selection for durable applications. Both are stalwarts of the stainless steel world, part of the "18-8" family (approximately 18% chromium and 8% nickel for 304), but it's the addition of a crucial alloying element – molybdenum – that sets 316 apart and gives it an edge in more demanding corrosive environments. At MFY, we supply large quantities of both 304 and 316 stainless steel plates to diverse industries, including manufacturing companies that produce food processing equipment, chemical tanks, and, critically for this discussion, marine hardware. Our clients often consult us on which grade is more appropriate for their specific application, and the conversation almost invariably touches upon the environment the product will face. While 304 offers excellent corrosion resistance in many atmospheric conditions and against various chemicals, its Achilles' heel is its susceptibility to chloride-induced corrosion, such as pitting and crevice corrosion. This is where 316, fortified with molybdenum, steps in to offer a significantly more robust defense. The decision isn't always about choosing the "better" steel, but rather the "right" steel for the job, balancing performance requirements with economic considerations. Understanding their intrinsic differences in composition and the resulting properties is the first step towards making that optimal choice.
Elemental Composition: The Molybdenum Advantage in 316
The foundational difference between 304 and 316 stainless steel lies in their chemical composition, as defined by standards like ASTM A240/A240M, which covers chromium and chromium-nickel stainless steel plate, sheet, and strip for pressure vessels and for general applications. Both are austenitic stainless steels, meaning their primary crystal structure is face-centered cubic, which contributes to their excellent ductility and formability.
- Type 304 Stainless Steel: Typically contains 18-20% chromium and 8-10.5% nickel. It also has low carbon content (e.g., <0.08% for standard 304, <0.03% for 304L for improved weldability) along with manganese, silicon, phosphorus, and sulfur in small amounts. Chromium is the key element providing the basic corrosion resistance by forming a passive chromium-oxide layer on the surface.
- Type 316 Stainless Steel: Contains slightly less chromium (16-18%) but more nickel (10-14%) compared to 304. The crucial distinction is the intentional addition of 2-3% molybdenum. Like 304, it also has controlled levels of carbon (standard 316 and low-carbon 316L), manganese, silicon, etc.
The presence of molybdenum in 316 stainless steel is the primary reason for its enhanced corrosion resistance, particularly against pitting and crevice corrosion in chloride-containing environments (like seawater, de-icing salts, and certain industrial chemicals). Molybdenum helps to stabilize the passive layer, making it more robust and quicker to repair itself if damaged. It also promotes the formation of molybdenum-rich compounds that inhibit the initiation and propagation of pits. This "molybdenum advantage" is quantitatively reflected in the Pitting Resistance Equivalent Number (PREN), calculated as PREN = %Cr + 3.3 %Mo + 16 %N. For 304, with no molybdenum and typical nitrogen, PREN is around 18-20. For 316, with 2-3% Mo, PREN jumps to about 24-26 (or higher for 316L with higher nitrogen). A higher PREN generally indicates better pitting corrosion resistance. As a supplier, MFY always ensures our 316 plates meet the specified molybdenum content, as this is critical for our clients relying on its superior performance, for example, in marine exhaust systems or desalination plant components.
Comparative Mechanical Properties and Formability
In terms of typical mechanical properties at room temperature, 304 and 316 stainless steel plates are quite similar, though 316 often exhibits slightly higher tensile and yield strengths due to its molybdenum content and often slightly higher nickel. Both grades are non-magnetic in the annealed condition but can become slightly magnetic after cold working.
- Tensile Strength: For annealed 304, it's typically around 515 MPa (75 ksi), while for 316, it might be slightly higher, around 515-580 MPa (75-84 ksi).
- Yield Strength (0.2% offset): For 304, it's typically around 205 MPa (30 ksi), and for 316, it's often around 205-290 MPa (30-42 ksi).
- Elongation (ductility): Both grades exhibit excellent ductility, typically around 40% or higher, making them highly formable.
- Hardness: Both are relatively soft in the annealed condition, with Brinell hardness around 150-170.
The excellent ductility and formability of both 304 and 316 mean they can be readily bent, stamped, drawn, and roll-formed. This is a significant advantage for manufacturing companies using MFY plates to produce complex shapes for various applications, from tanks and vessels to intricate architectural elements. While 316 might be marginally stronger, the difference in formability for most common operations is not substantial enough to be a deciding factor between them. However, it's worth noting that both grades are prone to work hardening; as they are cold worked, their strength and hardness increase, while ductility decreases. This needs to be considered in multi-stage forming operations, where intermediate annealing might be required. From my experience at MFY, our clients involved in heavy forming operations appreciate the consistent properties of our annealed plates, which ensures predictable behavior in their presses and forming tools.
Weldability and Post-Weld Considerations
Both 304 and 316 stainless steels are generally considered to have good weldability by common fusion and resistance welding processes. However, a key consideration for both is the potential for sensitization, which can compromise corrosion resistance in the heat-affected zone (HAZ) adjacent to the weld. Sensitization occurs when chromium carbides precipitate at grain boundaries during heating in the range of about 425-875°C (800-1600°F), a temperature range experienced during welding. This depletes chromium from the regions adjacent to the grain boundaries, reducing their corrosion resistance and making them susceptible to intergranular corrosion.
To mitigate sensitization, low-carbon versions of these alloys, designated as 304L (≤0.03% Carbon) and 316L (≤0.03% Carbon), are widely used, especially for welded structures that will not be subsequently annealed. The lower carbon content significantly reduces the tendency for chromium carbide precipitation. MFY predominantly supplies 304L and 316L plates for applications involving welding, particularly to our engineering and construction contractor clients building tanks, piping systems, or structural frameworks. If standard carbon grades (304 or 316) are welded, a post-weld annealing treatment might be necessary to redissolve any precipitated carbides and restore full corrosion resistance, though this is often impractical for large fabrications. Using matching filler metals (e.g., ER308L for 304L, ER316L for 316L) is also standard practice. While the molybdenum in 316/316L doesn't significantly alter the fundamental welding behavior compared to 304/304L, the higher alloy content means that maintaining proper heat input and interpass temperature control can be even more critical to preserve its superior corrosion resistance in the welded condition.
