2205 Plate vs 316L: Salt-Spray Corrosion Test
Choosing the wrong stainless steel for a corrosive environment can lead to premature failure, costly replacements, and significant safety risks. Imagine your critical equipment showing rust far sooner than expected, causing operational downtime and staggering repair costs. Understanding the corrosion resistance of grades like 2205 and 316L through standardized salt-spray testing1 is key to making a secure, cost-effective decision.
Duplex 2205 stainless steel outperforms 316L in salt-spray corrosion tests due to its higher chromium, molybdenum, and nitrogen content. This superior resistance makes it ideal for highly corrosive environments where 316L might falter, offering enhanced longevity and reliability for critical industrial applications.
For years, I've guided clients through the complex maze of material selection. The choice between a trusted workhorse like 316L and a high-performance grade like Duplex 2205 isn't just about comparing spec sheets; it's about forecasting the future performance of a critical asset. This decision hinges on understanding not just the initial cost, but the total cost of ownership over decades of service. Let’s dive into what these corrosion tests really tell us.
The global cost of corrosion is estimated to be over $2.5 trillion annually, according to NACE International2. This isn't just a financial drain; it represents a massive challenge in engineering, safety, and sustainability. In my role at MFY, I’ve seen firsthand how a strategic material choice can be the deciding factor between a project’s success and its early demise. It’s a battle fought at the microscopic level—between chloride ions and a steel’s passive layer. The salt-spray test3 is our laboratory battlefield, a controlled environment where we accelerate this conflict to predict the winner. This test doesn't just produce data; it tells a story of durability and reveals the fundamental character of each alloy, guiding us to choose the right material for the right battle.
What are the key findings from the salt-spray corrosion test for 2205 and 316L?
Are you struggling to translate technical data from material tests into real-world performance predictions? Without a clear understanding of the results, you risk either over-engineering and overspending on materials or, far worse, under-engineering and facing catastrophic failure. This section will break down the key findings from the salt-spray test, translating complex results into practical insights for your projects.
The most crucial finding is the significant difference in the time it takes for the first signs of red rust to appear. In a standardized salt-spray chamber, Duplex 2205 plate typically endures hundreds of hours longer than 316L before showing corrosion, highlighting its superior resistance.
These findings are more than just numbers on a certificate; they are a direct indicator of service life and reliability in chloride-rich environments. I recall a project with a client in the Middle East who was designing a coastal processing facility. They were initially leaning towards 316L for all their storage tanks to manage upfront costs. However, after we walked them through our side-by-side salt-spray test results, which visually demonstrated the rapid onset of pitting on the 316L sample compared to the pristine surface of the 2205 plate after the same duration, their perspective shifted. They realized that for tanks holding brine and other corrosive materials, the higher initial investment in 2205 wasn't a cost—it was insurance against future downtime and replacement expenses. This decision-making process, moving from a price focus to a performance focus, is something we champion at MFY. It’s about building infrastructure that lasts, and that journey begins with understanding what the tests are truly telling us. The visual and quantitative evidence from a simple salt-spray test can be one of the most powerful tools in an engineer's arsenal.

In a typical ASTM B117 neutral salt spray test, the visual evidence tells a compelling story. For a 316L stainless steel plate, it's not uncommon to see the first pinpoint rust spots—the initial signs of pitting corrosion—within 72 to 96 hours. These tiny spots can then slowly grow and multiply as the test continues. In stark contrast, a Duplex 2205 plate often remains completely free of any red rust for well over 500 hours, and in many cases, can exceed 1,000 hours without issue. This stark difference isn't just academic; for a component exposed to marine air or road salt, this can be the difference between a service life of a few years versus a few decades.
Interpreting the Pitting Resistance Equivalent Number (PREN)
The performance difference observed in the salt-spray test is not magic; it's predictable science, quantifiable by the Pitting Resistance Equivalent Number (PREN). This value is calculated from the steel's chemical composition and provides a reliable estimate of its resistance to localized pitting corrosion. The formula is: $PREN = \%Cr + 3.3 \times \%Mo + 16 \times \%N$. The higher the PREN, the greater the resistance.
For Grade 316L, with approximately 17% chromium, 2.1% molybdenum, and negligible effective nitrogen, the PREN is around 24. For Duplex 2205, with its higher 22% chromium, 3.2% molybdenum, and 0.15% nitrogen, the PREN jumps to over 35. This nearly 50% increase in the PREN value directly correlates to the dramatically improved performance we see in the salt-spray chamber. It's a clear, numerical justification for 2205's superior corrosion resistance.