Property/Element | Type 304 / 304L Stainless Steel | Type 316 / 316L Stainless Steel | Significance of Difference |
---|---|---|---|
Chromium (Cr) | ~18-20% | ~16-18% | Primary element for general corrosion resistance (passive layer). |
Nickel (Ni) | ~8-10.5% | ~10-14% | Stabilizes austenite, enhances formability and toughness. Slightly higher Ni in 316. |
Molybdenum (Mo) | Absent / Trace | ~2-3% | Key differentiator: Significantly improves resistance to pitting and crevice corrosion, especially in chloride environments. |
Carbon (C) | <0.08% (L: <0.03%) | <0.08% (L: <0.03%) | Low carbon ('L' grades) minimizes sensitization during welding. |
PREN (Typical) | ~18-20 | ~24-28 | Higher PREN for 316 indicates superior pitting resistance. |
Cost | Generally Lower | Generally Higher | Molybdenum and higher nickel content make 316 more expensive. |
Chloride Resistance | Moderate | Good to Excellent | 316 is much better suited for saltwater/chloride exposure. |
Typical Use Cases | Food equipment, architectural, general purpose | Marine hardware, chemical processing, medical implants | Reflects corrosion resistance differences. |
316 contains molybdenumTrue
316 stainless steel contains 2-3% molybdenum which significantly enhances its corrosion resistance, especially against chlorides.
304 is better for marine useFalse
316 is superior for marine applications due to its molybdenum content which provides better resistance to chloride-induced corrosion.
How does the marine environment affect the performance of 316 and 304 stainless plates?
You know 316 is often touted for marine use, but what exactly does the ocean do to stainless steel that makes this distinction so vital? Ignoring these effects can lead to rapid degradation and failure of components thought to be "stainless." Let's dive into the corrosive challenges.
The marine environment, rich in chloride ions from saltwater, accelerates corrosion in stainless steels. It primarily causes pitting and crevice corrosion, to which 304 is more susceptible. 316 stainless steel, with its molybdenum content, offers significantly better resistance to these localized attacks.
The aggressive nature of marine environments poses a formidable challenge to many materials, and stainless steels, despite their name, are not entirely immune. The combination of salinity (chlorides), constant moisture, oxygen, and sometimes pollutants or biological activity creates a highly corrosive cocktail. At MFY, when we discuss applications with clients like shipbuilders or coastal infrastructure developers in regions like Southeast Asia or the Middle East, understanding the specific exposure zone (e.g., atmospheric marine, splash zone, or full immersion) is critical. While both 304 and 316 stainless plates will eventually show signs of attack if misapplied, 304 is far more vulnerable to the localized corrosion mechanisms like pitting (formation of small holes) and crevice corrosion (corrosion in tight gaps or under deposits) that thrive in chloride-rich settings. The molybdenum in MFY's 316 plates provides a crucial defense, significantly slowing down these degradation processes and extending the service life of components. This section will explore the specific ways the marine environment attacks these steels and why 316 holds a distinct advantage2.
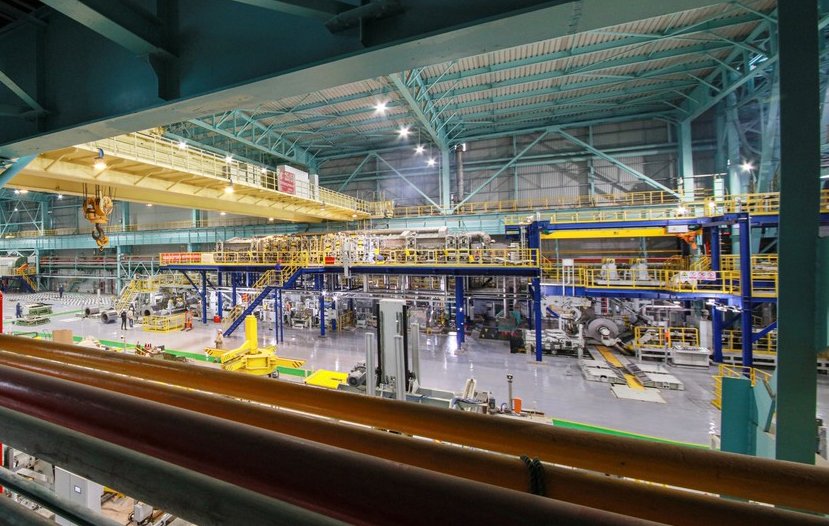
The allure of stainless steel in marine applications stems from its inherent resistance to general rusting, which plagues carbon steels. However, the marine environment is a complex and aggressive adversary, introducing specific corrosion mechanisms that can undermine even "stainless" materials if the wrong grade is chosen. At MFY, our experience supplying stainless steel plates for various marine-adjacent projects—from fittings on leisure boats to components in larger commercial vessels and coastal installations—has consistently demonstrated the critical importance of understanding these environmental impacts. It's not just about the visible saltwater spray; it's about the concentration of chloride ions, the presence of oxygen, temperature fluctuations, and even marine organisms that can influence corrosion rates and types. Factors like stagnant conditions, which can lead to crevice corrosion under washers or in unsealed joints, or the presence of surface deposits that can initiate pitting, are all part of the challenge. While 304 stainless steel might perform adequately in a mild atmospheric marine setting, far from direct spray, its limitations become starkly apparent when exposure becomes more severe. This is where the superior chemistry of 316 stainless steel, specifically its molybdenum content, provides the necessary resilience, a fact we always emphasize when guiding our clients in their material selection for MFY plates.
Chloride-Induced Pitting Corrosion
Pitting corrosion is a localized form of attack that results in the formation of small holes or "pits" in the metal surface. It is one of the most insidious forms of corrosion for stainless steels in chloride-containing environments like seawater because it can lead to failure with very little overall loss of material. The process typically initiates at microscopic imperfections on the surface or breaks in the passive chromium-oxide layer. Chloride ions are particularly aggressive in disrupting this passive layer and preventing its self-repair. Once a pit initiates, the local chemistry within the pit becomes even more aggressive (e.g., high chloride concentration, low pH), accelerating the corrosion process. Temperature also plays a significant role; higher temperatures generally increase the rate of pitting.
Type 304 stainless steel, lacking molybdenum, is significantly more susceptible to pitting corrosion in marine environments than Type 316. The PREN (Pitting Resistance Equivalent Number)3 value gives a good indication: 304 typically has a PREN around 18-20, while 316 boasts a PREN of 24-28 (or even higher for nitrogen-enhanced versions). This difference is primarily due to the 2-3% molybdenum in 316. Molybdenum enhances the stability and reparability of the passive film and makes it more resistant to breakdown by chlorides. I recall a case where an MFY client, a manufacturer of deck railings for small boats, initially used 304 stainless plates. In some coastal areas with warm, salty air and frequent spray, they started seeing visible pitting within a couple of years. Switching to MFY's 316L plates for the same application dramatically improved the longevity and appearance of their railings, much to their customers' satisfaction. Research data from sources like the Nickel Institute clearly shows significantly lower critical pitting temperatures (CPT) for 304 compared to 316 in chloride solutions, underscoring 316's superior resistance.
Crevice Corrosion in Marine Settings
Crevice corrosion is another localized form of corrosion that occurs in confined spaces or crevices where stagnant solutions can exist. Common sites for crevice corrosion on marine equipment include areas under washers, bolt heads, gaskets, lap joints, or beneath surface deposits like barnacles or sediment. Similar to pitting, the mechanism involves the depletion of oxygen within the crevice, leading to a breakdown of the passive film and an accumulation of aggressive species like chloride ions, along with a drop in pH. Once initiated, crevice corrosion can propagate rapidly, often remaining undetected until significant damage has occurred or leakage happens.
Both 304 and 316 stainless steels can be susceptible to crevice corrosion in seawater, but 316, again due to its molybdenum content, offers substantially better resistance. The geometry of the crevice (tightness and depth) and the aggressiveness of the environment (chloride concentration, temperature) are critical factors. In many marine applications, good design practices aim to eliminate or seal crevices. However, where crevices are unavoidable, selecting a more resistant alloy like 316 becomes crucial. For instance, MFY supplies 316L plates to manufacturers of through-hull fittings and seawater intake strainers. These components inherently have crevices and are fully immersed. Using 304 in such applications would be highly risky, with a high probability of failure due to crevice corrosion. Even with 316, careful design and assembly (e.g., using appropriate gasketing materials, ensuring smooth surfaces) are important to maximize performance. Some studies comparing crevice corrosion initiation times in seawater show 316 lasting many times longer than 304 before attack begins.
Uniform Corrosion and Galvanic Effects
While localized corrosion (pitting and crevice) is the primary concern for 304 and 316 stainless steels in marine environments, general or uniform corrosion (where the entire surface corrodes at a relatively uniform rate) is typically very low for both grades in seawater, especially when freely exposed and regularly washed by clean seawater. The passive film provides good protection against this form of attack. However, in highly polluted waters or under certain acidic conditions, even 316 might experience some uniform corrosion, though 304 would fare worse.
Another important consideration in marine environments is galvanic corrosion. This occurs when two dissimilar metals are electrically connected and immersed in a common electrolyte like seawater. The less noble (more active) metal will corrode preferentially to protect the more noble (less active) metal. Both 304 and 316 stainless steels are relatively noble. However, if they are coupled with a less noble metal like carbon steel, aluminum, or zinc in a marine structure, the less noble metal will corrode at an accelerated rate. Conversely, if stainless steel is coupled with a more noble metal like titanium or certain copper alloys, the stainless steel could become the anode and corrode faster than it would on its own, though this is less common. When using MFY stainless steel plates in mixed-metal assemblies for marine applications, it's crucial for designers to consider the galvanic series in seawater and implement appropriate insulation or cathodic protection measures if significant potential differences exist. The difference in galvanic behavior between 304 and 316 themselves is usually minor, but their interaction with other materials is key.
Corrosion Type | Susceptibility of 304 SS in Marine | Susceptibility of 316 SS in Marine | Key Influencing Factors | MFY's Recommendation Focus |
---|---|---|---|---|
Pitting Corrosion | High | Moderate to Low | Chloride concentration, temperature, surface condition | Molybdenum in 316 enhances passive film stability. |
Crevice Corrosion | High | Moderate | Crevice geometry, stagnant conditions, O2 depletion | 316 offers significantly better resistance in tight spaces. |
Uniform Corrosion | Low | Very Low | pH, pollution levels, general exposure | Generally not a primary concern for either if well-exposed. |
Stress Corrosion Cracking (SCC) | Moderate (esp. in warm chlorides) | Moderate (slightly better than 304) | Tensile stress, temperature (>60°C), chlorides | Both can be susceptible; Duplex SS often better. (Though SCC is less common for 304/316 in typical marine ambient temps than pitting/crevice) |
Galvanic Corrosion | Depends on coupled metal | Depends on coupled metal | Dissimilar metals, electrolyte conductivity | Proper material pairing and insulation. |
316 resists pitting better than 304True
316 stainless steel contains molybdenum which significantly improves its resistance to chloride-induced pitting corrosion compared to 304.
304 is suitable for full seawater immersionFalse
304 stainless steel lacks sufficient molybdenum content to withstand the aggressive pitting and crevice corrosion in full seawater immersion applications.
What have strength tests revealed about the durability of 316 vs 304 stainless plates in marine applications?
You've heard anecdotal evidence about 316's superiority, but what do actual "strength tests" in marine conditions really show about its endurance compared to 304? Without concrete data, choosing feels like a gamble, potentially leading to material failure or overspending. We need to look at test-backed evidence.
Marine "strength tests" (durability/corrosion tests) consistently show 316 stainless steel significantly outperforming 304 in resisting pitting, crevice corrosion, and overall degradation. This maintains 316's mechanical integrity and appearance far longer than 304 in saltwater exposure.
When we talk about "strength tests" in the context of marine applications for stainless steel, it's often less about traditional tensile or yield strength (which are inherent material properties not significantly altered by short-term marine exposure itself) and more about the material's durability and ability to retain its integrity and load-bearing capacity over extended periods in a corrosive environment. The real test is how well they resist corrosion that can lead to a loss of section, stress concentrations, and ultimately, a reduction in effective strength. At MFY, we rely on established industry data4 and practical field experience, which consistently demonstrate that 316 stainless steel plates maintain their structural and aesthetic qualities far better than 304 plates when subjected to the rigors of marine service. Numerous studies, including long-term exposure tests in various seawater locations, have quantified this difference, often measuring parameters like weight loss, pit depth, and the time to initiation of crevice corrosion. This section will synthesize these findings to provide a clearer picture of their comparative marine durability.