Element | Grade 316L (Typical) | Duplex 2205 (Typical) | Contribution to Corrosion Resistance |
---|---|---|---|
Chromium (Cr) | ~17.0% | ~22.5% | Forms the primary passive layer for protection. |
Molybdenum (Mo) | ~2.1% | ~3.2% | Significantly enhances resistance to pitting. |
Nitrogen (N) | ~0.03% | ~0.15% | Strengthens the passive layer and increases PREN. |
PREN Value | ~24 | ~36 | Higher value indicates superior pitting resistance. |
From Lab Test to Real-World Reliability
It’s crucial to connect these accelerated lab results to real-world applications. A salt-spray test simulates aggressive conditions to quickly differentiate between materials. This is invaluable for industries where chloride exposure is a constant threat. Consider a client of ours in Southeast Asia who operates a large fleet of chemical transport tankers. They previously used 316L for their tanks and constantly battled pitting corrosion when transporting certain industrial chlorides, leading to frequent and costly repairs.
After consulting with our technical team at MFY, they decided to build their next batch of tankers using Duplex 2205 plate. The decision was heavily influenced by the PREN values and our internal corrosion test data. The result? The new 2205 tankers have been in service for several years with virtually no signs of the pitting that plagued their 316L fleet. This not only saved them significant maintenance costs but also increased the operational availability and safety of their assets, proving that an informed material choice based on test data directly translates to a stronger bottom line.
How do the corrosion resistance levels of 2205 and 316L compare?
Are you concerned that focusing on a single test might obscure other potential failure modes? The term "corrosion resistance" is broad, and a material that excels in one area might be vulnerable in another, such as stress corrosion cracking and pitting corrosion4, leading to unexpected and dangerous failures. We will now directly compare 2205 and 316L across various corrosion types to give you a complete picture of their capabilities.
Duplex 2205 offers substantially higher resistance to pitting, crevice corrosion, and especially stress corrosion cracking compared to 316L. While 316L provides good general corrosion resistance, 2205's unique duplex microstructure provides a significant performance upgrade in more aggressive, chloride-rich conditions.
A holistic view is essential for long-term reliability. In my career, I've seen projects where engineers focused intensely on preventing pitting corrosion but completely overlooked the risk of stress corrosion cracking (SCC), simply because it's a less common but more insidious failure mechanism. This can be a critical mistake, especially in heated or high-stress applications. For example, a heat exchanger operating with hot, chlorinated water is a classic environment where 316L, despite its good name, can become susceptible to SCC. Understanding the full comparative profile of these two alloys is not just good engineering; it's a fundamental aspect of risk management. It ensures that the material you select is robust against all the challenges it will face in its intended service environment, not just the most obvious ones.
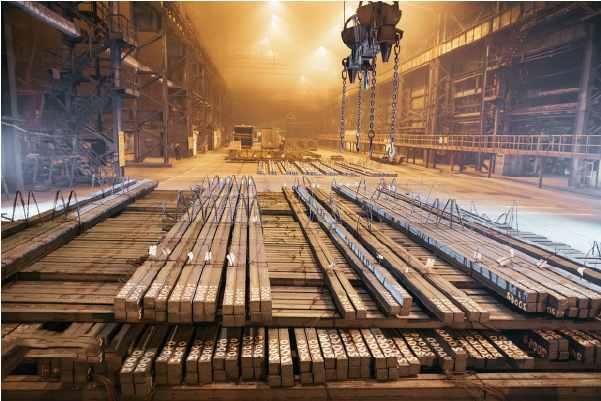
The battle against corrosion is fought on multiple fronts. While the salt-spray test5 is an excellent indicator of pitting resistance, a full comparison must also consider other common forms of attack, such as crevice corrosion and stress corrosion cracking (SCC). It's in this broader comparison that the advantages of Duplex 2205 become even more pronounced, justifying its selection for the most demanding applications. This deeper understanding allows our clients at MFY to make choices that ensure long-term integrity and safety.