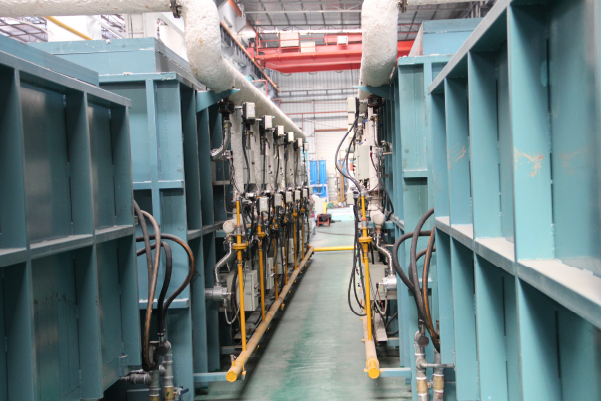
The term "strength test" in a marine context for stainless steel often encompasses a broader evaluation of durability, including resistance to corrosion mechanisms that can ultimately compromise mechanical integrity. While the inherent mechanical strengths (tensile, yield) of 304 and 316 stainless steel plates are well-defined and don't change simply by being near the ocean, their ability to maintain that strength over time in a corrosive marine environment is what truly matters. This is where corrosion resistance becomes a critical component of "marine strength." At MFY, we understand that our clients – whether they are engineering contractors building coastal infrastructure or manufacturing companies producing marine hardware – need materials that won't just be strong on day one, but will remain strong and reliable throughout their intended service life. This requires assessing how each grade withstands the relentless attack of chlorides, moisture, and marine growth. Long-term exposure tests, salt spray tests, and electrochemical tests conducted by research institutions and industry bodies provide valuable data on pitting rates, crevice corrosion propagation, and overall material degradation. These tests effectively simulate or accelerate the effects of marine exposure, offering insights into the long-term "strength" or endurance of these alloys.
Long-Term Seawater Exposure Tests
Numerous organizations and research institutions worldwide have conducted long-term exposure tests where samples of various materials, including 304 and 316 stainless steel, are immersed in natural seawater or exposed in marine atmospheric zones for extended periods (months to many years). These tests provide invaluable real-world performance data. Consistently, such studies reveal that 304 stainless steel exhibits significant pitting and crevice corrosion, especially in full immersion or splash zone conditions. For example, data published by organizations like the Nickel Institute or in corrosion journals often show 304 samples developing deep pits and severe crevice attack within a year or two, particularly in warmer waters. In contrast, 316 stainless steel samples under the same conditions typically show much better performance, with significantly less pitting, shallower pits if any, and a greater resistance to crevice corrosion initiation and propagation.
I recall a detailed study MFY reviewed when advising a client in the Middle East who was designing components for a seawater intake system. The study compared various stainless steels exposed for 5 years in the Arabian Gulf, known for its high salinity and temperature. The 304 samples were heavily pitted and showed extensive crevice corrosion, rendering them unsuitable. The 316L samples, while not entirely immune (some minor staining or very shallow pitting in aggressive crevices), were in vastly better condition and deemed acceptable for many components, though for critical parts, even higher alloys like duplex stainless steels were considered. This practical field data, which aligns with controlled laboratory findings, underscores the superior "marine strength" (i.e., durability) of 316 derived from its molybdenum content. The "strength" here is less about initial psi and more about resistance to section loss and structural weakening due to corrosion.
Accelerated Corrosion Testing (e.g., Salt Spray Tests)
While long-term exposure tests provide the most realistic performance data, they are time-consuming. Accelerated corrosion tests, such as the salt spray (or salt fog) test (e.g., ASTM B117), are widely used to quickly compare the relative corrosion resistance of different materials or coatings. In a salt spray test, samples are exposed to a dense fog of heated saltwater solution in a controlled chamber for a specified duration (e.g., hundreds or thousands of hours). While the correlation between salt spray test results and actual in-service marine performance can be debatable and depends on the specific material and application, these tests are useful for qualitative comparisons.
When 304 and 316 stainless steel plates are subjected to ASTM B117 salt spray testing, 316 consistently outperforms 304. After a few hundred hours, 304 samples often show signs of rust staining (from minor pitting initiation) and more evident corrosion, especially if any crevices are present. In contrast, 316 samples typically remain free of significant corrosion for much longer durations, often exhibiting only minor staining even after extended exposure periods where 304 has failed. For example, MFY has seen comparative test data where 304 might show notable rust spots after 200-300 hours, while 316 could go 800-1000 hours or more with minimal change. This accelerated testing, while not a perfect predictor of service life, clearly demonstrates 316's enhanced ability5 to withstand chloride attack, which contributes to its long-term "strength" by preserving the material's surface and structural integrity.
Impact of Corrosion on Mechanical Integrity
The "strength" of a stainless steel component in a marine application isn't just about its initial tensile or yield strength; it's about how corrosion affects these properties over time. Localized corrosion, such as pitting, can create stress concentration points. A deep pit in a plate under tensile load can act like a notch, significantly reducing the plate's fatigue life or its ability to withstand impact loads. Crevice corrosion can lead to a significant loss of cross-sectional area in critical locations like bolted joints, directly reducing the load-bearing capacity of the connection. While general uniform corrosion rates for both 304 and 316 are low in seawater, the localized attack in 304 can be severe enough to compromise structural integrity much sooner than in 316.
Consider a bolted connection using stainless steel plates in a marine structure. If 304 plates are used, crevice corrosion can occur under the bolt head and between the faying surfaces. This corrosion can reduce the effective thickness of the plate in that critical load-transfer area. If significant section loss occurs, the joint's capacity to carry shear or tensile loads is diminished, potentially leading to failure even if the uncorroded portions of the plate retain their original mechanical properties. MFY's 316L plates, with their superior resistance to crevice corrosion, would maintain their cross-sectional area and thus their load-bearing capacity for a much longer period in the same application. This preservation of mechanical integrity due to better corrosion resistance is the essence of 316's superior "marine strength." Therefore, when evaluating "strength tests," it's crucial to consider not just the pristine material properties but the degradation of these properties due to the specific corrosion mechanisms prevalent in the marine environment.
Test Type / Parameter | Observation for 304 SS | Observation for 316 SS | Implication for "Marine Strength" / Durability |
---|---|---|---|
Long-Term Immersion (Natural Seawater) | Significant pitting, crevice corrosion within 1-3 years. | Minimal to moderate pitting/crevice corrosion, much slower onset. | 316 maintains structural integrity much longer. |
Marine Atmospheric Exposure | Rust staining, shallow pitting in moderate/severe zones. | Generally good, minor staining in severe zones. | 316 offers better aesthetic and surface durability. |
ASTM B117 Salt Spray Test | Rusting/pitting often within 200-500 hours. | Significantly longer resistance, often >800-1000 hours. | Demonstrates 316's superior resistance to chloride attack. |
Critical Pitting Temp. (CPT) in Chloride Soln. | Lower CPT (e.g., 15-25°C in 1M NaCl) | Higher CPT (e.g., 25-35°C in 1M NaCl) | 316 resists pit initiation at higher temperatures/chloride levels. |
Crevice Corrosion Resistance (Electrochemical Tests) | Lower critical crevice temperature (CCT), faster propagation. | Higher CCT, slower propagation. | 316 is more robust against corrosion in confined spaces. |
Effect on Mechanical Integrity (Post-Exposure) | Potential for significant section loss, stress risers from pits. | Much less section loss, fewer/shallower stress risers. | 316 retains its load-bearing capacity better over time. |
316 outperforms 304 in marine testsTrue
Multiple long-term exposure and accelerated tests consistently show 316's superior resistance to pitting and crevice corrosion in marine environments.
304 and 316 have equal marine durabilityFalse
316's molybdenum content gives it significantly better corrosion resistance in chloride-rich marine environments compared to 304.
What are the recommended applications for 316 and 304 stainless plates in marine environments?
Knowing that 316 generally fares better, where can 304 still be responsibly used in marine settings, if at all, and where is 316 non-negotiable? Making the wrong choice can lead to premature failure and safety hazards, or conversely, unnecessary expenditure. Clear application guidelines are needed.
316 stainless steel plates are recommended for direct saltwater contact: boat fittings, hulls, propellers, offshore structures. 304 may be suitable for milder atmospheric marine applications with less direct spray or chloride exposure, like some indoor or sheltered components.
The suitability of 304 versus 316 stainless steel plates in marine environments hinges on the specific nature and severity of the exposure. As a rule of thumb, which we at MFY consistently communicate to our clients, if the component will experience direct and frequent contact with seawater (immersion, splash zone), or be subjected to significant salt spray in a warm climate, 316 (or 316L for welded parts) is the strongly preferred, often essential, choice. For these scenarios, using 304 would be courting premature failure due to pitting and crevice corrosion. However, there can be niche applications in a broader "marine environment" – perhaps components used indoors on a ship, or architectural elements in a coastal building that are well-sheltered and regularly washed by freshwater – where 304 might offer adequate performance at a lower cost. This section will provide more detailed application recommendations, drawing upon MFY’s experience supplying stainless steel plates to various manufacturing companies and engineering contractors in the marine sector.
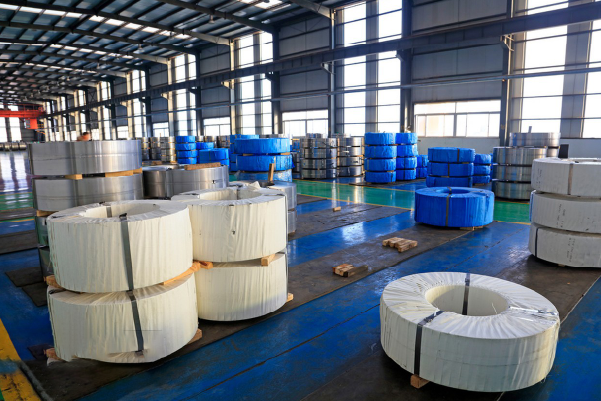
Choosing the correct grade of stainless steel for a specific marine application is a critical engineering decision that balances performance, longevity, safety, and cost. At MFY, our role as a supplier of both 304 and 316 stainless steel plates to a wide range of clients, including those in the marine and coastal construction industries across India, Southeast Asia, and the Middle East, means we often engage in discussions about optimal material selection. The "marine environment" is not monolithic; it encompasses a spectrum of conditions, from aggressive full seawater immersion and splash zones to milder atmospheric marine exposures further from the water's edge or in sheltered locations. Generally, the more direct and persistent the contact with chloride-rich seawater, and the higher the temperature, the stronger the case for 316 stainless steel. Conversely, for applications with only indirect or mild marine influence, 304 might be considered, but always with careful evaluation of the specific service conditions and expected lifespan. The cost difference between 304 and 316 (with 316 being more expensive due to its molybdenum and higher nickel content) often tempts users to specify 304, but this can be a false economy if it leads to premature replacement or failure.
Applications Where 316 Stainless Steel is Essential
For any application involving direct, prolonged contact with seawater or heavy salt spray, 316 (or preferably 316L for welded components) stainless steel plate is the standard recommendation and often a minimum requirement. Its superior resistance to pitting and crevice corrosion, endowed by its molybdenum content, is critical in these aggressive conditions. Examples of such applications where MFY regularly supplies 316/316L plates include:
- Boat and Ship Hardware: Deck fittings (cleats, chocks, railings, stanchions), anchor chains and components, rudder stocks, propeller shafts, exhaust fittings, through-hull fittings, and seawater piping systems.
- Offshore Oil and Gas Structures: Cladding for splash zones, piping for seawater cooling, cable trays, and various equipment housings.
- Desalination Plants: Components in contact with brine or seawater, such as pumps, valves, piping, and vessel internals.
- Coastal and Marine Infrastructure: Handrails, ladders, fasteners, and structural supports in piers, docks, and bridges exposed to direct saltwater splash or immersion.
- Aquaculture Equipment: Cages, pens, and support structures used in marine fish farming.