Pitting and Crevice Corrosion: The Chloride Challenge
Pitting corrosion is the localized breakdown of the passive layer, forming small pits that can rapidly penetrate the material. Crevice corrosion is a similar localized attack that occurs in tight spaces (like under gaskets or in un-welded overlaps) where oxygen is depleted and chlorides can concentrate. As established by the PREN, 2205's higher chromium, molybdenum, and nitrogen content6 gives it a far more resilient passive layer. A useful metric here is the Critical Pitting Temperature (CPT), the temperature at which pitting begins in a specific chloride solution. For 316L, the CPT can be as low as 25°C in standard test solutions. Duplex 2205, by contrast, often has a CPT above 80°C, making it suitable for heated, high-chloride environments where 316L would fail.
An engineering firm we work with in India was designing a water treatment plant that involved a filtration stage where seawater was slightly heated. Their initial design used 316L piping. We highlighted the risk of both pitting and crevice corrosion at the flanged connections given the elevated temperature. By presenting the CPT data for both grades, we demonstrated that 2205 offered a much larger safety margin. They revised the specification to 2205 for the critical sections, preventing what could have been a chronic maintenance problem and ensuring the plant's operational reliability from day one.
Stress Corrosion Cracking (SCC): The Hidden Danger
Stress Corrosion Cracking is a particularly dangerous form of failure, as it can occur at stress levels well below the material's yield strength and often with little to no visible warning before catastrophic failure. It requires a specific combination of tensile stress, a corrosive environment, and a susceptible material. Austenitic stainless steels like 316L are notoriously susceptible to chloride-induced SCC at temperatures above approximately 60°C (140°F). The duplex (austenitic-ferritic) microstructure of 2205 is its greatest defense against this threat. The ferrite phase within the structure acts as a barrier, effectively arresting the propagation of any stress corrosion cracks that might initiate in the austenite phase.
This property is non-negotiable in many industries. For instance, in the oil and gas sector, equipment often handles hot, sour (H₂S-containing) brines under high pressure. This combination of chlorides, temperature, and stress is a textbook recipe for SCC in 316L. Duplex 2205, and other super duplex grades, are the industry standard for this reason. Its resistance to SCC provides the security and reliability needed to operate safely in such a high-stakes environment. This intrinsic resistance is a fundamental advantage that goes far beyond what a simple salt-spray test can show.
General Corrosion: A More Balanced Comparison
While 2205 excels in resisting localized corrosion and SCC, the race is much closer when it comes to general or uniform corrosion, particularly in acidic environments. General corrosion is a more predictable, uniform loss of material from the surface. In many mineral and organic acids, the performance of 316L is often very similar to that of 2205, and in some specific cases, 316L can even have a slight edge.
For example, in a food processing plant making tomato-based sauces (which are acidic), 316L is typically more than adequate and is the cost-effective choice. The risk of chloride SCC or severe pitting is low. Here, the primary concern is maintaining hygiene and resisting uniform corrosion from organic acids, a task for which 316L is perfectly suited. This is why at MFY, our recommendations are always tailored to the specific application. We don't push for a higher-grade material unless the service environment truly demands its unique properties. It's about providing the right solution, ensuring both performance and economic viability for our clients.
What factors contribute to the difference in corrosion resistance between 2205 and 316L?
Have you ever wondered what fundamentally makes one steel grade stronger than another? It’s easy to look at specifications, but it can be difficult to grasp the underlying science. Without this core understanding, you're merely following guidelines rather than making strategic engineering decisions. This knowledge gap can limit your ability to innovate or identify more cost-effective material solutions for your projects.
The primary factors are chemical composition and physical microstructure. Duplex 2205's higher content of chromium, molybdenum, and nitrogen creates a more robust protective layer, while its two-phase (austenitic-ferritic) microstructure provides superior strength and resistance to stress corrosion cracking compared to the single-phase austenitic structure of 316L.
As a director at MFY, understanding this fundamental metallurgy is the bedrock of how we advise our clients. It enables us to explain why one material is better suited than another, building confidence and fostering a partnership based on technical expertise. When a client understands that the higher price of 2205 is directly tied to a specific alloying element that counters their biggest corrosion threat, the conversation shifts from cost to value. It’s about investing in the right chemistry and structure to guarantee performance, and that insight begins with demystifying the science behind the steel.