I recall an MFY client, an engineering contractor in India, who was building a new jetty. They initially considered 304 for handrails to save costs but, after discussing the direct splash zone exposure and our recommendations based on similar projects, they wisely opted for MFY's 316L plates, ensuring much longer service life and lower maintenance. The slightly higher initial investment in 316L is almost always offset by its extended durability and reduced risk of failure in these critical applications.
Limited and Cautious Use Cases for 304 Stainless Steel in Marine Settings
While 316 is the workhorse for direct marine exposure, there are situations within a broader marine context where 304 stainless steel plate6 might be considered, albeit with caution and careful assessment. These are typically applications where chloride exposure is significantly less severe:
- Atmospheric Marine (Mild Zones): Components located further from the shoreline, with less direct salt spray, and in regions with lower ambient temperatures and humidity might see acceptable performance from 304. Regular freshwater washing to remove salt deposits can also help.
- Indoor Marine Applications: Interior fittings on ships or boats that are not exposed to bilge water or direct seawater, such as galley equipment (sinks, countertops, if not heavily exposed to salt), decorative paneling, or some cabin hardware, might use 304.
- Sheltered Architectural Use in Coastal Areas: Cladding or trim on buildings in coastal towns that are well-sheltered from direct sea spray and are designed to allow for good drainage and regular cleaning.
However, even in these seemingly milder applications, factors like proximity to breaking surf, prevailing wind direction, local pollution levels, and design details (e.g., presence of crevices) must be carefully evaluated. MFY has supplied 304 plates for some coastal architectural projects where the design incorporated frequent freshwater washing schedules. But it's crucial to understand that 304's margin of safety in any chloride-containing environment is much lower than 316's. A common mistake is to underestimate the corrosivity of an "atmospheric marine" environment, especially in warm, humid climates where salt can travel further inland and remain on surfaces longer. Using 304 for outdoor railings even a few hundred meters from the sea in such climates can still lead to tea staining (superficial rust staining) and pitting over time.
Factors Influencing the Choice: Beyond Just the Alloy
The decision between 304 and 316 for a marine application isn't solely based on the alloy itself. Several other factors play a crucial role and should be considered by manufacturers and contractors:
- Design Details: The presence of crevices, areas that trap moisture, or rough surface finishes can accelerate corrosion even in a more resistant alloy. Good design aims to minimize these features.
- Surface Finish: A smoother, more polished surface (e.g., a 2B or BA finish from MFY) is generally more resistant to corrosion initiation than a rougher surface, as it offers fewer sites for chlorides to accumulate and for pits to start.
- Welding Practices: As discussed, using low-carbon "L" grades (304L, 316L) is vital for welded structures to prevent sensitization. Proper welding procedures and post-weld cleaning (e.g., removal of weld scale and heat tint) are also essential to maintain corrosion resistance.
- Maintenance and Cleaning: Regular freshwater washing to remove accumulated salt deposits can significantly extend the life of both 304 and 316 stainless steel in marine environments, though it's more critical for 304.
- Expected Service Life and Cost: While 316 has a higher upfront cost, its longer service life and lower maintenance requirements in aggressive marine environments often result in a lower total life-cycle cost compared to 304, which might require premature replacement or more frequent repairs. This is a key discussion point MFY has with clients like equipment integrators who need to guarantee long-term performance.
Ultimately, if there is any doubt about the severity of the marine exposure or if the application is critical for safety or long-term performance, opting for 316L stainless steel plate is the more prudent and reliable choice.
Application Category | Typical Exposure Level | Recommended SS Grade | MFY Example Product / Client Type | Justification |
---|---|---|---|---|
Direct Seawater Immersion | Severe | 316 / 316L | MFY 316L plates for ship hulls, seawater intake pipes (Eng. Contractor) | Highest chloride concentration, constant wetness; requires max pitting/crevice resistance. |
Splash Zone / Heavy Spray | Severe | 316 / 316L | MFY 316L plates for pier pilings, boat deck fittings (Manufacturing Co.) | Intermittent wetting and drying can concentrate chlorides. |
Marine Atmospheric (Coastal) | Moderate to Severe | 316 / 316L (preferred); 304 (cautious, with cleaning) | MFY 316L for coastal railings; 304 for sheltered, washed architectural trim (Distributor to builders) | Airborne salt; 304 may tea-stain or pit without diligent maintenance. |
Indoor Marine (Sheltered) | Mild to Moderate | 304 / 304L (often acceptable); 316L (for high humidity/condensation areas) | MFY 304 plates for ship interior galley (non-contact areas) (Equipment Integrator) | Lower direct chloride, but condensation can still be an issue. |
Fasteners in Marine Use | Varies (often Severe) | 316 / 316L (or higher alloys) | (MFY supplies plate, not fasteners directly, but advises users) | Crevices are inherent; high integrity needed. 304 fasteners often fail. |
316 is essential for direct seawater contactTrue
316 stainless steel's molybdenum content provides critical resistance to pitting and crevice corrosion in aggressive marine environments.
304 can replace 316 in all marine applicationsFalse
304 lacks sufficient chloride resistance for direct seawater exposure and should only be considered for mild, sheltered marine applications with proper maintenance.
How can manufacturers optimize the use of 316 and 304 stainless plates for marine applications?
Even after selecting a grade, how can manufacturers ensure they're getting the most out of their 316 or 304 stainless plates in marine designs? Suboptimal fabrication or design can compromise even the best material, leading to unexpected failures. Best practices are needed for optimization.
Optimize by: selecting 316L stainless steel for welded marine parts; ensuring smooth surface finishes; designing to avoid crevices and allow drainage; proper welding/post-weld cleaning; and considering regular freshwater washing, especially for 304 if used in milder marine atmospheric conditions.
Maximizing the performance and lifespan of stainless steel plates in marine applications goes beyond merely selecting the correct alloy grade; it involves a holistic approach encompassing design, fabrication, and maintenance. At MFY, we understand that our clients, whether they are large-scale engineering contractors or specialized manufacturing companies, need to translate the inherent properties of our 316 or 304 stainless steel plates into durable and reliable end-products. This means paying close attention to details that can significantly influence corrosion resistance. For instance, even the superior 316L can underperform if poor welding practices introduce sensitization or if designs create deep, unavoidable crevices where corrosive agents can concentrate. Similarly, if 304 is judiciously chosen for a very mild marine atmospheric application, its performance can be enhanced by specific design and maintenance protocols. This section will explore practical strategies that manufacturers can employ to optimize the use of MFY stainless steel plates, ensuring they achieve the best possible outcomes in the challenging marine environment.