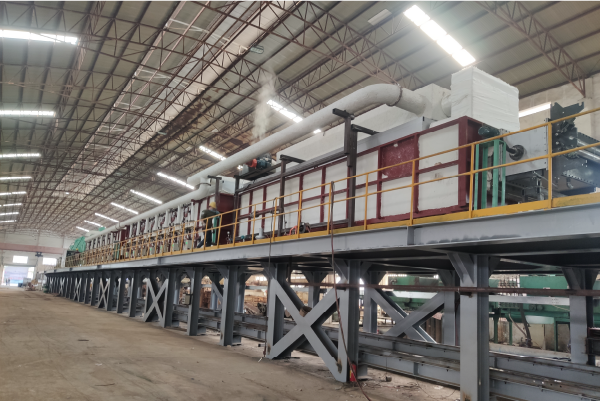
The superior performance of Duplex 2205 is not an accident; it is the result of deliberate metallurgical design7. The differences in corrosion resistance between 2205 and 316L can be traced back to two fundamental aspects: the specific alloying elements added to the iron base, and the resulting microscopic crystal structure of the steel. It's the powerful synergy between this advanced chemistry and unique microstructure that sets Duplex 2205 apart and makes it an indispensable material for modern, high-stress industries.
The Power of Alloying Elements: Cr, Mo, and N
The secret to stainless steel's corrosion resistance lies in its passive layer, a microscopically thin, invisible film of chromium oxide8 that forms on the surface and protects the iron from rusting. The quality of this layer is directly influenced by the alloying elements.
- Chromium (Cr): This is the most critical element. 2205 contains around 22% Cr, significantly more than the 17% in 316L. This higher chromium content creates a more stable, tenacious, and self-healing passive layer, providing a stronger first line of defense against corrosive attack.
- Molybdenum (Mo): This element is a specialist in fighting localized pitting corrosion. It strengthens the passive layer, making it particularly resistant to being breached by chloride ions. While both grades contain molybdenum, the higher percentage in 2205 (~3.2% vs. ~2.1%) provides a substantial boost in pitting resistance.
- Nitrogen (N): Nitrogen is a key differentiator for duplex grades. When added to the steel, it significantly enhances pitting resistance (as reflected in the PREN formula) and also increases the steel's strength. The intentional addition of ~0.15% nitrogen in 2205 is a primary reason for its leap in performance over 316L.
Microstructure Matters: Duplex vs. Austenitic
Beyond chemistry, the physical arrangement of the crystals in the steel—its microstructure—plays a decisive role. 316L is an austenitic stainless steel, meaning it has a single-phase structure of face-centered cubic crystals. This structure makes it tough and easy to form and weld, but as discussed, it is vulnerable to chloride stress corrosion cracking.
Duplex 2205, as its name implies, has a two-phase microstructure consisting of a balanced mixture of austenite and ferrite (a body-centered cubic crystal structure). You can think of it as a composite material at the microscopic level. This duplex structure combines the best attributes of both phases: the austenite provides good toughness and general corrosion resistance, while the ferrite provides high strength and, crucially, excellent resistance to stress corrosion cracking. The interface between these two phases acts to deflect and arrest the propagation of cracks, giving the material its signature toughness and reliability under stress.
The Synergy of Composition and Structure
It is the combination of these two factors—enhanced chemistry and a duplex structure—that gives 2205 its remarkable capabilities. The high alloy content creates a superior passive film capable of withstanding aggressive chloride environments, while the duplex microstructure provides a safety net against stress corrosion cracking and lends the material a higher yield strength (typically more than double that of 316L). This higher strength can be a significant advantage in its own right.
A client in the construction industry was designing a pedestrian bridge in a coastal, salt-spray-prone area. By choosing Duplex 2205 plate instead of 316L, they were not only guaranteeing long-term corrosion resistance but also able to reduce the required thickness of the structural elements due to 2205's higher strength. This reduced the overall weight and, consequently, the material cost, offsetting the higher per-kilogram price. This is a perfect example of how the inherent properties of 2205 can lead to more efficient, economical, and durable designs.
What measures can be taken to enhance the corrosion resistance of stainless steel plates?
Are you trying to maximize the lifespan of your steel components after you've already made your material selection? Poor handling, improper fabrication techniques, or a neglected surface finish can severely compromise the corrosion resistance of even the highest-grade stainless steel, effectively wasting your investment and paving the way for premature failure9.
To enhance corrosion resistance, ensure a proper surface finish through passivation and electropolishing, rigorously avoid iron contamination during fabrication, and design components to eliminate crevices and allow for complete drainage. Proper welding procedures and thorough post-weld cleaning are also critical for restoring and maintaining performance.