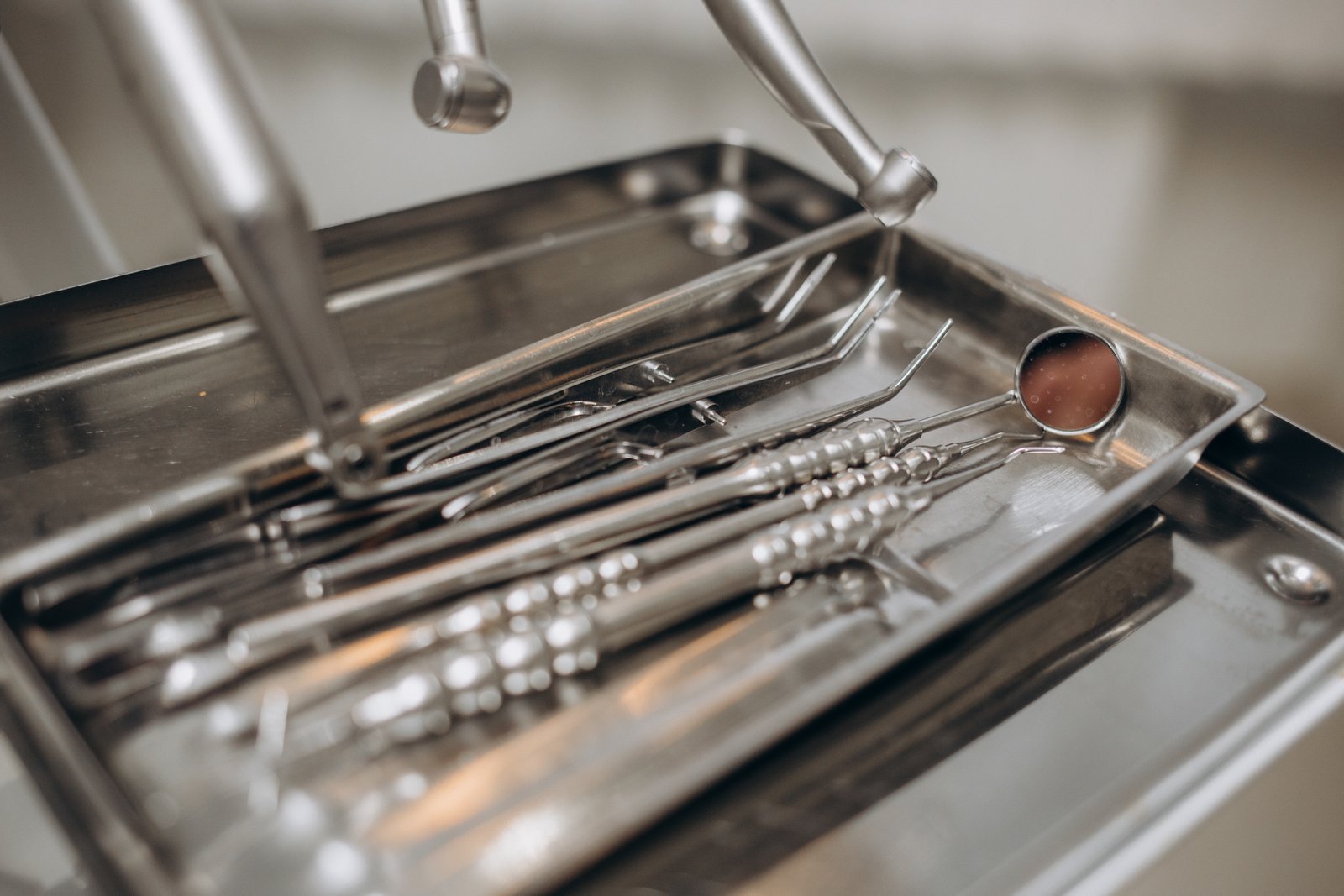
Optimizing the use of 304 and 316 stainless steel plates7 in marine environments is about leveraging their strengths while mitigating their weaknesses through intelligent design, careful fabrication, and appropriate maintenance. As a key supplier in the stainless steel industry, MFY is committed to helping our clients achieve this. It’s not enough to simply choose 316L for a demanding application; how that 316L plate is cut, formed, welded, and finished will significantly impact its real-world performance. For example, a rough surface finish can trap more chloride ions and act as initiation sites for pitting. Similarly, a design that allows water to pool or creates tight, unsealed crevices can turn even a moderately corrosive environment into a highly aggressive one locally. For the limited cases where 304 might be considered in a marine context, these optimization strategies become even more critical to eke out acceptable service life. Our most successful clients, from equipment integrators to construction firms, understand that material selection is just the first step; excellence in execution is what truly unlocks the potential of MFY’s stainless steel products, especially when facing the sea.
Design Best Practices for Marine Durability
Good design is the first line of defense in optimizing stainless steel performance in marine environments. The primary goal is to minimize conditions that promote localized corrosion.
- Avoid Crevices or Seal Them: Design joints and connections to eliminate tight gaps where seawater can become stagnant. If crevices are unavoidable (e.g., in bolted connections), they should be sealed with appropriate flexible sealants or gaskets (e.g., neoprene, PTFE) to prevent ingress of moisture and chlorides. Using continuous welds instead of intermittent welds or rivets can also eliminate crevices.
- Ensure Good Drainage: Design structures and components so that water can easily drain away. Avoid flat surfaces where water can pool, as this can lead to deposit formation and concentrated corrosion attack. Sloping surfaces and providing weep holes can be beneficial.
- Specify Smooth Surface Finishes: A smoother surface finish (e.g., MFY’s 2B or a polished finish) is generally more resistant to corrosion initiation than a rougher finish (like a No. 1 or HRAP finish). Rough surfaces have more sites for chloride accumulation and can be harder to clean. For critical applications, electropolishing can further enhance corrosion resistance by creating a very smooth, chromium-enriched passive layer.