The job isn't finished once the purchase order is signed. The "as-specified" material must become the "as-built" reality. I once had to troubleshoot a problem for a client whose brand-new Duplex 2205 tanks were showing surface rust after just a few weeks of installation. The material was perfect, but the investigation revealed the fabricator had used carbon steel wire brushes to clean the welds. This simple, careless mistake embedded iron particles into the surface, which then rusted and compromised the passive layer. It’s a harsh lesson that the performance of a multi-million dollar asset can be dictated by the quality of a ten-dollar brush. This is why at MFY, we emphasize that material selection is only the first step; proper handling and fabrication are what lock in that long-term performance.
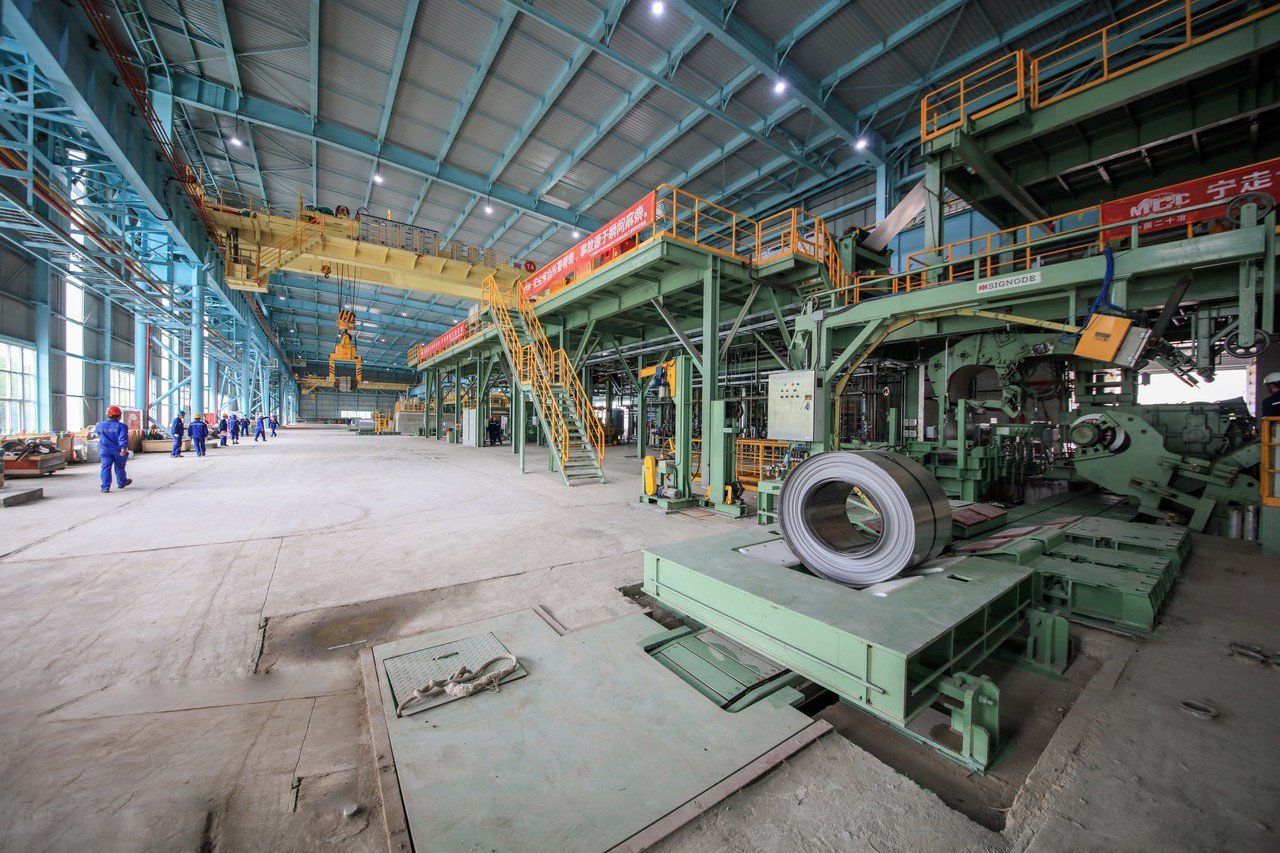
Selecting the right alloy is the cornerstone of corrosion control10, but it's not the whole story. The way a stainless steel plate is handled, fabricated, and finished can have a profound impact on its final performance. At MFY, we not only supply high-quality materials but also provide the technical guidance to ensure our clients unlock the full potential of their investment. Implementing best practices throughout the project lifecycle is key to achieving maximum durability and preventing premature failures that can arise from seemingly minor oversights.
Surface Finish and Passivation: The First Line of Defense
The surface of stainless steel is where the battle against corrosion is won or lost. A smooth, clean, and uncontaminated surface will always outperform a rough or dirty one. Rough surfaces can trap moisture and contaminants, creating ideal initiation sites for pitting. To optimize the surface, two key processes are employed:
- Passivation: This is a post-fabrication chemical treatment, typically using nitric acid or citric acid. Its purpose is twofold: first, it removes any free iron and other metallic contaminants left over from the manufacturing and fabrication processes. Second, it enhances the natural chromium-oxide passive layer, making it thicker, more uniform, and more protective. Passivation should be a standard final step for any high-performance stainless steel component.
- Electropolishing: For the most demanding applications, such as in the pharmaceutical or semiconductor industries, electropolishing offers the ultimate surface finish. It is an electrochemical process that removes a microscopic layer of the surface material, leveling out peaks and valleys. The result is an exceptionally smooth, mirror-like finish that is incredibly easy to clean and offers maximum resistance to corrosion by eliminating potential initiation sites.
Fabrication and Welding Best Practices
The fabrication shop can be a minefield of potential contamination. To preserve the integrity of stainless steel, a disciplined approach is essential.
- Avoiding Iron Contamination: This is the golden rule. Stainless steel should be fabricated in a dedicated area, away from carbon steel work. All tools—grinders, brushes, clamps, and handling equipment—must be exclusively used for stainless steel. A single touch with a tool used on carbon steel can transfer iron particles and lead to rusting.
- Proper Welding: Welding is a critical step that requires precision. Firstly, the correct filler metal must be used (e.g., a 2209 filler for welding 2205 base metal) to ensure the weld seam has comparable properties to the parent material. Secondly, the heat-affected zone next to the weld, often identified by a blue/gold "heat tint," has a temporarily depleted chromium layer and is susceptible to corrosion. This tint must be completely removed through mechanical means (grinding with a dedicated stainless brush) followed by chemical treatment with a pickling paste and subsequent passivation to fully restore corrosion resistance.
Design for Corrosion Control
Often, the best way to fight corrosion is to design the problem out of existence from the beginning. Thoughtful design can dramatically enhance the longevity of a component.
- Eliminate Crevices: Wherever possible, design to avoid tight gaps, sharp corners, and overlapping surfaces that can trap stagnant fluid. These crevices are prime locations for crevice corrosion. Specify continuous, smooth welds instead of intermittent or skip welds.
- Promote Drainage: For tanks, vessels, and piping systems, ensure the design allows for complete and total drainage. This prevents corrosive solutions from pooling during shutdowns, concentrating over time, and initiating corrosion.
- Isolate Dissimilar Metals: A common design error is to bolt a stainless steel component directly to a carbon steel or aluminum structure in the presence of moisture. This creates a galvanic cell, where the less noble metal will corrode at an accelerated rate. Always use insulating gaskets and washers to electrically isolate dissimilar metals and prevent this type of failure. I have seen contractors in the construction field overlook this, leading to the rapid deterioration of carbon steel supports attached to stainless steel facades.
What are the recommended uses for 2205 and 316L based on their corrosion test results?
Are you now ready to apply this knowledge but need clear, practical guidance on matching the right material to your specific application? Making the final choice can still feel daunting. Selecting a material that is overkill for the job is an unnecessary expense, while choosing an under-specified material is a direct risk to reliability and safety.
Based on its superior salt-spray performance and resistance to SCC, Duplex 2205 is recommended for marine hardware, desalination plants, and chemical processing involving chlorides. 316L remains the efficient, cost-effective choice for food processing, pharmaceutical equipment, and architectural applications in less corrosive environments.
The philosophy at MFY is not just to sell steel; it's to provide the right solution that ensures our clients' success. Sometimes, that means recommending the robust performance of Duplex 2205 for a critical application. Other times, it means confirming that the trusted and economical Grade 316L is more than sufficient for the task at hand. Our goal is to build long-term partnerships founded on trust and technical expertise. This final section will help you make that right choice, balancing performance, cost, and risk for your specific project context.