- Consider Galvanic Compatibility: When stainless steel (304 or 316) must be used in contact with other metals, carefully consider their relative positions in the galvanic series for seawater. If a significantly less noble metal is present (e.g., carbon steel, aluminum), it will corrode preferentially. If unavoidable, use insulating gaskets and washers to break the electrical circuit or provide cathodic protection to the less noble material. MFY often advises clients on material compatibility when they are integrating our stainless plates into larger, mixed-material assemblies.
Fabrication and Welding Excellence
The way stainless steel plates are fabricated and welded has a profound impact on their corrosion resistance in marine service.
- Use Low-Carbon "L" Grades for Welding: As repeatedly emphasized, for any welded components intended for marine environments, 304L or 316L stainless steel plates from MFY should be specified. The low carbon content (<0.03%) minimizes the risk of sensitization and subsequent intergranular corrosion in the heat-affected zone (HAZ) of welds.
- Proper Welding Procedures: Use appropriate filler metals (e.g., ER308L for 304L, ER316L for 316L). Control heat input during welding to minimize distortion and reduce the time spent in the sensitization temperature range. Ensure good weld penetration and avoid defects like undercut or porosity, which can act as corrosion initiation sites.
- Post-Weld Cleaning is Crucial: After welding, all weld scale (oxide layer), heat tint (discoloration), and spatter must be thoroughly removed. These surface contaminants can disrupt the passive layer and significantly reduce corrosion resistance. Methods include grinding, brushing (with stainless steel brushes only, to avoid iron contamination), pickling (using acid pastes or solutions), or electropolishing. A clean, properly passivated weld area is essential for long-term performance. I've seen MFY clients who invest in meticulous post-weld cleaning achieve noticeably better corrosion resistance from their 316L fabrications compared to those who skimp on this step.
- Avoid Iron Contamination: During fabrication (cutting, grinding, handling), ensure that tools used for carbon steel are not used on stainless steel, as this can transfer iron particles to the stainless surface, leading to rust spots and localized corrosion. Dedicated tools or thorough cleaning of tools is necessary.
Maintenance Strategies for Extended Service Life
Even with the best design, fabrication, and material selection (like MFY's 316L plates), some level of maintenance can further optimize performance and extend the service life of stainless steel in marine environments.
- Regular Freshwater Washing: One of the simplest yet most effective maintenance practices is regular washing with fresh water. This helps to remove accumulated salt deposits, chlorides, and other contaminants from the surface, reducing the risk of pitting and crevice corrosion. The frequency of washing depends on the severity of the exposure; components in heavy splash zones might benefit from daily or weekly washing, while those in milder atmospheric marine conditions might need it less often. This is particularly important if 304 has been used in a borderline application.
- Inspection and Cleaning of Crevices: Periodically inspect areas prone to crevice corrosion (e.g., under bolt heads, in lap joints if not fully sealed) and clean them if accessible.
- Prompt Repair of Damage: If the passive layer is damaged (e.g., by scratches or impact), it will naturally self-repair in the presence of oxygen. However, if damage is severe or if corrosion has initiated, prompt cleaning and repair (e.g., local passivation treatment if needed) can prevent further degradation.
- Consider Protective Coatings in Extreme Cases or for Aesthetics: While stainless steel is chosen for its inherent corrosion resistance, in extremely aggressive environments or for specific aesthetic requirements (e.g., colored finishes), specialized coatings can be applied. However, this is less common for general marine use of 304/316.
By implementing these optimization strategies, manufacturers can significantly enhance the durability and reliability of structures and equipment made from MFY’s 304 and 316 stainless steel plates, ensuring they deliver optimal performance even in the demanding conditions of the marine world.
Optimization Area | Strategy for 304 SS (Limited Marine Use) | Strategy for 316 SS (Preferred Marine Use) | MFY Product/Service Link |
---|---|---|---|
Material Selection | Use only in very mild atmospheric marine, sheltered, regularly washed. | Specify 316L for all welded parts in direct marine contact. | MFY supplies certified 304L and 316L plates. |
Design | Maximize drainage, avoid all crevices, ensure easy cleaning access. | Design to minimize crevices (seal if unavoidable), ensure good drainage. | MFY can advise on finishes (e.g., 2B) aiding cleanability. |
Surface Finish | Opt for smooth finishes (e.g., 2B), consider passivation. | Smooth finishes (2B, BA, polished) enhance resistance; electropolish for critical. | MFY offers various surface finishes. |
Fabrication & Welding | Strict avoidance of carbon steel contamination, thorough post-weld cleaning if welded (use 304L). | Use 316L filler, proper heat control, meticulous post-weld cleaning (pickling/passivation). | MFY emphasizes importance of L-grades for weld integrity. |
Maintenance | Frequent freshwater washing is critical. Inspect regularly. | Regular freshwater washing beneficial, inspect critical areas. | MFY products, when maintained, offer long service life. |
Cost Consideration | Lower initial cost but potentially higher life-cycle cost if misapplied. | Higher initial cost but generally lower life-cycle cost in marine. | MFY provides competitive pricing for both grades. |
316L is better for welded marine partsTrue
316L's low carbon content minimizes sensitization risk during welding, making it superior to standard 316 for marine applications.
304 requires no maintenance in marine useFalse
Even in mild marine conditions, 304 stainless steel requires regular freshwater washing and inspection to maintain performance.
Conclusion
Choosing between 316 and 304 stainless plate for marine use hinges on exposure: 316 excels in direct saltwater contact due to molybdenum, offering superior corrosion resistance. MFY provides both, guiding optimal selection for lasting marine strength and project success globally.
-
Discover insights on marine corrosion from a leading industry group ↩
-
Learn about the superior corrosion resistance of 316 steel ↩
-
Understand PREN and its impact on material selection ↩
-
Industry data ensures reliability and accuracy when assessing materials for specific applications. ↩
-
Understanding the mechanism behind 316's resistance aids in making informed material choice decisions. ↩
-
Discover specific marine situations where 304 stainless steel can be appropriate. ↩
-
Discover why 316 stainless steel is ideal for marine usage due to its corrosion resistance. ↩
Have Questions or Need More Information?
Get in touch with us for personalized assistance and expert advice.