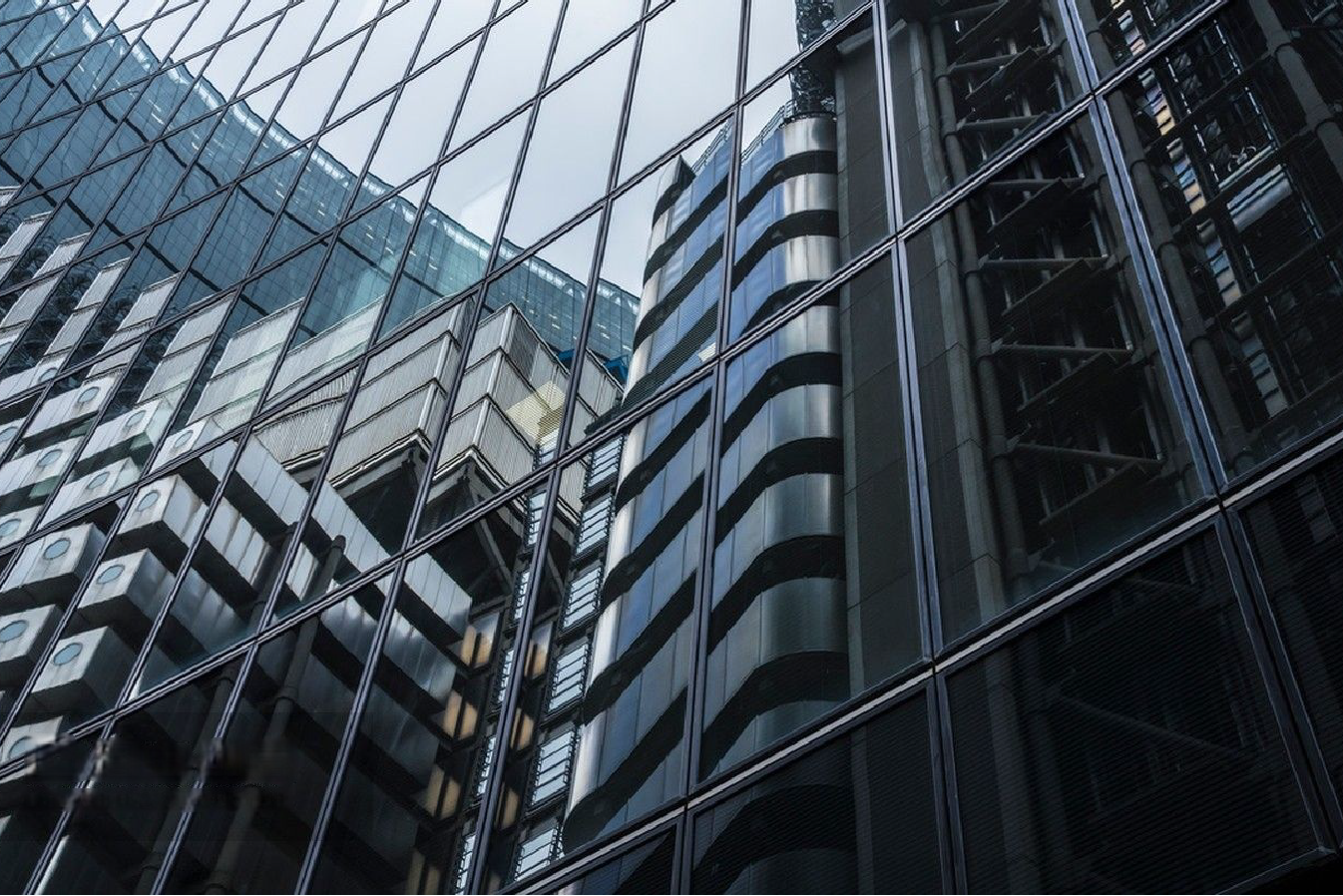
The ultimate goal of any corrosion testing is to inform intelligent material selection. The results from salt-spray tests, combined with an understanding of different corrosion mechanisms11, allow us to map the strengths of each grade to specific industrial applications. Choosing correctly is a strategic decision that balances upfront investment with long-term performance and reliability. It’s about ensuring the material is not just adequate, but optimal for its intended service life.
When to Choose Grade 316L: The Versatile Workhorse
Grade 316L has earned its reputation as an industry workhorse for good reason. It offers excellent corrosion resistance in a wide range of environments, is readily available, and is familiar to fabricators worldwide. Its selection is the smart, economical choice when the extreme performance of a duplex grade is not required.
- Key Industries:
- Food, Dairy, and Beverage: For equipment like tanks, pipes, and mixers that require high levels of hygiene and resistance to organic acids but have low chloride exposure, 316L is the industry standard.
- Pharmaceutical and Biomedical: In high-purity water systems, reactors, and sanitary fittings, the excellent surface finish and cleanability of 316L (often electropolished) are paramount.
- Architectural: For building facades, railings, and interior design elements in non-coastal urban and rural environments, 316L provides the desired aesthetic appeal and long-term durability against atmospheric corrosion.
- Cost-Benefit Analysis: In these applications, the additional cost of Duplex 2205 would not provide a proportional benefit. 316L is fully capable of meeting the service demands, making it the most resource-efficient choice. As a supplier, we frequently guide clients in the food processing and architectural sectors toward 316L to optimize their project budgets without compromising quality.
When to Upgrade to Duplex 2205: For Demanding Applications
Duplex 2205 is the solution when the service conditions become more severe. Its higher cost is an investment in reliability against aggressive corrosion and mechanical stress. The decision to upgrade is typically driven by the presence of chlorides, elevated temperatures, and high mechanical loads.
- Key Industries:
- Marine and Offshore: From boat shafts and rudders exposed to constant seawater immersion to structural components on oil and gas platforms battered by salt spray, 2205’s resistance to pitting and crevice corrosion is essential.
- Chemical Processing: For pressure vessels, heat exchangers, and piping that handle chlorides, caustics, and other aggressive chemicals, 2205’s resistance to both pitting and stress corrosion cracking is critical for safety and longevity.
- Desalination and Water Treatment: In reverse osmosis plants, 2205 is used for high-pressure pumps, piping, and vessels that handle concentrated brine, an environment where 316L would rapidly fail.
- Pulp and Paper: Equipment like bleach washers and digesters, which operate in hot, chloride-containing environments, rely on duplex steels to prevent SCC and pitting.
A Strategic Selection Matrix
To simplify the decision-making process, here is a quick-reference guide matching common applications to the recommended grade. I recently worked with an engineering contractor on a large, multi-faceted industrial park in Southeast Asia. We used a similar matrix to help them allocate the right materials efficiently, specifying 2205 for their coastal water intake and chemical storage areas, while using 316L for the food processing and domestic plumbing systems, optimizing both cost and performance across the entire project.
Application / Industry | Key Environmental Challenge | Recommended Grade | Justification |
---|---|---|---|
Coastal Architectural Railing | High chloride from salt spray | Duplex 2205 | Superior resistance to pitting and crevice corrosion. |
Dairy Processing Tank | Hygiene, organic acids, low chlorides | 316L | Sufficient corrosion resistance and cost-effective. |
Chemical Storage Tank (>1000 ppm Cl⁻) | High chloride concentration, SCC risk | Duplex 2205 | Essential for preventing pitting and SCC failure. |
Hospital Surgical Tray | Sterilization, hygiene, surface purity | 316L | Excellent cleanability and resistance to sterilization. |
Subsea Pipeline | High pressure, external seawater | Duplex 2205 | High strength and immunity to chloride SCC are critical. |
Brewery Fermentation Vessel | Mildly acidic, low chlorides | 316L | The industry standard; provides reliable performance. |
Conclusion
Ultimately, 2205's superior performance in salt-spray tests, driven by its advanced chemistry and duplex structure, makes it essential for high-chloride, high-stress environments. While 316L remains a versatile and reliable standard, choosing 2205 for demanding applications is a strategic investment in long-term safety and operational longevity.
-
Learn the basics of salt-spray testing standards and their role in comparing stainless steel grades ↩
-
Find the origins and analysis behind the $2.5 trillion annual corrosion cost figure ↩
-
Understand how salt-spray tests simulate corrosion in industrial stainless steels ↩
-
Learn the definitions and distinct risks posed by different forms of corrosion in stainless steels ↩
-
See how the salt-spray test is used to predict pitting in stainless steels like 316L and 2205 ↩
-
Discover how PREN is calculated and why it matters in selecting corrosion-resistant stainless steel grades ↩
-
Discover the intentional material engineering behind the superior properties of duplex 2205. ↩
-
Understand how the passive layer formed by chromium provides rust resistance in stainless steels. ↩
-
Learn why correct handling is critical for preserving stainless steel’s corrosion resistance ↩
-
Find out how alloy composition impacts corrosion performance in various environments ↩
-
Explore how testing and corrosion science help match materials to industrial needs ↩
Have Questions or Need More Information?
Get in touch with us for personalized assistance and expert advice.